Home>diy>Building & Construction>What Is Prefabricated Construction
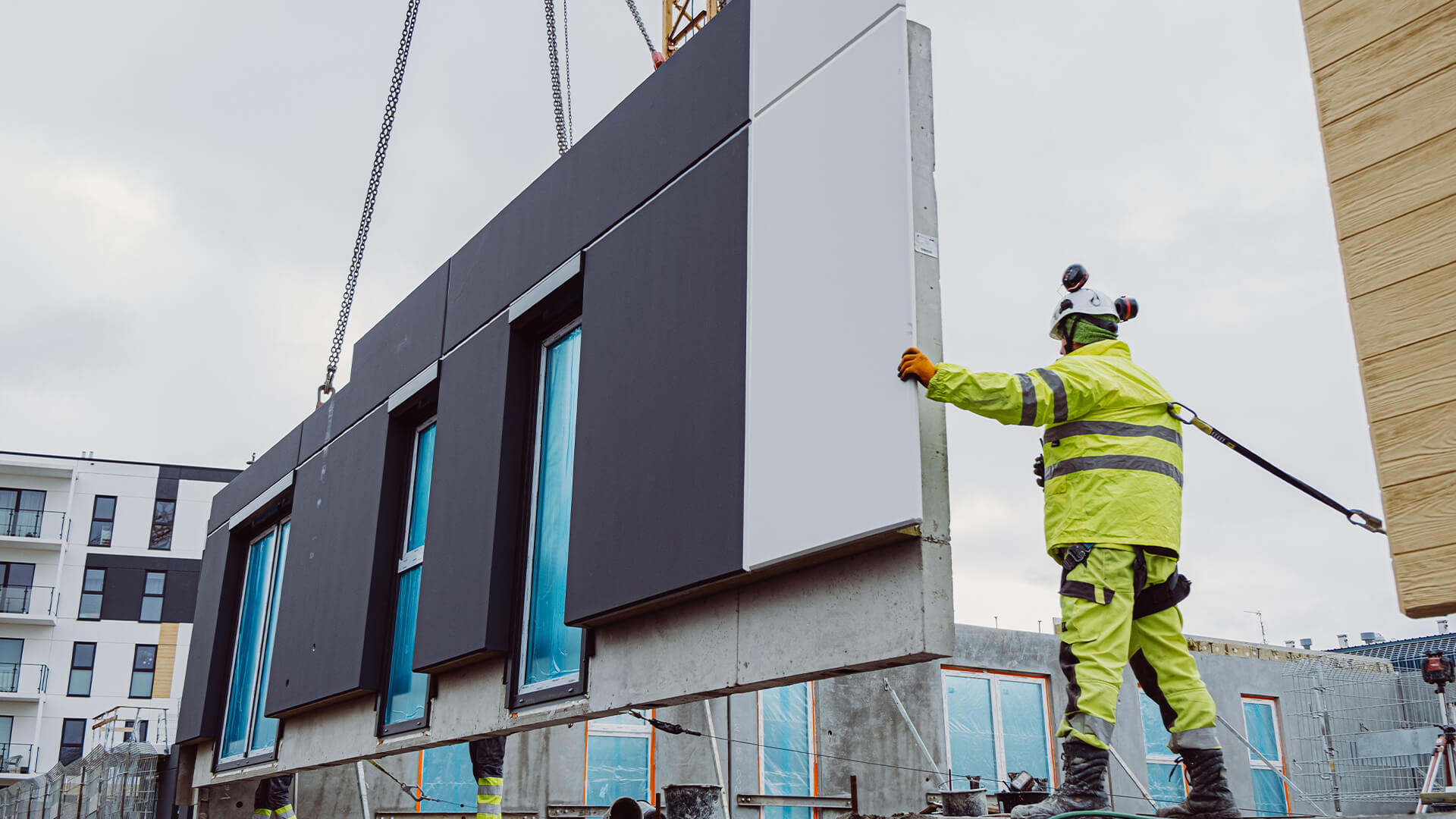
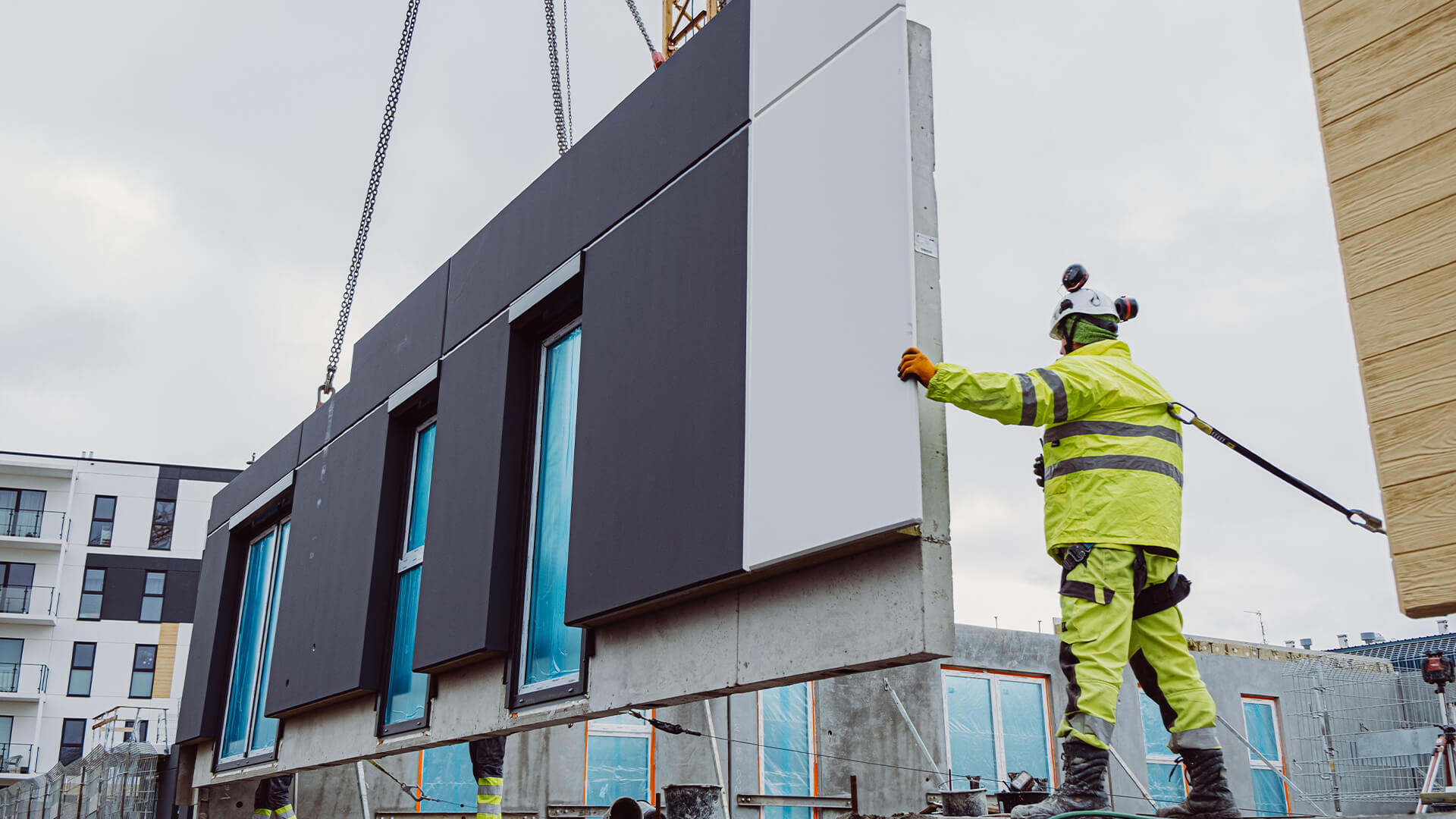
Building & Construction
What Is Prefabricated Construction
Modified: December 7, 2023
Discover the benefits and process of prefabricated construction in the building industry. Enhance efficiency and reduce construction time with this innovative method.
(Many of the links in this article redirect to a specific reviewed product. Your purchase of these products through affiliate links helps to generate commission for Storables.com, at no extra cost. Learn more)
Introduction
Prefabricated construction, also known as modular construction or offsite construction, is a method in which building components are manufactured offsite in a controlled environment and then transported to the construction site for assembly. This method differs from traditional construction, where materials are brought to the site and assembled on-site. Prefabricated construction has gained significant popularity in recent years due to its numerous advantages, including increased efficiency, cost savings, and reduced construction time.
With prefabricated construction, the building components are fabricated in factories using advanced technology and precise measurements. This allows for greater accuracy and quality control, as the controlled environment minimizes the possibility of errors or inconsistencies. Once the components are completed, they are transported to the construction site, where skilled workers assemble them to form the final structure.
One of the key advantages of prefabricated construction is the significant reduction in construction time. Since the building components are fabricated simultaneously in the factory, construction activities can already commence on-site. This parallel process of manufacturing and on-site assembly can result in a substantial time-saving, as compared to traditional construction methods.
Prefabricated construction also offers greater cost savings. The controlled environment of the factory allows for efficient use of materials, minimizing wastage. Additionally, the streamlined production process and reduced construction time contribute to lower labor costs. The scale and repeatability of prefabrication also enable bulk purchasing of materials, resulting in cost efficiencies.
Furthermore, prefabricated construction is known for its increased efficiency and enhanced sustainability. The controlled environment in the factory enables better monitoring of energy consumption and waste management. Additionally, since construction activities on-site are limited to assembling the prefabricated components, there is less noise, dust, and disruption to the surrounding environment. This makes prefabricated construction an attractive option for projects in densely populated or sensitive areas.
Despite the numerous advantages of prefabricated construction, there are also some challenges to consider. One of the main concerns is the limited design flexibility. Since the building components are manufactured offsite, changes to the design once fabrication has started can be complex and costly. Therefore, careful planning and coordination are essential during the design stage to ensure that the final structure meets the specifications and requirements.
In the following sections, we will delve deeper into the definition of prefabricated construction, explore its different types, discuss the process involved, highlight the key players in the industry, and examine its sustainability aspects. We will also look into future trends and innovations that are shaping the future of prefabricated construction. Whether you are a construction professional or simply interested in the field, this comprehensive guide will provide you with valuable insights into the world of prefabricated construction and its impact on the building industry.
Key Takeaways:
- Prefabricated construction offers increased efficiency, cost savings, and sustainability benefits. With advanced manufacturing techniques and design flexibility, it revolutionizes the building industry, shaping the future of construction practices.
- Despite design limitations and transportation challenges, prefabricated construction’s future trends and innovations, such as smart building technologies and sustainable materials, drive its evolution towards a more efficient, sustainable, and adaptable construction method.
Read more: What Is A Prefabricated Fireplace
Definition of Prefabricated Construction
Prefabricated construction, also known as modular construction or offsite construction, refers to a method of building where components or modules are manufactured in a controlled environment away from the construction site. These components are then transported to the site and assembled to create the final structure. Unlike traditional construction methods, where building components are fabricated and assembled on-site, prefabricated construction involves the use of pre-engineered units that are manufactured to precise specifications.
In prefabricated construction, the building components are fabricated in a factory using specialized equipment and machinery. This controlled environment allows for greater efficiency, quality control, and consistency in the manufacturing process. The components are typically made from materials such as steel, concrete, wood, or a combination of these, depending on the desired design and requirements of the project.
The prefabricated building components can range from basic elements like wall panels, floor slabs, and roof trusses to more complex modules containing complete rooms or functional units. These components are designed and manufactured to fit together seamlessly, ensuring a precise and efficient assembly process on-site.
One of the defining characteristics of prefabricated construction is its modular nature. The building components are produced as individual modules that can be easily transported and assembled. These modules can be standardized and repeated, allowing for efficient mass production and cost savings. They can also be customized to meet specific design requirements, allowing for flexibility in architectural expression.
Prefabricated construction offers several benefits over traditional construction methods. Firstly, the controlled factory environment ensures better quality control as the components are manufactured under strict supervision and adherence to standardized processes. This results in higher accuracy, consistency, and durability of the building elements.
Secondly, the prefabrication process can significantly reduce construction time. While the components are being manufactured offsite, site preparation work can be concurrently carried out. This parallel workflow can lead to faster project completion and reduced labor costs.
Additionally, prefabricated construction is often considered more sustainable compared to traditional construction methods. The controlled manufacturing environment allows for better waste management, recycling of materials, and optimization of energy usage. The reduced on-site construction activities also minimize environmental disturbances and disruptions to the surrounding area.
It is important to note that prefabricated construction is not limited to specific building types or sizes. It can be applied to various sectors such as residential, commercial, industrial, and institutional projects. From single-family homes and multi-story office buildings to hospitals and educational facilities, prefabricated construction offers a versatile and efficient solution.
In the next sections, we will explore the advantages and disadvantages of prefabricated construction, delve into the different types of prefabrication, and discuss the site preparation and construction process involved in this innovative building method.
Advantages of Prefabricated Construction
Prefabricated construction, also known as modular or offsite construction, offers numerous advantages over traditional construction methods. These advantages have contributed to the increasing popularity of prefabrication in the building industry. Let’s explore some of the key benefits:
- Increased Efficiency: Prefabrication allows for efficient and streamlined construction processes. Since the building components are manufactured offsite in a controlled environment, the production can be optimized for maximum efficiency. The use of advanced technology, such as computer-aided design (CAD) and automated machinery, ensures accurate and precise construction. This efficiency translates into better time management, reduced labor costs, and improved overall project performance.
- Cost Savings: Prefabricated construction offers significant cost savings compared to traditional construction methods. The factory-controlled environment allows for efficient use of materials, minimizing wastage. Bulk purchasing of materials for multiple projects can also lead to cost efficiencies. Additionally, the shortened construction time of prefabricated buildings reduces labor costs and overhead expenses associated with on-site construction activities.
- Faster Construction: One of the most notable advantages of prefabricated construction is the accelerated building process. Since the building components are fabricated simultaneously offsite, construction activities can commence on-site as soon as the foundation is ready. This parallel construction process can significantly reduce the overall project timeline, allowing for earlier occupancy or utilization of the built space.
- Quality Control: Prefabricated construction relies on standardized processes and strict quality control measures. The controlled and monitored factory environment ensures that the building components are fabricated to high standards of quality and precision. This results in better consistency, accuracy, and durability of the final structure. The use of modern manufacturing techniques and skilled labor further enhances the quality of prefabricated buildings.
- Flexibility and Customization: Contrary to common misconceptions, prefabricated construction offers a high degree of design flexibility and customization. While certain components may follow standardized modules, they can be easily adapted and customized to meet specific design requirements. This allows for architectural creativity and the ability to achieve unique and aesthetically appealing building designs.
- Sustainability: Prefabricated construction aligns well with sustainability principles. The controlled factory environment allows for better waste management, recycling, and responsible use of resources. The optimization of energy usage, reduction of material wastage, and potential for incorporating sustainable materials make prefabricated buildings an eco-friendly choice. Additionally, the reduced on-site construction activities minimize noise, air pollution, and disturbance to the surrounding environment, making it an environmentally conscious building method.
It is important to note that the advantages of prefabricated construction can vary depending on the specific project and its unique requirements. Proper planning, coordination, and communication between all stakeholders are essential to fully leverage the benefits offered by prefabrication. As the construction industry continues to evolve, prefabricated construction is likely to play an increasingly significant role, bringing innovation, efficiency, and sustainability to the forefront of modern building practices.
Disadvantages of Prefabricated Construction
While prefabricated construction offers numerous advantages, it is important to consider the potential disadvantages that may arise when implementing this building method. Here are some of the key challenges associated with prefabricated construction:
- Design Limitations: One of the main drawbacks of prefabricated construction is the limited design flexibility compared to traditional construction methods. The building components are manufactured offsite according to predetermined specifications, which may restrict the ability to make significant changes to the design during the construction process. Any design alterations or customization requests made after the fabrication has begun can be complex and costly, requiring careful coordination and potentially extending the overall project timeline.
- Transportation and Site Constraints: Prefabricated building components need to be transported from the manufacturing facility to the construction site. This transport can present logistical challenges, especially for large or complex modules. Access to the construction site may need to be carefully planned, taking into account the dimensions and weight of the prefabricated elements. Additionally, site conditions, such as limited space or restricted access, may impact the transportation and assembly of these components.
- High Initial Investment: Prefabricated construction may require a higher initial investment compared to traditional construction methods. The setup and establishment of a factory or manufacturing facility, along with the necessary specialized equipment and workforce, can involve significant upfront costs. However, it is important to note that these costs can be offset over time through the benefits of reduced labor expenses, improved time management, and potential cost savings in materials.
- Dependence on Skilled Labor: Prefabricated construction relies heavily on skilled labor for the manufacturing and assembly processes. Companies involved in prefabrication need to ensure that there is an adequate supply of skilled workers trained in the specific techniques and processes required for prefabrication. Limited availability of skilled labor can pose a challenge and may require additional training or recruitment efforts to meet the demands of prefabricated construction projects.
- Transport and Handling Risks: During transportation and on-site assembly, there is a risk of damage to the prefabricated components. Although the components are designed with durability in mind, incidents such as accidents or mishandling can result in structural damage or cosmetic defects. Proper handling, packaging, and transportation methods must be in place to minimize the risk of damage and ensure the structural integrity of the prefabricated elements.
- Permitting and Regulatory Considerations: Prefabricated construction projects may require additional permitting and regulatory considerations, depending on local building codes and regulations. Authorities may have specific requirements for the fabrication, transportation, and installation of prefabricated components. It is important to ensure compliance with all applicable regulations to avoid delays or complications during the construction process.
Despite these disadvantages, prefabricated construction continues to gain popularity due to its overall efficiency, cost-effectiveness, and sustainability benefits. Careful planning, collaboration, and coordination among all stakeholders are crucial to mitigate these challenges and fully leverage the advantages offered by prefabricated construction.
Types of Prefabricated Construction
Prefabricated construction encompasses various methodologies and techniques, each catering to different project requirements and design goals. Here are some common types of prefabricated construction:
- Panelized Construction: Panelized construction involves the fabrication of wall panels, floor panels, and roof panels in a factory-controlled environment. These panels are then transported to the construction site and assembled to form the structure. Panelized construction offers flexibility in design and can be easily customized to meet specific project requirements. It is a popular choice for residential and small to medium-sized commercial buildings.
- Modular Construction: Modular construction involves the fabrication of entire modules or units in a factory. These modules are self-contained and can include complete rooms or functional components such as bathrooms or kitchenettes. Modules are typically built with all the interior finishes, electrical and plumbing systems, fixtures, and fittings in place. Once manufactured, these modules are transported to the site and assembled to create the final structure. Modular construction is known for its versatility and faster installation time.
- Steel Framing: Steel framing is a popular choice for prefabricated construction due to its strength, durability, and sustainability. Steel components, such as beams, columns, and trusses, are fabricated offsite and then transported to the construction site for assembly. Steel framing offers excellent structural integrity and allows for clear spans and flexible interior layouts. It is commonly used in commercial, industrial, and institutional buildings.
- Bathroom Pods: Bathroom pods are fully finished and integrated bathroom units that are manufactured offsite. These modules include all the necessary fixtures, fittings, plumbing, and electrical systems. Bathroom pods offer the advantage of improved quality control as they are manufactured in a controlled environment, reducing the risk of on-site construction errors. They are commonly used in hotels, student accommodations, and healthcare facilities.
- Hybrid Systems: Hybrid prefabricated construction combines different types and methods of prefabrication to meet specific project requirements. This approach allows for a combination of panelized or modular construction with traditional on-site construction methods. Hybrid systems offer flexibility in design and construction, enabling the integration of various building components for a customized solution. They are often used in complex and larger-scale projects where both speed and design flexibility are important.
It is important to note that the choice of prefabricated construction method depends on several factors, including project size, design requirements, budget, and local regulations. Collaboration between architects, engineers, and contractors is essential during the planning and design phase to determine the most suitable prefabrication method for a given project.
Each type of prefabricated construction offers its own advantages and considerations. Regardless of the chosen method, careful coordination and communication with the prefabrication manufacturer, as well as efficient logistics planning, are crucial to ensure a seamless and successful construction process.
Read more: What Is Construction
Preparing the Site for Prefabricated Construction
Before the prefabricated components can be delivered and assembled on-site, adequate preparation of the construction site is essential. Proper site preparation ensures a smooth and efficient construction process for prefabricated construction projects. Here are some key steps involved in preparing the site:
- Site Clearance: The first step is to clear the site of any existing structures, debris, vegetation, or obstacles that may hinder the assembly and installation of the prefabricated components. This includes demolition and removal of any existing buildings or structures, as well as clearing the site of vegetation and leveling the ground if necessary.
- Foundation and Utilities: Once the site is cleared, the next step is to prepare the foundation and utilities. The type of foundation will depend on the specific project requirements and the recommendations of the structural engineer. Common foundation types for prefabricated construction include concrete slabs, strip footings, or piles. Utility connections, such as electrical, water, and sewerage, need to be planned and implemented at this stage.
- Access Roads and Crane Pads: Access roads need to be constructed to allow the transportation of the prefabricated components to the site. These roads should be able to accommodate the size and weight of the transportation vehicles. Additionally, crane pads need to be prepared to provide a stable and level surface for the cranes that will be used during the assembly of the prefabricated components.
- Temporary Facilities: Temporary facilities may be required to support the construction process. This can include on-site offices, storage areas for the prefabricated components, and facilities for workers such as toilets and rest areas. These temporary facilities need to be strategically placed to optimize workflow and ensure efficient operations during the construction process.
- Coordination with Transportation and Logistics: As prefabricated construction involves the transportation of large and heavy components, coordination with transportation and logistics companies is crucial. Plans for the delivery and storage of the prefabricated components on-site need to be made in advance to ensure seamless coordination. The availability of cranes or other heavy lifting equipment should also be coordinated to facilitate the smooth installation of the prefabricated components.
- Permits and Approvals: Before commencing site preparation, it is essential to obtain all necessary permits and approvals from local authorities. This includes building permits, environmental permits, and any other regulatory requirements specific to the project and the area. Compliance with these regulations is crucial to avoid delays or complications during the construction process.
Proper site preparation for prefabricated construction projects sets the stage for a successful construction process. The coordination and collaboration between the design team, construction team, and site preparation contractors are essential to ensure that the site is adequately prepared and ready to receive the prefabricated components. By carefully planning and executing the site preparation, the construction process can be streamlined, leading to faster project completion and successful assembly of the prefabricated components.
When considering prefabricated construction, be sure to carefully review the quality and durability of the materials used, as well as the reputation of the manufacturer. This will help ensure the long-term success of your project.
The Process of Prefabricated Construction
The process of prefabricated construction involves several stages, from design and manufacturing to on-site assembly and finishing. Let’s explore the key steps involved in the process:
- Design and Engineering: The process begins with the design and engineering phase. Architects work closely with structural engineers and other design professionals to develop the project’s architectural plans and specifications. During this phase, the design team considers the use of prefabricated components and structures, ensuring that the design is compatible with the prefabrication process.
- Material Procurement: Once the design is finalized, the next step is to procure the necessary materials. This includes ordering the required quantity of building components, such as walls, floors, roofs, and utilities, based on the project’s specifications. The materials are typically sourced from reputable suppliers who specialize in prefabrication materials.
- Factory Fabrication: The building components are then fabricated in a controlled factory environment according to the project’s design and specifications. Skilled workers use specialized machinery and equipment to manufacture the components with precision and accuracy. Quality control measures are implemented to ensure that the components meet the required standards.
- Transportation and Logistics: After fabrication, the prefabricated components are carefully loaded onto transportation vehicles for delivery to the construction site. Proper logistics planning is crucial to ensure the components arrive at the site in the correct order and on schedule. Coordination with transportation companies, traffic management, and adherence to safety regulations are essential during this stage.
- On-Site Assembly: Once the prefabricated components arrive at the construction site, the on-site assembly process begins. Skilled workers use cranes or other lifting equipment to position and connect the components as per the project’s design. The components are typically designed for easy and efficient assembly, with connections and joints carefully designed to ensure stability and structural integrity.
- Finishing and Services Installation: After the main structure is assembled, the finishing and services installation work begins. This includes the installation of interior finishes, such as flooring, wall cladding, and ceilings. Electrical and plumbing systems, as well as HVAC (Heating, Ventilation, and Air Conditioning) systems, are also installed during this stage. The goal is to achieve a fully functional and aesthetically pleasing space.
- Testing and Inspections: Once the construction is complete, thorough testing and inspections are carried out to ensure that all systems are functioning correctly and the structure is safe for occupancy. This includes checks on the electrical, plumbing, and HVAC systems, as well as structural inspections to verify the integrity of the prefabricated components. Any necessary adjustments or corrections are made during this phase.
- Final Touches and Handover: After successful testing and inspections, the final touches are applied to the project. This includes cleaning the site, landscaping, and any additional exterior finishes. Once all the work is completed, the project is handed over to the client or end-user for occupancy or utilization.
The process of prefabricated construction offers numerous advantages, including increased efficiency, reduced construction time, cost savings, and improved quality control. Collaboration and communication between the design team, fabricators, and construction team are essential throughout the process to ensure a smooth and successful execution of the prefabricated construction project.
Key Players in the Prefabricated Construction Industry
The prefabricated construction industry involves several key players who contribute to the design, manufacturing, and implementation of prefabricated building components and structures. These players play a crucial role in the success and growth of the industry. Let’s explore some of the key players:
- Architects and Designers: Architects and designers are responsible for creating the initial concept and design of the prefabricated construction project. They collaborate with the clients to understand their requirements and develop innovative and functional designs that can be translated into prefabricated components. Their expertise in design, materials, and construction techniques is essential in ensuring that the final structure meets the desired aesthetic and functional goals.
- Prefabrication Manufacturers: Prefabrication manufacturers are the entities that fabricate and produce the prefabricated building components. These manufacturers typically operate in controlled factory environments equipped with specialized machinery and skilled workers. They utilize advanced manufacturing techniques to ensure precision and high-quality production of the components. Prefabrication manufacturers work closely with architects, engineers, and contractors to ensure that the components meet the project specifications and requirements.
- Contractors: Contractors play a vital role in the prefabricated construction industry, especially during the on-site assembly and installation of the prefabricated components. They oversee the construction process, manage the logistics, and coordinate with various stakeholders, including architects, manufacturers, and subcontractors. Contractors are responsible for ensuring a smooth and efficient construction process, adhering to safety standards, and maintaining communication among all parties involved.
- Structural Engineers: Structural engineers are crucial in the prefabricated construction industry, as they are responsible for ensuring the structural integrity and safety of the prefabricated components and the overall structure. They work closely with architects and manufacturers to design the components and connections that meet the required structural standards. Structural engineers conduct thorough analysis and calculations to ensure that the prefabricated components can withstand the intended loads and forces.
- Material Suppliers: Material suppliers play a key role in the prefabricated construction industry by providing the necessary raw materials for the manufacturing of the prefabricated components. These suppliers specialize in providing high-quality and reliable materials such as steel, concrete, wood, insulation, and finishes. The quality of the materials used in prefabrication is crucial to ensure the durability and longevity of the final structure.
- Logistics and Transportation Companies: Transportation and logistics companies play a critical role in transporting the prefabricated components from the manufacturing facility to the construction site. They handle the coordination, scheduling, and safe delivery of the components, ensuring that they arrive on-site in a timely manner. Logistics companies also play a role in managing the storage and inventory of prefabricated components during the construction process.
These key players in the prefabricated construction industry work collaboratively to bring projects to fruition. Their expertise, knowledge, and dedication contribute to the successful implementation of prefabricated construction methods, resulting in efficient, cost-effective, and high-quality buildings. As the industry continues to evolve, these players will play an increasingly important role in shaping the future of prefabricated construction.
Sustainability and Prefabricated Construction
Prefabricated construction offers several sustainability benefits, making it an increasingly popular choice for environmentally conscious building projects. Here are some ways in which prefabricated construction promotes sustainability:
- Reduced Material Waste: The controlled factory environment in prefabrication allows for efficient use of materials. The precise measurements and accurate manufacturing processes minimize material waste, reducing the overall environmental impact. Additionally, any waste generated during the prefabrication process can be properly managed and recycled, further reducing the ecological footprint.
- Energy Efficiency: Prefabricated buildings often incorporate energy-efficient design principles. The components can be manufactured with insulation and air sealing measures, which improve energy efficiency and reduce the building’s energy consumption. This can lead to lower heating, cooling, and lighting costs, as well as a reduced carbon footprint over the building’s lifecycle.
- Optimized Resource Use: Prefabrication allows for the optimization of resource use. The ability to precisely plan and control the manufacturing process enables efficient utilization of raw materials. Additionally, the repeatability of prefabricated components allows for bulk purchasing of materials, leading to cost savings and reduced resource consumption.
- Reduced Construction Waste: Compared to traditional construction methods, prefabricated construction generates less construction waste on-site. Since most of the building components are manufactured in the factory, there is a substantial reduction in on-site waste, such as packaging materials, excess materials, and debris. This streamlining of the construction process minimizes environmental impact and reduces the need for waste management on-site.
- Improved Indoor Air Quality: Prefabricated construction can contribute to improved indoor air quality. The controlled manufacturing environment allows for better quality control, ensuring that the building components are produced in a clean and controlled setting. The components can be manufactured with low or zero volatile organic compounds (VOC) materials, promoting healthier indoor air quality for occupants.
- Reduced Site Disruption: Prefabricated construction minimizes disruption to the surrounding site and neighboring areas. Since most of the construction activities occur in the factory, on-site disturbances such as noise, dust, and waste are significantly reduced. This makes prefabricated construction a preferred choice for projects located in urban or sensitive areas.
It is important to note that while prefabricated construction offers sustainability benefits, it is essential to consider other factors to maximize its environmental impact. Choices related to transportation logistics, material sourcing, and energy-efficient design should be carefully considered. Adopting renewable energy sources, incorporating green building certifications, and implementing sustainable practices throughout the entire lifecycle of the building can further enhance the sustainability of prefabricated construction projects.
As the construction industry continues to prioritize sustainability, prefabricated construction provides a viable solution that aligns with sustainable development goals. By optimizing resource use, reducing waste, and improving energy efficiency, prefabricated construction contributes to a more sustainable built environment.
Read more: What Is Construction Surveying
Future Trends and Innovations in Prefabricated Construction
Prefabricated construction continues to evolve and innovate, driven by advancements in technology, sustainability goals, and the need for more efficient and cost-effective building methods. Here are some future trends and innovations shaping the prefabricated construction industry:
- Advanced Manufacturing Techniques: The use of advanced manufacturing techniques, such as robotics, 3D printing, and automation, is expected to increase in the prefabricated construction industry. These technologies enable faster and more precise fabrication of components, resulting in enhanced efficiency and quality control. 3D printing, in particular, has the potential to revolutionize the industry by enabling the fabrication of complex and customized components with minimal waste.
- Integrated Building Systems: The integration of building systems within prefabricated components is becoming more prevalent. This includes the incorporation of electrical, mechanical, and plumbing systems directly into the prefabricated elements. This integration streamlines the construction process and improves overall efficiency, as these systems can be installed and tested in the factory before delivery to the construction site.
- Green and Sustainable Materials: The use of sustainable and eco-friendly materials is gaining momentum in prefabricated construction. Manufacturers are exploring alternative materials, such as recycled and bio-based materials, to reduce the environmental impact of building components. Sustainable certification schemes and rating systems are also being developed to evaluate the ecological performance of prefabricated buildings, further driving the adoption of green materials.
- Smart Building Technologies: Prefabricated construction is embracing smart building technologies to enhance functionality and sustainability. Integration of sensors, Internet of Things (IoT) devices, and advanced building management systems allows for monitoring and control of various building parameters, such as energy consumption, indoor air quality, and occupant comfort. These technologies enhance operational efficiency, enable predictive maintenance, and contribute to the overall sustainability of the building.
- BIM and Digital Twins: Building Information Modeling (BIM) is being increasingly used in prefabricated construction projects. BIM facilitates enhanced coordination, visualization, and communication among stakeholders, enabling efficient collaboration and reducing errors during the design and fabrication stages. Additionally, the concept of digital twins, virtual replicas of the physical building, allows for real-time monitoring, performance analysis, and predictive modeling of prefabricated structures.
- Modular Multi-Story Construction: There is a growing trend towards modular multi-story construction, where entire modules containing multiple floors are prefabricated and assembled on-site. This method allows for the efficient construction of high-rise buildings, as the modules can be manufactured concurrently while site preparation work is underway. Modular multi-story construction offers benefits in terms of speed, cost-effectiveness, and reduced disruption to the surrounding area.
These trends and innovations are driving the transformation of the prefabricated construction industry, making it more sustainable, technologically advanced, and adaptable to diverse project requirements. As these methods become more refined and widely adopted, prefabricated construction has the potential to become the construction method of choice for a range of building projects, from residential homes to commercial and institutional structures.
It is important for industry professionals to stay informed, adapt to the evolving technologies, and embrace sustainable practices to fully leverage the benefits of prefabricated construction in the future. By embracing these advancements, the industry can further improve efficiency, reduce costs, and contribute to the creation of sustainable and resilient built environments.
Conclusion
Prefabricated construction, with its numerous advantages and innovative approaches, is revolutionizing the building industry. The efficient manufacturing processes, reduced construction time, cost savings, and increased sustainability make it an attractive choice for a wide range of construction projects. As we have explored in this comprehensive guide, prefabricated construction offers several key benefits:
First, prefabricated construction improves efficiency by streamlining the manufacturing process. Controlled factory environments, advanced technologies, and precise measurements allow for accurate production, reducing errors and delays. This efficiency translates into cost savings and faster project completion, making prefabricated construction a cost-effective solution.
Second, prefabricated construction offers a range of design options and customization possibilities. While there may be some constraints due to modularization, architects and designers can work within these boundaries to create unique and visually appealing structures. Prefabrication also allows for flexibility in architectural expression, ensuring that each project can be tailored to the specific needs and preferences of the client.
Moreover, prefabricated construction promotes sustainability and environmental responsibility. The controlled manufacturing environment enables efficient material usage, reducing waste and minimizing the ecological impact. Additionally, prefabricated components can be manufactured with energy-efficient designs, insulation, and other eco-friendly features, leading to reduced energy consumption and a smaller carbon footprint.
Looking to the future, the prefabricated construction industry is poised for further growth and advancement. Innovations, such as advanced manufacturing techniques, integrated building systems, and smart building technologies, are shaping the industry and driving increased efficiency and sustainability. Embracing these advancements along with green and sustainable materials will further enhance the positive impact of prefabricated construction on the environment and the construction industry as a whole.
As the appeal of prefabricated construction continues to grow, collaboration and engagement among architects, manufacturers, contractors, and other key players are essential. The collective efforts of these stakeholders can drive further innovation, improve construction practices, and expand the implementation of prefabricated construction methods.
In conclusion, prefabricated construction offers a compelling alternative to traditional construction methods. Its efficiency, cost-effectiveness, design flexibility, and sustainability benefits make it a valuable option for a wide range of projects. As the construction industry evolves towards more sustainable and efficient practices, prefabricated construction stands at the forefront of innovation and progress.
Frequently Asked Questions about What Is Prefabricated Construction
Was this page helpful?
At Storables.com, we guarantee accurate and reliable information. Our content, validated by Expert Board Contributors, is crafted following stringent Editorial Policies. We're committed to providing you with well-researched, expert-backed insights for all your informational needs.
0 thoughts on “What Is Prefabricated Construction”