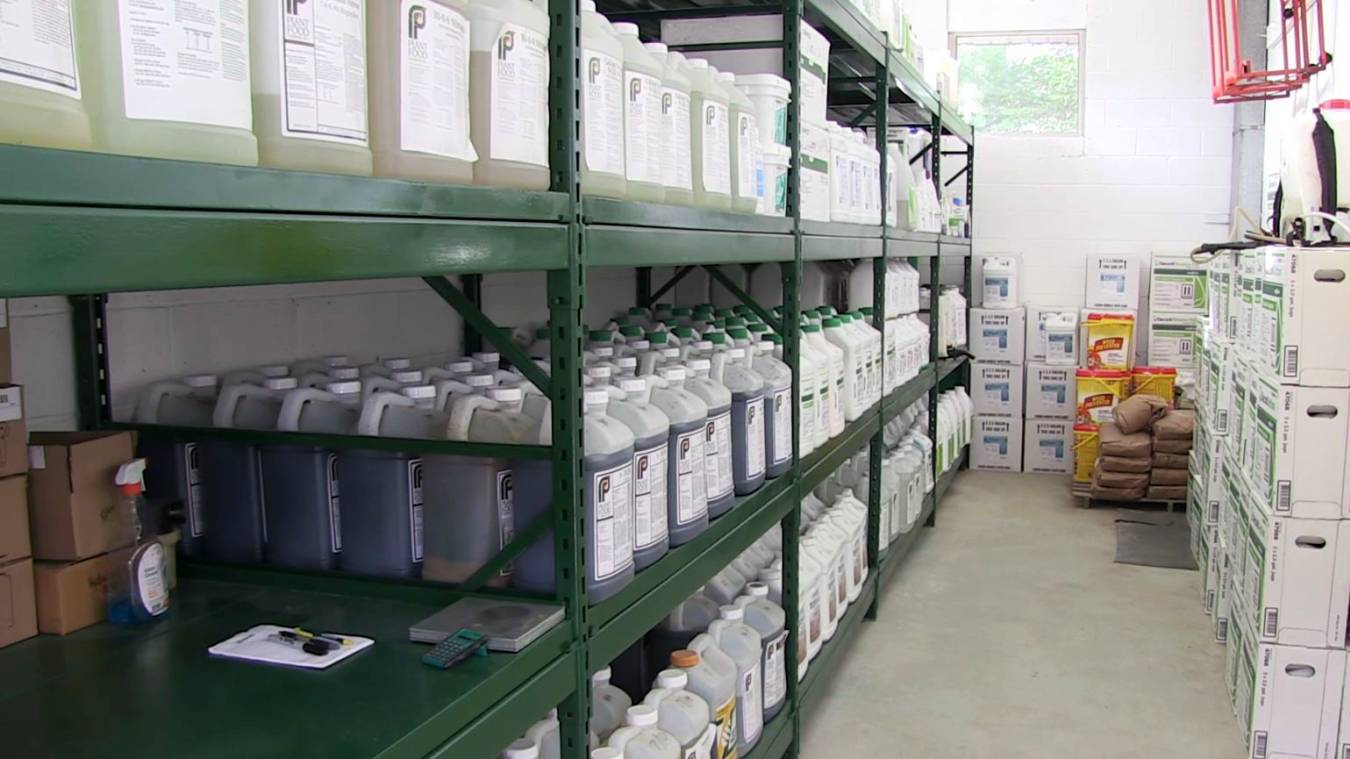
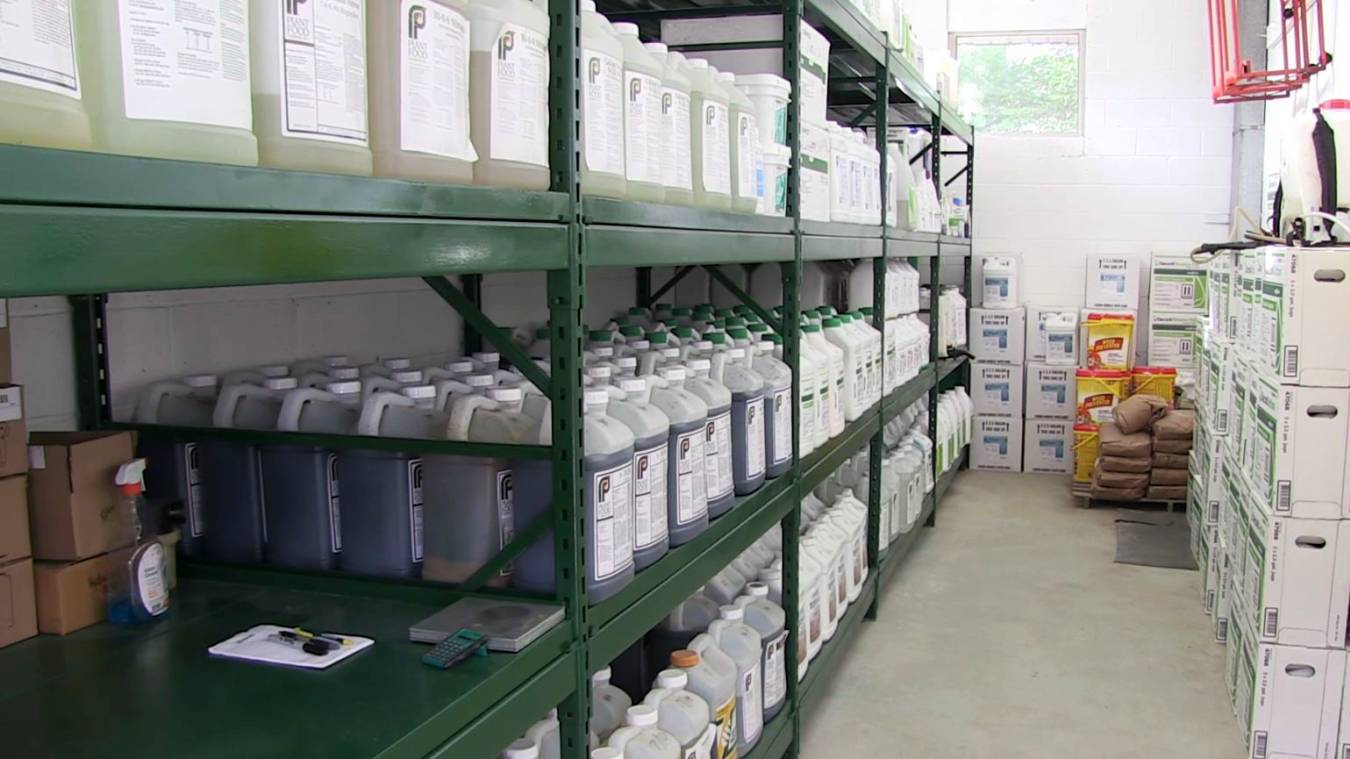
Articles
What Is The Requirement For Storing Chemicals
Modified: August 28, 2024
Looking for storage ideas for storing chemicals? Discover the requirements and best practices to ensure safe and efficient chemical storage.
(Many of the links in this article redirect to a specific reviewed product. Your purchase of these products through affiliate links helps to generate commission for Storables.com, at no extra cost. Learn more)
Introduction
Proper storage of chemicals is of paramount importance in various industries and sectors. Whether it’s manufacturing, laboratory research, or industrial operations, storing chemicals safely not only protects employees and the environment, but also ensures compliance with legal and regulatory requirements. In this article, we will delve into the key requirements for storing chemicals and explore the best practices for maintaining a safe and secure storage environment.
The significance of proper chemical storage cannot be understated. Chemicals, in their different forms and compositions, possess inherent hazards that can pose risks to human health and the environment if not appropriately managed. From corrosive liquids to flammable gases, chemicals need to be stored in a controlled manner to prevent accidents, leaks, spills, and other dangerous scenarios.
Moreover, maintaining proper chemical storage conditions is a legal obligation for businesses. Regulatory agencies, such as the Occupational Safety and Health Administration (OSHA) in the United States, have established guidelines and standards to ensure the safe handling and storage of chemicals. Failure to comply with these regulations can result in hefty fines, legal disputes, and reputational damage.
By adhering to the requirements outlined by regulatory bodies and implementing industry best practices, businesses can mitigate the potential risks associated with chemical storage. This not only safeguards the well-being of employees but also minimizes the environmental impact of mishandling or improperly storing hazardous substances.
In the following sections, we will outline the specific requirements necessary for safe chemical storage, covering aspects such as facility and infrastructure conditions, suitable storage containers, segregation and compatibility, ventilation, fire safety measures, labeling and documentation, personnel training, and emergency response protocols. By following these guidelines, businesses can ensure that chemical storage is conducted in a manner that protects both personnel and the surrounding environment.
Key Takeaways:
- Proper chemical storage is crucial for protecting employees, preventing environmental contamination, and ensuring compliance with legal and regulatory requirements. It involves facility conditions, suitable containers, segregation, labeling, and personnel training.
- Adhering to best practices for chemical storage, including proper ventilation, segregation, labeling, and emergency response, creates a safe and compliant environment. This safeguards employees, minimizes environmental impact, and ensures regulatory compliance.
Read more: What Zoning Is Required For A Restaurant
Importance of Proper Chemical Storage
Proper chemical storage is crucial for a multitude of reasons, including protecting the health and safety of employees, preventing environmental contamination, and ensuring regulatory compliance. Let’s explore the significance of each of these aspects.
First and foremost, the well-being of employees should be a top priority for any organization. Improperly stored chemicals can lead to accidents, injuries, and even fatalities. Exposure to toxic substances, fires, or explosions can occur if chemicals are not stored and handled correctly. By implementing proper storage practices, such as using appropriate containers, segregating incompatible substances, and providing adequate ventilation, the risk of accidents and health hazards can be significantly reduced.
Secondly, proper chemical storage is essential for environmental protection. Chemical spills or leaks can contaminate soil, groundwater, and nearby water bodies, causing long-lasting damage to ecosystems. This not only has a detrimental impact on flora and fauna but also jeopardizes the availability of clean drinking water. By ensuring that chemicals are stored securely and using spill containment measures, organizations can prevent environmental disasters and limit their ecological footprint.
Moreover, adhering to legal and regulatory requirements is imperative for any business handling and storing chemicals. Government agencies enforce various rules and regulations to safeguard workers’ rights and protect the environment. By following these guidelines, organizations demonstrate their commitment to compliance and avoid potential legal repercussions, including hefty fines, penalties, and possible shutdowns.
Proper chemical storage also enhances overall operational efficiency. By implementing organized storage systems and clearly labeling containers, employees can easily locate and access chemicals when needed. This saves time and prevents unnecessary delays in work processes, leading to increased productivity and reduced downtime.
Additionally, maintaining proper storage conditions prolongs the shelf life and functionality of chemicals. Some substances are sensitive to temperature, humidity, or light, and storing them incorrectly can result in degradation or loss of efficacy. By ensuring that chemicals are stored in the optimal conditions prescribed by the manufacturer, organizations can maximize their investment in these materials and avoid unnecessary wastage.
In summary, proper chemical storage is vital for protecting the health and safety of employees, preventing environmental contamination, ensuring regulatory compliance, enhancing operational efficiency, and maximizing the lifespan of chemicals. By prioritizing these aspects and implementing best practices, organizations can create a safe and sustainable environment for managing and storing chemicals.
Legal and Regulatory Requirements
When it comes to storing chemicals, businesses must adhere to strict legal and regulatory requirements to ensure the safety of their employees and the surrounding environment. These regulations are put in place by government agencies to mitigate potential hazards and prevent accidents. Let’s explore some of the key legal and regulatory requirements for chemical storage.
One of the primary regulatory bodies in the United States is the Occupational Safety and Health Administration (OSHA). OSHA has established specific standards, known as the Hazard Communication Standard (HCS), which mandate how chemicals should be labeled, categorized, and stored. These standards require businesses to provide employees with information about the hazards associated with chemicals, as well as proper handling and storage procedures.
Under the HCS, businesses are required to maintain Safety Data Sheets (SDS) for each chemical they store. SDS provides detailed information about the chemical’s properties, hazards, and safety precautions. It is crucial that SDS is readily accessible to employees and updated regularly to reflect any changes in the chemical’s composition or handling guidelines.
In addition to OSHA, other government agencies and regulatory bodies may have specific requirements for chemical storage. For example, in the transportation industry, the Department of Transportation (DOT) has established regulations for the safe transportation and storage of hazardous substances. These regulations outline guidelines for proper packaging, labeling, and documentation when transporting chemicals.
Moreover, depending on the nature of the business or industry, there may be additional regulations to comply with. For instance, healthcare facilities may need to adhere to standards set by the Joint Commission or state health departments. Laboratories may have to follow guidelines provided by organizations such as the National Fire Protection Association (NFPA) or the Centers for Disease Control and Prevention (CDC).
It is important for businesses to stay updated with the latest regulations and ensure compliance. This can be done through regular training sessions and communication with regulatory agencies. Non-compliance with these regulations can lead to severe consequences, including fines, legal actions, and reputational damage.
In summary, businesses must familiarize themselves with the legal and regulatory requirements for chemical storage. Agencies like OSHA and DOT have established guidelines to ensure the safe handling, storage, and transportation of hazardous substances. It is crucial to maintain accurate documentation, provide adequate training to employees, and stay informed about any changes in regulations. By following these requirements, businesses can create a safe and compliant environment for chemical storage.
Facility and Infrastructure Conditions
The condition of the facility and its infrastructure plays a crucial role in ensuring safe and compliant chemical storage. The design, construction, and maintenance of the storage area must meet specific requirements to prevent accidents, leaks, and spills. Let’s explore the key factors related to facility and infrastructure conditions for chemical storage.
Firstly, the storage area should be well-ventilated to prevent the buildup of harmful fumes or gases. Proper ventilation helps dissipate any vapors that may be released from the chemicals, reducing the risk of inhalation or fire hazards. Ventilation systems should be regularly inspected and maintained to ensure their effectiveness.
In addition, the facility should have appropriate temperature and humidity controls. Some chemicals are sensitive to extreme temperatures or high levels of humidity, which can affect their stability and potency. It is essential to store chemicals within the recommended temperature and humidity range specified by the manufacturer to maintain their integrity.
The structural integrity of the storage area is also crucial. The flooring and walls should be designed to contain any accidental spills or leaks. Impermeable materials, such as sealed concrete or chemical-resistant coatings, are commonly used to prevent the seepage of chemicals into the environment.
Storage facilities should have adequate lighting to ensure proper visibility and prevent accidents. Well-lit areas help employees in reading labels, locating chemicals, and safely handling them. Emergency exits and pathways should also be well-lit and clearly marked for easy evacuation.
Another important aspect is the availability of appropriate storage equipment and shelving. The storage containers used should be compatible with the chemicals being stored and capable of withstanding the substances’ properties. Shelving systems should be sturdy and secure to prevent accidental tip-overs or collapse. Proper organization and segregation of chemicals on the shelves help minimize the risk of cross-contamination.
Equipment for handling and dispensing chemicals, such as pumps or pipettes, should be well-maintained and regularly inspected for safety. Leakage prevention measures, such as drip pans or containment trays, should be in place to capture any spills or leaks that may occur during handling or storage.
Regular inspections and maintenance of facility infrastructure are essential to identify and address any structural defects or potential hazards. This includes checking for signs of corrosion, cracks, or deterioration in storage containers, pipes, or valves. Any damaged or malfunctioning equipment should be repaired or replaced promptly.
In summary, the facility and infrastructure conditions are critical factors in ensuring safe and compliant chemical storage. Proper ventilation, temperature controls, suitable storage equipment, well-maintained infrastructure, and adequate lighting are all important considerations. Regular inspections, maintenance, and adherence to best practices help create a secure environment for storing chemicals and mitigating potential risks.
Suitable Storage Containers
The choice of suitable storage containers is essential for the safe and secure storage of chemicals. Different chemicals have unique properties and hazards, requiring specific types of containers to prevent leaks, spills, and interactions. Let’s explore the key considerations when selecting storage containers for chemicals.
The first consideration is the compatibility between the chemical and the container material. Chemicals can react with certain materials, leading to container failure, contamination, or even hazardous reactions. It is crucial to consult the Safety Data Sheets (SDS) or chemical manufacturer’s guidance to determine the appropriate container material for each chemical. Common container materials include high-density polyethylene (HDPE), stainless steel, glass, and polypropylene.
The size of the container is another important consideration. It should be sufficiently large to accommodate the amount of chemical being stored without risking overfilling or overflow. Overfilling containers can lead to spills and compromise the integrity of the container. It is best to leave some headspace to allow for expansion if the chemical is volatile or subject to temperature changes.
Storage containers should have a secure and tight-fitting lid or closure mechanism to prevent accidental spills or leaks. The closure should be resistant to the chemicals being stored and should provide an airtight seal to prevent vapors from escaping. Containers with built-in safety features such as pressure relief valves or venting systems are recommended for certain chemicals that may generate pressure or release gases.
Labels and markings on storage containers are crucial for proper identification and communication. Containers should be labeled with the chemical name, concentration, hazards, handling instructions, and any other relevant information. Clear and legible labels help employees in identifying chemicals and handling them safely. Additionally, it is important to clearly mark containers with any necessary safety symbols or pictograms according to regulatory requirements.
When storing multiple chemicals, segregation and separation are imperative. Different chemicals may have incompatible properties that can lead to hazardous reactions if they come into contact with one another. Grouping chemicals based on their compatibility and storing them separately helps prevent accidental mixing and reduces the risk of chemical reactions. Proper storage cabinets or racks with individual compartments can aid in segregation and organization.
Regular inspections of storage containers are essential to identify any signs of deterioration, damage, or leaks. Containers that show signs of wear, corrosion, or weakened integrity should be promptly replaced to prevent accidents or spills. It is crucial to have a system in place for routine container maintenance and replacement to ensure the ongoing safety of chemical storage.
In summary, selecting suitable storage containers is crucial for the safe storage of chemicals. Considering compatibility, size, lids/closures, labeling, segregation, and regular inspections are key factors when choosing containers. By using appropriate containers and adhering to best practices, businesses can maintain a secure storage environment and minimize the risk of chemical spills, leaks, or reactions.
Read more: What Education Is Required For Construction
Segregation and Compatibility
Segregation and compatibility are critical aspects of proper chemical storage, ensuring the safety and integrity of stored substances. Chemicals must be stored in a way that minimizes the risk of accidental reactions or contamination. Let’s explore the key considerations for segregating chemicals and ensuring compatibility in storage.
Segregation involves separating chemicals based on their incompatibilities to prevent accidental mixing and reactions. Certain chemicals can react violently or produce hazardous byproducts when combined, leading to explosions, fires, or toxic gas releases. It is crucial to understand the compatibility of chemicals and segregate them accordingly.
Chemicals should be segregated based on their hazard category and potential for interaction. This can be determined by referring to chemical labels, Safety Data Sheets (SDS), or consulting other reliable sources of information. Hazard categories can include flammables, oxidizers, corrosives, reactives, and toxins. It is essential to have a comprehensive understanding of the different hazard classes and their associated risks.
Segregating chemicals can be achieved through physical barriers such as designated storage cabinets, shelving units, or separate storage areas for different hazard categories. Using containers with individual compartments or partitions within larger storage areas can also assist in segregation. Clear labeling and signage should be used to clearly delineate segregated areas and communicate the hazards present.
Compatibility is another critical factor in chemical storage. Certain chemicals may not be compatible even in their separate storage areas due to potential interactions through vapors or cross-contamination. Factors such as temperature, humidity, and the presence of other chemicals nearby can influence compatibility.
It is essential to consult chemical manufacturers, Safety Data Sheets (SDS), or other reliable references to determine the specific compatibility requirements for each chemical. Compatibility charts or databases are available to guide businesses in storing chemicals safely. These resources provide information on which chemicals can be safely stored together and which combinations should be avoided.
Compatibility considerations extend beyond just the chemicals themselves. Storage containers, including lids, seals, or gaskets, should be made of materials that are compatible with the chemicals they are holding. Containers that have been used for one type of chemical should be thoroughly cleaned before storing a different chemical to prevent contamination or reactions.
Proper ventilation is another aspect to consider for maintaining compatibility. Ventilation helps reduce the accumulation of vapors, which can potentially interact with other chemicals or ignite in the presence of a spark or flame. Adequate ventilation systems should be in place to prevent the buildup of hazardous fumes or gases.
Regular inspections and monitoring are crucial to ensuring the ongoing segregation and compatibility of stored chemicals. Employees should be trained to recognize signs of potential compatibility issues or changes in storage conditions that may impact segregation requirements. Any necessary adjustments or updates to storage arrangements should be promptly made to maintain a safe storage environment.
By implementing proper segregation practices and ensuring compatibility in chemical storage, businesses can significantly reduce the risk of accidents, reactions, and contamination. The use of clear labeling, designated storage areas, and regular monitoring allows for the effective management of chemicals and promotes a safe working environment.
Always store chemicals in a well-ventilated area, away from direct sunlight and sources of heat. Use appropriate containers and labels, and follow the manufacturer’s guidelines for storage temperature and conditions.
Adequate Ventilation
Adequate ventilation is a crucial element of proper chemical storage. It plays a vital role in maintaining a safe and healthy environment by minimizing the risks associated with chemical vapors, fumes, and gases. In this section, we will explore the importance of ventilation in chemical storage and the key considerations to ensure adequate airflow.
One of the primary purposes of ventilation in chemical storage areas is to control and disperse hazardous vapors and gases. Many chemicals release volatile vapors that can accumulate in confined spaces, leading to potentially dangerous concentrations. Adequate ventilation ensures that these vapors are continuously removed from the storage area, reducing the risk of inhalation hazards for employees.
In addition to reducing the concentration of vapor, ventilation also helps manage odors and prevent the buildup of unpleasant or noxious smells. This is particularly important in storage areas where chemicals with strong odors are present. Proper airflow can prevent the odors from permeating other areas of the facility and creating discomfort for employees.
Another critical aspect of ventilation is the prevention of potential chemical reactions. Some chemicals can react with the air, moisture, or other substances, resulting in the formation of new compounds or hazardous byproducts. Adequate ventilation helps dilute the concentration of reactive gases, reducing the likelihood of these undesired reactions.
When designing or assessing the ventilation system, several factors should be considered. The airflow rate should be sufficient to effectively remove vapors and maintain a safe working environment. The National Fire Protection Association (NFPA) provides guidelines and recommendations for the required airflow rates based on the type and quantity of chemicals stored.
It is important to ensure that the airflow reaches all areas of the storage space, including low-level areas where vapors may settle. Proper placement and positioning of ventilation openings and exhaust points help achieve this objective. The use of fans, blowers, or air circulation systems may be necessary to ensure adequate and consistent airflow.
The air filtration system is another aspect to consider in ventilation design. Filters should be appropriately selected and regularly maintained to remove contaminants, particulates, and harmful fumes from the air. Activated carbon filters are often used to absorb and neutralize odors or specific chemical vapors.
Regular inspection, cleaning, and maintenance of ventilation systems are essential to ensure their continued effectiveness. Filters should be replaced or cleaned according to the manufacturer’s recommendations, and airflow should be periodically assessed to verify that it meets the necessary requirements.
It is important to note that the design and installation of ventilation systems should comply with applicable local regulations, building codes, and industry standards. Consulting with professionals experienced in ventilation engineering is highly recommended to ensure compliance and optimal performance.
In summary, adequate ventilation is crucial for proper chemical storage. It helps control vapors, minimize odors, prevent hazardous reactions, and maintain a safe and healthy working environment. Proper design, placement, and maintenance of ventilation systems are necessary for effective airflow and removal of hazardous substances from storage areas.
Fire Safety Measures
Fire safety is of utmost importance when it comes to storing chemicals. Many chemicals are flammable or combustible, making them a significant fire hazard if not stored and managed properly. In this section, we will explore key fire safety measures that should be implemented to minimize the risk of fire and protect personnel and property.
The first step in fire safety is to conduct a thorough fire risk assessment of the storage area. This assessment should identify potential ignition sources, flammable materials, and any other fire hazards present. Understanding the specific risks associated with the chemicals being stored enables businesses to take appropriate preventive measures.
Proper storage and segregation are crucial for fire safety. Flammable substances should be stored in designated fire-resistant cabinets or rooms. Chemicals with different hazard classes or incompatibilities should be kept separate to prevent accidental reactions. The storage area should be well-ventilated, as adequate airflow helps disperse flammable vapors and reduce the risk of ignition.
Ensuring that the storage area is free from potential ignition sources is paramount. This includes keeping open flames, sparks, smoking, or hot surfaces away from the storage area. Electrical equipment, lighting fixtures, and switches should be explosion-proof or located outside the immediate storage area to minimize the risk of electrical fires.
Fire suppression systems should be in place and regularly maintained. This includes fire extinguishers, sprinkler systems, or other appropriate firefighting equipment. Employees should be trained in their proper use and know the location of firefighting equipment throughout the storage area.
Emergency exits and evacuation routes should be clearly marked and accessible at all times. Regular drills and training sessions should be conducted to familiarize employees with emergency procedures and evacuation plans. It is essential to have a robust emergency response plan in place, which includes communication protocols, designated assembly areas, and procedures for reporting and handling incidents.
Proper training and education for employees are crucial for fire safety. Employees should be educated on the hazards of the chemicals being stored, as well as the appropriate handling, storage, and emergency response procedures. Training should cover fire prevention, proper use of firefighting equipment, and the importance of immediate reporting of any fire or hazardous situations.
Regular inspections and maintenance of fire safety equipment, such as fire extinguishers, sprinkler systems, and emergency lighting, are essential. These inspections should be documented, and any issues or deficiencies should be promptly addressed. Fire safety equipment should be easily accessible, regularly tested, and comply with relevant safety standards.
In the event of a fire, immediate response is crucial. Employees should be trained on how to initiate emergency alarms, evacuate safely, and summon professional help, such as the fire department. It is important to have procedures in place for containing and extinguishing small fires, while ensuring the safety of employees and minimizing the risk of escalation.
In summary, fire safety is a critical aspect of chemical storage. Implementing proper storage, segregation, preventive measures, and emergency response protocols can significantly reduce the risk of fire and mitigate its potential impact. Regular inspections, employee training, and adherence to safety regulations are essential for maintaining a safe environment and protecting personnel and property.
Labeling and Documentation
Labeling and documentation are integral components of proper chemical storage practices. Clear and accurate labeling ensures that employees can easily identify chemicals, understand their hazards, and handle them safely. Comprehensive documentation, including Safety Data Sheets (SDS), provides essential information about chemical properties, safety precautions, and emergency response procedures. Let’s explore the importance of labeling and documentation in chemical storage.
Labeling plays a crucial role in communicating important information about stored chemicals. Each container should be clearly labeled with the chemical name, concentration or strength, hazard class, and any necessary hazard warnings or symbols. Labels should also indicate any special handling or storage requirements, such as temperature restrictions or compatibility considerations.
The purpose of labeling is to ensure that employees can quickly identify the contents of a container and understand the associated hazards. Clear and legible labels are important for safe handling, preventing mistaken identities, and avoiding potential accidents or reactions.
Labels should be resistant to the chemicals being stored and should not deteriorate or fade over time. Exposure to certain chemicals or environmental conditions may require the use of specific label materials, coatings, or laminates to ensure durability and clarity.
In addition to container labels, it is beneficial to have signage in the storage area that provides information about emergency procedures, locations of fire extinguishers and first aid kits, and evacuation routes. These signs help employees navigate the storage area and quickly access necessary resources in case of an emergency.
Comprehensive documentation, such as Safety Data Sheets (SDS), are vital for understanding the hazards and safe handling procedures associated with chemicals. SDS provide detailed information, including chemical composition, physical and chemical properties, health hazards, precautions for safe handling and storage, and procedures for emergency response.
SDS should be readily accessible to employees and kept up to date. They should be obtained from the chemical manufacturer or supplier and include the latest information available. Regular review and updating of SDS is essential to reflect any changes in the chemical’s composition, handling guidelines, or safety recommendations.
Documentation should also include records of chemical inventory, including quantities, dates received, and dates opened. This helps ensure proper stock rotation and identification of expired or outdated chemicals. Additionally, maintaining accurate documentation aids in tracking chemical usage, monitoring storage conditions, and complying with regulatory requirements.
It is crucial to establish a system for organizing and storing documentation, ensuring that it is easily accessible to employees who may need it. This can include both physical copies and electronic databases or document management systems. Regular training on how to locate and utilize the necessary documentation should be provided to employees.
In summary, labeling and documentation are essential for safe and compliant chemical storage. Clear and accurate labels communicate hazards and handling requirements, enabling employees to handle chemicals safely. Comprehensive documentation, including SDS and records of inventory, aids in understanding hazards, complying with regulations, and facilitating emergency response. By prioritizing proper labeling and documentation practices, businesses can maintain a safe storage environment while meeting regulatory requirements.
Personnel Training and Education
Personnel training and education are crucial aspects of ensuring safe and compliant chemical storage practices. Properly trained employees are equipped with the knowledge and skills necessary to handle, store, and respond to potential hazards effectively. Let’s explore the importance of personnel training and education in chemical storage.
The first step in personnel training is to provide employees with a comprehensive understanding of the hazards associated with the chemicals they will be working with. This involves educating them about the physical and chemical properties of the substances, potential health risks, and the appropriate precautions for safe handling and storage.
Employees should be trained on the proper use of personal protective equipment (PPE) relevant to their work tasks, including gloves, goggles, respirators, and protective clothing. They must understand the importance of using PPE correctly to minimize their exposure to chemicals and prevent potential injuries or health risks.
Proper handling and storage procedures should be a focal point of training programs. This covers techniques for safely transporting, transferring, and disposing of chemicals. Employees should be educated on best practices for handling equipment, such as pumps, valves, and storage containers, to prevent spills, leaks, or accidents.
Training should also emphasize the importance of proper storage practices, including the segregation of incompatible substances and the proper labeling of containers. Employees should be knowledgeable about the hazards associated with different chemicals and understand the consequences of improper storage.
Providing employees with training on emergency response and spill control is essential. They should be educated on the steps to take in the event of a chemical spill or leak, including how to safely contain and control the situation. This includes knowing the location of emergency response equipment, evacuation procedures, and how to effectively communicate the incident to relevant personnel.
Regular refresher training sessions should be conducted to reinforce knowledge and update employees on any changes in regulations or best practices. This ensures that employees stay informed and up to date with the latest safety procedures and guidelines.
Supervisors and management should lead by example and prioritize safety. They should actively demonstrate and encourage safe practices, providing guidance and support to employees. Supervisors should conduct regular safety inspections and offer feedback to employees to ensure compliance with safe storage protocols.
Documentation is an essential component of personnel training and education. Records should be maintained to document the completion of training programs, including specific topics covered and any exams or assessments conducted. This documentation provides evidence of compliance and serves as a reference for future training needs.
It is important to create a culture of safety within the organization. This can be achieved through ongoing communication, open dialogue, and encouraging employees to report any safety concerns or incidents. Regular safety meetings or toolbox talks can be conducted to address specific topics, reinforce safe practices, and address any questions or concerns.
In summary, personnel training and education are fundamental for safe and compliant chemical storage practices. Proper training ensures that employees understand the hazards associated with chemicals, follow proper handling and storage procedures, and are prepared to respond to emergencies. Ongoing training, documentation, and fostering a safety culture contribute to maintaining a secure storage environment and protecting both employees and the surrounding environment.
Emergency Response and Spill Control
Having a well-developed emergency response plan and effective spill control procedures are critical elements of safe chemical storage. Accidents, spills, and leaks can occur despite preventative measures, and a swift and organized response is crucial to minimize the impact and protect personnel and the environment. Let’s explore the importance of emergency response and spill control in chemical storage.
An emergency response plan should be developed and communicated to all employees involved in chemical storage. The plan should outline clear procedures to follow in the event of an emergency, such as a chemical spill, fire, or release of hazardous substances. It should also include emergency contact information and prompt communication protocols to notify appropriate personnel or emergency services.
Training employees on the emergency response plan is vital. They should be educated on how to recognize and respond to different types of emergencies, including how to safely evacuate the area, operate firefighting equipment, and manage potential hazards. Regular drills and simulations should be conducted to reinforce the response procedures and identify areas for improvement.
Establishing a designated area for spills or releases is an important aspect of spill control. This area should be equipped with appropriate spill control kits and supplies, such as absorbent materials, neutralizing agents, and containment barriers. Employees should know the location of these spill control resources and how to properly utilize them in case of a spill or leak.
Immediate action should be taken in the event of a chemical spill or leak to prevent further spread or contamination. Employees should be trained on how to contain the spill using appropriate absorbent materials or barriers. This includes taking precautions to prevent the spill from entering drains, sewers, or the surrounding environment.
Personal protective equipment (PPE) should be utilized when responding to spills or leaks. Employees should be trained on the selection and proper use of PPE based on the specific hazards involved. This may include gloves, goggles, respirators, or protective clothing to minimize exposure to hazardous substances.
Procedures for properly disposing of hazardous materials and contaminated spill response materials should be in place. Employees should be educated on the methods for safely disposing of these materials in compliance with applicable regulations and in an environmentally responsible manner.
Documentation of spill incidents and the emergency response should be maintained. This includes recording the date, time, location, description of the incident, actions taken, and any follow-up procedures. This documentation serves as an important record for future reference, regulatory compliance, and improvement in spill response procedures.
It is essential to engage and communicate with local emergency services, such as the fire department and hazardous material response teams. Sharing relevant information about the stored chemicals and the storage area can assist emergency responders in their efforts to mitigate the situation effectively.
Regular reviews and assessments of the emergency response procedures and spill control measures should be conducted. This ensures that the procedures remain effective and up to date with changing regulations and industry best practices. Lessons learned from actual incidents or drills should be incorporated into the plan to enhance response capabilities.
In summary, having a well-defined emergency response plan and effective spill control procedures are critical for safe chemical storage. Education, training, and regular drills enable employees to respond promptly and appropriately in the event of an emergency. By implementing proper spill control measures and maintaining open communication with emergency services, businesses can minimize the impact of incidents and protect personnel and the environment.
Conclusion
Proper chemical storage is crucial for the safety of personnel, the protection of the environment, and compliance with legal and regulatory requirements. Throughout this article, we have explored various key aspects and requirements for safe chemical storage.
We began by emphasizing the importance of proper chemical storage and its significance in different industries. We highlighted the legal and regulatory requirements set by organizations such as OSHA and emphasized the need to comply with these standards to avoid penalties and ensure a safe working environment.
We discussed the essential role of facility and infrastructure conditions in chemical storage. Adequate ventilation, suitable storage containers, and proper lighting are key factors to consider in maintaining a secure storage environment.
Segregation and compatibility were identified as critical considerations to prevent accidents or reactions between incompatible substances. We discussed the importance of proper labeling and documentation to ensure clear communication, easy identification, and access to essential information about chemicals.
Fire safety measures, including proper storage, prevention of ignition sources, and emergency response protocols, were explored to minimize the risk of fires and protect personnel and property.
Moreover, we emphasized the significance of personnel training and education in chemical storage. Proper training equips employees with the knowledge and skills necessary to handle, store, and respond to potential hazards. We discussed the importance of creating a culture of safety within the organization and maintaining documentation to ensure compliance and ongoing improvement.
Lastly, we outlined the importance of having an effective emergency response plan and spill control procedures in place. Swift and organized responses to emergencies and spills can significantly reduce the impact and mitigate potential harm to personnel and the environment.
In conclusion, by adhering to the requirements and best practices outlined for chemical storage, businesses and organizations can create a safe and compliant environment. Prioritizing proper ventilation, suitable storage containers, segregation, labeling, personnel training, and emergency response measures are key to protecting personnel, minimizing environmental impact, and ensuring regulatory compliance. By implementing these practices, businesses can safeguard their employees, reduce risks, and contribute to a safer and more sustainable working environment.
Frequently Asked Questions about What Is The Requirement For Storing Chemicals
Was this page helpful?
At Storables.com, we guarantee accurate and reliable information. Our content, validated by Expert Board Contributors, is crafted following stringent Editorial Policies. We're committed to providing you with well-researched, expert-backed insights for all your informational needs.
0 thoughts on “What Is The Requirement For Storing Chemicals”