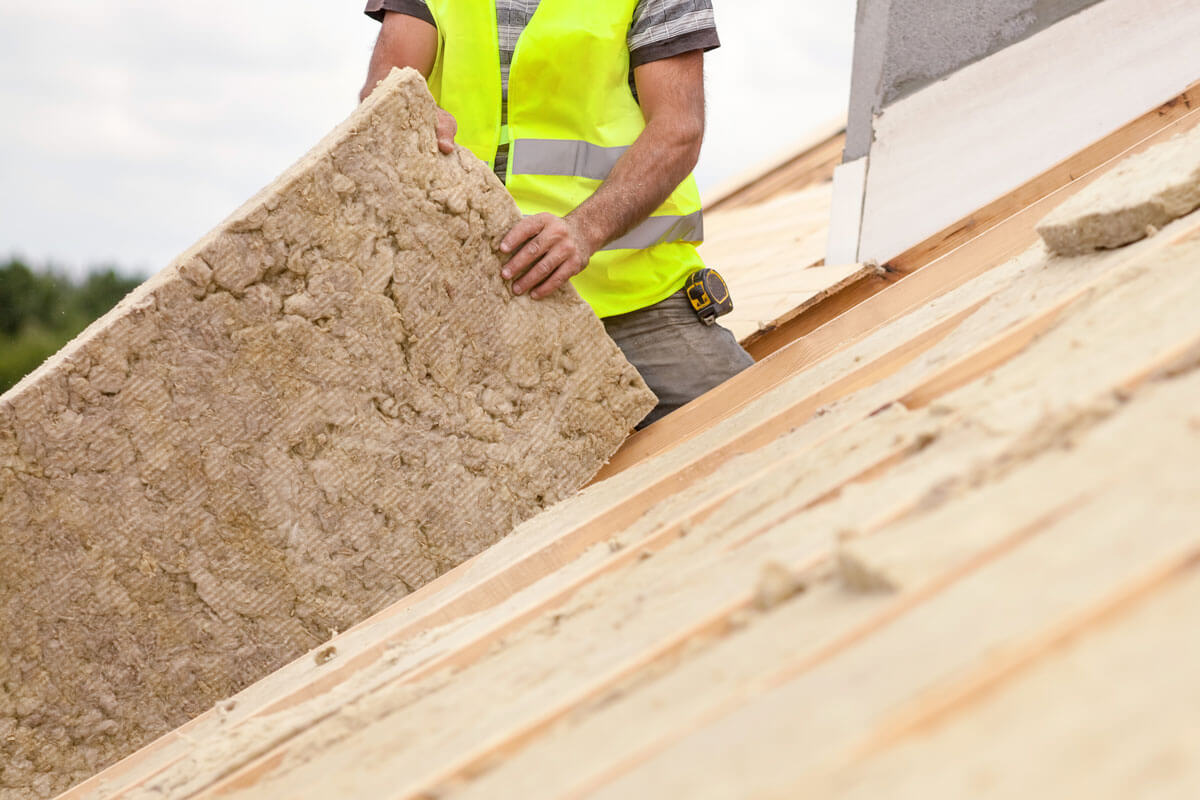
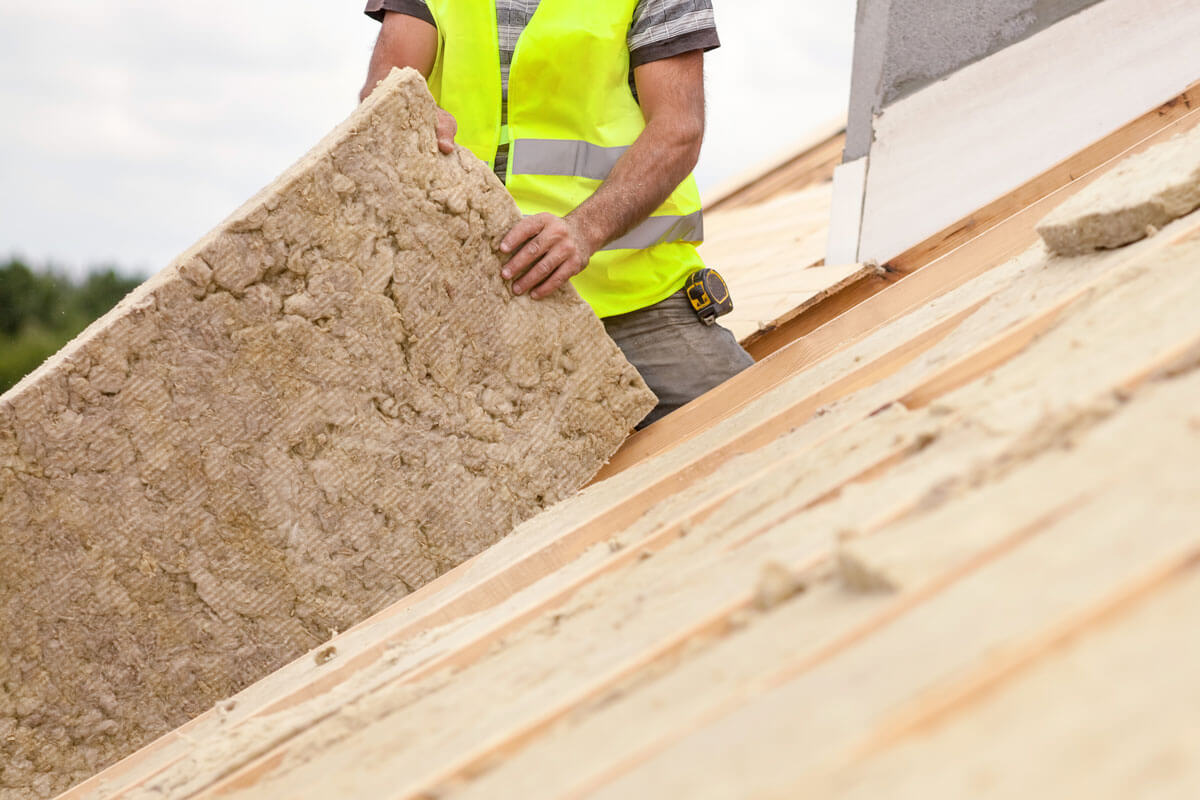
Articles
How Long Does Insulation Last
Modified: January 8, 2024
Discover how long insulation can last and learn about the factors that can affect its lifespan. Read more in our informative articles.
(Many of the links in this article redirect to a specific reviewed product. Your purchase of these products through affiliate links helps to generate commission for Storables.com, at no extra cost. Learn more)
Introduction
Insulation is an essential component of any building, providing thermal resistance to maintain a comfortable and energy-efficient environment. But, like any other material, insulation has a limited lifespan. Understanding the factors that affect the longevity of insulation is crucial in ensuring its effectiveness and making informed decisions about maintenance and replacement.
Several factors come into play when determining how long insulation will last. These factors include the type of insulation material, the installation quality, the climate conditions, and the level of maintenance. By considering these factors, you can assess the lifespan of your insulation and take appropriate measures to ensure its optimal performance over time.
There are various types of insulation materials available in the market, each with its own unique set of characteristics and lifespan. The most common types of insulation include fiberglass, foam, cellulose, and mineral wool. Understanding the expected lifespan of each can help you make an informed decision about the best type of insulation for your specific needs.
In addition to the type of insulation, the climate conditions in which it is installed play a significant role in determining its lifespan. Extreme temperatures, humidity, and exposure to moisture can accelerate the deterioration of insulation. Therefore, it is essential to consider the climate conditions of your region when assessing the longevity of your insulation.
Over time, insulation may show signs of wear and tear, indicating the need for replacement or maintenance. Recognizing these signs, such as decreased energy efficiency, moisture damage, or pest infestation, is crucial to prevent further damage and ensure the insulation continues to perform optimally.
Maintaining and extending the lifespan of insulation can be achieved through regular inspections, proper installation techniques, and timely repairs. This proactive approach can help you save money in the long run by avoiding costly replacements and maintaining the energy efficiency of your space.
In this comprehensive guide, we will explore the different types of insulation and their expected lifespans. We will examine the impact of climate conditions on insulation longevity and discuss the signs of deteriorating insulation. Additionally, we will provide practical tips on how to maintain and extend the lifespan of your insulation. By the end of this article, you will have a clear understanding of how long insulation lasts and how to optimize its performance in your building.
Key Takeaways:
- Regular maintenance, prompt repairs, and proper ventilation are crucial for extending the lifespan of insulation and maximizing energy efficiency in buildings.
- Understanding the impact of climate conditions, recognizing signs of deteriorating insulation, and implementing proactive maintenance measures are essential for optimizing insulation performance and longevity.
Read more: How Long Does Blown In Insulation Last
Factors Affecting the Lifespan of Insulation
The lifespan of insulation can be impacted by various factors that contribute to its degradation and wear over time. Understanding these factors is crucial in assessing the longevity of your insulation and taking appropriate measures to maintain its effectiveness. Let’s explore the key factors that can affect the lifespan of insulation:
- Type of Insulation Material: Different insulation materials have varying levels of durability and resistance to deterioration. Some materials, such as fiberglass and mineral wool, are known for their long lifespan and can last for several decades. On the other hand, foam insulation, although highly effective, may have a shorter lifespan due to its susceptibility to cracking and aging.
- Quality of Installation: The quality of insulation installation plays a significant role in determining its lifespan. Improper installation techniques or inadequate sealing can result in air leakage, condensation, and moisture build-up, leading to the deterioration of insulation. It is crucial to ensure that insulation is properly installed by professionals who follow industry standards and guidelines.
- Climate Conditions: The climate in which insulation is installed can greatly impact its lifespan. Extreme temperature fluctuations, high humidity, and exposure to moisture can accelerate the breakdown of insulation materials. For example, in regions with hot summers and cold winters, insulation may expand and contract, leading to cracks and reduced effectiveness over time.
- Maintenance and Care: Regular maintenance and care can significantly extend the lifespan of insulation. Inspections should be conducted periodically to identify any signs of damage, such as water stains, mold growth, or pest infestation. Prompt repairs should be made to mitigate further deterioration and maintain the insulation’s thermal resistance capabilities.
- Level of Usage: The amount of usage and activity in the space where the insulation is installed can impact its lifespan. High traffic areas or buildings with frequent renovations and modifications may experience more wear and tear on the insulation, reducing its effectiveness over time.
- Pest Infestation: Insulation can become a breeding ground for pests such as rodents and insects, which can damage and degrade the material. Regular pest control measures should be implemented to prevent infestations and protect the lifespan of the insulation.
It is important to consider these factors when evaluating the lifespan of your insulation and making decisions regarding maintenance, repairs, or replacement. By understanding these influences, you can take proactive steps to ensure the longevity and effectiveness of your insulation, ultimately maximizing energy efficiency and comfort in your building.
Types of Insulation and Their Lifespan
Insulation materials come in various forms, each with its own unique characteristics, R-values, and expected lifespan. Understanding the different types of insulation can help you make an informed decision when choosing the right material for your building. Let’s explore some common types of insulation and their expected lifespans:
- Fiberglass Insulation: Fiberglass insulation is one of the most popular and widely used types of insulation. It is made of tiny glass fibers that trap air and provide thermal resistance. Fiberglass insulation has a long lifespan, typically ranging from 20 to 30 years or more. With proper installation and maintenance, it can effectively retain its insulating properties for decades.
- Foam Insulation: Foam insulation, including spray foam and rigid foam boards, offers excellent thermal resistance and air sealing properties. However, foam insulation may have a shorter lifespan compared to other types of insulation. On average, foam insulation can last between 10 to 15 years, but this can vary depending on factors such as quality of installation, exposure to UV radiation, and potential for moisture damage.
- Cellulose Insulation: Cellulose insulation is made from recycled materials, such as newspapers or cardboard, treated with fire-retardant chemicals. It has a reasonably long lifespan, often lasting around 20 to 30 years. Regular maintenance and addressing moisture issues promptly can help prolong the lifespan of cellulose insulation.
- Mineral Wool Insulation: Mineral wool insulation, also known as rock wool or slag wool, is made from volcanic rock or industrial by-products. It offers excellent fire resistance and sound insulation properties. Mineral wool insulation has a long lifespan and can last for several decades, typically ranging from 30 to 50 years or more.
- Spray Foam Insulation: Spray foam insulation is a versatile and efficient insulation option. It is applied as a liquid and expands to fill gaps and crevices, providing an airtight seal. The lifespan of spray foam insulation can range from 20 to 30 years or more, depending on factors such as application quality, exposure to UV radiation, and proper maintenance.
It’s important to note that while these are general estimations, the lifespan of insulation can vary depending on installation quality, environmental factors, and maintenance practices. Regular inspections and maintenance by professionals can help identify any signs of deterioration and extend the lifespan of insulation materials.
By selecting the right type of insulation for your specific needs and ensuring proper installation and maintenance, you can maximize its lifespan and enjoy the energy-saving benefits for years to come.
Fiberglass Insulation
Fiberglass insulation is one of the most commonly used and well-known types of insulation. It is made of tiny glass fibers that are intertwined to form a mat. The air trapped within the fibers creates thermal resistance, helping to keep heat in during the winter and out during the summer. Fiberglass insulation is known for its affordability, effectiveness, and versatility in various applications.
When it comes to lifespan, fiberglass insulation is known for its durability and longevity. On average, fiberglass insulation can last between 20 to 30 years or more, depending on various factors such as installation quality, maintenance, and exposure to environmental conditions.
Proper installation is crucial for maximizing the lifespan of fiberglass insulation. It should be installed by professionals who follow industry best practices and guidelines. Improper installation can lead to compression of the insulation, reducing its effectiveness and lifespan.
Regular maintenance is also essential to ensure the insulation continues to perform optimally. Inspections should be conducted periodically to check for any signs of damage or moisture intrusion. Moisture can cause mold growth and degradation of the insulation material, reducing its thermal resistance capabilities.
Fiberglass insulation is known to be resistant to pests and insects, preventing infestations and damage to the insulation. However, it is still important to inspect for any signs of pest activity and address the issue promptly if detected.
While fiberglass insulation has a long lifespan, it can experience wear and tear over time. Signs of deteriorating fiberglass insulation may include visible gaps or tears in the insulation material, decreased energy efficiency, drafts, or increased noise infiltration. If any of these signs are present, it is advisable to consult a professional to assess the condition of the insulation and determine if replacement or repairs are necessary.
Regularly upgrading and maintaining your insulation can provide numerous benefits, such as improved energy efficiency, reduced utility bills, enhanced comfort, and a positive impact on the environment. By investing in quality fiberglass insulation and ensuring proper installation and maintenance, you can enjoy the long-lasting benefits it provides for many years to come.
Foam Insulation
Foam insulation is a popular choice for sealing and insulating buildings due to its exceptional thermal resistance and air sealing properties. It is available in two main forms: spray foam insulation and rigid foam boards. Foam insulation is known for its ability to provide a seamless and airtight barrier, reducing heat transfer and improving energy efficiency.
When considering the lifespan of foam insulation, it’s important to note that it may have a shorter lifespan compared to other types of insulation materials. On average, foam insulation can last between 10 to 15 years. However, it’s important to understand that this can vary depending on several factors:
Quality of Installation: The quality of foam insulation installation is crucial for its longevity. Proper application thickness, correct mixing of components, and adequate curing time are essential factors. Incorrect installation techniques or shortcuts can lead to premature aging, cracking, and reduced effectiveness of foam insulation.
Exposure to UV Radiation: Foam insulation exposed to direct sunlight or UV radiation without proper protection can degrade over time. Ultraviolet rays can cause the foam to break down, resulting in cracks and diminished performance. Application of a protective coating or covering can help mitigate UV damage and extend the lifespan of foam insulation.
Potential for Moisture Damage: Moisture can negatively impact foam insulation, especially if there are water leaks or high humidity levels. Excessive moisture can lead to the growth of mold and mildew, compromising the integrity and insulating properties of the foam. Proper ventilation and regular inspections are important to prevent and address moisture issues promptly.
Despite having a relatively shorter lifespan, foam insulation offers several advantages, including its high R-value, air sealing capabilities, and resistance to pests and insects. It provides an effective thermal barrier and can contribute to energy savings and improved indoor comfort.
Regular inspections and maintenance are essential to ensure that foam insulation continues to perform optimally. Periodic checks for signs of cracking, deterioration, or water damage should be conducted. Any detected issues should be addressed promptly to prevent further deterioration and maintain the insulation’s effectiveness.
In situations where foam insulation has reached the end of its lifespan or has suffered significant damage, replacement may be necessary. Consulting with insulation professionals can help determine the best course of action based on the specific conditions and requirements of your building.
By understanding the factors that can impact the lifespan of foam insulation and taking proper maintenance measures, you can maximize its longevity and continue to benefit from its excellent insulating properties for years to come.
Read more: How Long Does Foam Insulation Last
Cellulose Insulation
Cellulose insulation is an eco-friendly and cost-effective option for insulating buildings. It is composed of recycled paper materials, such as newspaper or cardboard, treated with fire-retardant chemicals to enhance its resistance to fire. Cellulose insulation offers excellent thermal resistance and is known for its ability to reduce energy consumption and enhance indoor comfort.
When it comes to the lifespan of cellulose insulation, it can last for an extended period with proper installation and maintenance. On average, cellulose insulation can have a lifespan ranging from 20 to 30 years.
The longevity of cellulose insulation depends on various factors, including:
Installation Quality: Proper installation is crucial for maximizing the lifespan of cellulose insulation. It should be installed by professionals who follow industry standards, ensuring that the material is evenly distributed and adequately compacted. Properly installed cellulose insulation can maintain its effectiveness over an extended period.
Maintenance: Regular maintenance and inspections are essential to ensure the longevity of cellulose insulation. Inspections should be conducted periodically to check for signs of water damage, mold growth, or pest infestation. Prompt repairs and addressing any issues can prevent further deterioration.
Moisture Control: Moisture can be detrimental to cellulose insulation, leading to mold growth and degradation of the material. It’s important to address any sources of moisture, such as leaks or condensation, and ensure proper ventilation. Adequate ventilation and moisture control measures will help extend the lifespan of cellulose insulation.
Climate Conditions: The climate in which cellulose insulation is installed can impact its lifespan. High humidity or exposure to extreme temperature fluctuations can potentially accelerate the deterioration of cellulose insulation. Insulation in regions with harsher climates may need more frequent inspections and maintenance.
Regular inspections by professionals can help identify any signs of damage or degradation in cellulose insulation. Signs of deteriorating cellulose insulation may include water stains, mold growth, or a decrease in energy efficiency.
If cellulose insulation has reached the end of its lifespan or suffered significant damage, it may require replacement. Consulting with insulation experts can help determine the best course of action based on the condition of your insulation and the specific requirements of your building.
Cellulose insulation offers numerous benefits, such as its environmentally friendly composition, thermal resistance, and soundproofing capabilities. By properly installing and maintaining cellulose insulation, you can enjoy its energy-saving benefits and enhanced comfort in your home or building for many years.
Insulation can last for 80-100 years if properly installed and maintained. However, factors like moisture and damage can reduce its lifespan. Regular inspections can help identify any issues early on.
Mineral Wool Insulation
Mineral wool insulation, also known as rock wool or slag wool, is a versatile and effective insulation material made from natural or synthetic minerals, such as basalt or slag. It is known for its excellent thermal and acoustic insulation properties, as well as its resistance to fire and pests. Mineral wool insulation can be used in a variety of applications, including residential, commercial, and industrial buildings.
When it comes to the lifespan of mineral wool insulation, it is known for its durability and longevity. On average, mineral wool insulation can last for several decades, often ranging from 30 to 50 years or more.
The longevity of mineral wool insulation is influenced by various factors, including:
Quality of Installation: Proper installation is essential for maximizing the lifespan of mineral wool insulation. It should be installed by professionals who follow manufacturer guidelines and industry best practices. Adequate coverage, proper sealing of joints, and correctly placed vapor barriers can help ensure the insulation’s effectiveness and longevity.
Maintenance: Regular maintenance and inspections are important to monitor the condition of mineral wool insulation. Periodic checks for signs of damage, water infiltration, or pest activity should be conducted. Any issues should be addressed promptly to prevent further damage and maintain the insulation’s integrity.
Climate Conditions: The climate in which mineral wool insulation is installed can impact its lifespan. Extreme temperature fluctuations, high humidity, and exposure to moisture can potentially accelerate the degradation of mineral wool insulation. Inspections and additional protective measures may be necessary in regions with severe weather conditions.
Mineral wool insulation is known for its resistance to pests, such as rodents and insects, which can help extend its lifespan. However, it is still important to conduct regular inspections for any signs of pest activity or damage that may compromise the insulation’s effectiveness.
Regular maintenance, including proper ventilation and moisture control, is essential for maximizing the lifespan of mineral wool insulation. Addressing any issues promptly and conducting periodic inspections can help ensure the insulation continues to perform optimally over time.
If mineral wool insulation has reached the end of its lifespan or has suffered significant damage, it may require replacement. Consulting with insulation professionals can help determine the best course of action based on the condition of your insulation and the specific requirements of your building.
Mineral wool insulation offers numerous benefits, such as its fire resistance, soundproofing capabilities, and thermal insulation properties. By properly installing and maintaining mineral wool insulation, you can enjoy its long-lasting performance and energy-saving benefits for many years.
Insulation Lifespan in Different Climate Conditions
The lifespan of insulation can vary depending on the climate conditions in which it is installed. Different weather patterns, temperature fluctuations, and levels of moisture can impact the durability and effectiveness of insulation materials. Understanding how climate conditions can affect insulation lifespan is crucial for making informed decisions about maintenance, replacement, or upgrades. Let’s explore how insulation lifespan can be influenced by different climate conditions:
Extreme Temperature Fluctuations: In regions with drastic temperature changes between seasons, such as cold winters and hot summers, insulation materials may experience expansion and contraction. This constant movement can lead to wear and tear, causing insulation to become less effective over time. It is important to choose insulation materials that can withstand these temperature fluctuations and to regularly inspect for any signs of damage or decreased performance.
High Humidity: Moisture is a common adversary for insulation, especially in areas with high humidity levels. Excessive moisture can lead to the growth of mold and mildew, which can compromise the integrity of insulation materials. Proper moisture control measures, such as ventilation and adequate vapor barriers, are essential in humid climates to prevent moisture-related damage and extend the lifespan of insulation.
Exposure to Moisture: Insulation installed in areas prone to water leaks, flooding, or high levels of precipitation may be at a higher risk of moisture damage. Continuous exposure to moisture can lead to the deterioration of insulation, reducing its thermal resistance properties and potentially causing mold growth. Inspections should be conducted regularly in these areas to detect and address any wetness or water damage promptly.
Harsh Weather Conditions: Insulation in regions prone to severe weather conditions, such as hurricanes or heavy snowfall, may experience increased wear and tear. Strong winds, heavy rains, or snow loads can put stress on insulation materials, potentially leading to damage or decreased effectiveness. Inspections should be conducted following severe weather events to identify any signs of damage and ensure proper functioning of the insulation.
Coastal Areas: Coastal regions often have a higher concentration of salt in the air, which can accelerate the corrosion process for certain insulation materials, such as metallic substances or fasteners. Insulation in coastal areas may require more frequent inspections and maintenance to detect any signs of corrosion and extend the lifespan of the materials used.
Insulation in different climate conditions may require tailored maintenance and care to maximize its lifespan and effectiveness. Regular inspections by professionals can help identify any signs of damage, moisture intrusion, or decreased performance. Addressing issues promptly and taking preventive measures, such as improving ventilation or adding insulation cladding, can help mitigate the negative impact of climate conditions on insulation lifespan.
It’s important to consult with insulation experts who are familiar with the specific climate conditions of your region and can provide guidance on selecting the most suitable insulation materials and maintenance practices for your building. By considering the impact of climate conditions and implementing appropriate measures, you can optimize the lifespan and performance of insulation in any environment.
Signs of Deteriorating Insulation
Insulation plays a critical role in maintaining energy efficiency, comfort, and indoor air quality in buildings. However, over time, insulation can deteriorate and lose its effectiveness, potentially leading to increased energy consumption, decreased thermal comfort, and other issues. Recognizing the signs of deteriorating insulation is crucial for taking timely action and ensuring the optimal performance of your insulation. Here are some common signs to look out for:
- Increased Energy Bills: One of the first indicators of deteriorating insulation is a sudden increase in energy bills. If your heating or cooling costs have significantly risen, it may be a sign that your insulation is no longer providing the necessary thermal resistance to maintain an efficient indoor temperature.
- Temperature Fluctuations: Inadequate insulation may result in noticeable temperature fluctuations within your building. You may feel drafts or hot and cold spots, indicating that the insulation is no longer effectively regulating the indoor temperature.
- Mold or Mildew Growth: Moisture damage can compromise insulation and lead to the growth of mold or mildew. If you notice any visible signs of mold or mildew on or near the insulation, it is essential to address the issue promptly to prevent further damage and potential health hazards.
- Visible Damage: Insulation materials may show visible signs of wear and tear, such as crumbling, disintegration, or compression. Cracked or peeling insulation can also indicate deterioration. Additionally, if you notice gaps or holes in the insulation, it may have been damaged by pests or other factors.
- Pest Infestation: Insulation can attract pests like rodents or insects, which may damage the material or build nests within it. Signs of pest activity, such as droppings or chewed insulation, may indicate the need for inspection and potential insulation replacement.
- Unpleasant Odors: Deteriorating insulation can emit unpleasant odors, especially if there is mold growth or pest activity. If you notice musty or foul smells in your building, it’s essential to investigate the source and address any insulation-related issues.
If you observe any of these signs, it is recommended to consult with insulation professionals for a thorough evaluation of your insulation’s condition. They can assess the extent of the damage, determine the underlying causes, and recommend the appropriate steps to rectify the situation. In some cases, insulation repair or replacement may be necessary to restore optimal performance.
Regular inspections and maintenance can help prevent insulation deterioration and identify any issues before they escalate. Timely repairs, moisture control measures, and taking proactive steps to address insulation-related concerns can help prolong the lifespan and functionality of your insulation, as well as enhance indoor comfort and energy efficiency in your building.
Read more: How Long Does Attic Insulation Last
Maintaining and Extending the Lifespan of Insulation
Maintaining and caring for your insulation is crucial for ensuring its longevity and optimal performance. With proper maintenance, you can extend the lifespan of your insulation, maximize energy efficiency, and prolong the comfort of your building. Here are some key tips for maintaining and extending the lifespan of insulation:
- Regular Inspections: Conduct regular inspections of your insulation to identify any signs of damage, wear and tear, or pest infestations. Inspections should include checking for visible damage, moisture intrusion, mold growth, or areas with compromised thermal resistance. Early detection of issues allows for timely repairs or replacements.
- Prompt Repairs: Address any issues or damage promptly to prevent further deterioration. If you notice damaged areas, gaps, or insulation compression, make necessary repairs to restore the insulation’s effectiveness. Repairing small areas of damage can help prevent them from spreading and impacting the overall performance of the insulation.
- Moisture Control: Moisture is one of the main contributors to insulation degradation. Ensure that your building has proper moisture control measures in place, such as adequate ventilation, vapor barriers, and addressing any sources of leaks or condensation. Moisture management will help prevent mold growth, rotting, and other forms of water damage to the insulation.
- Sealing Air Leaks: Insulation is most effective when there are minimal air leaks in the building envelope. Sealing air leaks, such as gaps around windows, doors, and electrical outlets, can prevent heat transfer and improve overall energy efficiency. Properly sealed and insulated spaces help maintain a consistent and comfortable indoor temperature.
- Proper Ventilation: Good ventilation plays a crucial role in maintaining insulation performance. Adequate airflow helps prevent moisture buildup and removes excess heat during hot weather. It’s important to keep vents clear and unobstructed to allow for proper airflow throughout the building.
- Regular Pest Control: Pests, such as rodents and insects, can damage insulation and compromise its thermal resistance. Implementing regular pest control measures can help prevent infestations and protect your insulation. Seal any openings or cracks that pests can use to access the insulation, and promptly address any signs of pest activity.
- Professional Maintenance: Consider engaging insulation professionals for routine maintenance and inspections. They have the expertise to identify any hidden issues, conduct comprehensive assessments, and provide recommendations for maintaining and optimizing insulation performance.
By following these maintenance practices, you can significantly extend the lifespan of your insulation and ensure its long-term effectiveness. Regular inspections, prompt repairs, moisture control, proper ventilation, sealing air leaks, pest control measures, and seeking professional assistance will contribute to maintaining the insulation’s functionality and maximizing energy efficiency in your building.
Remember that each type of insulation may have unique maintenance requirements, so consult with insulation experts and refer to manufacturer guidelines for specific care instructions. By investing time and effort into maintaining your insulation, you can enjoy its benefits for many years while saving on energy costs and creating a comfortable living or working environment.
Conclusion
Insulation is a vital component of any building, providing thermal resistance and contributing to energy efficiency and comfort. Understanding the factors that affect insulation lifespan, recognizing signs of deterioration, and implementing proper maintenance practices are essential for optimizing its performance and extending its lifespan.
We explored various factors that can impact the lifespan of insulation, such as the type of insulation material, installation quality, climate conditions, and maintenance. Each type of insulation, whether it be fiberglass, foam, cellulose, or mineral wool, has its own unique characteristics and expected lifespan. Fiberglass insulation is known for its durability, while foam insulation may have a relatively shorter lifespan. Cellulose insulation offers a reasonable lifespan, and mineral wool insulation is known for its long-term durability.
Climate conditions, such as extreme temperature fluctuations, high humidity, and exposure to moisture, can contribute to the deterioration of insulation materials. Regular inspections, prompt repairs, moisture control measures, and proper ventilation are key to preventing damage and extending the lifespan of insulation.
Recognizing the signs of deteriorating insulation, such as increased energy bills, temperature fluctuations, mold growth, visible damage, pest infestation, and unpleasant odors, is vital. Timely action and addressing these issues can help maintain insulation effectiveness and prevent further damage to your building.
Regular maintenance, professional inspections, sealing air leaks, and practicing proper moisture control and ventilation are important steps in maintaining insulation and maximizing its lifespan. By implementing these measures, you can enhance energy efficiency, reduce utility bills, and create a comfortable living or working environment.
In conclusion, maintaining and extending the lifespan of insulation requires proactive attention and regular maintenance. By understanding the factors that affect insulation lifespan, being vigilant to signs of deterioration, and following proper care techniques, you can ensure that your insulation continues to perform optimally for years to come. Not only will you benefit from energy savings and improved comfort, but you will also contribute to a more sustainable and environmentally friendly building.
Frequently Asked Questions about How Long Does Insulation Last
Was this page helpful?
At Storables.com, we guarantee accurate and reliable information. Our content, validated by Expert Board Contributors, is crafted following stringent Editorial Policies. We're committed to providing you with well-researched, expert-backed insights for all your informational needs.
0 thoughts on “How Long Does Insulation Last”