Home>diy>Building & Construction>What Are SIPs In Construction
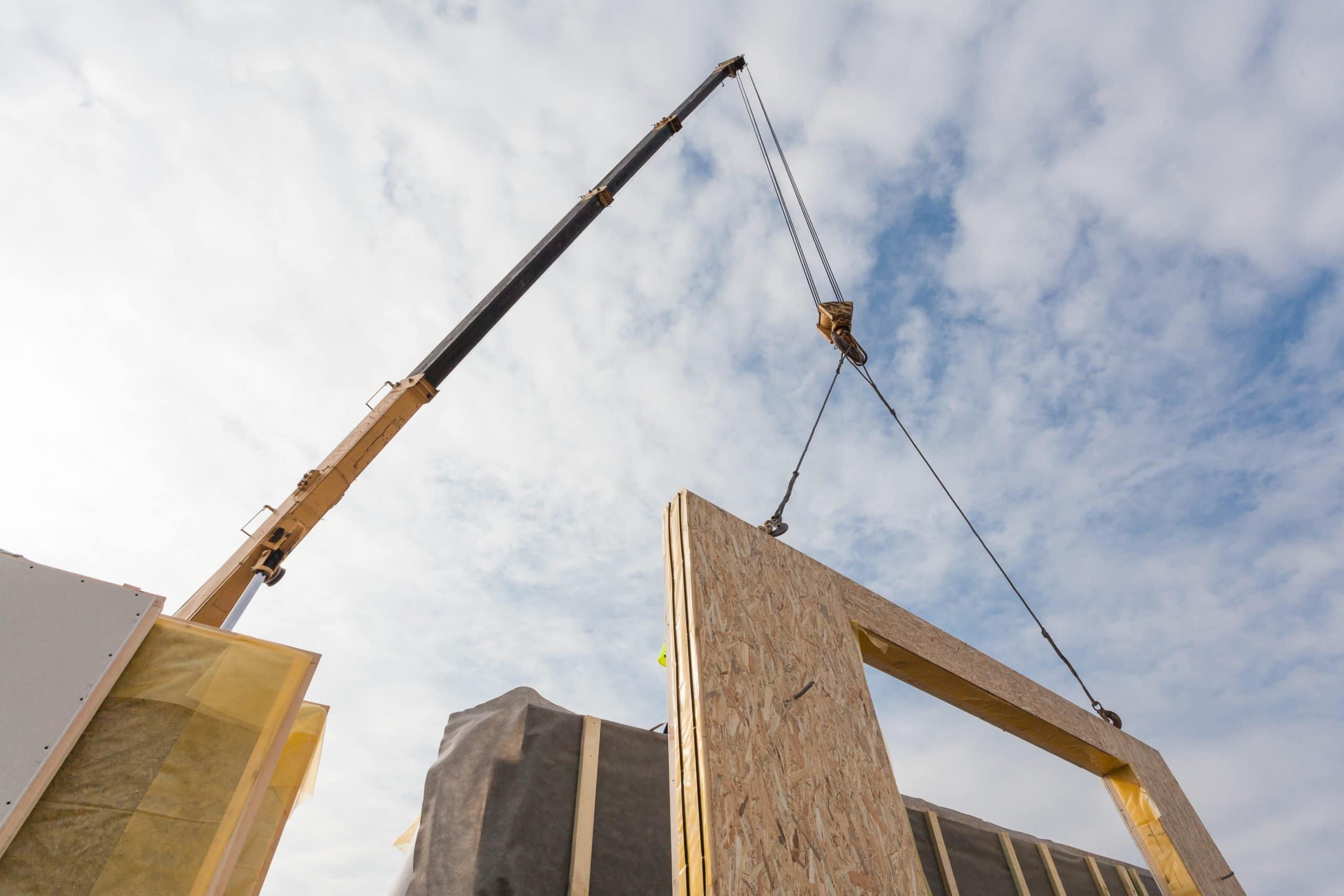
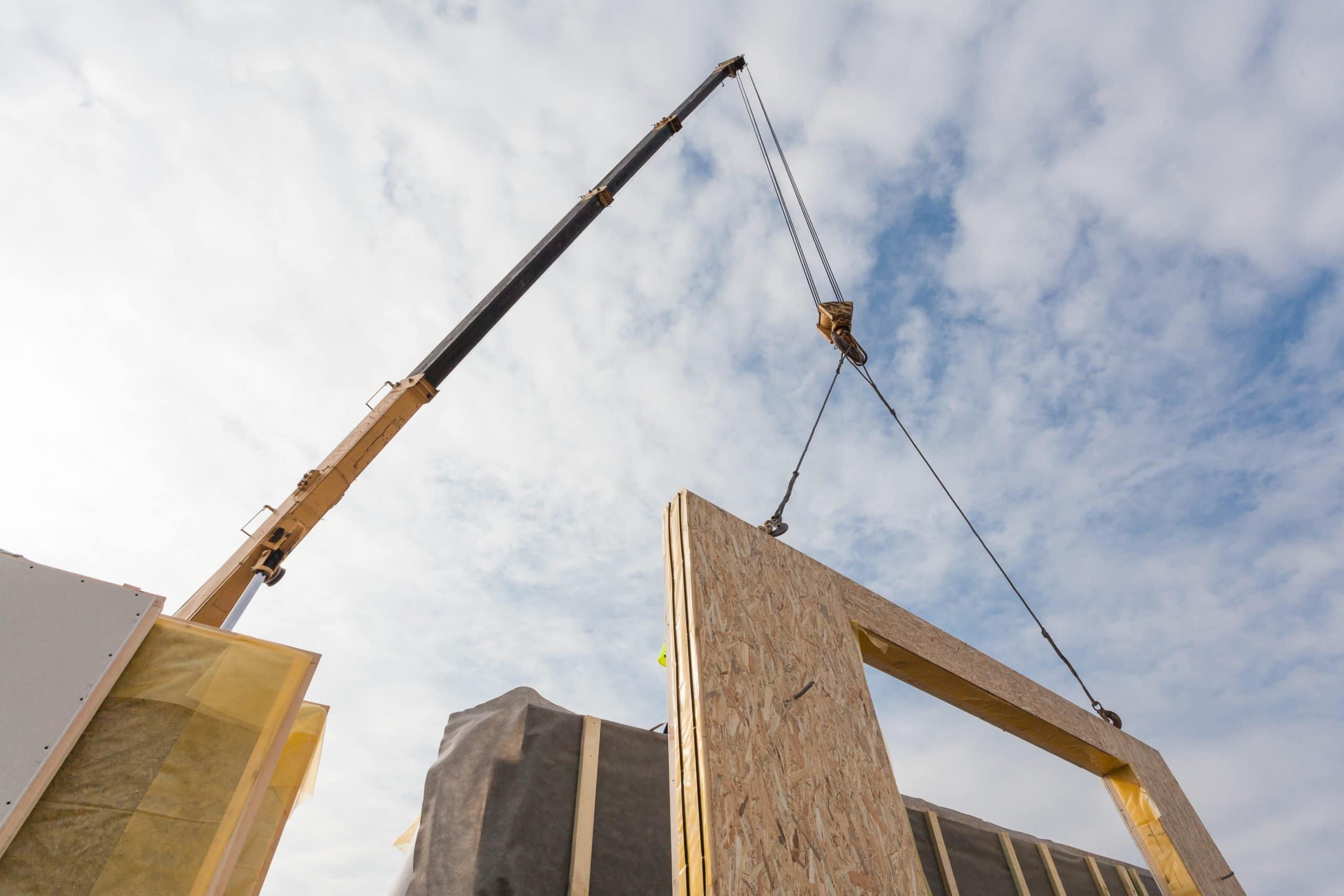
Building & Construction
What Are SIPs In Construction
Modified: December 7, 2023
Discover the benefits of Structural Insulated Panels (SIPs) in building construction. Learn how SIPs can improve energy efficiency and reduce construction time.
(Many of the links in this article redirect to a specific reviewed product. Your purchase of these products through affiliate links helps to generate commission for Storables.com, at no extra cost. Learn more)
Introduction
Welcome to the world of construction, where innovation and technology are constantly shaping the way we build. One such innovative building product that has gained widespread recognition in recent years is Structural Insulated Panels, commonly known as SIPs.
SIPs are a type of building material that revolutionizes the construction industry by offering several advantages over traditional construction methods. They have quickly become a popular choice for residential, commercial, and industrial projects due to their energy efficiency, durability, and ease of installation.
In this article, we will explore the definition of SIPs, different types of SIPs, their advantages and disadvantages, applications in construction, cost considerations, environmental benefits, and a comparison with traditional construction methods. By the end, you will have a comprehensive understanding of why SIPs are making waves in the construction industry.
Key Takeaways:
- SIPs offer energy efficiency, speed of construction, and design flexibility, making them an attractive choice for modern construction projects. Their long-term benefits offset the higher upfront costs, contributing to sustainable and efficient buildings.
- SIPs streamline construction, reduce labor, time, and waste, and provide excellent thermal performance for energy-efficient buildings. While they have higher upfront costs, their long-term benefits make them a compelling alternative to traditional construction methods.
Read more: What Is SIPS In Construction
Definition of SIPs
Structural Insulated Panels (SIPs) are composite building panels that consist of a core material sandwiched between two layers of sheathing. The core material is typically made of expanded polystyrene (EPS), polyurethane foam, or extruded polystyrene (XPS).
The sheathing layers, usually made of oriented strand board (OSB), plywood, or fiber cement, provide strength and rigidity to the panels. The combination of these materials results in a lightweight, high-strength, and energy-efficient building component.
One of the key features of SIPs is their ability to serve multiple purposes in construction. They act as both the structural support and insulation of a building, eliminating the need for separate framing and insulation installations. This significantly speeds up the construction process and reduces labor costs.
SIPs come in various sizes and thicknesses, depending on the specific requirements of the project. The panels can be customized to fit different architectural designs and can be used for walls, floors, and roofs.
Overall, SIPs offer an alternative approach to traditional construction methods by combining structural integrity, thermal efficiency, and simplicity into one versatile building component.
Types of SIPs
There are several types of Structural Insulated Panels (SIPs), each offering unique characteristics and suitability for different construction projects. Here are the commonly used types:
- EPS SIPs: These panels consist of a core made of Expanded Polystyrene (EPS), which is a lightweight and cost-effective insulation material. EPS SIPs are known for their excellent thermal performance, allowing buildings to stay well-insulated and energy-efficient. They are commonly used in residential and commercial construction.
- Polyurethane SIPs: Polyurethane SIPs have a core made of polyurethane foam, which offers superior insulation properties compared to EPS. These panels have a higher R-value, providing enhanced energy efficiency and better sound insulation. They are often used in projects that require high levels of insulation, such as passive houses or buildings in extreme weather conditions.
- Extruded Polystyrene (XPS) SIPs: XPS SIPs have a core made of extruded polystyrene foam, which provides excellent moisture resistance and thermal insulation. These panels are commonly used in areas prone to moisture or where higher compressive strength is required, such as below-grade applications or foundation walls.
- Hybrid SIPs: Hybrid SIPs combine different materials in their construction to optimize specific properties. For example, a hybrid SIP might have an EPS core for insulation purposes and an OSB facing for structural support. These panels offer flexibility in meeting project requirements while providing a balance between cost-effectiveness and performance.
- Specialty SIPs: In addition to the standard types mentioned above, there are specialty SIPs available for specific applications. These include fire-rated SIPs, which have additional fire-resistant properties, and acoustic SIPs, designed to minimize sound transmission. Specialty SIPs cater to specialized construction needs where specific performance criteria must be met.
It’s important to consult with professionals and experts in SIPs to determine the most suitable type for your project, considering factors such as climate, structural requirements, energy efficiency goals, and budget constraints.
Advantages of SIPs in Construction
Structural Insulated Panels (SIPs) offer numerous advantages over traditional construction methods. These advantages have contributed to the growing popularity of SIPs in the construction industry. Here are some of the key benefits:
- Energy Efficiency: SIPs are known for their exceptional thermal performance. The continuous insulation provided by the panels helps to minimize air leakage, reduce thermal bridging, and maintain a comfortable indoor temperature. This results in lower heating and cooling costs, making buildings more energy-efficient and environmentally friendly.
- Speed and Ease of Construction: SIPs are prefabricated off-site, allowing for faster and more efficient construction. The panels are precisely cut to the desired dimensions, reducing on-site labor and minimizing construction waste. The assembly process is quicker compared to traditional framing, as the panels can be quickly installed using mechanical fasteners or adhesives.
- Strength and Stability: SIPs provide excellent structural integrity and load-bearing capacity. The combination of the panel’s rigid foam core and sheathing layers creates a strong and durable building envelope. SIPs can withstand high winds, earthquakes, and heavy snow loads, making them suitable for different geographical regions.
- Design Flexibility: SIPs can be customized to fit various architectural designs and building requirements. They can be easily integrated into both residential and commercial projects, allowing for creative and unique designs. SIPs can accommodate large open spaces, curved walls, and custom shapes, providing flexibility to architects and designers.
- Improved Indoor Air Quality: SIPs contribute to healthier indoor environments by reducing the infiltration of outdoor pollutants, allergens, and drafts. The airtight nature of SIPs helps maintain better control over ventilation, ensuring a more comfortable and pollutant-free living or working space.
- Reduced Construction Waste: By using SIPs, the amount of construction waste generated is significantly reduced. The panels are fabricated with minimal material waste, and any remaining scraps can be recycled. This not only reduces landfill waste but also lowers the overall environmental impact of the construction project.
These advantages make SIPs an attractive option for modern construction projects. However, it is important to work with experienced professionals who are knowledgeable about SIPs to ensure proper installation and maximize the benefits offered by this innovative building material.
Disadvantages of SIPs in Construction
While Structural Insulated Panels (SIPs) offer several advantages, there are also some disadvantages that should be considered when using SIPs in construction projects. It’s important to weigh these factors against the benefits to make an informed decision. Here are some of the key disadvantages:
- Higher Upfront Cost: SIPs can be more expensive upfront compared to traditional construction materials. The cost of manufacturing the panels and the additional expertise required for installation can contribute to an increased project cost. However, it’s essential to consider the long-term energy savings and reduced labor costs associated with SIPs to determine their overall cost-effectiveness.
- Limited Availability: SIPs may not be readily available in all areas. Depending on your location, finding suppliers and manufacturers who produce SIPs can be a challenge. This limited availability can increase the difficulty and cost of sourcing the required materials for your project.
- Skill and Knowledge Requirements: Proper installation of SIPs requires specialized skills and knowledge. The panels must be handled and installed correctly to ensure the integrity and performance of the building envelope. Working with experienced SIPs installers or contractors is crucial to avoid potential problems or mistakes during the construction process.
- Moisture Control: SIPs are susceptible to moisture-related issues if not properly sealed and protected. It’s essential to implement proper moisture control measures, including the use of vapor barriers and adequate waterproofing techniques. Failure to address moisture issues can lead to mold growth, structural damage, and compromised insulation effectiveness.
- Limited Retrofitting Options: Retrofitting existing structures with SIPs can be challenging due to the fixed dimensions and structural considerations of the panels. Custom modifications may be required, which can add complexity and cost to retrofitting projects. In such cases, it’s important to consult with experienced professionals to ensure feasibility and proper implementation.
- Complex Electrical and Plumbing Integration: Incorporating electrical wiring and plumbing systems within SIPs can be more complex compared to traditional construction methods. Proper planning and coordination are required to ensure the accurate placement of fixtures and conduits. Working with knowledgeable contractors who have experience with SIP installations is crucial to avoid potential complications.
Considering these disadvantages, it is important to thoroughly evaluate the specific project requirements, budget constraints, and construction goals before deciding whether SIPs are the right choice for your construction project.
When using SIPs (Structural Insulated Panels) in construction, ensure that the panels are properly sealed to prevent air leakage and maximize energy efficiency.
Read more: How To Design A SIP House
Applications of SIPs in Construction
Structural Insulated Panels (SIPs) have a wide range of applications in the construction industry, offering versatility and adaptability to various project types. Here are some common applications of SIPs:
- Residential Buildings: SIPs are widely used in residential construction, including single-family homes, multi-family dwellings, and even modular or prefabricated homes. They offer energy-efficient and quick construction solutions, resulting in comfortable and durable living spaces.
- Commercial Buildings: SIPs are suitable for various commercial building types, including offices, retail spaces, schools, and healthcare facilities. They provide excellent thermal performance, helping to reduce energy consumption and create comfortable indoor environments.
- Industrial Buildings: SIPs are increasingly being used in industrial construction, such as warehouses, factories, and distribution centers. The strength and durability of SIPs make them suitable for withstanding heavy loads and providing insulation in these types of structures.
- Educational Institutions: SIPs can be utilized in the construction of schools, colleges, and universities. The quick installation process allows for shorter construction time, minimizing disruptions to educational activities. Additionally, the energy-efficient properties of SIPs contribute to sustainable and cost-effective educational facilities.
- Green Buildings: SIPs are a preferred choice for green building projects due to their energy efficiency and reduced environmental impact. Their airtight construction, low thermal bridging, and overall sustainability align with the principles of green building design and contribute to achieving various green building certifications.
- Extensions and Additions: SIPs can be used for additions to existing buildings or extending structures, providing an efficient solution for increasing usable space. Their versatility allows for seamless integration with the existing structure while improving insulation and energy performance.
- Modular Construction: SIPs can be combined with modular construction techniques to create off-site fabricated building modules. This method allows for efficient and controlled manufacturing processes, ensuring high-quality construction with reduced time and labor on-site.
- High-performance Buildings: Structures targeting high-performance standards, such as Passive House or Net Zero Energy buildings, can benefit from SIPs’ excellent thermal insulation properties. The airtightness and energy efficiency offered by SIPs contribute to achieving stringent energy performance goals.
It’s important to consult with architects, engineers, and SIPs manufacturers to assess the suitability of SIPs for specific applications and ensure compliance with local building codes and regulations.
Cost Considerations of SIPs
When considering the use of Structural Insulated Panels (SIPs) in construction, it is essential to evaluate the cost implications. While SIPs offer numerous advantages, they may have different cost considerations compared to traditional construction methods. Here are some key factors to consider:
- Upfront Material Cost: SIPs can initially be more expensive than traditional building materials like wood framing or concrete. The cost of manufacturing the panels, the type of insulation used, and the quality of the sheathing layers can contribute to the overall material cost. It is important to obtain detailed quotes from different suppliers and evaluate the cost-effectiveness in relation to the project scope and long-term benefits.
- Installation Costs: The cost of installing SIPs can vary depending on the complexity of the project, the size and thickness of the panels, and the expertise required for installation. The labor cost associated with SIPs might be higher compared to traditional construction methods due to the specialized skills and knowledge needed for proper installation. It is important to factor in these installation costs when budgeting for the project.
- Energy Efficiency Savings: One significant advantage of SIPs is their energy efficiency, which can lead to long-term cost savings on heating and cooling expenses. The improved insulation properties and reduced air leakage minimize energy consumption and provide better thermal comfort. While SIPs may have higher upfront costs, the potential energy savings over the lifespan of the building should be taken into account when considering their overall cost-effectiveness.
- Construction Time and Labor Cost: SIPs enable faster construction due to their prefabricated nature and ease of installation. The reduced construction time can result in cost savings on labor expenses and the overall project timeline. Additionally, the use of SIPs eliminates the need for separate insulation installation, further streamlining the construction process.
- Longevity and Durability: SIPs are known for their strength and durability. The long lifespan of SIPs means that there are potentially reduced maintenance and replacement costs over time compared to traditional construction methods. Incorporating SIPs into a construction project can contribute to long-term cost savings in terms of repairs and maintenance.
- Location and Availability: The availability of SIPs can vary depending on the region. If SIPs are not readily available in a particular area, additional transportation costs may be incurred to source the materials. It is advisable to research and identify local suppliers or manufacturers to minimize transportation costs and potential delays in the construction timeline.
It is crucial to carefully assess the specific cost considerations of SIPs in relation to the project requirements, budget, and long-term benefits. Working with experienced professionals who have knowledge of SIPs can help in making informed decisions that balance cost-effectiveness and the advantages offered by SIPs in construction.
Environmental Benefits of SIPs
Structural Insulated Panels (SIPs) offer a range of environmental benefits that make them an attractive option for sustainable construction. These benefits contribute to reducing the environmental impact of buildings and promoting a more sustainable future. Here are some key environmental advantages of SIPs:
- Energy Efficiency: SIPs provide excellent thermal insulation, resulting in reduced heat transfer and improved energy efficiency. The airtight construction of SIPs reduces air infiltration and energy loss, reducing the need for excessive heating and cooling. This leads to lower energy consumption and reduced greenhouse gas emissions.
- Reduced Energy Demand: SIPs’ high level of insulation helps to create a more stable indoor environment with reduced temperature fluctuations. This reduces the reliance on mechanical heating and cooling systems, resulting in lower energy demand. The reduced energy demand not only lowers carbon dioxide emissions but also decreases the strain on the power grid.
- Resource Efficiency: SIPs optimize the use of materials, resulting in reduced waste during the construction process. The panels are prefabricated and cut precisely to fit, minimizing on-site cutting and material wastage. Additionally, using SIPs eliminates the need for separate insulation installation, further reducing the amount of material required.
- Recyclability and Reusability: SIPs are made using recyclable materials, such as expanded polystyrene (EPS) or polyurethane foam, and oriented strand board (OSB). At the end of their lifespan, these materials can be repurposed or recycled. SIPs can also be disassembled and used in future construction projects, promoting a circular economy and reducing construction waste.
- Improved Indoor Air Quality: The airtightness of SIPs helps to prevent the infiltration of outdoor pollutants, allergens, and moisture into the building. This improves indoor air quality, creating a healthier and more comfortable living or working environment for occupants. Good indoor air quality contributes to the well-being and productivity of building occupants.
- Reduced Environmental Impact: SIPs’ energy efficiency and reduced waste contribute to a reduced overall environmental impact. By minimizing energy consumption and carbon dioxide emissions, SIPs help mitigate climate change and reduce the dependence on fossil fuels. The sustainable manufacturing processes and recyclability of SIPs also help in conserving natural resources.
- Sustainable Building Certifications: SIPs can contribute to achieving various sustainable building certifications, such as LEED (Leadership in Energy and Environmental Design) or Green Star ratings. The energy efficiency and environmental benefits offered by SIPs align with the criteria of these certifications and promote sustainable building practices.
By choosing SIPs for construction projects, developers and homeowners can significantly reduce the environmental impact of buildings and contribute to a more sustainable built environment.
Comparison of SIPs with Traditional Construction Methods
When considering construction methods, it is important to compare the advantages and disadvantages of Structural Insulated Panels (SIPs) with traditional construction methods. Here is a comparison between SIPs and traditional methods:
- Energy Efficiency: SIPs offer greater energy efficiency compared to traditional construction methods. The continuous insulation of SIPs minimizes thermal bridging and air leakage, resulting in reduced heating and cooling costs.
- Speed of Construction: SIPs can significantly expedite the construction process. Their prefabricated nature allows for faster installation, reducing labor time on-site. Traditional construction methods often involve a longer construction timeline due to the separate installation of framing, insulation, and sheathing components.
- Design Flexibility: SIPs offer design flexibility, allowing for creative and unique architectural designs. They can be customized and easily integrated into various building types. Traditional methods may present limitations in achieving complex designs and shapes.
- Strength and Stability: SIPs provide excellent structural integrity and load-bearing capacity. They can withstand high winds, earthquakes, and heavy snow loads. Traditional construction methods also offer structural stability, but SIPs often have higher strength-to-weight ratios.
- Environmental Impact: SIPs have a lower environmental impact due to their energy efficiency and reduced waste during construction. Traditional construction methods may generate more material waste and require additional insulation materials, leading to a higher carbon footprint.
- Noise Reduction: SIPs offer superior sound insulation properties compared to traditional construction methods. The combination of insulation and solid panels helps minimize noise transmission, resulting in quieter indoor spaces.
- Cost: SIPs may have higher upfront costs due to the specialized manufacturing and expertise required for installation. However, the energy savings and reduced labor costs can offset these initial expenses over the long term. Traditional construction methods may have lower upfront costs, but ongoing energy expenses could be higher.
- Familiarity and Availability: Traditional construction methods are well-established and widely used, making it easier to find skilled labor and materials. SIPs may have limited availability in some areas, requiring additional research and coordination for procurement and installation.
Ultimately, the choice between SIPs and traditional construction methods depends on project requirements, budget, and priorities. SIPs offer significant benefits in terms of energy efficiency, speed of construction, and design flexibility, making them a popular choice for sustainable and efficient building projects. It is important to consider the specific needs of each project and consult with professionals to determine the most suitable approach.
Read more: How To Store Cirkul Sips Between Uses
Conclusion
Structural Insulated Panels (SIPs) have emerged as a game-changer in the construction industry, offering a range of advantages over traditional construction methods. SIPs provide energy efficiency, speed of construction, design flexibility, and environmental benefits that make them an attractive choice for modern construction projects.
By combining insulation and structural components into one panel, SIPs streamline the construction process and reduce labor, time, and waste. Their excellent thermal performance helps to create energy-efficient buildings, resulting in reduced heating and cooling costs and lower carbon footprints. SIPs also offer design flexibility, allowing for creative architectural designs and customization.
While SIPs have higher upfront costs compared to traditional construction methods, the long-term benefits, such as energy savings and reduced maintenance, can offset these expenses. It is important to consider the overall cost-effectiveness and evaluate project-specific requirements when deciding to use SIPs.
Moreover, SIPs contribute to sustainable construction practices by reducing resource consumption, minimizing waste, and promoting energy efficiency. They provide a solution for creating comfortable and environmentally friendly buildings that prioritize occupant well-being and contribute to a greener future.
However, SIPs are not without their limitations. They require specialized skills and knowledge for installation, and their availability may vary in different regions. Adequate moisture control measures and proper sealing are essential to prevent potential issues. To ensure the successful implementation of SIPs, it is crucial to work with experienced professionals who have knowledge of SIPs and can provide guidance throughout the construction process.
In conclusion, SIPs offer a compelling alternative to traditional construction methods, providing energy-efficient, durable, and environmentally friendly building solutions. As technology and innovation continue to advance, SIPs are likely to play an increasingly significant role in the construction industry as we strive for sustainable and efficient buildings.
Frequently Asked Questions about What Are SIPs In Construction
Was this page helpful?
At Storables.com, we guarantee accurate and reliable information. Our content, validated by Expert Board Contributors, is crafted following stringent Editorial Policies. We're committed to providing you with well-researched, expert-backed insights for all your informational needs.
0 thoughts on “What Are SIPs In Construction”