Home>Home Maintenance>How Much Does It Cost To Renovate An Old Ventilation System
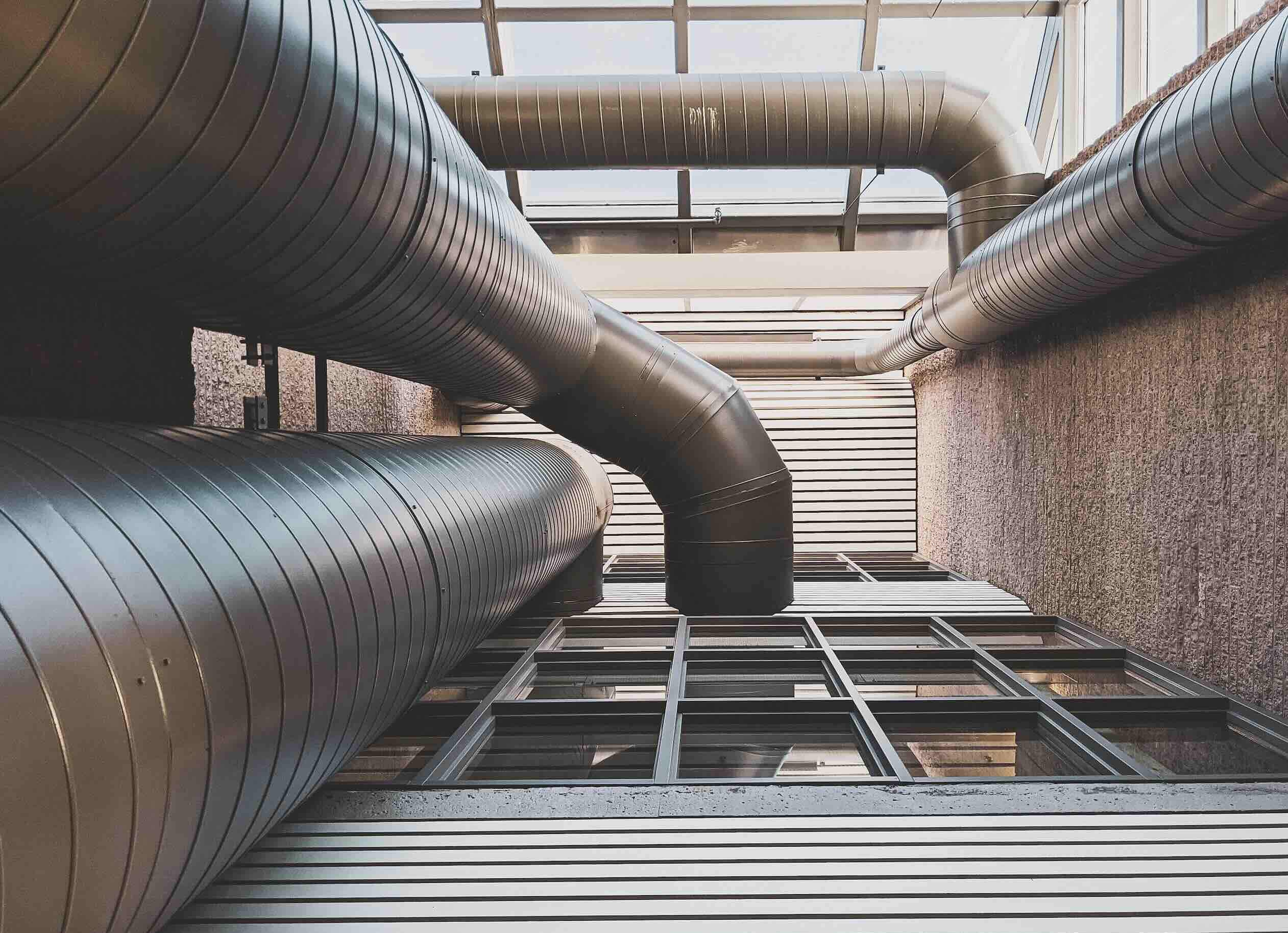
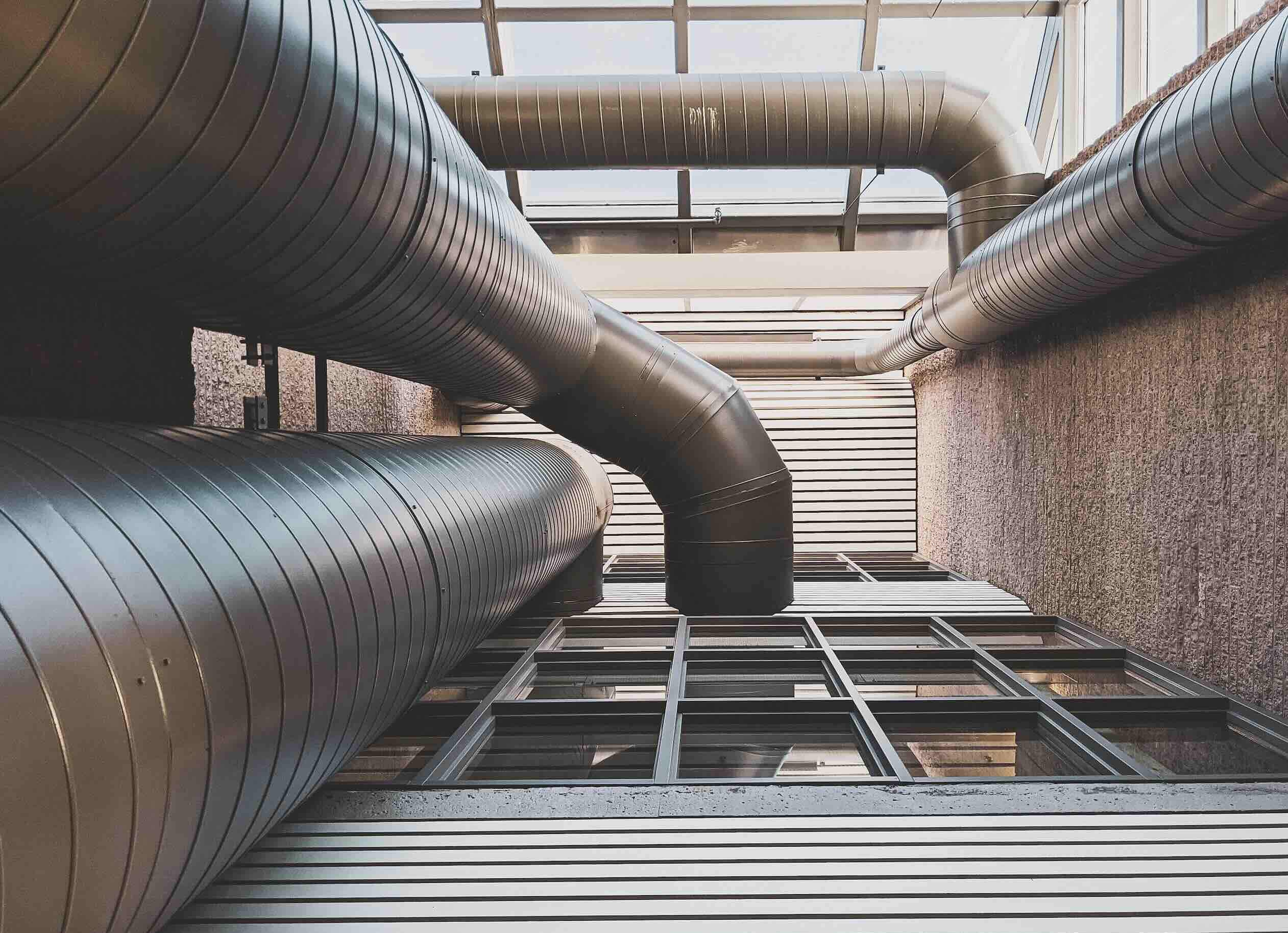
Home Maintenance
How Much Does It Cost To Renovate An Old Ventilation System
Modified: March 6, 2024
Find out the cost of renovating your old ventilation system and improving home maintenance with our comprehensive guide.
(Many of the links in this article redirect to a specific reviewed product. Your purchase of these products through affiliate links helps to generate commission for Storables.com, at no extra cost. Learn more)
Introduction
Maintaining a well-functioning ventilation system is essential for any home. It not only ensures a healthy indoor environment but also helps to regulate temperature and remove stale air. However, over time, ventilation systems may become outdated or inefficient, requiring renovation or replacement. If you are considering renovating an old ventilation system in your home, it’s important to understand the factors that affect the cost of such a project.
Renovating an old ventilation system comes with several benefits. It increases energy efficiency, improves air quality, and enhances comfort. However, it can also be a significant investment, depending on the complexity and condition of the existing system. To help you plan and budget for this project, let’s explore the factors that can influence the cost of renovating an old ventilation system.
Key Takeaways:
- Renovating an old ventilation system can be costly due to factors like system size, age, and accessibility. Thorough assessment and inspection are crucial for accurate cost estimation.
- Upgrading or replacing ductwork and installing new ventilation equipment are essential steps in renovating an old ventilation system, improving airflow, energy efficiency, and indoor air quality.
Read more: How Much Does An HVAC Inspection Cost
Factors Affecting the Cost of Renovating an Old Ventilation System
Renovating an old ventilation system involves various factors that can influence the overall cost of the project. Understanding these factors will help you determine the scope of work required and allocate a realistic budget. Here are the key factors that affect the cost of renovating an old ventilation system:
- Size and Complexity of the System: The size and complexity of the existing ventilation system play a significant role in determining the cost of renovation. Larger systems or those with intricate designs may require more extensive work and materials, resulting in higher costs.
- Age and Condition of the System: The age and condition of the old ventilation system can greatly impact the cost. If the system is severely deteriorated, it may require extensive repairs or even a complete replacement. Older systems may also require modifications to meet current building code standards.
- Accessibility: The ease of access to the existing ventilation system can affect the cost of renovation. If the system is located in hard-to-reach areas such as ceilings, attics, or crawl spaces, additional labor and equipment may be needed, increasing the overall cost.
- Type of Renovation: The nature of the renovation required will also influence the cost. Simple upgrades such as replacing filters and cleaning ducts will be less expensive compared to major modifications that involve replacing ductwork, installing new ventilation equipment, or upgrading electrical systems.
- Energy Efficiency Upgrades: If you wish to improve the energy efficiency of your ventilation system, additional costs may be involved. This can include installing energy-efficient fans, adding insulation to ducts, or upgrading to a programmable thermostat. While these upgrades may initially add to the cost, they can lead to long-term savings in energy bills.
- Local Labor and Material Costs: The cost of renovating an old ventilation system will vary depending on your location. Labor rates, availability of skilled professionals, and material costs can differ from one region to another. It’s essential to research and obtain quotes from local contractors to get an accurate estimate of the expenses involved.
Keep in mind that these factors are not exhaustive, and the actual cost will depend on your specific circumstances. It’s advisable to consult with experienced HVAC professionals who can assess your ventilation system and provide a detailed cost estimate based on your requirements.
Assessment and Inspection of the Existing Ventilation System
Before embarking on the renovation of an old ventilation system, a thorough assessment and inspection of the existing system is crucial. This step will help you identify any issues, determine the scope of work, and estimate the overall cost of the renovation project accurately. Here’s what is involved in the assessment and inspection process:
1. Visual Inspection: A visual inspection involves examining the visible components of the ventilation system, such as vents, registers, and grilles. This helps to identify signs of damage, deterioration, or blockages. It is essential to check for any signs of leakage, rust, mold growth, or excessive dust accumulation.
2. Duct Inspection: The inspection should also include a thorough examination of the ductwork, which is responsible for transporting air throughout the house. Ductwork should be checked for leaks, insulation condition, and proper sealing. It might be necessary to access hard-to-reach areas such as crawl spaces, attics, or basements to ensure a comprehensive assessment.
3. Airflow Evaluation: Assessing the airflow of the existing system is crucial to determine its efficiency. Airflow measurement techniques, such as a duct traverse or a flow hood, can help determine if the system is delivering adequate air to each room. Insufficient airflow may require modifications to the ductwork or additional equipment to improve performance.
4. Equipment Evaluation: The inspection should also include an evaluation of the ventilation equipment, including fans, filters, and controllers. Determine if the equipment is functioning properly and if there are any signs of wear and tear or outdated technology. In some cases, it may be necessary to replace outdated or malfunctioning equipment with newer, more efficient models.
5. Indoor Air Quality Assessment: Since a ventilation system plays a significant role in maintaining indoor air quality, it’s crucial to assess the air quality within the home. Consider conducting tests for pollutants, allergens, and volatile organic compounds (VOCs) to identify any potential health hazards. If the existing ventilation system is not effectively removing contaminants, it may need to be upgraded or replaced to ensure a healthy living environment.
By thoroughly assessing and inspecting the existing ventilation system, you can identify any shortcomings or issues that need to be addressed during the renovation process. This step will provide valuable insights into the necessary upgrades, repairs, or replacements required, allowing you to make informed decisions and accurately estimate the cost of the renovation project.
Upgrading or Replacing Ductwork
One of the critical components of a ventilation system is the ductwork, which plays a vital role in delivering conditioned air to various rooms in the house. Over time, ductwork can deteriorate, develop leaks, or become outdated, compromising the overall efficiency and effectiveness of the ventilation system. Upgrading or replacing the ductwork is often necessary during the renovation of an old ventilation system. Here’s what you need to know:
1. Assessment of Existing Ductwork: The first step is to assess the condition of the existing ductwork. Hiring a professional to inspect the ducts will help identify any leaks, damage, or inadequate insulation. It’s essential to determine if the existing ductwork is salvageable, or if it needs to be entirely replaced.
2. Ductwork Upgrades: In some cases, upgrading the existing ductwork may be sufficient to improve the system’s performance. This can involve sealing leaks, adding insulation, or resizing the ducts for better airflow. Upgrading the ductwork may also include adding dampers or air-balancing devices to control airflow to different zones within the home.
3. Duct Replacement: If the existing ductwork is in poor condition or if it does not meet current building code standards, complete duct replacement may be necessary. This typically involves removing the old ducts and installing new ones. The cost of duct replacement will depend on factors such as duct material, size, complexity of the layout, and accessibility.
4. Duct Material: The choice of duct material can impact the cost of upgrading or replacing the ductwork. Common types of duct materials include sheet metal, fiberglass, and flexible ducts. Sheet metal ductwork tends to be more durable and long-lasting but may be more expensive than other options. Fiberglass ducts are lightweight and less expensive but may not be as durable. Flexible ducts are easy to install but may have lower airflow efficiency.
5. Professional Installation: Upgrading or replacing ductwork requires the expertise of HVAC professionals. They will accurately size and install the ducts to ensure proper airflow and maximum efficiency. Hiring a licensed contractor will minimize installation errors, reduce the potential for leaks, and ensure compliance with building codes.
6. Balancing the System: After upgrading or replacing the ductwork, it is essential to balance the airflow throughout the house. This involves adjusting the dampers or installing dampers in the ductwork to control the amount of air flow to different rooms. Proper airflow balancing ensures that each room receives the necessary amount of conditioned air, improving comfort and energy efficiency.
Upgrading or replacing the ductwork is a crucial step in renovating an old ventilation system. It helps to improve airflow, reduce energy waste, and enhance comfort in the home. While it may involve a significant investment, it is a long-term solution that can maximize the effectiveness of the ventilation system and improve the overall indoor air quality.
Installation of New Ventilation Equipment
As part of renovating an old ventilation system, it may be necessary to install new ventilation equipment to improve airflow, energy efficiency, and overall performance. Upgrading the ventilation equipment can have a significant impact on the effectiveness of the system and the comfort of your home. Here are the key considerations when installing new ventilation equipment:
1. Type of Ventilation Equipment: There are various types of ventilation equipment available, including exhaust fans, supply fans, air exchangers, and heat recovery ventilators (HRVs). The type of equipment you need will depend on your specific requirements and the design of your home. Consult with an HVAC professional to determine the most suitable equipment for your renovation project.
2. Sizing and Capacity: Properly sizing the ventilation equipment is crucial for optimal performance. Oversized equipment can lead to excessive energy consumption, while undersized equipment may not adequately ventilate the space. HVAC professionals will assess factors such as the square footage, occupancy, and desired airflow rates to determine the appropriate capacity for the new equipment.
3. Energy Efficiency: When selecting new ventilation equipment, consider models that offer high energy efficiency. Look for equipment that is ENERGY STAR certified, as these typically consume less energy and can help reduce utility costs. Energy-efficient equipment often features advanced technologies, such as variable speed motors and programmable controls, which allow for more precise control and optimization of ventilation.
4. Installation Considerations: Installing new ventilation equipment may require modifications to the existing ductwork, electrical connections, and controls. It’s crucial to hire a qualified HVAC contractor who can ensure proper installation, including electrical wiring, venting, and connection to the existing system. Improper installation can lead to reduced efficiency, increased energy consumption, and potential safety hazards.
5. Control Options: New ventilation equipment often comes with advanced control options that allow for customized ventilation settings. These controls can include timers, humidity sensors, and CO2 sensors. Consider incorporating these features to optimize comfort and energy efficiency by automatically adjusting the ventilation rates based on occupancy and air quality.
6. Maintenance Requirements: It’s important to understand the maintenance requirements of the new ventilation equipment. Regular cleaning, filter replacement, and system inspections are essential to ensure proper operation and longevity of the equipment. Be sure to follow the manufacturer’s guidelines and consider scheduling regular maintenance with qualified technicians.
Installing new ventilation equipment as part of renovating an old ventilation system can significantly improve air quality, energy efficiency, and overall comfort in your home. Consult with HVAC professionals to determine the most suitable equipment, ensure proper sizing and installation, and take advantage of the latest advancements in ventilation technology.
Before renovating an old ventilation system, get a professional assessment to determine the extent of the work needed. This will help you budget more accurately.
Read more: How Much Does HVAC Ductwork Cost
Electrical Upgrades
Renovating an old ventilation system may require electrical upgrades to support the new equipment and ensure safe and efficient operation. Electrical upgrades are an important aspect of the renovation process and should be done by a qualified electrician. Here are the key considerations for electrical upgrades in a ventilation system renovation:
1. Evaluating Existing Electrical System: Before making any upgrades, it is essential to assess the existing electrical system. Determine if it has the capacity to handle the additional electrical load of the new ventilation equipment. Older homes may have outdated wiring or insufficient circuits, which may need to be upgraded to meet the electrical demands of the renovation project.
2. Additional Circuits and Outlets: Installing new ventilation equipment may require dedicated electrical circuits to ensure proper operation. Consult with an electrician to determine if additional circuits or outlets need to be installed. This will prevent overloading the system and reduce the risk of tripped breakers or electrical hazards.
3. Upgrading Wiring: In some cases, upgrading the electrical wiring in the home may be necessary, especially if the existing wiring is outdated or not up to code. Upgrading the wiring will ensure the safe and efficient operation of the ventilation system. It may also be an opportunity to improve the electrical system as a whole by replacing old knob-and-tube wiring or aluminum wiring with modern copper wiring.
4. Grounding and Surge Protection: Incorporating grounding and surge protection measures is important for the safety and longevity of the ventilation system and other electrical equipment in the home. Grounding ensures that electrical current is directed safely to the ground in the event of a fault, while surge protection safeguards against voltage spikes. These upgrades help protect the ventilation system from electrical damage and reduce the risk of electrical hazards.
5. Installation of Switches and Controls: The installation of new ventilation equipment may require the addition of switches, controls, or thermostats. These components allow for convenient operation and adjustment of the ventilation system. It’s important to plan the location of switches and controls strategically for easy access and optimal functionality.
6. Compliance with Electrical Codes: Upgrading the electrical system in a renovation project must comply with local electrical codes. Hiring a licensed electrician will ensure that the work meets the necessary safety standards and passes relevant inspections. Compliance with electrical codes is crucial for the safety of your home and its occupants.
Electrical upgrades are an integral part of renovating an old ventilation system. Proper planning, evaluation of the existing electrical system, and working with a qualified electrician will ensure that the ventilation equipment operates safely and efficiently. Prioritizing electrical upgrades will provide peace of mind and ensure a successful renovation project.
Additional Costs for Retrofitting in Older Buildings
When renovating an old ventilation system in an older building, there are additional costs to consider due to the unique challenges that these structures present. Retrofitting an older building requires careful planning and specialized knowledge to ensure that the ventilation system meets modern standards and functions optimally. Here are some of the additional costs commonly associated with retrofitting old ventilation systems in older buildings:
1. Structural Modifications: Older buildings may have unique architectural features and structural limitations that can impact the installation and modification of the ventilation system. Structural modifications may be required to accommodate new ductwork, equipment, or ventilation paths. These modifications can involve work such as cutting through walls, reinforcing structures, or creating new access points, all of which can add to the overall cost of the renovation project.
2. Architectural Preservation: Retrofitting an old ventilation system in a historic or architecturally significant building requires careful consideration of preserving its original features and aesthetics. The installation of new equipment and ductwork must be done sensitively to maintain the building’s character. This could involve custom fabrication of ductwork, hidden installation techniques, or integrating the ventilation system with existing architectural elements. Preserving the building’s historical integrity may result in additional costs for customized solutions and specialized craftsmanship.
3. Code Compliance and Permitting: Retrofitting an old building with a new ventilation system typically requires compliance with current building codes and obtaining the necessary permits. Older buildings may have different code requirements compared to newer structures, and meeting these requirements may involve additional work and expenses. This can include upgrades to fire-rated ductwork, asbestos removal, or addressing other safety concerns. It is essential to work closely with local building authorities to ensure compliance and secure the required permits.
4. Mechanical System Integration: Retrofitting a ventilation system in an older building may require integration with other mechanical systems, such as heating, cooling, or plumbing. The coordination and integration of these systems can add complexity and cost to the project. Additionally, modifications to these systems may be necessary to ensure compatibility and optimal performance of the entire mechanical system within the building.
5. Unique Ventilation Solutions: Older buildings may have unconventional layouts or design characteristics that require creative ventilation solutions. This can include complex duct routing, custom-designed grilles or vents, or the use of specialty equipment. These unique ventilation solutions often come at a premium cost due to the additional engineering, design, and custom fabrication involved.
Retrofitting an old ventilation system in an older building requires careful planning, coordination, and consideration of the building’s unique characteristics. It is advisable to work with experienced HVAC professionals and contractors who have expertise in retrofitting older buildings. While the additional costs associated with retrofitting older buildings can be significant, they are necessary to ensure the functionality, performance, and preservation of the building while providing a modern and efficient ventilation system.
Maintenance and Operational Costs
Once you have renovated an old ventilation system, it’s crucial to consider the ongoing maintenance and operational costs associated with keeping it running smoothly. Proper maintenance ensures that the system remains efficient, extends its lifespan, and maintains a healthy indoor environment. Here are some key factors to consider when budgeting for maintenance and operational costs:
1. Regular Maintenance: Regular maintenance is essential for the proper functioning of a ventilation system. This can include tasks such as cleaning or replacing filters, inspecting and cleaning ductwork, lubricating fan motors, and checking electrical connections. It is recommended to schedule professional maintenance at least once a year to ensure the system operates optimally and minimize the risk of breakdowns.
2. Filter Replacement: Filters play a crucial role in capturing dust, allergens, and other airborne particles, helping to maintain good indoor air quality. Depending on the type of filter used, they will need to be replaced on a regular basis. The frequency of filter replacement depends on factors such as air quality, system usage, and the type of filter being used. Regularly replacing filters not only improves air quality but also helps maintain the efficiency of the ventilation system.
3. Energy Consumption: It’s important to consider the energy consumption of the renovated ventilation system. High-efficiency equipment and proper system design can help reduce energy consumption. However, it’s important to monitor energy usage and factor in the cost of electricity to operate the system. Using energy-efficient components, such as variable speed motors and programmable controls, can help optimize energy usage and reduce operational costs.
4. Repair and Replacement: Despite regular maintenance, there may be instances where repairs or component replacements are necessary. Components such as fans, motors, or control panels can wear out over time and need to be repaired or replaced. It’s important to budget for potential repair costs and consider the lifespan and warranty of the equipment when making a replacement decision.
5. Indoor Air Quality Testing: Periodic testing of indoor air quality is recommended to ensure that the ventilation system is effectively removing pollutants and maintaining a healthy environment. This can involve testing for mold, allergens, carbon monoxide, or other contaminants. The cost of professional air quality testing and remediation, if necessary, should be factored into maintenance and operational costs.
6. Educating Occupants: Proper usage and maintenance by occupants is also important for the longevity and efficient operation of the ventilation system. Educating occupants on the importance of regular filter changes, minimizing blockages or obstructions, and reporting any issues or concerns can help prevent costly repairs and ensure the system operates optimally.
By considering the ongoing maintenance and operational costs of the renovated ventilation system, you can budget accordingly and ensure the system remains efficient, effective, and maintains good indoor air quality. A well-maintained ventilation system not only enhances the comfort and health of the occupants but also contributes to long-term savings by reducing energy consumption and preventing costly repairs or replacements.
Conclusion
Renovating an old ventilation system is a significant investment that can greatly enhance the comfort, energy efficiency, and indoor air quality of your home. However, it’s essential to consider the various factors that can influence the cost of the renovation project. Factors such as the size and complexity of the system, age and condition, accessibility, and type of renovation can all impact the overall cost.
Assessing and inspecting the existing ventilation system is crucial to identifying any necessary upgrades or repairs. Upgrading or replacing ductwork improves airflow and efficiency, while the installation of new ventilation equipment can enhance performance and energy efficiency. Electrical upgrades may be necessary to support the new system and ensure safe operation.
Renovating an old ventilation system in an older building may come with additional costs due to structural modifications, architectural preservation, and code compliance. It is important to work with experienced professionals who understand the unique challenges of retrofitting older buildings.
Ongoing maintenance and operational costs should also be considered when budgeting for a renovated ventilation system. Regular maintenance, filter replacements, energy consumption, repair and replacement, indoor air quality testing, and educating occupants are all factors to consider to maintain the system’s efficiency and effectiveness.
In conclusion, renovating an old ventilation system requires careful planning, budgeting, and working with knowledgeable professionals. Considering the factors that affect the cost, assessing the existing system, upgrading or replacing ductwork, installing new equipment, addressing electrical needs, and accounting for ongoing maintenance and operational costs will ensure a successful project that improves the overall comfort and air quality of your home for years to come.
Frequently Asked Questions about How Much Does It Cost To Renovate An Old Ventilation System
Was this page helpful?
At Storables.com, we guarantee accurate and reliable information. Our content, validated by Expert Board Contributors, is crafted following stringent Editorial Policies. We're committed to providing you with well-researched, expert-backed insights for all your informational needs.
0 thoughts on “How Much Does It Cost To Renovate An Old Ventilation System”