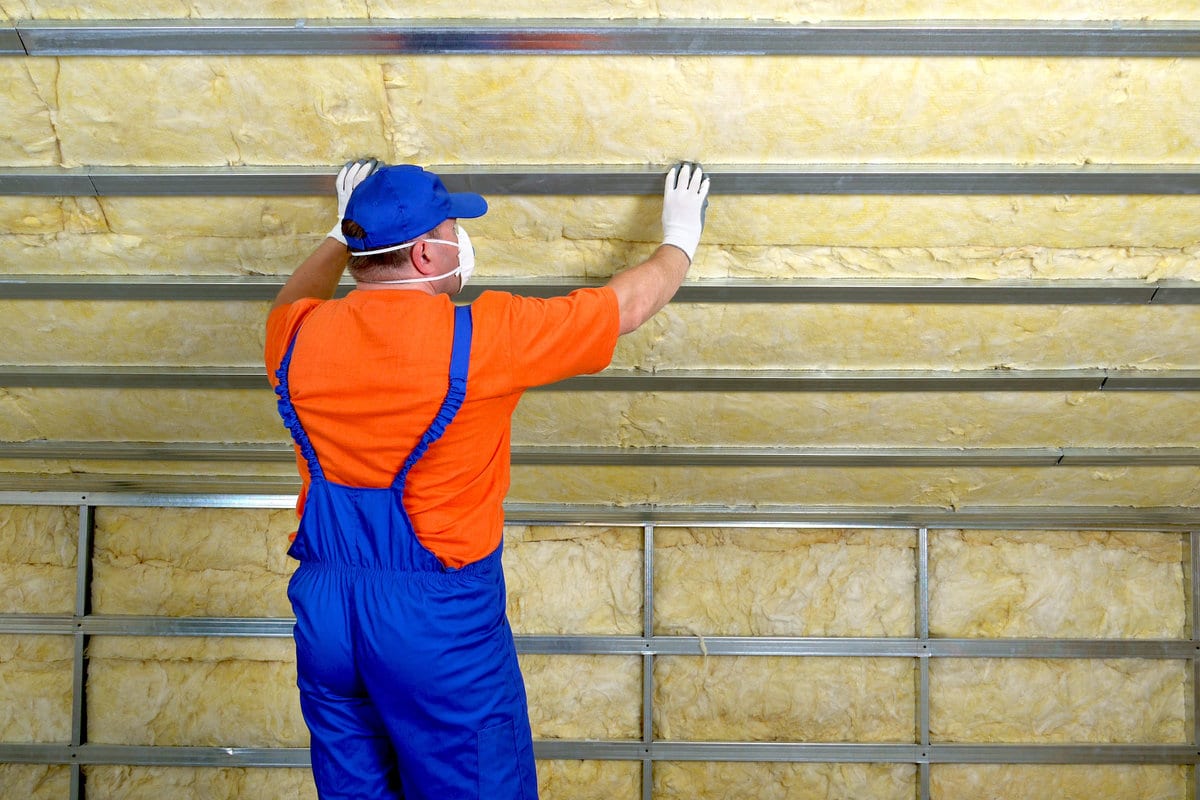
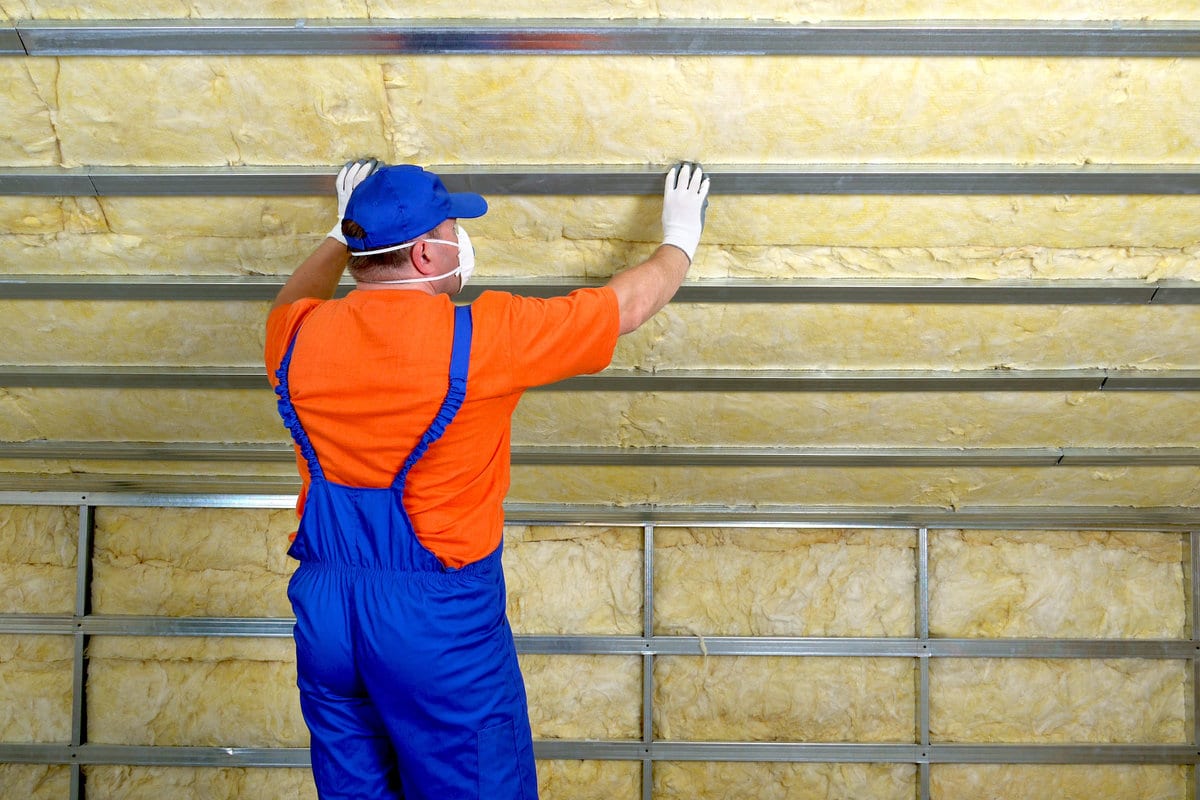
Articles
What Is Mineral Wool Insulation
Modified: December 7, 2023
Discover the benefits and uses of mineral wool insulation in our latest articles. Gain insights on its thermal properties and eco-friendly nature, making it an ideal choice for energy-efficient homes.
(Many of the links in this article redirect to a specific reviewed product. Your purchase of these products through affiliate links helps to generate commission for Storables.com, at no extra cost. Learn more)
Introduction
Welcome to the world of mineral wool insulation, a versatile and highly effective insulation material that has gained popularity in the construction industry. Whether you are building a new home or looking to improve the energy efficiency of your existing property, mineral wool insulation may be a great solution for you.
Mineral wool insulation is a type of insulation material that is made from fibers derived from minerals such as basalt, rock, and slag. It is known for its excellent thermal and acoustic insulation properties, as well as its fire resistance capabilities. This makes it a preferred choice for both residential and commercial applications.
In this article, we will explore the ins and outs of mineral wool insulation, including its composition, manufacturing process, types, advantages, and disadvantages. We will also discuss its common uses, installation process, maintenance requirements, and how it compares to other types of insulation on the market.
So, whether you are a homeowner, contractor, or simply curious about insulation options, let’s dive into the world of mineral wool insulation and discover why it is gaining recognition as a superior choice for thermal and acoustic insulation needs.
Key Takeaways:
- Mineral wool insulation offers exceptional fire resistance, sound absorption, and durability, making it a superior choice for energy-efficient and safe buildings in residential, commercial, and industrial settings.
- While mineral wool insulation provides excellent thermal and acoustic insulation, it may come with higher initial costs, heavier weight, and potential skin irritation, requiring careful consideration and proper maintenance for optimal performance.
Read more: What Is Mineral Glass
Definition of Mineral Wool Insulation
Mineral wool insulation, also known as rock wool or stone wool insulation, is a type of thermal and acoustic insulation material made from natural minerals like basalt, rock, and slag. It is manufactured by melting these minerals at high temperatures and then spinning or blowing the molten material into fibers. These fibers are then compressed and bonded together to create a dense and durable insulation product.
The resulting mineral wool insulation is known for its exceptional thermal performance, sound absorption capabilities, and fire resistance. It is commonly used in residential, commercial, and industrial buildings to improve energy efficiency, enhance indoor comfort, and provide acoustic insulation.
One of the key advantages of mineral wool insulation is its high melting point, which allows it to withstand extremely high temperatures without compromising its structural integrity. This makes it an ideal choice for applications where fire safety is a top priority, such as in fire-rated walls, roofs, and HVAC ducts.
Mineral wool insulation is available in various forms, including batts, blankets, boards, and loose-fill. It can be installed in walls, ceilings, floors, and attics to minimize heat transfer, reduce noise transmission, and create a more comfortable living or working environment.
Additionally, mineral wool insulation is non-combustible and does not release toxic gases when exposed to fire. This property makes it a safer option compared to other insulation materials that are more prone to combustion, such as fiberglass.
Overall, mineral wool insulation provides an effective and reliable solution for thermal and acoustic insulation needs in buildings. Its excellent fire resistance, sound absorption capabilities, and energy-saving properties make it a popular choice among architects, builders, and homeowners across the globe.
How Mineral Wool Insulation is Made
Mineral wool insulation is made through a complex manufacturing process that involves the melting, spinning, and bonding of natural minerals. Here is a step-by-step breakdown of how mineral wool insulation is made:
- Raw Materials: The production process begins with the collection of raw materials, which typically include basalt rock, limestone, and slag. These minerals are chosen for their high melting points and desirable thermal and acoustic properties.
- Melting: The raw materials are heated in a furnace at temperatures of around 1500-1700 degrees Celsius until they liquefy into molten form. This molten material is then transferred to the next stage of the process.
- Spinning or Blowing: Once in a molten state, the material is either spun or blown into fine fibers using a spinning or blowing mechanism. This process creates long, thin strands of mineral wool fibers.
- Binding: The fibers are then collected and compressed to form a mat or blanket. To ensure cohesion and stability, a binding agent is added to the fibers during the compression process. This binding agent can be an organic or inorganic substance, such as a resin or mineral-based binder.
- Curing: The compressed mat or blanket is then cured or hardened through a heating process. This further strengthens the material and promotes the formation of strong bonds between the fibers.
- Cutting and Shaping: Once cured, the mineral wool insulation is cut and shaped into the desired form, such as batts, blankets, boards, or loose-fill. These different forms allow for easy installation in a variety of applications.
- Packaging: The final step in the manufacturing process involves packaging the mineral wool insulation products for distribution and sale. The insulation products are typically packaged in rolls, bags, or bundles, ready for transportation to construction sites or retail outlets.
It is important to note that the manufacturing process of mineral wool insulation may vary slightly depending on the specific manufacturer and the intended application of the insulation. However, the overall process remains consistent in terms of melting the raw materials, forming fibers, bonding them together, and shaping the final product.
By understanding the intricate process behind the manufacturing of mineral wool insulation, we can appreciate the precision and craftsmanship involved in creating this highly effective and versatile insulation material.
Types of Mineral Wool Insulation
Mineral wool insulation is available in different types, each designed to cater to specific insulation needs and applications. Here are the most common types of mineral wool insulation:
- Batts and Blankets: This is the most commonly used form of mineral wool insulation. Batts and blankets consist of long, flexible fibers that are packed together tightly to form a dense and uniform product. They are available in various thicknesses and widths, making it easy to install between wall studs, attic joists, and ceiling rafters.
- Boards: Mineral wool insulation boards are rigid panels that provide excellent thermal and acoustic insulation. They are commonly used for insulating walls, roofs, and floors, where a more rigid and firm material is required. Mineral wool insulation boards can be easily cut and shaped to fit specific spaces and provide consistent insulation performance.
- Loose-Fill: Loose-fill mineral wool insulation consists of loose fibers that can be blown or poured into cavities, attics, or other hard-to-reach areas. It is an ideal choice for retrofitting or filling irregularly shaped spaces. Loose-fill mineral wool insulation provides excellent coverage and can conform to any shape, offering effective thermal and acoustic insulation.
- Pipe and Boiler Insulation: Mineral wool insulation is also available in the form of pre-formed cylindrical sections or sheets that are specifically designed for insulating pipes and boilers. These insulation products provide excellent thermal conductivity reduction, minimizing heat loss and energy consumption in plumbing and heating systems.
It is worth mentioning that mineral wool insulation comes in different densities, allowing for different levels of thermal and acoustic insulation. Higher density mineral wool insulation provides better thermal performance and sound absorption, making it suitable for applications where superior insulation properties are required, such as in commercial or industrial buildings.
Additionally, mineral wool insulation is available in various facing materials, such as foil or paper, which can enhance its vapor resistance and act as a radiant barrier. These facings help to prevent moisture buildup and improve the insulation’s overall performance.
When selecting the type of mineral wool insulation for your project, it is crucial to consider factors such as the desired insulation level, the specific application, and the building code requirements. Consulting with a professional insulation contractor can help you make an informed decision and ensure optimal insulation performance.
Advantages of Mineral Wool Insulation
Mineral wool insulation offers several advantages that make it a popular choice for both residential and commercial applications. Here are some of the key advantages of using mineral wool insulation:
- Excellent Thermal Performance: One of the primary advantages of mineral wool insulation is its exceptional thermal insulation properties. It helps to reduce heat transfer, keeping the interior spaces cooler in summer and warmer in winter. This can lead to significant energy savings and increased comfort levels in buildings.
- Superior Sound Absorption: Mineral wool insulation is known for its high sound absorption capabilities. It effectively reduces airborne noise transmission and can create a quieter and more peaceful indoor environment. This makes it an excellent choice for buildings located in noisy areas or those with specific acoustic requirements, such as studios, theaters, or office spaces.
- Fire Resistance: Mineral wool insulation is highly fire-resistant, with a high melting point that allows it to withstand extreme temperatures without igniting or spreading flames. It acts as a barrier, delaying the spread of fire and providing occupants with valuable time to evacuate a building. This makes it an ideal choice for fire-rated walls, ceilings, and HVAC systems.
- Moisture Resistance: Mineral wool insulation is moisture-resistant and does not readily absorb water. This property helps to prevent the growth of mold, mildew, and rot within the insulation material. It also maintains its insulation performance even in humid environments, ensuring long-term effectiveness and durability.
- Chemically Inert: Mineral wool insulation is chemically inert, meaning it does not react with common building materials or emit harmful gases. This makes it a safe and environmentally friendly choice for insulation. It does not release volatile organic compounds (VOCs), making it suitable for improving indoor air quality.
- Durable and Long-Lasting: Mineral wool insulation is highly durable and maintains its performance for the lifetime of the building. It does not deteriorate over time, shrink, or settle, ensuring long-lasting insulation value and energy efficiency. This can result in significant cost savings over the lifespan of the building.
- Easy Installation: Mineral wool insulation is relatively easy to install, whether it is in the form of batts, blankets, boards, or loose-fill. It can be cut, shaped, and fitted into various spaces without much effort. This makes it a popular choice for DIY projects or professional insulation installation.
Overall, mineral wool insulation offers a combination of thermal efficiency, sound absorption, fire resistance, durability, and eco-friendliness. Its numerous advantages make it a reliable and effective choice for enhancing the energy efficiency, comfort, and safety of buildings.
Read more: Why Is Glass Not A Mineral
Disadvantages of Mineral Wool Insulation
While mineral wool insulation offers many benefits, it is important to consider its potential disadvantages as well. Here are some of the main drawbacks associated with mineral wool insulation:
- Higher Cost: Compared to other insulation materials, mineral wool insulation tends to be more expensive. The manufacturing process involved in producing mineral wool insulation requires specialized equipment and techniques, which contribute to higher production costs. This can make it less affordable for some budget-conscious homeowners or construction projects.
- Heavier and Bulkier: Mineral wool insulation is relatively denser and heavier compared to other types of insulation, such as fiberglass or cellulose. This can make it more difficult to handle and install, especially in tight or hard-to-reach spaces. The heavier weight may also require additional structural support in ceilings or walls.
- Potential for Skin Irritation: The fine fibers in mineral wool insulation can cause skin irritation and itching if they come into direct contact with the skin. It is important to wear protective clothing and gear, such as gloves and masks, during the installation process to minimize the risk of irritation or allergic reactions.
- Limited Availability: In some areas, mineral wool insulation may not be as readily available compared to other types of insulation. This could be due to limited distribution or a lack of local suppliers. Limited availability can increase costs and lead to longer wait times for delivery.
- Lower R-Value per Inch: The R-value measures the thermal resistance of insulation, with higher values indicating better insulation performance. Compared to some other insulation materials, mineral wool insulation may have a slightly lower R-value per inch of thickness. This means that a thicker layer of mineral wool insulation may be required to achieve the same level of insulation effectiveness.
- Volatile Organic Compound (VOC) Emissions: While mineral wool insulation itself does not emit VOCs, some binding agents or facing materials used in the production of mineral wool products may contain small amounts of VOCs. It is important to select mineral wool insulation products that have low VOC content or are certified as low-emission to ensure better indoor air quality.
Despite these potential disadvantages, mineral wool insulation remains a popular and effective choice for thermal and acoustic insulation in many applications. It is always recommended to weigh the pros and cons and consult with a professional to determine the best insulation material for your specific needs and budget.
When installing mineral wool insulation, be sure to wear protective clothing, gloves, and a mask to avoid irritation from the fibers. Proper ventilation is also important during installation to minimize exposure to airborne particles.
Common Uses of Mineral Wool Insulation
Mineral wool insulation is a versatile material that finds application in various residential, commercial, and industrial settings. Here are some of the common uses of mineral wool insulation:
- Residential Buildings: Mineral wool insulation is widely used in residential buildings for thermal insulation. It is commonly installed in walls, attics, roofs, and floors to minimize heat transfer, improve energy efficiency, and enhance indoor comfort. It helps to keep homes cooler during hot summer months and retains warmth during colder seasons.
- Commercial Buildings: Mineral wool insulation is extensively used in commercial buildings, including offices, schools, hospitals, and retail spaces. It provides effective thermal insulation, reduces energy consumption, and creates a comfortable working environment. Its sound absorption properties also help to minimize noise transmission, creating a quieter and more conducive atmosphere in commercial spaces.
- Industrial Applications: Mineral wool insulation is commonly used in industrial applications where high-performance thermal and acoustic insulation is required. It can be found in factories, manufacturing facilities, warehouses, and power plants. In industrial settings, it helps to regulate temperature, reduce noise from machinery and equipment, and improve overall energy efficiency.
- HVAC Systems: Mineral wool insulation is commonly used to insulate HVAC (Heating, Ventilation, and Air Conditioning) ductwork, pipes, and boilers. It helps to prevent heat loss, maintain optimal temperatures, and improve the efficiency of HVAC systems. Insulating these components can result in energy savings and more efficient heating and cooling distribution.
- Fire-Rated Applications: Due to its exceptional fire resistance, mineral wool insulation is frequently used in fire-rated construction applications. It is installed in fire walls, fire doors, and other fire barrier systems to effectively restrict the spread of flames and provide passive fire protection. Mineral wool insulation acts as a barrier, helping to delay the spread of fire and providing valuable time for evacuation.
- Acoustic Treatments: Mineral wool insulation is an excellent choice for improving sound insulation in buildings. It is used in theaters, music studios, conference rooms, and other spaces requiring optimal acoustic performance. Mineral wool’s fibrous structure helps to absorb sound waves, reducing echo and improving the overall quality of sound within a space.
These are just a few examples of the common uses of mineral wool insulation. It is a versatile and adaptable insulation material that can be tailored to suit various applications, providing excellent thermal efficiency, sound absorption, fire resistance, and energy-saving benefits.
Installation Process of Mineral Wool Insulation
The installation process of mineral wool insulation may vary depending on the specific application and the form of insulation being used. Here is a general overview of the installation process:
- Prepare the Work Area: Before installation, ensure that the work area is clean, dry, and free from any debris. Clear any obstacles and ensure that the surfaces to be insulated are smooth and in good condition.
- Measure and Cut: Measure the dimensions of the space that needs to be insulated and make precise cuts to the mineral wool insulation material to fit the area. Use a sharp utility knife or insulation cutter to cut the material with precision.
- Install Batts or Blankets: If using batts or blankets, align the insulation material between wall studs, roof rafters, or floor joists. Gently press the mineral wool insulation into place, ensuring a snug fit. Use staples or insulation supports to hold the insulation in place if necessary.
- Install Mineral Wool Boards: If using boards, anchor them to the walls, ceilings, or floors using appropriate fasteners, following the manufacturer’s instructions. Ensure that seams between boards are properly aligned and sealed to prevent thermal bridging.
- Install Loose-Fill Insulation: If using loose-fill mineral wool insulation, use a blower machine or pour the insulation material into the designated spaces, such as attics or wall cavities. Ensure that the insulation is evenly distributed and fills all gaps and voids. Use a rake or similar tool to level and smooth the insulation if needed.
- Seal Air Gaps: Inspect the installation for any gaps or air leakages, especially around windows, doors, electrical outlets, and penetrations. Use weatherstripping, caulk, or foam sealants to seal any gaps and air leaks, ensuring an airtight and energy-efficient insulation envelope.
- Adhere to Safety Precautions: When working with mineral wool insulation, it is essential to follow safety precautions. Wear protective clothing, including gloves, goggles, and a mask, to prevent skin and respiratory irritation from the fine fibers. Dispose of any waste material in accordance with local regulations.
It is important to note that the installation process for mineral wool insulation may require additional steps or considerations based on the specific application and building requirements. It is advisable to consult the manufacturer’s guidelines and, if needed, seek assistance from a professional insulation contractor to ensure proper installation and optimal insulation performance.
Proper Maintenance of Mineral Wool Insulation
While mineral wool insulation is known for its durability and long-lasting performance, proper maintenance can enhance its effectiveness and longevity. Here are some essential tips for maintaining mineral wool insulation:
- Regular Inspection: Conduct regular inspections of your mineral wool insulation to check for any signs of damage or deterioration. Look for any moisture intrusion, sagging, compression, or displacement of the insulation material. Address any issues promptly to prevent further damage.
- Ensure Adequate Ventilation: Proper ventilation is essential to prevent moisture buildup within the insulation. Make sure that your building has proper airflow in areas where mineral wool insulation is installed, such as attics or crawlspaces. Inspect ventilation systems, exhaust fans, and air vents to ensure they are functioning correctly.
- Seal Air Leaks: Inspect and seal any air leaks around windows, doors, electrical outlets, and other penetrations. Air leaks can compromise the insulation’s thermal performance and lead to energy loss. Use weatherstripping, caulk, or foam sealants to seal gaps and cracks and improve energy efficiency.
- Prevent Moisture Intrusion: Moisture can negatively impact the performance of mineral wool insulation and lead to mold growth or damage. Ensure that your building’s envelope is properly sealed and waterproofed. Repair any leaks or water damage immediately to prevent moisture from reaching the insulation.
- Address Pest Issues: Inspect your mineral wool insulation for any signs of pest infestation, such as rodents or insects. These pests can damage the insulation by nesting or burrowing through it. Take appropriate pest control measures to prevent further damage and maintain the integrity of the insulation.
- Keep Insulation Dry: Mineral wool insulation should be kept dry at all times. If you discover any moisture intrusion, identify and address the source promptly. In case of accidental water exposure or flooding, ensure that the insulation is thoroughly dried before continuing to use it. Wet or damp mineral wool insulation can lose its thermal and acoustic properties.
- Professional Maintenance: Consider scheduling periodic professional inspections and maintenance for your mineral wool insulation. A trained insulation professional can assess the condition of the insulation, identify any potential issues, and recommend appropriate maintenance or repairs.
By following these maintenance tips, you can ensure that your mineral wool insulation remains in optimal condition and continues to provide effective thermal and acoustic insulation for your building.
Read more: What Mineral Is Used For Most Sandpaper
Comparison with Other Types of Insulation
When it comes to insulation, there are various types available, each with its own characteristics and benefits. Here is a comparison of mineral wool insulation with other commonly used types of insulation:
- Fiberglass Insulation: Fiberglass insulation is another popular choice for thermal and acoustic insulation. It is made from glass fibers and is available in batts, blankets, or loose-fill form. Both mineral wool and fiberglass insulation offer similar thermal performance and sound absorption capabilities. However, mineral wool insulation has a higher melting point, making it more fire-resistant than fiberglass insulation.
- Cellulose Insulation: Cellulose insulation is made from recycled paper fibers treated with fire-retardant chemicals. It is available in loose-fill form and is often used in walls and attics. Mineral wool insulation provides better fire resistance and moisture resistance compared to cellulose insulation. Cellulose insulation may settle over time, reducing its effectiveness, whereas mineral wool insulation maintains its performance over the long term.
- Spray Foam Insulation: Spray foam insulation is a high-density insulation material that is applied as a liquid and expands to fill voids and cavities. It provides excellent air sealing and thermal insulation properties. While spray foam insulation offers superior air sealing capabilities, mineral wool insulation is more cost-effective and provides better sound absorption capabilities.
- Polystyrene Insulation: Polystyrene insulation, also known as EPS or XPS insulation, is a rigid foam material that offers good thermal insulation properties. Mineral wool insulation provides better sound absorption and fire resistance compared to polystyrene insulation. Polystyrene insulation boards are lightweight and easy to handle, while mineral wool insulation boards are denser and may require additional support.
Overall, mineral wool insulation offers a balance of thermal performance, sound absorption, fire resistance, and durability. It is an ideal choice for applications where fire safety, moisture resistance, and acoustics are important considerations. However, the choice of insulation will depend on various factors, including budget, specific insulation needs, building codes, and personal preferences.
It is recommended to consult with an insulation professional to assess your building’s requirements and determine the most suitable insulation material for your project.
Conclusion
Mineral wool insulation is a highly effective and versatile insulation material that offers numerous benefits for residential, commercial, and industrial applications. Its excellent thermal performance, sound absorption capabilities, fire resistance, and durability make it a preferred choice for improving energy efficiency, enhancing indoor comfort, and ensuring the safety of buildings.
Throughout this article, we have explored the various aspects of mineral wool insulation, including its definition, manufacturing process, types, advantages, and disadvantages. We have also discussed its common uses, installation process, proper maintenance, and compared it to other types of insulation.
Mineral wool insulation stands out for its exceptional fire resistance, making it an ideal choice for fire-rated applications. Its ability to reduce thermal bridging, minimize noise transmission, and withstand high temperatures contributes to its popularity in the construction industry.
While mineral wool insulation offers numerous benefits, it is essential to consider the potential drawbacks such as higher initial cost, heavier weight, and the need for protective gear during installation due to possible skin irritation.
Proper maintenance practices, including regular inspections, adequate ventilation, sealing air leaks, and addressing moisture issues, are crucial for maximizing the longevity and performance of mineral wool insulation.
When comparing mineral wool insulation with other types of insulation, it is important to consider factors such as fire resistance, sound absorption, thermal properties, moisture resistance, and cost. Each insulation type has its own strengths and weaknesses, and the choice ultimately depends on the specific requirements, building codes, and budget.
In conclusion, mineral wool insulation offers a reliable and high-performing solution for thermal and acoustic insulation needs. Its benefits make it a valuable investment for energy-efficient and comfortable buildings. By understanding its characteristics and proper installation and maintenance practices, you can harness the full potential of mineral wool insulation to create an environment that is well-insulated, safe, and conducive to optimal comfort.
Frequently Asked Questions about What Is Mineral Wool Insulation
Was this page helpful?
At Storables.com, we guarantee accurate and reliable information. Our content, validated by Expert Board Contributors, is crafted following stringent Editorial Policies. We're committed to providing you with well-researched, expert-backed insights for all your informational needs.
0 thoughts on “What Is Mineral Wool Insulation”