Home>diy>Building & Construction>How Does Subcontracting Work In Construction
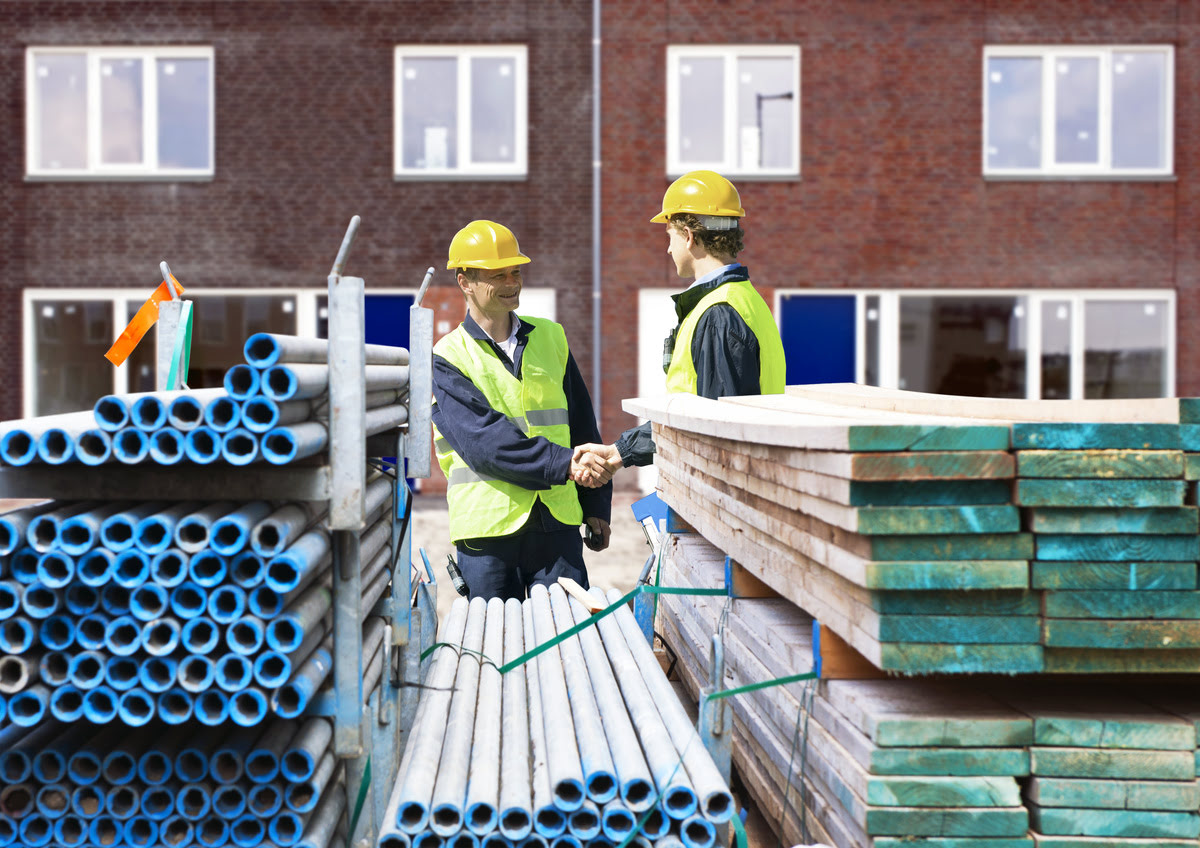
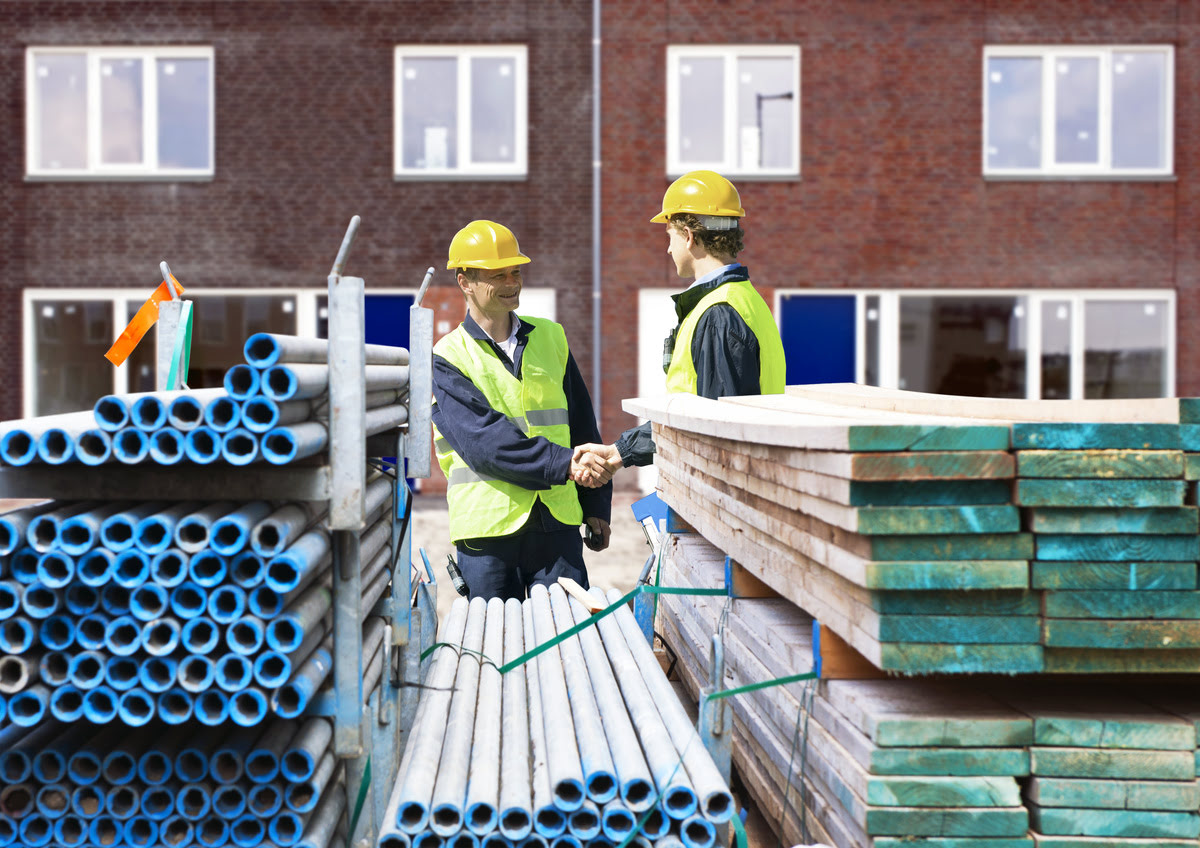
Building & Construction
How Does Subcontracting Work In Construction
Modified: August 27, 2024
Discover how subcontracting works in the building construction industry and understand the processes involved for successful project completion.
(Many of the links in this article redirect to a specific reviewed product. Your purchase of these products through affiliate links helps to generate commission for Storables.com, at no extra cost. Learn more)
Introduction
Welcome to the world of construction, where collaboration and teamwork are essential for successful project completion. Construction projects, whether residential, commercial, or industrial, are complex undertakings that require the expertise of various professionals in different trades. To ensure smooth operations and timely delivery, construction companies often rely on subcontractors to handle specific aspects of the project.
In this article, we will explore the concept of subcontracting in the construction industry, discussing its definition, reasons, benefits, types of subcontractors, roles and responsibilities, the subcontracting process, factors to consider when selecting subcontractors, challenges, risks, and best practices. Whether you are a construction professional or someone interested in gaining a better understanding of how subcontracting works, this article will provide valuable insights.
Subcontracting in construction refers to the practice of hiring external companies or individuals, known as subcontractors, to perform specific tasks or provide specialized services that are beyond the capabilities of the main contractor. These tasks can range from electrical and plumbing work to carpentry, painting, and landscaping. The subcontractors work under the supervision of the main contractor and play a critical role in completing different stages of the project.
One of the primary reasons for subcontracting in construction is the need for specialized expertise. Construction projects involve a wide range of skills and trades, and it is often more cost-effective and efficient to bring in subcontractors who specialize in specific areas. For example, a construction company may hire a subcontractor who specializes in installing HVAC systems or another subcontractor skilled in concrete pouring and finishing. This allows the main contractor to leverage the subcontractor’s expertise and focus on managing the overall project.
There are several benefits to subcontracting in construction. Firstly, subcontractors bring specialized knowledge and experience to the project. They are experts in their respective fields and are up-to-date with the latest industry practices and regulations. This ensures that the work is carried out to the highest standards and meets all necessary requirements. Additionally, subcontractors often have their own tools, equipment, and resources, reducing the need for the main contractor to invest in additional resources.
Furthermore, subcontracting allows the main contractor to scale resources as needed. Construction projects can be dynamic, with fluctuating demands for labor and expertise at different stages. By subcontracting, the main contractor can easily adjust the workforce and bring in additional manpower when required. This flexibility helps to optimize efficiency and minimize delays.
Subcontractors in construction can be classified into different types based on their areas of expertise. Common types include electrical subcontractors, plumbing subcontractors, HVAC subcontractors, carpentry subcontractors, painting subcontractors, roofing subcontractors, and landscaping subcontractors. Each type of subcontractor brings a specific skill set to the project, contributing to the overall construction process.
Now that we have covered the basics of subcontracting in construction, let’s dive deeper into the roles and responsibilities of subcontractors, the subcontracting process, factors to consider when selecting subcontractors, challenges and risks involved, and best practices for effective subcontracting in construction.
Key Takeaways:
- Subcontracting in construction allows main contractors to bring in specialized experts for tasks like electrical work, plumbing, and carpentry, leading to higher quality work and efficient resource allocation.
- Effective subcontracting requires clear communication, proactive project management, and building positive relationships with subcontractors to ensure successful construction projects.
Read more: How Does Retention Work In Construction
Definition of Subcontracting in Construction
Subcontracting in the construction industry is a common practice wherein a contractor hires external entities or individuals, referred to as subcontractors, to perform specific tasks or provide specialized services as part of a construction project. The subcontractors work under the supervision of the main contractor and play a crucial role in completing various stages of the project.
Subcontracting involves outsourcing certain portions of a construction project to subcontractors who possess the necessary expertise and skills in specific trades. These trades can include electrical work, plumbing, carpentry, painting, roofing, landscaping, and more. By subcontracting, the main contractor can leverage the expertise of these specialized subcontractors and streamline the construction process.
When a construction project is undertaken, the main contractor, sometimes referred to as the general contractor, is responsible for overseeing the project as a whole. They are typically responsible for managing the construction timeline, procuring materials, coordinating with subcontractors, ensuring compliance with building codes and regulations, and maintaining quality control.
However, due to the diverse nature of construction projects, it is often not feasible for a single contractor to possess expertise in all trades required for the project. This is where subcontracting comes into play. The main contractor can subcontract specific portions of the project to subcontractors who specialize in those particular trades. This allows for more efficient and effective completion of the project while ensuring that the work is carried out by experienced professionals.
Subcontractors in construction are typically small to medium-sized businesses or independent contractors who have developed expertise and specialized skills in a particular trade. They may have their own crew, equipment, and resources to carry out the work assigned to them. Subcontractors often enter into contractual agreements with the main contractor, specifying the scope of work, timelines, payment terms, and other relevant details.
It is important to note that subcontractors are not employed directly by the main contractor. Instead, they are hired on a project-by-project basis to perform specific tasks within the construction project. The main contractor retains overall management and accountability for the project, while the subcontractor is responsible for executing their assigned tasks according to the agreed-upon terms and specifications.
Subcontracting offers several advantages in the construction industry. It allows main contractors to access specialized skills and expertise, enables more efficient resource allocation, reduces the need to invest in additional equipment or labor, and promotes collaboration and teamwork among different trades. However, successful subcontracting requires effective communication, coordination, and project management to ensure seamless integration of subcontractor work into the overall construction process.
Reasons for Subcontracting in Construction
Subcontracting plays a vital role in the construction industry, offering numerous advantages to main contractors and project owners. There are several reasons why subcontracting is commonly practiced in construction projects:
- Specialized Expertise: Construction projects often require a wide range of skills and trades. Subcontracting allows main contractors to bring in subcontractors who specialize in specific trades or have expertise in niche areas. These subcontractors have the necessary knowledge, experience, and certifications to perform their tasks efficiently and effectively. By leveraging their specialized expertise, the quality of work can be enhanced, ensuring that each aspect of the project is handled by trained professionals.
- Optimal Resource Allocation: Construction projects have varying demands for labor, equipment, and materials at different stages. Subcontracting allows main contractors to allocate resources optimally by leveraging the resources of subcontractors. This avoids overstaffing or underutilization of resources, resulting in cost savings and improved project efficiency. The subcontractors bring their own tools, equipment, and workforce, reducing the burden on the main contractor to acquire and maintain additional resources.
- Time Efficiency: Subcontracting can significantly improve the timeline of a construction project. By employing specialized subcontractors, the main contractor can ensure that each trade is executed in a timely manner. This eliminates the need for the main contractor to coordinate and manage various trades simultaneously, reducing the risk of delays. The subcontractors’ expertise in their respective fields allows for quicker completion of tasks, minimizing downtime and ensuring smooth project progression.
- Risk Mitigation: Construction projects entail inherent risks, including safety hazards, compliance with building codes, and potential financial liabilities. Hiring subcontractors who specialize in their respective trades can mitigate these risks. Subcontractors are typically well-versed in industry regulations, safety protocols, and legal requirements. They bring their expertise and experience to adhere to safety standards and ensure compliance, reducing the risk of accidents, errors, and subsequent liabilities.
- Cost-Effectiveness: Subcontracting can often be a cost-effective solution for construction projects. By hiring subcontractors for specific trades, main contractors can avoid the need to invest in training their own staff or acquiring specialized equipment for tasks that may not be recurring. Subcontractors bring their own tools and equipment, reducing the capital investment required from the main contractor. Additionally, subcontractors are responsible for their own insurance, taxes, and benefits, alleviating a financial burden for the main contractor.
In summary, subcontracting in construction offers benefits such as access to specialized expertise, efficient resource allocation, time savings, risk mitigation, and cost-effectiveness. By leveraging the knowledge and skills of subcontractors, main contractors can enhance the overall quality, efficiency, and success of construction projects.
Benefits of Subcontracting in Construction
Subcontracting in the construction industry provides several benefits to main contractors, project owners, and even subcontractors themselves. Understanding these benefits is crucial for making informed decisions regarding project management and resource allocation. Here are some advantages of subcontracting in construction:
- Specialized Expertise: Subcontracting allows main contractors to tap into the specialized expertise of subcontractors. Construction projects often require various trades, such as electrical work, plumbing, carpentry, and roofing. Subcontractors are professionals who have honed their skills and knowledge in specific trades, ensuring that each aspect of the project is handled by experts. This results in higher quality workmanship and minimizes the risk of errors or rework.
- Efficient Resource Allocation: Construction projects have fluctuating resource requirements at different stages. Subcontracting enables main contractors to allocate resources efficiently. By bringing in subcontractors, the main contractor can leverage their resources, including tools, equipment, and labor, without the need for additional investment. This flexibility allows for optimized resource utilization and improved cost management.
- Time Savings: Subcontractors specialize in their respective trades, allowing them to work faster and more efficiently. This leads to time savings in project execution as subcontractors focus on their specific tasks without the need for constant coordination with other trades. By streamlining the construction process, subcontracting helps to reduce project timelines and potential delays, ensuring timely project completion.
- Reduced Liability: Subcontractors are responsible for their own workers’ compensation, liability insurance, and compliance with regulations. This reduces the liability of the main contractor in case of unforeseen accidents or legal issues related to the subcontractor’s work. Subcontractors also bring their own expertise in safety procedures and compliance, minimizing the risk of accidents and ensuring adherence to industry standards.
- Cost-Effectiveness: Subcontracting can contribute to cost savings in construction projects. Instead of hiring and training an in-house team for every specialized trade, main contractors can hire subcontractors on an as-needed basis. Subcontractors bring their own tools and equipment, reducing the need for the main contractor to invest in costly resources. Additionally, subcontractors are responsible for their own taxes, insurance, and benefits, alleviating financial burdens for the main contractor.
- Flexibility: Subcontracting provides flexibility in workforce allocation. Construction projects often have varying labor demands due to different stages and tasks. Subcontracting allows the main contractor to easily scale up or down the workforce as needed, bringing in additional subcontractors when required. This flexibility enables main contractors to respond to project changes promptly and efficiently.
Overall, subcontracting in construction offers numerous benefits, including access to specialized expertise, efficient resource allocation, time savings, reduced liability, cost-effectiveness, and workforce flexibility. Main contractors can enhance project quality, streamline operations, and improve project outcomes by leveraging the skills and knowledge of subcontractors. Subcontractors, on the other hand, can benefit from steady work opportunities and the chance to showcase their specialized skills in the construction industry.
Types of Construction Subcontractors
In the construction industry, subcontractors are hired to perform specific tasks or provide specialized services as part of a construction project. These subcontractors play a critical role in the successful completion of the project. There are various types of construction subcontractors, each specializing in a specific trade or aspect of the construction process. Here are some common types of construction subcontractors:
- Electrical Subcontractors: Electrical subcontractors specialize in electrical installations, wiring, and systems within a building. They are responsible for the installation, maintenance, and repair of electrical systems, including lighting, power outlets, electrical panels, and wiring connections. Electrical subcontractors ensure that electrical work is done safely and in compliance with relevant codes and regulations.
- Plumbing Subcontractors: Plumbing subcontractors handle the installation, repair, and maintenance of plumbing systems within a building. They are responsible for the installation of pipes, fixtures, valves, and appliances that ensure the proper functioning of water supply, drainage, and sewage systems. Plumbing subcontractors work closely with other trades, such as carpenters and electricians, to ensure seamless integration of their work.
- HVAC Subcontractors: HVAC (Heating, Ventilation, and Air Conditioning) subcontractors are specialized in the installation, repair, and maintenance of heating, cooling, and ventilation systems in buildings. They ensure that the indoor climate is comfortable and conducive to occupants’ needs. HVAC subcontractors handle tasks like ductwork installation, HVAC unit placement, and maintenance of HVAC systems to ensure energy efficiency and proper airflow.
- Carpentry Subcontractors: Carpentry subcontractors specialize in woodworking and structural work within a construction project. They handle tasks such as framing, flooring installation, drywall work, cabinetry, and finishing carpentry. Carpentry subcontractors are skilled in using various tools and techniques to create structural frameworks and aesthetically appealing features of a building.
- Painting Subcontractors: Painting subcontractors are responsible for applying paint and finishes to interior and exterior surfaces of a building. They handle tasks such as surface preparation, priming, and applying coats of paint or other finishes. Painting subcontractors have knowledge of different paint types, application methods, and color schemes to ensure a high-quality and visually appealing finish.
- Roofing Subcontractors: Roofing subcontractors specialize in the installation, repair, and maintenance of roofing systems. They handle tasks such as laying roofing materials, installing insulation, and ensuring proper drainage. Roofing subcontractors work with different types of roofing materials, including shingles, tiles, metal sheets, and membranes, to provide weatherproof and durable roofs for buildings.
- Landscaping Subcontractors: Landscaping subcontractors focus on the outdoor areas of a construction project. They are responsible for the design, installation, and maintenance of landscape elements such as gardens, lawns, trees, shrubs, and hardscape features. Landscaping subcontractors enhance the aesthetics and functionality of outdoor spaces, creating visually appealing and sustainable landscapes around the building.
These are just a few examples of the various types of construction subcontractors. Depending on the complexity and scope of a construction project, other specialized subcontractors may be required, such as flooring subcontractors, concrete subcontractors, masonry subcontractors, and more. Each subcontractor brings their unique skills and expertise to the project, contributing to the overall construction process and ensuring the successful realization of the project’s goals.
Read more: How Does Bidding Work In Construction
Roles and Responsibilities of Subcontractors in Construction
Subcontractors play a crucial role in the construction industry, as they are hired by main contractors to perform specific tasks or provide specialized services within a construction project. They bring their expertise in various trades and contribute to the overall success of the project. Here are some important roles and responsibilities of subcontractors in construction:
- Professional Expertise: Subcontractors are hired for their specialized skills and knowledge in specific trades or areas of expertise. They are expected to perform their assigned tasks with a high level of professionalism and proficiency. Subcontractors must stay updated with the latest industry standards, regulations, and best practices relevant to their trade to ensure the quality and compliance of their work.
- Communication and Coordination: Subcontractors need to maintain effective communication and coordination with the main contractor and other subcontractors involved in the project. They must follow the project’s timeline and provide regular updates on the progress of their work. Clear communication is vital to ensure that all parties are informed of any changes, challenges, or issues that may arise during the construction process.
- Execution of Tasks: Subcontractors are responsible for executing their assigned tasks according to the project’s specifications, plans, and schedule. They must adhere to the highest standards of craftsmanship and workmanship in their trade. Subcontractors should ensure proper installation, assembly, or construction techniques, paying attention to detail while maintaining efficiency and meeting project requirements.
- Worksite Safety: Subcontractors have a responsibility to prioritize worksite safety. They must adhere to safety regulations, implement safe work practices, and use personal protective equipment to protect themselves and others on the construction site. This includes identifying and mitigating potential hazards related to their work and promptly reporting any safety concerns to the main contractor.
- Quality Control: Subcontractors must take responsibility for the quality of their work. They should conduct regular inspections and tests to ensure that their work meets the required standards and specifications. Any defects or deficiencies should be promptly addressed and corrected. Subcontractors should work collaboratively with the main contractor to maintain and improve the overall quality of the construction project.
- Documenting and Reporting: Subcontractors should maintain accurate documentation of their work, including invoices, receipts, permits, and any other relevant documentation. They should also provide progress reports and updates to the main contractor as required. This documentation is valuable for record-keeping, billing purposes, and future reference in case of any disputes or warranty claims.
- Professional Conduct: Subcontractors are expected to conduct themselves professionally while on the construction site. This includes being punctual, respecting others’ property, maintaining a tidy workspace, and communicating courteously with all stakeholders. Subcontractors should also resolve any conflicts or disputes in a professional manner, working towards collaborative solutions that prioritize the project’s success.
By fulfilling these roles and responsibilities, subcontractors contribute to the smooth execution of construction projects. Their expertise, professionalism, and commitment ensure that their assigned tasks are completed to the highest standards, contributing to the overall success and quality of the project.
When subcontracting in construction, make sure to clearly define the scope of work, timeline, and payment terms in the subcontract agreement to avoid misunderstandings and disputes.
Subcontracting Process in Construction
The subcontracting process in construction involves a series of steps to identify, hire, and manage subcontractors for specific tasks or services within a construction project. An effective subcontracting process ensures that the project runs smoothly, subcontractors are aligned with the project goals, and the work is completed to the required standards. Here are the key steps involved in the subcontracting process:
- Identify Subcontracting Needs: The first step is to identify the specific tasks or trades that require subcontractors. The main contractor assesses the project requirements and determines which areas require specialized expertise beyond their capabilities. This includes considering the scope of work, timeline, and budget constraints.
- Prequalification and Selection: Once the subcontracting needs are identified, the main contractor begins the prequalification and selection process. This involves researching and identifying potential subcontractors who have the necessary expertise, experience, and resources. The main contractor may request bids or proposals from interested subcontractors and evaluate them based on criteria such as qualifications, past performance, reputation, and cost.
- Negotiation and Contracting: After selecting the subcontractors, the main contractor engages in negotiations to determine the terms and conditions of the subcontracting agreement. This includes discussing project scope, pricing, timelines, payment terms, insurance requirements, and other relevant details. Once the negotiations are finalized, a legally binding subcontract agreement is prepared and signed by both parties.
- Coordination and Planning: Once the subcontractors are onboarded, the main contractor works closely with them to coordinate and plan their work within the overall project schedule. This involves aligning subcontractor activities with other trades, establishing communication channels, and sharing project plans, specifications, and timelines. Regular meetings and updates help streamline collaboration and ensure a cohesive construction process.
- Supervision and Quality Control: The main contractor is responsible for supervising and managing the subcontractors’ work. They monitor progress, review deliverables, and ensure that the work meets the required quality standards and specifications. Regular inspections, testing, and quality control procedures are implemented to identify and address any issues or deficiencies early on.
- Paying Subcontractors: Payment terms and processes are established in the subcontract agreement. The main contractor is responsible for ensuring timely and accurate payment to subcontractors for the work completed. This may involve verifying invoices, tracking progress, and adhering to agreed-upon payment schedules. Maintaining transparent and efficient payment processes helps to foster positive relationships with subcontractors.
- Documentation and Closeout: Throughout the subcontracting process, both the main contractor and subcontractors maintain documentation related to their work. This includes contracts, change orders, progress reports, invoices, warranties, permits, and other relevant documentation. At the closeout of the project, all documentation is reviewed, finalized, and archived for future reference, warranty claims, or legal purposes.
Effective communication, collaboration, and project management are crucial throughout the subcontracting process. By following these steps and establishing clear expectations and processes, the main contractor can ensure that subcontractors are aligned with the project goals and deliver their work to the required standards, ultimately contributing to the successful completion of the construction project.
Factors to Consider When Selecting Subcontractors in Construction
Selecting the right subcontractors is crucial for the success of a construction project. The quality of their work, reliability, and adherence to project requirements play a significant role in delivering a project on time and within budget. When choosing subcontractors, main contractors should consider several factors to ensure a successful partnership. Here are key factors to consider when selecting subcontractors in construction:
- Experience and Expertise: Assess the subcontractor’s experience and expertise in the specific trade required for the project. Review their track record, completed projects, and industry reputation. It is important to choose subcontractors with a proven ability to deliver high-quality work that meets project requirements.
- Qualifications and Certifications: Verify that subcontractors possess the necessary qualifications, licenses, and certifications to perform the work. This includes confirming that they comply with local building codes, safety regulations, and industry standards. Working with qualified subcontractors reduces any potential liability and ensures compliance with regulatory requirements.
- References and Past Performance: Request and review references from previous clients or projects the subcontractor has worked on. This provides insights into their reliability, workmanship, and ability to meet project deadlines. Contacting these references allows for a firsthand account of the subcontractor’s performance and helps in making an informed decision.
- Financial Stability: Consider the financial stability of subcontractors to ensure they can sustain their operations throughout the duration of the project. Assess their financial reputation, payment history, and ability to manage their finances. A financially stable subcontractor is less likely to encounter financial difficulties that could impact their work on the project.
- Availability and Capacity: Evaluate the subcontractor’s availability and capacity to take on the project. Consider their current workload and whether they have sufficient resources, including manpower and equipment, to handle the project’s demands. It is essential to choose subcontractors who can commit to the project timeline and deliver their work within the specified timeframe.
- Communication and Collaboration: Effective communication and collaboration are vital for a successful subcontractor relationship. Assess the subcontractor’s ability to communicate clearly and promptly. Evaluate their willingness to collaborate with the main contractor, other subcontractors, and stakeholders. Choose subcontractors who demonstrate a proactive and responsive communication approach.
- Safety Record: Safety is a critical consideration in construction. Review the subcontractor’s safety record and their commitment to maintaining a safe work environment. Evaluate their safety policies, training programs, and incident history. Choosing subcontractors who prioritize safety helps mitigate risks and ensures a safe construction site.
- Insurance Coverage: Verify that the subcontractor has adequate insurance coverage, including general liability insurance, workers’ compensation insurance, and property damage insurance. This protects both the main contractor and subcontractor in case of accidents, damage, or other unforeseen events on the construction site.
- Cost and Value: While cost is a consideration, it should not be the sole determining factor. Assess the subcontractor’s pricing in relation to the value they bring. Evaluate their ability to deliver work of high quality, meet project timelines, and provide reliable service. Choosing a subcontractor based on a balance of cost and value ensures the best outcome for the project.
By considering these factors when selecting subcontractors, main contractors can make informed decisions that align with the project’s requirements and goals. Thorough evaluation and due diligence contribute to building strong partnerships and maximizing the chances of project success.
Challenges and Risks in Construction Subcontracting
While subcontracting plays a vital role in construction projects, it is not without its challenges and risks. Main contractors and project owners must be aware of these potential pitfalls to effectively manage subcontracting relationships and mitigate associated risks. Here are some common challenges and risks in construction subcontracting:
- Quality Control: Maintaining consistent quality across subcontractors can be a challenge. Each subcontractor brings their own work practices, standards, and level of craftsmanship. Ensuring that subcontractors adhere to the project’s quality requirements and deliver work of a consistent standard requires effective communication, supervision, and quality control measures from the main contractor.
- Coordination and Project Management: Coordinating multiple subcontractors to ensure seamless project execution can be complex. Each subcontractor has its own schedule, priorities, and dependencies. Managing and coordinating their work in sync with other trades requires strong project management skills, clear communication, and regular updates to maintain smooth project progress.
- Timeline and Schedule: Delays in subcontractor work can have a domino effect on the overall project timeline. Subcontractors may face unexpected delays due to unforeseen circumstances, such as labor shortages, equipment breakdowns, or weather conditions. Main contractors need to closely monitor subcontractor progress, address delays promptly, and have contingency plans in place to mitigate potential schedule disruptions.
- Contractual and Legal Issues: Subcontracting agreements can be complex, involving various contractual terms, warranties, indemnifications, and dispute resolution mechanisms. Failure to clearly define the roles, responsibilities, and expectations in the subcontracting agreement can lead to legal disputes, cost overruns, and project delays. Careful contract drafting and regular contract administration are important to safeguard the interests of all parties involved.
- Financial Risks: Main contractors are responsible for honoring their payment obligations to subcontractors. However, disputes over payment terms, change orders, or performance issues can arise. Subcontractors may encounter financial risks if payment is delayed or withheld. Main contractors need to ensure prompt and accurate payment to subcontractors, as financial disputes can strain relationships and impact the project’s progress.
- Worksite Safety: Ensuring a safe work environment for subcontractors is a shared responsibility. However, subcontractors may have their own safety practices and standards. Failure to enforce consistent safety measures across the construction site can result in accidents, injuries, and legal liabilities. Regular safety inspections, clear safety protocols, and ongoing communication about safety expectations are essential to mitigate worksite risks.
- Dependency on Subcontractors: Subcontractors are essential contributors to the construction project, and delays or deficiencies in their work can have a cascading effect. Main contractors may become dependent on subcontractors for critical tasks or expertise, making it challenging to find suitable alternatives in case of performance issues or unforeseen circumstances. Diversifying subcontractor options and maintaining backup plans can mitigate this risk.
- Reputation and Client Perception: The quality and performance of subcontractors reflect directly on the main contractor. Poor subcontractor performance, delays, or quality issues can tarnish the reputation of the main contractor and impact client satisfaction. Main contractors need to maintain regular communication with clients, manage expectations, and proactively address any subcontractor-related issues to protect their reputation.
Effectively managing these challenges and risks requires proactive project management, clear communication, and a comprehensive understanding of subcontracting relationships. Strong contract administration, ongoing monitoring of subcontractor performance, and timely issue resolution are key to minimizing the impact of these challenges and risks. By addressing these potential pitfalls head-on, main contractors can foster successful subcontractor relationships and maximize the chances of project success.
Read more: How Does A Bond Work In Construction
Best Practices for Effective Subcontracting in Construction
Subcontracting in construction can be a complex process, but implementing best practices can help main contractors and project owners ensure successful and efficient collaboration with subcontractors. By following these best practices, construction professionals can foster strong relationships, improve project outcomes, and mitigate potential risks. Here are some key best practices for effective subcontracting in construction:
- Thorough Prequalification: Conduct thorough prequalification processes to select reliable subcontractors. Evaluate their experience, qualifications, past performance, and financial stability. A comprehensive prequalification process helps in selecting subcontractors who are competent, reliable, and well-suited for the project requirements.
- Clear and Comprehensive Subcontract Agreements: Develop clear and comprehensive subcontract agreements that outline the roles, responsibilities, deliverables, timelines, pricing, payment terms, and dispute resolution mechanisms. Well-drafted contracts mitigate potential disputes and provide a solid foundation for a successful partnership.
- Effective Communication: Establish open and regular communication channels with subcontractors. Communicate project details, expectations, and updates effectively and promptly. Regular meetings, progress reports, and written instructions clarify requirements, address concerns, and ensure everyone is aligned with project goals.
- Collaborative Planning: Involve subcontractors in the project planning phase to ensure their insights and expertise contribute to the overall project strategy. Incorporate their input in scheduling, sequencing, and resource allocation to optimize project efficiency and minimize conflicts during the construction process.
- Proactive Project Management: Implement proactive project management practices to monitor subcontractor performance, progress, and compliance. Regularly assess subcontractor work quality, address issues promptly, and provide constructive feedback. This maintains accountability, promotes quality workmanship, and helps avoid delays or rework.
- Timely Payment and Incentives: Adhere to timely payment schedules and promptly resolve any payment-related issues. Timely payment strengthens subcontractor relationships and motivates them to prioritize the project’s success. Consider offering performance-based incentives to reward exceptional work, fostering subcontractor loyalty and collaboration.
- Regular Site Inspections: Conduct regular site inspections to ensure subcontractor work meets quality standards and adheres to project specifications. This helps identify issues early on, enabling timely corrective action. Site inspections also emphasize the importance of worksite safety, reducing the potential for accidents or violations.
- Document Management: Maintain accurate and organized documentation related to subcontractor agreements, change orders, communications, inspections, and invoices. Proper documentation ensures accountability, assists in dispute resolution, and provides a record for future reference or audits, enhancing the project’s transparency and legal protection.
- Continuous Improvement: Foster a culture of continuous improvement by soliciting feedback from subcontractors on project processes, collaboration, and communication. Encourage subcontractors to provide suggestions for enhancing productivity, streamlining operations, and improving the overall construction process.
- Positive Relationship Building: Cultivate positive relationships with subcontractors based on mutual respect, fairness, and transparency. Establishing strong relationships promotes trust, encourages collaboration, and can result in long-term partnerships. Maintaining open lines of communication and recognizing subcontractor contributions fosters a positive work environment.
By implementing these best practices, main contractors and project owners can optimize subcontracting relationships, reduce risks, enhance project efficiency, and deliver successful construction projects. Effective subcontracting relies on clear communication, collaboration, proactive management, and building strong partnerships based on mutual respect and shared goals.
Conclusion
Subcontracting is a fundamental aspect of the construction industry, allowing main contractors to leverage specialized expertise and efficiently manage complex projects. By subcontracting specific tasks or services to qualified professionals, construction projects can benefit from enhanced quality, improved resource allocation, and streamlined operations.
In this article, we have explored the definition of subcontracting in construction and discussed the reasons and benefits behind its widespread use. We have covered various types of construction subcontractors, their roles, and responsibilities within the construction process. Additionally, we have outlined the subcontracting process, including prequalification, negotiation, coordination, and documentation.
While subcontracting offers significant advantages, there are challenges and risks to be mindful of. Maintaining quality control, managing coordination and project timelines, addressing contractual and legal issues, ensuring worksite safety, and handling financial considerations are critical aspects that require careful attention and effective management.
To navigate these challenges and mitigate risks, we have highlighted a set of best practices for effective subcontracting in construction. Thorough prequalification, clear subcontract agreements, open communication, collaborative planning, proactive project management, and timely payment are among the key practices that promote successful subcontractor relationships.
By implementing these best practices, main contractors and project owners can foster productive partnerships, optimize project outcomes, and minimize risks. Effective subcontracting relies on establishing strong lines of communication, maintaining transparency, and building trust between all parties involved.
In conclusion, subcontracting plays a pivotal role in the construction industry, allowing for the seamless integration of specialized trades and expertise into construction projects. By harnessing the skills and knowledge of subcontractors, construction professionals can enhance the quality of work, improve project efficiency, and deliver successful outcomes. With careful planning, effective project management, and strong relationships, subcontracting can be a powerful tool for achieving construction project goals.
Frequently Asked Questions about How Does Subcontracting Work In Construction
Was this page helpful?
At Storables.com, we guarantee accurate and reliable information. Our content, validated by Expert Board Contributors, is crafted following stringent Editorial Policies. We're committed to providing you with well-researched, expert-backed insights for all your informational needs.
0 thoughts on “How Does Subcontracting Work In Construction”