Home>diy>Building & Construction>What Is An MEP In Construction
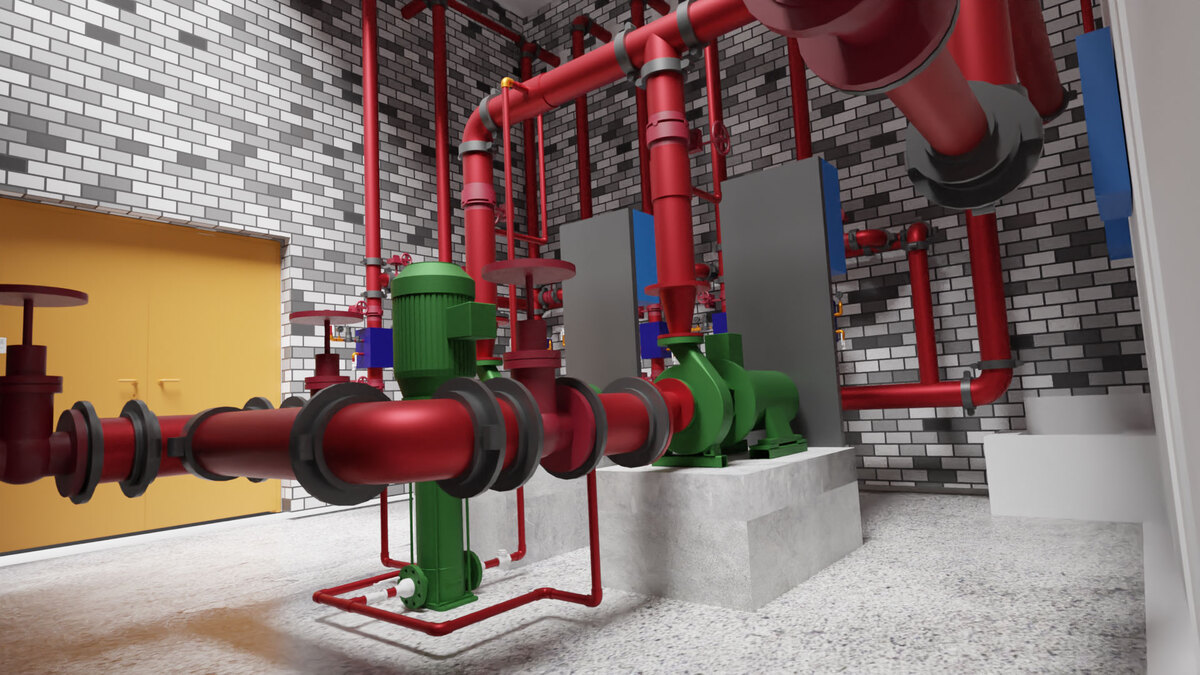
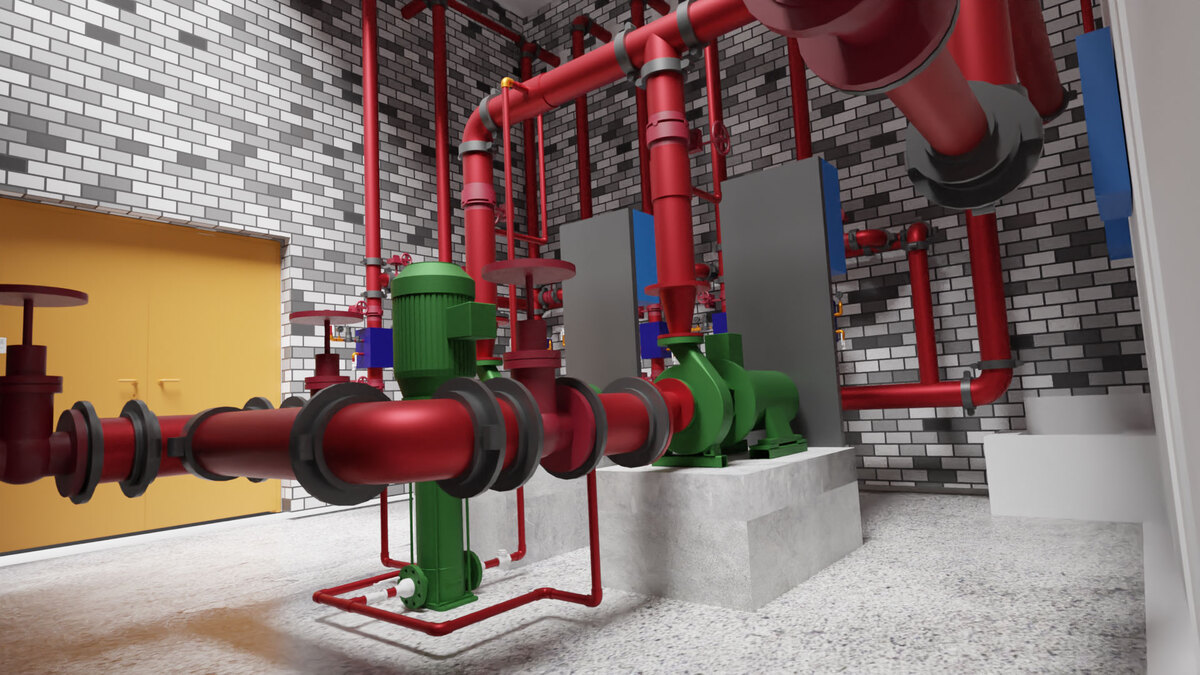
Building & Construction
What Is An MEP In Construction
Modified: January 6, 2024
Learn what an MEP is in construction and how it is crucial for building-construction projects. Find out the importance of MEP systems in ensuring efficient and functional buildings.
(Many of the links in this article redirect to a specific reviewed product. Your purchase of these products through affiliate links helps to generate commission for Storables.com, at no extra cost. Learn more)
Introduction
When it comes to building construction, there are various components and systems that need to be carefully designed, installed, and integrated to ensure the smooth functioning and efficiency of a structure. One crucial aspect of construction is the MEP (Mechanical, Electrical, and Plumbing) systems, which play a vital role in creating functional and comfortable spaces for occupants.
MEP refers to the integrated systems that encompass mechanical, electrical, and plumbing services within a building. These systems are responsible for providing essential functions such as heating, ventilation, air conditioning, lighting, electrical power distribution, and plumbing services, including water supply and drainage. MEP professionals are experts in designing, installing, and maintaining these systems to ensure optimal performance and sustainability.
In this article, we will delve into the world of MEP in construction and explore the role and responsibilities of MEP professionals, the common components of MEP systems, the integration with structural and architectural elements, the importance of coordination in construction projects, and the latest innovations and technologies in MEP construction.
Understanding the intricacies of MEP systems is essential for architects, engineers, contractors, and anyone involved in the construction industry. It not only ensures the safety and comfort of occupants but also contributes to the overall efficiency, durability, and sustainability of the building project.
Now, let us dive deeper into the world of MEP and explore its fundamental concepts, components, and significance in the realm of construction.
Key Takeaways:
- MEP systems, encompassing mechanical, electrical, and plumbing services, are vital for building functionality and occupant comfort. Coordination, innovation, and sustainability are key focus areas for MEP professionals in construction projects.
- The integration of MEP systems with structural and architectural elements, along with the adoption of the latest technologies, ensures efficient building operation and occupant well-being. MEP professionals navigate challenges and drive advancements in the construction industry.
Read more: What Are MEP Works In Construction
Understanding MEP in Construction
MEP systems are an integral part of any building construction project, encompassing mechanical, electrical, and plumbing services. These systems ensure the functionality, comfort, and safety of a structure by providing essential services and amenities to occupants.
The mechanical aspect of MEP focuses on heating, ventilation, and air conditioning (HVAC) systems. HVAC systems are responsible for regulating the temperature, humidity, and air quality within a building. This includes heating and cooling systems, ventilation fans, air distribution networks, and control systems. Proper HVAC design and installation are crucial for maintaining a comfortable and healthy indoor environment.
The electrical component of MEP involves the design and installation of electrical systems, including power distribution, lighting, and communication networks. Electrical systems provide electrical power to the building, ensuring that lights, appliances, and equipment operate efficiently. With the increasing use of technology, such as smart home systems and automation, electrical design in modern buildings has become more sophisticated and complex.
Plumbing services are also an important part of MEP. Plumbing systems involve the supply of clean water for various purposes, such as drinking, sanitation, and irrigation. Additionally, plumbing systems manage the drainage and disposal of waste water. Plumbing design includes pipes, fixtures, pumps, water treatment systems, and waste management infrastructure. Proper plumbing design and installation are vital for ensuring reliable water supply and efficient waste management.
MEP systems are interconnected and rely on each other for optimal performance. For example, HVAC systems require electrical power and control systems for operation, while plumbing systems may involve pumps and electrical controls for water distribution. Therefore, coordination and integration are crucial to ensure the seamless functioning of MEP systems within a building.
MEP professionals, including engineers, designers, and technicians, are responsible for the design, installation, and maintenance of these systems. They utilize their expertise to ensure that MEP systems comply with building codes, regulations, and industry standards. MEP professionals must possess in-depth knowledge of the mechanical, electrical, and plumbing aspects of construction, as well as an understanding of sustainability practices and energy-efficient solutions.
Now that we have a basic understanding of MEP systems in construction, let us explore the specific roles and responsibilities of MEP professionals in the next section.
Role and Responsibilities of an MEP Professional
MEP professionals play a vital role in the successful implementation of MEP systems in construction projects. Their expertise and knowledge ensure the seamless integration and operation of mechanical, electrical, and plumbing services within a building. Let’s explore the specific roles and responsibilities of MEP professionals in more detail:
1. Designing MEP Systems: One of the primary responsibilities of an MEP professional is to design the MEP systems of a building. This involves analyzing and understanding the project requirements, developing design concepts, and creating detailed drawings and specifications. The design must comply with building codes, safety regulations, and energy efficiency standards. MEP professionals utilize computer-aided design (CAD) software and simulation tools to optimize system layouts, equipment selection, and energy performance.
2. Coordinating with Other Disciplines: MEP professionals need to collaborate closely with architects, structural engineers, and other professionals involved in the construction project. They coordinate their designs and ensure that MEP systems integrate seamlessly with the structural and architectural elements of the building. This coordination is essential to avoid conflicts or clashes between MEP systems and other components.
3. Sizing and Selecting Equipment: MEP professionals are responsible for determining the appropriate sizes and capacities of mechanical and electrical equipment required for the project. They consider factors such as building size, occupancy, thermal loads, and energy efficiency requirements. Proper equipment selection ensures optimal performance, energy efficiency, and cost-effectiveness of the MEP systems.
4. Estimating and Cost Control: MEP professionals are involved in estimating the costs associated with MEP systems, including equipment, materials, installation, and maintenance. They closely monitor the project budget to ensure cost control and identify potential cost-saving measures without compromising on system efficiency and functionality.
5. Project Management: MEP professionals are often responsible for managing and overseeing the installation and commissioning of MEP systems. They ensure that the installation is carried out according to the design specifications, monitor the progress of construction activities, and coordinate with contractors and sub-contractors. They also conduct inspections and tests to verify the performance and functionality of MEP systems.
6. Maintenance and Upgrades: After the construction phase is complete, MEP professionals are involved in the ongoing maintenance and operation of the MEP systems. They develop maintenance plans, conduct regular inspections, and address any issues or malfunctions that may arise. They also stay updated on the latest advancements in MEP technology and recommend upgrades or modifications to improve system efficiency and sustainability.
In summary, MEP professionals are responsible for designing, coordinating, and managing the MEP systems in construction projects. Their expertise ensures that buildings have efficient and well-functioning mechanical, electrical, and plumbing services that meet safety, comfort, and sustainability requirements.
MEP Systems in Construction
MEP systems are an essential component of any construction project, ensuring the functionality, comfort, and safety of a building. Let’s delve into the different MEP systems commonly found in construction:
1. Mechanical Systems: Mechanical systems in MEP encompass heating, ventilation, and air conditioning (HVAC) systems. HVAC systems provide thermal comfort and air quality within a building. Heating systems, such as boilers or furnaces, generate heat to raise the indoor temperature during colder months. Ventilation systems ensure the exchange of indoor and outdoor air, removing pollutants and replenishing fresh air. Air conditioning systems provide cooling by removing heat and humidity from the indoor air.
2. Electrical Systems: Electrical systems in MEP include the power distribution, lighting, and communication networks of a building. Power distribution systems deliver electrical energy from the main power source to various areas of the building. This includes wiring, circuit breakers, transformers, and distribution panels. Lighting systems encompass the design and installation of indoor and outdoor lighting, considering factors such as energy efficiency, aesthetics, and functionality. Communication networks involve the installation of structured cabling systems, telephone lines, data networks, and audio-visual systems.
3. Plumbing Systems: Plumbing systems in MEP focus on the water supply and wastewater management of a building. This involves the design and installation of pipes, fixtures, pumps, and water treatment systems. The water supply system ensures the delivery of clean, potable water to sinks, showers, toilets, and other water outlets. Wastewater management systems handle the safe disposal and drainage of used water and sewage. Plumbing systems also include fire protection systems, such as sprinklers and fire hydrants, to ensure the safety of occupants in case of a fire emergency.
4. Fire Protection Systems: Fire protection systems are an integral part of MEP in construction. These systems include fire alarm systems, fire sprinklers, fire extinguishers, and fire hydrants. MEP professionals design and install these systems to detect, suppress, and control fires effectively. The integration of fire protection systems with other MEP systems and structural elements is crucial for ensuring the safety of occupants and minimizing property damage in the event of a fire.
5. Sustainable and Renewable Energy Systems: With the increasing focus on sustainability, MEP systems now often incorporate sustainable and renewable energy technologies. These systems include solar panels, wind turbines, geothermal systems, and energy-efficient lighting and HVAC systems. MEP professionals design and implement these systems to reduce energy consumption, lower carbon emissions, and promote sustainable practices in construction.
MEP systems are interconnected and require careful coordination during the design, installation, and maintenance phases of a construction project. Efficient integration of MEP systems with structural and architectural elements is vital to ensure smooth operation and optimal performance.
In the next section, we will explore the common components that make up MEP systems in more detail.
Common MEP Components
MEP systems consist of various components that work together to provide the necessary mechanical, electrical, and plumbing services in a building. Here are some common components found in MEP systems:
1. HVAC Components: HVAC systems utilize a range of components to control temperature, humidity, and air quality. These include:
– Heating Equipment: Furnaces, boilers, heat pumps, and radiant heaters are used to provide warmth during colder months.
– Cooling Equipment: Air conditioners, chillers, and cooling towers help remove heat and reduce indoor temperature.
– Ventilation Equipment: Fans, air handlers, and ventilation ducts enable the circulation of fresh air and the removal of stale air.
2. Electrical Components: Electrical systems in MEP consist of several components, such as:
– Power Distribution: Transformers, switchboards, and electrical panels distribute electrical power to different areas of the building.
– Lighting Fixtures: Various types of light fixtures, including LED lights, fluorescent lights, and recessed lights, provide illumination.
– Electrical Wiring: Cables, conduits, and wiring channels carry electrical current throughout the building.
– Switches and Outlets: Switches control the on/off function of lights and appliances, while outlets provide access to electrical power.
3. Plumbing Components: Plumbing systems in MEP include the following components:
– Pipes and Fittings: Water supply and drainage pipes, along with various fittings, are used to transport water throughout the building.
– Fixtures: Sinks, toilets, showers, bathtubs, and faucets are fixtures that provide water supply and drainage points.
– Pumps: Water pumps are used for increasing water pressure in the supply system or for circulation in heating or cooling systems.
– Valves: Valves control the flow and pressure of water and other fluids within the plumbing system.
4. Fire Protection Components: Fire protection systems in MEP include components such as:
– Fire Alarm Systems: Smoke detectors, heat detectors, and alarm panels provide early warning in case of a fire.
– Fire Sprinklers: Sprinkler heads disperse water when activated by heat, suppressing fires and preventing their spread.
– Fire Extinguishers: Portable devices that contain extinguishing agents, such as water, foam, or dry chemicals, for immediate use in case of a fire.
5. Renewable Energy Components: With the growing emphasis on sustainability, MEP systems may incorporate components for renewable energy generation, including:
– Solar Panels: Photovoltaic cells convert sunlight into electricity, providing clean and renewable energy for the building.
– Wind Turbines: Generate electricity from wind energy and can be integrated into the building’s power supply system.
– Geothermal Systems: Utilize the Earth’s natural heat to provide heating and cooling for the building.
These are just a few examples of the many components involved in MEP systems. MEP professionals carefully select and integrate these components to create efficient and functional systems that meet the specific needs of each construction project.
In the next section, we will explore the integration of MEP systems with structural and architectural elements in a building.
When working with MEP (mechanical, electrical, and plumbing) systems in construction, it’s important to coordinate closely with all trades to ensure proper installation and functionality. Effective communication and collaboration are key to successful MEP integration.
Read more: What Is Pre-Construction In Construction
Integration of MEP Systems with Structural and Architectural Elements
In any construction project, the integration of MEP (Mechanical, Electrical, and Plumbing) systems with structural and architectural elements is essential for the successful operation and functionality of the building. Let’s take a closer look at how MEP systems are integrated with these elements:
Integration with Structural Elements:
MEP systems are designed to seamlessly integrate with the structural elements of a building. This integration involves coordinating the design and installation of various MEP components with the structural framework. Some key aspects of integration include:
1. Space Planning: MEP professionals work closely with architects and structural engineers to allocate space within the building for MEP systems. This ensures that sufficient space is available for equipment, ductwork, pipes, and other MEP components. Additionally, space planning considers accessibility for maintenance and repairs.
2. Load-bearing Considerations: MEP systems must be designed and installed in a way that minimizes the impact on structural load-bearing elements. Proper coordination and consultation between MEP professionals and structural engineers are crucial to ensure that the weight and forces exerted by MEP systems do not compromise the structural integrity of the building.
3. Penetrations and Openings: MEP systems often require penetrations through structural elements such as walls and floors for the passage of pipes, ducts, and wiring. These penetrations must be carefully coordinated and sealed to maintain the integrity of the building envelope and prevent water or air leakage.
Integration with Architectural Elements:
MEP systems also need to blend seamlessly with the architectural elements of a building. This integration involves careful coordination between MEP professionals and architects to ensure a harmonious and aesthetically pleasing design. Some important considerations for integration with architectural elements include:
1. Lighting Design: MEP professionals work closely with lighting designers and architects to ensure that lighting fixtures are strategically placed to enhance the architectural features of the building. They also consider factors like natural light, daylighting strategies, and energy efficiency in the overall lighting design.
2. Ductwork and Distribution: Ductwork, for HVAC systems, and other distribution components like wiring and plumbing pipes must be designed to blend into the architectural design while maintaining functionality and efficiency. These components can be concealed within ceiling spaces, false ceilings, or behind architectural features to maintain a clean and unobstructed aesthetic appearance.
3. Fixtures and Outlets: MEP professionals collaborate with architects to ensure that plumbing fixtures, electrical outlets, and other service points are strategically placed and aesthetically aligned with the overall design of the space. This involves carefully considering the layout, finishes, and materials used for these components so that they seamlessly integrate with the architectural concept.
The integration of MEP systems with structural and architectural elements involves close collaboration and coordination between MEP professionals, architects, and structural engineers. It ensures that the MEP systems are not only functional and efficient but also enhance the overall design and functionality of the building.
In the next section, we will discuss the importance of MEP coordination in construction projects.
Importance of MEP Coordination in Construction Projects
Coordination is paramount in ensuring the successful implementation of MEP (Mechanical, Electrical, and Plumbing) systems in construction projects. Effective coordination between the different stakeholders involved, including MEP professionals, architects, structural engineers, and contractors, is crucial for several reasons:
1. Avoidance of Conflicts and Clashes: MEP systems comprise a complex network of components that must coexist harmoniously with each other and with other structural and architectural elements of the building. Proper coordination helps identify and resolve conflicts or clashes in advance, preventing costly and time-consuming rework during construction. For example, coordination ensures that ductwork does not interfere with structural beams, electrical conduits are not obstructed by beams or walls, and plumbing lines do not interfere with other MEP systems.
2. Optimal Space Planning: MEP coordination ensures efficient utilization of space within the building. Collaboration between MEP professionals and architects allows for proper allocation of space for MEP system equipment, distribution networks, and service access points. This results in well-designed spaces that maximize functionality while maintaining aesthetic appeal.
3. Enhanced Energy Efficiency: Effective coordination between MEP professionals and other stakeholders facilitates the integration of energy-efficient strategies into the project design. For example, coordination between HVAC designers and architects can optimize the building envelope, ensuring proper insulation and minimizing energy loss. Coordinated lighting design can maximize natural lighting and reduce reliance on artificial lighting, improving energy efficiency. Integrating sustainable practices into MEP systems through coordination leads to reduced energy consumption and lower operational costs for the building.
4. Clarity in Design Intent: Through coordination, the design intent of the MEP systems can be effectively communicated and understood by all stakeholders. MEP professionals can collaborate with architects and structural engineers to ensure that the design intent aligns with project requirements and objectives. This clarity in design minimizes the potential for miscommunication, errors, and misunderstandings during construction, saving time and resources.
5. Seamless Integration of Systems: MEP systems rely on integration and coordination to function optimally. Mechanical, electrical, and plumbing components need to be properly integrated and interconnected to ensure the smooth operation of the building. Coordination enables the seamless integration of these systems, ensuring that they operate efficiently and effectively without compromising the structural integrity or architectural vision of the building.
6. Compliance with Regulations and Standards: Coordinated MEP design and installation ensure compliance with building codes, regulations, and industry standards. MEP professionals stay updated on the latest codes and regulations and work closely with other stakeholders to ensure that the MEP systems meet all requirements regarding safety, electrical and plumbing standards, energy efficiency, and sustainability.
MEP coordination is an ongoing process that starts from the initial design phase and continues throughout the construction and maintenance stages of the project. Regular meetings, collaboration, and communication between stakeholders are crucial for successful MEP coordination.
In the next section, we will explore the challenges faced by MEP professionals in the execution of construction projects.
Challenges Faced by MEP Professionals
MEP (Mechanical, Electrical, and Plumbing) professionals play a critical role in the successful implementation of MEP systems in construction projects. However, they often encounter several challenges that require careful navigation and problem-solving skills. Let’s explore some of the common challenges faced by MEP professionals:
1. Coordination and Communication: Coordinating the various disciplines involved in a construction project is a significant challenge for MEP professionals. Collaboration between MEP professionals, architects, structural engineers, and contractors is essential to ensure effective coordination. Communicating design intent, resolving conflicts, and addressing issues in a timely manner require clear and consistent communication among all parties involved.
2. Space Constraints: Limited space within a building can pose challenges for MEP professionals. Designing and installing MEP systems in tight spaces can be complex, requiring careful planning and optimization of components. Space constraints can also impact the maintenance, access, and future expansion of MEP systems, requiring innovative solutions to overcome the limitations.
3. Rapidly Advancing Technology: The field of MEP systems is constantly evolving, with new technologies and innovations emerging regularly. Keeping up with the latest advancements and incorporating them into projects can be challenging for MEP professionals. Staying updated with changing codes, standards, and best practices is crucial to deliver efficient and sustainable MEP systems.
4. Cost Management: Balancing the functionality, efficiency, and cost-effectiveness of MEP systems can be a challenge. MEP professionals must carefully consider the financial implications of design choices, equipment selection, maintenance requirements, and energy consumption. Finding cost-effective solutions that meet project goals without compromising performance is a constant challenge in MEP projects.
5. Contractor Selection and Management: MEP professionals often face challenges in selecting and managing contractors during the construction phase. Ensuring that contractors have the requisite expertise, experience, and resources to carry out the installation of MEP systems requires careful evaluation and monitoring. Effective contractor management is critical for maintaining quality, adhering to project schedules, and resolving any issues that arise during installation.
6. Sustainability and Energy Efficiency: As sustainability and energy efficiency become increasingly important in construction, MEP professionals face the challenge of integrating green practices into MEP systems. This includes incorporating renewable energy sources, implementing energy-efficient equipment and controls, and optimizing system designs for reduced energy consumption. Balancing sustainability goals with budgetary constraints and client expectations can be a complex challenge for MEP professionals.
7. Ongoing Maintenance and Operation: The responsibility of MEP professionals extends beyond the construction phase to the maintenance and operation of MEP systems. Ensuring the longevity and efficiency of MEP systems through regular inspections, maintenance, and upgrades presents ongoing challenges. Adapting to evolving industry standards and identifying potential issues before they become major problems require proactive maintenance strategies.
Despite these challenges, MEP professionals bring their expertise, problem-solving skills, and industry knowledge to overcome obstacles and deliver successful MEP systems in construction projects. With effective coordination, communication, and a forward-thinking approach, these challenges can be managed to achieve the desired outcomes.
In the next section, we will explore the latest innovations and technologies in MEP construction.
Latest Innovations and Technologies in MEP Construction
The field of MEP (Mechanical, Electrical, and Plumbing) construction is constantly evolving, with new innovations and technologies emerging to improve the efficiency, sustainability, and performance of MEP systems. Let’s explore some of the latest advancements in MEP construction:
1. Building Information Modeling (BIM): BIM technology has revolutionized the design and coordination process in MEP construction. BIM enables the creation of a virtual 3D model that integrates MEP systems with architectural and structural components. This collaborative platform allows stakeholders to visualize, coordinate, and analyze MEP systems before construction, reducing conflicts, improving coordination, and optimizing system performance.
2. Prefabrication and Modular Construction: Prefabrication and modular construction methods are gaining popularity in MEP construction projects. Prefabrication involves the off-site manufacturing of MEP components, such as ductwork, piping, and electrical panels, which are then delivered to the construction site for assembly. This approach reduces construction time, improves quality control, and enhances efficiency in installation.
3. Energy-efficient HVAC Systems: HVAC systems are continuously evolving to improve energy efficiency and reduce environmental impact. Variable Refrigerant Flow (VRF) systems, for example, provide precise zone control and energy-efficient operation. Additionally, the use of geothermal heat pumps, heat recovery ventilation systems, and advanced controls enables optimized energy consumption and improved indoor air quality.
4. Smart Building Automation: The advent of smart building automation technology has transformed the way MEP systems are controlled and managed. Integrated building management systems (BMS) allow for centralized control and monitoring of MEP systems. Sensors, data analytics, and machine learning algorithms enable real-time monitoring, predictive maintenance, and energy optimization for improved performance and energy efficiency.
5. LED Lighting Technology: Light Emitting Diode (LED) lighting technology has revolutionized the lighting industry, providing energy-efficient and longer-lasting lighting solutions. LED lights offer significant energy savings compared to traditional lighting systems and provide more design flexibility. Moreover, advancements in LED technology have led to dynamic lighting control systems that allow for personalized lighting experiences and enhanced occupant comfort.
6. Renewable Energy Integration: The integration of renewable energy sources in MEP systems is gaining momentum. Solar photovoltaic (PV) systems, wind turbines, and geothermal heat pumps are being incorporated into buildings to generate clean and sustainable energy. These systems help reduce carbon emissions, lower energy costs, and increase overall energy independence.
7. Water Conservation Solutions: Water conservation is a growing concern, leading to innovations in MEP systems to reduce water consumption. Intelligent irrigation systems with sensors and controllers optimize water usage for landscaping. Low-flow fixtures and water recycling systems contribute to significant water savings and sustainable water management.
8. Indoor Air Quality Enhancement: Enhanced indoor air quality has gained attention, especially in light of the COVID-19 pandemic. MEP systems now focus on technologies such as air purification, ultraviolet germicidal irradiation, and advanced filtration systems to improve air quality and protect occupants from airborne contaminants and pathogens.
These are just a few examples of the latest innovations and technologies transforming the MEP construction industry. Adaptation of these advancements in MEP systems improves efficiency, sustainability, occupant comfort, and overall building performance.
In the final section, we will conclude our exploration of MEP systems in construction.
Read more: What Is Construction
Conclusion
In the realm of construction, MEP (Mechanical, Electrical, and Plumbing) systems play a crucial role in ensuring the functionality, comfort, and safety of buildings. MEP professionals, with their expertise and knowledge, are responsible for designing, coordinating, and implementing these systems to meet the specific requirements of each construction project.
From heating, ventilation, and air conditioning (HVAC) systems to electrical distribution and plumbing services, MEP systems provide essential functions that contribute to the overall efficiency and sustainability of a building. Proper integration of MEP systems with structural and architectural elements is essential to ensure seamless operation and performance.
MEP professionals face various challenges during the design, installation, and maintenance of MEP systems. Coordination and communication among stakeholders, effective space planning, consideration of rapidly advancing technologies, and sustainable design practices are crucial for overcoming these challenges.
The field of MEP construction is constantly evolving, with innovations and technologies shaping the future of building systems. Building Information Modeling (BIM), prefabrication, energy-efficient HVAC systems, smart building automation, LED lighting technology, renewable energy integration, water conservation solutions, and advancements in indoor air quality are just a few examples of the latest developments revolutionizing the MEP industry.
In conclusion, a well-designed and coordinated MEP system ensures the efficient operation, comfort, and sustainability of a building. MEP professionals, with their expertise in mechanical, electrical, and plumbing systems, are instrumental in delivering successful construction projects. By embracing the latest innovations and technologies, MEP professionals will continue to enhance building performance, energy efficiency, and occupant well-being.
As construction practices evolve and technology advances, the importance of MEP systems will only grow. The continuous collaboration and coordination between MEP professionals and other stakeholders will pave the way for innovative and sustainable solutions in the construction industry.
Frequently Asked Questions about What Is An MEP In Construction
Was this page helpful?
At Storables.com, we guarantee accurate and reliable information. Our content, validated by Expert Board Contributors, is crafted following stringent Editorial Policies. We're committed to providing you with well-researched, expert-backed insights for all your informational needs.
0 thoughts on “What Is An MEP In Construction”