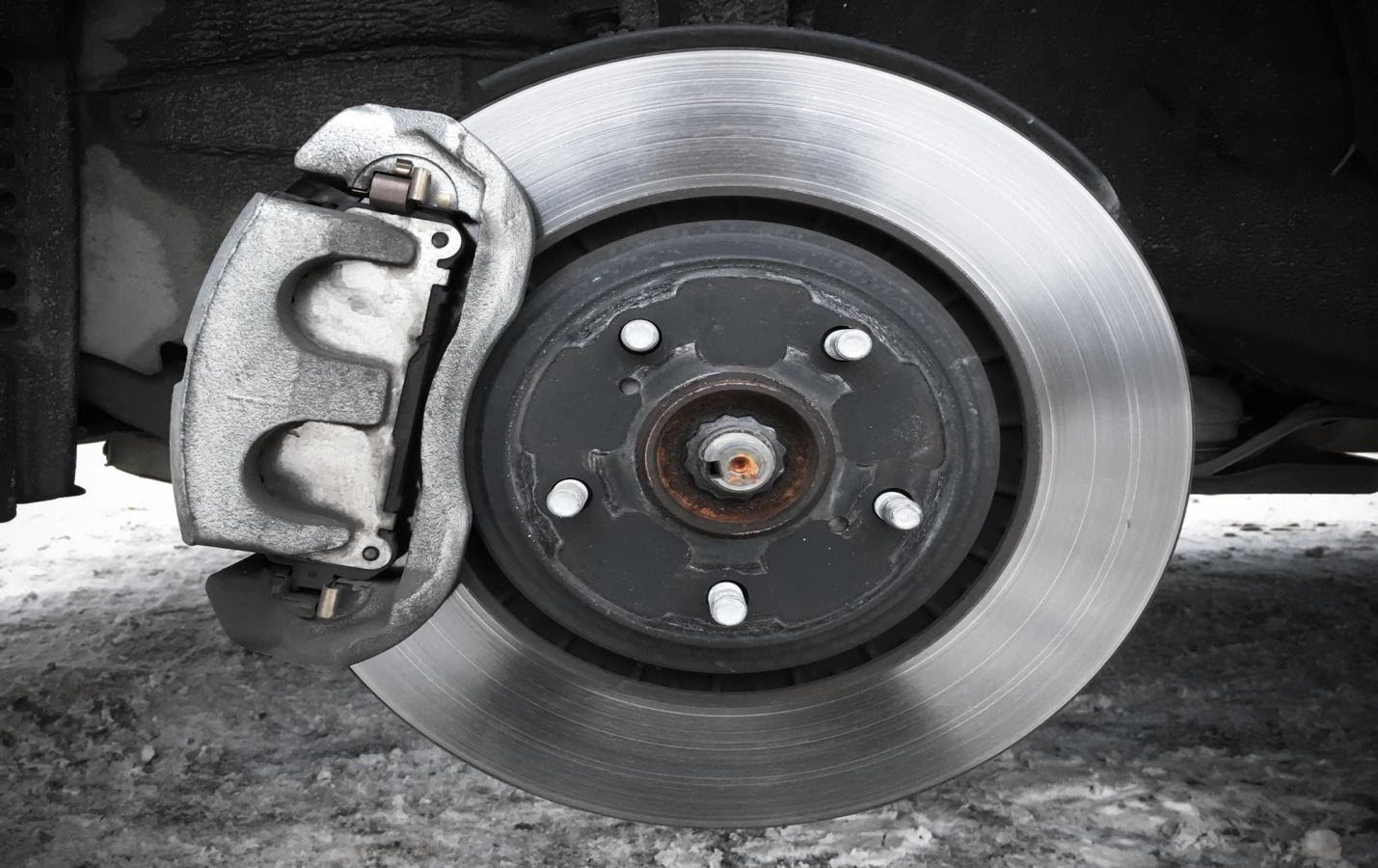
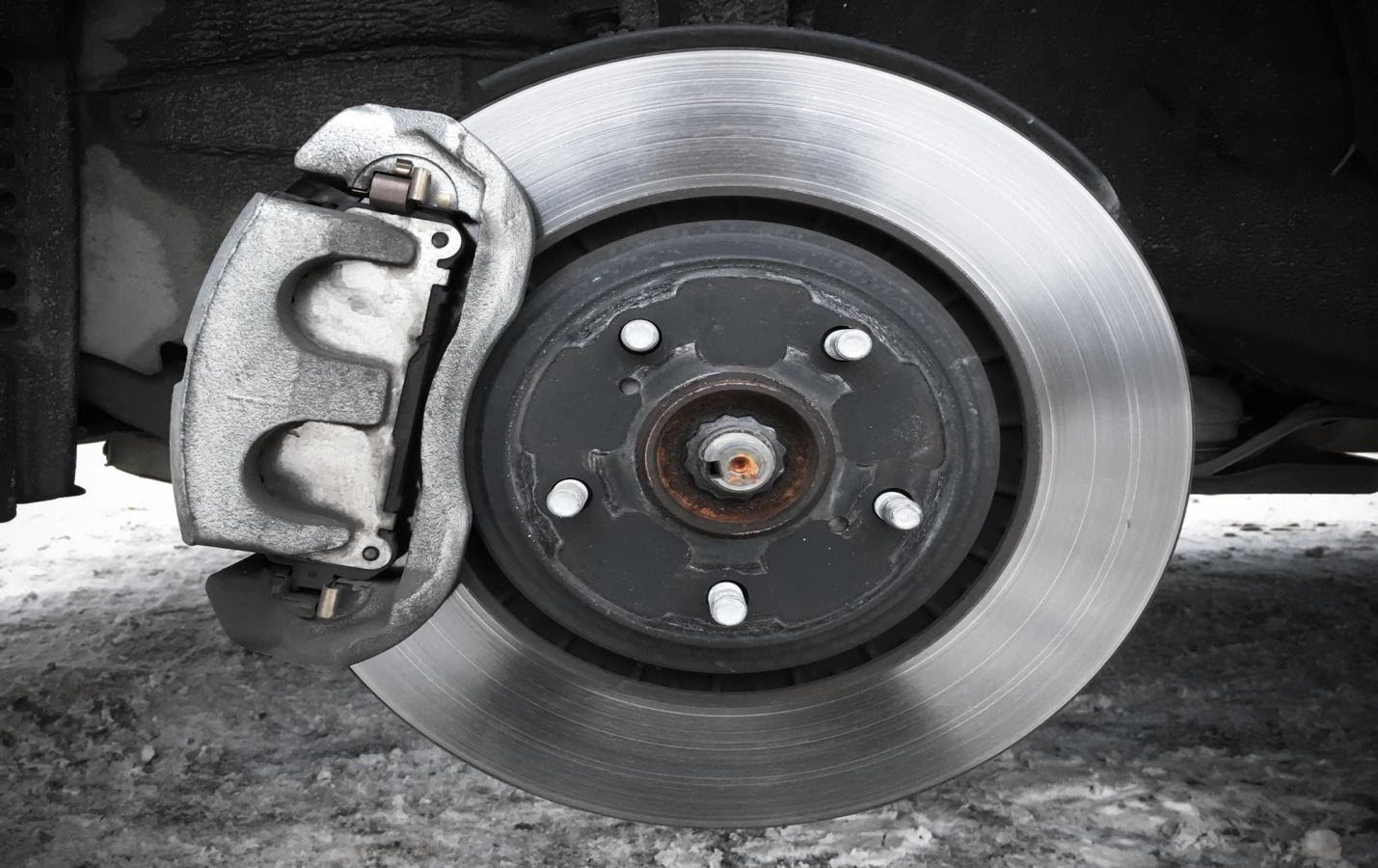
Articles
How Does Electric Motor Brake Work
Modified: December 7, 2023
Discover how electric motor brakes work in this informative article. Explore the principles and components behind this essential feature for various applications.
(Many of the links in this article redirect to a specific reviewed product. Your purchase of these products through affiliate links helps to generate commission for Storables.com, at no extra cost. Learn more)
Introduction
The electric motor brake is a vital component in various industrial and automotive applications. It plays a crucial role in controlling the speed and motion of electric motors, ensuring safety and efficiency in different operating conditions. Understanding the principles and workings of electric motor brakes is essential for engineers, technicians, and anyone involved in motor control systems. In this article, we will explore the fundamental concepts behind electric motor brakes, the different types available, their working mechanisms, advantages, applications, and some considerations to keep in mind.
Key Takeaways:
- Electric motor brakes operate on the principle of electromagnetic induction, generating a braking force to control motor speed and stopping power, contributing to safety and efficiency in various applications.
- Understanding the principles, types, and working mechanisms of electric motor brakes is crucial for engineers and technicians, empowering them to make informed decisions in selecting, installing, and maintaining these essential components.
Read more: How Does A Electric Motor Work
Principle of Electric Motor Brakes
Electric motor brakes operate based on the principle of electromagnetic induction. When an electric current flows through a conductor, it generates a magnetic field around it. This magnetic field interacts with another magnetic field, causing a force that opposes the motion of the conductor. This force is known as electromagnetic braking, and it is used to slow down or stop the rotation of the motor shaft.
The braking mechanism generally consists of an electromagnet and a rotor. The electromagnet is energized by an electrical power source, creating a magnetic field. When the electrical power is supplied to the electromagnet, it attracts the rotor present in the motor assembly. This attraction produces a braking torque, which acts opposite to the direction of the rotor’s rotation, resulting in deceleration or complete braking of the motor shaft.
The amount of braking torque generated can be controlled by varying the electrical current supplied to the electromagnet. By adjusting the current, the strength of the magnetic field is altered, affecting the braking force. This allows for precise control over the motor’s speed and stopping power.
The principle of electric motor brakes is closely related to the concept of regenerative braking. In regenerative braking systems, the kinetic energy of the motor and connected load is converted into electrical energy and fed back into the power supply. This energy can be reused, contributing to energy efficiency and reducing the overall power consumption of the system.
Types of Electric Motor Brakes
There are several types of electric motor brakes, each designed for specific applications and operating conditions. Let’s explore some of the common types:
- Electromagnetic Brakes: Electromagnetic brakes use an electromagnet to generate the braking force. When the power supply is disconnected, the brake engages, exerting a braking torque on the motor shaft. These brakes are commonly found in industrial machinery and vehicles.
- Failsafe Brakes: Failsafe brakes are designed to engage automatically when there is a power loss or failure. They provide an added layer of safety, ensuring that the motor stops in critical situations. These brakes are commonly used in elevators, cranes, and other equipment where safety is a top priority.
- Eddy Current Brakes: Eddy current brakes use the principle of eddy currents to generate braking force. They work by inducing a magnetic field in a conductive disc or drum attached to the motor shaft. This induced current creates an opposing magnetic field, generating a braking force that slows down the motor. Eddy current brakes are commonly used in high-speed trains, roller coasters, and other applications that require precise control over braking force.
- Disk Brakes: Disk brakes consist of a stationary stator and a rotating disk. When the brake is engaged, the stator applies pressure on the disk, generating a frictional force that slows down the motor. Disk brakes are widely used in automotive applications, such as cars and motorcycles.
- Drum Brakes: Drum brakes consist of a stationary stator and a rotating drum. Similar to disk brakes, when the brake is applied, the stator presses against the drum, creating a frictional force that decelerates the motor. Drum brakes are commonly used in heavy-duty applications, such as trucks and cranes.
These are just a few examples of the types of electric motor brakes available in the market. The selection of the appropriate brake depends on factors such as the motor’s power rating, operating environment, required braking torque, and precision control requirements.
Working of Electric Motor Brakes
The working of electric motor brakes can vary depending on the type of brake used. However, the basic principle remains the same: generating a braking force to slow down or stop the motor shaft. Let’s explore a general working mechanism for electric motor brakes:
- Engagement: When the brake is activated, an electrical signal is sent to the brake assembly, energizing the electromagnet or initiating the braking mechanism.
- Generation of Magnetic Field: The energized electromagnet creates a magnetic field. The strength of this magnetic field can be adjusted by varying the current supplied to the electromagnet.
- Braking Force: The generated magnetic field interacts with the rotor or a conductive disc/drum attached to the motor shaft. This interaction creates a braking force that acts opposite to the direction of rotation, resulting in deceleration or complete braking of the motor shaft.
- Control and Release: The amount of braking force can be controlled by adjusting the current supplied to the electromagnet. This allows for precise control over the motor’s speed and stopping power. When the brake is disengaged, the electrical power to the brake assembly is cut off, releasing the rotor or disc/drum and allowing the motor to rotate freely.
It is important to note that the working mechanism can differ for specific types of electric motor brakes. For example, eddy current brakes rely on the induction of eddy currents in a conductive disc/drum, which creates an opposing magnetic field and generates braking force. Similarly, disk brakes and drum brakes utilize frictional force between the stator and the rotating element to slow down or stop the motor.
The working efficiency and effectiveness of electric motor brakes depend on factors such as the quality of components, proper maintenance, and appropriate sizing for the application. It is crucial to follow manufacturer guidelines and industry best practices to ensure optimal performance and safety.
When an electric motor brake is engaged, it creates a magnetic field that opposes the rotation of the motor, slowing it down and bringing it to a stop. This is achieved by applying a current to the motor windings in a way that creates resistance to the motor’s movement.
Advantages and Applications
Electric motor brakes offer several advantages and find applications in a wide range of industries and systems. Let’s explore some of the key advantages and popular applications of electric motor brakes:
Advantages:
- Precise Control: Electric motor brakes provide precise control over the speed and stopping of the motor. The ability to adjust the braking force allows for fine-tuning of the motor’s performance and enhances overall system efficiency and productivity.
- Quick Response: Electric motor brakes can respond quickly to commands, allowing for rapid stopping or deceleration of the motor. This is particularly beneficial in applications where safety is a concern, as it reduces the risk of accidents or equipment damage.
- Energy Efficiency: Some types of electric motor brakes, such as regenerative brakes, can convert the kinetic energy of the motor into electrical energy, which can be fed back into the power supply. This helps in reducing energy consumption and optimizing the system’s overall efficiency.
- Durability: Electric motor brakes are designed to withstand high levels of mechanical stress and wear. They are built to be durable and reliable, ensuring long-term operation in demanding industrial environments.
- Flexibility: Electric motor brakes can be applied to a wide range of motors and systems, making them versatile in various applications. They can be integrated into different motor control systems with relative ease.
Applications:
– Industrial Machinery: Electric motor brakes are widely used in industrial machinery such as conveyors, cranes, hoists, machine tools, and elevators. They provide precise control over motor speed and stopping, ensuring safe and efficient operation in manufacturing and material handling processes.
– Automotive Industry: Electric motor brakes are utilized in automotive applications, including cars, motorcycles, and electric vehicles. They assist in controlling vehicle acceleration, deceleration, and stabilization, contributing to improved road safety and enhanced driving performance.
– Railway Systems: Electric motor brakes, especially regenerative brakes, are commonly employed in railway systems like trains, trams, and metro systems. The ability to convert kinetic energy into electrical energy helps in reducing power consumption and increasing the overall efficiency of these transportation systems.
– Robotics: Electric motor brakes play a crucial role in robotics, providing precise control over the movement and stopping of robotic arms, joints, and grippers. This ensures accurate positioning and increases the safety and efficiency of robotic operations.
– Renewable Energy Systems: Electric motor brakes are used in renewable energy systems such as wind turbines and hydroelectric generators. They assist in controlling the speed and stopping of the turbine or generator, enabling optimal power generation and system stability.
These are just a few examples of the many applications where electric motor brakes are utilized. Their versatility and advantages make them essential components in various industries and systems, contributing to enhanced performance, safety, and energy efficiency.
Read more: How Does A Dc Electric Motor Work
Challenges and Considerations
While electric motor brakes offer numerous benefits, there are also some challenges and considerations to keep in mind when utilizing them in different applications. Understanding these factors is crucial for ensuring the optimal performance and longevity of the motor brake system. Let’s explore some of these challenges and considerations:
Heat Dissipation:
During braking, electric motor brakes generate heat due to friction or electrical resistance. Adequate heat dissipation is essential to prevent overheating and subsequent damage to the brake components. Proper ventilation and cooling mechanisms should be in place to maintain the temperature within safe limits.
Maintenance and Inspection:
Regular maintenance and inspections are necessary to keep the electric motor brake system working effectively. This includes checking for signs of wear, lubricating moving parts, and ensuring proper alignment. Regular inspection helps identify any potential issues early on and allows for timely repairs or replacements.
Compatibility and Sizing:
When selecting an electric motor brake, it is crucial to ensure compatibility with the motor and its control system. The brake should be appropriately sized to handle the braking torque required for the specific application. Improper sizing can lead to inadequate brake performance or even damage to the motor and brake system.
Environmental Conditions:
The operating environment can impact the performance and lifespan of electric motor brakes. Factors such as temperature extremes, humidity, dust, and chemicals can affect the functioning and durability of the brake system. Special enclosures or protective measures may be required to safeguard the brake components in harsh environments.
Emergency Braking:
In applications where rapid and emergency braking is crucial, it is essential to ensure that the electric motor brake can handle the required stopping torque and respond quickly. Fail-safe brake systems that engage automatically during power loss or failure can provide an additional layer of safety in such situations.
Cost Considerations:
Electric motor brakes can vary in cost depending on their type and features. It’s important to consider the budgetary constraints of a project while selecting the appropriate brake. However, it is also essential to prioritize quality and reliability to ensure long-term performance and avoid potential operational issues.
By considering these challenges and factors, engineers and system designers can make informed decisions when selecting, installing, and maintaining electric motor brakes. Addressing these considerations helps optimize the performance and reliability of the motor brake system, contributing to safe and efficient operation in various applications.
Conclusion
Electric motor brakes are essential components in a wide range of industrial and automotive applications. With their ability to control the speed and stopping of electric motors, they ensure safe and efficient operation in various operating conditions. Understanding the principles behind electric motor brakes, the different types available, and their working mechanisms is vital for engineers and technicians involved in motor control systems.
The principle of electromagnetic induction forms the foundation for electric motor brakes, generating a braking force that opposes the rotation of the motor shaft. Different types of electric motor brakes, such as electromagnetic brakes, eddy current brakes, disk brakes, and drum brakes, offer specific features and advantages suited for different applications.
The working mechanism of electric motor brakes involves engaging the brake, generating a magnetic field, generating a braking force, and controlling and releasing the brake as required. The benefits of electric motor brakes include precise control, quick response, energy efficiency, durability, and flexibility in various applications.
However, there are also challenges and considerations to keep in mind when utilizing electric motor brakes. Addressing factors such as heat dissipation, maintenance, compatibility, environmental conditions, emergency braking, and cost considerations is crucial for optimizing performance and ensuring the longevity of the brake system.
In conclusion, electric motor brakes play a crucial role in motor control systems, providing precise control, safety, and efficiency. Understanding the principles, types, working mechanisms, and associated challenges of electric motor brakes empowers engineers to make informed decisions in selecting, installing, and maintaining these essential components. By doing so, they can ensure the reliable and effective operation of electric motor brakes in various industrial and automotive applications.
Frequently Asked Questions about How Does Electric Motor Brake Work
Was this page helpful?
At Storables.com, we guarantee accurate and reliable information. Our content, validated by Expert Board Contributors, is crafted following stringent Editorial Policies. We're committed to providing you with well-researched, expert-backed insights for all your informational needs.
0 thoughts on “How Does Electric Motor Brake Work”