Home>diy>Building & Construction>What Is A Good Way To Address Hazards On A Construction Site
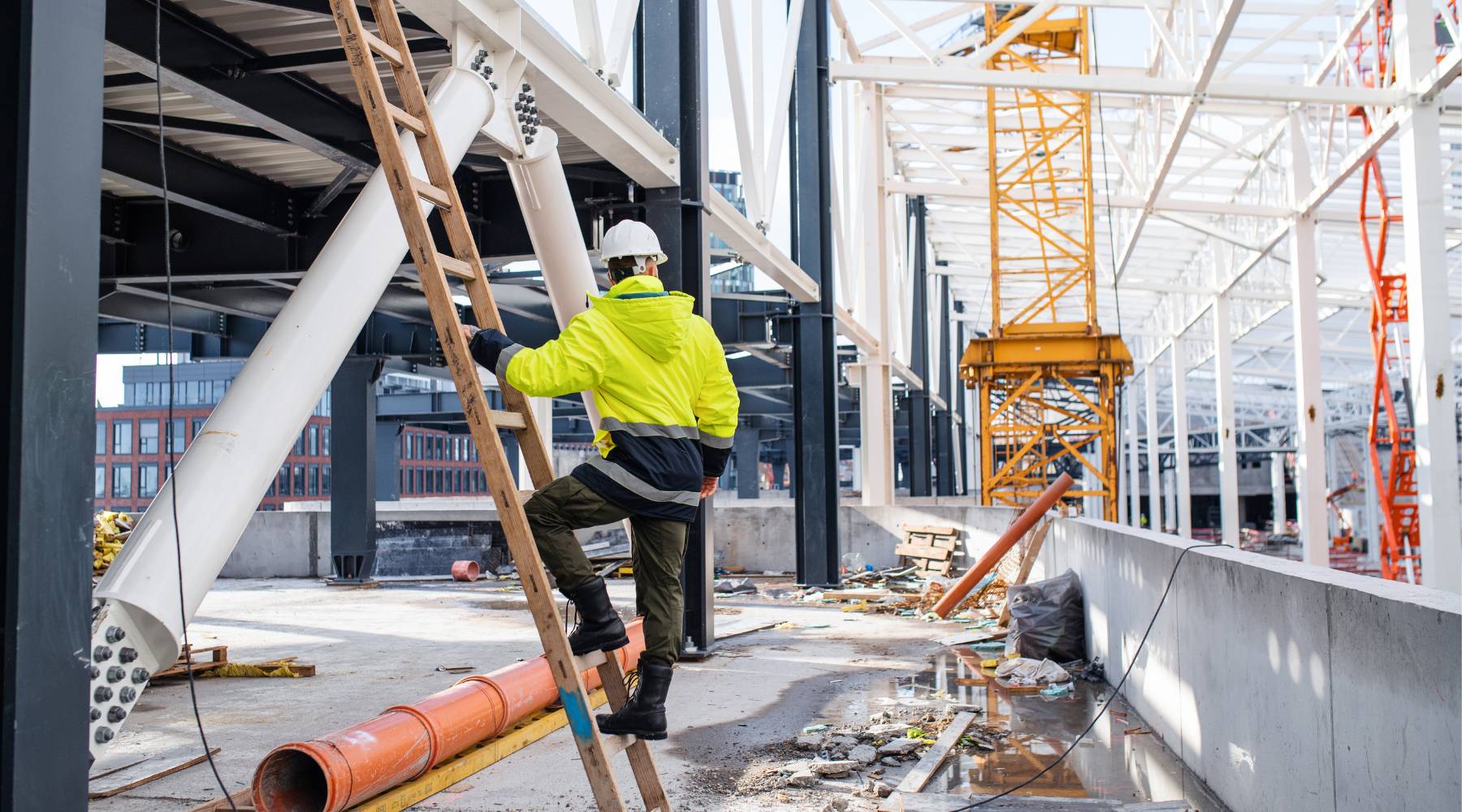
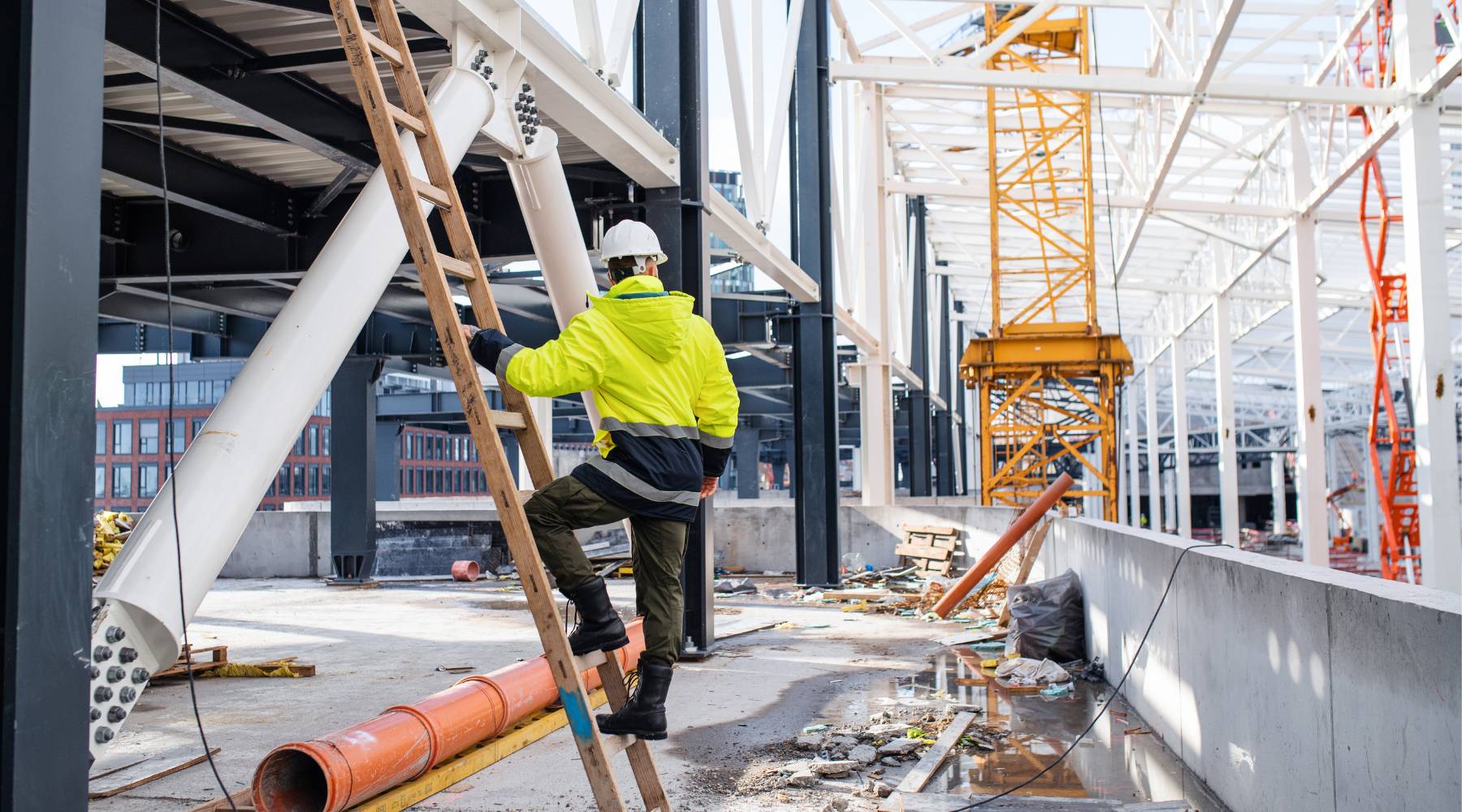
Building & Construction
What Is A Good Way To Address Hazards On A Construction Site
Modified: January 4, 2024
Looking for a safe solution to tackle hazards on your construction site? Discover effective strategies and best practices for hazard management in building construction.
(Many of the links in this article redirect to a specific reviewed product. Your purchase of these products through affiliate links helps to generate commission for Storables.com, at no extra cost. Learn more)
Introduction
Welcome to the world of construction, where skilled workers transform blueprints into towering structures and magnificent buildings. However, amidst the chaos and creativity, there are risks and hazards that can threaten both the safety of the workers and the success of the project. Addressing these hazards is crucial to ensure a safe and productive construction site.
The construction industry holds a vital role in society, shaping the infrastructure we rely on every day. From residential buildings to commercial complexes, construction projects require meticulous planning, precise execution, and strict adherence to safety protocols. By understanding and addressing the hazards that arise in the construction industry, builders can safeguard their workers and deliver projects on time and within budget, without compromising quality.
Construction sites are dynamic environments that constantly evolve as the project progresses. With the presence of heavy machinery, complex equipment, and a multitude of tasks happening simultaneously, hazards can arise at any moment. Therefore, it is essential to adopt a proactive approach to address these hazards and minimize the risks associated with construction work.
Through a combination of safety regulations, training programs, and on-site practices, construction companies can create a safety culture that permeates every aspect of their operations. From hazard identification and assessment to implementing control measures and conducting regular inspections, addressing hazards becomes an integral part of every construction project.
This comprehensive guide aims to provide an in-depth understanding of the importance of addressing hazards on a construction site. It will cover common hazards in construction, safety regulations and guidelines, creating a safety culture, developing a hazard identification and assessment program, implementing effective control measures, training and education for workers, regular inspections and audits, and incident reporting and investigation procedures. By following these best practices, construction companies can minimize accidents, protect their workers, and ensure the successful completion of their projects.
Key Takeaways:
- Prioritizing safety on construction sites is crucial for protecting workers, reducing costs, and enhancing productivity, reputation, and client confidence.
- Implementing a safety culture, hazard identification program, effective control measures, and ongoing training ensures a safe and successful construction environment.
Read more: How To Avoid Hazards On A Construction Site
Importance of Addressing Hazards on a Construction Site
Addressing hazards on a construction site is of paramount importance due to the inherent risks associated with the industry. Construction sites are dynamic and complex environments, where workers perform a wide range of tasks involving heavy machinery, power tools, and often at heights. Failing to address hazards can result in severe accidents, injuries, and even loss of life. Beyond the ethical obligation to protect workers, there are several reasons why addressing hazards is crucial in the construction industry:
- Worker Safety: The well-being and safety of construction workers should always be the top priority. By addressing hazards and implementing safety measures, construction companies can reduce the risk of accidents and injuries. This not only protects the lives and physical well-being of workers but also creates a positive work environment that promotes efficiency and productivity.
- Legal Compliance: Construction sites are subject to various safety regulations and guidelines, enforced by local, state, and national authorities. Compliance with these regulations is not only a legal requirement but also ensures that construction companies maintain their credibility and reputation. Failure to address hazards can result in penalties, legal liabilities, and even project shutdowns.
- Reduced Costs: Addressing hazards can help minimize costs associated with accidents and injuries. Workplace accidents often incur substantial financial implications, including medical expenses, compensation claims, increased insurance premiums, and potential project delays. By proactively identifying and addressing hazards, construction companies can mitigate these risks and reduce overall project costs.
- Enhanced Productivity: A safe working environment fosters productivity and efficiency. When workers feel safe and confident in their surroundings, they can focus on their tasks without being distracted by potential hazards. Additionally, addressing hazards through proper training and implementing safety measures can optimize workflow and prevent workflow disruptions caused by accidents or equipment failures.
- Reputation and Client Confidence: Construction companies that prioritize safety and effectively address hazards are often viewed more favorably by clients, stakeholders, and the community at large. Demonstrating a commitment to worker safety enhances a company’s reputation and builds confidence among clients, potentially leading to more business opportunities and long-term success.
Ultimately, addressing hazards on a construction site is not only about protecting lives but also about creating an environment where workers can thrive. By prioritizing safety and implementing comprehensive hazard management strategies, construction companies can ensure the successful completion of projects while safeguarding the well-being of their most valuable asset—their workers.
Common Hazards in Construction
Construction sites present a myriad of hazards that can pose significant risks to workers’ safety. Being aware of these hazards is essential for effectively addressing them and implementing appropriate safety measures. Some common hazards found in the construction industry include:
- Falls: Falls from heights are one of the leading causes of injuries and fatalities in construction. Working on scaffolds, ladders, or at elevated platforms without proper fall protection can result in severe injuries or even death.
- Electrical Hazards: Construction sites often involve working with electrical systems, wiring, and equipment. Improper handling of live electrical wires or faulty wiring can lead to electrocution and electrical burns.
- Struck-by Accidents: Workers are at risk of being struck by falling objects, moving machinery, or vehicles on construction sites. It is crucial to establish clear procedures for securing tools and materials and ensuring that workers wear appropriate personal protective equipment (PPE).
- Trenching and Excavation Hazards: Excavation work poses significant risks, such as cave-ins, engulfment, or exposure to hazardous gases. Proper shoring, sloping, or shielding techniques must be implemented to prevent accidents.
- Caught-in or Between Hazards: Workers can suffer injuries if they become caught, entangled, or compressed between moving machinery, equipment, or structures. This can occur during equipment operation, material handling, or while working in confined spaces.
- Hazardous Materials: Construction sites may contain hazardous materials, such as asbestos, lead, or chemicals. Workers must receive proper training on handling and disposing of these substances safely to prevent exposure and health risks.
- Noise and Vibration: Construction sites often produce high levels of noise and vibrations from machinery and equipment. Long-term exposure to excessive noise can lead to hearing loss, and prolonged exposure to vibrations can cause musculoskeletal disorders.
- Heat and Cold Stress: Working outdoors in extreme temperatures can pose hazards such as heat exhaustion, heat stroke, or hypothermia. Adequate measures, like providing shade, hydration, and proper protective clothing, must be implemented to prevent heat and cold-related illnesses.
- Fire and Explosion Hazards: Construction sites may have flammable materials, combustible gases, or inadequate electrical installations, creating fire and explosion risks. Implementing appropriate fire prevention measures and emergency response protocols is critical.
- Overexertion: Construction work often involves repetitive or strenuous tasks, such as heavy lifting, pushing, or carrying materials. Workers can experience overexertion, leading to musculoskeletal injuries if proper ergonomics and lifting techniques are not followed.
These are just a few examples of the common hazards encountered on construction sites. Each construction project may have its unique set of hazards, necessitating a thorough hazard identification and assessment program to address specific risks effectively.
By identifying these hazards and implementing appropriate control measures, construction companies can significantly reduce the incidence of accidents and injuries, creating a safer working environment for their employees.
Safety Regulations and Guidelines
The construction industry is governed by various safety regulations and guidelines to ensure the well-being of workers and the overall safety of construction sites. These regulations are put in place to mitigate hazards, prevent accidents, and promote a culture of safety. Here are some important safety regulations and guidelines that construction companies should be familiar with:
- Occupational Safety and Health Administration (OSHA): OSHA is a government agency responsible for setting and enforcing safety standards for workplaces in the United States. Construction companies must adhere to OSHA regulations, such as the Construction Standards (29 CFR 1926), which cover a wide range of topics, including fall protection, hazard communication, electrical safety, scaffolding, and more.
- National Fire Protection Association (NFPA): The NFPA provides standards and codes related to fire prevention and protection. Construction sites must comply with NFPA standards, such as NFPA 70 (National Electrical Code) and NFPA 241 (Standard for Safeguarding Construction, Alteration, and Demolition Operations).
- Building Codes: Building codes are regulations that set minimum standards for the design, construction, and occupancy of buildings. Compliance with building codes ensures the structural integrity and safety of buildings. Construction companies must adhere to local, state, and national building codes, which vary depending on the jurisdiction.
- Hazard Communication (HAZCOM): HAZCOM standards, such as the OSHA Hazard Communication Standard (29 CFR 1910.1200), require employers to communicate information about hazardous chemicals to employees. This includes labeling containers, providing Safety Data Sheets (SDS), and training employees on the proper handling and use of hazardous substances.
- Personal Protective Equipment (PPE): PPE regulations outline the requirements for providing appropriate protective equipment to workers. This includes items such as hard hats, safety glasses, gloves, steel-toed boots, and high-visibility vests. Employers must assess the workplace hazards and provide the necessary PPE to ensure worker safety.
- Construction Equipment Safety: Different types of construction equipment have their specific safety regulations and guidelines. This includes standards for the operation, maintenance, and inspection of equipment such as cranes, forklifts, excavators, and scaffolding systems. Construction companies must follow manufacturer guidelines and applicable safety regulations to ensure the safe use of equipment.
- Fall Protection: Falls from heights are a significant hazard in construction. Safety regulations and guidelines on fall protection require the use of guardrails, safety nets, harnesses, and other fall arrest systems when working at elevated heights. OSHA’s Fall Protection Standard (29 CFR 1926.501) provides detailed requirements for fall protection in construction.
These are just a few examples of safety regulations and guidelines that construction companies must comply with. It is essential to stay updated on any changes or updates to these regulations and ensure that all employees are aware of and trained on the proper safety procedures. Failure to comply with safety regulations not only puts workers at risk but can also result in legal consequences, fines, and project delays.
By following safety regulations and guidelines, construction companies demonstrate their commitment to protecting their workers and creating a safe working environment.
Creating a Safety Culture on Construction Sites
Creating a safety culture is fundamental in ensuring the well-being of construction workers and minimizing the risks associated with hazards on construction sites. A safety culture goes beyond simply implementing safety regulations and guidelines—it involves fostering an environment where safety is prioritized, embraced by all workers, and integrated into every aspect of the construction process. Here are key steps to create a safety culture on construction sites:
- Leadership Commitment: Strong leadership commitment is crucial to establishing a safety culture. Management must actively advocate for safety and visibly demonstrate their commitment by allocating resources, setting clear safety objectives, and leading by example. When workers witness their leaders prioritizing safety, they are more likely to follow suit.
- Communication and Training: Effective communication is vital for promoting a safety culture. Regularly communicate safety expectations, policies, and any updates or changes. Provide comprehensive training to workers on hazard identification, safe work practices, proper use of equipment, and emergency procedures. Encourage open communication channels where workers can report hazards or raise safety concerns without fear of retribution.
- Employee Involvement: Empower workers to actively participate in the safety process. Encourage them to identify and report hazards, provide input on safety procedures, and take ownership of their safety and the safety of their colleagues. Recognize and reward employees for their contributions to maintaining a safe work environment.
- Risk Assessment and Hazard Mitigation: Implement a systematic process for identifying, assessing, and mitigating hazards on construction sites. Conduct regular risk assessments to identify potential hazards and develop strategies to eliminate or control them. Engage workers in hazard identification, encourage reporting of near-misses, and promptly address any identified hazards to prevent accidents.
- Accountability: Establish accountability for safety at all levels of the organization. Ensure that workers are held accountable for adhering to safety protocols and taking responsibility for their actions. Implement consequences for non-compliance with safety procedures or engaging in unsafe behaviors, while also recognizing and rewarding those who consistently prioritize safety.
- Continuous Improvement: Foster a culture of continuous improvement by regularly reviewing and evaluating the effectiveness of safety programs and procedures. Encourage feedback from workers and use their input to identify areas for improvement. Stay updated on industry best practices, technological advancements, and changes in safety regulations to enhance safety measures and minimize evolving risks.
- Leading by Example: As leaders, set the example by consistently following safety protocols and engaging in safe behaviors. Wear appropriate personal protective equipment (PPE), adhere to safe work practices, and actively participate in safety initiatives. When workers see leaders prioritizing safety, they are more likely to internalize its importance.
Creating a safety culture is an ongoing process that requires commitment and effort from everyone involved in the construction project. It requires a collaborative effort from management, supervisors, workers, and subcontractors to ensure that safety is at the forefront of every decision and action. By fostering a safety culture, construction companies can significantly reduce accidents and injuries, increase productivity, and create a work environment that values the health and well-being of their employees.
Developing a Hazard Identification and Assessment Program
Developing a comprehensive hazard identification and assessment program is crucial for proactively identifying and mitigating potential risks on construction sites. By systematically identifying hazards and assessing their level of risk, construction companies can implement appropriate control measures to ensure the safety of their workers. Here are key steps to develop an effective hazard identification and assessment program:
- Establish a Team: Form a team or designate a responsible individual to lead the hazard identification and assessment program. This team should include representatives from different departments and roles to ensure a comprehensive and diverse perspective.
- Identify Potential Hazards: Conduct a thorough evaluation of your construction site to identify potential hazards. This can be done through site inspections, reviewing project plans and specifications, and engaging workers in hazard identification. Consider all aspects, such as equipment, materials, tools, tasks, work environment, and any specific hazards unique to the project.
- Document Hazards: Document all identified hazards in a centralized system or hazard register. Include details like the hazard description, location, potential consequences, and individuals at risk. This register will serve as a reference for ongoing risk assessments and control measures.
- Assess Risk: Assess the level of risk associated with each identified hazard. This involves determining the likelihood and severity of potential consequences. Use a risk matrix or other assessment tools to prioritize hazards based on their level of risk, allowing you to focus on high-risk hazards first.
- Implement Control Measures: Develop and implement control measures to eliminate or mitigate identified hazards. Control measures can include engineering controls (e.g., implementing fall protection systems), administrative controls (e.g., developing safe work procedures), and personal protective equipment (PPE).
- Review and Monitor: Regularly review and monitor the effectiveness of control measures. Continuously assess the hazards and the control measures in place to ensure they remain effective. Take feedback from workers, conduct inspections, and adapt control measures as necessary based on new information or changing conditions.
- Document and Communicate: Document the hazard identification and risk assessment process, as well as the control measures implemented. Clearly communicate this information to all workers, supervisors, and subcontractors involved in the construction project. Regularly remind workers of the identified hazards and the necessary control measures to promote an ongoing culture of safety.
- Training and Education: Provide comprehensive training and education to workers regarding hazard identification and control measures. Ensure they understand the potential hazards, how to report new hazards, and the importance of adhering to safety protocols. Regularly refresh and reinforce this training to ensure continued awareness.
By developing a hazard identification and assessment program, construction companies have a structured approach to identify and mitigate potential risks on their sites. This program ensures that hazards are proactively addressed, reducing the likelihood of accidents and injuries. It also demonstrates a commitment to worker safety and compliance with safety regulations.
Remember, hazard identification and assessment should be an ongoing process, adapting to the changing nature of construction projects. Regularly review and update your program to incorporate new hazards and control measures based on lessons learned and new industry developments.
Regularly inspect the construction site for potential hazards such as uneven ground, exposed wires, and unstable structures. Implement safety protocols and provide proper training for all workers to mitigate these risks.
Implementing Effective Hazard Control Measures
Implementing effective hazard control measures is crucial for minimizing risks and creating a safe working environment on construction sites. These measures are designed to eliminate or mitigate identified hazards, reducing the potential for accidents and injuries. Here are key steps for implementing effective hazard control measures:
- Hierarchy of Controls: Familiarize yourself with the hierarchy of controls, which provides a framework for selecting the most appropriate control measures. The hierarchy prioritizes control measures from most effective to least effective, including elimination, substitution, engineering controls, administrative controls, and personal protective equipment (PPE).
- Elimination and Substitution: Where possible, aim to eliminate hazards altogether or substitute them with safer alternatives. This can involve redesigning processes, using less hazardous materials, or implementing new technologies to eliminate or minimize the risk posed by the hazard.
- Engineering Controls: Implement engineering controls to prevent or reduce hazards. Examples include installing guardrails or safety nets to prevent falls, implementing ventilation systems to control exposure to hazardous substances, or utilizing equipment with built-in safety features.
- Administrative Controls: Implement administrative controls to change work practices and policies to minimize hazards. This can involve developing and enforcing safe work procedures, implementing job rotation to minimize exposure to hazards, or conducting regular training to ensure workers understand and follow safety protocols.
- Personal Protective Equipment (PPE): If hazards cannot be eliminated or adequately controlled using other measures, provide appropriate personal protective equipment (PPE) to workers. Examples include safety goggles, hard hats, gloves, respirators, and safety footwear. Ensure that PPE is properly selected, fits well, and that workers are trained on its correct use and maintenance.
- Regular Inspections: Conduct regular inspections to ensure that control measures are in place and effective. Inspections help identify any deficiencies or areas for improvement. Inspectors should be trained to identify hazards, understand control measures, and document any issues or potential hazards promptly.
- Worker Participation: Involve workers in the implementation and monitoring of control measures. Encourage their feedback and suggestions, as they often have valuable insights regarding hazards and control measures. Workers should feel empowered to report any deficiencies or hazards they observe, and their concerns should be promptly addressed.
- Supervisor Training and Support: Provide comprehensive training and support to supervisors, as they play a crucial role in ensuring that control measures are effectively implemented and workers comply with safety protocols. Supervisors should be knowledgeable about hazards, control measures, and enforcement of safe work practices.
- Continuous Improvement: Continuously monitor the effectiveness of control measures and make adjustments as necessary. Regularly review incident reports, near-miss reports, and feedback from workers to identify areas for improvement. Stay informed about new technologies, best practices, and industry advancements to enhance hazard control measures.
Implementing effective hazard control measures not only helps create a safer working environment but also demonstrates a commitment to worker safety. By eliminating or minimizing hazards, construction companies can greatly reduce the risks associated with construction work, protecting the well-being of their workers and improving overall project outcomes.
Training and Education for Construction Workers
Training and education are crucial elements in ensuring the safety and competency of construction workers. This comprehensive and ongoing process equips workers with the knowledge, skills, and awareness necessary to perform their tasks safely in the dynamic and hazardous construction environment. Here are key aspects to consider when providing training and education for construction workers:
- Orientation and Onboarding: Start by providing comprehensive orientation and onboarding programs for new workers. This includes familiarizing them with the construction site, company policies, emergency procedures, and the importance of safety.
- Hazard Awareness: Train workers to recognize and understand the various hazards they may encounter on construction sites. This includes identifying potential fall hazards, electrical dangers, equipment-related risks, and the proper handling of hazardous materials.
- Safe Work Practices: Educate workers on safe work practices specific to their tasks and trades. This involves teaching proper lifting techniques, correct usage of tools and equipment, effective communication and signaling, and the importance of personal protective equipment (PPE).
- Equipment Operation: Provide training on the safe operation of construction equipment and machinery. Workers should receive proper instruction, certification, and ongoing refresher training for operating equipment such as cranes, forklifts, excavators, and other powered tools.
- Emergency Preparedness: Train workers in emergency response protocols, including first aid, CPR, and the proper use of fire extinguishers. Conduct mock drills and simulations to ensure workers are prepared to handle emergency situations effectively.
- Health and Hygiene: Educate workers on maintaining good health and hygiene practices on construction sites. This includes training on recognizing and preventing common work-related illnesses, promoting proper hygiene practices, and facilitating access to facilities for personal hygiene.
- Specialized Training: Depending on the nature of the construction project, workers may require specialized training. This can include working at heights, confined space entry, scaffold erection, welding safety, or working with specific hazardous materials. Ensure that workers receive appropriate and up-to-date training for such specialized tasks.
- Supervisor Development: Provide comprehensive training and development programs for supervisors and foremen. They play a vital role in overseeing worker safety and enforcing safe work practices. Training should focus on leadership, hazard identification, hazard control, and effective communication skills.
- Ongoing Refresher Training: Safety training should not be a one-time event. Schedule regular refresher training sessions to reinforce knowledge, update workers on any changes in regulations or procedures, and address emerging safety concerns.
- Record Keeping: Maintain accurate records of all training provided, including attendance, topics covered, and assessment results. This ensures compliance with regulatory requirements and provides a reference for tracking individual workers’ training history.
By investing in comprehensive training and education programs, construction companies foster a culture of safety, enhance worker competency, and reduce the risks associated with construction work. It is essential to allocate resources, provide ongoing support, and continually evaluate and refine training initiatives to ensure their effectiveness.
Remember, the goal is not just to meet minimum training requirements but to strive for continuous improvement and to empower workers with the knowledge and skills needed to keep themselves and their colleagues safe on construction sites.
Regular Inspections and Audits
Regular inspections and audits are essential components of a successful safety management system on construction sites. They help identify potential hazards, monitor compliance with safety regulations, and ensure that control measures are effective. Here are key considerations for conducting regular inspections and audits:
- Establish an Inspection Schedule: Develop a schedule for conducting regular inspections and audits. Determine the frequency based on the complexity of the project, the stage of construction, and any specific safety requirements. Assign qualified personnel to carry out the inspections.
- Inspection Checklists: Develop comprehensive checklists to ensure that all areas of concern are adequately addressed during inspections. These checklists should cover various aspects, including overall site conditions, hazard control measures, worker compliance with safety procedures, and the condition and maintenance of equipment and tools.
- Document Findings: Document the findings and observations during inspections. Note any hazards identified, deficiencies in control measures, workers’ adherence to safety protocols, and any safety concerns raised by workers. These records serve as a reference for implementing corrective actions and monitoring progress.
- Hazard Reporting: Encourage workers to report hazards or near-miss incidents they observe during their work. Provide a system or platform for workers to easily report these hazards, and ensure prompt follow-up and resolution of reported issues. This encourages participation, creates a proactive safety culture, and leads to more effective hazard mitigation.
- Corrective Actions: Promptly address any deficiencies or hazards identified during inspections. Establish a system for implementing corrective actions and follow-ups. Assign responsibility and set deadlines for the completion of corrective measures. Regularly review and track progress to ensure timely resolution.
- Third-Party Audits: Consider engaging third-party auditors to conduct periodic audits of your safety management system. These independent audits provide an objective evaluation of your construction site’s safety practices, helping identify potential gaps and providing recommendations for improvement.
- Worker Involvement: Involve workers in the inspection process. Encourage their participation and solicit their input during inspections and audits. Workers on the front lines often have valuable insights and can help identify hazards or improvements to safety procedures that might otherwise be overlooked.
- Training and Awareness: Provide training to the inspection team to ensure they have the necessary knowledge and skills to perform thorough inspections. Train them on hazard recognition, the importance of accurate documentation, and how to effectively communicate findings and recommendations.
- Continual Improvement: Use the findings from inspections and audits to drive continual improvement in your safety management system. Regularly review inspection reports and audit findings to identify trends, recurring issues, or areas for improvement. Implement changes and updates to safety procedures based on these insights.
- Recognition and Rewards: Recognize and reward individuals or teams that demonstrate exceptional commitment to safety and actively contribute to hazard identification and control measures. This positive reinforcement fosters a culture of safety and encourages others to actively participate in creating a safe working environment.
Regular inspections and audits are vital for identifying hazards, evaluating control measures, and ensuring compliance with safety regulations. By conducting thorough inspections, promptly addressing issues, and continuously improving safety practices, construction companies can create a safer workplace and protect the well-being of their workers.
Remember, inspections and audits should be seen as opportunities for improvement rather than just a compliance process. They provide valuable insights into the effectiveness of your safety management system and guide you in taking proactive measures to mitigate risks on construction sites.
Read more: What Are The Hazards In Construction
Incident Reporting and Investigation Procedures
Implementing effective incident reporting and investigation procedures is essential for identifying the root causes of accidents, near-misses, and other safety incidents on construction sites. These procedures help uncover underlying hazards, improve safety measures, and prevent similar incidents from occurring in the future. Here are key steps to follow:
- Prompt Reporting: Establish a clear and straightforward process for workers to report incidents, near-misses, or hazards they observe. Encourage open communication and create a culture where workers feel comfortable reporting without fear of reprisal. Ensure that reporting can be done easily, either through an online platform, dedicated reporting forms, or direct communication with supervisors or safety personnel.
- Response and Immediate Actions: Respond promptly to reported incidents. Provide any necessary medical attention to injured workers and ensure their well-being. If there is an immediate hazard that requires immediate action to eliminate or control, address it promptly to prevent further accidents or injuries. Document all initial actions taken.
- Preservation of the Incident Scene: Where possible, preserve the scene of the incident to allow for a proper investigation. This may involve securing the area, limiting access, or taking photographs of the scene. Preserving evidence is vital for accurately identifying causes and contributing factors.
- Investigation Team: Establish a team responsible for conducting thorough incident investigations. This team should consist of qualified individuals who have a strong understanding of safety practices, hazard identification, and incident investigation techniques. It may include safety personnel, supervisors, and representatives from relevant departments.
- Root Cause Analysis: Conduct a comprehensive investigation to determine the root causes of the incident. Use techniques such as the “5 Whys” or the “Fishbone Diagram” to delve deeper into the underlying factors that contributed to the incident. Identify any direct causes, contributing factors, and systemic issues that need to be addressed.
- Documentation: Document the details of the incident investigation, including descriptions of the incident, witness statements, findings, and recommendations. Maintain accurate records of all documentation related to the incident, ensuring confidentiality where necessary.
- Corrective Actions: Based on the findings of the investigation, develop and implement corrective actions to address the root causes and prevent similar incidents from recurring. These actions may involve changes to policies, procedures, training programs, hazard control measures, or wider safety management systems.
- Communication and Follow-Up: Communicate the investigation findings and subsequent actions to all relevant parties, including workers, supervisors, and management. Provide clear guidance on any changes to policies or procedures resulting from the incident investigation. Follow up with workers involved in the incident to ensure their well-being and offer any necessary support or additional training.
- Learn from Incidents: Use incidents as learning opportunities to improve overall safety performance. Share lessons learned from incident investigations with workers through toolbox talks, safety meetings, or safety bulletins. Take measures to continuously educate workers on the hazards and risks identified from incident investigations.
- Continuous Improvement: Regularly review and evaluate the effectiveness of incident reporting and investigation procedures. Identify any areas for improvement and make necessary adjustments. This ensures that the procedures remain current, address emerging safety concerns, and maintain compliance with regulatory requirements.
By implementing comprehensive incident reporting and investigation procedures, construction companies can gain valuable insights into the underlying causes of incidents and take proactive measures to prevent future occurrences. It demonstrates a commitment to safety, fosters a culture of accountability, and protects the well-being of workers on construction sites.
Remember, the goal of incident reporting and investigation procedures is not only to assign blame or punishment, but to identify system failures, improve safety practices, and prevent similar incidents from happening in the future. Open and transparent communication throughout the process is crucial in creating a positive safety culture and fostering continuous improvement.
Conclusion
Addressing hazards on construction sites is of utmost importance to ensure the safety, well-being, and success of construction projects. By understanding and proactively mitigating hazards, construction companies can create a safe work environment, protect their workers, and enhance overall project outcomes.
Throughout this comprehensive guide, we have explored various aspects of addressing hazards on construction sites. We discussed the importance of addressing hazards, highlighting the impact on worker safety, legal compliance, cost reduction, productivity enhancement, reputation, and client confidence.
We explored the common hazards found in the construction industry, such as falls, electrical hazards, struck-by accidents, trenching and excavation hazards, hazardous materials, noise and vibration, heat and cold stress, fire and explosion hazards, and overexertion. Understanding these hazards enables construction companies to identify potential risks and implement effective control measures.
We emphasized the significance of safety regulations and guidelines, including OSHA standards, NFPA codes, building codes, hazard communication requirements, and personal protective equipment regulations. Compliance with these regulations ensures legal adherence and promotes a safe work environment.
Creating a safety culture on construction sites is crucial for maintaining a high level of safety. We discussed the importance of leadership commitment, communication, employee involvement, risk assessment, and accountability in fostering a safety culture that permeates every aspect of a construction project.
Developing a hazard identification and assessment program enables construction companies to proactively identify potential hazards, assess their risks, and implement appropriate control measures. Through ongoing program evaluation and worker participation, hazards can be continuously identified and controlled.
Implementing effective hazard control measures involves following the hierarchy of controls, which includes elimination, substitution, engineering controls, administrative controls, and personal protective equipment. By applying these measures, construction companies can minimize or eliminate hazards, ensuring the safety of their workers.
Training and education are vital in creating a knowledgeable and competent workforce. By providing orientation, hazard awareness training, safe work practice education, equipment operation training, and ongoing refresher courses, construction companies empower their workers to prioritize safety in every aspect of their work.
Regular inspections and audits allow for continuous monitoring of hazard control measures and regulatory compliance. By conducting thorough inspections, promptly addressing deficiencies, and engaging workers in the process, construction companies can maintain a safe work environment.
Incident reporting and investigation procedures are essential for identifying root causes, implementing corrective actions, and preventing future incidents. Establishing a culture of reporting, conducting thorough investigations, and taking corrective measures help ensure continuous improvement and a proactive approach to safety.
In conclusion, addressing hazards on construction sites requires a comprehensive approach that includes a commitment to safety, adherence to regulations, hazard identification and control, ongoing training and education, regular inspections and audits, and effective incident reporting and investigation procedures. By implementing these practices, construction companies can create a safety-oriented culture, protect their workers, and achieve successful project outcomes.
Remember, safety should always be the top priority when it comes to construction. By prioritizing safety, construction companies not only protect their workers but also build a strong foundation for their success and reputation in the industry.
Frequently Asked Questions about What Is A Good Way To Address Hazards On A Construction Site
Was this page helpful?
At Storables.com, we guarantee accurate and reliable information. Our content, validated by Expert Board Contributors, is crafted following stringent Editorial Policies. We're committed to providing you with well-researched, expert-backed insights for all your informational needs.
0 thoughts on “What Is A Good Way To Address Hazards On A Construction Site”