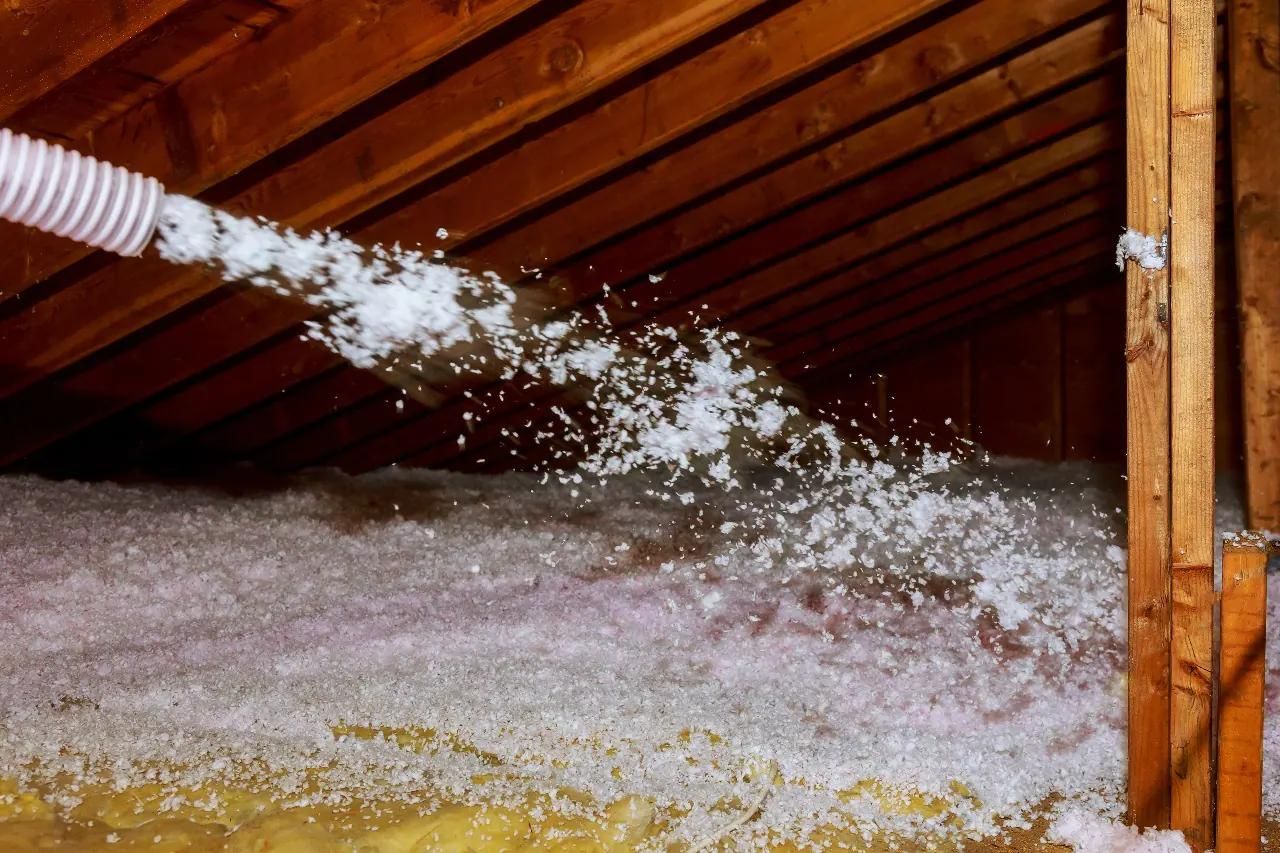
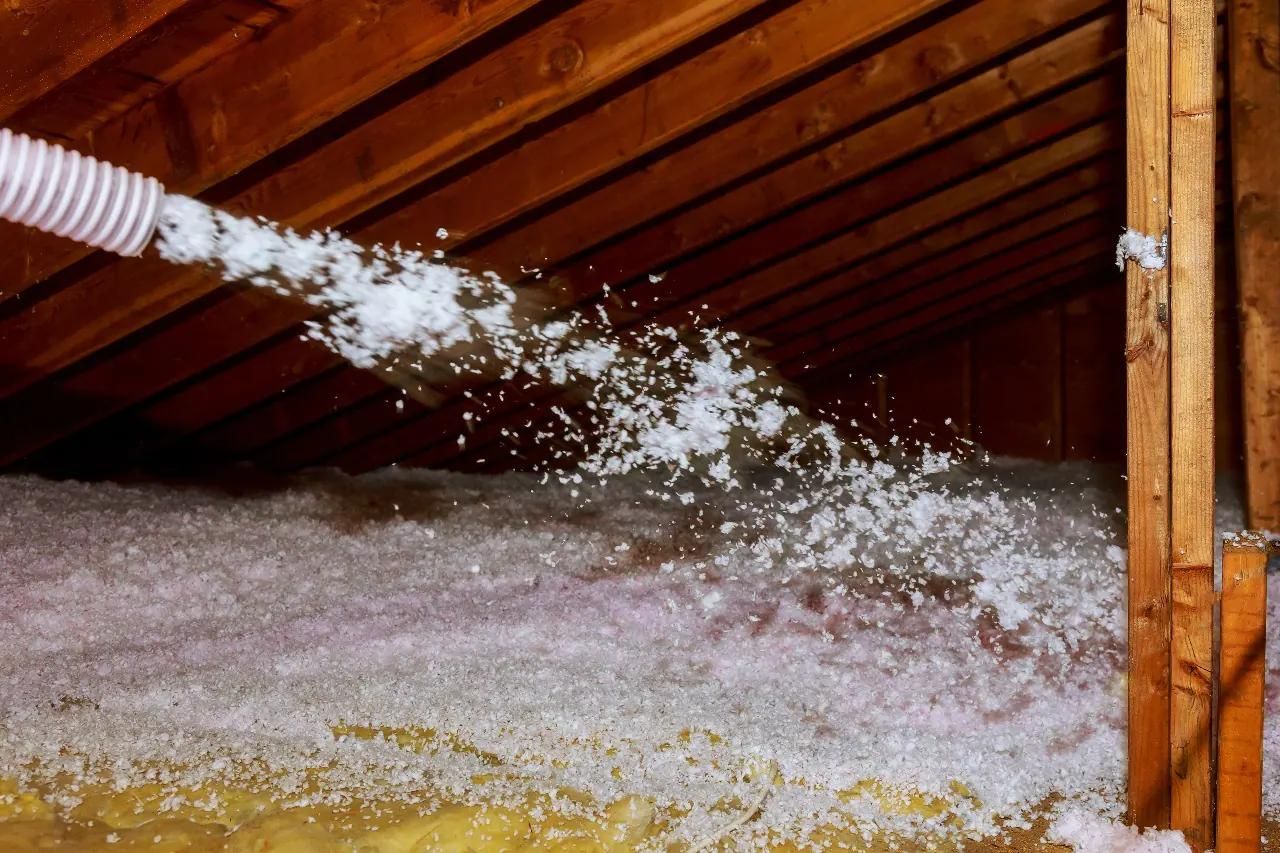
Articles
How Much Does Blow-In Insulation Cost
Modified: August 31, 2024
Get all the information you need about the cost of blow in insulation with our comprehensive articles, helping you make an informed decision.
(Many of the links in this article redirect to a specific reviewed product. Your purchase of these products through affiliate links helps to generate commission for Storables.com, at no extra cost. Learn more)
Introduction
Welcome to our comprehensive guide on blow-in insulation costs! If you’re considering insulating your home or building, blow-in insulation is an excellent option to consider due to its ability to enhance energy efficiency and reduce heating and cooling costs. In this article, we will delve into the details of blow-in insulation and provide you with key insights into the factors that affect its cost.
Blow-in insulation, also known as loose-fill insulation, involves the process of filling cavities, attics, and walls with small, loose particles of insulation material. The insulation material is blown into the designated areas using specialized equipment, allowing for a seamless and efficient installation process.
Now that you have a general understanding of blow-in insulation, let’s explore the factors that can influence the cost of this type of insulation. Understanding these factors will help you make an informed decision and ensure that you get the most value out of your investment.
Key Takeaways:
- The cost of blow-in insulation ranges from $1.50 to $3.50 per square foot, influenced by factors like insulation material, area size, labor costs, and additional components. Consider long-term energy savings and insulation performance when making a decision.
- DIY blow-in insulation may save on labor costs, but professional installation offers expertise, convenience, and potential warranties. Consider factors like energy savings, R-value, air sealing, and long-term maintenance for a well-informed decision.
Read more: How Much Does It Cost For Insulation
What is Blow-in Insulation?
Blow-in insulation, also known as loose-fill insulation, is a type of insulation material that is installed by blowing or spraying it into designated spaces, such as attics, walls, or crawl spaces. It consists of small, loose particles or fibers made from various insulating materials, such as fiberglass, cellulose, or mineral wool.
This method of insulation offers several advantages over traditional insulation methods. Firstly, blow-in insulation can fill small crevices and gaps, ensuring a more complete coverage and reducing the risk of heat transfer. It also provides excellent resistance to air infiltration, preventing drafts and improving energy efficiency.
Blow-in insulation is suitable for both new construction and retrofitting older homes or buildings. It can be installed in areas where it may be challenging to place other types of insulation, such as existing walls or hard-to-reach spots. The flexibility and ease of installation make blow-in insulation a popular choice for homeowners looking to improve their home’s energy efficiency and comfort.
The most common types of materials used in blow-in insulation are:
- Fiberglass: Made from fine glass fibers, fiberglass is known for its thermal insulation properties and fire resistance.
- Cellulose: Composed of recycled paper fibers treated with fire retardants, cellulose insulation is environmentally friendly and provides good thermal and sound insulation.
- Mineral wool: Made from mineral fibers, this type of insulation offers excellent fire resistance and sound absorption.
Before installing blow-in insulation, it is crucial to determine the appropriate R-value for your specific climate and location. The R-value measures the insulation’s resistance to heat flow. Higher R-values indicate better insulation. Consulting with an insulation professional can help you determine the optimal R-value for your area.
Now that you have a better understanding of blow-in insulation, let’s explore the various factors that can influence its cost.
Factors Affecting the Cost of Blow-in Insulation
The cost of blow-in insulation can vary based on several factors. Understanding these factors will help you estimate the overall cost and make informed decisions. Here are the key factors that can influence the cost of blow-in insulation:
- Insulation material: The type of insulation material used can significantly impact the cost. Fiberglass insulation is generally more affordable compared to cellulose or mineral wool, which may have slightly higher costs due to the materials used in their production.
- Area to be insulated: The size of the area to be insulated is a crucial factor in determining the overall cost. Larger areas will require more insulation material and labor, which can increase the cost.
- Labor costs: The cost of professional installation will depend on labor rates in your area. Labor costs can vary based on the complexity of the installation, accessibility of the space, and regional factors.
- Insulation depth or thickness: The required insulation depth or thickness can influence the cost. The thicker the insulation layer, the more material will be needed, which can increase the overall cost.
- Access and ease of installation: If the installation area is easily accessible, the installation process may be quicker and more straightforward, resulting in lower labor costs. However, if the installation requires additional effort or modifications, such as removing existing insulation, the cost may increase.
- Additional components: In some cases, additional components may be needed to ensure proper insulation, such as vapor barriers, insulation baffles, or air sealing. These additional materials can add to the overall cost of the insulation project.
- Location: The cost of blow-in insulation can also vary based on your geographical location. Factors such as market demand, cost of living, and availability of insulation contractors can influence the overall pricing in different regions.
Keep in mind that these factors interact with each other, and the final cost will depend on the specific requirements of your project. To get an accurate estimate, it is recommended to consult with experienced insulation professionals who can assess your needs and provide a detailed cost breakdown.
Now that we’ve explored the factors that can affect the cost of blow-in insulation, let’s move on to discussing the average cost you can expect to incur.
Average Cost of Blow-in Insulation
The cost of blow-in insulation can vary depending on the factors mentioned earlier. However, to provide you with a general idea, we will outline the average cost range for blow-in insulation installation.
On average, the cost of blow-in insulation ranges from $1.50 to $3.50 per square foot. This estimate includes both the material and labor costs. Keep in mind that this is a rough estimate and the actual cost can be higher or lower depending on your specific circumstances.
The total cost of blow-in insulation will depend on factors such as the type of insulation material chosen, the size of the area to be insulated, insulation depth, labor costs in your area, and any additional components required.
For example, fiberglass blow-in insulation is generally more affordable, with an average cost range of $1.50 to $2.50 per square foot. Cellulose insulation tends to be slightly higher in cost, ranging from $2.00 to $3.00 per square foot. Mineral wool, on the other hand, may have a higher cost range, typically ranging from $3.00 to $3.50 per square foot.
It’s important to note that these costs are approximate and can vary based on the factors mentioned earlier. It is recommended to obtain detailed quotes from multiple insulation contractors to get a more accurate estimate for your specific project.
Now that we have explored the average cost of blow-in insulation, let’s move on to comparing its cost with other insulation types to help you make an informed decision.
Cost Comparison with Other Insulation Types
When considering insulation options, it’s important to compare the costs of different types of insulation to make an informed decision. Let’s explore the cost comparison between blow-in insulation and other common insulation types:
- Batt or roll insulation: Batt or roll insulation is a popular and relatively affordable option. It is sold in pre-cut rolls and typically made of fiberglass or mineral wool. The average cost of batt or roll insulation ranges from $0.50 to $1.50 per square foot. Compared to blow-in insulation, batt or roll insulation is generally cheaper, but it may not provide the same level of coverage and energy efficiency.
- Spray foam insulation: Spray foam insulation is a high-performance option known for its excellent insulation qualities and air sealing properties. However, it comes with a higher price tag. The average cost of spray foam insulation ranges from $1.50 to $3.50 per square foot. Spray foam insulation provides superior thermal insulation but can be more expensive compared to blow-in insulation.
- Rigid foam insulation: Rigid foam insulation is a durable and moisture-resistant option that provides excellent thermal insulation. It is typically sold in large panels and can be pricier compared to other insulation types. The average cost of rigid foam insulation varies from $1.00 to $3.00 per square foot. While rigid foam insulation has its advantages, such as high R-values, it may not be the most cost-effective option for every project.
Each insulation type has its own pros and cons, and the cost will depend on factors such as insulation material, installation method, and project requirements. It’s essential to consider not only the initial cost but also the long-term energy savings and benefits of each insulation type when making your decision.
Now that we have compared the cost of blow-in insulation with other insulation types, let’s break down the cost of blow-in insulation installation to help you better understand the expenses involved.
The cost of blow-in insulation can vary depending on factors such as the type of insulation, the size of the area to be insulated, and the location. On average, the cost can range from $1.50 to $3.00 per square foot. It’s best to get quotes from multiple contractors to find the best price for your specific needs.
Read more: How Much Does USA Insulation Cost
Cost Breakdown of Blow-in Insulation Installation
When estimating the cost of blow-in insulation installation, it’s important to understand the different components that contribute to the overall expense. Here is a breakdown of the potential costs involved:
- Material cost: The cost of the insulation material itself is one of the primary expenses. The type of insulation material chosen, such as fiberglass, cellulose, or mineral wool, will determine the cost per square foot. On average, the material cost can range from $0.50 to $2.50 per square foot, depending on the material chosen.
- Labor cost: Hiring professional insulation contractors to handle the installation is a common choice to ensure proper and efficient installation. The labor cost is influenced by factors such as the size and complexity of the project, accessibility of the installation area, and regional labor rates. On average, the labor cost can range from $1.00 to $2.50 per square foot.
- Additional materials: Depending on the specific requirements of your project, there may be additional materials needed. This can include vapor barriers, air sealing materials, insulation baffles, or any necessary repairs or modifications. The cost of additional materials should be factored into the overall expenses.
- Equipment rental: In some cases, insulation contractors may need to rent specialized equipment for the blow-in insulation installation. The rental cost of the equipment can vary depending on the duration of the project and the rental rates in your area. This expense should be discussed with the contractors during the estimation process.
- Cleanup and disposal: After the installation is complete, there may be a need for cleanup and disposal of any waste materials. This may incur an additional cost, so it’s important to clarify with the insulation contractors if this is included in the overall estimate or if there are any additional charges.
It’s important to note that these costs are estimates and can vary depending on your specific project requirements and location. To get a more accurate cost breakdown, it is recommended to obtain detailed quotes from insulation contractors who can assess your project and provide a customized estimate.
Now that we have explored the cost breakdown of blow-in insulation installation, let’s discuss the potential cost differences between DIY (Do-It-Yourself) and professional installation.
DIY vs Professional Blow-in Insulation Installation Costs
When considering blow-in insulation installation, you may be wondering whether to tackle the project yourself or hire professionals. Let’s compare the costs and implications of DIY (Do-It-Yourself) versus professional blow-in insulation installation:
DIY Blow-in Insulation:
Opting for a DIY approach to blow-in insulation installation can potentially save you money on labor costs. However, it’s essential to consider the following factors:
- Equipment: DIY installation requires renting or purchasing specialized equipment, such as blow-in machines. The rental or purchase cost of these machines can vary, and the quality of the equipment may affect the efficiency and outcome of the installation.
- Expertise: Properly installing blow-in insulation requires knowledge of insulation techniques, safety precautions, and the ability to navigate challenging areas. If you’re not experienced in insulation installation, there is a risk of improper installation, gaps, or coverage issues that may impact the effectiveness of the insulation.
- Time and effort: DIY installation can be time-consuming and physically demanding, especially for larger areas or hard-to-reach spaces. It’s important to assess whether you have the necessary time, energy, and resources to complete the project on your own.
- Potential risks: DIY installation comes with potential risks, such as accidental damage to the property, injury, or inadequate insulation coverage. These risks can lead to additional expenses and potential long-term issues.
Professional Blow-in Insulation:
Hiring professional insulation contractors offers several benefits, including:
- Expertise and experience: Insulation professionals have the necessary knowledge, experience, and specialized equipment to perform the installation efficiently and correctly. They can ensure proper coverage, minimize gaps, and address any specific requirements of your project.
- Time and convenience: Professional installation saves you the time and effort required for DIY installation. Contractors will handle the entire process, from material selection to clean-up, allowing you to focus on other important tasks.
- Guarantees and warranties: Reputable insulation contractors often provide guarantees and warranties on their workmanship and materials. This offers added peace of mind and protection in case of any issues that may arise.
While professional installation generally comes at a higher upfront cost due to labor charges, it can provide long-term benefits, ensuring the insulation is installed correctly and maximizing energy efficiency.
Ultimately, the choice between DIY and professional blow-in insulation installation depends on your budget, time availability, expertise, and comfort level. It is recommended to consult with insulation professionals to assess your project requirements and receive personalized advice regarding the most suitable option for your specific situation.
Now that we have discussed the DIY vs professional blow-in insulation installation costs, let’s consider some additional factors to keep in mind during the decision-making process.
Additional Factors to Consider
When it comes to blow-in insulation installation, there are several additional factors you should consider to ensure a successful and cost-effective project. These factors can impact both the overall cost and the effectiveness of the insulation. Let’s explore them:
- Energy savings: While blow-in insulation is an investment, it can lead to long-term energy savings by reducing heating and cooling costs. Consider the potential energy savings over time when evaluating the cost of the insulation.
- Insulation quality and R-value: The insulation’s quality and R-value, which measures its thermal resistance, can impact both the comfort of your home and the overall cost. Higher-quality insulation with a higher R-value may have a higher upfront cost but can provide better insulation performance and energy savings in the long run.
- Air sealing: Proper air sealing is essential for maximizing the effectiveness of blow-in insulation. Before installation, assess the need for air sealing to minimize air leakage and enhance the insulation’s performance. Air sealing may incur additional costs but can greatly improve energy efficiency.
- Permits and regulations: Depending on your location, there may be specific permits or regulations governing insulation installation. Check with your local authorities to ensure compliance and factor in any associated costs or requirements.
- Contaminants and pest control: If there are existing contaminants, such as mold or pests, in the area to be insulated, additional measures may be needed to address these issues before installing blow-in insulation. Addressing contaminants and pests can add to the overall cost but is important for a healthy living environment.
- Long-term maintenance: Consider the long-term maintenance requirements of the insulation material chosen. Some materials may require periodic inspection or maintenance to ensure their effectiveness and durability.
By considering these additional factors, you can make a more informed decision regarding your blow-in insulation project. It’s advisable to consult with insulation professionals who can assess your specific needs, provide detailed cost estimates, and guide you through the decision-making process.
Now that we have explored these additional factors, let’s conclude our discussion on blow-in insulation costs.
Conclusion
When it comes to insulating your home, blow-in insulation is a popular and effective option. It offers numerous benefits, including improved energy efficiency, reduced heating and cooling costs, and enhanced comfort. However, it’s important to consider the cost of blow-in insulation to ensure a cost-effective and successful project.
Factors that can impact the cost of blow-in insulation include the type of insulation material, the size of the area to be insulated, labor costs, insulation depth, access and ease of installation, and additional components required. These factors interact with each other, influencing the overall cost.
The average cost of blow-in insulation installation typically ranges from $1.50 to $3.50 per square foot, including both material and labor costs. However, this is a rough estimate, and the actual cost can vary depending on your unique project requirements and location.
When comparing blow-in insulation with other insulation types, such as batt or roll insulation, spray foam insulation, or rigid foam insulation, it’s important to consider factors like the initial cost, long-term energy savings, and insulation performance to ensure the best choice for your specific needs.
A cost breakdown of blow-in insulation installation includes material cost, labor cost, additional materials, equipment rental, and cleanup and disposal. Depending on your preferences, you may choose to undertake the installation as a DIY project or hire professional insulation contractors. DIY installation can save on labor costs, but it requires time, expertise, and access to specialized equipment. Professional installation ensures proper installation, convenience, expertise, and potential warranties, although it comes at a higher upfront cost.
Additional factors to consider include energy savings, insulation quality and R-value, air sealing, permits and regulations, contaminants and pest control, and long-term maintenance requirements of the insulation material.
By considering all these factors and seeking guidance from insulation professionals, you can make an informed decision about blow-in insulation that suits your budget, energy efficiency goals, and specific project requirements.
In conclusion, blow-in insulation is an excellent choice for improving the energy efficiency and comfort of your home. By weighing the costs and benefits, and taking into account the various factors discussed in this article, you can make an educated decision that will lead to a well-insulated and cost-effective living space.
Frequently Asked Questions about How Much Does Blow-In Insulation Cost
Was this page helpful?
At Storables.com, we guarantee accurate and reliable information. Our content, validated by Expert Board Contributors, is crafted following stringent Editorial Policies. We're committed to providing you with well-researched, expert-backed insights for all your informational needs.
0 thoughts on “How Much Does Blow-In Insulation Cost”