Home>Furniture & Design>Interior Design Trends>How Window Glass Is Made
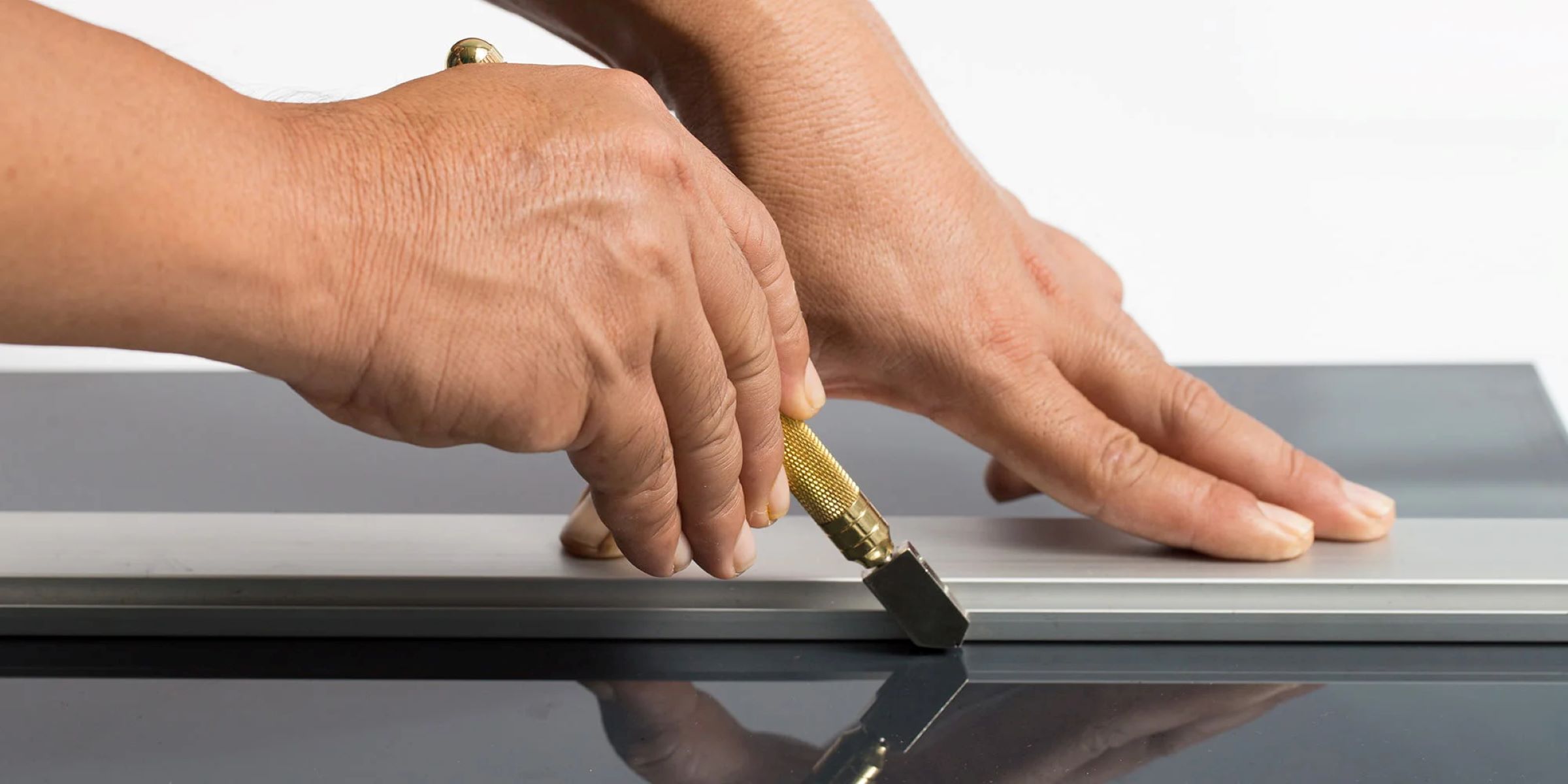
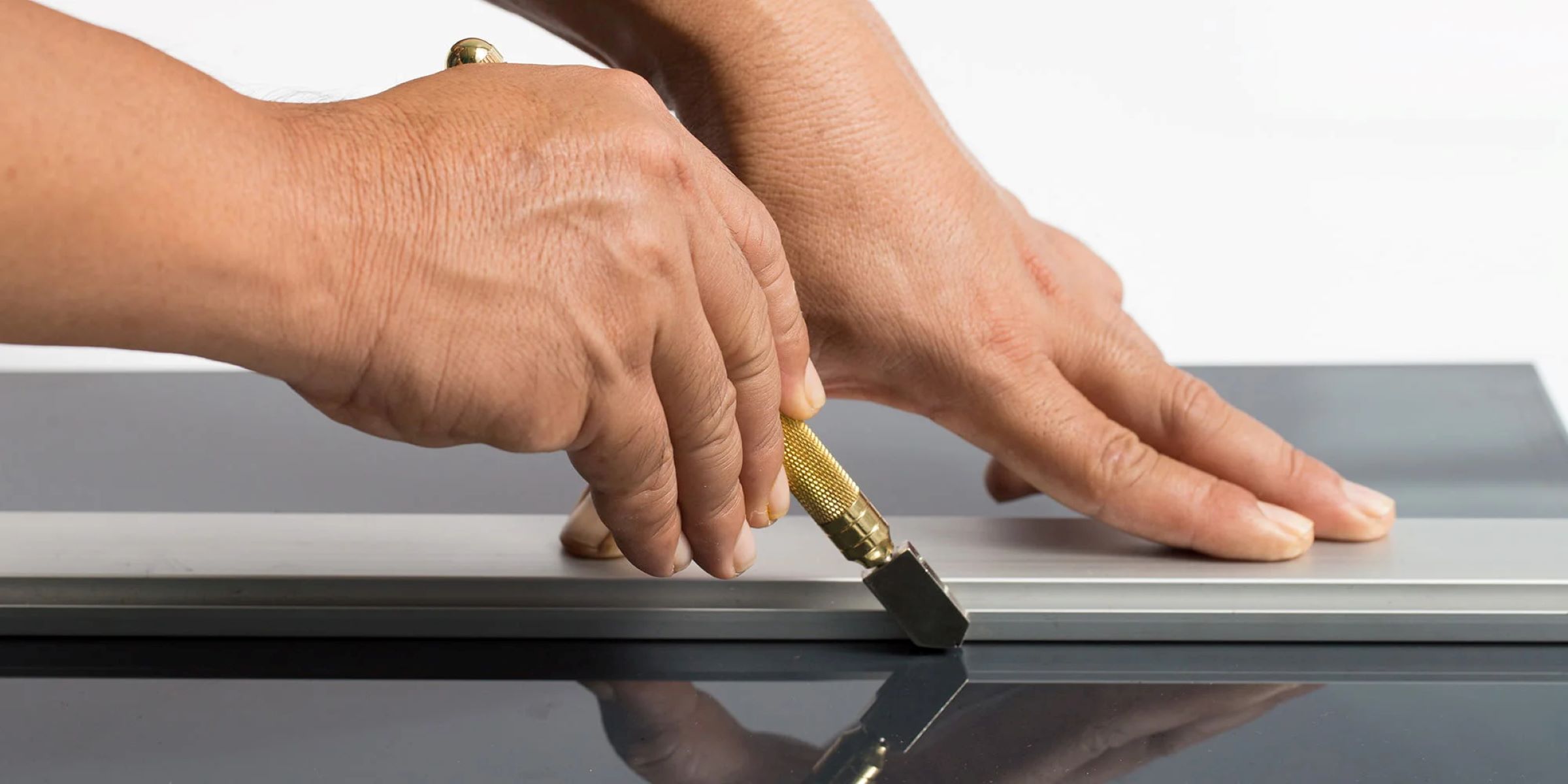
Interior Design Trends
How Window Glass Is Made
Modified: October 18, 2024
Discover the fascinating process of how window glass is made and stay updated on the latest interior design trends. Explore the intricate art of glassmaking and find inspiration for your interior design projects.
(Many of the links in this article redirect to a specific reviewed product. Your purchase of these products through affiliate links helps to generate commission for Storables.com, at no extra cost. Learn more)
Introduction
Window glass is an essential component of modern architecture, providing transparency, insulation, and protection from the elements. The process of creating window glass involves a series of intricate steps that transform raw materials into a versatile and durable material. From the initial sourcing of raw materials to the meticulous quality control measures, each stage plays a crucial role in producing high-quality window glass.
The creation of window glass is a testament to the fusion of science, technology, and craftsmanship. It is a process that has evolved over centuries, with advancements in materials and manufacturing techniques continually shaping the quality and functionality of the final product. Understanding the journey of window glass production unveils the complexity and precision involved in crafting a material that is so ingrained in our daily lives.
As we delve into the intricacies of how window glass is made, we will explore the raw materials that form its foundation, the transformative processes of melting and refining, the shaping and strengthening through forming and annealing, the enhancement of performance through coating and insulating, and the rigorous measures of quality control that ensure the reliability and longevity of the end product. Each stage in the production of window glass contributes to its ability to provide natural light, thermal insulation, and aesthetic appeal to buildings and homes.
The journey of window glass production is a fascinating blend of art and science, where the interplay of heat, chemistry, and craftsmanship converges to create a material that is both functional and visually captivating. By unraveling the intricacies of this process, we gain a deeper appreciation for the window glass that surrounds us, shaping our living and working spaces while seamlessly integrating with the architectural landscape.
Key Takeaways:
- Window glass production involves a fascinating journey from raw materials to quality control, blending art, science, and precision engineering to create a material that shapes our architectural landscape.
- The fusion of silica sand, soda ash, limestone, and cullet forms the foundation for the versatile and indispensable window glass, showcasing the precision and finesse of glassmakers.
Read more: How Are Stained Glass Windows Made
Raw Materials
The production of window glass begins with the careful selection of raw materials, each playing a pivotal role in determining the characteristics and quality of the final product. The primary components of window glass include silica sand, soda ash, limestone, and cullet, which is recycled glass. These raw materials form the foundation of the glass composition, contributing to its transparency, strength, and thermal properties.
Silica sand, also known as silicon dioxide, serves as the primary ingredient in glass manufacturing, comprising approximately 70-75% of the glass batch. Its high purity and uniform particle size are essential for achieving clarity and consistency in the glass. Soda ash, or sodium carbonate, acts as a flux, lowering the melting point of the silica to facilitate the glass-forming process. Limestone, rich in calcium carbonate, aids in stabilizing the chemical composition of the glass, enhancing its durability and resistance to environmental factors.
In addition to these primary components, the inclusion of cullet, or recycled glass, is a sustainable practice that reduces energy consumption and raw material usage. Cullet not only promotes environmental responsibility but also contributes to the overall quality of the glass, as it facilitates the melting process and helps maintain the desired viscosity of the molten glass.
The careful selection and precise combination of these raw materials are fundamental to achieving the desired properties of window glass, such as clarity, strength, and thermal insulation. The meticulous sourcing and processing of these components lay the groundwork for the subsequent stages of glass production, ensuring that the final product meets the stringent standards of modern architecture and design.
The harmonious fusion of silica sand, soda ash, limestone, and cullet sets the stage for the transformative journey of these raw materials into the versatile and indispensable material that adorns our buildings and homes. As we transition from the sourcing of raw materials to the intricate processes of melting, shaping, and refining, the inherent qualities of these components will continue to shape the evolution of window glass, embodying both tradition and innovation in its composition and performance.
Melting and Refining
The journey of window glass production reaches a pivotal stage with the process of melting and refining, where the raw materials undergo a remarkable transformation through the application of intense heat and meticulous control. This stage serves as the crucible of creativity and precision, where the alchemy of raw materials gives rise to the molten glass, laying the foundation for its inherent strength, clarity, and versatility.
The raw materials, carefully selected and proportioned, are introduced into a furnace, typically a continuous tank furnace, where they are subjected to temperatures exceeding 1700°C (3092°F). The intense heat causes the raw materials to undergo a series of complex chemical reactions, culminating in the formation of a viscous, molten mass known as glass. This molten glass possesses remarkable fluidity, allowing it to be shaped and manipulated into various forms that serve as the building blocks for windows, doors, and architectural facades.
The process of refining the molten glass is equally crucial, as it involves the removal of any impurities that may compromise the integrity and visual appeal of the final product. This is achieved through the meticulous control of temperature and the addition of refining agents, such as oxygen and hydrogen, which help eliminate bubbles and other imperfections within the glass. The refining stage is a testament to the precision and expertise of glassmakers, who skillfully navigate the nuances of temperature and composition to ensure the purity and homogeneity of the molten glass.
As the raw materials yield to the transformative power of heat, the molten glass becomes a canvas for creativity and functionality, embodying the potential to illuminate spaces, provide insulation, and enhance the aesthetic appeal of architectural designs. The fusion of silica, soda ash, limestone, and cullet gives rise to a material that embodies both strength and transparency, a testament to the harmonious interplay of science and art in the realm of glass production.
The stage of melting and refining stands as a testament to the ingenuity and precision that define the art of glassmaking. It is a stage where the raw materials transcend their inherent properties, emerging as a molten symphony of form and function. From this molten crucible, the journey of window glass production continues, as the molten glass is shaped, strengthened, and refined to meet the exacting standards of modern architecture and design.
Forming and Annealing
Following the transformative stage of melting and refining, the molten glass enters a realm of precision and finesse as it undergoes the processes of forming and annealing. This pivotal stage in the production of window glass is where the molten glass is shaped into its desired form and then carefully strengthened to ensure its structural integrity and resilience.
The process of forming the molten glass into flat sheets, the most common form of window glass, involves the use of a continuous ribbon process or the float glass method. In the continuous ribbon process, the molten glass is poured onto a shallow bath of molten tin, allowing it to spread out and form a continuous ribbon. As the glass cools and solidifies, it is gradually drawn out of the tin bath, resulting in a smooth and uniform sheet of glass. The float glass method, on the other hand, involves floating the molten glass on a bed of molten metal, typically tin, to create a pristine and distortion-free surface. These methods ensure that the glass achieves the desired thickness and surface quality, setting the stage for its subsequent transformation into windows, doors, and architectural elements.
Once the glass has been formed into its desired shape, it undergoes the critical process of annealing, which involves controlled cooling to relieve internal stresses and enhance its strength and durability. The annealing process is meticulously orchestrated to ensure that the glass cools at a uniform rate, allowing its molecular structure to stabilize and minimize the risk of internal strain. This is achieved through carefully calibrated cooling chambers that gradually reduce the temperature of the glass, imparting resilience and toughness to the material.
The combination of forming and annealing represents a harmonious fusion of artistry and engineering, where the molten glass is sculpted into a versatile and resilient material that embodies both functionality and aesthetic appeal. The precision and expertise required to shape and strengthen the glass during this stage are a testament to the mastery of glassmakers, who navigate the delicate balance of temperature, time, and technique to produce glass of exceptional quality.
As the molten glass transitions through the stages of forming and annealing, it emerges as a material that is not only visually captivating but also structurally robust, capable of withstanding the rigors of architectural applications. The journey of window glass production continues to unfold, as the meticulously formed and annealed glass undergoes further enhancements to optimize its performance and functionality, ensuring that it meets the exacting standards of modern architecture and design.
When making window glass, ensure the raw materials are carefully measured and mixed to create the desired composition for strength and clarity. This will result in high-quality glass for windows.
Coating and Insulating
The stage of coating and insulating represents a pivotal phase in the production of window glass, where the meticulously formed and annealed glass undergoes enhancements to optimize its performance and functionality. This transformative stage adds layers of functionality and efficiency to the glass, ensuring that it meets the stringent demands of modern architecture and design.
Coating plays a crucial role in enhancing the performance of window glass, offering benefits such as solar control, thermal insulation, and self-cleaning properties. One of the most common coating techniques is the application of thin film coatings through a process known as sputter coating. This involves depositing multiple layers of metal oxides, such as titanium dioxide and tin oxide, onto the surface of the glass. These coatings can selectively filter out ultraviolet and infrared radiation, reducing heat gain while allowing visible light to pass through. Additionally, some coatings possess hydrophilic properties, enabling water to spread evenly and wash away dirt and debris, thereby maintaining the glass's clarity and transparency.
Insulating glass units (IGUs) further enhance the thermal performance of window glass by incorporating a space between two or more panes of glass, which is filled with insulating gas, such as argon or krypton. This design minimizes heat transfer, improving energy efficiency and reducing heating and cooling costs. The edges of the glass panes are sealed to create a hermetically sealed unit, preventing moisture ingress and ensuring long-term insulation performance.
The integration of advanced coatings and insulating technologies elevates window glass to a new level of efficiency and sustainability, aligning with the evolving demands of energy-efficient building designs. By harnessing the power of coatings and insulating techniques, window glass not only provides transparency and aesthetics but also contributes to the overall energy performance of buildings, reducing environmental impact and enhancing occupant comfort.
As the glass undergoes the transformative processes of coating and insulating, it evolves into a multifaceted material that embodies both visual appeal and functional excellence. The harmonious fusion of advanced coatings and insulating technologies ensures that window glass meets the diverse needs of modern architecture, offering a balance of aesthetics, energy efficiency, and environmental responsibility.
The journey of window glass production continues to unfold, as the meticulously coated and insulated glass undergoes rigorous quality control measures to ensure its reliability and longevity. From the sourcing of raw materials to the final enhancements of coating and insulating, each stage contributes to the evolution of window glass, shaping the built environment and enriching the lives of those who inhabit it.
Read more: How Is Candy Glass Made
Quality Control
The culmination of the intricate journey of window glass production is marked by the rigorous stage of quality control, where meticulous measures are employed to ensure the reliability, durability, and performance of the final product. This critical phase encompasses a comprehensive array of tests, inspections, and certifications, all aimed at upholding the highest standards of quality and safety in the realm of window glass.
Quality control begins with the careful examination of the raw materials, where stringent quality checks are conducted to verify the purity, consistency, and compatibility of the components. This initial assessment sets the foundation for the subsequent stages of glass production, ensuring that the glass batch meets the precise specifications required for the desired glass composition.
Throughout the stages of melting, refining, forming, and annealing, continuous monitoring and sampling are conducted to assess the chemical composition, homogeneity, and structural integrity of the glass. Advanced analytical techniques, such as spectroscopy and microscopy, are employed to scrutinize the glass at a molecular level, identifying any deviations from the specified parameters and enabling prompt corrective actions.
The optical quality of the glass is also subjected to rigorous scrutiny, with specialized instruments used to evaluate its clarity, flatness, and surface smoothness. Any distortions, blemishes, or imperfections are meticulously identified and addressed to ensure that the glass meets the exacting visual standards demanded by architectural applications.
Furthermore, the performance characteristics of the glass, including its thermal insulation, solar control, and impact resistance, undergo comprehensive testing to validate its compliance with industry standards and regulatory requirements. These assessments serve to ascertain that the glass is capable of withstanding environmental stresses, providing energy efficiency, and ensuring the safety and comfort of building occupants.
The final phase of quality control involves the verification of the glass dimensions, edge quality, and overall conformance to architectural specifications. Each piece of glass is meticulously inspected to guarantee precise dimensions, uniform thickness, and flawless edges, aligning with the exacting requirements of architectural designs.
The culmination of these stringent quality control measures ensures that the window glass produced is not only visually captivating but also structurally robust, energy-efficient, and compliant with industry standards. The unwavering commitment to quality control underscores the dedication of glassmakers to deliver a product that embodies excellence, reliability, and enduring performance.
As the meticulously crafted and quality-assured window glass makes its way into architectural designs and building projects, it serves as a testament to the precision, expertise, and unwavering commitment to quality that define the art of glass production. The journey of window glass production, marked by the fusion of tradition and innovation, culminates in a material that transcends its functional role, shaping the architectural landscape and enriching the lives of those who experience its luminous embrace.
Conclusion
The journey of window glass production is a testament to the fusion of artistry, science, and precision engineering, where raw materials are transformed into a material that transcends its functional role, shaping the architectural landscape and enriching the lives of those who experience its luminous embrace. From the meticulous sourcing of raw materials to the transformative processes of melting, forming, and refining, each stage plays a pivotal role in crafting window glass of exceptional quality and functionality.
The harmonious fusion of silica sand, soda ash, limestone, and cullet sets the stage for the transformative journey of these raw materials into the versatile and indispensable material that adorns our buildings and homes. The alchemy of heat and chemistry during the stage of melting and refining gives rise to the molten glass, laying the foundation for its inherent strength, clarity, and versatility. The subsequent processes of forming and annealing further sculpt the molten glass into a material that embodies both functionality and aesthetic appeal, showcasing the precision and finesse of glassmakers.
The integration of advanced coatings and insulating technologies elevates window glass to a new level of efficiency and sustainability, aligning with the evolving demands of energy-efficient building designs. By harnessing the power of coatings and insulating techniques, window glass not only provides transparency and aesthetics but also contributes to the overall energy performance of buildings, reducing environmental impact and enhancing occupant comfort.
The culmination of the intricate journey of window glass production is marked by the rigorous stage of quality control, where meticulous measures are employed to ensure the reliability, durability, and performance of the final product. The unwavering commitment to quality control underscores the dedication of glassmakers to deliver a product that embodies excellence, reliability, and enduring performance.
As the meticulously crafted and quality-assured window glass makes its way into architectural designs and building projects, it serves as a testament to the precision, expertise, and unwavering commitment to quality that define the art of glass production. The journey of window glass production, marked by the fusion of tradition and innovation, culminates in a material that transcends its functional role, shaping the architectural landscape and enriching the lives of those who experience its luminous embrace.
Frequently Asked Questions about How Window Glass Is Made
Was this page helpful?
At Storables.com, we guarantee accurate and reliable information. Our content, validated by Expert Board Contributors, is crafted following stringent Editorial Policies. We're committed to providing you with well-researched, expert-backed insights for all your informational needs.
0 thoughts on “How Window Glass Is Made”