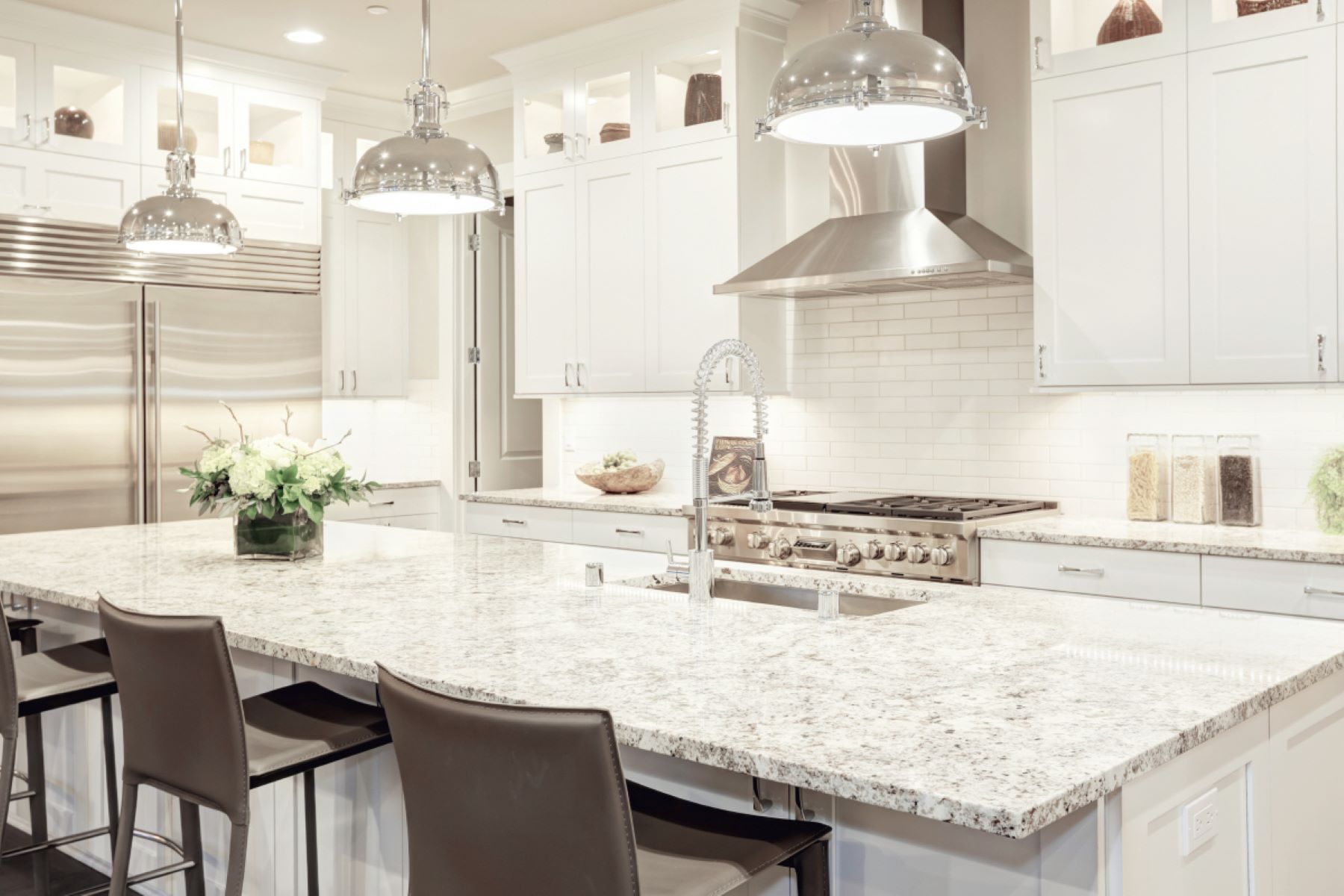
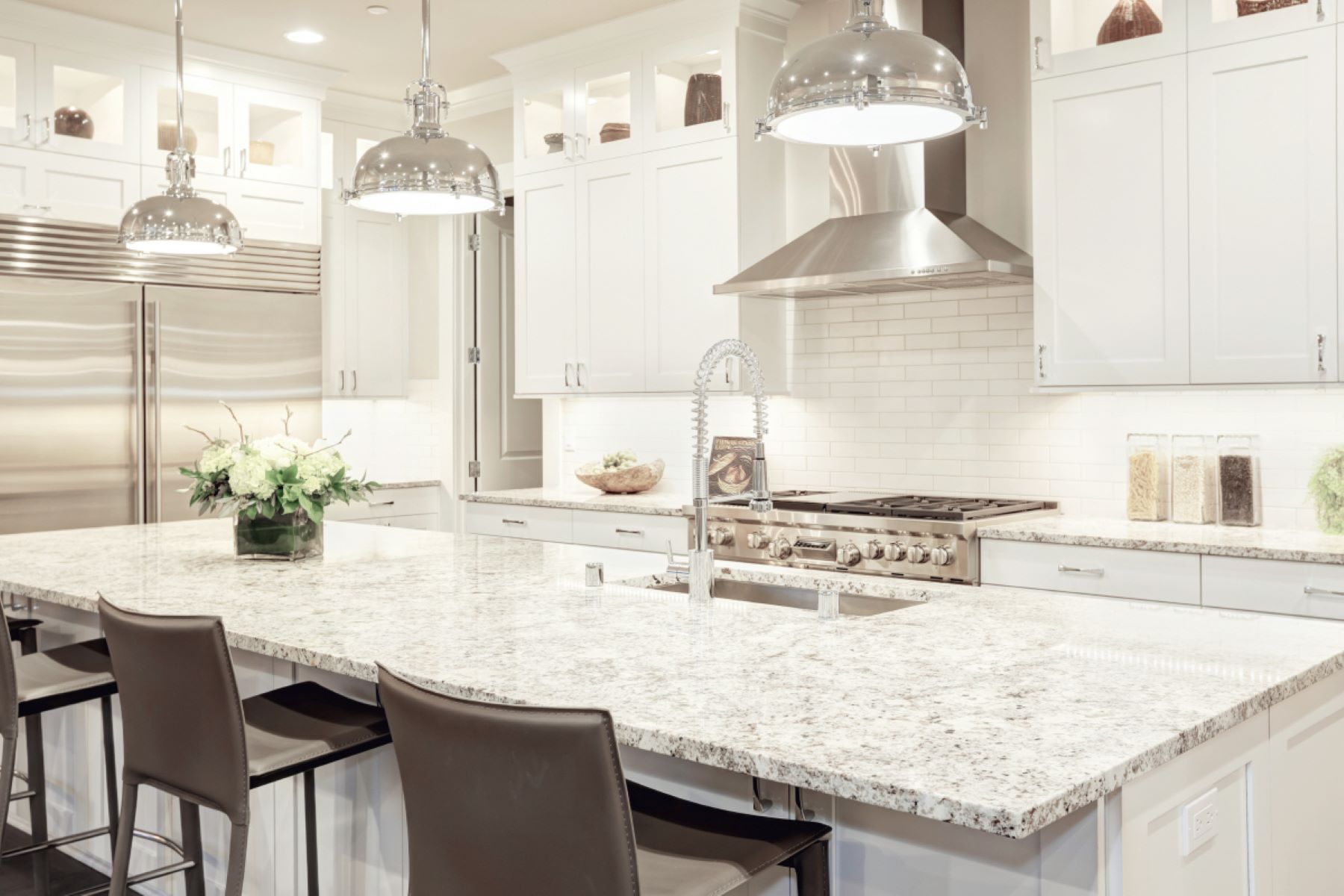
Articles
How Are Granite Countertops Made
Modified: December 13, 2023
Discover the process of creating granite countertops in this informative article. Learn how they are made and the steps involved in their production.
(Many of the links in this article redirect to a specific reviewed product. Your purchase of these products through affiliate links helps to generate commission for Storables.com, at no extra cost. Learn more)
Introduction
Granite countertops are a popular choice for homeowners due to their durability, beauty, and timeless appeal. Whether you’re remodeling your kitchen or building a new home, understanding how granite countertops are made can give you a deeper appreciation for this natural stone and help you make an informed decision for your next countertop project.
Granite is a natural stone that is formed deep within the earth’s crust through the slow cooling and solidification of molten magma. It is composed mainly of feldspar, quartz, and other minerals, giving it its unique texture and speckled appearance.
In the quarrying process, large blocks of granite are extracted from the earth’s surface using various techniques. The blocks are then cut, shaped, and polished to create stunning countertops that can withstand the test of time.
In this article, we will take a closer look at the process of how granite countertops are made. From quarrying to installation and maintenance, we will explore the intricate journey of this natural stone from the earth’s crust to your kitchen.
So, let’s dive in and uncover the fascinating world of granite countertop production.
Key Takeaways:
- The intricate process of creating granite countertops involves skilled craftsmanship, advanced technology, and attention to detail, ensuring their durability and stunning appearance for years to come.
- Proper maintenance and care, such as regular cleaning, avoiding stains and scratches, and following recommended sealing schedules, are essential for preserving the beauty and longevity of granite countertops, making them a worthwhile investment.
Read more: What Are Granite Countertops
Formation of Granite
Granite is an igneous rock that is formed by the cooling and solidification of molten magma deep within the earth’s crust. This process takes millions of years and involves a combination of geological forces and intense pressure.
Granite begins its formation as magma, which is a molten mixture of minerals and gases. Magma is generated when the earth’s mantle melts due to the extreme heat from the Earth’s core. As the magma rises towards the surface, it undergoes a process called crystallization, where the liquid minerals solidify and form interlocking crystals.
The composition of granite is primarily made up of feldspar, quartz, and mica, along with traces of other minerals. These minerals give granite its unique characteristics, such as its hardness, durability, and distinctive patterns.
As the magma cools, it solidifies and forms into a large mass of crystalline rock. The rate of cooling and the mineral composition determine the size, shape, and texture of the crystals within the granite. Slow cooling allows for larger crystals to form, while rapid cooling leads to smaller crystals.
Over millions of years, geological forces such as tectonic plate movements and erosion expose the granite formations on the Earth’s surface. This allows for quarrying and extraction to take place.
Now that we understand the formation of granite, let’s explore the process of quarrying and extracting blocks of granite for countertop production.
Quarrying
Quarrying is the first step in the process of creating granite countertops. It involves the extraction of large blocks of granite from natural stone deposits located deep within the earth. Granite quarries can be found in various locations around the world, each known for its unique color and quality of stone.
The quarrying process begins with the research and identification of suitable granite deposits. Geologists analyze the geological data and survey the land to determine the potential for granite extraction.
Once a suitable site is identified, the quarrying process begins with the clearing of vegetation and topsoil to expose the granite bedrock. Heavy machinery, such as excavators and bulldozers, are used to remove excess dirt and debris.
Next, the quarry operators employ drilling and blasting techniques to break the granite into manageable-sized blocks. This involves drilling holes into the granite face and inserting explosives. The controlled explosion fractures the granite, allowing for easier extraction.
After the blasting process, the granite blocks are carefully inspected to ensure they are free from any structural flaws or fractures. Blocks that do not meet the quality standards are discarded, and only the best blocks are selected for further processing.
The extraction of granite blocks can be a labor-intensive process that requires skilled operators and specialized equipment. Cranes and forklifts are commonly used to lift and move the large granite blocks for transportation to the processing facilities.
Quarrying is a crucial step in the manufacturing of granite countertops, as it determines the quality and availability of the raw materials. Now that we have extracted the granite blocks, let’s move on to the process of cutting and shaping them into countertops.
Extracting Blocks
Once the granite blocks have been extracted from the quarry, they are transported to a processing facility where they undergo a series of cutting and shaping processes to transform them into usable countertops.
The first step in extracting blocks is to carefully transport the large granite blocks from the quarry to the processing facility. This often involves the use of heavy-duty trucks or specialized machinery to ensure the blocks are transported safely and efficiently.
At the processing facility, the granite blocks are carefully inspected again for any imperfections or structural flaws. Any blocks that do not meet the quality standards are set aside or used for other purposes, such as landscaping or building materials.
Once the inspection is complete, the granite blocks are ready to be cut into smaller, more manageable sizes. Diamond wire saws or large circular saws are used to make precise cuts along the natural grain of the granite. This process requires skill and precision to ensure clean and straight cuts.
After the blocks have been cut into smaller sizes, they are then shaped according to the desired specifications. This can involve using a combination of saws, routers, and other cutting tools to shape the granite into the required dimensions and edge profiles for the countertops.
During the block extraction process, the aim is to maximize the yield of usable material while minimizing waste. Skilled craftsmen and advanced equipment work together to ensure that the extracted blocks are transformed into high-quality granite countertops.
Now that we have extracted and shaped the granite blocks, let’s explore the next step in the process: polishing.
Cutting and Shaping
Once the granite blocks have been extracted and transported to the processing facility, they undergo a precise cutting and shaping process to transform them into the desired dimensions and edge profiles for countertops.
The first step in cutting and shaping the granite is to carefully measure and mark the blocks according to the desired specifications. Skilled craftsmen use specialized tools, such as measuring tapes and templates, to ensure accurate measurements and precise cuts.
Diamond wire saws or large circular saws are commonly used to make the initial cuts on the granite blocks. These saws are equipped with diamond-impregnated blades that can efficiently cut through the hard surface of the granite.
Once the initial cuts have been made, the granite pieces are then shaped according to the desired dimensions. This can involve using a combination of saws, routers, and other cutting tools to create straight edges, curved profiles, and intricate designs.
Skilled craftsmen meticulously work on each piece of granite, ensuring that the cuts and shapes are precise and meet the exact specifications. They have a keen eye for detail and expertise in working with granite to bring out its natural beauty.
In addition to cutting and shaping the granite, the craftsmen also pay attention to the edge profiles. They use specialized tools, such as diamond routers, to create different edge profiles, such as bullnose, bevel, or ogee, based on the customer’s preferences.
The cutting and shaping process requires a combination of craftsmanship and modern technology to achieve the desired results. Skilled artisans work closely with advanced machinery to ensure that the granite is cut and shaped accurately and efficiently.
Now that the granite pieces have been cut and shaped, the next step is to move on to the polishing process to enhance their beauty and luster.
Granite countertops are made by cutting and polishing large slabs of natural granite stone. The slabs are then shaped to fit the specific dimensions of the countertop and sealed to protect against stains and damage.
Read more: How To Restore Granite Countertops
Polishing
Polishing is a crucial step in the process of creating granite countertops. It enhances the beauty and luster of the granite, providing a smooth, glossy finish that highlights the natural patterns and colors of the stone.
The polishing process begins after the granite has been cut and shaped to the desired specifications. The granite pieces are first inspected to ensure that there are no rough edges or uneven surfaces that need to be addressed before polishing.
To achieve a high-quality polish, craftsmen use a series of progressively finer diamond abrasives to grind and polish the surface of the granite. This process is typically done using automated machinery specifically designed for polishing natural stone.
The initial stage of the polishing process involves rough-grinding the surface of the granite using coarse-grit diamond pads. This helps to remove any imperfections or surface scratches and create a more uniform appearance.
As the polishing process continues, finer-grit diamond pads are used to refine the surface and gradually bring out the natural shine of the granite. The pads are applied with water or a polishing compound to lubricate the surface and prevent overheating.
Throughout the polishing process, the craftsmen closely monitor the progress to ensure that each piece of granite receives an even and consistent polish. They pay attention to every detail, ensuring that the natural patterns and colors of the granite are accentuated.
Once the polishing is complete, the granite pieces are thoroughly cleaned and dried to remove any residues or watermarks. This allows the true beauty of the polished granite to shine through, revealing its depth, clarity, and stunning visual appeal.
Polishing is a skillful and meticulous process that requires both expertise and attention to detail. It is the final touch that brings out the full potential of the granite, making it ready for the next step: finishing and sealing.
Finishing and Sealing
After the granite countertops have been polished to a high sheen, the next step in the manufacturing process is finishing and sealing. These steps add the final touches to the countertops, ensuring their longevity, durability, and resistance to stains and damage.
Finishing involves the application of various treatments to enhance the appearance and protect the surface of the granite. One common finishing technique is called honing, which gives the granite a matte or satin-like finish. This finish is popular for those looking for a more subtle and understated look.
Another option for finishing is called antiquing, which involves creating a textured or aged appearance on the surface of the granite. This technique is achieved through different methods, such as brushing, sandblasting, or creating intentional imperfections. Antiquing can give the granite countertops a unique and rustic charm.
Once the finishing process is complete, the granite countertops are sealed to protect them from staining and moisture absorption. A high-quality sealant is applied to the surface of the granite, creating a protective barrier that helps to repel liquids and prevent the penetration of stains.
The sealing process involves evenly applying the sealant across the entire surface of the countertops. It is important to ensure that all areas, including the edges and seams, are adequately sealed to provide maximum protection.
After the sealant is applied, it is left to dry and cure. This can take a few hours or even a day, depending on the specific sealant used. Once the sealant is fully cured, the granite countertops are ready for installation.
Finishing and sealing play a crucial role in the longevity and maintenance of granite countertops. The finishing techniques enhance the visual appeal of the countertops, while the sealing process protects them from potential damage.
Now that we have completed the finishing and sealing process, let’s move on to the final step: the installation process of granite countertops.
Installation Process
The installation process of granite countertops is a meticulous and precise task that requires the expertise of skilled professionals. It involves careful planning, precise measurements, and precise placement to ensure a seamless and secure fit.
The installation process typically begins with a site visit by the installation team. They will take accurate measurements of the area where the countertops will be installed, including the dimensions of the cabinets or base structure.
Based on these measurements, the installation team will then create a template that serves as a guide for cutting the granite slabs to the correct size and shape. This template ensures a precise fit and allows for any necessary adjustments to be made before the final installation.
Once the template is created, the granite slabs are carefully transported to the installation site. The slabs are usually quite heavy and may require specialized equipment, such as hoists or cranes, to safely lift and maneuver them into place.
Prior to installing the granite countertops, the installation team will prepare the base structure, ensuring it is level, stable, and properly supported to bear the weight of the granite.
The installation team will then apply a thin layer of adhesive or mortar to the base structure and carefully place the granite slabs onto the prepared surface. They will ensure that each piece fits snugly and is aligned with the surrounding elements, such as walls and cabinets.
Next, the installation team will use leveling tools to ensure that the countertops are perfectly level. This step is crucial to prevent any unevenness or issues with the functionality of the countertops.
Once the granite slabs are securely in place, any visible seams or joints between the slabs are carefully filled with color-matched epoxy or resin. This helps to create a seamless appearance and ensure a smooth, even surface.
To complete the installation process, the installation team will clean the countertops, remove any excess adhesive or debris, and apply a final sealant to the granite surface. This final sealant provides added protection and maintains the aesthetic appeal of the countertops.
After the installation is complete, the homeowners can enjoy their beautiful and functional granite countertops. It is important to follow the recommended maintenance and care instructions to ensure the longevity and beauty of the countertops.
Now that we have covered the installation process, let’s move on to some maintenance tips to keep your granite countertops looking their best.
Maintenance Tips
Granite countertops are known for their durability and resistance to stains and scratches. However, proper maintenance is still essential to keep them looking their best and prolong their lifespan. Here are some key maintenance tips to ensure the longevity and beauty of your granite countertops:
- Regular Cleaning: Clean your granite countertops regularly using a mild, pH-neutral cleaner and a soft cloth or sponge. Avoid using abrasive cleaners, acidic substances, or harsh chemicals that can damage the surface.
- Avoiding Stains: Quickly wipe up any spills, especially those from acidic substances like citrus juices, red wine, or oils. Even though granite is relatively resistant to stains, prolonged exposure to certain substances can still cause discoloration.
- Preventing Scratches: Use cutting boards or chopping blocks when preparing food on the countertops. While granite is highly durable, sharp objects or excessive force can still leave scratches on the surface.
- Protecting from Heat: Use trivets or hot pads when placing hot pans or pots on the granite countertops. Although granite can withstand high temperatures, sudden changes in temperature may cause thermal shock and lead to cracks or damage.
- Sealing Regularly: Depending on the type of sealant used, granite countertops may require resealing every 1 to 3 years. Follow the manufacturer’s instructions and consult with your installer to determine the appropriate sealing schedule for your countertops.
- Avoiding Heavy Objects: Do not place heavy objects or apply excessive pressure on one specific area of the countertop. This can cause the granite to crack or chip. Distribute weight evenly across the surface.
- Using Gentle Cleaning Tools: Avoid using abrasive scrub pads or sharp tools to clean the granite surface. Instead, use soft microfiber cloths or non-abrasive sponges to gently clean and dry the countertops.
- Regular Inspections: Periodically check the countertops for any signs of damage, such as chips, cracks, or lifting at the seams. If you notice any issues, contact a professional to address them promptly and prevent further damage.
- Professional Maintenance: Consider hiring a professional granite maintenance company for deep cleaning, polishing, and resealing, if needed. They have the knowledge and specialized equipment to maintain the beauty and integrity of your granite countertops.
- Follow Manufacturer’s Guidelines: Always follow the specific care and maintenance guidelines provided by the manufacturer or your countertop installer. They can provide valuable insights and instructions tailored to your specific granite countertops.
By following these maintenance tips and practicing regular care, you can ensure that your granite countertops remain beautiful, functional, and a stunning addition to your home for years to come.
Now that you’re equipped with these maintenance tips, you can enjoy the beauty and durability of your granite countertops with confidence.
Read more: How To Dispose Of Granite Countertops
Conclusion
Granite countertops are not only aesthetically pleasing but also durable, making them a popular choice for homeowners. Understanding the process of how granite countertops are made can give you a deeper appreciation for this natural stone and help you make informed decisions when it comes to your countertop projects.
From the formation of granite deep within the Earth’s crust to the meticulous process of quarrying, extracting blocks, cutting, shaping, polishing, and finishing, each step in the manufacturing process contributes to the beauty and functionality of granite countertops.
Granite countertops undergo a journey that involves skilled craftsmanship, advanced technology, and attention to detail. The selection of high-quality granite blocks, precise cutting and shaping, meticulous polishing, and thoughtful finishing and sealing ensures that these countertops can withstand daily use and maintain their stunning appearance.
Proper maintenance and care are also essential for preserving the beauty and longevity of granite countertops. Regular cleaning, avoiding stains and scratches, using heat protection, and following recommended sealing schedules are key steps to keeping your countertops looking their best for years to come.
Whether you’re remodeling your kitchen or building a new home, granite countertops offer a timeless elegance that can elevate the look and value of any space. The durability, natural beauty, and low-maintenance qualities of granite make it a worthwhile investment that can withstand the test of time.
Now that you have a comprehensive understanding of how granite countertops are made and how to maintain them, you can confidently embark on your countertop project, knowing that you have made an informed choice in selecting this exquisite natural stone.
So go ahead, enjoy the beauty and functionality of your granite countertops, and immerse yourself in the timeless allure of this magnificent natural stone.
Frequently Asked Questions about How Are Granite Countertops Made
Was this page helpful?
At Storables.com, we guarantee accurate and reliable information. Our content, validated by Expert Board Contributors, is crafted following stringent Editorial Policies. We're committed to providing you with well-researched, expert-backed insights for all your informational needs.
0 thoughts on “How Are Granite Countertops Made”