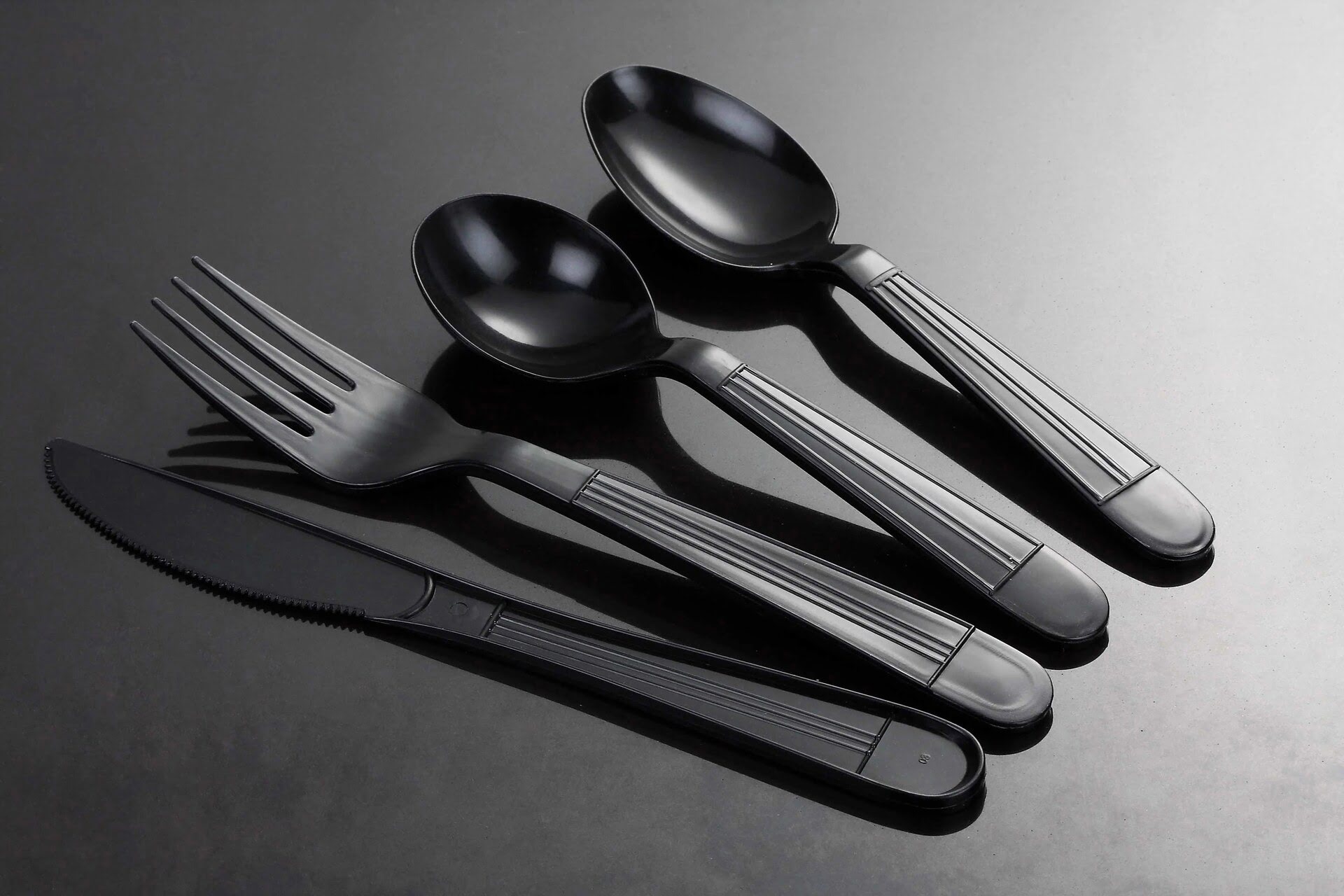
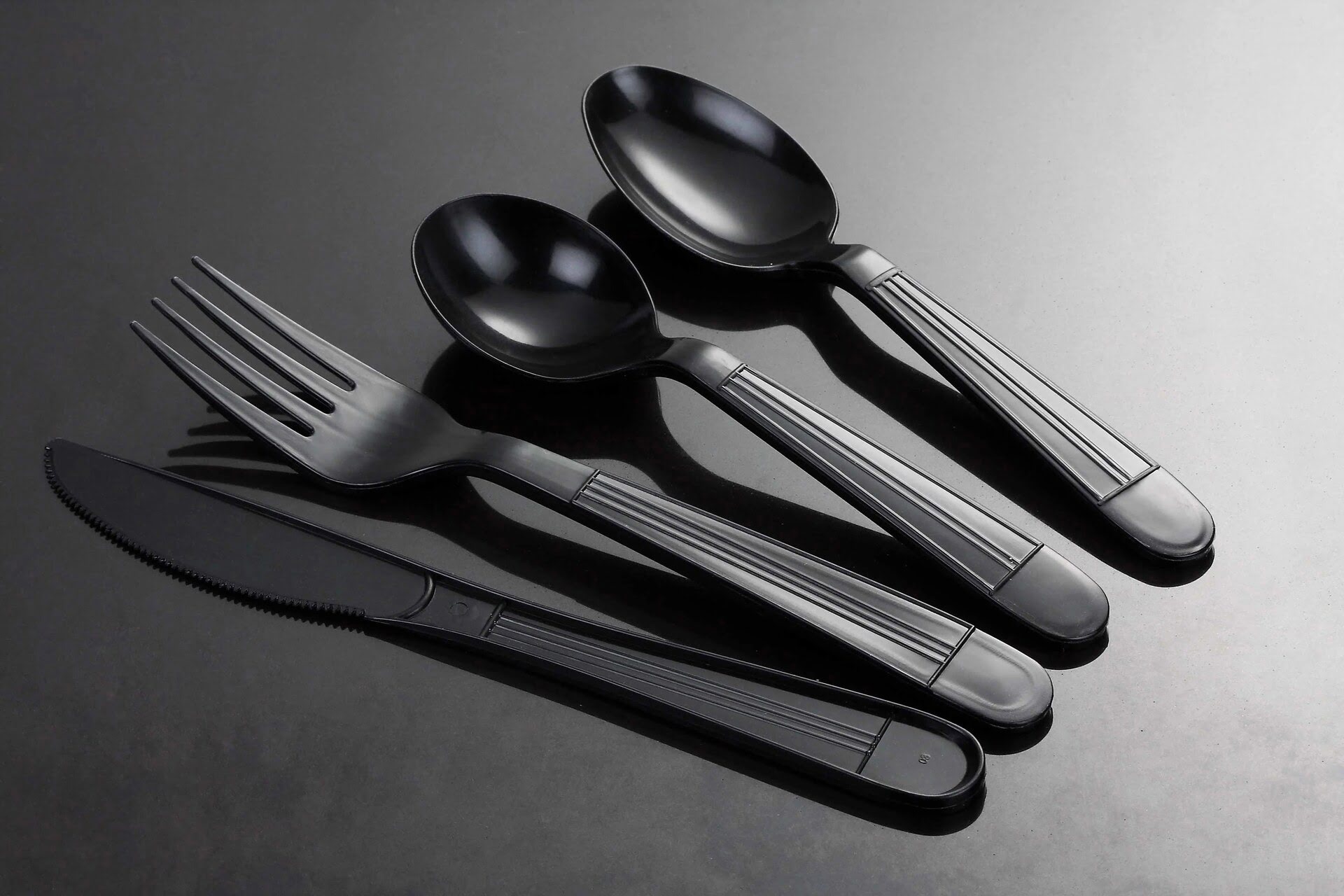
Tableware
How Is Plastic Cutlery Made
Modified: December 7, 2023
Discover the fascinating process of manufacturing plastic cutlery, from the creation of raw materials to the molding and shaping of durable tableware items.
(Many of the links in this article redirect to a specific reviewed product. Your purchase of these products through affiliate links helps to generate commission for Storables.com, at no extra cost. Learn more)
Introduction
Welcome to the world of tableware! In this article, we will delve into the intriguing realm of plastic cutlery, exploring its production process, the different types of plastics used, and its environmental impact. Whether you’re a food enthusiast, a hospitality industry professional, or simply curious about the manufacturing process behind everyday objects, this article will provide you with a comprehensive understanding of how plastic cutlery is made.
Plastic cutlery has become a staple in our modern society due to its convenience, affordability, and versatility. It is used in various settings, from homes and restaurants to fast-food chains and outdoor events. However, the production and disposal of plastic cutlery have not been without controversy due to the environmental impact associated with plastic pollution.
Before we delve into the intricacies of plastic cutlery production, let’s first provide an overview of what plastic cutlery is. Plastic cutlery typically includes items such as spoons, forks, and knives, all made from different types of plastic polymers. These utensils are lightweight, durable, and disposable, making them ideal for single-use purposes.
Now that we have a general understanding of plastic cutlery, let’s explore the fascinating production process behind it. Stay tuned for the next sections where we’ll walk you through each step of the manufacturing process, starting with the material selection.
Key Takeaways:
- Plastic cutlery production and disposal have significant environmental impacts, but embracing reusable, compostable, and recyclable alternatives can mitigate plastic waste and contribute to a cleaner, greener future.
- Educating consumers, promoting responsible waste management, and advocating for legislative measures can help address the environmental challenges posed by plastic cutlery, paving the way for sustainable practices and eco-friendly choices.
Read more: What Is Cutlery Made Of
Overview of Plastic Cutlery
Plastic cutlery is a convenient and widely used option for dining purposes. It offers several advantages over traditional metal cutlery, including affordability, convenience, and hygiene. Plastic cutlery is lightweight, making it easy to transport and handle, and it eliminates the need for washing and maintenance.
The production process of plastic cutlery involves several steps, starting with the selection of suitable materials and ending with the quality control of the final products. Let’s take a closer look at each of these steps:
Production Process of Plastic Cutlery
Step 1: Material Selection
The first step in the production of plastic cutlery is the selection of the appropriate plastic material. The most commonly used plastics for cutlery production are polypropylene (PP), polystyrene (PS), and polyethylene (PE). These plastics are chosen for their durability, flexibility, and heat resistance.
Different types of plastics offer varying properties, such as rigidity or flexibility, which is essential for different types of cutlery. For example, forks require more rigidity to handle firm foods, while spoons and knives need flexibility to scoop and cut through various textures. The selected plastic material is usually in the form of pellets, which are melted and shaped into the desired cutlery.
Step 2: Extrusion
In the extrusion process, the plastic pellets are fed into a heated chamber, where they are melted and forced through a small opening known as a die. This creates a long and continuous tube of molten plastic, which is then cooled and solidified. The extrusion process is used primarily for the production of handles for cutlery.
Read more: Where Are Chicago Cutlery Knives Made
Step 3: Injection Molding
The injection molding process is widely used for producing plastic cutlery. In this step, the molten plastic material is injected into pre-designed molds or cavities using a specialized injection molding machine. The molds are shaped like the desired cutlery, and the plastic is injected under high pressure to fill the cavities completely.
Once the plastic is injected, it is left to cool and solidify inside the mold. The cooling time varies depending on the size and thickness of the cutlery. After cooling, the molds are opened, and the solidified plastic cutlery is ejected from the molds.
Step 4: Cooling and Ejection
After the injection molding process, the plastic cutlery needs to cool and harden before it can be handled further. The cooling process can be accelerated by the use of cooling chambers or water baths, depending on the manufacturer’s requirements.
Once the plastic cutlery has sufficiently cooled and hardened, it is ejected from the molds. The ejected cutlery is then inspected for any visible defects or imperfections, such as warping or incomplete filling of the molds. Any defective pieces are discarded, and only the high-quality cutlery is retained for further processing.
Step 5: Trimming and Finishing
After the cutlery is ejected from the molds, it may require additional trimming and finishing touches. This involves removing any excess plastic or flash that may have formed during the injection molding process. Trimming helps achieve the desired shape and smooth edges of the cutlery.
Once the excess material is removed, the cutlery may undergo further finishing processes, such as polishing or buffing, to enhance its appearance and quality. These additional steps ensure that the final plastic cutlery is aesthetically pleasing and ready for use.
Step 6: Quality Control
The final step in the production process is quality control. The plastic cutlery undergoes thorough inspection to ensure that it meets the required standards and specifications. This includes checking for any defects, such as cracks, uneven surfaces, or weak areas in the cutlery.
Quality control also involves conducting tests to assess the durability and functionality of the cutlery. Examples of tests include measuring resistance to bending and breaking, evaluating heat resistance, and assessing the overall performance of the cutlery.
Once the plastic cutlery passes the quality control tests, it is ready for packaging and distribution to various markets, where it will be used for various dining occasions.
Now that we have explored the production process of plastic cutlery in detail, let’s move on to discussing the different types of plastics used for cutlery production.
Read more: Where Is Frost Cutlery Made
Step 1: Material Selection
The first crucial step in the production process of plastic cutlery is the careful selection of the appropriate plastic material. Different types of plastics offer distinct properties, making them suitable for various applications. The most commonly used plastics for cutlery production are polypropylene (PP), polystyrene (PS), and polyethylene (PE).
Polypropylene (PP)
Polypropylene (PP) is a popular choice for plastic cutlery due to its excellent balance of strength, flexibility, and heat resistance. PP cutlery can withstand high temperatures without melting or deforming, making it suitable for use with hot food and beverages. Additionally, PP has a low moisture absorption rate, making it resistant to staining and retaining odors.
PP is also known for its recyclability, which has become an essential factor in today’s environmentally conscious world. Recycled PP can be used in the production of new plastic cutlery, reducing the reliance on virgin plastic materials and minimizing waste.
Polystyrene (PS)
Polystyrene (PS) is another common plastic used in the production of cutlery. PS is known for its clarity and transparency, which makes PS cutlery visually appealing. It is lightweight and easy to handle, offering convenience for both manufacturers and consumers.
One of the drawbacks of PS cutlery is its lower heat resistance compared to PP. PS cutlery may deform or melt when exposed to high temperatures, making it more suitable for use with cold or room temperature foods. However, advancements in technology have allowed manufacturers to produce heat-resistant PS cutlery, which expands its application range.
Polyethylene (PE)
Polyethylene (PE) is a versatile plastic commonly used in various industries, including cutlery production. PE cutlery is known for its flexibility, making it ideal for disposable spoons and forks that require bending or scooping. It is also resistant to chemicals and moisture, ensuring that the cutlery remains intact even when in contact with liquids or food substances.
Similar to PP, PE is recyclable, allowing for greater sustainability in the production and disposal of plastic cutlery.
Read more: Where Is Circle SH Cutlery Made
Others
In addition to PP, PS, and PE, other types of plastics may also be used in the production of cutlery, depending on specific requirements. For example, Acrylonitrile Butadiene Styrene (ABS) is a type of plastic used for its durability and impact resistance, making it suitable for heavy-duty cutlery applications.
Manufacturers carefully evaluate the properties and characteristics of each plastic material to determine the most suitable option for the type of cutlery they are producing. Factors such as cost, availability, and environmental impact also play a role in the material selection process.
Now that we have explored the material selection phase, we will proceed to the next step in the production process: extrusion.
Step 2: Extrusion
After the material selection phase, the next step in the production process of plastic cutlery is extrusion. This process is primarily used for creating the handles of the cutlery.
The Extrusion Process
Extrusion is a manufacturing process that involves melting plastic pellets and shaping them into a continuous profile. The process starts with the plastic material, usually in the form of small pellets or granules, being fed into a heated chamber known as the extruder.
Inside the extruder, the plastic material is subjected to high temperatures, causing it to melt into a viscous state. The molten plastic is then forced through a small opening called a die, which determines the shape and dimensions of the extruded profile.
As the molten plastic is pushed through the die, it takes on the shape of the die and emerges as a long, continuous profile. In the case of plastic cutlery handles, the extruded profile is shaped like a long cylindrical rod.
Types of Extrusion
There are different types of extrusion processes that can be utilized for plastic cutlery production, depending on the desired outcome:
- Tube Extrusion: This is the most commonly used type of extrusion for plastic cutlery handles. The molten plastic is forced through a round die, resulting in a cylindrical shape.
- Profile Extrusion: This type of extrusion is used when more complex shapes are required for the handles. The die is custom-made to match the desired shape, allowing for greater design versatility.
- Coextrusion: Coextrusion involves combining multiple materials or colors during the extrusion process. This technique allows for the creation of cutlery handles with different layers or patterns, enhancing their aesthetic appeal.
Read more: Where Are Chipaway Cutlery Knives Made
Cooling and Cutting
Once the plastic profile is extruded, it goes through a cooling process to solidify the plastic. This is typically done using water baths or cooling chambers, where the extruded profile is immersed or passed through chilled water to rapidly cool it down.
After the cooling process, the solidified plastic profile is cut into the desired lengths. The cut pieces will serve as the handles for the plastic cutlery. The length of the handles depends on the specific requirements of the cutlery design, ensuring they are comfortable to hold and use.
Addition and Integration
In some cases, the extruded plastic handles may need further processing before being integrated into the final cutlery products. This can include additional steps such as punching holes for attaching the utensil heads or customizing the handles with unique textures or patterns.
Once the extruded plastic handles are ready, they move on to the next phase of production, where they will be integrated with the utensil heads through injection molding or other assembly methods. This integration completes the manufacturing process of plastic cutlery.
Now that we have covered the extrusion process, let’s move on to the next step: injection molding, which is critical in producing the main components of plastic cutlery.
Step 3: Injection Molding
The third step in the production process of plastic cutlery is injection molding. Injection molding is a widely used manufacturing technique that allows for the mass production of plastic products with high precision and efficiency.
The Injection Molding Process
Injection molding begins with the preparation of the injection molding machine, which consists of a heating chamber, an injection unit, and a mold cavity. The plastic material, in the form of pellets, is loaded into the heating chamber, where it is melted and brought to a suitable temperature for injection.
Once the plastic material has melted, it is injected into the mold cavity under high pressure through a specialized nozzle. The mold cavity is created by two halves of a mold, which has the shape and design of the desired cutlery product.
As the molten plastic material fills the mold cavity, it takes on the shape and details of the mold. It flows into every intricate crevice, ensuring the final cutlery product is accurately replicated. The pressure is maintained until the plastic cools and solidifies inside the mold.
Advantages of Injection Molding
Injection molding offers several advantages in the production of plastic cutlery:
- High Efficiency: Injection molding allows for the rapid production of large quantities of cutlery with minimal manual intervention. The cycle time for each injection molding cycle is relatively short, making it a highly efficient process.
- Precision and Consistency: Injection molding ensures precise and consistent replication of the cutlery mold, resulting in uniformity in the shape and dimensions of the final products. This is crucial for maintaining the functionality and aesthetics of the cutlery.
- Design Freedom: The versatility of injection molding enables the production of cutlery with complex designs, patterns, and textures. The mold can be customized to incorporate various features and details, providing design freedom for manufacturers.
- Material Variety: Injection molding can accommodate a wide range of plastic materials, allowing manufacturers to choose the most suitable material for their specific cutlery requirements.
- Cost-Effective: Once the mold is created, the production cost per unit of cutlery significantly decreases, making injection molding a cost-effective manufacturing method for high-volume production.
Quality Control and Ejection
After the injected plastic has cooled and solidified inside the mold, the mold is opened, and the newly formed plastic cutlery is ejected. At this stage, quality control measures are implemented to ensure that the cutlery meets the required standards and specifications.
The ejected cutlery is inspected for any visible defects or imperfections, such as uneven surfaces, air bubbles, or incomplete filling of the mold. Any defective pieces are discarded, and only the high-quality cutlery is retained for further processing.
In some cases, additional processes may be conducted after ejection to trim off any excess plastic or to add finishing touches to the cutlery. Trimming helps achieve the desired shape and smooth edges of the cutlery, while finishing processes, such as polishing or buffing, enhance the appearance and quality of the final product.
Now that we have covered the injection molding process, let’s move on to the next steps in the production of plastic cutlery: cooling and ejection.
Step 4: Cooling and Ejection
After the injection molding process, the plastic cutlery needs to undergo the cooling and ejection stages. These steps are essential to ensure that the plastic solidifies, and the cutlery is successfully released from the molds.
Cooling Process
Once the molten plastic is injected into the mold cavity, it rapidly cools and solidifies to form the desired shape of the cutlery. The duration of the cooling process varies depending on the size and thickness of the cutlery. Cooling can occur naturally or be accelerated using cooling systems, such as water baths or cooling chambers.
The cooling process aims to achieve uniform solidification of the plastic material, ensuring that the final cutlery has the desired strength and integrity. Rapid and even cooling helps prevent deformations, warping, or unwanted stress within the cutlery.
During the cooling process, the plastic undergoes a transition from a molten state to a solid state. As the plastic cools, its molecules arrange themselves into a stable structure, providing the cutlery with the necessary strength and rigidity.
Read more: How To Use Cutlery
Ejection of the Cutlery
Once the plastic cutlery has sufficiently cooled and solidified inside the mold, the molds are opened, and the cutlery is ejected. This is typically done using ejector pins or plates within the mold, which apply force to push the cutlery out of the mold cavity.
It’s important to note that the ejection process needs to be carefully controlled to ensure that the cutlery is released without any damage or distortion. The design of the mold and the ejection system plays a crucial role in achieving a smooth and efficient ejection process.
After the cutlery is ejected from the molds, it undergoes inspection for any visible defects or imperfections. This includes checking for factors such as incomplete filling of the mold, blemishes, or inconsistencies in the surface finish. Any defective pieces are discarded, while high-quality cutlery is retained for further processing.
In some cases, additional finishing steps may be required after ejection. This can involve trimming off any excess plastic or using secondary operations, such as polishing or buffing, to enhance the appearance and quality of the cutlery. These finishing touches ensure that the final plastic cutlery is aesthetically pleasing and ready for use.
Now that we have covered the cooling and ejection stages, let’s move on to the next step: trimming and finishing the cutlery.
Step 5: Trimming and Finishing
After the plastic cutlery is ejected from the molds, it may undergo additional steps for trimming and finishing. These processes are essential to refine the shape, remove any excess material, and enhance the overall quality of the cutlery.
Trimming
Trimming is the process of removing any excess plastic or flash that may have formed during the injection molding process. Flash refers to the thin layer of excess plastic that protrudes from the edges of the cutlery. It can occur due to slight variations in pressure or temperature during the molding process.
To trim the cutlery, specialized trimming equipment or tools are used, such as blades or cutting machines. Trimming not only improves the appearance of the cutlery but also ensures that there are no rough edges or uneven surfaces that could pose a safety risk to users.
The trimming process is carefully controlled to remove the excess material without affecting the shape or structure of the cutlery. It helps achieve the desired final shape, ensuring that the cutlery looks clean and well-defined.
Finishing
In addition to trimming, the cutlery may undergo further finishing processes to enhance its appearance, functionality, and overall quality. These finishing touches can vary depending on the manufacturer’s specifications and the intended use of the cutlery.
Some common finishing processes include polishing or buffing the cutlery to achieve a smooth and shiny surface. This improves the visual appeal of the cutlery, making it more attractive to users. The polishing or buffing may be done mechanically or with the use of polishing compounds or abrasive materials.
Furthermore, the cutlery can be customized with unique textures or patterns to provide a more ergonomic grip or add a decorative element. This can be achieved through embossing, engraving, or texturing techniques, depending on the desired result.
Finishing also includes inspecting the cutlery for any remaining defects, such as scratches or blemishes. Any imperfections found during this stage are rectified or discarded to ensure that only high-quality cutlery is released for packaging and distribution.
By completing the trimming and finishing processes, the plastic cutlery is transformed into a polished and refined product that is ready for use. The attention to detail during these steps ensures that the final cutlery meets the highest standards of quality and aesthetics.
Now that we have covered the trimming and finishing stages, let’s move on to discussing the importance of quality control in the production process of plastic cutlery.
Read more: How To Clean Cutlery
Step 6: Quality Control
Quality control is a vital step in the production process of plastic cutlery. It involves rigorous inspection and testing to ensure that the cutlery meets the required standards of functionality, durability, and appearance. This step helps maintain consistency and ensures that only high-quality products are released to the market.
Inspection and Testing
During the quality control phase, the plastic cutlery is carefully inspected for any visible defects or imperfections. Trained personnel examine each piece, looking for issues such as surface irregularities, air bubbles, warping, or incomplete filling of the molds. Any defective pieces are removed from the production line.
In addition to visual inspection, specific tests may be conducted to assess the quality and performance of the cutlery. This can include tests for strength, flexibility, heat resistance, and durability. For example, plastic spoons may undergo bending tests to ensure they can withstand the pressure applied during eating without breaking or snapping.
The quality control process also involves testing the cutlery against specific industry standards. These standards vary depending on the region and the intended application of the cutlery. Compliance with these standards confirms that the product meets the necessary safety and quality requirements.
Packaging and Labeling
As part of quality control, packaging and labeling are also important considerations. The packaging should protect the cutlery during transportation and storage, preventing any damage or contamination. Additionally, labeling should provide accurate information about the product, including the type of plastic used, any certifications or standards met, and proper usage instructions.
By implementing a robust quality control process, manufacturers can identify and rectify any issues before the cutlery reaches consumers. This ensures that customers receive plastic cutlery that not only meets their expectations but also adheres to safety and quality standards.
Types of Plastic Used for Cutlery
Plastic cutlery is typically made from different types of plastics, each offering specific properties that make them suitable for different applications. The choice of plastic depends on factors such as durability, temperature resistance, and cost-effectiveness. Here are the most common types of plastics used for cutlery:
Polypropylene (PP)
Polypropylene is a popular choice for cutlery due to its strength, flexibility, and heat resistance. It is lightweight yet durable, making it suitable for everyday use. PP cutlery is resistant to high temperatures, allowing it to be used with hot food or in microwave ovens. It is also recyclable, contributing to sustainability efforts.
Polystyrene (PS)
Polystyrene is a versatile plastic used for lightweight and disposable cutlery. PS cutlery is transparent, making it aesthetically pleasing. It is commonly used for various applications due to its affordability and ease of production. However, PS cutlery may not be suitable for high-temperature applications, as it can melt or deform.
Polyethylene (PE)
Polyethylene is known for its flexibility and resistance to moisture, chemicals, and impact. PE cutlery is commonly used for disposable spoons, as its flexibility allows for easy scooping and stirring. It can withstand low and high temperatures, making it suitable for both hot and cold food applications.
Other Plastics
In addition to PP, PS, and PE, other types of plastics may also be used for cutlery production. Acrylonitrile Butadiene Styrene (ABS) is a durable and impact-resistant plastic often used for heavy-duty cutlery applications. Compostable or biodegradable plastics, such as polylactic acid (PLA), are also gaining popularity as environmentally friendly alternatives to traditional plastics.
The choice of plastic for cutlery production depends on various factors, including the desired properties, cost, and environmental considerations. Manufacturers carefully assess these factors to determine the most suitable plastic for their specific cutlery requirements.
Now that we have explored the types of plastics used for cutlery, we will move on to discussing the environmental impact of plastic cutlery and potential alternatives.
Read more: What Is Cutlery
Polypropylene (PP)
Polypropylene (PP) is a widely used plastic in the production of cutlery due to its excellent balance of strength, flexibility, and heat resistance. PP cutlery exhibits a range of desirable properties that make it a popular choice for both manufacturers and consumers.
Strength and Durability
PP cutlery is known for its strength and durability. It can withstand the rigors of regular use without bending or breaking, making it reliable for various dining applications. This strength is especially important for cutlery items such as forks, which need to withstand the force of piercing and lifting food.
Flexibility
Flexibility is another advantageous property of PP cutlery. PP can be molded into various shapes and designs, allowing manufacturers to create cutlery with ergonomic and user-friendly features. This flexibility is particularly beneficial for spoons, which need to be able to scoop and hold various food textures.
Heat Resistance
PP cutlery can withstand high temperatures without melting or deforming, making it suitable for use with hot foods and beverages. This heat resistance ensures that the cutlery remains intact and does not release harmful chemicals when used with hot substances. It also makes PP cutlery suitable for microwave use, as it can withstand the heat generated during the reheating process.
Read more: How To Remove Rust On Cutlery
Recyclability
One of the significant advantages of PP cutlery is its recyclability. PP is a widely accepted plastic for recycling, and it can be processed and reused to produce various plastic products, reducing the dependence on virgin plastic materials. Recycling PP cutlery contributes to sustainability efforts and helps reduce environmental impact.
Hygienic and Easy to Clean
PP cutlery is hygienic and easy to clean, making it suitable for use in both domestic and commercial settings. It has a low moisture absorption rate, which prevents staining and the retention of food odors. This property ensures that the cutlery can be cleaned thoroughly, maintaining a high level of hygiene.
Overall, PP cutlery offers a reliable and versatile option for everyday dining needs. Its strength, flexibility, heat resistance, recyclability, and ease of cleaning make it a preferred choice for manufacturers and consumers alike. However, it’s important to consider the environmental impact of plastic cutlery and explore alternatives that are more sustainable.
Now that we have explored the features of PP cutlery, let’s discuss the other types of plastics commonly used for cutlery production.
Polystyrene (PS)
Polystyrene (PS) is a versatile plastic widely used in the production of cutlery. It possesses unique characteristics that make it a popular choice for both manufacturers and consumers.
Clarity and Transparency
One of the notable features of PS cutlery is its clarity and transparency. PS has excellent optical properties, allowing it to transmit light without significant distortion. This transparency enhances the visual appeal of PS cutlery, making it particularly suitable for applications where aesthetics play a crucial role.
Read more: How To Store Cutlery Without Drawers
Lightweight and Easy to Handle
PS cutlery is lightweight, making it easy to handle and comfortable to use. Its lightweight nature makes it suitable for applications where ease of use and convenient disposal are essential factors, such as in fast food restaurants, outdoor events, and picnics.
Affordability
PS cutlery is cost-effective, making it an attractive choice for manufacturers. The relative affordability of PS makes it an ideal material for disposable or single-use cutlery applications, where cost-efficiency is a significant consideration.
Versatility in Design
PS can be easily molded into various shapes, making it a versatile material for cutlery production. It allows manufacturers to create unique and intricate designs, catering to different dining preferences and occasions. These design possibilities make PS cutlery well-suited for events where presentation and aesthetics are paramount.
Limitations in Heat Resistance
It’s important to note that PS has limitations in terms of heat resistance. It may not be suitable for applications involving high temperatures, as it can deform or melt when exposed to excessive heat. Therefore, PS cutlery is typically recommended for use with cold or room temperature food and beverages.
While PS cutlery offers several advantages, it is essential to consider the environmental impact of disposable plastic cutlery. PS is a non-biodegradable plastic and can contribute to plastic waste. As a result, there has been growing concern about the impact of PS cutlery on the environment.
It’s crucial to explore alternative solutions, such as reusable or compostable cutlery, that can help reduce plastic pollution. However, PS cutlery still plays a significant role in certain applications where its unique properties are valued.
Now that we have discussed the features of PS cutlery, let’s delve into another commonly used plastic in cutlery production.
Read more: What Is A Cutlery Set
Polyethylene (PE)
Polyethylene (PE) is a versatile plastic widely used in the production of cutlery. It offers various beneficial properties that make it suitable for different dining applications.
Flexibility and Durability
PE cutlery is known for its flexibility, which allows for easy bending and scooping. This flexibility makes PE spoons ideal for various types of food, such as scooping ice cream or stirring soups. Despite its flexibility, PE cutlery is also durable and able to withstand regular use.
Chemical and Moisture Resistance
PE has excellent resistance to chemicals and moisture. This property ensures that PE cutlery remains intact and reliable even when in contact with liquids or food substances. It also prevents the cutlery from absorbing moisture or retaining food odors.
Read more: How To Store Cutlery Without Drawers
Lightweight and Easy to Handle
PE cutlery is lightweight, making it easy to handle and convenient for single-use purposes. Its lightweight nature is particularly advantageous in settings such as picnics, outdoor events, or fast food restaurants, where disposable cutlery is preferred for its ease of use and quick disposal.
Heat Resistance
PE cutlery has good heat resistance, allowing it to withstand both high and low temperatures. It remains stable and does not deform when exposed to hot or cold substances, making it suitable for various dining applications. PE cutlery can be used with hot foods and beverages without any concern of melting or warping.
Read more: How To Remove Rust On Cutlery
Recyclability
PE is a recyclable plastic, contributing to efforts in reducing environmental impact. Recycling PE cutlery helps to minimize the reliance on virgin plastic materials and decreases the amount of plastic waste ending up in landfills or polluting natural environments.
It’s important to note that while PE cutlery offers several advantages, including its flexibility, durability, and heat resistance, there are growing concerns about plastic pollution and the impact of disposable cutlery on the environment. Exploring more sustainable alternatives, such as reusable or compostable cutlery, can help mitigate these concerns.
However, PE cutlery still has its place in various dining settings where convenience and affordability are primary considerations. With proper waste management and recycling initiatives in place, the environmental impact of PE cutlery can be minimized.
Now that we have discussed the features of PE cutlery, let’s explore other types of plastics used in cutlery production.
Others
In addition to polypropylene (PP), polystyrene (PS), and polyethylene (PE), other types of plastics may be used in the production of cutlery, depending on specific requirements.
Acrylonitrile Butadiene Styrene (ABS)
Acrylonitrile Butadiene Styrene (ABS) is a durable and impact-resistant plastic. It is commonly used for heavy-duty cutlery applications, where additional strength and resilience are required. ABS cutlery can withstand more demanding usage without breaking or bending, making it suitable for use in fast-food restaurants or cafeterias.
Read more: How To Roll Cutlery In A Napkin
Compostable or Biodegradable Plastics
Compostable or biodegradable plastics have gained popularity as environmentally friendly alternatives to traditional plastics. These plastics, such as polylactic acid (PLA), are derived from renewable sources, such as cornstarch, and are designed to break down into natural components when subjected to the right conditions. Cutlery made from compostable or biodegradable plastics can reduce the environmental impact associated with plastic waste.
It is important to note that while compostable or biodegradable plastics offer potential benefits, proper disposal infrastructure and conditions are necessary for them to degrade effectively. Without proper composting facilities or suitable environmental conditions, their degradation may be limited, and they could persist in the environment for an extended period.
The choice of plastic for cutlery production depends on specific requirements, such as strength, heat resistance, and environmental considerations. Manufacturers balance these factors to select the most appropriate plastic for their particular cutlery applications.
Environmental Impact of Plastic Cutlery
The widespread use of plastic cutlery has raised concerns about its environmental impact, particularly regarding plastic waste and pollution. Here are some key points to consider:
Issues with Disposal
Plastic cutlery, often used for only a short period, contributes to the accumulation of plastic waste. The lightweight and disposable nature of plastic cutlery make it prone to ending up in landfills or being improperly disposed of, leading to environmental pollution.
Plastic waste takes hundreds of years to degrade naturally, often breaking down into smaller microplastics that can enter the soil, water bodies, and food systems. These microplastics pose significant risks to ecosystems, wildlife, and human health.
Alternatives and Solutions
Efforts are underway to address the environmental impact of plastic cutlery by promoting alternative solutions:
Reusable Cutlery:
Encouraging the use of reusable cutlery, such as stainless steel or bamboo, can significantly reduce the consumption of single-use plastic cutlery. It involves carrying personal cutlery or using communal cutlery in dining establishments, helping to minimize plastic waste.
Compostable and Biodegradable Cutlery:
Compostable or biodegradable cutlery made from plant-based materials offers a more sustainable option. These materials break down more readily under appropriate composting conditions, returning to the environment in a shorter time frame.
Advancements in Plastic Recycling:
Technological advancements in plastic recycling processes enable more effective recycling of plastic cutlery. Improvements in waste segregation, collection, and recycling infrastructure can help divert plastic cutlery from landfills and promote the creation of new plastic products from recycled materials.
It is important for individuals, businesses, and policymakers to promote sustainable practices and raise awareness about the environmental impact of plastic cutlery. By adopting alternative solutions and supporting initiatives that reduce plastic waste, we can work towards a more sustainable future.
Now that we have discussed the environmental impact of plastic cutlery, let’s conclude our exploration of this topic.
Read more: How To Pack Cutlery For Moving
Issues with Disposal
Plastic cutlery poses significant challenges when it comes to disposal, leading to various environmental issues. Here are some key considerations regarding the disposal of plastic cutlery:
Landfill Accumulation
Plastic cutlery is often seen as a convenient option for single-use purposes, leading to a substantial accumulation of waste in landfills. Due to its lightweight nature, plastic cutlery can fill up landfill space quickly, exacerbating the strain on waste management systems.
Persistence of Plastic Waste
Plastic cutlery takes hundreds of years to degrade naturally, contributing to the persistence of plastic waste in the environment. Plastics break down into smaller microplastics over time, which can have detrimental effects on ecosystems and organisms at various levels of the food chain.
Litter and Marine Pollution
Improper disposal of plastic cutlery, such as littering or inadequate waste management, can result in these items ending up in natural ecosystems, including rivers, lakes, and oceans. Plastic cutlery, along with other plastic waste, poses a severe threat to marine life through entanglement and ingestion, leading to detrimental impacts on ecosystems and biodiversity.
Read more: How To Pack Cutlery For Moving
Sustainability Challenges
The production of plastic cutlery consumes significant amounts of energy and fossil fuels, contributing to greenhouse gas emissions and environmental degradation. Additionally, the reliance on virgin plastic materials further depletes finite resources. These sustainability challenges highlight the need for more responsible practices and alternatives to plastic cutlery.
Promoting Sustainable Solutions
To address the issues associated with the disposal of plastic cutlery, it is crucial to adopt sustainable solutions:
Reduce Single-Use Consumption:
Minimizing the use of single-use plastic cutlery by opting for reusable alternatives can help to reduce waste. This can be achieved by carrying personal cutlery or using durable options available at dining establishments.
Improve Waste Management:
Efficient waste management practices, such as recycling and proper segregation, are essential for diverting plastic cutlery from landfills. Investing in infrastructure and raising awareness about recycling programs can encourage individuals and businesses to dispose of plastic cutlery responsibly.
Promote Biodegradable and Compostable Alternatives:
Switching to biodegradable or compostable cutlery made from plant-based materials offers a more sustainable option. These materials break down more readily under appropriate composting conditions, reducing the long-term environmental impact of plastic waste.
By addressing the issues associated with disposal and promoting sustainable alternatives, we can work towards reducing the environmental impact of plastic cutlery and moving closer to a more sustainable future.
Now that we have explored the issues with disposal, let’s conclude our discussion on plastic cutlery and its environmental impact.
Alternatives and Solutions
The environmental impact of plastic cutlery has prompted the exploration of alternative solutions that can help mitigate plastic waste and pollution. Here are some alternatives and solutions to consider:
Reusable Cutlery
Encouraging the use of reusable cutlery is an effective way to reduce plastic waste. Individuals can carry their own reusable cutlery sets made from materials like stainless steel or bamboo. Restaurants and food establishments can also provide reusable cutlery options and promote their usage to customers.
Read more: How To Pack Cutlery For Moving
Compostable and Biodegradable Cutlery
Another eco-friendly option is compostable or biodegradable cutlery. Cutlery made from plant-based materials, such as polylactic acid (PLA) or bagasse (sugarcane fiber), can break down naturally in composting facilities or under suitable environmental conditions. These materials offer a more sustainable alternative to conventional plastic cutlery.
Promote Recycling and Proper Disposal
Efforts should be made to raise awareness about recycling programs and facilitate proper disposal of plastic cutlery. Communities, businesses, and municipalities can improve waste management systems, enhance recycling infrastructure, and clearly communicate recycling guidelines to ensure that plastic cutlery is properly recycled instead of ending up in landfills or polluting the environment.
Legislation and Regulation
Government bodies can play a crucial role in addressing the environmental impact of plastic cutlery by implementing regulations and legislation. This can include measures such as bans or restrictions on single-use plastic cutlery, promoting the use of eco-friendly alternatives, and supporting initiatives to reduce plastic waste.
Consumer Education
Education and awareness campaigns aimed at consumers can help highlight the environmental consequences of plastic cutlery and encourage behavior change. Providing information about alternative options, the importance of recycling, and the benefits of reusable or compostable cutlery can empower individuals to make more sustainable choices.
Read more: How To Pack Cutlery For Moving
Conclusion
The production and disposal of plastic cutlery have significant environmental implications, but there are alternatives and solutions available to address these issues. By promoting reusable cutlery, compostable and biodegradable options, recycling initiatives, and responsible waste management, we can reduce plastic waste and mitigate the impact of plastic cutlery on the environment.
It is essential for individuals, businesses, and governments to work together to create a sustainable future. By embracing these alternatives and implementing sustainable practices, we can move towards a world where plastic cutlery no longer poses a threat to our planet’s ecosystems and resources.
Let’s make conscious choices and take actions that contribute to a cleaner and greener future for generations to come.
Frequently Asked Questions about How Is Plastic Cutlery Made
Was this page helpful?
At Storables.com, we guarantee accurate and reliable information. Our content, validated by Expert Board Contributors, is crafted following stringent Editorial Policies. We're committed to providing you with well-researched, expert-backed insights for all your informational needs.
0 thoughts on “How Is Plastic Cutlery Made”