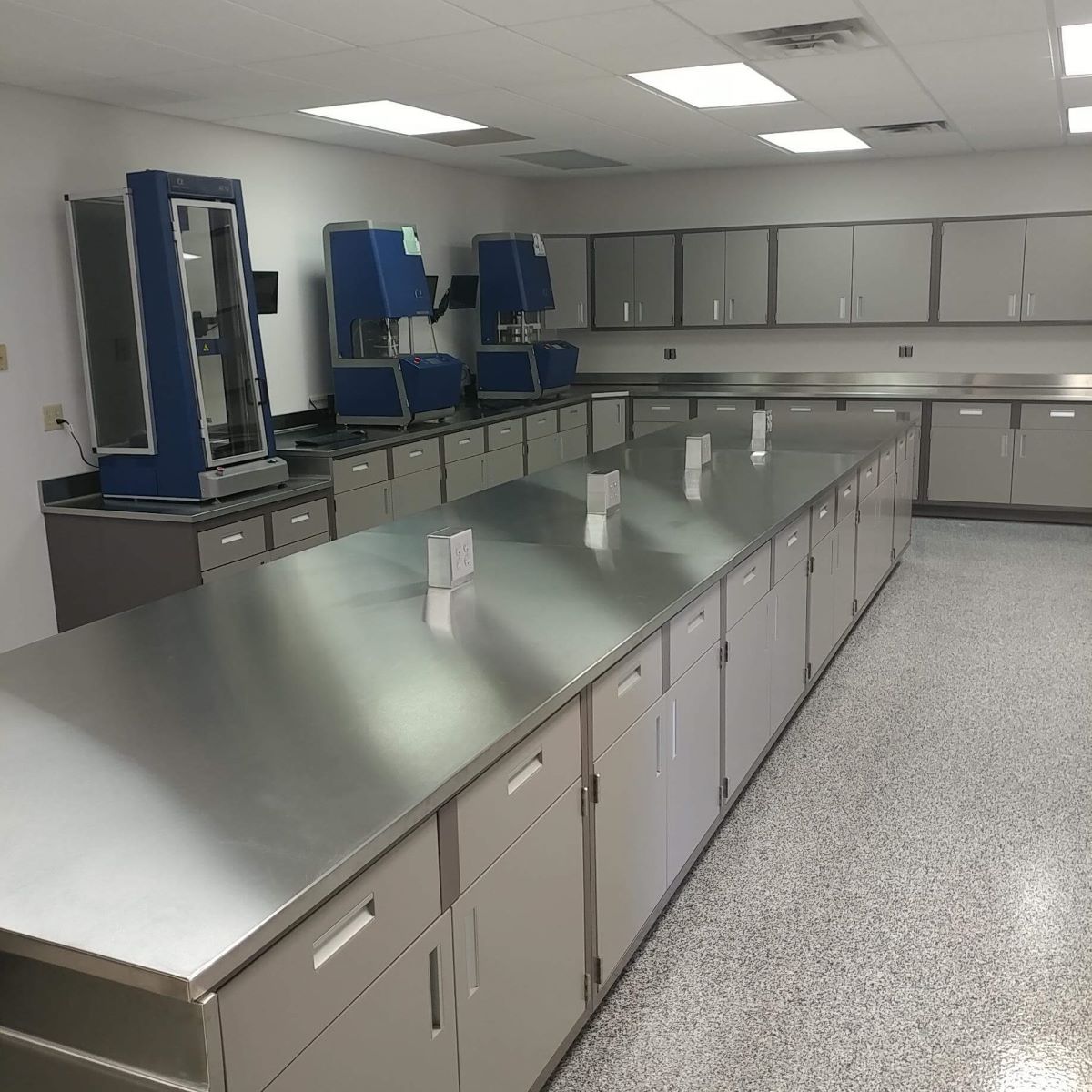
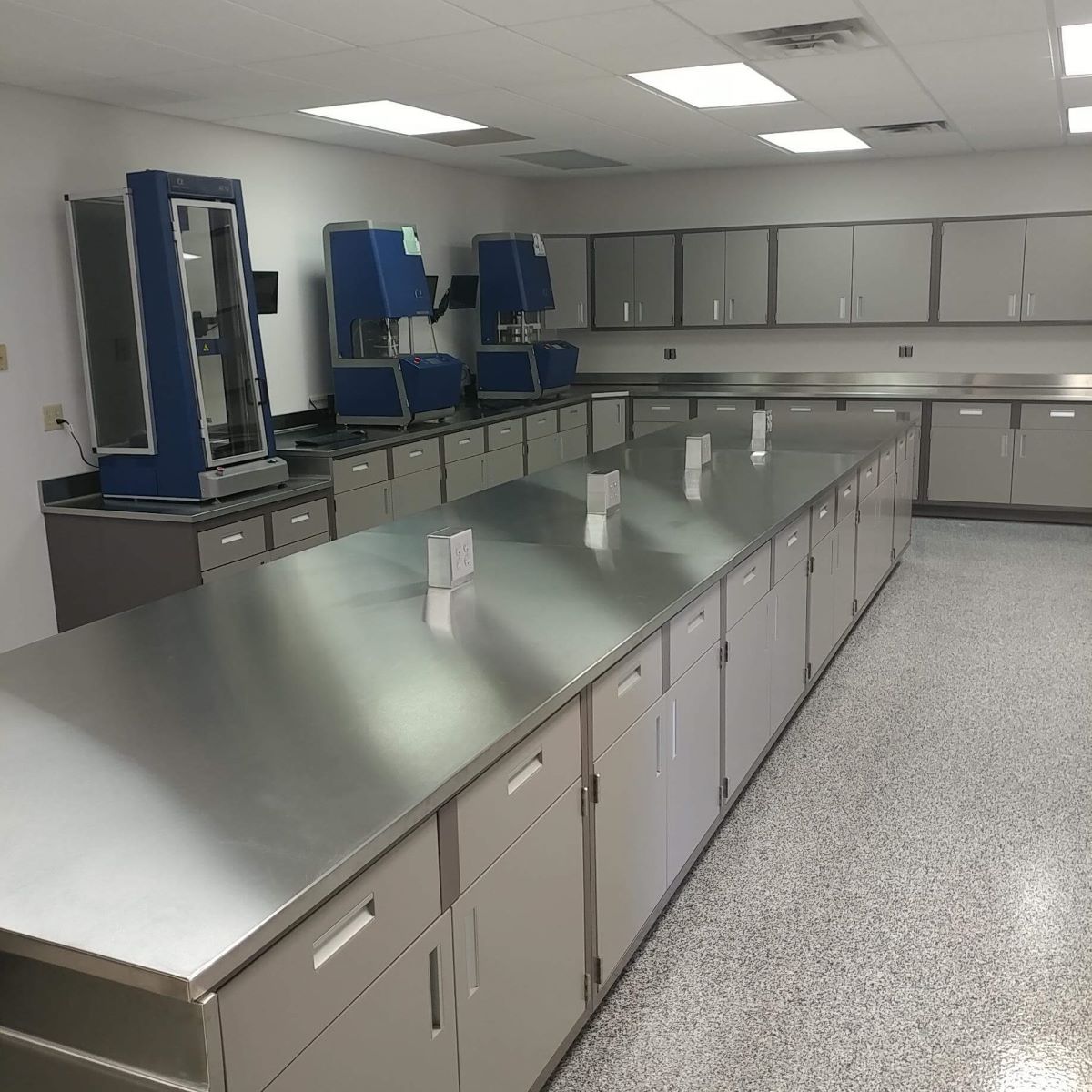
Articles
What Are Lab Countertops Made Of
Modified: January 18, 2024
Discover the different materials used for lab countertops in this informative article. Explore the benefits and drawbacks of each option to make the best choice for your laboratory.
(Many of the links in this article redirect to a specific reviewed product. Your purchase of these products through affiliate links helps to generate commission for Storables.com, at no extra cost. Learn more)
Introduction
Laboratory countertops play a critical role in providing a safe and functional workspace for scientists, researchers, and professionals in various scientific fields. The materials used for lab countertops must be durable, resistant to chemicals and heat, easy to clean, and capable of withstanding rigorous laboratory procedures. There are several common materials used for lab countertops, each with its own unique properties and benefits.
In this article, we will explore the different materials commonly used for lab countertops, including epoxy resin countertops, phenolic resin countertops, stainless steel countertops, granite countertops, and chemical-resistant laminate countertops. We will also discuss the factors to consider when choosing the right countertop material for your lab.
So, if you’re interested in learning more about lab countertops and the materials they are made of, read on!
Key Takeaways:
- Choose the right lab countertop material based on your specific needs, considering factors like chemical resistance, heat resistance, durability, hygiene, aesthetics, maintenance, and budget. Create a safe, functional, and visually appealing workspace for scientific excellence.
- Epoxy resin, phenolic resin, stainless steel, granite, and chemical-resistant laminate are popular lab countertop materials, each with unique properties. Consider their chemical resistance, heat resistance, durability, and maintenance requirements to make an informed decision for your lab.
Read more: What Are Countertops Made Of
Common Materials Used for Lab Countertops
When it comes to lab countertops, there are several materials that are commonly used due to their durability and suitability for laboratory environments. Each material has its own set of advantages and considerations, so let’s take a closer look at them:
- Epoxy Resin Countertops: Epoxy resin countertops are a popular choice for laboratories due to their excellent chemical resistance and durability. They are made by mixing epoxy resin with a filler material such as silica or ceramic to create a solid surface. Epoxy resin countertops are resistant to a wide range of chemicals, including acids, solvents, and bases, making them ideal for chemical laboratories. They are also heat-resistant and easy to clean, making them suitable for rigorous lab procedures.
- Phenolic Resin Countertops: Phenolic resin countertops are another common choice for lab countertops. They are made by impregnating layers of kraft paper with phenolic resin and then compressing them under high heat and pressure. Phenolic resin countertops are highly resistant to chemicals, heat, and impact, making them suitable for both wet and dry lab environments. They are also easy to clean and maintain, making them a practical choice for laboratories.
- Stainless Steel Countertops: Stainless steel countertops are known for their durability, corrosion resistance, and easy maintenance. They are made of a combination of iron, chromium, and other metals, which gives them their unique properties. Stainless steel countertops are ideal for labs that require a sterile and hygienic environment, such as medical and research labs. They are resistant to chemicals, heat, and stains, making them suitable for a variety of lab applications.
- Granite Countertops: Granite countertops are a popular choice for labs that require an aesthetically pleasing and durable surface. They are made from natural stone, which gives them their unique patterns and colors. Granite countertops are heat-resistant, scratch-resistant, and chemically inert, making them suitable for various lab applications. However, it is important to note that granite countertops may require regular sealing to maintain their durability and stain resistance.
- Chemical-Resistant Laminate Countertops: Chemical-resistant laminate countertops are made by bonding layers of kraft paper soaked in phenolic resin with a decorative layer and a clear melamine overlay. These countertops offer excellent resistance to chemicals, stains, and impact, making them ideal for labs that handle corrosive substances. They are also budget-friendly and come in a wide range of colors and designs, allowing for customization to suit different lab settings.
These are the most common materials used for lab countertops. Each material has its own unique set of qualities and considerations, so it’s important to evaluate your specific lab requirements before making a decision. Factors such as chemical resistance, heat resistance, durability, ease of maintenance, and budget should all be taken into account.
In the next section, we will delve deeper into the factors to consider when choosing the right countertop material for your lab.
Epoxy Resin Countertops
Epoxy resin countertops are a popular choice for laboratories due to their exceptional chemical resistance and durability. They are composed of a combination of epoxy resin and a filler material, such as silica or ceramic, which is mixed together to create a solid and seamless surface.
One of the primary advantages of epoxy resin countertops is their resistance to a wide range of chemicals. They can withstand exposure to acids, solvents, and bases, making them suitable for a variety of laboratory applications. This chemical resistance ensures that the countertops remain intact and durable, even when exposed to harsh substances that could damage or degrade other countertop materials.
In addition to chemical resistance, epoxy resin countertops are also highly heat-resistant. They can withstand high temperatures without warping or melting, making them ideal for labs that frequently use hot equipment or perform experiments involving heat. This heat resistance ensures that the countertops can withstand the rigors of laboratory procedures without compromising their structural integrity.
Another benefit of epoxy resin countertops is their ease of cleaning. The smooth and non-porous surface makes it difficult for chemicals, spills, or contaminants to penetrate, allowing for easy cleanup and maintenance. The countertops can be effortlessly wiped down with common laboratory cleaning agents, ensuring a sterile and hygienic workspace.
Additionally, epoxy resin countertops offer excellent durability. They are highly resistant to impact, scratches, and abrasions, ensuring a long lifespan and reducing the need for frequent maintenance or replacement. This durability makes them a cost-effective choice in the long run.
It is important to note that while epoxy resin countertops have impressive chemical resistance, prolonged exposure to certain chemicals, such as strong solvents, can cause discoloration or surface damage. Therefore, it’s essential to follow proper handling and cleaning procedures to maintain the countertop’s longevity.
Overall, epoxy resin countertops are a versatile and reliable option for laboratory settings. Their high chemical resistance, heat resistance, ease of cleaning, and durability make them suitable for a wide range of applications, from academic research labs to pharmaceutical and industrial laboratories. When choosing epoxy resin countertops, it is important to consider the specific needs and requirements of your lab to ensure optimal performance and longevity.
Phenolic Resin Countertops
Phenolic resin countertops are widely used in laboratory settings due to their exceptional chemical resistance, heat resistance, and durability. They are composed of layers of kraft paper impregnated with phenolic resin and then compressed under high heat and pressure to create a solid and sturdy surface.
One of the key advantages of phenolic resin countertops is their excellent chemical resistance. They can withstand exposure to a wide range of chemicals, including acids, solvents, and bases, without sustaining damage or degradation. This chemical resistance ensures that the countertops remain intact and functional even in highly corrosive laboratory environments.
In addition to chemical resistance, phenolic resin countertops are highly heat-resistant. They can withstand high temperatures without warping, melting, or losing their structural integrity. This makes them suitable for labs that regularly work with hot equipment or perform experiments involving elevated temperatures.
Durability is another standout feature of phenolic resin countertops. They are highly resistant to impact, scratches, and abrasions, ensuring a long lifespan even in demanding laboratory environments. This durability reduces the need for frequent maintenance or replacement, making phenolic resin countertops a cost-effective choice in the long run.
Phenolic resin countertops are also known for their ease of cleaning and maintenance. The non-porous surface prevents chemicals, spills, or contaminants from seeping into the material, allowing for easy cleanup using common laboratory cleaning agents. This ensures a hygienic and sterile workspace, minimizing the risk of cross-contamination in the lab.
Furthermore, phenolic resin countertops are available in a range of thicknesses and colors, allowing for customization and flexibility in laboratory design. They can be seamlessly integrated into different lab settings, providing a cohesive and visually appealing workspace.
While phenolic resin countertops offer numerous advantages, it is important to note that they may not be as resistant to certain solvents as other materials like epoxy resin countertops. Prolonged exposure to strong solvents can cause discoloration or surface damage. Therefore, it is essential to follow proper handling and cleaning procedures to maintain the countertops’ longevity.
In summary, phenolic resin countertops are a reliable and versatile option for laboratory settings. Their excellent chemical resistance, heat resistance, durability, and ease of maintenance make them suitable for a wide range of applications. When choosing phenolic resin countertops, consider the specific needs and requirements of your lab to ensure optimal performance and long-lasting functionality.
Stainless Steel Countertops
Stainless steel countertops are highly valued in laboratory settings for their durability, corrosion resistance, and hygienic properties. They are made from a combination of iron, chromium, and other metals, which gives them their unique stainless steel properties.
One of the primary advantages of stainless steel countertops is their exceptional durability. They are resistant to impact, scratches, and dents, making them able to withstand the rigors of daily laboratory activities. This durability ensures that stainless steel countertops have a long lifespan and require minimal maintenance or replacement.
Another standout feature of stainless steel countertops is their excellent corrosion resistance. They are highly resistant to chemical attack, making them ideal for labs that handle corrosive substances. Stainless steel countertops can withstand exposure to acids, solvents, and bases without sustaining damage or degradation, ensuring a safe and functional workspace.
Hygiene is a crucial consideration in laboratory environments, and stainless steel countertops excel in this regard. They have a non-porous surface, preventing the growth of bacteria, fungi, and mold. This makes stainless steel countertops easy to clean and ideal for labs that require a sterile and hygienic working environment, such as medical and research labs.
Stainless steel countertops are also heat-resistant, allowing them to withstand high temperatures without warping or melting. This heat resistance makes them suitable for labs that frequently use hot equipment or conduct experiments involving heat sources.
In addition to their durability and resistance to chemicals and heat, stainless steel countertops have a sleek and professional appearance. They provide a modern and clean aesthetic, making them an attractive choice for laboratory settings.
It is important to note that stainless steel countertops may be prone to scratches and fingerprints, which can affect their appearance. However, these surface imperfections can often be easily buffed out or minimized with proper maintenance and care.
Overall, stainless steel countertops are a reliable and practical option for laboratory environments. Their durability, corrosion resistance, hygienic properties, and heat resistance make them suitable for a wide range of applications. When choosing stainless steel countertops, consider the specific needs and requirements of your lab to ensure optimal performance and longevity.
Lab countertops are commonly made of materials such as epoxy resin, phenolic resin, stainless steel, or chemical-resistant laminate. Each material has its own advantages and is suitable for different types of laboratory work.
Read more: What Is Silestone Countertops Made Of
Granite Countertops
Granite countertops are a popular choice for laboratory environments that require both durability and aesthetics. Made from natural stone, granite countertops offer a unique blend of style and functionality.
One of the key advantages of granite countertops is their exceptional durability. Granite is a hard and dense material, making it highly resistant to impact, scratches, and abrasions. This durability ensures that the countertops can withstand the demands of a laboratory environment and maintain their integrity over time.
In addition to durability, granite countertops are heat-resistant. They can withstand high temperatures without warping or melting, making them suitable for labs that use heat-generating equipment or perform experiments involving heat sources.
Granite countertops are naturally resistant to chemicals, ensuring that they can withstand exposure to various substances that laboratories may encounter. They are less likely to be damaged or discolored by common laboratory chemicals, acids, or solvents. However, it is important to note that certain strong acids or corrosive chemicals may still affect the surface of granite countertops over time if not cleaned promptly.
Besides their functional benefits, granite countertops also offer aesthetic appeal. Each slab of granite is unique, with natural variations in pattern, color, and texture, adding a touch of elegance to the laboratory environment. Granite countertops come in a wide range of colors and finishes, allowing for flexibility in design and customization to suit different lab settings.
However, it is important to note that granite countertops require regular maintenance to keep them in optimal condition. They may need to be sealed periodically to maintain their stain resistance and prevent liquid absorption. Proper cleaning and maintenance instructions should be followed to preserve the longevity and appearance of granite countertops.
Overall, granite countertops provide a balance between functionality and aesthetic appeal in laboratory settings. Their durability, heat resistance, chemical resistance, and natural beauty make them a popular choice for labs that value both performance and style. When considering granite countertops, it’s essential to assess the specific needs and requirements of your lab to ensure the best fit.
Chemical-Resistant Laminate Countertops
Chemical-resistant laminate countertops are a cost-effective and versatile choice for laboratory environments that require durability and resistance to chemical exposure. These countertops are constructed by bonding layers of kraft paper soaked in phenolic resin with a decorative layer and a clear melamine overlay.
One of the primary advantages of chemical-resistant laminate countertops is their exceptional resistance to a wide range of chemicals. They can withstand exposure to acids, solvents, and bases without sustaining damage or degradation, making them suitable for laboratories that handle corrosive substances.
In addition to chemical resistance, laminate countertops are known for their durability. The layers of paper and resin create a solid and sturdy surface that can handle the rigors of daily lab activities. These countertops have excellent impact resistance, making them less susceptible to chipping or cracking compared to other materials.
Chemical-resistant laminate countertops are also easy to clean and maintain. The smooth and non-porous surface resists staining and makes it easy to wipe away spills and contaminants. Routine cleaning with mild detergents is typically sufficient to keep the countertops clean and hygienic, making them suitable for labs that require a low-maintenance solution.
Furthermore, chemical-resistant laminate countertops offer a wide range of design options. They come in various colors, patterns, and finishes, allowing for customization and flexibility in lab design. This enables labs to create a visually appealing workspace that aligns with their specific needs and aesthetic preferences.
It is important to note that chemical-resistant laminate countertops may not provide the same level of heat resistance as other materials such as stainless steel or epoxy resin. Care should be taken to avoid placing hot objects directly on the surface to prevent discoloration or damage.
In summary, chemical-resistant laminate countertops offer a cost-effective and versatile solution for laboratory environments. Their resistance to chemicals, durability, easy maintenance, and design options make them suitable for various lab applications. When considering chemical-resistant laminate countertops, it is important to evaluate the specific needs of your lab to ensure compatibility and longevity.
Factors to Consider when Choosing Lab Countertop Materials
Choosing the right countertop material for your lab is crucial for creating a safe, functional, and efficient workspace. There are several factors to consider when selecting lab countertop materials. Let’s explore some of the key considerations:
1. Chemical Resistance: Lab environments often involve the use of various chemicals, acids, solvents, and bases. It is essential to choose a countertop material that is highly resistant to the specific chemicals used in your lab to ensure long-term durability and safety. Materials such as epoxy resin, phenolic resin, and stainless steel are known for their excellent chemical resistance.
2. Heat Resistance: Labs that frequently work with heat-generating equipment or perform experiments involving high temperatures require countertop materials with good heat resistance. Materials like stainless steel, epoxy resin, and granite are known for their ability to withstand high temperatures without warping or melting.
3. Durability and Impact Resistance: Labs can be high-activity environments where accidental spills, impacts, and heavy equipment are common. Countertop materials with good durability and impact resistance, such as phenolic resin and stainless steel, can withstand these demands and maintain their structural integrity over time.
4. Hygiene and Cleanliness: Maintaining a clean and sterile lab environment is crucial. Countertop materials that have non-porous surfaces, like stainless steel and chemical-resistant laminate, are easier to clean and disinfect, reducing the risk of contamination and promoting a hygienic workspace.
5. Aesthetics: While functionality and performance are paramount, aesthetics should also be considered. Countertop materials like granite and chemical-resistant laminate offer a range of colors, patterns, and finishes, allowing you to create a visually appealing environment that aligns with your lab’s design preferences.
6. Maintenance and Longevity: Consider the level of maintenance required to keep the countertops in optimal condition. Some materials, such as granite, may require regular sealing to maintain stain resistance, while others, like stainless steel, may require periodic polishing to remove scratches. Understanding the maintenance requirements will help you assess the long-term costs and effort involved.
7. Budget: Of course, the budget is an important factor when choosing lab countertop materials. Some materials, such as stainless steel and epoxy resin, may have a higher upfront cost but offer long-term durability and performance, making them a worthwhile investment. Assess your budget and balance it with the desired functionality and durability of the countertop materials.
Considering these factors will help you make an informed decision when choosing the most suitable countertop material for your lab. It’s essential to evaluate your lab’s specific needs, the types of experiments conducted, and the potential hazards encountered to select the material that provides the best combination of performance, safety, and cost-effectiveness.
Conclusion
When it comes to lab countertops, choosing the right material is crucial for creating a safe, functional, and efficient workspace. Each countertop material has its own unique properties and benefits, making it important to carefully consider your lab’s specific needs and requirements.
Epoxy resin countertops are known for their exceptional chemical resistance, heat resistance, and durability, making them ideal for labs that handle a wide range of chemicals. Phenolic resin countertops offer similar qualities but with added impact resistance, making them suitable for labs requiring a sturdy surface. Stainless steel countertops provide excellent durability, corrosion resistance, and hygienic properties, making them a practical choice for sterile lab environments. Granite countertops offer a combination of durability, heat resistance, and aesthetic appeal, adding a touch of elegance to the lab. Chemical-resistant laminate countertops are a cost-effective option with excellent chemical resistance and a wide range of design possibilities.
Factors such as chemical resistance, heat resistance, durability, hygiene, aesthetics, maintenance, and budget should all be carefully considered when choosing the right countertop material for your lab. The specific needs of your lab, the types of experiments conducted, and the potential hazards encountered should guide your decision-making process.
Remember that while durability and functionality are crucial, it’s also important to create an environment that inspires productivity and enhances the overall lab experience. A well-designed lab, with visually appealing countertops, can contribute to the morale and efficiency of the lab team.
In conclusion, the selection of lab countertop materials should be a thoughtful and informed decision. By considering the specific needs of your lab, evaluating the properties of different countertop materials, and striking a balance between functionality and aesthetics, you can create a lab space that promotes safety, productivity, and scientific excellence.
Frequently Asked Questions about What Are Lab Countertops Made Of
Was this page helpful?
At Storables.com, we guarantee accurate and reliable information. Our content, validated by Expert Board Contributors, is crafted following stringent Editorial Policies. We're committed to providing you with well-researched, expert-backed insights for all your informational needs.
0 thoughts on “What Are Lab Countertops Made Of”