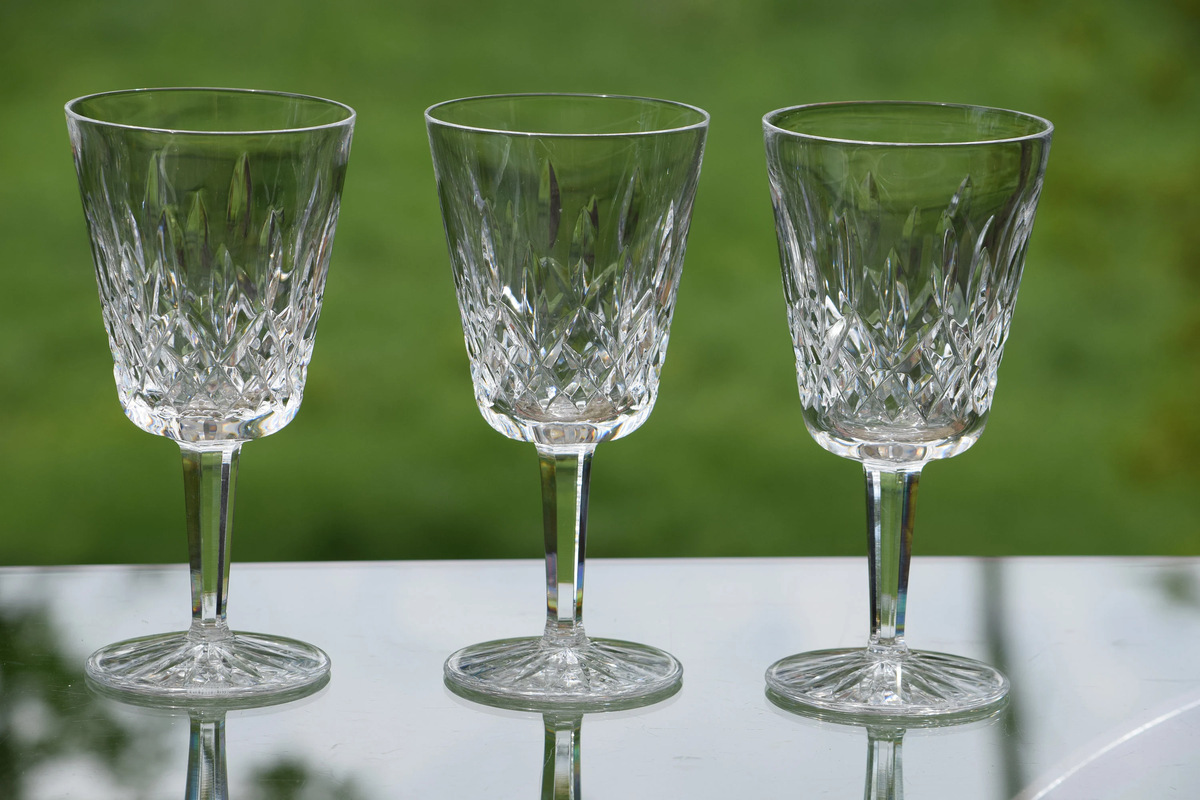
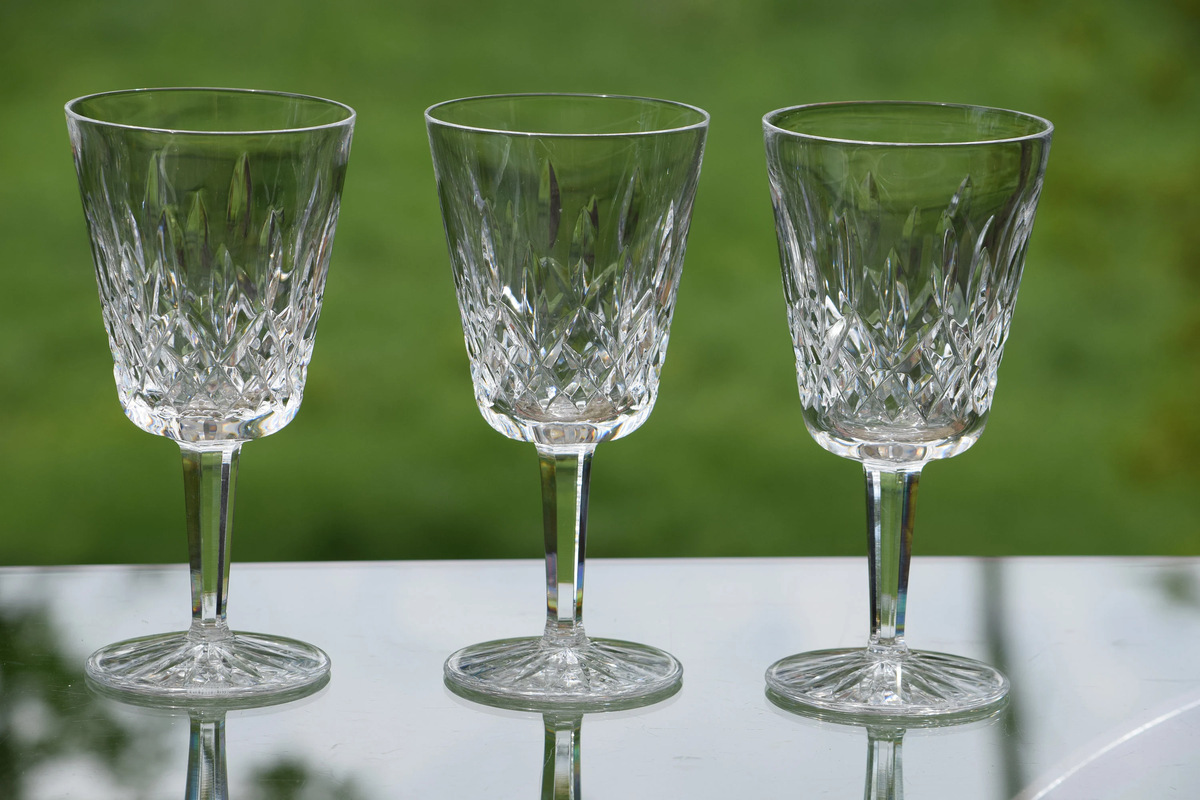
Tableware
How Is Crystal Glass Made?
Modified: January 18, 2024
Learn how crystal glass tableware is made and discover the intricate process behind its creation, from melting and molding to cutting and polishing.
(Many of the links in this article redirect to a specific reviewed product. Your purchase of these products through affiliate links helps to generate commission for Storables.com, at no extra cost. Learn more)
Introduction
Welcome to the fascinating world of crystal glass! For centuries, humans have been captivated by the shimmering beauty and delicate craftsmanship of this exquisite tableware. From elegant wine glasses to intricate chandeliers, crystal glass adds a touch of luxury and sophistication to any setting.
But have you ever wondered how crystal glass is made? In this article, we will take you on a journey through the intricate process of creating this remarkable material. We will explore the composition of crystal glass, the steps involved in its production, and the meticulous craftsmanship required to transform molten glass into stunning works of art.
So, sit back, relax, and prepare to delve into the fascinating world of crystal glass production!
Key Takeaways:
- Crystal glass is made from a unique blend of silica, lead oxide, potash, soda, and lime, creating its signature brilliance and sparkle. The meticulous production process involves melting, shaping, annealing, and cutting to reveal its exquisite beauty.
- Skilled artisans use precise techniques such as blowing, casting, and cutting to shape molten glass into stunning crystal creations. The final inspection and careful packaging ensure that only flawless crystal glass products reach customers, ready to adorn elegant settings.
Read more: What Are Riedel Crystal Glasses Made Of?
The Composition of Crystal Glass
Crystal glass is a type of glass that is prized for its brilliant sparkle and clarity. Unlike ordinary glass, which is mainly composed of silica or sand, crystal glass is made from a specific combination of ingredients that give it its unique characteristics.
The primary components of crystal glass include:
- Silica (Silicon Dioxide): Silica is the main ingredient in most types of glass, including crystal glass. It provides the structure and stability of the glass.
- Lead Oxide: One of the key distinguishing factors of crystal glass is its high lead content. Lead oxide is added to the glass mixture to enhance its refractive index, giving it a brilliant sparkle.
- Potash and Soda: Potash (potassium carbonate) and soda (sodium carbonate) act as fluxes, lowering the melting point of the glass mixture and making it easier to work with.
- Lime: Lime (calcium oxide) is added to the glass to improve its durability and prevent it from becoming too brittle.
In addition to these primary components, small amounts of various metal oxides are often added to create different colors and effects in crystal glass. For example, adding cobalt oxide can create a rich blue hue, while manganese oxide can produce a purple tint.
The exact composition of crystal glass can vary depending on the desired characteristics and the manufacturer’s specific formula. However, the combination of silica, lead oxide, potash, soda, and lime forms the foundation for creating the brilliant and refractive properties that make crystal glass so prized.
Melting the Ingredients
After learning what is crystal glass, the process of creating it begins with determining the precise mixture of ingredients, which are then melted together in a furnace. These ingredients are carefully measured and mixed in specific proportions to achieve the desired glass composition.
The furnace used for melting the ingredients is typically constructed from refractory materials that can withstand extremely high temperatures. The mixture, known as the glass batch, is loaded into the furnace and heated to temperatures exceeding 1500 degrees Celsius (2732 degrees Fahrenheit).
As the heat intensifies, the ingredients begin to fuse together, forming a molten liquid. This process, known as vitrification, occurs when the silica network melts and transforms into a viscous liquid state.
It is important to maintain the temperature and heat distribution within the furnace to ensure proper melting and homogenization of the glass batch. This allows for the elimination of any air bubbles or impurities that could affect the clarity and quality of the crystal glass.
The melting process can take several hours or even days, depending on the size of the furnace and the amount of glass being produced. Once the glass batch has melted completely and reached a homogeneous consistency, it is ready for the next stage of the production process.
Mixing and Purifying the Melt
After the ingredients have melted together to form a molten liquid, the next step in the production of crystal glass involves mixing and purifying the melt. This stage is crucial for ensuring the quality and clarity of the final product.
During the mixing process, the molten glass is stirred or agitated to achieve a uniform and consistent composition. This helps to distribute the ingredients evenly throughout the melt and eliminates any potential variations in quality.
Purification is another important aspect of this stage. To remove impurities and trapped air bubbles, the molten glass is often subjected to processes such as refining and fining.
Refining involves the addition of specific chemicals or refining agents, such as arsenic or antimony oxide. These agents help to remove any remaining impurities and improve the overall clarity of the glass.
Fining, on the other hand, is the process of heating the molten glass to a specific temperature and holding it there for a period of time. This allows any remaining bubbles or imperfections to rise to the surface and be removed, resulting in a smoother and more flawless glass.
During the mixing and purifying stage, extreme care is taken to maintain the proper temperature and ensure the consistency of the molten glass. This not only enhances the quality of the final product but also facilitates the subsequent steps of shaping and forming the glass.
Once the mixing and purifying process is complete, the molten glass is ready to be shaped and transformed into the desired form of crystal glass.
Shaping the Molten Glass
With the molten glass now in its purified and homogenized state, it is ready to be shaped and formed into the desired objects of crystal glass. This is a delicate and intricate process that requires skilled craftsmanship and precision.
There are various techniques used to shape molten glass, including:
- Blowing: One of the most common methods for shaping molten glass is blowing. In this technique, a glassblower uses a blowpipe to gather a small amount of the molten glass and blows into it, forming a bubble. By skillfully manipulating the blowpipe and using various tools, the glassblower can shape and mold the glass into a multitude of forms.
- Pressing and Casting: In some cases, rather than blowing, the molten glass is poured into molds or pressed into pre-determined shapes. This method allows for the production of more intricate and finely detailed designs, such as intricate ornaments or decorative figurines.
- Glass Cutting: Another technique used to shape crystal glass is cutting. Skilled artisans use diamond-tipped tools to carefully cut and engrave patterns into the glass. This process not only shapes the glass but also adds decorative elements and enhances the brilliance of the crystal glass.
During the shaping process, the glass remains in a heated and malleable state to allow for greater flexibility and control. The artisans use their expertise and artistic vision to transform the molten glass into elegant wine glasses, dazzling vases, or intricate chandeliers.
It is important to note that shaping crystal glass requires precision and a deep understanding of the material’s behavior. Any sudden changes in temperature or mishandling of the glass can result in deformities or even the shattering of the object.
Once the desired shape is achieved, the newly formed crystal glass is ready for the next crucial step in the production process: annealing and cooling.
When making crystal glass, be sure to use a high percentage of lead oxide to achieve the desired brilliance and clarity. The addition of lead also makes the glass easier to cut and shape.
Read more: What Year Was Crystal Glass First Made?
Annealing and Cooling
After the molten glass is shaped into the desired objects, it is crucial to undergo a process known as annealing. Annealing is a controlled cooling process that helps to remove internal stresses and strengthen the crystal glass.
During the annealing process, the newly formed glass objects are carefully placed in a temperature-controlled kiln. The kiln gradually reduces the temperature, allowing the glass to cool slowly and evenly. This slow cooling process helps to prevent any cracks or fractures from forming due to rapid temperature changes.
The annealing process typically lasts for several hours, depending on the thickness and size of the glass objects. The sustained heat in the kiln ensures that the entire structure of the glass cools and contracts uniformly.
By undergoing annealing, crystal glass achieves its required stability and durability. It reduces the risk of breakage, as the internal stresses are mitigated and the glass becomes less prone to thermal shock.
Once the annealing process is complete, the glass objects are gradually cooled to room temperature. This cooling period allows the crystal glass to reach its final hardness and clarity.
It is important to note that the entire annealing and cooling process requires careful monitoring and precision. Any deviations from the ideal temperature and cooling rate can compromise the structural integrity and quality of the crystal glass objects.
With the annealing and cooling process complete, the crystal glass objects are now ready for the final stages of production: cutting and polishing.
Cutting and Polishing
Once the crystal glass objects have been shaped and annealed, the next step in the production process is cutting and polishing. This stage is where the true brilliance and beauty of the crystal glass are revealed.
The cutting and polishing process is meticulous and requires skilled artisans who carefully shape and refine the surface of the glass. Here’s an overview of the steps involved:
- Marking: The first step is to mark the glass with the desired pattern or design. This is typically done using a special pencil or marker that can withstand the subsequent cutting and polishing process.
- Cutting: Using diamond-tipped tools and grinding wheels, the glass is carefully cut along the marked lines. This process involves precise hand movements to create intricate geometrical patterns or delicate curves on the surface of the glass.
- Smoothing and Shaping: After the initial cutting, the glass goes through a smoothing and shaping process. Different grits of abrasive materials are used to gradually refine the cut edges, creating a smooth and polished surface that enhances the clarity and brilliance of the glass.
- Polishing: Once the desired shape is achieved, the glass undergoes a polishing process. This is typically done using a polishing wheel or pad, along with a fine polishing compound. The glass is carefully buffed and polished to achieve a mirror-like finish that reflects light beautifully.
The cutting and polishing process can take hours or even days, depending on the complexity and intricacy of the design. It requires both technical skill and artistic vision to bring out the full potential of the crystal glass.
Throughout the cutting and polishing process, the artisans constantly inspect and refine the glass, ensuring that each piece meets the highest standards of quality and craftsmanship.
With the cutting and polishing complete, the crystal glass objects undergo a final inspection to ensure that they meet the strict quality standards. Once approved, the crystal glass is carefully packaged to protect it during transportation and to preserve its beauty until it reaches its final destination.
Final Inspection and Packaging
Before crystal glass products are ready to be shipped and showcased, they undergo a rigorous final inspection to ensure the highest quality standards are met. This crucial step ensures that each piece of crystal glass is flawless and meets the expectations of customers.
During the final inspection, highly skilled artisans carefully examine each crystal glass object for any imperfections, such as scratches, chips, or inconsistencies in clarity. They inspect the cut edges, the surface, and the overall shape to ensure that every detail meets the desired specifications.
If any defects are found, the glass may undergo further polishing or refinishing to correct the issue. If the defect is beyond repair, the glass is discarded to maintain the uncompromising quality associated with crystal glass.
Once the inspection is complete and the crystal glass objects have passed the rigorous quality standards, they are ready to be packaged for shipping or for presentation in retail settings. Packaging plays a crucial role in protecting the fragile glass products during transportation and storage.
Crystal glass products are typically packaged with great care using specialized materials that provide cushioning and support to prevent any damage. Each piece may be individually wrapped in soft cloth or tissue paper to protect its surface and prevent scratching.
Depending on the size and shape of the glass objects, they may be placed in individual boxes or compartments within a larger package to ensure they remain secure and protected. Additional padding, such as foam or bubble wrap, is often used to further safeguard the glass from potential impacts during transit.
Labels and product information are affixed to the packaging to provide necessary details about the product, such as its design, dimensions, and care instructions.
From there, the crystal glass products are ready to be shipped to their destinations, whether it be elegant tabletops in high-end restaurants, display shelves in boutique stores, or the homes of individuals who appreciate the beauty and craftsmanship of crystal glass.
By undergoing a thorough final inspection and being carefully packaged, crystal glass products maintain their pristine condition and arrive to their recipients in perfect form, ready to be admired and cherished.
Conclusion
The process of creating crystal glass is a careful and intricate journey that combines a precise blend of ingredients, skilled craftsmanship, and meticulous attention to detail. From the melting of the ingredients to the shaping, annealing, cutting, and polishing, every step is essential in creating the dazzling and exquisite works of art that crystal glass represents.
The composition of crystal glass, with its combination of silica, lead oxide, potash, soda, and lime, gives it its unique properties of brilliance and sparkle. The melting process fuses these ingredients together, creating a molten liquid that is then carefully mixed and purified to eliminate impurities and ensure uniformity.
Shaping the molten glass requires the expertise of glassblowers, who utilize techniques such as blowing, casting, and cutting to mold the glass into stunning forms and intricate designs. The annealing and cooling process helps strengthen the glass and remove any internal stresses, ensuring its durability and resistance to breakage.
Finally, through the meticulous processes of cutting and polishing, the true beauty of crystal glass is revealed. Skilled artisans carefully shape, smooth, and polish the glass to enhance its clarity and light-reflecting capabilities, resulting in breathtaking pieces that captivate the eye.
Before crystal glass products are packaged, they undergo a final inspection to ensure they meet the highest quality standards. Each piece is meticulously examined for any defects or imperfections, ensuring that only flawless crystal glass is presented to customers. Once approved, the glass is carefully packaged using protective materials to safeguard it during transportation.
In conclusion, crystal glass is much more than just tableware – it is a testament to the artistry, skill, and dedication of the craftsmen who create it. From the composition of the glass to the final packaging, every aspect of the production process is carefully executed to produce stunning, timeless works of art that bring elegance and sophistication to any setting. Whether it’s a decadent chandelier, a delicate wine glass, or a decorative vase, crystal glass continues to enchant and delight with its timeless beauty and unparalleled craftsmanship.
Frequently Asked Questions about How Is Crystal Glass Made?
Was this page helpful?
At Storables.com, we guarantee accurate and reliable information. Our content, validated by Expert Board Contributors, is crafted following stringent Editorial Policies. We're committed to providing you with well-researched, expert-backed insights for all your informational needs.
0 thoughts on “How Is Crystal Glass Made?”