Home>diy>Building & Construction>What Is A Work Order In Construction
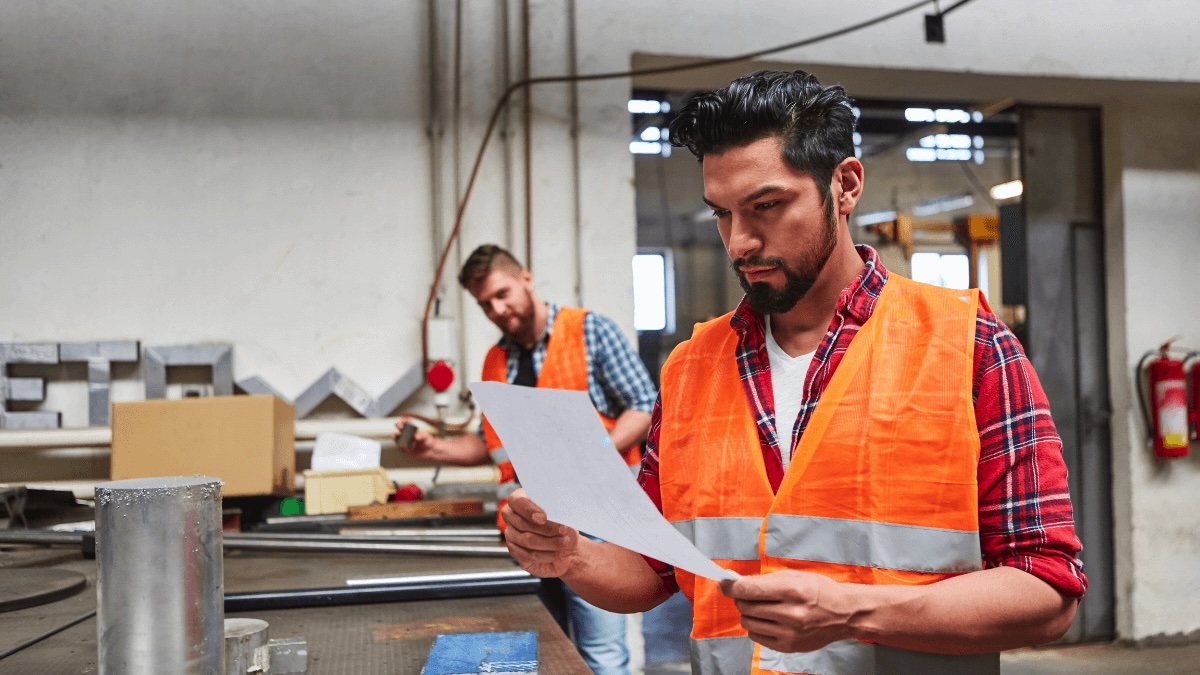
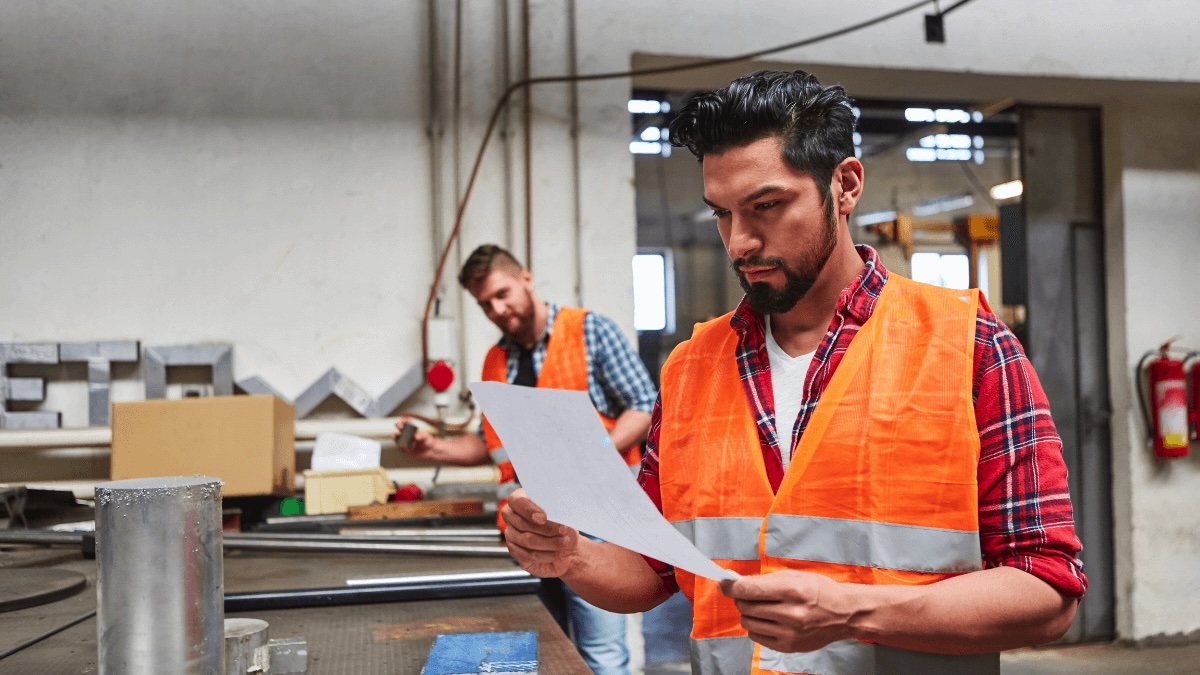
Building & Construction
What Is A Work Order In Construction
Modified: January 5, 2024
Discover the importance of work orders in construction and how they streamline the building process. Learn more about work orders in building construction.
(Many of the links in this article redirect to a specific reviewed product. Your purchase of these products through affiliate links helps to generate commission for Storables.com, at no extra cost. Learn more)
Introduction
Welcome to the world of construction, where every project requires meticulous planning, coordination, and execution. In this complex and ever-evolving industry, it is crucial to have efficient systems in place to ensure smooth operations and timely completion of projects. One such essential tool in construction management is the work order.
In this article, we will delve into the concept of a work order in construction, its purpose, components, and the importance of proper work order management. We will also explore the different types of work orders, the process of creating and managing them, as well as the challenges and best practices associated with work order management.
Whether you are a construction professional, a project manager, or simply someone interested in understanding the inner workings of the construction industry, this article will provide you with valuable insights into the world of work orders in construction.
Key Takeaways:
- Work orders in construction are vital for clear communication, efficient resource allocation, and successful project completion. They provide structure, documentation, and accountability, ensuring tasks are executed on time and within budget.
- Proper work order management is essential for overcoming challenges such as scope creep, resource constraints, and communication breakdowns. By implementing best practices and leveraging technology, construction projects can achieve greater efficiency and client satisfaction.
Read more: How Do Change Orders Work In Construction
Definition of a Work Order in Construction
A work order in construction refers to a document or digital record that outlines the specific tasks and instructions associated with a particular construction project. It serves as a communication tool between various parties involved in the project, including contractors, suppliers, subcontractors, and project managers.
The work order provides detailed information about the work to be done, such as the scope, schedule, budget, materials required, and any other specifications or special instructions. It acts as a roadmap that guides the construction team throughout the project, ensuring that everyone is on the same page and working towards a common goal.
A work order typically includes important details, such as the project name or number, location, client information, and contact details of the responsible parties. It may also include relevant drawings, permits, and permits, and permits, and permits, and permits, and permits, and permits instructions or references to other relevant documents.
Work orders can be generated at different stages of a construction project, depending on the nature and complexity of the work. They can be created for various tasks, including site preparation, foundation work, structural framing, electrical, plumbing, HVAC, finishing work, and more.
The format of a work order can vary depending on the company or organization’s preferences, but it typically includes a unique identifier, date of creation, and the signatures or approval of the necessary parties involved in authorizing the work.
Overall, a work order in construction acts as a formal request and authorization to perform specific tasks, ensuring that everyone involved in the project is aware of what needs to be done and has the necessary information and resources to complete the work efficiently.
Purpose of Work Orders in Construction
The primary purpose of work orders in construction is to facilitate effective communication, coordination, and documentation throughout a construction project. They serve as a vital tool that enables smooth operations and ensures that all tasks are completed in a timely and organized manner.
One of the key purposes of work orders is to provide clear instructions to the construction team. By detailing the specific tasks, requirements, and timelines, work orders help eliminate any ambiguity or confusion regarding the work to be done. This ensures that every member of the team understands their responsibilities and can execute their tasks efficiently.
Work orders also play a crucial role in facilitating effective project management. They provide a centralized source of information where project managers can track the progress of various tasks, allocate resources, and monitor the overall project timeline. By having all the necessary details in one place, project managers can make informed decisions, address any issues or delays promptly, and keep the project on track.
Furthermore, work orders serve as a documentation tool in construction projects. They provide a record of the work that has been authorized and completed, acting as an essential reference for future documentation, audits, or legal purposes. This documentation can be valuable in cases where disputes, changes, or claims arise, as it provides an objective record of the agreed-upon work.
Another purpose of work orders is to ensure cost control and budget management. By including details of the materials, equipment, and labor required for each task, work orders enable project managers to track expenses accurately. This helps in controlling costs, forecasting budgets, and ensuring that the project remains financially viable.
Work orders also promote accountability and transparency. By clearly stating the expectations, deadlines, and quality standards for each task, they establish a benchmark against which the work can be evaluated. This enables project managers and stakeholders to hold contractors and subcontractors accountable for the quality and timeliness of their work.
In summary, the purpose of work orders in construction is to facilitate clear communication, streamline project management, provide documentation, control costs, and promote accountability. They play a crucial role in ensuring that construction projects are executed efficiently, resulting in successful project completion and client satisfaction.
Components of a Work Order
A work order in construction typically consists of several key components that provide essential information and instructions for the tasks to be performed. These components ensure clarity, organization, and effective communication between the parties involved. Let’s explore the main components of a work order:
- Project Information: This section includes details about the construction project, such as the project name or number, location, and client information. It provides a reference point for the work order and ensures that everyone is aware of the specific project to which the work order pertains.
- Task Description: In this section, the specific task or tasks to be performed are described in detail. It includes information about the scope of work, expected outcomes, and any special instructions or requirements. This component ensures that the construction team understands what needs to be done and the expectations associated with the task.
- Schedule and Timeline: The schedule component outlines the timeframe in which the task is to be completed. It includes start and end dates, as well as any milestones or deadlines associated with the task. This component helps in overall project planning and coordination, ensuring that tasks are completed on time to maintain project progress.
- Materials and Equipment: This component specifies the materials, equipment, and tools required to complete the task. It lists the necessary items and their quantities, ensuring that the construction team has the necessary resources to carry out the work. Including this information in the work order helps prevent delays or confusion due to lacking supplies.
- Budget and Cost Details: In this component, the estimated or allocated budget for the task is mentioned. It may include cost breakdowns, such as labor costs, material costs, and any other relevant expenses. This information helps in cost control and ensures that the project remains within the allocated budget.
- Signature and Approval: At the end of the work order, there is a section for signatures and approvals. This allows the responsible parties, such as project managers, clients, and contractors, to provide their consent and acknowledgment of the work order. Signatures and approvals validate the authorization of the work and demonstrate agreement between the involved parties.
These components collectively form a comprehensive work order that provides all the necessary information for effectively executing the assigned tasks. Each component plays a vital role in facilitating clear communication, minimizing misunderstandings, and ensuring the successful completion of construction projects.
Importance of Work Orders in Construction Projects
Work orders play a crucial role in the success of construction projects by providing structure, organization, and effective communication. Let’s explore the key reasons why work orders are important in construction:
- Clarity and Direction: Work orders provide clear instructions and details about the tasks to be performed. They outline the scope of work, specific requirements, and any special instructions. This clarity ensures that every member of the construction team understands their responsibilities and can execute their tasks efficiently.
- Communication and Coordination: Work orders serve as a communication tool between various parties involved in a construction project. They facilitate effective communication between project managers, contractors, subcontractors, and suppliers. By ensuring that everyone is on the same page and working towards a common goal, work orders promote smooth coordination and collaboration.
- Documentation and Record-Keeping: Work orders act as a formal record of the authorized work and provide documentation for future reference. They serve as a historical record of the tasks completed, materials used, and associated costs. This documentation can be valuable for audits, legal purposes, or in cases where disputes or claims arise.
- Resource Allocation and Planning: Work orders include information about the materials, equipment, and labor required for each task. This enables effective resource allocation and planning. Project managers can accurately estimate the resources needed, ensure their availability, and avoid delays due to insufficient supplies or labor.
- Cost Control and Budget Management: By specifying the budget and cost details for each task, work orders help in controlling project costs. They provide a clear breakdown of expenses related to labor, materials, and other expenses. This allows project managers to monitor expenses, track the budget, and take necessary measures to keep the project financially viable.
- Quality Assurance: Work orders establish the quality standards and expectations for each task. They ensure that the construction team is aware of the desired outcomes and the level of quality expected. By providing clear guidelines, work orders promote quality assurance, helping to deliver projects that meet or exceed client expectations.
In summary, work orders are essential in construction projects as they provide clarity, facilitate communication and coordination, enable documentation and record-keeping, support resource allocation and planning, aid in cost control and budget management, and ensure quality assurance. Their importance lies in their ability to streamline operations, reduce errors and conflicts, and contribute to the successful completion of construction projects.
Read more: What Is A Change Order In Construction
Types of Work Orders in Construction
In construction projects, various types of work orders are utilized to categorize and manage different types of tasks. Let’s explore some common types of work orders:
- Maintenance Work Orders: Maintenance work orders are created to address ongoing maintenance and repair tasks on a construction site or within a completed structure. These orders can include tasks such as fixing plumbing issues, repairing electrical systems, or replacing damaged fixtures.
- Change Order Work Orders: Change order work orders are generated when there are modifications or changes to the original project scope. These orders document the changes requested by the client or identified during the construction process, indicating the revised tasks, timelines, budgets, and any other relevant details.
- Repair Work Orders: Repair work orders are issued specifically for addressing damage, defects, or issues identified during or post-construction. These orders outline the repairs needed, allocate resources, and ensure that the necessary repairs are executed promptly to maintain the integrity and safety of the structure.
- Installation Work Orders: Installation work orders are created for the installation of specific components, systems, or equipment in a construction project. These orders outline the installation requirements and instructions, ensuring that the installation process is carried out accurately and according to industry standards.
- Inspection Work Orders: Inspection work orders are generated to schedule inspections and quality checks throughout the construction process. These orders specify the areas to be inspected, the required documentation, and any corrective actions needed based on the inspection findings.
- Project Closeout Work Orders: Project closeout work orders are created towards the end of a construction project to ensure that all final tasks, such as documentation, warranty information, and final inspections, are completed. These orders help in the smooth transition from construction to the project’s completion stage.
- Emergency Work Orders: In case of unforeseen circumstances or emergencies, such as fire, flooding, or structural damages, emergency work orders are generated to address the immediate needs and ensure the safety and stability of the construction site or structure.
These are just a few examples of the types of work orders that can exist in construction projects. The specific types of work orders utilized may vary depending on the project, its complexity, and the specific requirements and circumstances.
By categorizing tasks into different types of work orders, construction professionals can effectively manage and track the various aspects of the project, ensuring that all necessary work is performed, documented, and aligned with the project’s objectives.
A work order in construction is a document that details the specific tasks, materials, and timeline for a project. It is essential for tracking and managing the work being done on a construction site.
Process of Creating and Managing Work Orders
The process of creating and managing work orders in construction involves several crucial steps to ensure effective communication, coordination, and execution of tasks. Let’s explore the general process of creating and managing work orders:
- Identification of Work: The first step is to identify the work that needs to be done. This can involve assessing project requirements, conducting inspections, and consulting with relevant stakeholders to determine the scope of work for each task.
- Task Description and Planning: Once the work is identified, detailed task descriptions are created. This includes specifying the objectives, requirements, timelines, and any special instructions or considerations for each task. Project managers work closely with the team to plan and allocate resources accordingly.
- Work Order Generation: Using a standardized format or digital system, a work order is generated for each task. The work order includes essential information such as the project details, task descriptions, materials needed, budget allocation, and any other relevant instructions or specifications.
- Review and Approval: The work order is then reviewed by relevant parties, including project managers, clients, and contractors, to ensure accuracy, feasibility, and alignment with project goals. Any required modifications or clarifications are addressed, and once approved, the work order moves to the implementation phase.
- Assignment of Responsibilities: The implementation phase involves assigning responsibilities to the appropriate team members. Each team member is made aware of their specific tasks and provided with the necessary information, resources, and access to the work order documentation.
- Execution and Progress Tracking: The assigned tasks are executed according to the work order specifications. Project managers track the progress of each task, ensuring that they are completed within the allocated timelines and meet the required quality standards. They may conduct regular site visits, inspections, or meetings to monitor progress and address any issues or delays.
- Documentation and Record-Keeping: Throughout the process, documentation and record-keeping play a crucial role. Project managers and team members document all relevant information, such as materials used, labor hours, and any changes or deviations from the original work order. This documentation helps maintain a comprehensive project record and supports future reference and analysis.
- Closure and Evaluation: Once the task is completed, the work order is closed, and a final evaluation is conducted. This involves assessing the outcomes, comparing the actual results with the planned goals, and identifying any lessons learned or areas for improvement. This feedback is invaluable for future projects and continuous process improvement.
By following a systematic process, construction professionals can effectively create and manage work orders, ensuring that tasks are executed successfully, projects stay on track, and stakeholders are informed and satisfied with the progress and outcomes.
Benefits of Proper Work Order Management in Construction
Proper work order management is essential in construction projects as it brings numerous benefits that contribute to the successful execution and completion of tasks. Let’s explore the key benefits of proper work order management in construction:
- Improved Efficiency: Proper work order management streamlines the workflow and ensures that tasks are executed in a structured and organized manner. It eliminates confusion, reduces delays, and improves overall project efficiency by providing clear instructions and timelines for each task.
- Better Communication: Work order management facilitates effective communication among project stakeholders. It ensures that everyone involved understands the expectations, responsibilities, and requirements associated with each task. This promotes collaboration, minimizes misunderstandings, and enhances teamwork.
- Enhanced Project Planning: With proper work order management, project managers can accurately plan and schedule tasks based on the work orders. They can allocate resources, estimate timelines, and identify potential bottlenecks or conflicts. This allows for proactive project planning and effective resource management.
- Increased Transparency: Work order management provides transparency by documenting all relevant information about tasks and their progress. This transparency ensures that stakeholders have access to real-time updates and can monitor the project’s progress. It promotes accountability and builds trust among project team members and clients.
- Better Cost Control: Efficient work order management allows project managers to track and manage costs effectively. Work orders provide detailed information about the required materials, labor, and equipment for each task. This helps in controlling expenses, avoiding cost overruns, and ensuring that the project remains within the defined budget.
- Improved Quality Control: Work orders outline quality standards and expectations for each task. By closely following the work order instructions, the construction team can ensure that work is completed to the desired quality level. This leads to improved quality control and client satisfaction.
- Effective Change Management: Proper work order management enables efficient handling of changes or modifications in a project. By issuing change order work orders, project managers can document and communicate changes effectively, ensuring that all parties are aware of the revised scope, timelines, and budgets.
- Documentation and Compliance: Work order management facilitates proper documentation and record-keeping throughout the project. Work orders serve as a comprehensive repository of information, including task descriptions, approvals, financial details, and changes. This documentation aids in compliance with regulations, audits, and legal requirements.
In summary, proper work order management in construction offers several benefits, including improved efficiency, better communication, enhanced project planning, increased transparency, better cost control, improved quality control, effective change management, and proper documentation. These benefits contribute to the success of construction projects by enabling effective coordination, minimizing errors, and ensuring that tasks are completed on time and within budget.
Challenges in Work Order Management in Construction
While work order management is vital for effective construction project execution, it comes with its own set of challenges. Let’s explore some common challenges in work order management in construction:
- Lack of Standardization: One major challenge in work order management is the lack of standardized processes and formats across construction projects and organizations. This can lead to inconsistencies, confusion, and difficulties in efficiently managing and tracking work orders. Establishing standardized practices can help overcome this challenge.
- Poor Communication: Communication breakdowns can occur between project stakeholders, leading to delays, misunderstandings, and errors in work orders. Insufficiently defined or unclear task descriptions and instructions can hinder proper execution. Regular and effective communication is crucial in overcoming these challenges.
- Scope Creep: Scope creep refers to uncontrolled changes or additions to the project scope, which can result in work orders becoming outdated or inaccurate. Managing scope changes effectively and implementing proper change management processes can help mitigate this challenge.
- Resource Constraints: Limited availability of resources, such as materials, equipment, or skilled labor, can pose challenges in work order management. Insufficient resources can lead to delays, cost overruns, and compromising on the quality of work. Proper resource planning and coordination can help alleviate this challenge.
- Incomplete or Inaccurate Information: Inadequate or incorrect information in work orders can lead to misunderstandings, delays, and errors in task execution. Missing crucial details, such as specifications, drawings, or measurements, can hamper the effectiveness of work order management. Thoroughly reviewing work orders for completeness and accuracy is essential.
- Change Management: Managing changes to work orders, including scope changes or client requests, can be challenging. Ensuring that proper change management processes are in place, including documentation, approvals, and communication, is crucial to effectively handle changes without disrupting project progress.
- Technology and Systems: Implementing and utilizing suitable technology or systems for work order management can be a challenge. Lack of appropriate software or tools to create, track, and update work orders can hinder efficiency and lead to data inaccuracies. Investing in modern construction management solutions can help address this challenge.
- Time Constraints: Construction projects often have tight schedules, making it challenging to manage and execute work orders within strict timelines. Proper planning, realistic scheduling, and efficient project management practices are essential to ensure work orders are completed on time.
Overcoming these challenges requires proactive measures, effective communication, standardized processes, and adherence to industry best practices. By addressing these challenges, construction professionals can enhance work order management practices, leading to smoother project execution and successful completion.
Best Practices for Effective Work Order Management
Implementing best practices for work order management in construction projects is crucial for streamlining operations, improving communication, and ensuring successful project execution. Here are some key best practices to consider:
- Standardize Work Order Processes: Establish standardized processes and templates for work order creation, review, approval, and closure. This ensures consistency and efficiency in managing work orders across projects, reduces errors, and facilitates smoother communication between project stakeholders.
- Clearly Define Task Descriptions and Requirements: Ensure that work orders contain clear, concise, and detailed task descriptions. Specify requirements, expectations, and any special instructions to eliminate ambiguity and ensure everyone understands the scope of work involved.
- Implement Centralized Work Order Management: Utilize a centralized management system or software for work orders. This allows for easy access, tracking, and update of work orders by all relevant parties involved. A digital system improves efficiency, reduces paperwork, enhances collaboration, and provides real-time visibility into work order status.
- Establish Effective Communication Channels: Maintain open and effective communication channels among project stakeholders. Clearly communicate work order details, changes, and updates to ensure smooth execution. Regular meetings, progress reports, and collaboration platforms can facilitate effective communication and keep everyone informed.
- Streamline Change Management Processes: Develop a robust change management process to handle scope changes. Clearly define the procedure for initiating, reviewing, and approving change order work orders. Ensure all changes are documented, communicated, and properly accounted for to avoid misunderstandings or scope creep.
- Integrate Work Order Management with Scheduling: Integrate work order management with project scheduling to align tasks, timelines, and resource allocation. This ensures that work orders are aligned with the overall project schedule, preventing conflicts, delays, and resource constraints.
- Promote Training and Education: Provide training and education to project team members on work order management processes and systems. Ensure that everyone understands their roles, responsibilities, and how to effectively use the work order management tools and software.
- Encourage Documentation and Record-Keeping: Promote proper documentation and record-keeping of work orders, including any changes, materials used, labor hours, and other relevant information. Maintain a centralized repository of work order documentation for future reference, audits, and compliance purposes.
- Regular Monitoring and Evaluation: Continuously monitor and evaluate work order management processes. Regularly review the effectiveness of work order execution, identify bottlenecks, and implement necessary improvements. Gather feedback from project team members, stakeholders, and clients to refine work order management practices.
- Embrace Technology and Automation: Leverage technology and automation tools for work order management. Implement construction management software and mobile applications that enable real-time access, updates, and data synchronization. Automation can streamline processes, reduce manual errors, and improve overall efficiency.
By incorporating these best practices into work order management processes, construction professionals can enhance communication, efficiency, and collaboration, ultimately leading to successful project completion and client satisfaction. Regular evaluation and refinement of work order management practices ensure continuous improvement and optimized project management workflows.
Conclusion
In the dynamic world of construction, effective work order management is crucial for successful project execution. Work orders serve as a communication tool, providing clear instructions, timelines, and expectations for each task. They facilitate coordination, resource allocation, and documentation, ensuring that projects stay on track and are completed efficiently.
Throughout this article, we have explored the definition of work orders in construction, their purpose, components, and the importance of proper work order management. We have also discussed the various types of work orders, the process of creating and managing them, as well as the challenges and best practices associated with work order management.
Proper work order management brings numerous benefits to construction projects. It improves efficiency, enhances communication, enables effective project planning, increases transparency, aids in cost control, promotes quality assurance, facilitates change management, and ensures proper documentation and compliance.
However, work order management also comes with its challenges, such as lack of standardization, poor communication, scope creep, resource constraints, incomplete or inaccurate information, change management complexities, technological limitations, and time constraints.
To overcome these challenges, it is essential to implement best practices for work order management. Standardizing processes, clearly defining task descriptions, utilizing centralized management systems, promoting effective communication, streamlining change management, integrating work order management with scheduling, providing training, encouraging documentation, and embracing technology and automation are key practices to consider.
In conclusion, effective work order management is a cornerstone of successful construction projects. By implementing robust processes, leveraging technology, and fostering collaboration, construction professionals can navigate the complexities of work order management, optimize project workflows, and ensure timely, cost-effective, and high-quality project completion. With proper work order management practices in place, construction projects can achieve greater efficiency, transparency, and client satisfaction.
Frequently Asked Questions about What Is A Work Order In Construction
Was this page helpful?
At Storables.com, we guarantee accurate and reliable information. Our content, validated by Expert Board Contributors, is crafted following stringent Editorial Policies. We're committed to providing you with well-researched, expert-backed insights for all your informational needs.
0 thoughts on “What Is A Work Order In Construction”