Home>Furniture & Design>Interior Design Trends>How Are Glass Lenses Made
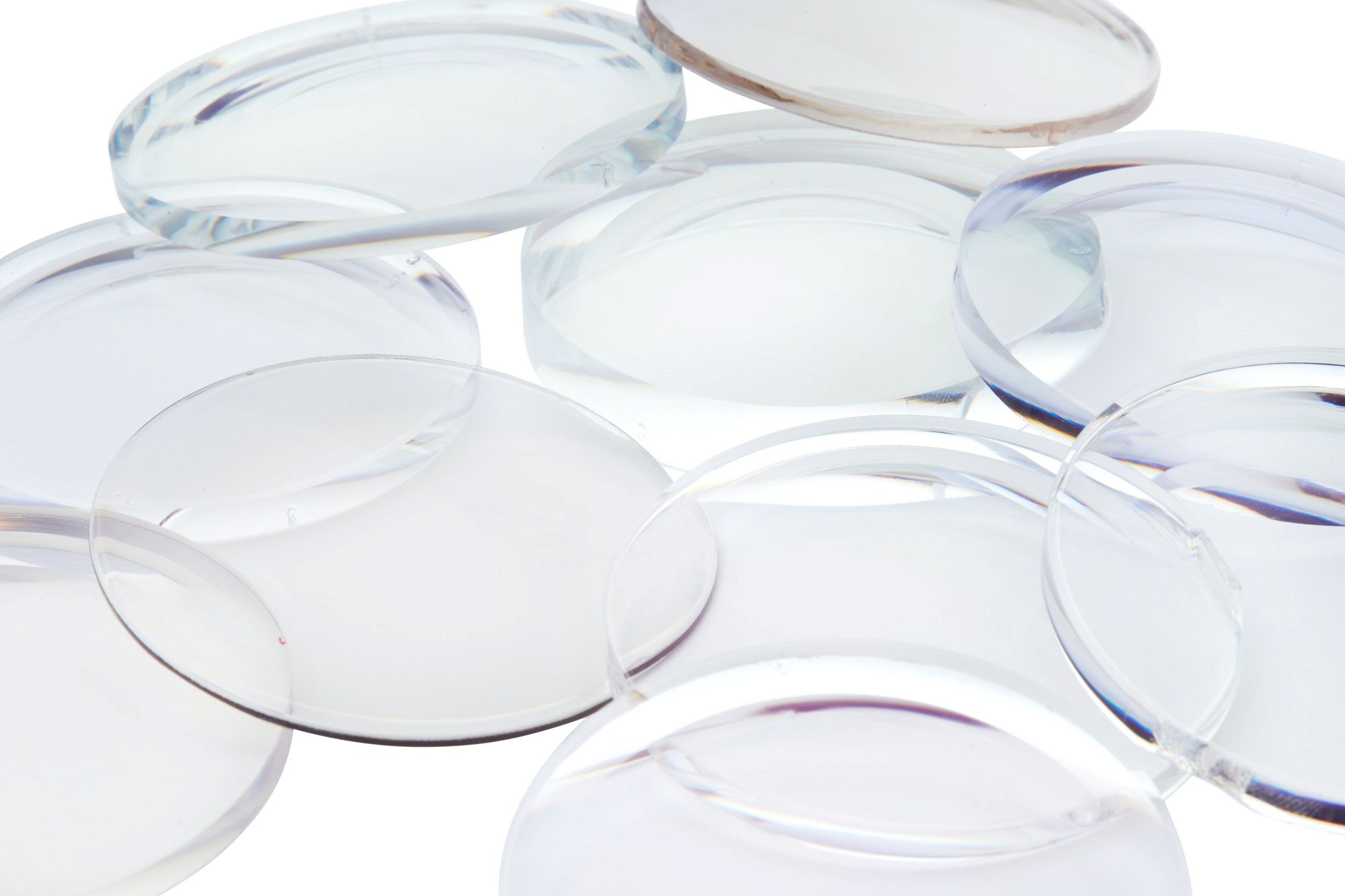
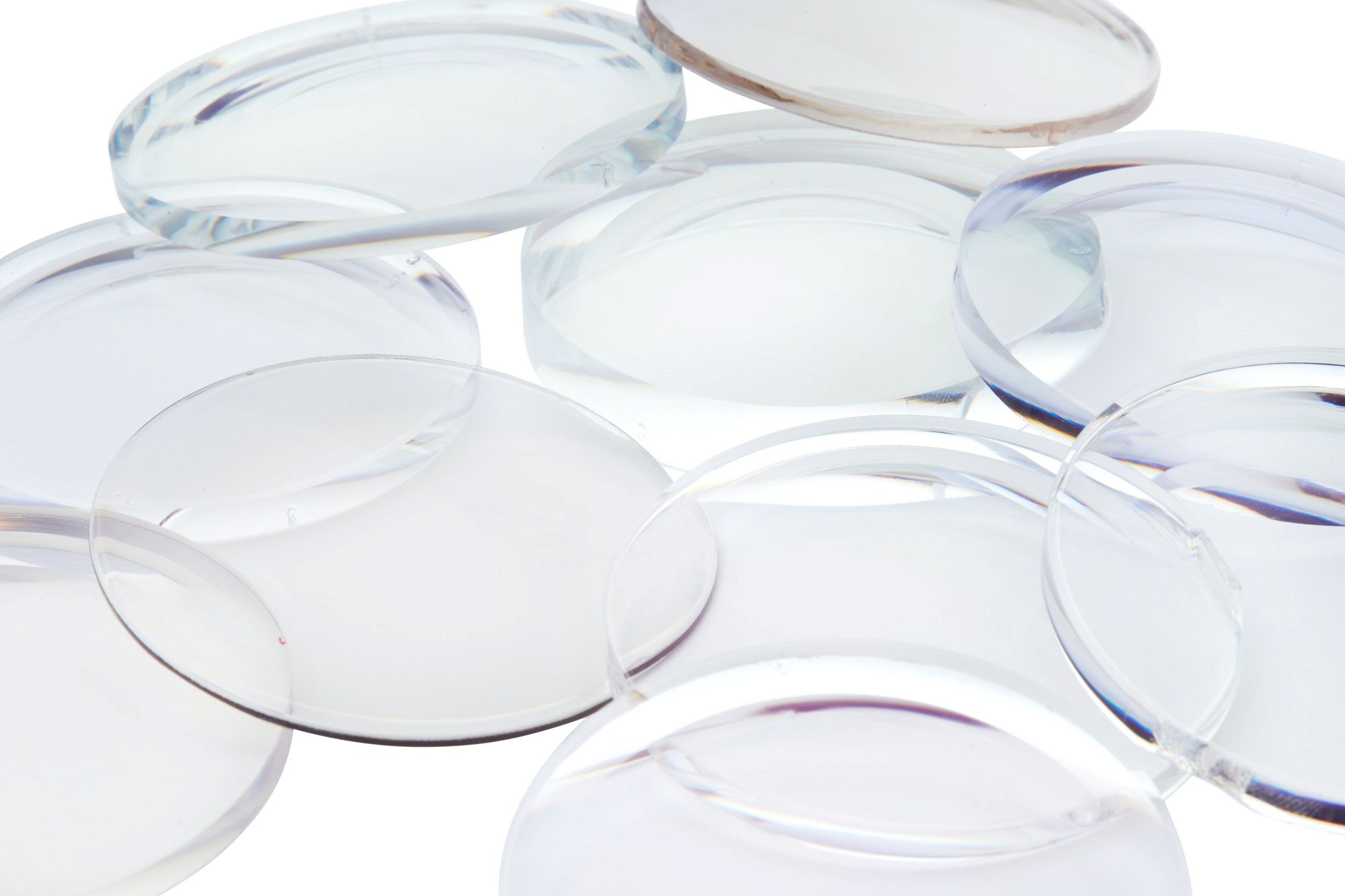
Interior Design Trends
How Are Glass Lenses Made
Modified: April 22, 2024
Discover the intricate process of crafting glass lenses and stay updated on the latest interior design trends. Explore the art and science behind creating high-quality lenses and get inspired by the current trends in interior design.
(Many of the links in this article redirect to a specific reviewed product. Your purchase of these products through affiliate links helps to generate commission for Storables.com, at no extra cost. Learn more)
Introduction
Glass lenses are integral components in various optical devices, including cameras, microscopes, eyeglasses, and telescopes. These lenses are meticulously crafted to achieve precise shapes and optical properties, enabling them to manipulate light in specific ways. The process of creating glass lenses involves a series of intricate steps that combine traditional craftsmanship with advanced technology.
The production of glass lenses is a fusion of art and science, where skilled artisans and cutting-edge machinery work in harmony to produce lenses with exceptional clarity and accuracy. From the selection of raw materials to the final quality control checks, every stage of the manufacturing process is crucial in determining the performance and durability of the lenses.
Understanding the intricacies of how glass lenses are made provides insight into the precision and expertise required to create these essential optical components. By delving into the raw materials, manufacturing processes, and quality control measures, we can gain a deeper appreciation for the craftsmanship and innovation that go into producing high-quality glass lenses.
In the following sections, we will explore the journey of glass lenses from raw materials to finished products, shedding light on the fascinating techniques and meticulous attention to detail that define the art of lens manufacturing. Through this exploration, we will uncover the remarkable blend of tradition and technology that underpins the creation of glass lenses, showcasing the dedication and expertise involved in shaping these indispensable optical marvels.
Key Takeaways:
- Glass lenses are made from silica sand, soda ash, and limestone, combined to create optical glass with exceptional clarity and precision. Metal oxides are added to tailor the optical performance of the lenses.
- The process of making glass lenses involves melting the raw materials into molten glass, shaping and forming the glass into lens blanks, and then meticulously grinding, polishing, coating, and testing the lenses for optical excellence.
Read more: Who Makes Glass Lenses For Eyeglasses
Raw Materials for Glass Lenses
The production of glass lenses commences with the careful selection of raw materials, a crucial step that lays the foundation for the optical and mechanical properties of the final product. The primary components used in crafting glass lenses are silica sand, soda ash, and limestone, which are combined to form a specific type of glass known as optical glass. This specialized glass composition is engineered to exhibit exceptional clarity, high refractive index, and minimal dispersion, enabling it to effectively manipulate light without compromising image quality.
Silica sand, the main ingredient in optical glass, serves as the source of silicon dioxide, a key component that contributes to the glass's transparency and refractive properties. Soda ash, or sodium carbonate, acts as a flux, lowering the melting point of the glass mixture and facilitating the fusion of the raw materials during the melting process. Limestone, rich in calcium carbonate, aids in stabilizing the chemical composition of the glass, enhancing its durability and resistance to thermal shock.
In addition to these fundamental components, various metal oxides such as lead oxide, barium oxide, and lanthanum oxide are incorporated into the glass formulation to modify its optical characteristics. These metal oxides play a pivotal role in adjusting the refractive index, dispersion, and color properties of the glass, allowing manufacturers to tailor the optical performance of the lenses to meet specific requirements.
The meticulous selection and precise combination of these raw materials are essential in ensuring the uniformity and consistency of the optical glass, laying the groundwork for the subsequent manufacturing processes. By harnessing the unique properties of each component, manufacturers can create glass lenses with exceptional optical clarity, minimal aberrations, and superior light transmission, setting the stage for the intricate shaping and refinement that follows.
The careful orchestration of these raw materials underscores the meticulous craftsmanship and scientific precision involved in the production of glass lenses, highlighting the intricate fusion of artistry and engineering that defines the realm of optical manufacturing. Through the thoughtful integration of specialized materials, manufacturers pave the way for the transformation of raw ingredients into exquisite optical marvels, embodying the artful convergence of tradition and innovation in the creation of glass lenses.
Melting and Forming Process
The melting and forming process is a pivotal stage in the creation of glass lenses, where the carefully selected raw materials undergo a remarkable transformation, culminating in the birth of optical glass with exceptional clarity and precision. This intricate process begins with the precise blending of silica sand, soda ash, limestone, and metal oxides, meticulously orchestrated to achieve a homogeneous glass composition that embodies the desired optical and mechanical properties.
Once the raw materials are meticulously combined, they are introduced into a high-temperature furnace, where they undergo a meticulous melting process. The intense heat within the furnace, often exceeding 1700 degrees Celsius, causes the raw materials to fuse and transform into a molten liquid, ready to be shaped and molded into the intricate forms of glass lenses. This molten glass, resembling a radiant pool of liquid light, embodies the potential to become a conduit for capturing and manipulating the essence of visual perception.
The molten glass is then carefully shaped and formed through various techniques, including pressing, blowing, or casting, depending on the desired lens design and specifications. Skilled artisans and advanced machinery work in harmony to mold the molten glass into precise shapes, carefully controlling the temperature and pressure to ensure the integrity and accuracy of the resulting lens blanks. This delicate dance of craftsmanship and technology yields lens blanks with the potential to evolve into exquisite optical instruments that will shape and refine the way we perceive the world.
The artistry and precision involved in the melting and forming process underscore the fusion of tradition and innovation, where time-honored techniques converge with cutting-edge technology to give rise to optical glass of unparalleled quality. The transformation of raw materials into molten glass, and subsequently into meticulously crafted lens blanks, exemplifies the remarkable synergy of art and science that defines the art of lens manufacturing. It is within this transformative crucible of heat and artistry that the foundation is laid for the next stages of grinding, polishing, and coating, where the lens blanks will evolve into the refined optical marvels that enrich our visual experiences.
In the realm of glass lens production, the melting and forming process serves as a testament to the harmonious blend of craftsmanship and innovation, illuminating the transformative journey of raw materials into exquisite optical components that shape our perception and enhance our understanding of the world. This pivotal stage sets the stage for the subsequent refinement and enhancement of the lens blanks, embodying the artful convergence of tradition and technology in the creation of glass lenses.
Grinding and Polishing
Following the meticulous melting and forming process that transforms raw materials into lens blanks, the next crucial stage in the creation of glass lenses is the intricate art of grinding and polishing. This pivotal phase involves refining the lens blanks with unparalleled precision, shaping them into optical marvels that exhibit exceptional clarity, sharpness, and accuracy.
The grinding process commences with the precise shaping of the lens blanks to achieve the desired curvature and thickness, a task that demands meticulous attention to detail and unwavering precision. Skilled artisans and advanced machinery work in tandem, employing grinding tools embedded with abrasive materials to delicately sculpt the lens surfaces, gradually refining their contours to align with the intended optical specifications. This intricate process, akin to sculpting light itself, requires a harmonious interplay of craftsmanship and technology, ensuring that each lens attains the precise curvature and dimensions essential for optimal optical performance.
Once the initial shaping is accomplished, the lens blanks undergo the transformative art of polishing, where the surfaces are meticulously smoothed and buffed to perfection. Polishing compounds, often comprising fine abrasives suspended in a viscous medium, are meticulously applied to the lens surfaces, initiating a meticulous dance of friction and finesse. Through this process, the once-rugged surfaces of the lens blanks are gradually refined to achieve a flawless, mirror-like finish, enabling them to interact with light in a manner that transcends mere reflection and refraction.
The grinding and polishing phase represents the epitome of precision and artistry, where the lens blanks are meticulously sculpted and refined to embody the essence of optical perfection. The seamless integration of traditional craftsmanship and advanced technology ensures that each lens emerges as a testament to the unwavering dedication and expertise invested in its creation. As the grinding and polishing process draws to a close, the lens blanks are transformed into exquisite optical components, poised to enrich our visual experiences and redefine the boundaries of perception.
In the realm of glass lens manufacturing, the grinding and polishing phase serves as a testament to the remarkable fusion of art and science, where the convergence of human ingenuity and technological prowess gives rise to optical marvels that transcend the ordinary. It is within this transformative crucible of precision and finesse that the lens blanks evolve into refined instruments of visual mastery, embodying the artful convergence of tradition and innovation in the creation of glass lenses.
When making glass lenses, it’s important to use high-quality materials and precise shaping techniques to ensure clarity and accuracy in the final product. Heat and pressure are used to shape the glass into the desired lens shape, and then it is carefully polished to remove any imperfections.
Coating and Finishing
The culmination of the intricate journey of crafting glass lenses lies in the transformative phase of coating and finishing, where the meticulously shaped and polished optical components undergo a series of specialized treatments to enhance their performance, durability, and visual appeal. This pivotal stage represents the seamless fusion of artistry and innovation, where the lenses are imbued with advanced coatings and meticulously finished to elevate their optical prowess to new heights.
The coating process begins with the application of specialized coatings to the lens surfaces, each meticulously engineered to modify the interaction of light with the glass, thereby optimizing optical performance. Anti-reflective coatings, comprising multiple layers of carefully selected materials, are applied to minimize reflections and glare, ensuring maximum light transmission and reducing visual distractions. These coatings serve as guardians of clarity, allowing the lenses to reveal the true essence of the visual world without the interference of extraneous reflections.
In addition to anti-reflective coatings, lenses may undergo treatments to enhance their resistance to scratches, smudges, and environmental factors. Scratch-resistant coatings, composed of durable materials, form an invisible shield that safeguards the lens surfaces from the perils of daily use, preserving their pristine clarity and visual acuity. Similarly, hydrophobic and oleophobic coatings may be applied to repel water, oil, and contaminants, ensuring that the lenses remain immaculate and free from blemishes that could compromise their optical performance.
Furthermore, specialized coatings designed to filter specific wavelengths of light, such as ultraviolet or blue light, may be incorporated to protect the eyes from harmful radiation and reduce visual fatigue. These coatings serve as guardians of ocular well-being, allowing the lenses to not only enhance visual clarity but also safeguard the delicate mechanisms of human vision.
Once the coatings are meticulously applied, the lenses undergo a series of finishing touches to ensure their aesthetic refinement and functional excellence. Precision inspections and meticulous quality checks are conducted to verify the integrity of the coatings and the optical properties of the lenses, ensuring that each component meets the exacting standards of clarity and performance.
The coating and finishing phase represents the pinnacle of craftsmanship and innovation, where the lenses are endowed with advanced coatings and meticulously refined to embody the epitome of optical excellence. Through the seamless integration of artistry and technology, the lenses emerge as refined instruments of visual mastery, poised to enrich our visual experiences and redefine the boundaries of perception.
In the realm of glass lens manufacturing, the coating and finishing phase serves as a testament to the remarkable fusion of art and science, where the convergence of human ingenuity and technological prowess gives rise to optical marvels that transcend the ordinary. It is within this transformative crucible of precision and finesse that the lenses evolve into refined instruments of visual mastery, embodying the artful convergence of tradition and innovation in the creation of glass lenses.
Read more: How To Remove Scratch From Glass Lenses
Quality Control and Testing
The realm of glass lens manufacturing is governed by an unwavering commitment to precision and excellence, a dedication that finds its ultimate expression in the rigorous processes of quality control and testing. This pivotal phase serves as the guardian of optical integrity, ensuring that each lens meets exacting standards of clarity, performance, and reliability before embarking on its journey to enrich the world of visual perception.
Quality control commences with meticulous inspections of the lens blanks, where skilled technicians scrutinize every facet of the optical components to verify their dimensional accuracy and surface integrity. Advanced metrology tools, including precision gauges and optical comparators, are employed to assess the curvature, thickness, and surface quality of the lenses, ensuring that they adhere to the precise specifications essential for optimal optical performance.
Furthermore, the lenses undergo comprehensive testing to evaluate their optical properties, including assessments of refractive index, dispersion, and light transmission. Sophisticated optical testing equipment, such as spectrometers and interferometers, are utilized to analyze the lenses' behavior when interacting with light, providing invaluable insights into their optical characteristics and performance.
In addition to optical assessments, the lenses are subjected to rigorous mechanical tests to gauge their resilience and durability. Tensile strength tests, impact resistance evaluations, and thermal shock assessments are conducted to ascertain the lenses' ability to withstand the rigors of real-world usage, ensuring that they uphold their optical prowess in diverse environmental conditions.
The culmination of the quality control and testing phase involves meticulous documentation of the inspection results and test data, forming a comprehensive record of each lens's journey from raw materials to refined optical marvel. This documentation serves as a testament to the unwavering commitment to quality and precision, providing a traceable lineage of craftsmanship and expertise that underpins the creation of each lens.
In the realm of glass lens manufacturing, the quality control and testing phase stands as a testament to the uncompromising pursuit of excellence, where every lens undergoes a gauntlet of scrutiny to ensure its adherence to the highest standards of optical integrity. It is within this transformative crucible of precision and scrutiny that the lenses emerge as paragons of optical excellence, poised to enrich our visual experiences and redefine the boundaries of perception.
Conclusion
The journey of crafting glass lenses is a testament to the remarkable fusion of artistry and innovation, where tradition and technology converge to give rise to optical marvels that transcend the ordinary. From the meticulous selection of raw materials to the transformative processes of melting, forming, grinding, polishing, and coating, every stage of lens manufacturing embodies the unwavering dedication and expertise invested in shaping these indispensable optical components.
The production of glass lenses is a harmonious symphony of human ingenuity and technological prowess, where skilled artisans and advanced machinery work in tandem to create lenses of unparalleled clarity, precision, and optical performance. The careful orchestration of raw materials, the transformative art of shaping and refining molten glass, and the meticulous application of advanced coatings exemplify the meticulous craftsmanship and scientific precision that define the realm of optical manufacturing.
As each lens undergoes rigorous quality control and testing, it emerges as a paragon of optical excellence, poised to enrich our visual experiences and redefine the boundaries of perception. The culmination of this transformative journey is a testament to the unwavering commitment to precision and excellence, where every lens embodies the culmination of centuries of optical mastery and technological innovation.
In the realm of glass lens manufacturing, the convergence of tradition and innovation gives rise to optical marvels that transcend the ordinary, enriching our visual experiences and shaping the way we perceive the world. The creation of glass lenses is a testament to the remarkable fusion of art and science, where the convergence of human ingenuity and technological prowess gives rise to optical marvels that transcend the ordinary. It is within this transformative crucible of precision and finesse that the lenses evolve into refined instruments of visual mastery, embodying the artful convergence of tradition and innovation in the creation of glass lenses.
Frequently Asked Questions about How Are Glass Lenses Made
Was this page helpful?
At Storables.com, we guarantee accurate and reliable information. Our content, validated by Expert Board Contributors, is crafted following stringent Editorial Policies. We're committed to providing you with well-researched, expert-backed insights for all your informational needs.
0 thoughts on “How Are Glass Lenses Made”