Home>diy>Building & Construction>What Are The Hazards In Construction
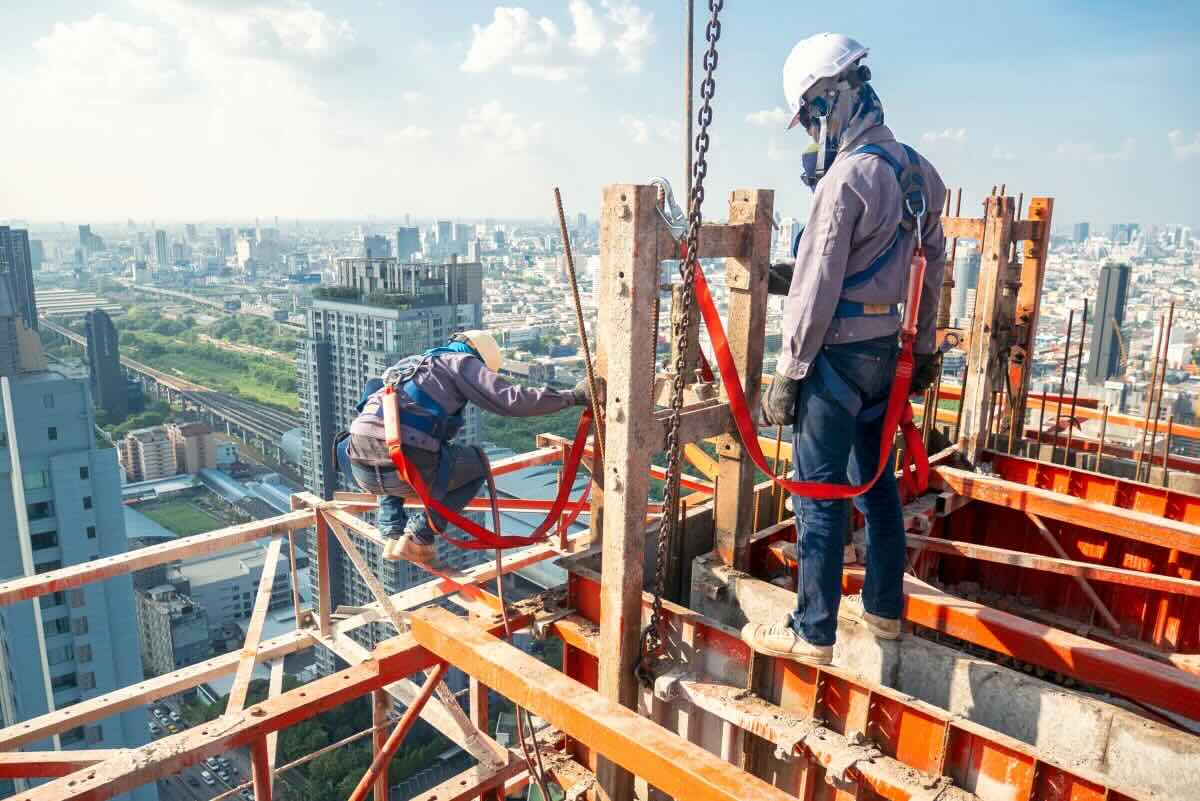
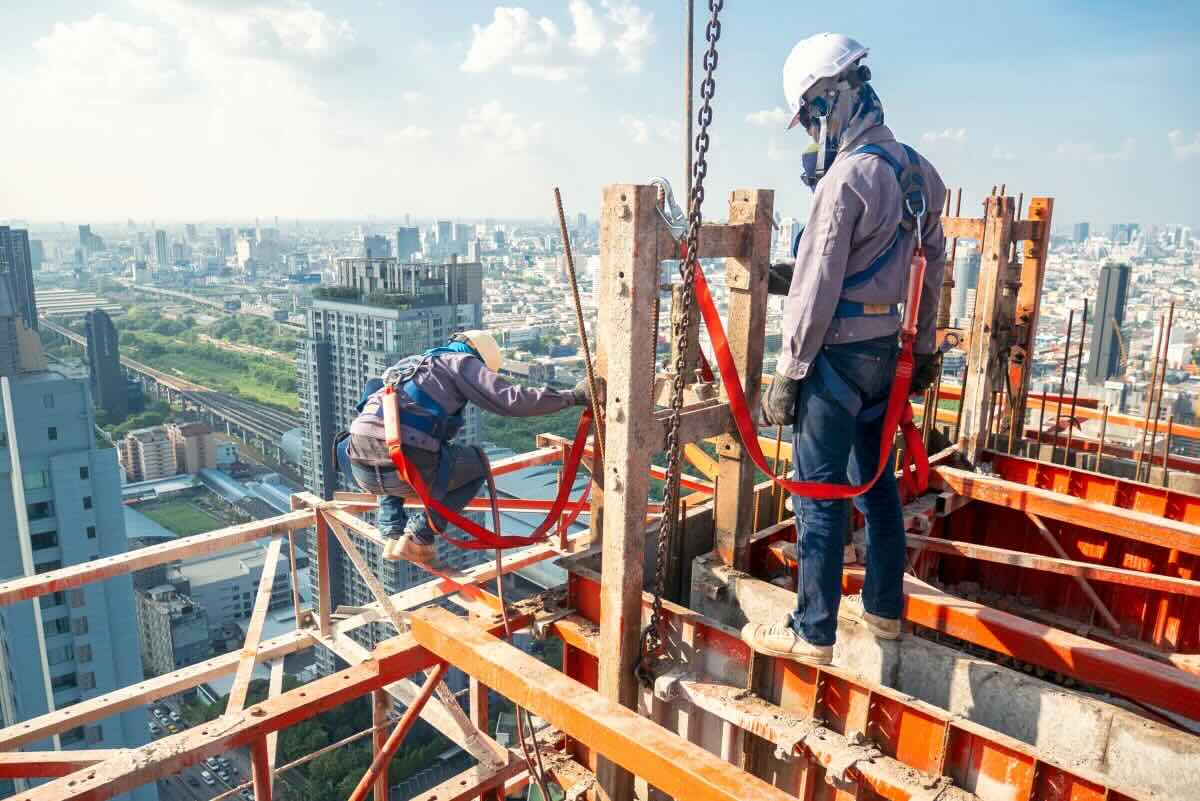
Building & Construction
What Are The Hazards In Construction
Modified: December 7, 2023
Discover the potential hazards involved in building construction and learn how to mitigate risks. Stay safe with our comprehensive guide on construction safety.
(Many of the links in this article redirect to a specific reviewed product. Your purchase of these products through affiliate links helps to generate commission for Storables.com, at no extra cost. Learn more)
Introduction
Construction is a complex and dynamic industry that plays a vital role in shaping the infrastructure of our society. From towering skyscrapers to residential houses, construction projects require meticulous planning, skilled labor, and dedicated professionals. However, amidst the hustle and bustle of construction sites, there are inherent hazards that need to be identified and managed to ensure the safety of workers and the general public.
The construction industry is known for its unique set of hazards, which can pose significant risks to workers if not properly addressed. These hazards range from falls to electrical hazards, struck-by hazards, and much more. It is crucial for construction companies and workers to be aware of these risks and implement proactive measures to mitigate them.
Falls are the leading cause of fatalities in the construction industry. Working at heights, be it on scaffolding, roofs, or ladders, poses a significant risk if proper fall protection systems are not in place. Employers must provide adequate training, proper equipment, and enforce strict safety protocols to prevent falls and protect workers from potentially life-threatening injuries.
Struck-by hazards are another common danger in construction. These hazards occur when workers are struck by moving objects such as tools, equipment, or falling debris. The use of safety barriers, signage, and personal protective equipment (PPE) can greatly reduce the likelihood and severity of struck-by incidents.
Electrical hazards are prevalent on construction sites, with the potential to cause electric shock, fires, and explosions. Workers must be trained to recognize and avoid electrical hazards, and electrical equipment should be regularly inspected and properly maintained to prevent accidents.
Key Takeaways:
- Prioritizing safety in construction is crucial to protect workers from hazards such as falls, struck-by incidents, and electrical accidents. Proper training, maintenance, and communication are essential for creating a safer work environment.
- Effective management of chemical, heat, and cold stress hazards, along with ergonomic and noise control measures, is vital to safeguard the health and well-being of construction workers. Prioritizing safety fosters a productive and efficient work environment.
Falls
Falls are the most common and deadly hazard in the construction industry. Working at heights, whether on scaffolding, roofs, or ladders, puts workers at risk of severe injuries or even fatalities if proper safety measures are not in place.
To prevent falls, employers must prioritize safety by implementing comprehensive fall protection programs. This includes providing training on proper usage of fall protection equipment, such as harnesses, lanyards, and guardrails. Workers should be trained to identify potential fall hazards and to use the appropriate safety measures when working at heights.
In addition, regular inspections of scaffolding, ladders, and elevated work platforms should be conducted to ensure that they are in good condition and meet safety standards. Any damaged or defective equipment should be immediately repaired or replaced to prevent accidents.
Furthermore, employers must ensure that workers have a clear and unobstructed path to exit in case of an emergency. Stairways and walkways should be properly illuminated and adequately maintained to reduce the risk of tripping and falling.
It is also crucial to establish clear communication channels and provide ongoing training to workers about fall prevention. This will enable them to stay informed about new safety protocols and reinforce the importance of following safe practices.
By prioritizing fall prevention and implementing proper safety measures, employers can create a safer working environment and protect workers from devastating falls.
Struck-by Hazards
Struck-by hazards are a significant concern in the construction industry and can result in severe injuries or fatalities. These hazards occur when workers are struck by moving objects, such as tools, equipment, or falling debris.
To mitigate struck-by hazards, it is essential to establish clear safety protocols and provide adequate training to all workers. This includes identifying potential hazards and implementing measures to prevent them. For example, tools and equipment should be properly secured, and workers should be trained on how to use them safely.
Another crucial aspect of preventing struck-by hazards is maintaining a clean and organized work area. Construction sites can be chaotic and cluttered, which increases the risk of objects falling or being inadvertently thrown. Regular inspections and housekeeping practices should be implemented to keep the work area free of potential hazards.
Personal protective equipment (PPE) also plays a vital role in preventing struck-by incidents. Hard hats, safety glasses, steel-toed boots, and high-visibility clothing should be worn by workers at all times to provide protection against falling objects and enhance visibility.
Additionally, barricades, signage, and warning systems should be utilized to alert workers to potential struck-by hazards. This can help create a safer work environment and prevent accidents caused by unexpected movement of equipment or vehicles.
By promoting a culture of safety, providing thorough training, and implementing effective control measures, construction companies can significantly reduce the risk of struck-by hazards. This not only protects the well-being of workers but also ensures a more productive and efficient work environment.
Electrical Hazards
Electrical hazards are a common concern in the construction industry and can result in electric shock, fires, and even fatalities if not properly managed. Construction sites often have a high concentration of electrical equipment, including power tools, wiring, and temporary electrical installations.
To prevent electrical hazards, it is crucial to follow proper electrical safety protocols. This starts with ensuring that all electrical work is performed by qualified and trained personnel who understand the principles of electrical safety.
During construction, temporary electrical installations should be installed and maintained in accordance with relevant electrical codes and standards. Regular inspections of electrical equipment and wiring systems are necessary to detect and address any potential issues or hazards.
One of the key steps in electrical hazard prevention is identifying and labeling electrical panels, circuits, and equipment. Clear and visible signage should be used to communicate potential dangers and indicate the presence of live electrical systems.
Workers should also be trained to recognize electrical hazards and understand the appropriate actions to take in the event of an emergency. This includes knowing how to properly de-energize equipment, using lockout/tagout procedures, and understanding the importance of using personal protective equipment (PPE) when working around electrical systems.
Furthermore, proper grounding and bonding should be implemented to mitigate the risk of electrical faults and ensure safe electrical operation. Ground fault circuit interrupters (GFCIs) should be used to provide protection against electric shock, particularly in wet or damp environments.
Regular communication and training programs can help promote awareness of electrical hazards and reinforce safe work practices. By taking these proactive measures, construction companies can significantly reduce the risk of electrical accidents and protect the well-being of their workers.
Caught-in or between Hazards
Caught-in or between hazards are a significant concern in the construction industry and can result in serious injuries or fatalities. These hazards occur when workers become stuck, squeezed, caught, crushed, or otherwise trapped between two objects or machinery.
To prevent caught-in or between hazards, it is vital to implement proper safety protocols and provide thorough training to workers. This includes identifying potential hazards and implementing measures to eliminate or minimize them.
One of the primary ways to address caught-in or between hazards is through machine guarding. Proper guarding systems should be in place on machinery and equipment to prevent workers from coming into contact with moving parts or hazardous areas.
Regular maintenance and inspection of machinery are also crucial to ensure that all safety features are in proper working condition. Any faulty equipment should be immediately repaired or replaced to prevent accidents.
Proper communication and coordination among workers are essential in preventing caught-in or between hazards. Clear signals and warning systems should be established to ensure that workers are aware of potential dangers and can take appropriate actions to mitigate risks.
In confined spaces, where the risk of caught-in or between hazards is higher, specific procedures should be implemented. This includes proper ventilation, monitoring of atmospheric conditions, and following confined space entry protocols to ensure worker safety.
Worker training is a vital component of preventing caught-in or between hazards. Employees should receive comprehensive training on safe work practices, proper use of equipment, and the importance of situational awareness in order to avoid getting caught in hazardous situations.
By prioritizing safety, fostering a culture of awareness, and implementing the necessary safety measures, construction companies can significantly reduce the risk of caught-in or between hazards. This will create a safer work environment for all employees and prevent devastating accidents from occurring.
Read more: How To Avoid Hazards On A Construction Site
HAZCOM and Hazardous Materials
The handling and use of hazardous materials is an integral part of many construction projects. Whether it’s paint, solvents, fuels, or other chemicals, it is crucial to properly manage and communicate the associated risks to ensure the safety of workers and the surrounding environment.
The Hazard Communication Standard (HAZCOM) is a key regulation that governs the proper labeling, handling, and communication of hazardous materials in the construction industry. Employers have a responsibility to provide comprehensive training to workers on the safe use, storage, and handling of hazardous materials.
One of the primary aspects of HAZCOM is proper labeling and identification of hazardous materials. Containers of chemicals should have clear and readable labels that include information such as the name of the hazardous substance, associated hazards, and precautionary measures.
Employees should also have access to safety data sheets (SDS) for all hazardous materials used on site. These sheets provide detailed information about the chemical composition, physical and chemical properties, potential hazards, and recommended safety precautions for each substance.
It is vital for employers to train workers on how to interpret and understand the information presented on the labels and SDS. This includes educating employees about the potential health effects of exposure to hazardous materials and the proper use of personal protective equipment (PPE).
Proper storage of hazardous materials is another critical aspect of HAZCOM. Incompatible substances should never be stored together, and flammable materials should be stored in designated storage areas away from ignition sources.
In the event of a spill or release of hazardous materials, there should be established procedures for containment, cleanup, and reporting. Proper procedures for disposing of hazardous waste should also be followed to prevent environmental contamination.
Regular inspections and audits should be conducted to ensure compliance with HAZCOM requirements. Any deficiencies or non-compliance should be promptly addressed to maintain a safe working environment.
By adhering to HAZCOM regulations and implementing effective safety measures, construction companies can effectively manage and communicate the risks associated with hazardous materials, protecting the health and well-being of workers and the environment.
Scaffolding Hazards
Scaffolding is a crucial component in many construction projects, providing a platform for workers to perform tasks at elevated heights. However, scaffolding can be a source of significant hazards if not properly erected, maintained, and used.
To ensure the safety of workers, it is essential to identify and address potential scaffolding hazards. One of the primary concerns is the structural stability of the scaffold. It should be properly designed, erected, and inspected by competent personnel to ensure its integrity and ability to support the intended load.
Regular inspections should be conducted to check for any damage, corrosion, or weaknesses in the scaffold structure. In addition, proper access to scaffolds should be provided, such as ladders, stairs, or ramps, to minimize the risk of falls during ascent or descent.
Scaffolding should be equipped with guardrails, midrails, and toeboards to prevent workers from falling off the scaffold. These fall protection systems should be properly installed, secure, and able to withstand the force of a worker leaning against them.
Workers should also be trained on safe work practices when using scaffolding. This includes avoiding overloading the scaffold, not using the scaffold during adverse weather conditions, and not modifying the scaffold without proper authorization and engineering oversight.
Frequent communication and coordination should take place between workers on the scaffold and those working below. Tools, equipment, and materials should be securely stored and not allowed to accumulate on the scaffold, which can increase the risk of tripping or falling objects.
Scaffolding should also be protected from electrical hazards. It should be kept at a safe distance from power lines and electrical sources to prevent accidental contact and electrocution.
Lastly, proper training on the inspection and use of personal fall arrest systems (PFAS) should be provided to workers when working on scaffolds at heights. This ensures that workers are equipped with the knowledge and skills to properly secure themselves in the event of a fall.
By addressing scaffolding hazards through proper design, installation, maintenance, and worker training, construction companies can significantly reduce the risk of accidents and injuries associated with scaffolding. This will help create a safer working environment for all construction personnel.
Crane and Hoisting Hazards
Crane and hoisting operations are an integral part of many construction projects, allowing for the transportation and movement of heavy materials and equipment. However, these operations also come with inherent hazards that need to be carefully managed to ensure the safety of workers and the surrounding environment.
One of the primary concerns in crane and hoisting operations is the potential for accidents due to equipment failure or improper use. It is crucial to regularly inspect and maintain cranes, hoists, and rigging equipment to ensure they are in proper working condition. Any signs of damage or wear should be immediately addressed, and defective equipment should be taken out of service until repaired or replaced.
Proper training and certification of crane operators are essential to ensure they have the necessary skills and knowledge to operate the equipment safely. Operators must know the weight limits and capacity of the cranes and understand proper lifting techniques and load securement practices.
Clear communication and coordination between the crane operator and other workers on the ground is vital to prevent accidents. Hand signals or radios should be used to relay instructions and alert the operator of any potential hazards in the lifting area.
Establishing an exclusion zone around the operating area is essential to keep unauthorized personnel out of harm’s way. Adequate signage and barriers should be used to denote restricted areas and prevent entry by unauthorized individuals.
Weather conditions play a significant role in crane and hoisting operations. High winds, rain, or snow can impact the stability and safety of the equipment. It is crucial to closely monitor weather conditions and suspend operations if necessary to prevent accidents.
Proper rigging techniques and inspections are crucial in safe crane and hoisting operations. Rigging equipment, including slings, shackles, and hooks, should be inspected regularly for wear, damage, or defects. Workers involved in rigging operations should have the necessary training and knowledge to identify potential hazards and ensure proper load securement.
Regular maintenance and inspection of crane support structures, such as outriggers or stabilizers, are also crucial to ensure stability during lifting operations. All safety devices, including limit switches, emergency stop buttons, and anti-two-blocking systems, should be regularly tested and maintained.
By prioritizing proper training, regular equipment maintenance, clear communication, and adherence to established safety protocols, construction companies can effectively mitigate the hazards associated with crane and hoisting operations. This will help ensure the safety of workers and the success of construction projects.
Always wear appropriate personal protective equipment (PPE) such as hard hats, gloves, and safety glasses to protect yourself from hazards on construction sites.
Excavation Hazards
Excavation work is a common and essential activity in construction projects, involving the removal of soil or rock to create a foundation, trenches, or underground structures. However, excavation work poses significant hazards that need to be identified and properly managed to ensure the safety of workers.
One of the most significant hazards in excavation work is the potential for cave-ins. Excavations that are not adequately sloped, shored, or supported are at risk of collapsing, potentially trapping and burying workers. Proper planning and engineering expertise are required to determine the appropriate methods for preventing cave-ins based on the soil type and depth of the excavation.
Regular inspections by competent personnel are crucial to identify any signs of instability or potential cave-in hazards. These inspections should be conducted before work begins, during excavation, and after any significant changes occur that could impact the stability of the excavation.
Proper shoring and support systems, such as trench boxes or hydraulic supports, should be employed to prevent cave-ins and protect workers inside the excavation. Inspections and maintenance of these systems should be conducted to ensure their integrity and effectiveness.
Excavation sites can also present hazards related to falling or rolling materials, such as soil, rocks, or equipment. Proper slope grading, barricades, and warning signs should be used to control and prevent the movement of materials that could pose a danger to workers.
It is essential to locate and identify underground utilities before commencing excavation work. Accidental damage to gas, water, or electrical lines can lead to serious injuries, explosions, or service disruptions. Proper communication with utility companies and the use of appropriate detection equipment are necessary to identify and avoid these hazards.
Workers should also be trained on safe entry and exit procedures when working in excavations, as well as how to recognize signs of hazardous atmospheric conditions, such as low oxygen levels or the presence of toxic gases. Adequate ventilation, atmospheric monitoring, and the use of personal protective equipment (PPE) are necessary to safeguard workers from respiratory hazards.
Furthermore, construction companies should establish emergency response and rescue procedures in the event of an excavation-related incident. Proper training and resources should be available to promptly respond to potential emergencies and ensure the safety of workers.
By prioritizing safety, using proper excavation techniques, conducting regular inspections, and providing comprehensive training, construction companies can significantly reduce the hazards associated with excavation work. This will help create a safer work environment and protect the well-being of all workers involved.
Welding and Cutting Hazards
Welding and cutting processes are integral to many construction projects, allowing for the joining, shaping, and modification of various materials. However, these processes also come with inherent hazards that need to be effectively managed to ensure the safety of workers.
One of the primary hazards in welding and cutting operations is the potential for fires and explosions. Sparks, heat, and hot materials can ignite flammable substances if proper precautions are not taken. It is crucial to identify and remove or isolate any flammable materials in the vicinity before starting welding or cutting work.
Proper ventilation is essential in welding and cutting operations to control the accumulation of hazardous fumes and gases. Adequate ventilation systems, such as local exhaust ventilation or adequate air exchange rates, should be in place to ensure the removal of airborne contaminants.
Workers engaged in welding and cutting activities should wear appropriate personal protective equipment (PPE), including welding helmets with proper shade lenses, flame-resistant clothing, goggles, gloves, and respiratory protection, as necessary. Training on the proper use, maintenance, and limitations of PPE is crucial to ensure worker safety.
Before starting work, a thorough assessment of the work area should be conducted to ensure proper grounding of equipment and connections. Faulty or inadequate grounding can lead to electrical shocks or fires. All electrical cables and connections should be inspected regularly for damage and replaced as needed.
In confined spaces, special precautions should be taken to prevent the accumulation of hazardous gases or lack of oxygen. Adequate testing and monitoring must be carried out before entering confined spaces, and proper ventilation and respiratory protection should be provided.
Proper training in safe welding and cutting practices is essential for all workers involved in these operations. This includes knowledge of proper equipment setup, safe work distances, and the use of fire extinguishers. Training should also cover emergency procedures in the event of a fire, injury, or hazardous material release.
Work areas should be clearly marked and barriers established to prevent unauthorized personnel from entering the welding and cutting zone. Regular inspections and adherence to established safety protocols help maintain a safe work environment.
By proactively identifying and addressing welding and cutting hazards, providing comprehensive training, and enforcing strict safety measures, construction companies can mitigate the risks associated with these operations. This will promote a safer work environment and protect the well-being of workers.
Noise and Vibration Hazards
Noise and vibration hazards are common in the construction industry and can have detrimental effects on the health and well-being of workers. Prolonged exposure to high levels of noise and vibration can lead to hearing loss, musculoskeletal disorders, and other serious health conditions.
Noise hazards in construction can arise from various sources, including equipment such as power tools, generators, and heavy machinery. To mitigate these hazards, it is essential to identify areas with high noise levels and implement measures to reduce exposure.
Engineering controls should be the first line of defense against noise hazards. This can include modifying equipment or using noise-dampening technologies to reduce noise emissions at the source. Enclosing noisy equipment or using sound-absorbing materials can also help reduce noise levels.
Administrative controls should also be implemented. This includes implementing work rotations to limit individual exposure to high noise levels, scheduling noisy activities during periods when fewer workers are present, and establishing quiet areas where workers can take breaks away from noisy areas.
Personal protective equipment (PPE), such as earmuffs or earplugs, should be provided to workers who are exposed to high noise levels. Training on the proper use of PPE, maintenance, and limitations is essential to ensure its effectiveness.
Vibration hazards are commonly associated with the use of power tools, heavy machinery, and vibrating equipment. Prolonged exposure to hand-arm vibrations can lead to disorders such as Hand-Arm Vibration Syndrome (HAVS) or vibration white finger.
To mitigate vibration hazards, employers should assess the risk and provide workers with tools and equipment that have reduced vibration levels. Regular maintenance and proper fitting of anti-vibration handles and grips should be ensured.
Training on the proper use of vibrating tools and equipment, as well as the recognition of early symptoms of vibration-related disorders, is crucial. Job rotation and frequent rest breaks can also help minimize the effects of vibration exposure.
Periodic medical evaluations should be conducted to monitor the health of workers who are exposed to noise and vibration. This helps identify early signs of hearing loss or musculoskeletal disorders, enabling appropriate interventions and control measures.
By implementing a comprehensive noise and vibration control program, construction companies can protect the health and well-being of their workers. This includes identifying noise and vibration hazards, implementing engineering and administrative controls, providing suitable PPE, and emphasizing worker training and education.
Heat and Cold Stress Hazards
Heat and cold stress hazards are prevalent in the construction industry and can have serious implications on the health and safety of workers. Working in extreme temperatures for prolonged periods can lead to heat-related illnesses or cold-related injuries if not properly managed.
Heat stress occurs when the body’s ability to regulate heat is overwhelmed, leading to conditions such as heat exhaustion or heat stroke. To prevent heat stress, it is crucial to implement proper controls and provide training to workers.
Workers should have access to shaded areas or rest breaks in cool areas to minimize exposure to high temperatures. Adequate hydration is essential, and water or electrolyte-rich beverages should be readily available on-site. Encouraging workers to drink frequently and take breaks to rehydrate is vital in preventing heat-related illnesses.
Personal protective equipment (PPE) should allow for proper ventilation and breathability to minimize heat stress. Adjusting work schedules to avoid the hottest times of the day and providing appropriate ventilation or cooling systems in enclosed spaces can also help mitigate heat stress hazards.
Cold stress occurs when the body loses heat faster than it can generate, leading to conditions such as frostbite or hypothermia. Proper protective clothing, including insulated outerwear and gloves, should be provided to workers in cold environments.
Workers should be encouraged to take breaks and warm up in heated areas during extremely cold conditions. Training on frostbite and hypothermia symptoms and the importance of early intervention is crucial to prevent cold-related injuries.
Regular monitoring of weather conditions can help identify periods of extreme heat or cold, allowing for proactive measures to be implemented. Weather alerts and guidelines should be provided to workers to ensure their safety and well-being.
Education and training on heat and cold stress hazards should be provided to all workers. This should include recognizing the signs and symptoms of heat-related illnesses and cold-related injuries, as well as appropriate response and first aid measures.
Workers should be encouraged to report any discomfort, symptoms, or concerns related to heat or cold stress hazards. Prompt response and intervention are essential to prevent further health issues or injuries.
By implementing comprehensive heat and cold stress management programs, construction companies can ensure the well-being of their workers and minimize the risks associated with working in extreme temperatures. This will create a safer and healthier work environment for all construction personnel.
Ergonomic Hazards
Ergonomic hazards in the construction industry can arise from the physical demands and repetitive tasks that workers perform on a daily basis. These hazards can lead to musculoskeletal disorders, such as strains, sprains, and chronic pain, if not properly addressed.
One of the primary ergonomic hazards in construction is the manual lifting and carrying of heavy loads. Workers may be required to lift and transport materials, tools, or equipment, potentially putting strain on their backs, shoulders, and other body parts. Proper lifting techniques, such as bending the knees and using leg muscles, should be employed to minimize the risk of injury.
Repetitive motions, such as hammering or using vibrating tools, can also contribute to ergonomic hazards. Using ergonomic tools with vibration-dampening features or practicing job rotation to minimize prolonged exposure to these tasks can help reduce the risk of musculoskeletal disorders.
Poorly designed workstations or equipment can place unnecessary strain on workers’ bodies. Employers should ensure that workstations are adjustable and provide proper support for workers’ backs, wrists, and other body parts. Tools and equipment with ergonomically designed handles and grips can also help reduce the risk of ergonomic injuries.
Awkward and uncomfortable working postures, such as bending, twisting, or reaching overhead, can increase the risk of musculoskeletal disorders. Employers should strive to eliminate or minimize these postures by optimizing work processes, providing adequate workspace, and using assistive devices when necessary.
Regular rest breaks should be encouraged, and workers should be given the opportunity to change positions and stretch their muscles throughout the workday. This helps reduce fatigue and muscle tension, preventing the onset of ergonomic-related injuries.
Training and education on proper ergonomics should be provided to all workers. This includes instruction on how to recognize ergonomic hazards, apply ergonomic principles to their work tasks, and report concerns or discomfort associated with ergonomic hazards.
By prioritizing ergonomic practices and implementing preventive measures, such as providing ergonomic tools and equipment, promoting proper lifting techniques, and educating workers, construction companies can minimize the risk of musculoskeletal disorders. This will create a safer and healthier work environment, improve productivity, and enhance the well-being of workers.
Chemical Hazards
Chemical hazards are a significant concern in the construction industry, as workers often come into contact with various substances that can pose significant risks to their health and safety. Hazardous chemicals, such as solvents, adhesives, paints, and cleaning agents, are commonly used in construction projects which necessitate proper management and control.
One of the key aspects of chemical hazard management is the implementation of a comprehensive Hazard Communication Program. This program ensures that workers are informed about the potential hazards, safe handling procedures, and proper storage of the chemicals they work with.
Proper labeling of containers is essential to communicate the contents and associated hazards. Employers must ensure that all containers are clearly labeled with the name of the chemical, hazards, and precautionary measures to be taken.
Safety Data Sheets (SDS) should be readily available for all hazardous chemicals used on-site. These documents provide detailed information about the chemical composition, physical and chemical properties, handling procedures, and emergency response protocols. It is important for workers to have easy access to SDS and understand how to interpret the information presented.
Appropriate personal protective equipment (PPE) should be provided to workers who handle or are exposed to hazardous chemicals. This may include gloves, goggles, respirators, or protective clothing. Training on the proper use, maintenance, and limitations of PPE is crucial to ensure worker safety.
Proper ventilation systems should be installed and maintained to control the release of hazardous fumes, vapors, or dust. This helps minimize the risk of inhalation or exposure to dangerous chemicals.
Regular inspections and maintenance of chemical storage areas are necessary to identify and address any potential leaks, spills, or improper storage practices. Chemical spills should be promptly cleaned up using proper containment and disposal methods.
Education and training on the safe handling and use of hazardous chemicals should be provided to all workers. This includes proper storage, mixing, and disposal procedures, as well as recognizing and responding to chemical spills or exposures.
Periodic monitoring and testing of air quality should be conducted to assess the level of chemical exposure in the work environment. This helps ensure that exposure levels are within acceptable limits and allows for the implementation of additional control measures if needed.
By implementing effective chemical hazard management programs, construction companies can protect the health and safety of their workers. This includes proper labeling, access to SDS, provision of PPE, installation of ventilation systems, regular inspections, and comprehensive training. Through these efforts, the risk of chemical-related incidents can be significantly reduced.
Conclusion
The construction industry is a crucial sector that shapes our built environment, but it is not without its hazards. From falls to electrical hazards, struck-by hazards to chemical exposures, it is essential for construction companies to effectively manage and mitigate these risks to ensure the safety and well-being of workers.
By prioritizing safety and implementing proactive measures, construction companies can significantly reduce the occurrence of accidents and injuries. Proper training, clear communication, and the use of personal protective equipment (PPE) are vital components of a comprehensive safety program.
Falls are one of the leading causes of fatalities in construction, highlighting the need for proper fall protection systems and training. Struck-by hazards and electrical hazards also pose significant risks that can be mitigated through proper equipment maintenance, training, and hazard identification.
HAZCOM programs and proper handling of hazardous materials are essential to prevent chemical exposures and ensure worker safety. Scaffolding hazards, crane and hoisting hazards, excavation hazards, and welding and cutting hazards all require careful planning, training, and adherence to safety protocols.
Heat and cold stress hazards, ergonomic hazards, noise and vibration hazards must be effectively managed to protect workers from potential health issues. Construction companies should implement proper controls, training, and monitoring to prevent these hazards from causing harm.
In conclusion, construction companies must prioritize the safety and well-being of their workers by identifying and mitigating the various hazards present in construction environments. Through thorough training, proper equipment maintenance, comprehensive safety programs, and ongoing communication, construction sites can become safer spaces for all workers involved in building our infrastructure.
By continuously improving safety practices, construction companies can create a culture of safety that not only protects workers but also fosters a more productive and efficient work environment. Investing in safety is an investment in the success and longevity of the construction industry as a whole.
Frequently Asked Questions about What Are The Hazards In Construction
Was this page helpful?
At Storables.com, we guarantee accurate and reliable information. Our content, validated by Expert Board Contributors, is crafted following stringent Editorial Policies. We're committed to providing you with well-researched, expert-backed insights for all your informational needs.
0 thoughts on “What Are The Hazards In Construction”