Home>diy>Building & Construction>What Is SIPS In Construction
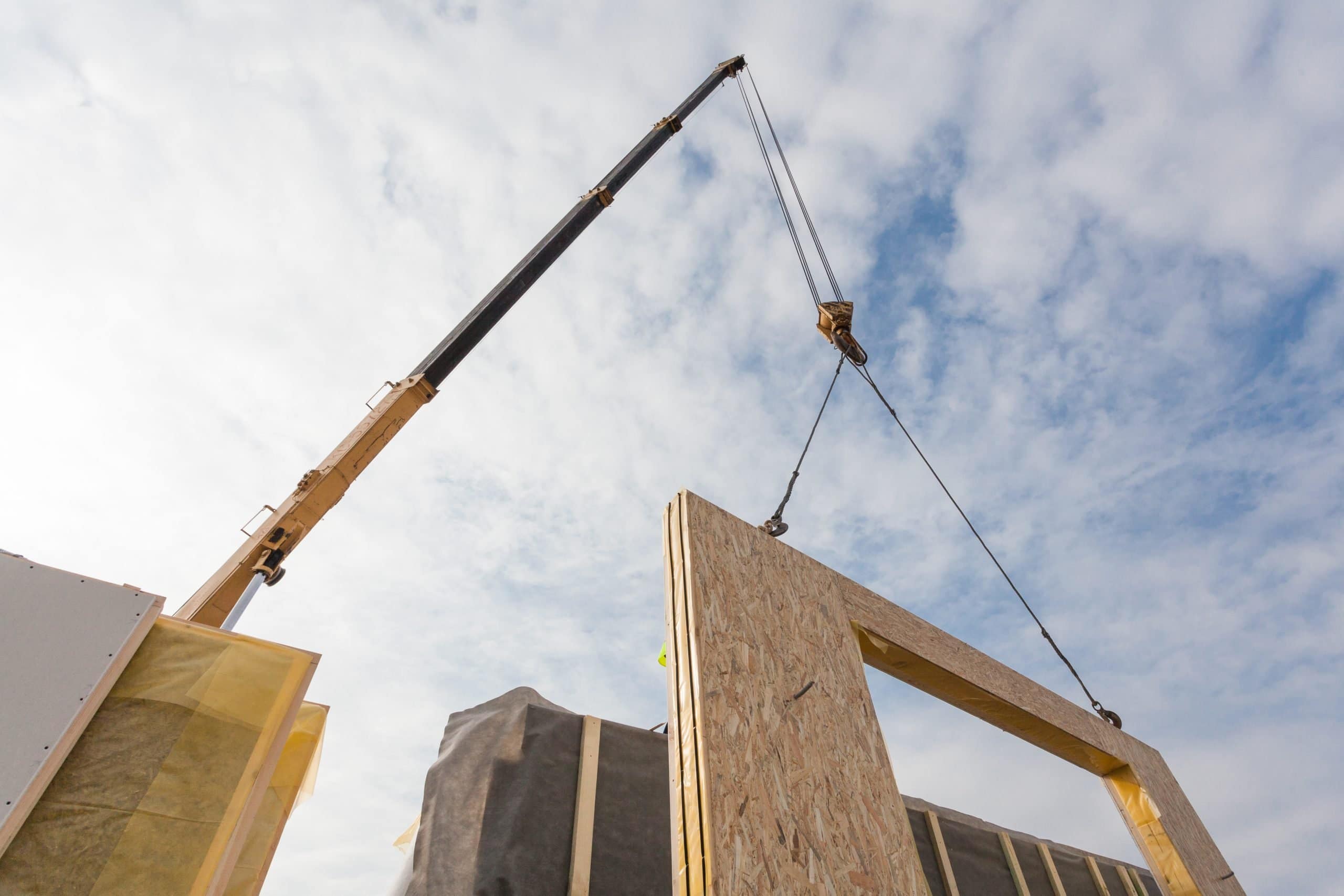
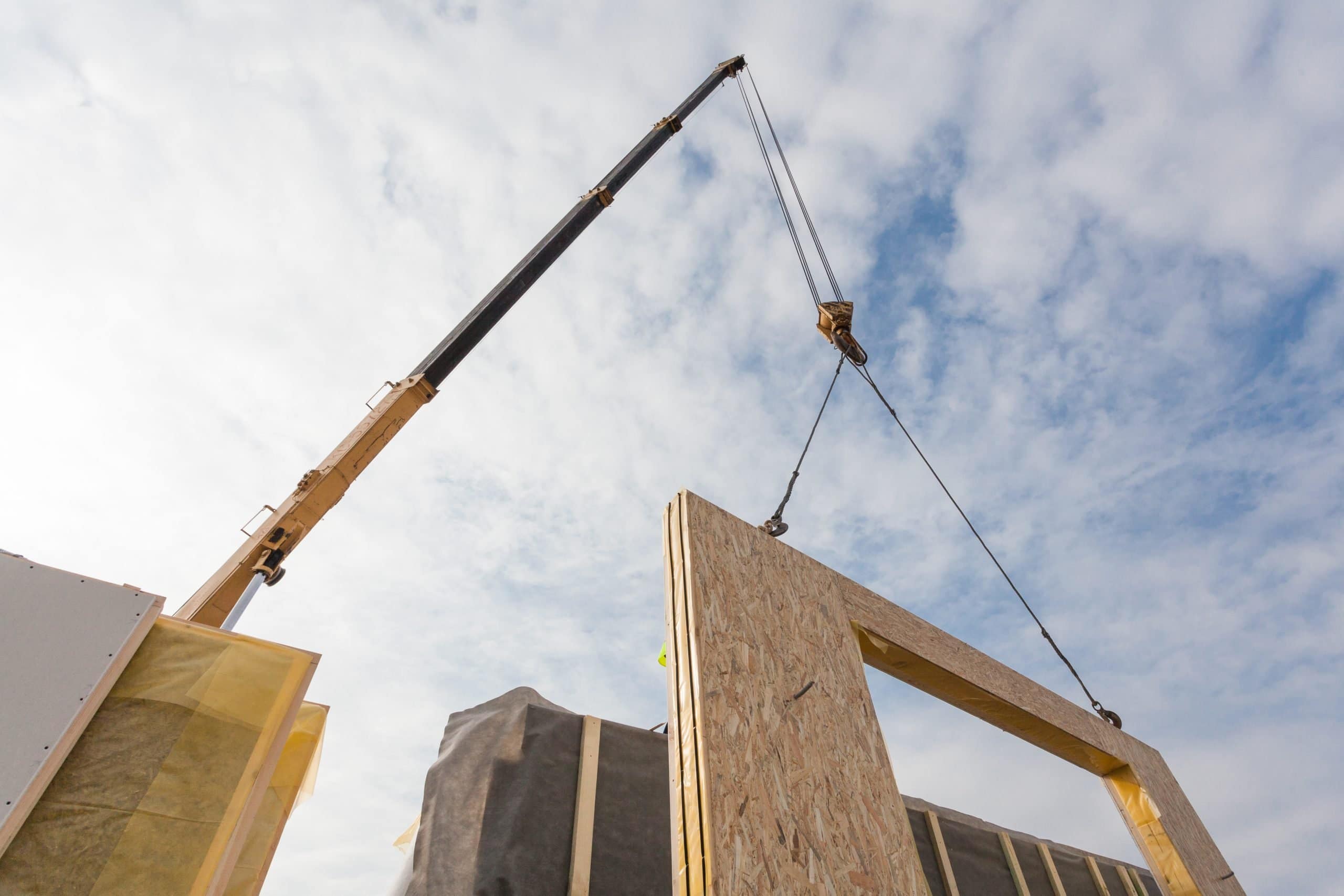
Building & Construction
What Is SIPS In Construction
Modified: February 27, 2024
Discover the benefits of SIPS in building construction and learn how this innovative method is revolutionizing the industry. Find out how SIPS can improve energy efficiency and reduce construction time.
(Many of the links in this article redirect to a specific reviewed product. Your purchase of these products through affiliate links helps to generate commission for Storables.com, at no extra cost. Learn more)
Introduction
In today’s ever-evolving construction industry, builders and contractors are constantly seeking innovative methods and materials to improve the efficiency, durability, and sustainability of their projects. One such method that has gained significant popularity over the years is the use of Structural Insulated Panels (SIPS) in construction.
SIPS have revolutionized the way buildings are designed and constructed, offering a host of benefits in terms of energy efficiency, structural integrity, and construction speed. This article will delve into the world of SIPS, exploring their definition, benefits, types, components, installation process, common applications, environmental impact, cost considerations, and potential drawbacks.
So, what exactly are SIPS? SIPS are prefabricated building panels consisting of an insulating foam core sandwiched between two structural facings, typically made of oriented strand board (OSB). The foam core provides excellent thermal insulation properties, while the facings offer strength and rigidity to the panel.
Now that we have an overview of what SIPS are, let’s explore the numerous benefits they provide in construction.
Key Takeaways:
- SIPS offer superior insulation, energy efficiency, and quick installation, making them a versatile and sustainable choice for residential, commercial, and institutional construction projects.
- While SIPS provide numerous benefits, it’s important to consider potential drawbacks such as upfront cost, design limitations, and specialized installation knowledge to make informed decisions when incorporating SIPS into construction projects.
Read more: What Are SIPs In Construction
Definition of SIPS
SIPS, or Structural Insulated Panels, are prefabricated building panels that consist of an insulation core sandwiched between two rigid facings. The core is typically made of expanded polystyrene (EPS), polyurethane foam, or polyisocyanurate foam.
What sets SIPS apart from traditional building methods is their integrated approach to insulation, structural support, and air tightness. The insulation core provides superior thermal performance, minimizing energy losses and reducing heating and cooling costs. The rigid facings add strength and rigidity to the panel, allowing for structural stability and load-bearing capacity.
SIPS are designed to be customizable based on the project requirements. They can be manufactured in various sizes, thicknesses, and configurations to suit specific architectural designs and building codes. The panels are typically fabricated off-site in a controlled factory environment, ensuring high-quality construction and precise measurements.
These panels can be used for both walls and roofs, making them versatile in various construction applications. They can be easily integrated into different building systems, such as timber frames, steel frames, or concrete structures.
Overall, SIPS offer a modern and efficient approach to construction by combining insulation and structure into a single panel. This integration leads to faster installation times, improved energy efficiency, and enhanced building performance.
Benefits of SIPS in Construction
SIPS provide numerous advantages over traditional construction methods, making them an attractive choice for builders, architects, and homeowners alike. Let’s explore some of the key benefits of using SIPS in construction:
- Superior Insulation: The insulation core of SIPS offers excellent thermal resistance, resulting in energy-efficient buildings. This helps reduce heating and cooling expenses and creates a comfortable indoor environment.
- Energy Efficiency: The airtight nature of SIPS minimizes air leakage and thermal bridging, ensuring better energy performance. This translates to reduced energy consumption and lower carbon footprint.
- Structural Integrity: SIPS provide exceptional strength and stability due to their rigid facings. They can withstand heavy loads, making them suitable for both residential and commercial constructions.
- Quick Installation: SIPS are prefabricated off-site, which allows for faster construction compared to traditional methods. The panels are manufactured with precision and can be swiftly erected, speeding up the overall construction process.
- Design Flexibility: SIPS can be customized to meet specific architectural designs and building requirements. They can be easily integrated with various building systems, allowing for versatile and creative design options.
- Improved Indoor Air Quality: The airtight construction of SIPS helps prevent the infiltration of pollutants, dust, and allergens into the building. This contributes to a healthier indoor environment and enhances occupant comfort.
- Reduced Waste: Since SIPS are manufactured in a controlled factory setting, there is minimal waste generated during the production process. Additionally, the efficiency of SIPS reduces the amount of construction waste generated on-site.
- Sound Insulation: The dense structure of SIPS helps reduce noise transmission, providing excellent sound insulation. This is particularly beneficial for buildings located in noisy environments or where privacy is crucial.
With their combination of energy efficiency, durability, and design flexibility, SIPS have become a go-to choice for sustainable and high-performance construction projects. Whether it’s a residential home, commercial building, or institutional facility, the benefits of using SIPS are evident in terms of energy savings, construction speed, and occupant comfort.
Types of Structural Insulated Panels
Structural Insulated Panels (SIPS) come in various types, each catering to specific construction needs and requirements. Let’s explore some of the common types of SIPS:
- Expanded Polystyrene (EPS) SIPS: EPS SIPS are the most widely used type of SIPS in construction. The insulation core is made of expanded polystyrene, a lightweight and cost-effective material. EPS SIPS offer good thermal insulation properties and are known for their durability and moisture resistance.
- Polyurethane (PUR) SIPS: Polyurethane foam has a higher R-value, providing superior thermal insulation compared to EPS. PUR SIPS are thinner and lighter than other types, making them suitable for projects with limited space. They offer excellent energy efficiency and have good fire resistance properties.
- Polyisocyanurate (PIR) SIPS: PIR SIPS have a higher R-value than EPS and PUR, making them highly energy-efficient. They provide excellent thermal insulation and are commonly used in buildings that require superior insulation performance. PIR SIPS are also known for their fire resistance and moisture resistance.
- Transitional SIPS: Transitional SIPS combine different insulation materials within the same panel. For example, one side of the panel may have EPS insulation while the other side has PUR insulation. Transitional SIPS offer design flexibility and cater to specific project requirements where different levels of insulation are needed in different areas.
- Cementitious SIPS: Cementitious SIPS use a core made of cement-based materials like fiber cement or magnesium oxide board. These panels offer excellent fire resistance and can be used in applications where enhanced fire safety is required. Cementitious SIPS also provide good thermal insulation and have high durability.
These are just a few examples of the types of SIPS available in the market. The choice of SIPS type will depend on factors such as climate conditions, energy efficiency goals, budget constraints, and specific project requirements. Consulting with a professional builder or architect can help determine the most suitable type of SIPS for a particular construction project.
Components of SIPS
Structural Insulated Panels (SIPS) consist of several components that work together to create a high-performance building envelope. Understanding the different components of SIPS is essential for proper installation and optimal performance. Let’s explore the key components:
- Insulation Core: The insulation core is the heart of SIPS and is typically made of materials like expanded polystyrene (EPS), polyurethane foam, or polyisocyanurate foam. The insulation core provides excellent thermal resistance, reducing energy losses and improving the energy efficiency of the building. It helps keep the interior temperature comfortable, regardless of external weather conditions.
- Structural Facings: The rigid facings on both sides of the SIPS panel provide structural support and protect the insulation core. The most common facing material is oriented strand board (OSB), which is known for its strength and durability. Other options include plywood or cementitious board. The facings add rigidity to the panel, allowing it to bear loads and resist impact.
- Adhesive: Adhesives are used to bond the insulation core to the structural facings. The adhesive ensures a strong and secure connection between the components, creating a solid and stable panel. The type of adhesive used will depend on the specific SIPS manufacturer and their recommended installation process.
- Fasteners: Fasteners, such as screws or nails, are used to secure the SIPS panels to the building’s framing. These fasteners penetrate the structural facings and provide additional support and stability. The size and spacing of the fasteners will be determined by the specific SIPS design and the local building codes.
- Gaskets and Sealants: To achieve a tight and airtight construction, gaskets and sealants are used to seal the joints and edges of the SIPS. This helps prevent air leakage and reduces thermal bridging, improving the overall energy efficiency of the building. Proper sealing is crucial to maintain indoor comfort and prevent moisture infiltration.
By combining these components, SIPS create a well-insulated, structurally sound, and energy-efficient building envelope. The insulation core provides thermal resistance, while the structural facings and fasteners ensure stability and load-bearing capacity. The adhesive, gaskets, and sealants work together to create a tight and airtight construction, minimizing energy losses and enhancing the performance of the building.
Read more: How To Store Cirkul Sips
Installation Process of SIPS
Installing Structural Insulated Panels (SIPS) requires careful planning and attention to detail to ensure a successful and efficient construction process. Here is a step-by-step guide to the typical installation process of SIPS:
- Design and Preparation: Before installation, the building design should include precise measurements and layout plans for the SIPS. The foundation and framing should be prepared according to the design specifications, ensuring proper support and alignment for the panels.
- Panel Delivery: The SIPS panels are delivered to the construction site, typically in pre-cut sizes based on the building design. It is important to inspect the panels upon delivery for any damage or defects.
- Panel Placement: The first step in the installation process is placing the SIPS panels in their designated positions. The panels are lifted into place using cranes, forklifts, or other suitable equipment. Care should be taken to align the panels accurately and securely fit them into the framing.
- Fastening the Panels: Once the panels are in position, they are fastened to the building’s framing using appropriate screws or nails. The fasteners should be driven through the structural facings and into the framing members at recommended intervals. It is important to follow the manufacturer’s guidelines to ensure proper fastening and structural integrity.
- Sealing and Insulating: After the panels are secured, attention should be given to sealing the joints and edges to create an airtight construction. Sealants and gaskets are applied to the panel seams, ensuring proper insulation and reducing air leakage. Any gaps or penetrations should be properly sealed to maintain the energy efficiency of the building.
- Roof Installation: If SIPS are being used for the roof, the installation process would involve placing and securing the roof panels in a similar manner as the wall panels. Special attention should be given to proper sealing of the roof panels to prevent water infiltration and ensure a watertight roof system.
- Finishing: Once all the SIPS panels are installed and properly sealed, the exterior and interior finishes can be applied according to the design requirements. This includes siding, cladding, drywall, and other finishes to complete the building envelope and interior spaces.
It is important to note that the installation process may vary depending on the specific project requirements and the manufacturer’s recommendations. It is crucial to consult the SIPS manufacturer and follow their installation guidelines to ensure a successful and compliant installation.
By following proper installation techniques, SIPS can provide a fast, efficient, and durable building construction method, offering enhanced energy efficiency, structural integrity, and overall performance.
When using SIPS (Structural Insulated Panels) in construction, ensure proper installation to maximize energy efficiency and structural integrity. Proper sealing and joining of panels is crucial for optimal performance.
Common Applications of SIPS
Structural Insulated Panels (SIPS) have gained popularity in a wide range of construction projects due to their numerous benefits and versatile nature. Here are some common applications of SIPS:
- Residential Construction: SIPS are extensively used in residential construction, ranging from single-family homes to multi-unit buildings. They provide excellent thermal insulation, helping to create energy-efficient and comfortable living spaces. SIPS also offer design flexibility, allowing for various architectural styles and layouts.
- Commercial Buildings: SIPS are increasingly used in commercial construction, including offices, retail spaces, schools, and healthcare facilities. The energy efficiency provided by SIPS helps reduce operating costs and contributes to sustainability goals. The speed of installation is an added advantage for commercial projects with tight timelines.
- Institutional Structures: SIPS are ideal for institutional buildings such as schools, colleges, and government buildings. The insulation properties of SIPS create a conducive learning environment and promote energy savings, while the strength and stability of the panels contribute to a durable and long-lasting structure.
- Industrial Facilities: SIPS can be used in the construction of industrial facilities such as warehouses, manufacturing plants, and storage facilities. The quick installation process of SIPS helps minimize downtime, allowing businesses to be up and running faster. The high thermal performance of SIPS also helps maintain controlled interior temperatures.
- Modular Construction: SIPS are well-suited for off-site modular construction methods. The panels can be prefabricated and transported to the construction site, enabling faster and more efficient assembly. Modular construction with SIPS is commonly used for modular homes, classrooms, healthcare units, and other portable or temporary structures.
- Renovation and Retrofitting: SIPS can also be retrofitted onto existing structures as an energy-efficient alternative. They can be used to upgrade the insulation and structural integrity of older buildings, enhancing their overall performance and reducing energy consumption.
The applications of SIPS are not limited to these examples. The versatility and adaptability of SIPS make them suitable for a wide range of construction projects, catering to various building types, sizes, and styles.
As SIPS continue to gain recognition for their energy efficiency, durability, and design flexibility, their usage is expected to grow in both residential and commercial construction, contributing to sustainable and high-performance buildings.
Environmental Impact of SIPS
Structural Insulated Panels (SIPS) offer several environmental benefits compared to traditional construction methods. Let’s explore the positive environmental impact of SIPS:
- Energy Efficiency: SIPS provide excellent thermal insulation, resulting in reduced energy consumption for heating and cooling. By minimizing the need for artificial climate control, SIPS help reduce greenhouse gas emissions and overall energy usage, leading to a smaller carbon footprint.
- Reduced Material Waste: SIPS are prefabricated off-site, resulting in less construction waste compared to traditional on-site building methods. The factory-controlled manufacturing process allows for precise cutting and minimal material waste, contributing to a more sustainable construction process.
- Recyclable Materials: The components of SIPS, such as the insulation core and structural facings, are often made from recyclable materials. For example, the insulation core may utilize recycled content, including post-consumer recycled foam. At the end of their service life, SIPS can be disassembled and recycled, reducing the environmental impact.
- Minimal Site Disruption: SIPS require fewer construction materials to achieve the same level of structural integrity, resulting in less disruption to the construction site. With faster installation times, there is reduced noise pollution, traffic congestion, and disturbance to the surrounding environment.
- Improved Indoor Air Quality: The airtight construction of SIPS helps prevent the ingress of outdoor pollutants and allergens, thus improving indoor air quality. This is beneficial for occupant health and well-being by reducing the risk of respiratory issues and promoting a healthier living environment.
- Longevity and Durability: SIPS are known for their strength and durability, resulting in longer building lifespans. By creating long-lasting structures, SIPS minimize the need for frequent renovations or demolitions, reducing waste generation and resource consumption associated with rebuilding.
- Energy-Neutral and Passive House Construction: SIPS can be used in energy-neutral or passive house construction, where the goal is to create buildings that produce as much energy as they consume. By combining SIPS with energy-efficient systems and renewable energy sources, buildings can minimize their dependence on non-renewable energy sources and achieve high levels of sustainability.
The environmental impact of SIPS can be further enhanced by incorporating sustainable practices throughout the construction process, such as using environmentally-friendly adhesives, sealants, and finishes, as well as implementing water conservation measures and responsibly managing construction waste.
Overall, SIPS contribute to greener and more sustainable construction practices by reducing energy consumption, minimizing waste generation, improving indoor air quality, and promoting long-lasting structures. By embracing SIPS in construction projects, we can move towards a more environmentally conscious and sustainable future.
Cost Considerations for SIPS Construction
When considering the use of Structural Insulated Panels (SIPS) in construction, it is important to evaluate the cost implications. While SIPS offer various benefits, there are certain cost considerations to keep in mind. Let’s explore some of the key factors to consider:
- Material Costs: The material cost of SIPS can vary depending on factors such as the type of insulation core, the thickness of the panels, and the structural facing material. Generally, SIPS may have a higher upfront cost compared to traditional building materials such as wood or concrete. However, this initial investment is offset by the long-term energy savings and the potential for reduced labor costs during construction.
- Construction Timeline: SIPS can significantly reduce construction time due to their prefabricated nature. The speed and ease of installation translate into reduced labor costs and potentially shorter project schedules, leading to potential cost savings. However, it is important to note that any potential time savings can also depend on project complexity, site conditions, and the availability of skilled labor experienced in working with SIPS.
- Design Complexity: The design complexity of the project can influence the cost of using SIPS. Simple, rectangular structures are typically more cost-effective due to the standardized panel sizes and simpler installation process. Complex architectural designs with irregular shapes, multiple openings, or customized panel sizes may require additional engineering and fabrication, potentially increasing the overall cost.
- Transportation and Handling: The transportation and handling costs of SIPS should be considered, especially for projects located far from the SIPS manufacturer. The larger size and dimensions of SIPS panels may require specialized transportation and equipment for safe delivery to the construction site. These additional costs should be factored into the overall project budget.
- Building Code Requirements: Building codes and regulations vary across regions, and it is crucial to ensure that the use of SIPS complies with local codes. Additional expenses may arise from obtaining necessary permits and certifications, as well as any required structural engineering assessments to meet building code requirements.
- Additional Trades and Finishes: SIPS provide a solid structural envelope, but additional trades may be required to complete the building. This can include electrical, plumbing, HVAC, and interior finishes such as drywall, flooring, and painting. The costs for these trades should be accounted for in the overall project budget.
It is important to note that while SIPS may have upfront cost considerations, the long-term benefits such as energy savings, lower maintenance costs, and increased durability can outweigh the initial investment. Consulting with experienced professionals and obtaining accurate cost estimates specific to the project will help make informed decisions when considering SIPS construction.
By carefully assessing these cost considerations, developers, builders, and homeowners can determine the feasibility and financial implications of incorporating SIPS into their construction projects.
Read more: How To Design A SIP House
Potential Drawbacks of SIPS
While Structural Insulated Panels (SIPS) offer numerous benefits in terms of energy efficiency, time savings, and sustainability, it is important to consider some potential drawbacks before deciding to utilize SIPS in construction. Understanding these drawbacks can help make informed decisions and mitigate any challenges that may arise. Let’s explore some of the potential drawbacks:
- Upfront Cost: SIPS can have a higher upfront cost compared to traditional building materials. The cost of the materials and specialized manufacturing process of SIPS can contribute to a higher initial investment. However, it is essential to weigh this against the potential long-term energy savings and reduced labor costs during construction.
- Design Limitations: SIPS are prefabricated panels, which may limit the design options in terms of architectural freedom. Structures with complex designs, unique angles, or irregular shapes may require more customization and engineering expertise, potentially adding to the cost and project timeline.
- Transportation and Handling: The size and weight of SIPS panels can make transportation and handling more challenging compared to traditional building materials. Specialized equipment and extra care are often required to safely deliver and install the panels, which can add to the overall project cost.
- Moisture Concerns: Although SIPS are designed to be moisture-resistant, improper installation or penetration of the panel can lead to moisture infiltration. If moisture is allowed to penetrate the panels, it may result in mold growth or deteriorated insulation performance. Proper sealing and adherence to installation guidelines are critical to mitigate moisture-related issues.
- Specialized Installation Knowledge: Working with SIPS requires a certain level of expertise and knowledge of the specific installation techniques. Contractors and builders who are not familiar with SIPS installation may face a learning curve, potentially leading to errors or inefficiencies during the construction process.
- Repair and Modification: Making modifications or repairs to SIPS structures can be more challenging compared to traditional building methods. Cutouts or alterations to the panels may affect their structural integrity and thermal performance. Careful planning and consultation with professionals are necessary when considering any modifications or repairs to SIPS buildings.
- Limited Availability: SIPS may not be readily available in all regions or from all suppliers. Availability can vary depending on the geographic area and market demand. It is important to work with reputable manufacturers or suppliers who can provide reliable and quality SIPS panels for the project.
Despite these potential drawbacks, addressing them through proper planning, skilled installation, and adherence to guidelines can help mitigate any challenges. Consulting with professionals experienced in using SIPS can provide valuable insights and ensure a successful construction process.
By weighing the benefits and considering the potential drawbacks, stakeholders can make informed decisions on whether SIPS are the right choice for their specific construction project.
Conclusion
Structural Insulated Panels (SIPS) have revolutionized the construction industry by offering numerous benefits in terms of energy efficiency, structural integrity, and sustainability. These prefabricated building panels consist of insulation cores sandwiched between rigid facings, providing superior thermal performance and creating airtight structures.
Throughout this article, we have explored the definition of SIPS, their benefits, types, components, installation process, common applications, environmental impact, cost considerations, and potential drawbacks. SIPS have proven to be a versatile and efficient construction solution with the potential to create highly energy-efficient buildings and reduce the carbon footprint.
The benefits of SIPS include superior insulation, energy efficiency, structural integrity, quick installation, design flexibility, improved indoor air quality, reduced waste, and sound insulation. These advantages translate into comfortable and sustainable living and working spaces, as well as potential cost savings in terms of energy consumption and construction timelines.
Common applications of SIPS span across residential, commercial, institutional, and industrial sectors. They are used in the construction of residential homes, commercial buildings, schools, warehouses, and modular structures. The design flexibility and durability of SIPS make them suitable for a wide range of architectural styles and building systems.
While SIPS offer many advantages, it is important to consider the potential drawbacks, such as upfront cost, design limitations, transportation and handling, moisture concerns, specialized installation knowledge, repair and modification challenges, and limited availability. Addressing these considerations through proper planning, qualified professionals, and adherence to guidelines can help mitigate any challenges that may arise.
Ultimately, the decision to use SIPS in construction should be based on a comprehensive evaluation of project needs, budget constraints, and sustainability goals. Consulting with experienced professionals and trusted suppliers can provide valuable insights and assistance in implementing SIPS effectively.
With its combination of energy efficiency, structural integrity, and design flexibility, SIPS have proven to be a game-changer in modern construction practices. By embracing the benefits of SIPS, builders and homeowners can create sustainable, comfortable, and high-performance buildings for the present and future generations.
Frequently Asked Questions about What Is SIPS In Construction
Was this page helpful?
At Storables.com, we guarantee accurate and reliable information. Our content, validated by Expert Board Contributors, is crafted following stringent Editorial Policies. We're committed to providing you with well-researched, expert-backed insights for all your informational needs.
0 thoughts on “What Is SIPS In Construction”