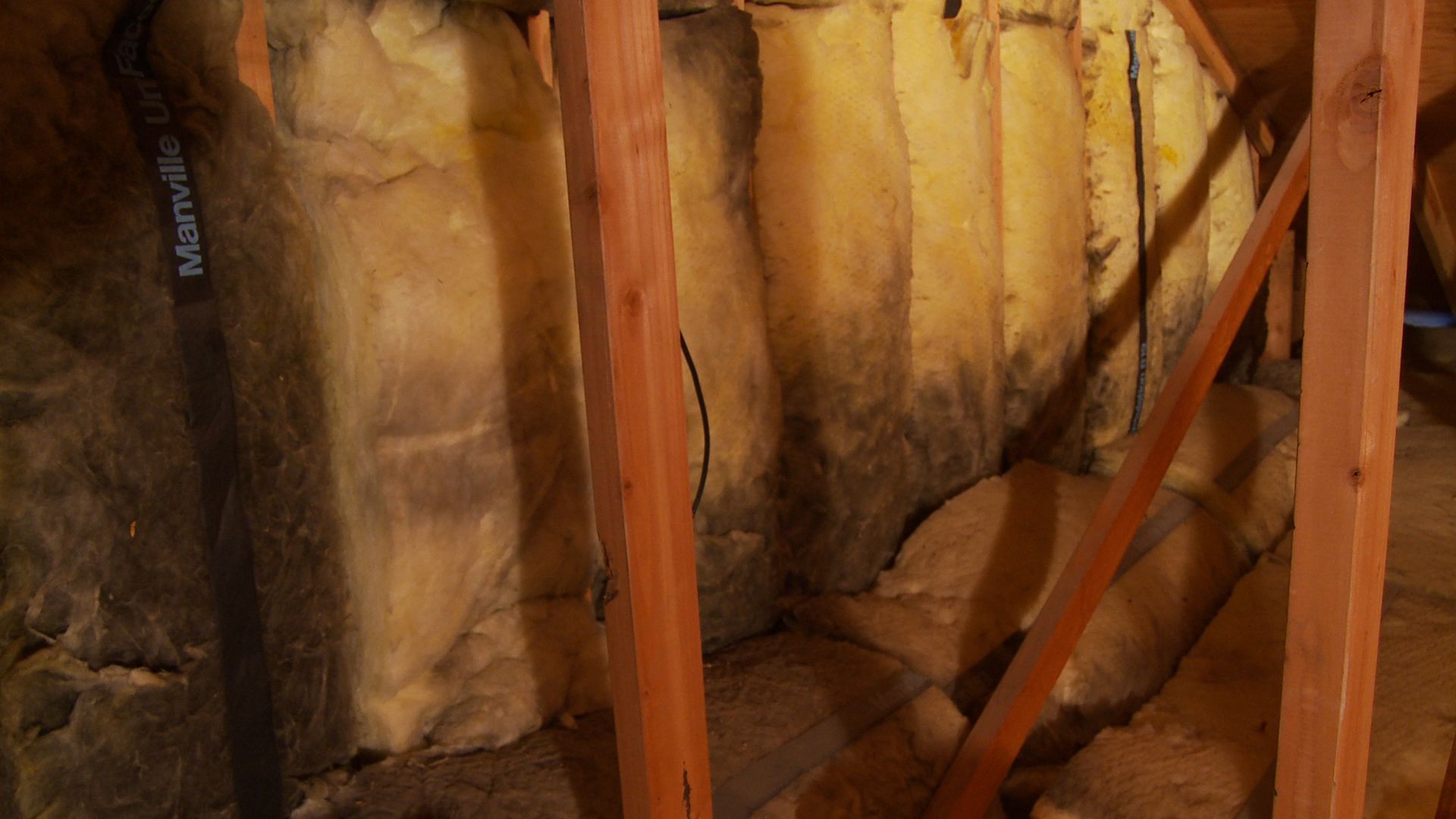
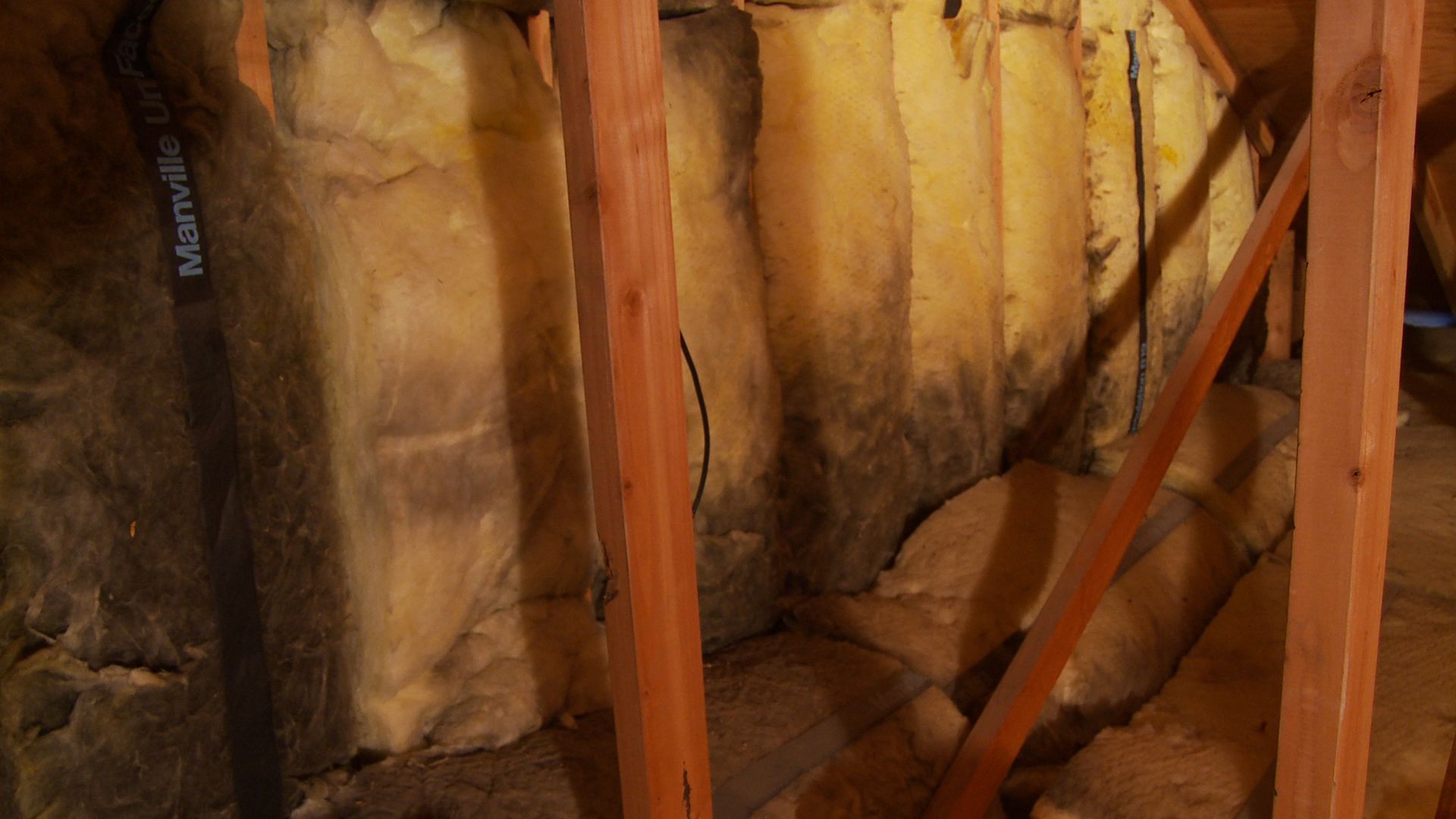
Articles
Why Does Insulation Turn Black
Modified: January 6, 2024
Discover why insulation turns black and learn effective methods to prevent it. Read our informative articles for valuable insights.
(Many of the links in this article redirect to a specific reviewed product. Your purchase of these products through affiliate links helps to generate commission for Storables.com, at no extra cost. Learn more)
Introduction
Insulation is an essential component of any building, providing thermal resistance and reducing energy consumption. It is typically installed in walls, ceilings, and floors to keep the indoor temperature regulated and minimize heat loss or gain. However, over time, insulation may develop discoloration and turn black, which can raise concerns among homeowners about its effectiveness and safety.
In this article, we will explore the reasons why insulation may turn black, the potential causes behind this discoloration, and the impact it may have on your home and health. Understanding these factors can help you take appropriate measures to address the issue and ensure the efficiency and longevity of your insulation system.
Key Takeaways:
- Insulation turning black may indicate moisture, mold, air pollution, or aging issues. Regular maintenance, moisture control, and proper ventilation are crucial for preventing discoloration and ensuring insulation efficiency and safety.
- Addressing moisture, mold, and air pollution promptly is essential for maintaining a healthy living environment. Professional consultation and regular cleaning can help prevent insulation from turning black and ensure long-term effectiveness.
Read more: Why Is My Zoysia Grass Turning Black
Understanding Insulation
Before delving into the reasons why insulation may turn black, it is important to have a basic understanding of what insulation is and how it functions.
Insulation is designed to resist the flow of heat, keeping the indoor temperature stable by blocking the transfer of heat through the walls, ceiling, or floors. It acts as a barrier, preventing the exchange of heat between the interior and exterior of a building. This helps maintain a comfortable living environment and reduces the need for excessive use of heating and cooling systems, ultimately saving energy and reducing utility bills.
There are various types of insulation materials available, including fiberglass, cellulose, mineral wool, and foam. These materials are chosen for their ability to trap pockets of air, which are poor conductors of heat. The more air trapped within the insulation material, the higher its thermal resistance or R-value is, effectively reducing heat conduction.
Insulation is typically installed in attics, crawl spaces, and between walls. It can also be found in basements and around pipes and ductwork. While the primary purpose of insulation is to provide thermal resistance, it can also offer soundproofing benefits, reducing noise levels between rooms or from external sources.
Insulation is a critical component of energy-efficient buildings, as it helps to minimize heat transfer, keeping indoor spaces cool in hot weather and warm during colder months. However, when insulation starts turning black, it could indicate issues that may affect its performance and overall effectiveness.
Causes of Insulation Turning Black
There are several potential causes behind the discoloration and blackening of insulation. Understanding these causes can help you identify the underlying issue and take appropriate action to mitigate it.
1. Moisture and Mold Growth: Moisture infiltration is one of the primary culprits for insulation turning black. If water or excessive humidity enters the insulation material, it creates an environment conducive to mold growth. Mold spores thrive in damp conditions, breaking down organic matter and causing discoloration. This not only affects the appearance of the insulation but also compromises its integrity and thermal resistance.
2. Air Pollution and Soot Deposition: Insulation located near sources of air pollution, such as industrial areas or buildings with combustion appliances, can accumulate soot and other particulate matter over time. This can contribute to the blackening of insulation and reduce its effectiveness. Soot, in particular, is a byproduct of incomplete combustion and can contain harmful substances that pose health risks.
3. Aging and Deterioration: Over time, insulation materials can naturally degrade due to wear and tear, exposure to the elements, and the aging process. As insulation ages, it may develop discoloration and black spots. This is a sign of its deterioration and reduced performance. Aging insulation may also become more susceptible to moisture infiltration and mold growth.
4. Chemical Reactions: Some insulation materials, such as certain types of foam insulation, can undergo chemical reactions when exposed to certain substances or conditions. These reactions can lead to discoloration, including turning black. Chemical reactions can occur due to incompatible building materials, exposure to chemicals or solvents, or improper installation methods.
5. Environmental Factors: Environmental factors, such as excessive sunlight exposure or high levels of UV radiation, can also contribute to the blackening of insulation. UV rays can break down the outer layers of the insulation material, causing it to deteriorate and discolor. This is more common in exposed insulation, such as in attics or on rooftops.
In some cases, the blackening of insulation may be purely cosmetic and not impact its thermal resistance significantly. However, it is crucial to investigate the underlying cause and determine if any remedial action is required to maintain the efficiency and safety of the insulation system.
Moisture and Mold Growth
Moisture infiltration and subsequent mold growth are common causes of insulation turning black. When water or excessive humidity enters the insulation material, it creates a favorable environment for mold spores to thrive. Mold spores are microscopic organisms that can colonize and spread rapidly in the presence of moisture and organic matter.
Mold growth not only affects the appearance of insulation, but it also poses health risks and compromises the performance of the insulation system. Here’s how moisture and mold can impact insulation:
1. Moisture Infiltration: Water can enter the insulation material through various sources, such as roof leaks, plumbing leaks, condensation, or inadequate moisture barriers. Once moisture infiltrates the insulation, it becomes trapped within the material, leading to dampness and increased humidity levels. This provides an ideal breeding ground for mold.
2. Mold Growth: When mold spores come into contact with moisture, they germinate and begin to grow. As mold colonies multiply, they release spores into the air, which can spread to other areas of the building, potentially affecting indoor air quality. The presence of mold can cause a musty odor, discoloration, and visible black spots on the insulation and surrounding surfaces.
3. Health Concerns: Exposure to mold can have adverse health effects, especially for individuals with allergies, asthma, or weakened immune systems. Common symptoms of mold exposure include respiratory issues, coughing, sneezing, congestion, skin irritation, and eye or throat irritation. Prolonged exposure to mold can potentially lead to more severe health problems.
4. Structural Damage: Mold growth can weaken the structure of the insulation material and compromise its thermal resistance. Over time, the presence of mold can cause the insulation to degrade, leading to reduced efficiency in terms of heat insulation. Additionally, mold can spread to other building materials, such as drywall, wood, or fabrics, causing further damage and requiring costly repairs.
Prevention and Remediation: To prevent moisture and mold growth in insulation, it is crucial to address any sources of water intrusion promptly. Regular inspections of the building envelope, roof, and plumbing systems can help identify and fix potential leaks. Proper ventilation and maintaining indoor humidity levels between 30-50% can also discourage mold growth. If mold is already present, professional remediation is necessary to safely remove the mold and restore the insulation to its pre-damaged condition.
By addressing moisture issues and preventing mold growth, you can maintain the performance, longevity, and safety of your insulation system.
Air Pollution and Soot Deposition
Air pollution and the deposition of soot are another significant cause of insulation turning black. Insulation located near sources of air pollution, such as industrial areas or buildings with combustion appliances, is more susceptible to accumulating soot and other particulate matter over time.
Here’s how air pollution and soot can impact insulation:
1. Soot Deposition: Soot is a black, powdery substance that consists of small particles and carbon-based materials. It is a byproduct of incomplete combustion and is commonly associated with sources like chimneys, fireplaces, wood-burning stoves, diesel engines, and industrial processes. When these particles are released into the air, they can settle on surfaces, including insulation, creating a layer of black residue.
2. Reduced Insulation Performance: The accumulation of soot on insulation can compromise its ability to resist heat transfer. Soot acts as an insulator itself, creating a barrier that inhibits the insulation material from effectively blocking the flow of heat. As a result, the thermal resistance and energy-saving properties of the insulation can be significantly reduced.
3. Health Risks: Soot contains harmful substances, such as polycyclic aromatic hydrocarbons (PAHs), heavy metals, and fine particulate matter (PM2.5). These substances can be released into the air when disturbed or become airborne due to ventilation or air movement. Inhalation of these particles can trigger respiratory issues, cardiovascular problems, and other health concerns.
4. Aesthetic Impacts: The blackening of insulation due to soot deposition also affects the aesthetic appeal of the building. Soot can leave unsightly black stains and marks on the insulation surface and may spread to adjacent areas or materials if not addressed promptly.
Prevention and Remediation: To minimize the impact of air pollution and soot on insulation, it is important to address the sources of soot emissions. Regular maintenance and cleaning of combustion appliances, such as fireplaces and stoves, can help reduce soot production. Using proper ventilation systems and filters can also help to filter out airborne particles, improving indoor air quality and reducing the deposition of soot on insulation surfaces. If significant soot deposition occurs, professional cleaning and restoration may be required to restore the insulation’s appearance and performance.
By taking steps to reduce air pollution and prevent the deposition of soot, you can ensure the long-term effectiveness and visual appeal of your insulation system.
Insulation turns black due to soot and dirt accumulation from air pollution, candles, or gas appliances. Regular cleaning and maintenance can help prevent this.
Read more: Why Is My Grass Turning Black In Spots
Aging and Deterioration
Over time, insulation materials can naturally age and deteriorate due to various factors, leading to the blackening of insulation. This aging process can affect the performance and longevity of the insulation system.
Here’s how aging and deterioration can impact insulation:
1. Wear and Tear: Insulation is exposed to daily stresses, including temperature fluctuations, vibrations, and physical impacts. These factors can contribute to the gradual breakdown of insulation materials, causing them to become brittle, lose their elasticity, or develop cracks. The aging process of insulation can result in the formation of black spots or discoloration, indicating areas of deterioration.
2. Exposure to the Elements: Insulation located in exposed areas, such as attics, roofs, or exterior walls, is particularly susceptible to the effects of weather conditions. Exposure to sunlight, UV radiation, rain, snow, and high humidity levels can degrade the insulation material over time. This exposure can lead to the breakdown of organic compounds within the insulation, resulting in discoloration and blackening.
3. Oxidation: Insulation materials that contain organic components, such as cellulose or certain types of foam, can be prone to oxidation over time. Oxidation occurs when these materials react with oxygen in the air, which can cause them to deteriorate and change in appearance. This process can contribute to the blackening of insulation.
4. Pest Infestation: In regions where pests, such as rodents or insects, are prevalent, insulation can be a target for their nesting or burrowing. Pests can damage the insulation material, disrupt its structure, and introduce debris or feces, which can lead to discoloration and blackening. Additionally, the presence of pests can contribute to moisture infiltration, further accelerating the aging process of the insulation.
5. Reduced Performance: As insulation ages and deteriorates, its ability to resist heat transfer is compromised. The thermal resistance, or R-value, of the insulation can decrease, resulting in decreased energy efficiency and increased heating or cooling costs. The blackening of insulation due to aging and deterioration is often a visual indicator that the insulation’s effectiveness may be diminished.
Maintenance and Replacement: Regular maintenance and inspection of insulation can help identify signs of aging and deterioration early on. Repairing or replacing damaged insulation can help restore its performance and improve energy efficiency. Regular sealing of gaps and cracks can also prevent moisture infiltration and slow down the aging process. If the insulation is significantly degraded or no longer effective, it may be necessary to replace it with new insulation to ensure optimal thermal performance.
By addressing the effects of aging and deterioration, you can maintain the efficiency, integrity, and longevity of your insulation system.
Health Concerns and Risks
When insulation turns black, it may raise concerns about potential health risks associated with its presence. While the discoloration itself may not pose an immediate health threat, it can be an indication of underlying issues that may have health implications. Here are some health concerns to be aware of:
1. Mold-Related Health Issues: If the blackening of insulation is due to moisture infiltration and mold growth, there can be health risks associated with exposure to mold spores. Mold spores can trigger allergies, respiratory problems, and worsen existing conditions such as asthma. Prolonged exposure to mold can also lead to more severe health issues, especially for individuals with compromised immune systems.
2. Poor Indoor Air Quality: Insulation that has turned black due to soot deposition or chemical reactions can negatively impact indoor air quality. Soot particles and chemicals released by insulation can become airborne and may be inhaled. Inhalation of these substances can cause respiratory irritation, coughing, throat irritation, or even more serious health problems in the long run.
3. Irritation and Allergies: The presence of deteriorated or contaminated insulation can release particles or fibers into the air, leading to irritation of the skin, eyes, nose, and throat. These particles may also trigger allergic reactions in sensitive individuals, resulting in symptoms such as sneezing, itching, or rash.
4. Inadequate Insulation and Comfort: Blackened or degraded insulation may have reduced thermal resistance, leading to heat loss or gain. Inadequate insulation can result in discomfort, as the indoor temperature becomes harder to maintain. In extreme weather conditions, it can also put additional strain on heating and cooling systems, increasing energy consumption and costs.
5. Fire Safety Concerns: In some cases, the blackening of insulation might be an indication of fire damage or compromised fire-resistant properties. Insulation that has been exposed to fire or extreme heat might lose its ability to slow down the spread of flames, potentially putting occupants at a higher risk in the event of a fire.
Prevention and Mitigation: To address health concerns related to blackened insulation, it is crucial to address the underlying issues causing the discoloration. This may involve remediation of moisture issues, removal or remediation of mold growth, cleaning or replacing damaged insulation, and improving ventilation and indoor air quality. It is always beneficial to consult with professionals to assess the situation and take appropriate measures to mitigate any health risks.
By proactively addressing potential health concerns associated with insulation discoloration, you can ensure a safe and comfortable living environment for you and your family.
Prevention and Maintenance
To prevent insulation from turning black and to ensure its long-term effectiveness, it is important to prioritize regular maintenance and take proactive measures. By implementing preventive strategies, you can extend the lifespan of your insulation and minimize the chances of discoloration or deterioration. Here are some key prevention and maintenance tips:
1. Moisture Control: Moisture is one of the primary culprits behind insulation discoloration and damage. Regularly inspect your home for any signs of leaks or water intrusion, such as roof leaks, plumbing leaks, or condensation. Promptly address any moisture issues to prevent mold growth and the degradation of insulation. Install proper moisture barriers, such as vapor barriers, to minimize the risk of moisture infiltration.
2. Proper Ventilation: Adequate ventilation is essential to maintain healthy indoor air quality and prevent the buildup of moisture. Ensure that your home is properly ventilated, particularly in areas such as attics, basements, and crawl spaces. Proper ventilation helps to dissipate excess humidity and prevent the accumulation of moisture within the insulation.
3. Regular Inspections: Conduct regular inspections of the insulation to check for any signs of deterioration, discoloration, or damage. Look for black spots, mold growth, or any unusual changes in appearance. Early detection can help you address problems promptly, preventing further damage and potential health risks.
4. Pest Control: Pests, such as rodents or insects, can cause damage to insulation and contribute to its blackening. Take preventive measures to keep pests away, such as sealing gaps or cracks, storing food properly, and keeping the surrounding areas clean and free from debris. If you suspect a pest infestation, promptly address the issue and consider seeking professional assistance for effective pest control.
5. Proper Installation: Ensure that insulation is properly installed by following manufacturer guidelines and best practices. Improper installation can lead to gaps, voids, or compressions, affecting the insulation’s effectiveness and longevity. Hiring a professional installer can help ensure that the insulation is installed correctly, maximizing its performance and minimizing the risk of discoloration or damage.
6. Regular Cleaning: Periodically clean the insulation, especially in areas prone to outdoor pollutants or soot deposition. Use appropriate cleaning methods and tools, following manufacturer recommendations. Consult with professionals if significant staining or debris accumulation occurs, as they may provide specialized cleaning solutions.
7. Professional Consultation: If you notice severe blackening, persistent mold growth, or significant damage to the insulation, it is advisable to seek professional consultation. They can assess the situation, provide appropriate remediation solutions, and help restore the integrity and performance of the insulation.
By implementing these preventive measures and conducting regular maintenance, you can prolong the lifespan of your insulation, maintain its efficiency, and prevent the discoloration and deterioration that leads to potential problems.
Conclusion
Insulation turning black can be a cause for concern, as it may indicate underlying issues that can affect its performance and pose potential health risks. From moisture and mold growth to air pollution and aging, there are various factors that can contribute to the discoloration of insulation.
Understanding the causes and taking appropriate preventive measures is crucial to maintain the efficiency, longevity, and safety of your insulation system. Regular maintenance, moisture control, proper ventilation, and addressing any signs of damage or deterioration are essential steps for preventing the blackening of insulation.
In addition, it is important to address any issues promptly, such as mold growth, soot deposition, or pest infestation, to mitigate potential health risks and ensure a healthy living environment. Consulting with professionals can provide expert insights and guidance for effective remediation and maintenance strategies.
By prioritizing preventive measures, regular inspections, and proper cleaning, you can extend the lifespan of your insulation, optimize energy efficiency, and enhance the overall comfort of your home. A well-maintained insulation system will not only save energy and reduce utility bills, but it will also contribute to a healthier and more sustainable living environment for you and your family.
Remember, if you have concerns about the condition of your insulation, seek professional assistance for a comprehensive assessment and guidance tailored to your specific situation. With proper care and maintenance, your insulation will continue to provide the thermal resistance and energy efficiency that it was designed for, ensuring a comfortable and healthy home for years to come.
Frequently Asked Questions about Why Does Insulation Turn Black
Was this page helpful?
At Storables.com, we guarantee accurate and reliable information. Our content, validated by Expert Board Contributors, is crafted following stringent Editorial Policies. We're committed to providing you with well-researched, expert-backed insights for all your informational needs.
0 thoughts on “Why Does Insulation Turn Black”