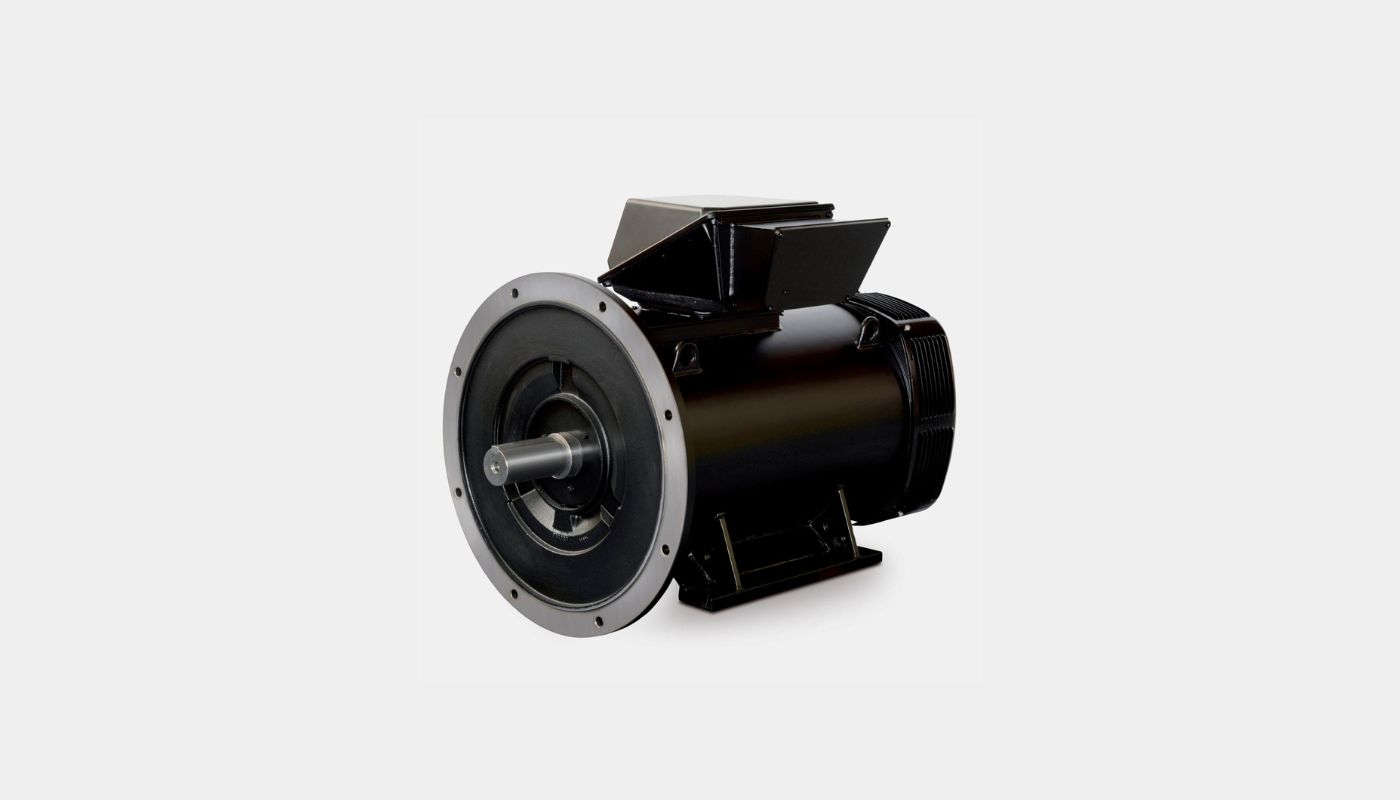
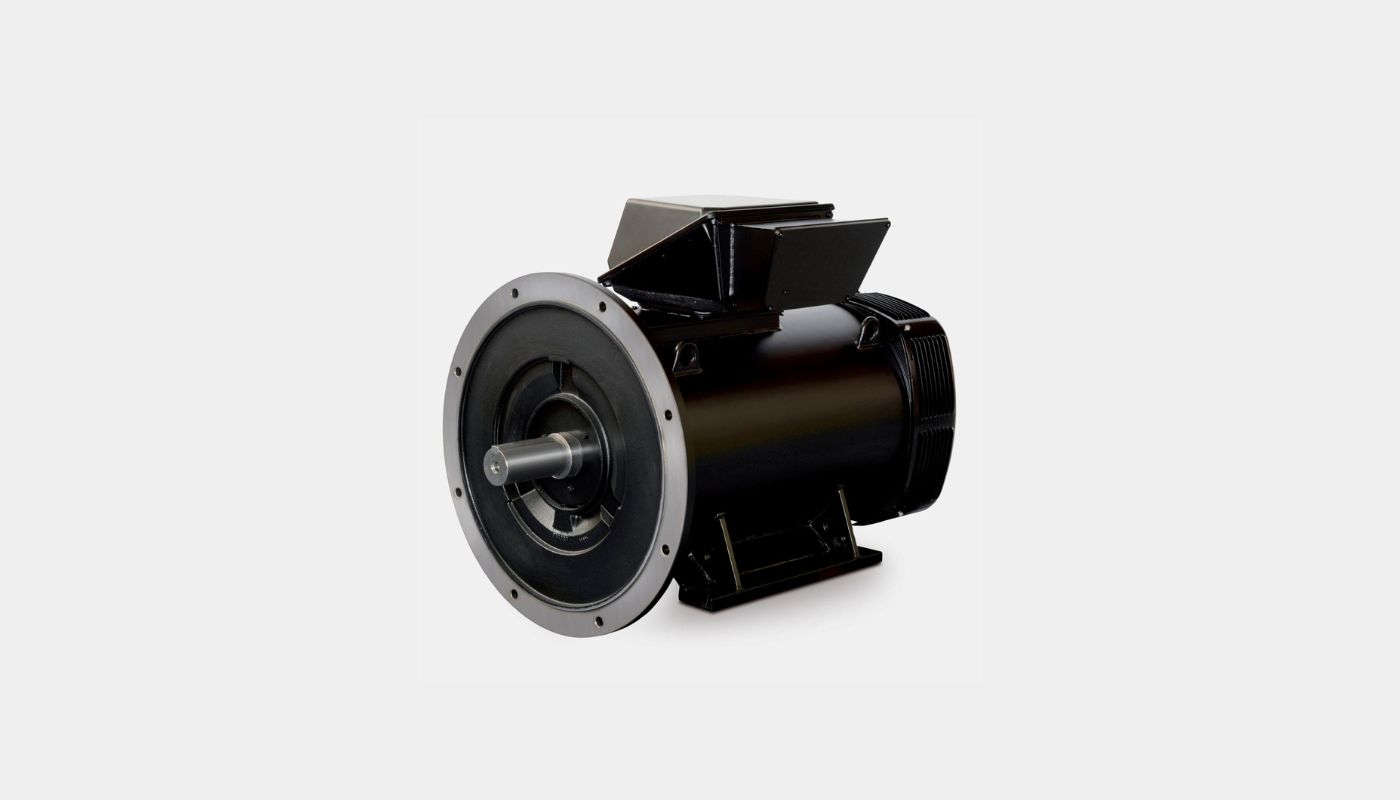
Articles
How To Choose The Right Electric Motor
Modified: March 21, 2024
Looking for expert advice on choosing the right electric motor? Our informative articles provide valuable insights to help you make the best decision.
(Many of the links in this article redirect to a specific reviewed product. Your purchase of these products through affiliate links helps to generate commission for Storables.com, at no extra cost. Learn more)
Introduction
Electric motors play a crucial role in many aspects of our daily lives, from powering industrial machinery to propelling electric vehicles. With advancements in technology, there are now numerous options to choose from when it comes to electric motors. However, selecting the right motor for your specific needs can be a daunting task.
In this article, we will guide you through the process of choosing the right electric motor. We will explore various factors that need to be considered, such as power requirements, speed and torque, motor types, efficiency and energy consumption, size and weight, cost considerations, motor control and compatibility, maintenance and lifespan, noise and vibration levels, and environmental considerations.
By understanding these factors and their significance, you will be able to make an informed decision and ensure that the electric motor you choose meets your specific requirements, whether it’s for a DIY project, a commercial application, or any other purpose.
So, let’s delve into the world of electric motors and discover how to choose the right one for your needs.
Key Takeaways:
- Choose the right electric motor by considering power requirements, motor types, efficiency, and environmental impact. Balance performance and cost for optimal results in your application.
- Prioritize noise and vibration levels, energy efficiency, and environmental compliance when selecting an electric motor. Ensure seamless integration and sustainable operation for long-term success.
Read more: How To Choose An Electric Motor For A Car
Understanding Electric Motors
Before diving into the factors to consider when choosing an electric motor, let’s first understand the basic principles behind how electric motors work.
An electric motor is a device that converts electrical energy into mechanical energy. It operates based on the principle of electromagnetism. The motor consists of a stator (stationary part) and a rotor (rotating part). When an electric current passes through the motor’s windings, a magnetic field is created, which interacts with the magnetic field produced by permanent magnets or electromagnets in the rotor. This interaction causes the rotor to rotate, thus generating mechanical energy.
Electric motors are available in various sizes, power capacities, and types, offering versatility for different applications. The factors to consider when choosing an electric motor depend on the specific requirements of your project or application.
Let’s explore these factors in detail, starting with power requirements.
Factors to Consider
When choosing an electric motor, there are several crucial factors to take into consideration. These factors will help determine the motor’s suitability for your specific application and ensure optimal performance. Let’s explore these factors in detail:
Power Requirements
The power requirements of your application will dictate the size and capacity of the electric motor needed. Consider the voltage, current, and power output requirements of your project. Make sure to choose a motor that can handle the required power without overheating or straining.
Speed and Torque
The desired speed and torque of your application play a significant role in motor selection. Speed refers to the rotational speed of the motor, typically measured in revolutions per minute (RPM). Torque, on the other hand, refers to the rotational force or turning ability of the motor. Depending on your application, you may require high torque for heavy loads or high speed for quick acceleration.
Read more: How To Choose The Right Mortar
Types of Electric Motors
There are various types of electric motors available, each with its own advantages and disadvantages. The most common types include:
DC Motors:
Direct Current (DC) motors run on DC power and are known for their simplicity and controllability. They are widely used in applications such as robotics, electric vehicles, and small appliances.
AC Motors:
Alternating Current (AC) motors are powered by AC power and are commonly found in industrial machinery, HVAC systems, and household appliances. They offer high efficiency and are suitable for continuous operation.
Brushed Motors:
Brushed motors use brushes and a commutator to transfer electrical power to the rotor. They are relatively affordable and easy to control, making them popular in certain applications.
Brushless Motors:
Brushless motors, as the name suggests, do not have brushes or a commutator. They offer higher efficiency, longer lifespan, and reduced maintenance compared to brushed motors. They are widely used in applications requiring high performance.
Power Requirements
One of the most crucial factors to consider when choosing an electric motor is its power requirements. Understanding and accurately assessing the power needs of your application is essential to ensure that the motor can perform optimally and meet your expectations. To determine the power requirements, you need to consider several key factors:
Voltage
The voltage required by the electric motor should match the power supply available in your application. Most motors are designed to operate on either AC (Alternating Current) or DC (Direct Current) power. Make sure to check the voltage compatibility of the motor to avoid any potential damage or inefficiency.
Current
The current, measured in Amperes (A), is another important consideration. It indicates the amount of electrical current the motor will draw from the power supply. Ensure that the motor and power source can handle the expected current load without overheating or tripping circuit breakers.
Read more: How To Choose The Right Conduit Size
Power Output
The power output required for your application depends on the specific tasks and workload. It is typically measured in Watts (W) or Horsepower (HP). Consider the demands of your application, such as the load to be moved or the task to be performed, and choose a motor that can generate the necessary power output.
It is important to note that power requirements may vary based on whether the motor is intended for continuous or intermittent duty. Continuous-duty motors are designed to operate continuously without overheating, making them suitable for applications with long-running operations. On the other hand, intermittent-duty motors are designed to handle short periods of operation followed by rest periods, such as in intermittent pumping or cycling operations.
Additionally, consider any specific power factor requirements your application may have. The power factor is a measure of the efficiency of electrical power utilization. Some applications may require motors with a high power factor for improved energy efficiency or to comply with certain regulations.
By accurately assessing the voltage, current, power output, and power factor requirements of your application, you can choose an electric motor that is compatible with your power supply and capable of delivering the necessary performance.
Speed and Torque
The desired speed and torque of your application are crucial factors to consider when choosing an electric motor. Speed refers to the rotational speed at which the motor operates, typically measured in revolutions per minute (RPM). Torque, on the other hand, refers to the rotational force or twisting power produced by the motor.
Speed
The required speed of the motor depends on the specific application. Some applications may require motors that operate at high speeds for quick acceleration or fast movement, while others may require slower speeds for precision control or increased torque. It is important to select a motor with a speed range that can meet the demands of your application.
Consider factors such as the load to be moved, the desired response time, and the efficiency requirements. If your application requires variable speed control, you may want to consider motors that can be easily adjusted or those that come with built-in speed control features.
Torque
Torque is a measure of the rotational force or turning ability of the motor. It determines the motor’s ability to overcome resistance and perform tasks that require force or torque, such as lifting heavy loads or driving machinery. The torque requirements of your application will depend on factors like the load to be moved, the required acceleration, and the level of precision needed.
High torque motors are capable of delivering greater force and can handle heavy loads more effectively. On the other hand, low torque motors are suitable for applications where precise control and fine movements are required.
It’s important to ensure that the motor you choose can provide the necessary speed and torque to meet the requirements of your application. Consider the operational speed range and the torque curve of the motor to ensure compatibility.
Keep in mind that the speed and torque characteristics of electric motors can be influenced by factors such as the voltage and current supplied to the motor, motor efficiency, and mechanical losses. Therefore, it is essential to carefully analyze and select a motor that can provide the appropriate speed and torque for your specific application.
Read more: How To Choose The Right Kitchenaid Mixer
Types of Electric Motors
When choosing an electric motor, it is essential to consider the different types available and understand their characteristics and suitability for your specific application. Each type of motor has its own advantages and disadvantages. Let’s explore some of the most common types:
DC Motors
Direct Current (DC) motors are among the simplest and most widely used types of electric motors. They operate using direct current power and are known for their controllability and reliability. DC motors are used in various applications, including robotics, electric vehicles, small appliances, and industrial machinery. They offer good speed control, high starting torque, and efficient operation. However, they may require a separate power supply, such as a battery or DC power source.
AC Motors
Alternating Current (AC) motors operate using alternating current power and are commonly found in industrial machinery, HVAC systems, and household appliances. AC motors are highly efficient, require minimal maintenance, and can operate at various speeds. Induction motors, synchronous motors, and universal motors are some of the common types of AC motors. AC motors are known for their reliability, ease of use, and wide availability.
Brushed Motors
Brushed motors are a type of DC motor that uses brushes and a commutator to transfer electrical power to the rotor. They are relatively simple and inexpensive, making them popular in certain applications. Brushed motors offer good starting torque, easy controllability, and compact size. However, they have limited lifespan due to wear and tear of the brushes and commutator, and they may generate more heat and electromagnetic interference.
Brushless Motors
Brushless motors, as the name suggests, do not have brushes or a commutator. Instead, they employ electronic commutation to control the motor’s operation. Brushless motors offer several advantages over brushed motors, including higher efficiency, longer lifespan, reduced maintenance, and improved performance. These motors are widely used in applications requiring high performance and reliability, such as drones, electric vehicles, and industrial machinery. However, brushless motors tend to be more expensive than their brushed counterparts.
There are also specialized types of electric motors available for specific applications, such as stepper motors, servo motors, and linear motors. These motors offer precise control, high accuracy, and specific functionality, making them suitable for robotics, CNC machines, and other intricate systems.
By understanding the different types of electric motors and their characteristics, you can choose a motor that best aligns with your application’s requirements in terms of control, efficiency, performance, and cost.
DC Motors
Direct Current (DC) motors are a popular type of electric motor that operate using direct current power. They are widely used in a range of applications due to their controllability, reliability, and ease of use. DC motors convert electrical energy into mechanical energy through the interaction of magnetic fields generated by the stator and rotor. Let’s take a closer look at the features and applications of DC motors:
Features of DC Motors
DC motors have several distinct features that make them preferred choices in many industries and applications:
- Controllability: DC motors offer precise speed and torque control, making them versatile for various applications.
- High Starting Torque: DC motors provide high starting torque, which makes them suitable for applications that require quick acceleration or heavy loads.
- Efficiency: DC motors are known for their high efficiency, meaning they can convert a significant amount of electrical energy into mechanical power.
- Compact Size: DC motors are available in compact sizes, making them suitable for applications where space is limited. They can be easily integrated into different systems and devices.
- Reliability: DC motors are durable and reliable, requiring minimal maintenance and offering long lifespans with proper care.
Applications of DC Motors
DC motors find applications in various industries and fields due to their versatility and controllability. Some common applications include:
- Robotics: DC motors are widely used in robotics for tasks such as locomotion, gripping, and arm movement. Their controllable speed and torque make them suitable for precise movements and tasks.
- Electric Vehicles: Many electric vehicles, including electric cars, bikes, and scooters, utilize DC motors for propulsion. DC motors provide the necessary torque and control to drive these vehicles efficiently.
- Small Appliances: DC motors are commonly found in a range of small appliances such as fans, vacuum cleaners, and hairdryers. Their compact size and controllable speed make them ideal for these applications.
- Industrial Machinery: Various types of industrial machinery use DC motors for specific operations such as conveyor systems, pumps, and material handling equipment. The precise control and high torque capabilities of DC motors make them suitable for these demanding applications.
It’s important to consider the specific requirements of your application, such as voltage and current requirements, speed, torque, and power output, when selecting a DC motor. Additionally, be sure to choose a motor from a reputable manufacturer to ensure quality and reliable performance.
Overall, DC motors offer excellent controllability, reliability, and efficiency, making them a popular choice in numerous industries and applications.
AC Motors
AC motors are a widely used type of electric motor that operates using alternating current (AC) power. They are known for their efficiency, reliability, and versatility, making them suitable for a wide range of applications across various industries. AC motors convert electrical energy into mechanical energy through the interaction of magnetic fields generated by the stator and rotor. Let’s explore the features and applications of AC motors:
Features of AC Motors
AC motors possess several key features that make them highly advantageous in numerous applications:
- Efficiency: AC motors are known for their high efficiency, allowing them to convert electrical energy into mechanical power with minimal energy loss. This results in cost savings and reduced environmental impact.
- Reliability: AC motors are durable and reliable, requiring minimal maintenance. They are designed to operate continuously for extended periods without overheating or sustaining damage.
- Versatility: AC motors offer a wide range of operating speeds and power outputs, ensuring compatibility with various applications and operational requirements.
- Smooth Operation: AC motors provide smooth and consistent operation due to the constant frequency nature of AC power. This results in reduced vibration and noise levels in many applications.
- Easy Integration: AC motors are readily available and can be easily integrated into existing systems or equipment. They come in different sizes and configurations, allowing for flexibility and ease of installation.
Applications of AC Motors
AC motors are utilized in a diverse range of applications across different industries. Some common applications include:
- Industrial Machinery: AC motors are extensively used in industrial machinery and equipment such as pumps, compressors, conveyors, and fans. Their high reliability and efficiency make them ideal for these demanding applications.
- Household Appliances: Many household appliances, including refrigerators, air conditioners, washing machines, and dishwashers, rely on AC motors for various functions. AC motors provide the necessary power output and efficiency required for these everyday appliances.
- HVAC Systems: Heating, ventilation, and air conditioning (HVAC) systems commonly use AC motors for fans, blowers, and compressors. AC motors offer the required performance and reliability to circulate air and regulate temperature in residential, commercial, and industrial settings.
- Electric Power Tools: AC motors are utilized in a wide range of electric power tools, including drills, saws, and grinders. They provide the necessary power and efficiency to handle demanding tasks.
- Renewable Energy Systems: AC motors are commonly used in renewable energy systems, such as wind turbines and hydroelectric generators. They convert the mechanical energy of wind or flowing water into electrical energy, contributing to the production of clean and sustainable power.
When selecting an AC motor, consider factors such as voltage compatibility, power output, speed range, and required operational conditions. It’s essential to choose a motor from a reputable manufacturer to ensure quality, reliability, and optimal performance for your specific application.
Overall, AC motors are highly reliable, efficient, and versatile, making them an excellent choice for numerous industrial, commercial, and residential applications.
Brushed Motors
Brushed motors are a type of DC (Direct Current) motor that incorporates brushes and a commutator to transfer electrical power to the rotor. They are widely used in various applications due to their simplicity, affordability, and controllability. Brushed motors are known for their ease of use and reliability. Let’s explore the features, advantages, and applications of brushed motors:
Features of Brushed Motors
Brushed motors possess several key features that make them suitable for a range of applications:
- Simple Design: Brushed motors are relatively simple in design, consisting of a stationary part called the stator and a rotating part called the rotor. The brushes and commutator facilitate the flow of electrical current, allowing the motor to function.
- Affordability: Brushed motors are generally more affordable compared to other types of electric motors. Their relatively simple design and widespread availability contribute to their cost-effectiveness.
- Controllability: Brushed motors offer excellent speed control, allowing for precise adjustments to meet specific application requirements.
- Compact Size: Brushed motors are compact and lightweight, making them suitable for applications where space is limited or weight is a concern.
- Low Starting Voltage: Brushed motors can start and operate at relatively low voltages, enabling them to work well with low-power systems or batteries.
Advantages of Brushed Motors
Brushed motors offer several advantages compared to other types of motors:
- Easy Speed Control: Brushed motors provide excellent speed control through the adjustment of the voltage applied. This simplicity makes them highly suitable for applications that require precise speed adjustments.
- High Starting Torque: Brushed motors provide high starting torque, making them capable of handling heavy loads and enabling quick acceleration.
- Cost-Effective: Brushed motors tend to be more affordable compared to other types of motors, making them an economical choice for many applications.
- Reliability: Brushed motors have a long history of reliable performance, and their simple design contributes to their durability.
Applications of Brushed Motors
Brushed motors find applications in various industries and fields:
- Consumer Electronics: Brushed motors are commonly found in small household appliances, such as electric toothbrushes, hairdryers, and handheld vacuum cleaners, where compact size and cost-effectiveness are important.
- Automotive Industry: Brushed motors are still used in some automotive applications, such as electric power windows, windshield wipers, and HVAC blowers.
- Robotics: Brushed motors are often employed in hobby robotics and educational projects due to their simplicity, affordability, and controllable speed.
- Toy Industry: Many battery-operated toys, such as remote-controlled cars, rely on brushed motors for their propulsion and control.
Despite their advantages and widespread use, brushed motors also have some limitations. They tend to generate more heat and electromagnetic interference compared to brushless motors. Additionally, the brushes and commutator undergo wear and tear over time, affecting the motor’s lifespan and necessitating periodic maintenance.
When considering a brushed motor for your application, carefully evaluate its compatibility with voltage requirements, speed range, torque output, and maintenance needs. Choosing a motor from a reputable manufacturer will ensure quality and reliable performance.
In summary, brushed motors are a cost-effective and controllable option for various applications that require simplicity, affordability, and precise speed control.
Brushless Motors
Brushless motors are a type of electric motor that offer numerous advantages over traditional brushed motors. These motors operate without brushes or a commutator, resulting in improved performance, increased efficiency, and reduced maintenance. Brushless motors are widely used in various applications where high performance, durability, and precise control are required. Let’s explore the features, advantages, and applications of brushless motors:
Features of Brushless Motors
Brushless motors possess several key features that make them highly desirable for a wide range of applications:
- Efficiency: Brushless motors are more efficient than brushed motors due to their design without brushes or commutators. This increased efficiency results in reduced energy consumption and longer battery life in battery-powered applications.
- Longer Lifespan: Without brushes that wear out over time, brushless motors have a longer lifespan and require less maintenance compared to brushed motors. This makes them more reliable and cost-effective in the long run.
- Compact Size and High Power Output: Brushless motors can be designed to have a compact size while delivering a high power output. This makes them ideal for applications where space is limited, such as drones or electronic devices.
- Improved Control: Brushless motors offer precise speed and torque control, making them suitable for applications that require high-performance and responsiveness, such as robotics or industrial automation.
- Reduced Electromagnetic Interference: Brushless motors generate less electromagnetic interference compared to brushed motors, resulting in improved reliability and reduced interference with other electronic devices.
Advantages of Brushless Motors
Brushless motors provide several advantages over brushed motors:
- Higher Efficiency: Brushless motors are more efficient, which contributes to energy savings and longer battery life in battery-powered applications. This efficiency is especially beneficial in applications that require extended operation or have limited power sources.
- Improved Performance: The absence of brushes and commutators in brushless motors eliminates the friction and wear associated with brushed motors. This results in smoother, quieter operation and improved overall performance.
- Lower Maintenance: Brushless motors require minimal maintenance due to the absence of brushes that need replacement. This reduces downtime and maintenance costs associated with motor upkeep.
- Compact and Lightweight: Brushless motors can be designed to be smaller and lighter than brushed motors of similar power output, making them ideal for applications where size and weight are crucial factors.
- Wide Range of Applications: Brushless motors are used in a variety of applications, including drones, electric vehicles, HVAC systems, robotics, industrial machinery, and more. Their high performance, controllability, and efficiency make them ideal for demanding applications.
Applications of Brushless Motors
Brushless motors find applications in numerous industries and fields:
- Aerospace and Drones: Brushless motors are commonly used in aerospace applications and drones due to their lightweight design, high efficiency, and precise control.
- Electric Vehicles (EVs): Many electric vehicles, including cars, motorcycles, and scooters, utilize brushless motors for propulsion. The high efficiency and power output of brushless motors contribute to the performance and range of electric vehicles.
- Industrial Automation: Brushless motors are widely used in industrial automation processes, such as CNC machines, robotics, and motion control systems, where precise control, high performance, and durability are essential.
- HVAC Systems: HVAC systems, including fans and pumps, often incorporate brushless motors due to their efficiency, reliability, and precise speed control.
- Consumer Electronics: Brushless motors are found in various consumer electronics, such as computer cooling fans, hard disk drives, and electric kitchen appliances, where their compact size and controllability are advantageous.
When selecting a brushless motor, consider factors such as voltage and current requirements, speed range, power output, and specific application needs. Ensure that the motor is from a reputable manufacturer to guarantee quality and reliable performance.
In summary, brushless motors offer higher efficiency, improved performance, and reduced maintenance compared to brushed motors. Their versatility and controllability make them highly desirable for applications that require high performance, precision, and reliability.
Motor Efficiency and Energy Consumption
Motor efficiency and energy consumption are important considerations when choosing an electric motor. Maximizing motor efficiency not only saves energy and reduces operating costs but also contributes to environmental sustainability. Let’s explore the concepts of motor efficiency and energy consumption in more detail:
Motor Efficiency
The efficiency of an electric motor is a measure of how effectively it converts electrical energy into mechanical energy. It is expressed as a percentage and represents the ratio of output power (mechanical power) to input power (electrical power). The higher the efficiency, the more effectively the motor converts electrical energy into useful work, and the less energy is wasted as heat.
Motor efficiency is influenced by various factors, including the motor design, construction materials, winding resistance, and operating conditions. Today, many electric motors are designed to have high efficiencies, ranging from 75% to over 95%, depending on the motor type and size.
Energy Consumption
The energy consumption of an electric motor refers to the amount of electrical energy it uses to perform a certain amount of work over a given period of time. It is measured in kilowatt-hours (kWh) and is directly related to the power rating and operational characteristics of the motor.
When selecting a motor, it is essential to consider the energy consumption, as it directly impacts the operating costs and environmental impact. A more energy-efficient motor will consume less electricity to accomplish the same task, resulting in reduced energy bills and lower carbon footprint.
Factors Affecting Efficiency and Energy Consumption
Several factors can affect the efficiency and energy consumption of electric motors:
- Motor Type: Different types of motors have varying efficiencies. For example, brushless motors generally have higher efficiencies compared to brushed motors.
- Load Profile: The type and characteristics of the load being driven by the motor can impact its efficiency and energy consumption. Motors operating at full load tend to have higher efficiencies compared to motors operating at partial loads.
- Motor Speed: Motors operating closer to their rated speed tend to have higher efficiencies compared to motors operating at lower speeds.
- Maintenance: Proper maintenance, such as lubrication, cleaning, and checking for worn-out components, can help maintain motor efficiency and prevent energy losses due to mechanical issues.
Energy-Efficient Motor Selection
When selecting an electric motor, consider the following tips to ensure energy efficiency:
- Look for High-Efficiency Ratings: Check the motor’s efficiency rating, which is usually provided by the manufacturer. Motors with higher efficiency ratings are designed to consume less energy.
- Proper Sizing: Select a motor that is appropriately sized for the specific application to avoid oversized motors that are less efficient at lower loads.
- Variable Speed Drives: Consider using motors with variable speed drives (VSDs) when possible. VSDs allow the motor to match the speed and power output to the actual requirements of the load, resulting in energy savings.
- Maintain Optimal Conditions: Ensure the motor is operated under optimal conditions, such as proper voltage and current levels, adequate cooling, and regular maintenance.
Motor efficiency and energy consumption play significant roles in the overall operation and cost-effectiveness of electric motors. By choosing an energy-efficient motor and implementing good maintenance practices, you can not only reduce energy consumption but also lower operating costs and contribute to a more sustainable future.
Motor Size and Weight
Motor size and weight are important considerations when selecting an electric motor for your application. The size and weight of the motor can impact the efficiency, performance, and compatibility with the intended system or equipment. Let’s explore the significance of motor size and weight:
Motor Size
The size of an electric motor refers to its physical dimensions, including the length, width, and height. The size of a motor can vary significantly depending on factors such as power rating, motor type, and design. It’s important to consider the available space and clearance requirements in your application when choosing a motor.
Using an appropriately sized motor is crucial for ensuring optimal performance and compatibility. An oversized motor may be physically too large to fit within the designated space, resulting in installation challenges or constraints. On the other hand, an undersized motor may not provide sufficient power output or thermal dissipation, leading to inefficiency, overheating, and premature failure.
Consider the physical constraints of your application, such as the dimensions of the motor mounting space, the weight-bearing capacity, and any size limitations imposed by the system or equipment. Additionally, ensure that the motor specifications provide the necessary information regarding the physical dimensions to aid in proper selection.
Motor Weight
The weight of an electric motor is another important factor to consider, especially in applications where weight is a critical factor. The weight of a motor depends on various factors, including the motor type, construction materials, and power rating. It is crucial to assess the weight-bearing capacity of the system or equipment and choose a motor that is within the acceptable range.
Applications that involve mobile or portable systems, such as robotics, drones, or handheld devices, often prioritize lightweight motors to minimize the overall weight and improve maneuverability. Conversely, in stationary applications where weight is less of a concern, such as industrial machinery or HVAC systems, the motor’s weight may not be as critical.
Consider the impact of motor weight on the overall system performance, balance, stability, and power efficiency. Ensure that the selected motor can be safely supported and integrated into the intended application without compromising its functionality or safety.
Keep in mind that motor size and weight can often be directly influenced by factors such as power rating, motor type, and construction materials. Striking the right balance between size, weight, and performance is crucial to ensure that the motor aligns with your specific application requirements.
Consult the manufacturer’s specifications and documentation for detailed information on the motor’s dimensions and weight. Additionally, consider seeking expert advice or consulting with motor specialists to ensure that the selected motor’s size and weight are appropriate for your application.
Cost Considerations
Cost is an important factor to consider when choosing an electric motor for your application. Understanding the various cost components and trade-offs will help you make an informed decision that balances your budget constraints with the desired performance and quality. Let’s explore the different cost considerations when selecting an electric motor:
Initial Cost
The initial cost of an electric motor includes the price of the motor itself. The factors that influence the initial cost include motor type, power rating, efficiency, and brand reputation. Generally, more specialized motors with higher power ratings and efficiencies tend to have higher initial costs. However, it’s important to consider the overall value the motor provides in terms of performance, durability, and energy savings over its lifespan.
Operating Costs
In addition to the initial cost, it’s crucial to consider the operating costs of the motor over its lifetime. Operating costs include factors such as energy consumption, maintenance, and any necessary accessories or control devices. Energy-efficient motors may have higher initial costs but can result in significant energy savings, leading to lower operating costs in the long run. Additionally, motors with higher reliability and durability may require less frequent maintenance and repairs, reducing ongoing maintenance expenses.
Energy Efficiency
While energy efficiency can impact both initial and operating costs, it is worth highlighting its cost-saving potential. Energy-efficient motors, indicated by higher efficiency ratings, consume less electricity for the same amount of work output. This translates to reduced energy bills and lower environmental impact. Although energy-efficient motors may have slightly higher initial costs, the long-term energy savings often offset the initial investment, making them a more cost-effective choice in the long run.
Motor Lifespan
The expected lifespan of the motor also influences its cost-effectiveness. High-quality motors with reliable construction and superior components tend to have longer lifespans and, therefore, lower replacement and maintenance costs over time. It’s important to consider the warranty offered by the manufacturer, as a longer warranty period often indicates their confidence in the motor’s durability and performance.
Read more: How To Choose The Right Bean Bag Chair Size
Brand and Supplier
The brand and supplier of the motor can affect the cost and reliability of the product. Established brands with a reputable track record may come with higher price tags but offer a higher level of quality, customer support, and after-sales service. It is essential to research various brands, read customer reviews, and consider the supplier’s reputation to ensure you are investing in a reliable motor.
Application Requirements
Finally, consider the specific requirements of your application when assessing the cost of the motor. Determine the necessary power rating, speed, torque, and control features required for your application. Over- or under-specifying the motor for your application can result in unnecessary expenses or compromises in performance. Choose a motor that aligns with your application’s needs to achieve a balance between cost and performance.
When evaluating cost considerations, it’s crucial to take a holistic approach, considering both upfront and long-term costs, energy efficiency, motor lifespan, and the specific requirements of your application. Weighing these factors will help you make a cost-effective decision that meets your budgetary constraints without compromising on performance or reliability.
Motor Control and Compatibility
Motor control and compatibility are important factors to consider when choosing an electric motor for your application. The control options and compatibility with your existing system or equipment will determine how effectively and seamlessly the motor can be integrated and operated. Let’s explore the significance of motor control and compatibility:
Motor Control Options
Motor control refers to the ability to regulate and adjust the motor’s speed, torque, and direction of rotation. Different applications require varying degrees of control, and the motor you choose should align with your specific control needs. Several common motor control options are available:
- On/Off Control: This is the simplest form of control that involves manually turning the motor on or off. It is suitable for applications where basic motor operation is sufficient without the need for speed or torque adjustments.
- Variable Speed Control: Some applications require the ability to adjust the motor’s speed to meet changing requirements. In such cases, variable speed control options such as adjustable drives, inverters, or motor controllers may be needed.
- Forward/Reverse Control: Some applications, such as conveyors or reversible machinery, require motors that can operate in both forward and reverse directions. Forward/reverse control options allow you to easily change the motor’s rotation direction as needed.
- Position Control: For applications that require precise positioning, such as robotics or CNC machines, position control options such as encoders or servo drives may be necessary. These control methods enable accurate control over the motor’s position and movement.
- Remote Control: In certain applications, remote control options are essential for convenience or to ensure operator safety. Wireless or remote control systems allow operators to control the motor from a distance, which can be beneficial in various scenarios.
Compatibility with Existing Systems
When choosing an electric motor, it is important to consider its compatibility with your existing system or equipment. Compatibility relates to the electrical and mechanical specifications required for seamless integration and operation. Consider the following factors:
- Voltage and Current Ratings: Ensure that the motor’s voltage and current ratings match the power supply available in your system or the electrical requirements of your application. Mismatched ratings can result in damage to both the motor and the system.
- Mechanical Fit: Consider the physical dimensions and mounting requirements of the motor to ensure it can be properly installed within the existing system or equipment. Improper fit can lead to installation challenges, strain on the motor, or restrictions on the operation of the application.
- Interface and Communication: If the motor needs to communicate with other devices or systems, such as control panels, PLCs, or computers, ensure that it is compatible with the required interface protocols and communication standards.
- Environmental Compatibility: Consider the environmental conditions in which the motor will operate, including temperature, humidity, dust, or vibration levels. Ensure that the motor is designed to handle these conditions without compromising performance or reliability.
Consult the motor manufacturer’s specifications and technical documentation to verify the control options and compatibility details. If needed, seek the assistance of experts or consult with motor specialists to ensure a seamless integration that meets the control requirements and compatibility needs of your application.
By considering motor control options and ensuring compatibility with your existing systems, you can choose a motor that not only meets your performance requirements but also allows for efficient and effective operation within your specific application.
Maintenance and Lifespan
Maintenance and lifespan are critical factors to consider when selecting an electric motor. Proper maintenance practices can prolong the motor’s lifespan, improve its performance, and minimize unexpected downtime. Understanding the maintenance requirements and expected lifespan of the motor will help you make an informed decision. Let’s explore the significance of maintenance and lifespan:
Maintenance Requirements
Maintenance requirements for electric motors vary based on factors such as motor type, operating conditions, and usage intensity. It is important to understand the manufacturer’s recommended maintenance procedures and frequency to ensure the motor operates optimally. Some common maintenance practices for electric motors include:
- Lubrication: Regularly lubricating the motor’s bearings, gears, or other moving parts helps reduce friction, heat, and wear. Follow the manufacturer’s guidelines for the appropriate lubricant and lubrication schedule.
- Inspection: Perform regular visual inspections to check for signs of damage, loose connections, or abnormal wear. Address any issues promptly to prevent further damage or failure.
- Cleaning: Keep the motor clean and free from dirt, dust, and debris accumulation. Regular cleaning helps maintain efficiency and prevents overheating due to restricted airflow.
- Ventilation: Ensure proper ventilation around the motor to prevent overheating. Clear obstructions and ensure that the motor’s cooling system, if applicable, is functioning effectively.
- Electrical Testing: Periodically perform electrical tests, such as insulation resistance or motor winding resistance measurements, to detect any potential issues and ensure electrical safety.
- Load Monitoring: Monitor the motor’s load conditions to ensure it is not operating beyond its capacity. Operating motors under excessive loads can lead to premature failure.
Motor Lifespan
The lifespan of an electric motor refers to its expected operational lifetime before it requires significant repairs or replacement. The lifespan can vary depending on factors such as motor type, quality, usage intensity, operating conditions, and adherence to maintenance practices. Quality motors from reputable manufacturers typically have longer lifespans due to superior construction and component quality.
It is important to understand the manufacturer’s provided lifespan or expected service life for the motor. This information, along with proper maintenance practices, can help estimate the motor’s useful life and plan for future replacements or repairs. Keep in mind that the lifespan can vary based on factors specific to each application, so consult with the manufacturer or motor specialists for more accurate estimations.
Proactive Maintenance Approach
Adopting a proactive maintenance approach can significantly prolong the motor’s lifespan and prevent unexpected breakdowns. Regular maintenance, inspection, and early detection of any issues can help address problems before they escalate, reducing the risk of motor failure and costly repairs.
Implementing a maintenance schedule and keeping detailed records of maintenance tasks can help track the motor’s performance, address any recurring issues, and ensure timely maintenance activities. Regularly review and update your maintenance practices based on the motor’s performance and any changes in operating conditions.
Additionally, following the manufacturer’s guidelines, seeking professional assistance when needed, and complying with industry standards will help ensure that maintenance activities are performed properly and safely.
By practicing regular maintenance, monitoring the motor’s performance, and promptly addressing any issues, you can extend the lifespan of your electric motor, optimize its performance, and achieve long-term reliability for your application.
Noise and Vibration Levels
Noise and vibration levels are important considerations when selecting an electric motor. Excessive noise and vibration can impact the comfort and safety of occupants, as well as the performance and longevity of the motor and surrounding equipment. Understanding the noise and vibration characteristics of a motor will help you choose a motor that meets the acoustic requirements of your application. Let’s explore the significance of noise and vibration levels:
Noise Levels
Noise levels are measured in decibels (dB) and indicate the intensity or loudness of sound. Excessive noise from motors can be disruptive, affect communication, and contribute to workplace fatigue or discomfort. Some key factors that influence motor noise levels include:
- Mechanical Construction: The design and construction of the motor, including the materials used and housing design, can impact noise levels. Motors with noise-reducing features, such as sound-dampening insulation or vibration isolation mounts, help minimize noise transmission.
- Operating Speed: Higher rotational speeds can lead to increased noise levels due to the higher frequency of sound produced. Selecting a motor that operates at an appropriate speed for your application can help control noise levels.
- Bearing Quality: High-quality bearings can reduce friction and minimize noise generation. Motors equipped with quality bearings tend to operate more quietly and reliably.
- Maintenance: Regular maintenance practices, such as proper lubrication and regular inspections, can help ensure optimal motor performance and reduce noise levels caused by mechanical wear or misalignment.
It is important to consider the permissible noise levels for your specific application, especially in noise-sensitive environments such as residential areas, hospitals, offices, or recording studios. Check the manufacturer’s specifications and seek motors that meet the required noise standards and regulations.
Vibration Levels
Vibration levels refer to the amount of oscillation or movement exhibited by the motor during operation. Excessive vibration can negatively impact the motor’s performance, cause premature wear and fatigue on components, and affect the surrounding equipment or structural integrity of the system. Key factors influencing motor vibration levels include:
- Motor Balance: Properly balanced rotors and other rotating parts minimize vibration. Imbalances in the motor’s rotating components can cause uneven forces and lead to increased vibration levels.
- Mechanical Alignment: Accurate mechanical alignment of the motor and connected equipment reduces vibration caused by misalignment. Proper alignment ensures smooth operation and minimizes unnecessary stress on motor components.
- Bearing Quality: High-quality bearings facilitate smooth operation and minimize vibration. Bearings with reduced friction and improved damping capabilities can help reduce vibration levels.
- Mounting and Fixing: Proper mounting and fixing of the motor using vibration-damping materials or mounts can help isolate vibrations and minimize their transmission to the surrounding structure.
Consider the acceptable vibration levels for your application, especially if it involves delicate equipment, precision processes, or sensitive operations. Consult the manufacturer’s specifications for vibration limits and select motors that meet the required vibration standards.
Testing and Monitoring
To ensure that the chosen motor operates within acceptable noise and vibration levels, it is advisable to perform initial testing and ongoing monitoring. Testing and monitoring procedures may include sound level measurements, vibration analysis, or visual inspections. Regular monitoring enables proactive identification of any increase in noise or vibration levels, prompt detection of potential issues, and timely corrective actions to prevent damage or failure.
Consider engaging with experts, such as acoustic engineers or vibration specialists, to analyze and address noise and vibration concerns specific to your application. They can provide valuable insights and recommendations for noise and vibration control measures, including the selection of appropriate motors or the use of additional noise or vibration mitigation techniques.
By considering noise and vibration levels, selecting motors that meet the required standards, and implementing appropriate control measures, you can ensure a safe, comfortable, and reliable working environment while minimizing the impact on surrounding systems or equipment.
Environmental Considerations
Environmental considerations are crucial when choosing an electric motor as they impact sustainability, energy efficiency, and compliance with environmental regulations. By selecting a motor that aligns with environmental goals, you can reduce your carbon footprint and contribute to a more sustainable future. Let’s explore the significance of environmental considerations when selecting an electric motor:
Energy Efficiency
Energy efficiency is a key environmental consideration as it directly affects energy consumption, greenhouse gas emissions, and overall environmental impact. Energy-efficient motors, indicated by higher efficiency ratings, convert a greater portion of the electrical input into useful mechanical work, reducing energy wastage. By selecting an energy-efficient motor, you can minimize energy consumption and the associated environmental footprint. Look for motors with high efficiency ratings and certifications from organizations such as ENERGY STAR or International Electrotechnical Commission (IEC) to ensure optimal energy performance.
Compliance with Regulations
When choosing an electric motor, it is essential to consider compliance with environmental regulations and standards. These regulations may include requirements for energy efficiency, noise emissions, or hazardous substances. Familiarize yourself with relevant regulations such as the International Electrotechnical Commission (IEC) standards, European Union’s Eco-Design Directive, or local environmental regulations to ensure that the motor meets the necessary compliance criteria. Compliance not only ensures adherence to legal requirements but also contributes to sustainable practices and the reduction of harmful environmental impacts.
Materials and Recycling
The materials used in the construction of the motor can have environmental implications. Consider motors that use eco-friendly or recyclable materials to promote sustainable practices. Additionally, evaluate the motor’s end-of-life disposal options and recyclability. Motors that can be easily disassembled and recycled help minimize waste and contribute to a circular economy. Look for manufacturers or programs that offer motor take-back or recycling initiatives to ensure responsible handling and disposal at the end of the motor’s lifespan.
Noise and Emissions Reduction
Noise pollution and harmful emissions can have negative impacts on the environment and human health. Selecting motors that operate quietly helps reduce noise pollution, improving the quality of life in residential areas, workplaces, or public spaces. Motors that produce minimal emissions or meet stringent emissions standards contribute to air quality preservation. This is especially relevant in applications such as electric vehicles or indoor environments where emissions from combustion engines can be a concern. Consider motors that are designed to minimize noise and emissions for a more environmentally friendly operation.
Environmental Management Systems
Manufacturers that implement Environmental Management Systems (EMS), such as ISO 14001 certification, demonstrate their commitment to sustainable practices. Consider motors from manufacturers with established EMS, as they are more likely to prioritize environmental responsibility and sustainable manufacturing processes. Manufacturers with clear environmental policies and initiatives not only highlight their commitment to reducing environmental impact but also ensure continuous improvement in environmental performance.
By taking environmental considerations into account when selecting an electric motor, you can play a vital role in promoting sustainability and furthering environmental goals. Choosing energy-efficient motors, complying with regulations, considering materials and recycling options, reducing noise and emissions, and supporting manufacturers with strong environmental management practices are all steps towards a greener and more sustainable future.
Conclusion
Choosing the right electric motor is a crucial step in ensuring optimal performance, energy efficiency, and longevity for your application. By considering the various factors discussed in this article, including power requirements, speed and torque, motor types, efficiency, size and weight, cost, control options, maintenance, noise and vibration levels, and environmental considerations, you can make an informed decision that aligns with your specific needs and goals.
Understanding the power requirements and selecting a motor that can handle the voltage, current, and power output necessary for your application is essential. You should also consider the desired speed and torque requirements to ensure that the motor can meet the workload demands effectively.
Exploring the different types of electric motors, such as DC motors and AC motors, brushed motors, and brushless motors, allows you to assess their advantages and disadvantages and choose the most suitable option for your application. Evaluating the motor’s efficiency, size, weight, and cost considerations helps you find the right balance between performance and budget constraints.
Motor control options and compatibility with existing systems play a significant role in the seamless integration and operation of the motor. Understanding and adhering to maintenance requirements can extend the motor’s lifespan, reduce downtime, and prevent unexpected failures.
Considering noise and vibration levels ensures a comfortable and safe working environment while protecting surrounding equipment and structures. Environmental considerations, including energy efficiency, compliance with regulations, recyclability, and emissions reduction, contribute to sustainability and environmental responsibility.
In conclusion, by carefully considering these factors, you can select an electric motor that meets your specific requirements, performs optimally, reduces energy consumption, complies with regulations, and aligns with environmental goals. Whether your application involves robotics, industrial machinery, HVAC systems, or consumer electronics, choosing the right electric motor sets the foundation for success and efficiency in your operations.
Remember, when in doubt, consult with motor specialists or manufacturers who can provide expert guidance tailored to your unique needs. With the right electric motor, you can power your vision and propel your application forward.
Frequently Asked Questions about How To Choose The Right Electric Motor
Was this page helpful?
At Storables.com, we guarantee accurate and reliable information. Our content, validated by Expert Board Contributors, is crafted following stringent Editorial Policies. We're committed to providing you with well-researched, expert-backed insights for all your informational needs.
0 thoughts on “How To Choose The Right Electric Motor”