Home>Furniture & Design>Interior Design Trends>Why Does Tempered Glass Explode
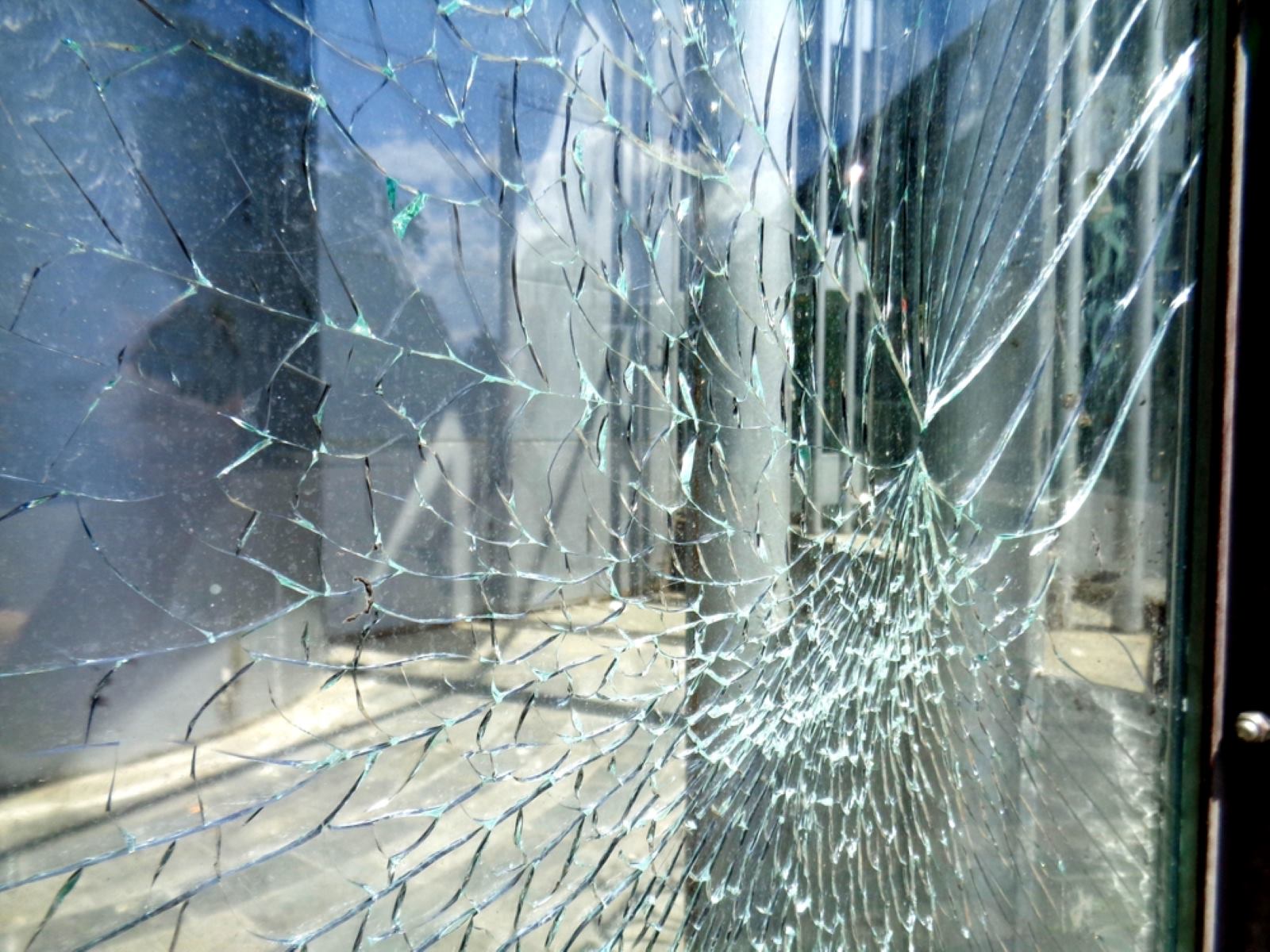
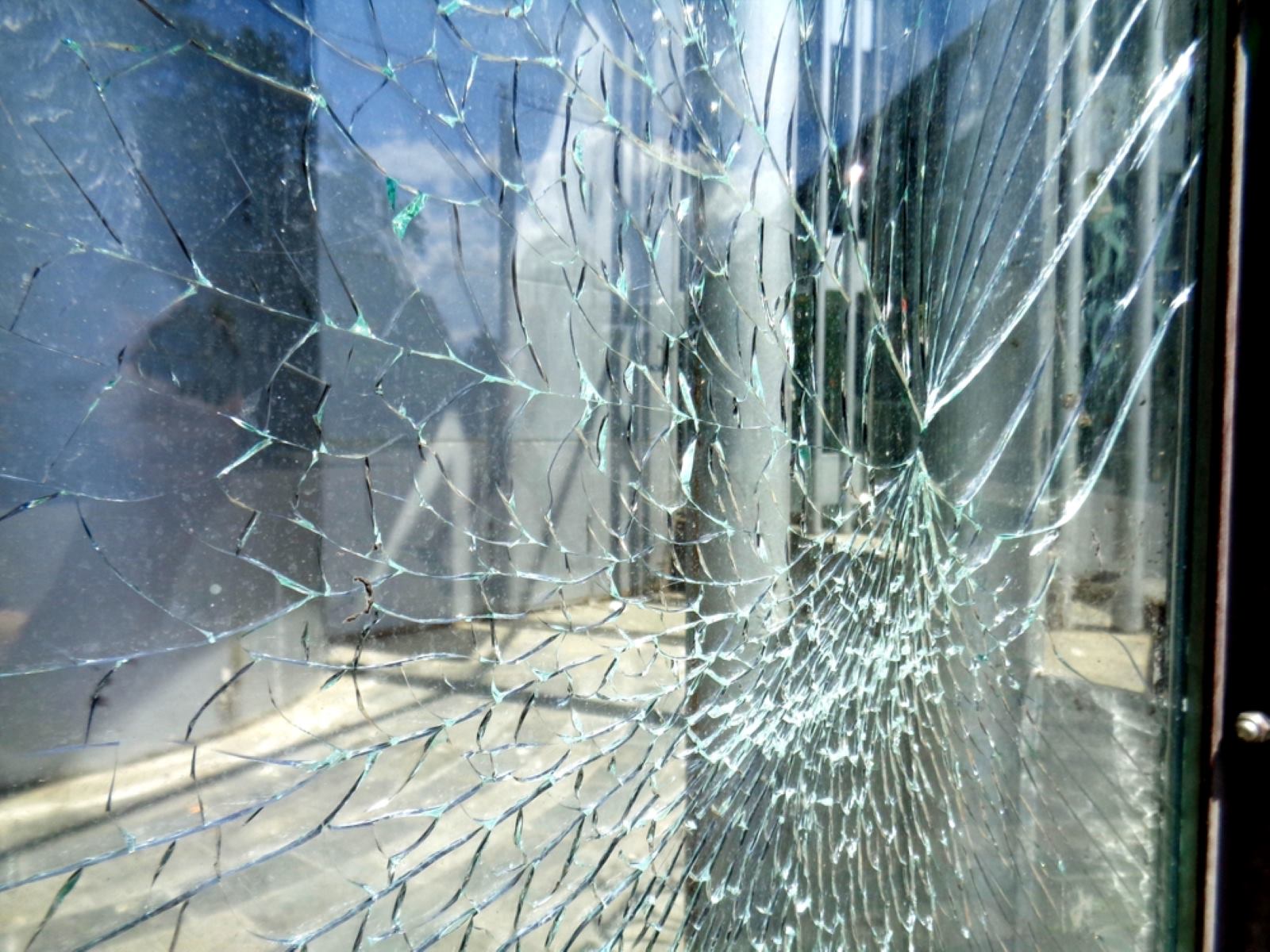
Interior Design Trends
Why Does Tempered Glass Explode
Modified: October 20, 2024
Discover the reasons behind tempered glass explosions and stay informed about the latest interior design trends. Explore the potential risks and design solutions.
(Many of the links in this article redirect to a specific reviewed product. Your purchase of these products through affiliate links helps to generate commission for Storables.com, at no extra cost. Learn more)
Introduction
Tempered glass is widely used in various applications due to its strength, durability, and safety features. However, there are instances where tempered glass unexpectedly shatters or explodes, causing concern and confusion among users. Understanding the reasons behind this phenomenon is crucial for both consumers and industry professionals.
Exploring the factors that contribute to tempered glass explosions can shed light on the complexities of this material and help individuals make informed decisions about its usage. In this article, we will delve into the intricacies of tempered glass, its manufacturing process, and the common causes of spontaneous breakage. By gaining insights into these aspects, readers can develop a deeper appreciation for the unique properties and potential vulnerabilities of tempered glass.
Key Takeaways:
- Tempered glass can explode due to thermal stress, manufacturing defects, and impact damage. Proper installation, regular inspections, and strategic shading can help mitigate these risks and ensure safety.
- Understanding the complexities of tempered glass and implementing proactive measures can help prevent unexpected breakage. Advanced manufacturing techniques and quality control are crucial for its reliability.
Read more: Why Does A Light Bulb Explode
What is tempered glass?
Tempered glass, also known as toughened glass, is a type of safety glass that is processed to enhance its strength and resilience. Unlike standard glass, tempered glass undergoes a specialized thermal or chemical treatment, resulting in a product with distinct properties. One of its key features is its ability to shatter into small, granular pieces instead of sharp shards when broken, reducing the risk of injury.
The tempering process involves heating the glass to a high temperature and then rapidly cooling it, a technique known as quenching. This rapid cooling induces high surface compression and tensile stress within the glass, contributing to its increased strength. As a result, tempered glass is approximately four times stronger than regular glass of the same thickness and is highly resistant to impact and thermal stress.
Due to its enhanced durability and safety characteristics, tempered glass is widely utilized in various applications, including shower enclosures, glass doors, automobile windows, and electronic devices. Its ability to withstand mechanical and thermal stresses makes it a preferred choice for environments where safety is paramount.
In addition to its strength, tempered glass also exhibits resistance to temperature differentials, making it suitable for use in areas exposed to varying climatic conditions. This property is particularly valuable in architectural and automotive applications, where the glass may be subjected to rapid temperature changes without compromising its structural integrity.
The unique properties of tempered glass make it a versatile and reliable material for diverse uses, offering both safety and aesthetic benefits. Its widespread adoption in construction, automotive, and consumer electronics industries underscores its significance as a key component in modern design and engineering.
In summary, tempered glass is a specialized type of safety glass that undergoes a controlled thermal or chemical treatment to enhance its strength and safety features. Its ability to shatter into small, granular pieces and withstand mechanical and thermal stresses makes it an indispensable material in various applications, contributing to the safety and functionality of numerous products and structures.
How is tempered glass made?
Tempered glass is created through a carefully controlled thermal or chemical process to enhance its strength and safety properties. The manufacturing process involves several precise steps to ensure the glass achieves the desired characteristics.
-
Selection of Raw Materials: The production of tempered glass begins with the selection of high-quality raw materials, primarily silica sand, soda ash, and limestone. These materials are carefully measured and mixed to form a homogeneous glass batch.
-
Melting and Refining: The glass batch is then fed into a furnace, where it undergoes a high-temperature melting process. During this stage, any impurities are removed, and the molten glass is refined to achieve the desired clarity and consistency.
-
Shaping and Cooling: Once the molten glass attains the required viscosity, it is shaped into flat sheets using various techniques such as floating, rolling, or pressing. The glass is then gradually cooled to anneal it, reducing internal stresses and enhancing its overall stability.
-
Tempering Process: The tempered glass is subjected to a process known as quenching, which involves rapidly cooling the glass surface while maintaining the inner portion at a higher temperature. This rapid cooling induces high surface compression and tensile stress within the glass, resulting in its characteristic strength and safety features.
-
Quality Inspection: After the tempering process, the glass undergoes rigorous quality checks to ensure it meets industry standards for strength, flatness, and visual clarity. Any defects or irregularities are identified and addressed to maintain the integrity of the tempered glass.
-
Cutting and Packaging: Once the tempered glass passes the quality inspection, it is cut into specific dimensions according to customer requirements. The finished glass panels are then carefully packaged to prevent damage during transportation and handling.
The meticulous manufacturing process of tempered glass ensures that it meets stringent quality and safety standards, making it a reliable and durable material for a wide range of applications. By understanding the intricacies of its production, consumers and industry professionals can appreciate the craftsmanship and engineering behind tempered glass, leading to informed decisions regarding its usage in various settings.
Common reasons for tempered glass to explode
Tempered glass is renowned for its strength and safety features, but there are instances where it unexpectedly shatters or explodes, causing concern and confusion among users. Understanding the common reasons behind tempered glass explosions is crucial for both consumers and industry professionals. By delving into these factors, individuals can gain valuable insights into the vulnerabilities of tempered glass and make informed decisions about its usage.
Thermal stress
One of the primary reasons for tempered glass to explode is thermal stress. This occurs when the glass is subjected to sudden and extreme temperature differentials, causing uneven expansion and contraction across its surface. For example, exposure to direct sunlight or contact with hot and cold air simultaneously can create significant thermal differentials, placing immense stress on the glass. Over time, this stress can exceed the glass's tolerance, leading to spontaneous breakage or explosion. In architectural settings, such as glass facades or windows, the combination of solar radiation and shading can exacerbate thermal stress, increasing the risk of tempered glass failure.
Read more: Why Does Soda Explode In The Freezer
Manufacturing defects
Another factor contributing to tempered glass explosions is manufacturing defects. Despite stringent quality control measures, occasional defects such as microscopic impurities or surface damage may go undetected during the production process. These imperfections can compromise the structural integrity of the glass, making it susceptible to spontaneous breakage under certain conditions. Additionally, variations in the tempering process, such as uneven cooling or quenching, can introduce internal stresses that weaken the glass over time, potentially leading to unexpected explosions.
Impact damage
Furthermore, tempered glass can explode due to impact damage. While tempered glass is designed to withstand significant force, severe impacts from sharp objects or heavy items can create localized stress concentrations, compromising its strength. Even minor surface damage, such as scratches or chips, can weaken the glass and serve as potential initiation points for spontaneous breakage. In high-traffic areas or environments with frequent handling, the cumulative effects of minor impacts can gradually compromise the glass's structural integrity, increasing the likelihood of explosive failure.
By recognizing these common reasons for tempered glass explosions, consumers and industry professionals can take proactive measures to mitigate the associated risks. Implementing proper installation techniques, regular inspections, and adherence to recommended usage guidelines can help minimize the potential for tempered glass failures, ensuring the continued safety and reliability of this versatile material.
Thermal stress
Thermal stress is a significant factor contributing to the unexpected breakage or explosion of tempered glass. This phenomenon occurs when the glass is exposed to rapid and extreme temperature differentials, leading to uneven expansion and contraction across its surface. The resulting stress can exceed the glass's tolerance, ultimately causing spontaneous breakage.
In architectural and automotive applications, thermal stress is a common concern, particularly in environments where tempered glass is exposed to fluctuating temperature conditions. For example, in buildings with expansive glass facades, the combination of direct sunlight and shaded areas can create substantial temperature differentials across the glass surface. As a result, the areas exposed to intense solar radiation may undergo significant expansion, while the shaded regions remain relatively cool. This stark contrast in temperature can induce internal stress within the glass, potentially leading to spontaneous breakage over time.
Similarly, in automotive settings, tempered glass windows and sunroofs are susceptible to thermal stress, especially when subjected to rapid temperature changes. The exposure to direct sunlight, followed by sudden cooling from air conditioning or contact with cold external environments, can create thermal differentials that place considerable strain on the glass. Over repeated cycles of heating and cooling, the cumulative effects of thermal stress can compromise the structural integrity of the glass, increasing the risk of unexpected breakage.
Moreover, in residential and commercial settings, tempered glass doors, windows, and partitions are exposed to varying temperature conditions throughout the day. The impact of external factors, such as weather fluctuations and indoor heating or cooling systems, can contribute to thermal stress, potentially leading to spontaneous breakage if not properly managed.
To mitigate the risks associated with thermal stress, proper installation techniques and the use of appropriate glass thickness and quality are essential. Additionally, the strategic placement of shading devices, such as awnings or blinds, can help minimize direct exposure to intense sunlight, reducing the likelihood of thermal stress-induced failures in architectural settings.
By understanding the implications of thermal stress on tempered glass, industry professionals and consumers can implement proactive measures to minimize the potential for spontaneous breakage, ensuring the continued safety and reliability of this essential material in various applications.
Manufacturing defects
Manufacturing defects represent a significant contributing factor to the unexpected breakage or explosion of tempered glass. Despite stringent quality control measures, occasional imperfections may go undetected during the production process, compromising the structural integrity of the glass. These defects can manifest in various forms, including microscopic impurities, surface damage, or inconsistencies in the tempering process, all of which can weaken the glass and increase the risk of spontaneous breakage.
Microscopic impurities, such as nickel sulfide inclusions, are among the common defects that can compromise the strength of tempered glass. These tiny particles, if present in the glass, can act as stress concentration points, making the glass susceptible to sudden failure. While manufacturers employ meticulous quality control protocols to minimize the presence of impurities, the inherent challenges of detecting and eliminating these microscopic flaws pose a persistent risk to the structural reliability of tempered glass.
Surface damage, such as scratches or chips, can also serve as potential initiation points for spontaneous breakage. Even minor imperfections on the glass surface can weaken its overall strength, particularly when subjected to external stressors or temperature differentials. Additionally, variations in the tempering process, such as uneven cooling or quenching, can introduce internal stresses that compromise the glass's structural integrity over time, increasing the likelihood of unexpected failures.
In architectural and automotive applications, where tempered glass is subjected to diverse environmental conditions and mechanical stresses, the presence of manufacturing defects poses a significant concern. The cumulative effects of these imperfections, combined with external factors such as thermal stress and impact damage, can heighten the risk of spontaneous breakage, potentially compromising the safety and reliability of the glass.
To address the challenges associated with manufacturing defects, continuous advancements in quality control technologies and processes are essential. Manufacturers are increasingly leveraging advanced inspection techniques, such as automated optical inspection systems and enhanced material testing methods, to detect and mitigate potential defects before the glass reaches the market. By implementing rigorous quality assurance measures throughout the production cycle, the industry strives to minimize the occurrence of manufacturing defects and uphold the integrity of tempered glass in various applications.
By acknowledging the impact of manufacturing defects on tempered glass, industry professionals and consumers can advocate for stringent quality control standards and proactive defect mitigation strategies, ensuring the continued safety and reliability of this essential material.
When tempered glass is damaged or has internal defects, it can lead to stress concentrations that cause it to explode. Regular inspections and careful handling can help prevent this.
Read more: Why Did My Glass Candle Explode
Impact damage
Impact damage represents a significant factor contributing to the unexpected breakage or explosion of tempered glass. While tempered glass is designed to withstand substantial force, severe impacts from sharp objects or heavy items can create localized stress concentrations, compromising its structural integrity. Even minor surface damage, such as scratches or chips, can weaken the glass and serve as potential initiation points for spontaneous breakage.
In architectural and automotive applications, where tempered glass is exposed to various mechanical stresses, the risk of impact damage is a prevalent concern. For instance, in commercial buildings with glass facades or partitions, the potential for accidental impact from moving objects or maintenance activities poses a constant threat to the integrity of the glass. Similarly, in automotive settings, the susceptibility of tempered glass windows and windshields to impact damage from road debris or collisions necessitates careful consideration of the material's resilience.
Furthermore, in residential environments, tempered glass doors, tabletops, and shower enclosures are susceptible to impact damage from everyday use and accidental collisions. The cumulative effects of minor impacts over time can compromise the glass's structural integrity, increasing the likelihood of unexpected breakage.
To address the challenges associated with impact damage, proactive measures such as regular inspections and prompt repair of any surface imperfections are essential. Additionally, the strategic placement of protective barriers or films in high-traffic areas can help mitigate the risk of impact damage, prolonging the lifespan of tempered glass in various applications.
By recognizing the implications of impact damage on tempered glass, industry professionals and consumers can implement proactive measures to minimize the potential for spontaneous breakage, ensuring the continued safety and reliability of this essential material.
Conclusion
In conclusion, the unexpected breakage or explosion of tempered glass can be attributed to a combination of factors, including thermal stress, manufacturing defects, and impact damage. The unique properties of tempered glass, such as its enhanced strength and safety features, make it a preferred choice for a wide range of applications, from architectural and automotive uses to consumer electronics and household fixtures. However, the vulnerabilities associated with thermal stress, manufacturing defects, and impact damage underscore the importance of understanding the complexities of this material and implementing proactive measures to mitigate potential risks.
Thermal stress, arising from rapid and extreme temperature differentials, poses a significant challenge to the structural integrity of tempered glass. In architectural and automotive settings, where the glass is exposed to fluctuating temperature conditions, the cumulative effects of thermal stress can lead to unexpected breakage over time. Proper installation techniques, strategic shading, and adherence to recommended usage guidelines are essential in managing the risks associated with thermal stress.
Manufacturing defects represent another critical factor contributing to tempered glass failures. Despite stringent quality control measures, the presence of microscopic impurities, surface damage, or variations in the tempering process can compromise the strength of the glass, increasing the likelihood of spontaneous breakage. Continuous advancements in quality control technologies and rigorous inspection protocols are crucial in minimizing the occurrence of manufacturing defects and upholding the reliability of tempered glass in diverse applications.
Impact damage, resulting from severe impacts or cumulative minor collisions, also poses a significant risk to the structural integrity of tempered glass. In high-traffic areas and environments with frequent handling, the potential for accidental impact necessitates proactive measures, such as regular inspections and the use of protective barriers, to mitigate the risk of unexpected breakage.
By gaining insights into the common reasons for tempered glass explosions, industry professionals and consumers can make informed decisions about its usage and implement proactive measures to ensure the continued safety and reliability of this essential material. Through a combination of advanced manufacturing techniques, meticulous quality control, and strategic usage guidelines, tempered glass can continue to serve as a durable and resilient material in various applications, contributing to the safety and functionality of modern designs and structures.
Frequently Asked Questions about Why Does Tempered Glass Explode
Was this page helpful?
At Storables.com, we guarantee accurate and reliable information. Our content, validated by Expert Board Contributors, is crafted following stringent Editorial Policies. We're committed to providing you with well-researched, expert-backed insights for all your informational needs.
0 thoughts on “Why Does Tempered Glass Explode”