Home>diy>Building & Construction>Which Cement Is Used In Underwater Construction
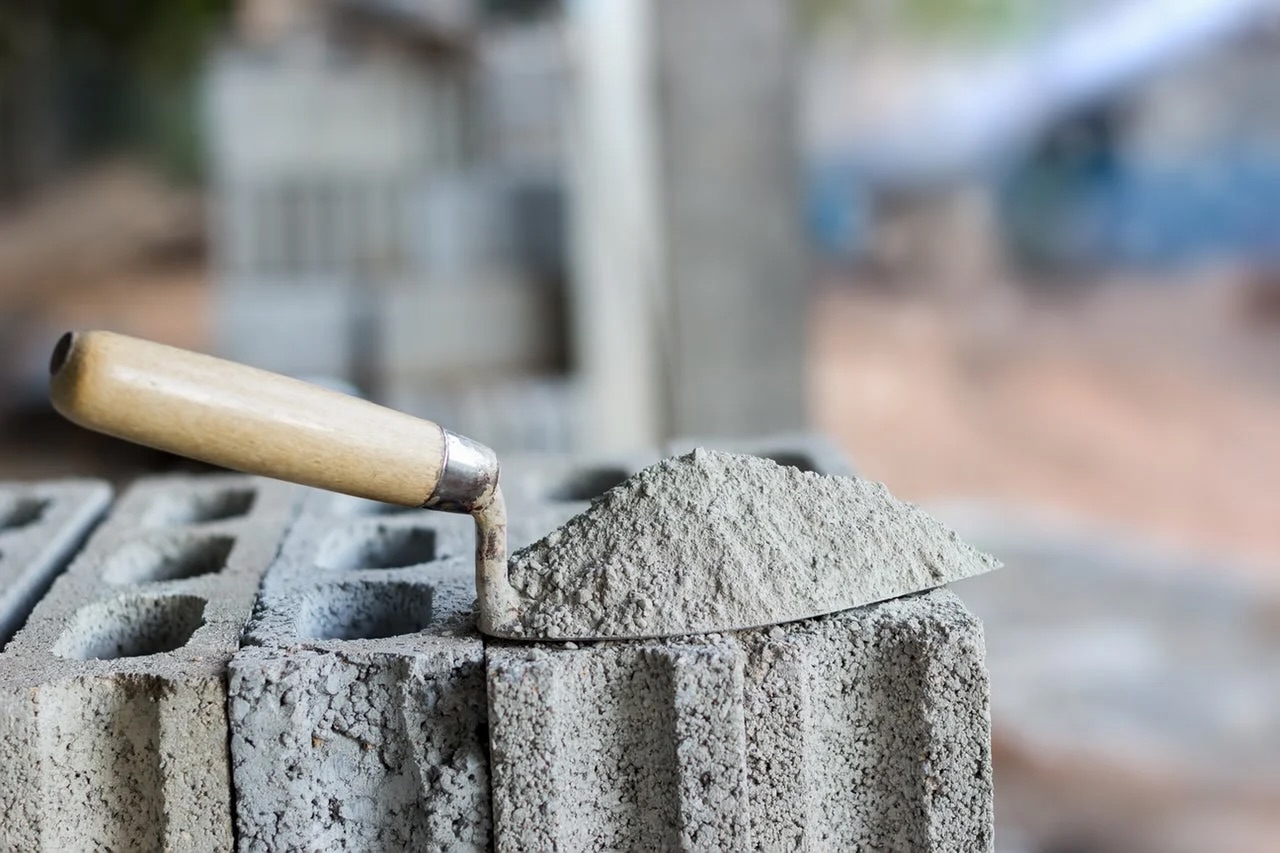
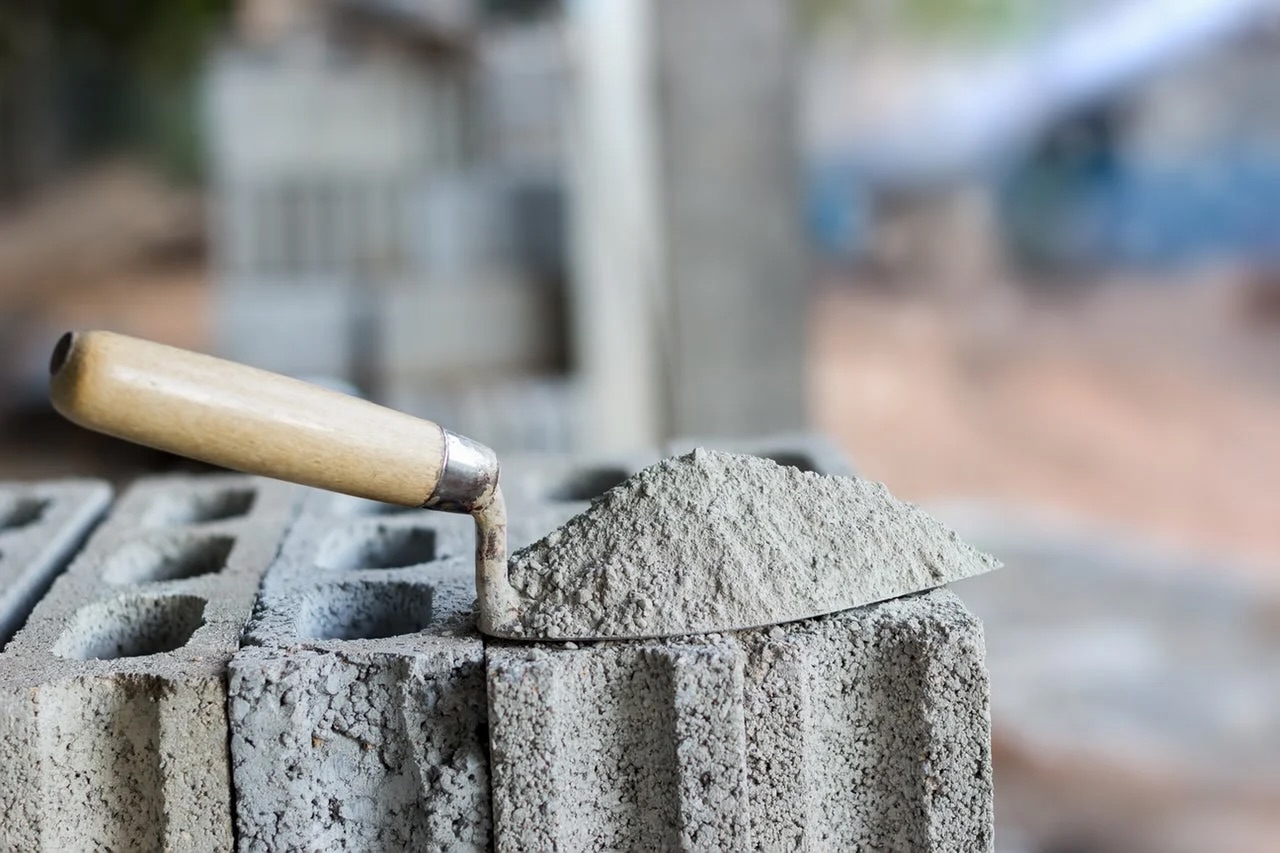
Building & Construction
Which Cement Is Used In Underwater Construction
Modified: December 7, 2023
Discover the ideal cement for underwater construction projects. Learn about the benefits and applications of this specialized building construction cement.
(Many of the links in this article redirect to a specific reviewed product. Your purchase of these products through affiliate links helps to generate commission for Storables.com, at no extra cost. Learn more)
Introduction
Underwater construction is a unique and challenging field that requires specialized knowledge and materials. One crucial component in underwater construction is cement. Cement serves as the binding agent that holds various construction materials together, providing strength and stability to underwater structures. It plays a vital role in ensuring the integrity and longevity of these projects.
When it comes to underwater construction, the selection of the right type of cement is of utmost importance. The chosen cement must possess specific properties that enable it to withstand the harsh underwater environment, including water pressure, corrosion, and other detrimental factors. Additionally, it should provide excellent adhesion, durability, and resistance to chemical attacks.
In this article, we will explore the different types of cement used in underwater construction and discuss the factors to consider when selecting the appropriate type for a project. By understanding the significance of cement in underwater construction and making informed choices, engineers and construction professionals can ensure the success of their underwater projects.
Key Takeaways:
- The right cement is crucial for underwater construction, providing strength, durability, and resistance to water and chemical attacks. Factors like water resistance, adhesive strength, and setting time must be considered for successful projects.
- Different types of cement, such as Portland, high alumina, super sulphated, blast furnace, and hydraulic, offer unique properties suitable for underwater construction. Engineers must carefully evaluate these options to ensure the longevity and performance of underwater structures.
Read more: Which Cement Is Best For House Construction
Importance of Cement in Underwater Construction
Cement plays a crucial role in underwater construction due to its ability to provide strength, durability, and stability to structures in environments with high water pressure and corrosive conditions.
One of the primary functions of cement in underwater construction is to bind together various construction materials. By creating a strong adhesive bond, cement ensures that the structure remains intact even under the immense pressure exerted by the surrounding water.
Furthermore, cement provides excellent water resistance, preventing the ingress of water and the subsequent deterioration of the structure due to corrosion. Without an effective water-resistant material like cement, underwater structures would be prone to damage, compromising their stability and longevity.
Another essential property of cement in underwater construction is its ability to resist chemical attacks. The harsh marine environment often exposes structures to corrosive elements, such as saltwater and chemicals. Cement with proper chemical resistance minimizes the risk of degradation and deterioration, ensuring the structural integrity of the project.
Moreover, cement possesses the ability to adapt and conform to the underwater environment. For example, it can hydrate and harden underwater without being compromised by the surrounding moisture. This unique property allows for efficient construction and reduces the need for extensive dewatering measures.
Additionally, cement offers the advantage of versatility in underwater construction. It can be used for various applications, including the construction of foundations, piers, bridges, dams, and underwater tunnels. Its adaptability makes it a valuable material that can accommodate a wide range of construction needs.
Without the use of cement, underwater construction would be impractical and structurally unsound. Cement’s ability to provide strength, durability, resistance to water and chemicals, and versatility makes it an indispensable material for successful underwater construction projects.
Factors to Consider in Choosing Cement for Underwater Construction
Choosing the right type of cement for underwater construction involves considering several key factors to ensure the structural integrity and longevity of the project. Here are the factors that should be taken into account when selecting cement for underwater construction:
- Water Resistance: The cement must have excellent water resistance properties to withstand the constant exposure to water and prevent water ingress. It should effectively resist permeability and maintain its strength and durability in a moist environment.
- Durability: Underwater structures are subjected to harsh conditions, including corrosion caused by saltwater and chemicals. The cement chosen should possess high durability to resist chemical attacks, prevent rusting of steel reinforcements, and maintain its structural integrity over the long term.
- Adhesive Strength: Cement used for underwater construction should have good adhesion properties to ensure a strong bond with various construction materials, such as concrete, rocks, and steel. It should provide a reliable connection between different components of the structure to withstand water pressure and wave action.
- Setting Time: Considering the setting time of the cement is crucial when working underwater. It should have a suitable setting time that allows for proper placement and curing. Rapid-setting or self-leveling cement can be advantageous for underwater construction to expedite the construction process.
- Chemical Resistance: The cement should be resistant to chemical attacks commonly found in marine environments, such as saltwater, sulfates, and acids. It should be able to maintain its properties and resist degradation caused by chemical exposure for long-term durability.
- Workability: When working underwater, it is essential to choose a cement that has good workability and can be easily mixed, placed, and finished underwater. Proper workability ensures efficient construction and reduces the need for extensive dewatering measures.
- Cost: Considering the cost is an important factor in any construction project. While it is crucial to select a cement with the necessary performance properties, it is also essential to assess the cost-effectiveness of different options to ensure that the chosen cement fits within the project budget.
By carefully considering these factors, engineers and construction professionals can make informed decisions when selecting the most appropriate cement for underwater construction. Choosing the right cement will contribute to the overall success, longevity, and performance of the underwater structure.
Types of Cement Used in Underwater Construction
In underwater construction, several types of cement are commonly used due to their specific properties that make them suitable for the marine environment. Let’s explore the main types of cement used in underwater construction:
- Portland Cement: Portland cement is the most widely used type of cement and is commonly found in underwater construction projects. It is known for its exceptional adhesive and binding properties. Portland cement sets and hardens by reacting with water, making it suitable for underwater applications where it can hydrate and cure even in a submerged state. It provides good water resistance and durability, making it a reliable choice for underwater structures.
- High Alumina Cement: High alumina cement, also known as calcium aluminate cement, is a specialized cement that contains a high amount of alumina (around 50-70%). It offers excellent resistance to chemical attacks and high temperatures, making it suitable for use in aggressive marine environments. High alumina cement sets rapidly and has good strength development, making it ideal for underwater construction projects that require quick-setting properties and chemical resistance.
- Super Sulphated Cement: Super sulphated cement is a blend of granulated blast furnace slag, calcium sulphate, and Portland cement clinker. It is specifically formulated to resist aggressive chemical attacks, including sulphate attack commonly encountered in marine environments. Super sulphated cement provides excellent resistance to seawater, making it a suitable choice for underwater construction projects.
- Blast Furnace Cement: Blast furnace cement is produced by grinding a mixture of clinker, gypsum, and granulated blast furnace slag. It offers good strength, low heat of hydration, and improved durability. Blast furnace cement is known for its high resistance to chloride and sulphate attacks, making it suitable for use in marine environments.
- Hydraulic Cement: Hydraulic cement is a type of cement that sets and hardens when exposed to water. It is commonly used in underwater construction due to its ability to set underwater and its high water resistance. Hydraulic cement can resist water pressure, bond well with various materials, and provide reliable protection against water ingress.
Each type of cement has its own unique properties, making it suitable for specific applications in underwater construction. The selection of the appropriate cement type depends on the project requirements, including water resistance, durability, setting time, and chemical resistance.
By understanding the different types of cement available, engineers and construction professionals can make informed decisions when choosing the most suitable cement for their underwater construction projects, ensuring the longevity and performance of the structures.
Portland Cement
Portland cement is the most commonly used type of cement in construction, including underwater construction. It is named after the resemblance of the hardened cement to the natural limestone found in Portland, England. Portland cement is a versatile and reliable cement that provides excellent strength, durability, and workability, making it widely used in various applications.
Portland cement is manufactured by grinding clinker, a combination of calcium silicates, with gypsum. The clinker is produced by burning limestone and clay at high temperatures in a kiln. This process creates fine powder particles, which, when mixed with water, undergo a chemical reaction known as hydration. The hydration process forms a paste that hardens and gains strength over time, providing the necessary durability for construction projects.
In underwater construction, Portland cement is favored for its ability to hydrate and harden underwater. It has a unique property called hydraulicity, meaning it can set and develop strength even when submerged in water. This characteristic is essential in ensuring the stability and integrity of underwater structures.
Furthermore, Portland cement exhibits good adhesive properties, allowing it to bond well with other construction materials. It provides a strong and reliable connection between components, ensuring structural stability and resistance to water pressure. This adhesive strength is crucial in preventing water ingress and maintaining the integrity of the underwater structure.
Portland cement also offers excellent water resistance. Once fully cured, it forms a dense and impermeable structure that resists the penetration of water. This is vital in underwater construction, as it protects the reinforced steel from rusting and prevents degradation due to prolonged exposure to water.
Additionally, Portland cement offers a wide range of options that suit various project requirements. Different formulations of Portland cement, such as ordinary Portland cement (OPC) and Portland Pozzolana cement (PPC), provide flexibility in terms of setting time, strength development, and specific performance characteristics.
It is important to note that when working with Portland cement underwater, proper mixing, placement, and curing techniques should be followed to ensure optimal results. Adequate measures, such as the use of underwater admixtures or fast-setting additives, can be employed to expedite the construction process and enhance the performance of the cement.
In summary, Portland cement is a reliable and versatile choice for underwater construction projects. Its unique hydraulic properties, adhesive strength, water resistance, and variety of formulations make it a preferred cement type. By utilizing Portland cement in underwater construction, engineers and construction professionals can ensure the durability, stability, and longevity of their projects.
Read more: What Type Of Cement Is Used For Stucco
High Alumina Cement
High alumina cement, also known as calcium aluminate cement, is a specialized type of cement that contains a higher proportion of alumina (approximately 50-70%) compared to other types of cement. This higher alumina content gives it unique properties that make it ideal for specific applications, including underwater construction.
One of the key characteristics of high alumina cement is its exceptional resistance to high temperatures and chemical attacks. It has a high refractoriness, which means it can withstand elevated temperatures without significant loss of strength or structural integrity. This property makes it suitable for use in aggressive marine environments, where the structure may be exposed to high temperatures due to heat from the surrounding water or other sources.
High alumina cement also offers excellent chemical resistance, including resistance to sulfates, acids, and seawater. This makes it highly durable and prevents the cement from deteriorating or degrading when exposed to corrosive agents. In underwater construction, where structures are continuously exposed to saltwater, high alumina cement provides a reliable solution to combat the effects of corrosion and ensure the longevity of the project.
The rapid-setting properties of high alumina cement are another advantage for underwater construction. It sets and hardens at a faster rate compared to other types of cement, allowing for quicker construction processes. This is particularly beneficial in situations where the project timeline is tight or in emergency repairs that require swift completion to avoid further damage to the underwater structure.
Furthermore, high alumina cement exhibits good bonding strength and adhesion properties. It forms a strong and stable bond with other construction materials, such as concrete, stones, and steel. This ensures structural integrity and resistance to water pressure and wave action, which are crucial factors in underwater construction projects.
It is important to note that while high alumina cement offers several advantages for underwater construction, it also has some limitations. It has higher heat generation during the hydration process, which may lead to thermal cracking if not properly managed. Additionally, high alumina cement has a shorter working time, requiring careful coordination during placement and curing.
Overall, high alumina cement is a specialized cement type that offers unique properties suitable for underwater construction. Its high temperature resistance, chemical resistance, rapid-setting characteristics, and strong bonding capability make it an excellent choice for marine environments. When used correctly and in combination with proper construction techniques, high alumina cement can contribute to the durability and success of underwater construction projects.
When it comes to underwater construction, it’s important to use hydraulic cement, which is specially designed to set and harden even when submerged in water. This type of cement is ideal for creating strong and durable structures in underwater environments.
Super Sulphated Cement
Super sulphated cement is a specialized type of cement that combines granulated blast furnace slag, calcium sulphate, and Portland cement clinker. The unique blend of these materials gives super sulphated cement its distinctive properties, making it suitable for specific applications, including underwater construction.
One of the key characteristics of super sulphated cement is its exceptional resistance against aggressive chemical attacks, particularly from sulphates. Sulphates are commonly found in seawater and certain soil conditions, and they can cause significant damage to traditional cementitious materials. However, super sulphated cement contains high levels of sulphate-resistant compounds, providing enhanced protection against sulphate attack. This resistance makes it highly suitable for use in marine environments where exposure to seawater is constant.
In addition to its superior sulphate resistance, super sulphated cement offers excellent durability in marine conditions. It is less prone to cracking or deterioration from the harsh marine environment, ensuring long-term structural integrity and reduced maintenance requirements for underwater constructions.
Another advantage of super sulphated cement is its ability to achieve substantial early strength development. It sets and gains strength quickly compared to other types of cement. This rapid strength development is beneficial for underwater construction, where early load-bearing capacity is often necessary to maintain the stability and integrity of the structures during construction and beyond.
Super sulphated cement also provides good workability, allowing for ease of mixing, placing, and finishing. This workability is important in underwater construction, where efficient construction processes are essential due to the challenging working conditions. The ability to work with the cement effectively underwater can help expedite construction and reduce the need for extensive dewatering measures.
However, it is important to note that super sulphated cement does have some limitations. It is generally less resistant to chloride attacks than other specialized cement types. Therefore, it may not be the best choice for underwater construction projects in chloride-rich environments.
In summary, super sulphated cement is a specialized cement type suitable for underwater construction projects in sulphate-rich marine environments. Its resistance to aggressive chemical attacks, rapid strength development, and good workability make it a reliable choice for structures that require enhanced durability and protection against sulphate degradation. By utilizing super sulphated cement, engineers and construction professionals can ensure the longevity and performance of their underwater construction projects.
Blast Furnace Cement
Blast furnace cement is a type of cement that is produced by grinding a mixture of clinker, gypsum, and granulated blast furnace slag. It is a blended cement that combines the benefits of both Portland cement and ground granulated blast furnace slag (GGBFS). Blast furnace cement is widely used in various construction projects, including underwater construction.
One of the key advantages of blast furnace cement is its high resistance to both chloride and sulphate attacks. Chloride attacks can occur in marine environments due to exposure to seawater, while sulphate attacks can be caused by sulphate-rich soils or industrial effluents. The inclusion of blast furnace slag in the cement mixture significantly enhances its resistance to these aggressive elements, ensuring long-term durability and reducing the risk of corrosion and degradation in underwater structures.
Blast furnace cement also offers improved workability compared to traditional Portland cement. The inclusion of blast furnace slag results in a finer and more uniform particle size distribution, which contributes to better plasticity and flowability of the cementitious mixture. This enhanced workability is particularly beneficial in underwater construction, where proper placement and compaction of the cement are essential, even in challenging underwater conditions.
In addition to its improved workability, blast furnace cement exhibits lower heat evolution during the hydration process compared to ordinary Portland cement. This reduced heat generation helps prevent thermal cracking, which is particularly advantageous in large-scale underwater construction projects.
Furthermore, blast furnace cement contributes to the sustainability of construction projects as it incorporates a by-product of the steel industry, granulated blast furnace slag. By utilizing blast furnace slag, the cement industry helps reduce waste and environmental impact while providing a cementitious material that offers improved performance.
It is important to note that blast furnace cement does have certain limitations. Its lower early strength development compared to Portland cement may require additional curing time for underwater structures. However, the long-term strength gain of blast furnace cement is comparable or even superior to that of Portland cement.
In summary, blast furnace cement is a blended cement that combines the advantages of Portland cement with the performance benefits of blast furnace slag. Its resistance to chloride and sulphate attacks, improved workability, and reduced heat evolution make it a preferred choice for underwater construction projects. By utilizing blast furnace cement, engineers and construction professionals can ensure the durability, sustainability, and longevity of their underwater structures.
Hydraulic Cement
Hydraulic cement is a specialized type of cement that sets and hardens when exposed to water. It is widely used in various construction applications, including underwater construction, where the presence of water is a constant challenge. The unique properties of hydraulic cement make it an ideal choice for projects in submerged or wet environments.
One of the key advantages of hydraulic cement is its ability to set and harden even when fully submerged in water. Unlike other types of cement, hydraulic cement undergoes a chemical reaction called hydration when mixed with water, which allows it to adapt and cure in the presence of moisture. This property makes hydraulic cement well-suited for underwater construction, as it eliminates the need for extensive dewatering measures and allows for efficient construction in challenging conditions.
Hydraulic cement offers excellent water resistance once fully cured. It forms a dense and impermeable structure that prevents water penetration and protects the underlying materials from moisture damage. This water resistance is crucial in underwater construction, where structures are constantly exposed to water pressure and the possibility of corrosion.
Another advantage of hydraulic cement is its ability to bond well with various construction materials, such as concrete, rocks, and steel. It provides a strong and reliable connection between different components, ensuring the structural integrity and stability of the underwater structure. This adhesive strength helps withstand water pressure and wave action, which are common challenges in underwater construction projects.
It is important to note that hydraulic cement sets and hardens relatively quickly, requiring careful coordination during the construction process. Proper mixing, placement, and curing techniques should be followed to ensure optimal performance. In some cases, additives or admixtures may be used to control the setting time and enhance the workability of hydraulic cement in underwater applications.
Hydraulic cement is available in different formulations, such as ordinary Portland cement (OPC) and various specialized cements. These variations provide flexibility in terms of setting time, strength development, and specific performance characteristics tailored to the project requirements.
In summary, hydraulic cement is a versatile and reliable choice for underwater construction projects. Its ability to set and harden underwater, excellent water resistance, strong adhesive properties, and various formulations make it a preferred material in submerged or wet environments. By utilizing hydraulic cement, engineers and construction professionals can ensure the success and durability of their underwater structures.
Read more: What Paint To Use On Outdoor Cement Statues
Factors to Consider in Selecting the Right Cement for Underwater Construction
Choosing the right cement for underwater construction is crucial to ensure the durability, longevity, and performance of the structures. Several important factors should be considered when selecting the appropriate cement for an underwater construction project:
- Water Resistance: The cement chosen must possess excellent water resistance properties to withstand the constant exposure to water in the underwater environment. It should resist permeability and maintain its strength and durability even in moist conditions.
- Durability: Underwater structures are subjected to harsh conditions, including water pressure, wave action, and corrosion from saltwater. The selected cement should be highly durable and capable of withstanding these challenges to ensure the longevity of the structure.
- Adhesive Strength: The cement used for underwater construction should have strong adhesive properties to ensure a secure bond between various construction materials, such as concrete, rocks, and steel. This adhesive strength is crucial in maintaining the structural integrity and stability of the underwater structure.
- Setting Time: Considering the setting time is important in underwater construction, as it affects the efficiency of the construction process. Rapid-setting or self-leveling cement can be advantageous to expedite the construction timeline, especially in projects with tight schedules or emergency repairs.
- Chemical Resistance: The cement selected should be resistant to chemical attacks commonly found in marine environments, such as saltwater, sulfates, and acids. It should be able to withstand the corrosive effects of these chemicals and maintain its properties over the long term.
- Workability: Workability is a crucial factor when working underwater. The cement should have good workability, allowing for easy mixing, placement, and finishing even in challenging underwater conditions. It should be able to adapt to the specific construction requirements and facilitate efficient construction processes.
- Environmental Considerations: Environmental sustainability is becoming increasingly important in construction. Choosing a cement with lower carbon footprint or incorporating supplementary cementitious materials, such as fly ash or slag, can contribute to environmentally friendly underwater construction practices.
- Cost: Considering the project budget is essential when selecting the appropriate cement for underwater construction. While it is important to choose a cement that meets the necessary performance requirements, the cost-effectiveness of different options should be assessed to ensure they align with the financial constraints of the project.
By carefully evaluating these factors and considering the specific project requirements, engineers and construction professionals can make informed decisions in selecting the right cement for underwater construction. Choosing the appropriate cement will contribute to the success, durability, and performance of the underwater structures, ensuring their long-term functionality and structural integrity.
Conclusion
Undertaking underwater construction projects requires careful consideration of various factors, with the selection of the right cement being of utmost importance. The chosen cement must possess specific properties that enable it to withstand the harsh underwater environment, including water pressure, corrosion, and other detrimental factors. It should provide excellent adhesion, durability, and resistance to chemical attacks.
Throughout this article, we have explored the importance of cement in underwater construction and discussed key factors to consider when selecting the appropriate cement. We have also examined different types of cement commonly used in underwater construction, such as Portland cement, high alumina cement, super sulphated cement, blast furnace cement, and hydraulic cement. Each type offers unique characteristics and advantages suitable for specific applications in the marine environment.
Considering factors such as water resistance, durability, adhesive strength, setting time, chemical resistance, workability, environmental considerations, and cost is crucial in selecting the right cement for underwater construction. Each factor plays a significant role in ensuring the success and durability of the structures.
The use of cement in underwater construction is essential to provide strength, durability, and stability to the structures. It bonds various construction materials together, protects against water ingress and chemical attacks, and withstands the challenges posed by the underwater environment. By making informed decisions and considering the specific project requirements, engineers and construction professionals can choose the most suitable cement type for underwater construction.
In conclusion, the selection of the right cement for underwater construction is a critical aspect of ensuring the longevity and performance of underwater structures. By understanding the importance of cement, evaluating the various types available, and considering the relevant factors, construction professionals can make informed choices that meet the specific needs of their underwater projects. With the right cement in place, engineers can successfully navigate the unique challenges of underwater construction and deliver structures that are strong, durable, and built to withstand the test of time.
Frequently Asked Questions about Which Cement Is Used In Underwater Construction
Was this page helpful?
At Storables.com, we guarantee accurate and reliable information. Our content, validated by Expert Board Contributors, is crafted following stringent Editorial Policies. We're committed to providing you with well-researched, expert-backed insights for all your informational needs.
0 thoughts on “Which Cement Is Used In Underwater Construction”