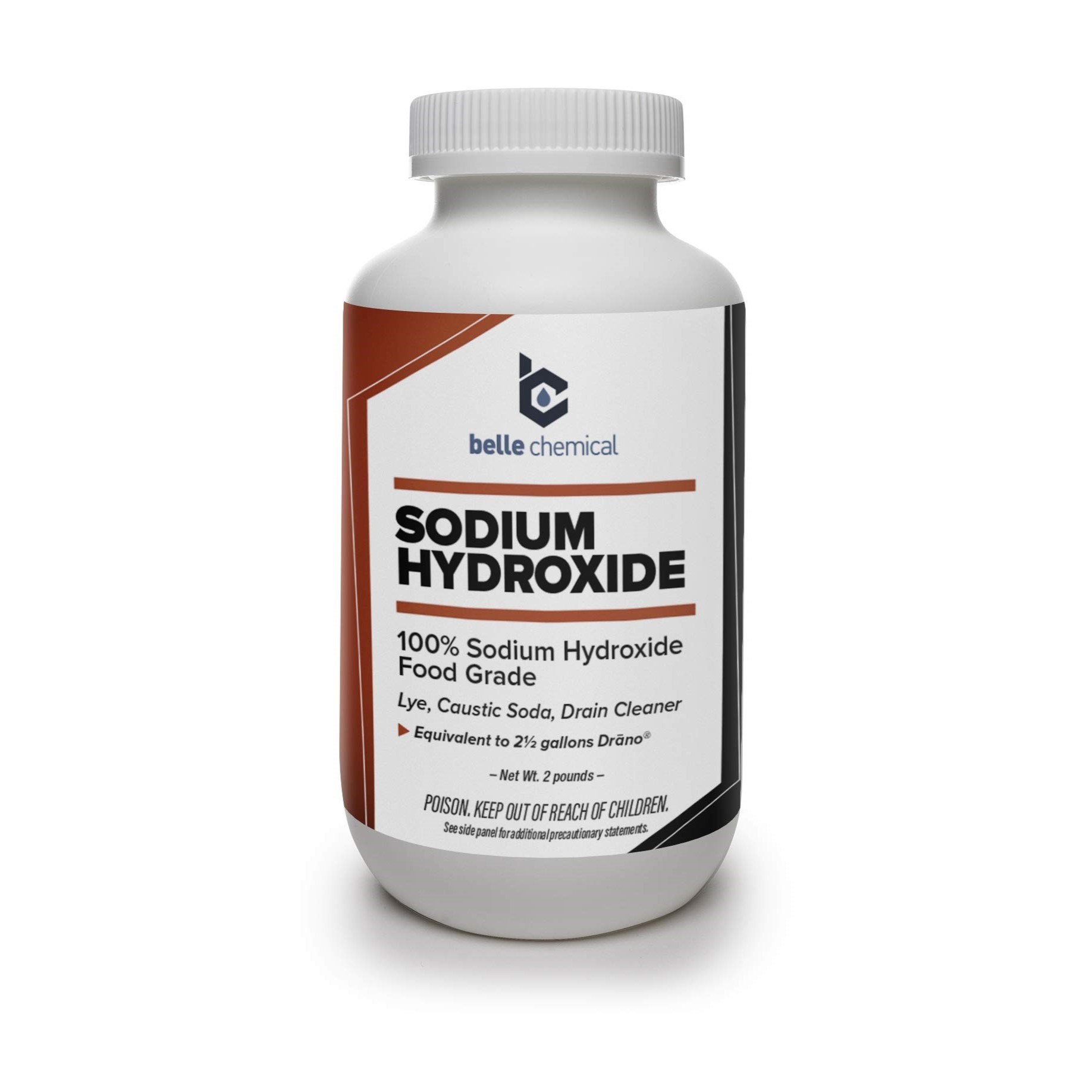
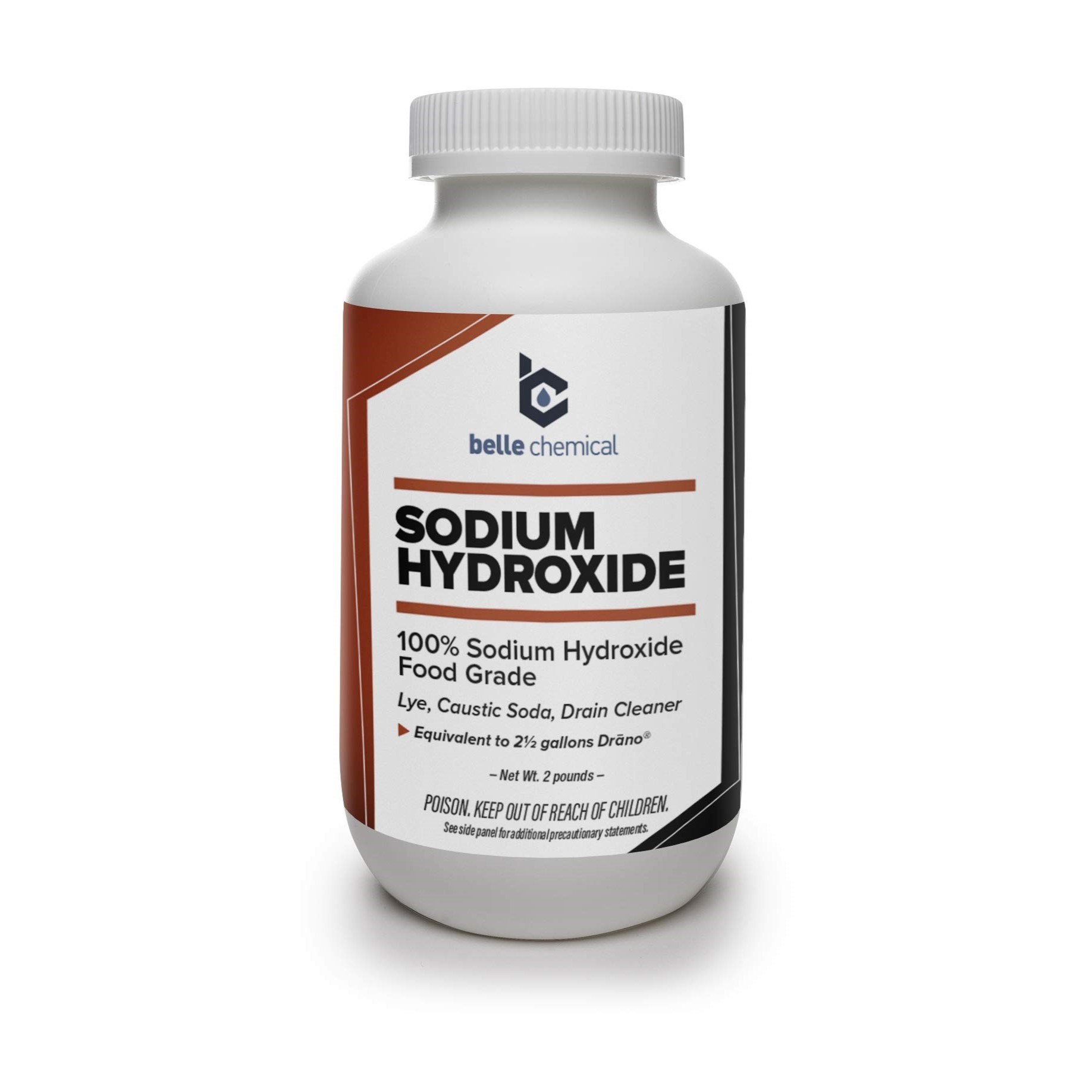
Articles
How To Store Sodium Hydroxide
Modified: December 7, 2023
Learn the best ways to safely store sodium hydroxide in this informative article. Get tips and guidelines to ensure proper handling and storage of this corrosive substance.
(Many of the links in this article redirect to a specific reviewed product. Your purchase of these products through affiliate links helps to generate commission for Storables.com, at no extra cost. Learn more)
Introduction
Welcome to our comprehensive guide on how to store sodium hydroxide. Sodium hydroxide, also known as caustic soda, is a highly reactive and corrosive chemical commonly used in various industries such as manufacturing, cleaning, and water treatment. With its potent properties, proper storage and handling of sodium hydroxide are crucial to ensure safety and extend its shelf life.
In this article, we will provide you with essential guidelines and safety precautions to effectively store sodium hydroxide. By following these recommendations, you can maintain the integrity of the chemical and reduce the risk of accidents or chemical reactions.
It is important to note that sodium hydroxide is classified as a hazardous substance, posing health and safety risks if not stored and handled properly. Therefore, it is imperative to understand and implement the recommended storage practices to protect yourself, your employees, and the environment.
Before diving into the specifics of proper storage, let’s take a moment to highlight some safety precautions that should be followed when handling sodium hydroxide:
– Always wear appropriate personal protective equipment (PPE) such as gloves, goggles, and a lab coat to minimize contact and exposure to the chemical.
– Ensure that the storage area is well-ventilated to prevent the accumulation of fumes or gases.
– Never mix sodium hydroxide with other chemicals unless instructed by a qualified professional.
– Keep sodium hydroxide away from heat sources, sparks, or open flames, as it is highly flammable.
– In case of accidental contact with the skin or eyes, immediately rinse with copious amounts of water and seek medical attention.
In the next sections, we will discuss the different aspects of storing sodium hydroxide, including suitable storage containers, the ideal storage temperature, humidity control, avoiding contamination, labeling and documentation, ventilation requirements, handling and transportation, and emergency response procedures. By following these guidelines, you can ensure the safe and effective storage of this corrosive substance. Let’s jump into it!
Key Takeaways:
- Proper storage and handling of sodium hydroxide is crucial for safety, efficacy, and environmental protection. Following guidelines for PPE, container selection, and emergency response ensures secure storage and minimizes risks.
- Prioritizing safety, ventilation, and emergency preparedness when storing sodium hydroxide safeguards individuals and the environment. Compliance with regulations, proper labeling, and regular training are essential for effective storage practices.
Read more: How To Store Sodium Hypochlorite
Safety Precautions
When it comes to handling and storing sodium hydroxide, safety should always be the top priority. The caustic nature of sodium hydroxide requires strict adherence to proper safety protocols to minimize the risk of accidents and chemical reactions. Here are some key safety precautions to follow:
1. Protective Equipment: Always wear appropriate personal protective equipment (PPE), including gloves, goggles, and a lab coat, when working with sodium hydroxide. This will minimize direct contact and protect your skin, eyes, and respiratory system from potential harm.
2. Ventilation: Ensure that the storage area is well-ventilated. Sodium hydroxide can release fumes and gases, especially when exposed to air or water. Proper ventilation will prevent the build-up of these hazardous substances and promote a safe working environment.
3. No Mixing: Never mix sodium hydroxide with other chemicals unless specifically instructed to do so by a qualified professional. Mixing sodium hydroxide with incompatible substances can lead to dangerous chemical reactions and potentially result in explosions or toxic gas release.
4. Avoid Heat Sources: Keep sodium hydroxide away from heat sources, sparks, or open flames. The chemical is highly flammable and can ignite easily. Store it in a cool, dry area away from any potential ignition sources to prevent fire hazards.
5. Handling: Use caution when handling sodium hydroxide. Avoid splashing or spilling the chemical, as it can cause severe burns and damage to surfaces. Always use appropriate containers and equipment to safely transfer or dispense the substance.
6. Labels and Warning Signs: Clearly label all containers that hold sodium hydroxide with the necessary hazard warning signs and identification labels. This ensures that everyone in the vicinity is aware of the potential dangers associated with the chemical and can take appropriate precautions.
7. Storage Area Access: Restrict access to the storage area to authorized personnel only. This helps prevent accidental exposure or misuse of sodium hydroxide by untrained individuals.
8. Emergency Preparedness: Have a well-defined emergency response plan in place in case of accidental spills, leaks, or chemical reactions involving sodium hydroxide. Provide proper training to employees on how to respond to emergencies and have the necessary safety equipment readily available.
Remember, maintaining a safe working environment and following proper safety precautions are vital when dealing with sodium hydroxide. By implementing the above measures, you can minimize the risk of accidents and ensure the well-being of everyone involved in handling and storing this corrosive chemical.
Storage Containers
Choosing the right storage containers for sodium hydroxide is crucial to maintain its integrity and minimize the risk of leaks or spills. When selecting containers, consider the following factors:
1. Material Compatibility: Sodium hydroxide is highly corrosive and can react with certain materials. It is essential to use containers made of compatible materials such as high-density polyethylene (HDPE), polypropylene (PP), or stainless steel. These materials have excellent chemical resistance and can withstand the corrosive properties of sodium hydroxide.
2. Tight Sealing: Ensure that the storage containers have tight-fitting lids or seals to prevent any leakage or evaporation of the chemical. This will help maintain the concentration and effectiveness of the sodium hydroxide.
3. Chemical Resistance: Sodium hydroxide can corrode certain plastics and metals. Avoid using containers made of materials such as aluminum, copper, brass, or polycarbonate, as they may react with sodium hydroxide and compromise its quality.
4. Container Size: Consider the volume of sodium hydroxide you need to store when choosing container size. It is generally recommended to use smaller containers to minimize the risk of spills and make handling more manageable. If using larger containers, ensure that appropriate handling equipment, such as a drum dolly or pallet, is available to safely move and transport them.
5. Secondary Containment: Implement a secondary containment system to capture any potential leaks or spills from the storage containers. This can be in the form of spill containment trays or bunds, which provide an extra layer of protection and prevent the spread of the chemical in case of container failure.
6. Storage Location: Store the containers of sodium hydroxide in a dedicated storage area away from incompatible chemicals. This will minimize the risk of accidental mixing and potential chemical reactions. Consider installing shelves or racks to keep the containers organized and prevent them from being knocked over or damaged.
7. Accessibility: Ensure that the storage containers are easily accessible for inspection, regular maintenance, and emergency response purposes. Do not overcrowd the storage area, as it may impede movement and increase the risk of accidents.
It is essential to regularly inspect the storage containers for any signs of damage or deterioration. If any damage is detected, promptly replace the container to prevent any potential leaks or compromise to the chemical’s quality. Additionally, follow any manufacturer guidelines for proper usage and storage of the containers.
By using appropriate containers, you can effectively store sodium hydroxide and maintain its stability and integrity throughout its shelf life. Always prioritize safety when handling and storing corrosive substances like sodium hydroxide to protect yourself, others, and the environment.
Storage Temperature
Proper storage temperature is essential for maintaining the stability and effectiveness of sodium hydroxide. Extreme temperatures can accelerate chemical reactions and impact the quality of the substance. Here are some guidelines to consider when storing sodium hydroxide:
1. Cool and Dry Location: Store sodium hydroxide in a cool, dry area away from direct sunlight and sources of heat. Excessive heat can degrade the chemical and compromise its efficacy.
2. Avoid Freezing: Sodium hydroxide has a freezing point of 12.6°C (54.7°F). While it is relatively high, freezing can cause the formation of ice crystals and damage the container. Ensure that the storage area maintains a temperature above freezing to prevent any potential issues.
3. Temperature Range: Ideally, the storage temperature for sodium hydroxide should be between 10°C and 25°C (50°F and 77°F). This range provides a stable environment for the chemical and minimizes the risk of undesired reactions or degradation.
4. Temperature Monitoring: Regularly monitor the storage temperature to ensure it remains within the recommended range. Consider using temperature monitoring devices, such as thermometers or data loggers, to accurately assess the storage conditions.
5. Avoid Temperature Fluctuations: Rapid temperature changes can affect the integrity of sodium hydroxide. Avoid storing the chemical near HVAC vents, open windows, or other areas where temperature fluctuations are common.
6. Separation from Heat Sources: Keep sodium hydroxide away from sources of heat, such as radiators, furnaces, or hot pipes. Elevated temperatures can lead to increased evaporation, concentration, and potential reactions.
7. Insulation: If the storage area is subject to extreme temperature variations, consider insulating the storage containers to help maintain a more consistent temperature. This will minimize the impact of external temperature changes on the chemical.
Remember to follow any specific manufacturer recommendations regarding storage temperature. Different sodium hydroxide formulations or concentrations may have specific temperature requirements for optimal storage.
By storing sodium hydroxide at the appropriate temperature range, you can ensure its stability and maintain its integrity for longer periods. This will help maximize its effectiveness and reduce the risk of unforeseen reactions or breakdowns. Always prioritize proper storage conditions to ensure the safe and efficient utilization of sodium hydroxide.
Humidity Control
Humidity control is an essential aspect of storing sodium hydroxide to maintain its quality and prevent any unwanted reactions or degradation. Excessive humidity can lead to the absorption of moisture by the chemical, affecting its concentration and efficacy. Here are some guidelines for humidity control when storing sodium hydroxide:
1. Low Humidity Environment: Store sodium hydroxide in a low humidity environment to minimize the risk of moisture absorption. The ideal humidity range is below 60% relative humidity (RH). High humidity can cause the formation of lumps or clumps in the chemical, reducing its solubility and effectiveness.
2. Storage Area Ventilation: Ensure proper ventilation in the storage area to prevent the accumulation of moist air and condensation. Good air circulation helps maintain a drier environment and reduces the chances of moisture exposure.
3. Dehumidifiers: In areas with high humidity, consider using dehumidifiers to remove excess moisture from the air. This will help maintain a controlled humidity level and prevent the potential absorption of moisture by sodium hydroxide.
4. Desiccant Packs: Consider using desiccant packs or moisture-absorbing agents in the storage containers or around the storage area. Silica gel packs or drying agents can help absorb any residual moisture and maintain a dry environment.
5. Avoid Water Exposure: Keep sodium hydroxide away from contact with water or other sources of moisture. Moisture can cause unwanted reactions and compromise the chemical’s stability. Ensure that the storage area is free from any water leaks or potential sources of water damage.
6. Container Integrity: Inspect the storage containers regularly for any signs of damage or leakage. Damaged containers can allow moisture to enter and interact with the sodium hydroxide. Replace any damaged containers promptly to maintain the integrity of the chemical.
7. Monitoring: Use humidity monitoring devices, such as hygrometers, to assess the humidity levels in the storage area. Regular monitoring allows you to identify any fluctuations and take appropriate measures to maintain a controlled humidity environment.
Remember, sodium hydroxide is highly hygroscopic, meaning it readily absorbs moisture from its surroundings. Therefore, proper humidity control is crucial to ensure the chemical’s stability and efficacy. By implementing these guidelines, you can minimize the risk of moisture absorption and maintain the quality of sodium hydroxide throughout its storage period.
Read more: Why Does A Sodium Street Lamp Glow
Avoidance of Contamination
Preventing contamination is vitally important when storing sodium hydroxide to maintain its purity and effectiveness. Contamination can compromise the chemical’s properties, lead to unexpected reactions, or render it unsuitable for use. Here are some guidelines to help you avoid contamination when storing sodium hydroxide:
1. Dedicated Storage: Store sodium hydroxide in a dedicated storage area separate from other chemicals or substances. This reduces the risk of accidental mixing or contamination with incompatible materials. Proper segregation ensures the integrity of the sodium hydroxide and prevents any unwanted reactions.
2. Container Integrity: Inspect storage containers regularly and ensure their integrity. Damaged containers can lead to leaks, spills, or contamination of the sodium hydroxide. Promptly replace any damaged containers to prevent any compromise to the chemical’s quality.
3. Proper Sealing: Ensure that storage containers are tightly sealed to prevent any entry of foreign substances or contaminants. A secure seal keeps the sodium hydroxide free from external impurities and maintains its purity over time.
4. Secondary Containment: Implement secondary containment measures, such as spill trays or bunding, to capture any potential leaks or spills from the storage containers. This prevents contamination of the surrounding environment and facilitates easy cleanup if any accidents occur.
5. Handling Equipment: Use appropriate handling equipment, such as dedicated scoops or funnels, when transferring sodium hydroxide from one container to another. This helps prevent cross-contamination with other chemicals and ensures the chemical remains pure.
6. Clean Storage Area: Keep the storage area clean and free from dirt, dust, and other impurities. Regularly sweep or vacuum the area to eliminate any potential sources of contamination. Avoid storing sodium hydroxide on the floor, as it is more susceptible to dirt and debris.
7. Proper Labeling: Clearly label all storage containers with the necessary identification labels, including the chemical name, concentration, and hazard warnings. Proper labeling ensures easy identification and prevents accidental use or mixing of different chemicals.
8. Good Hygiene Practices: Practice good hygiene when handling sodium hydroxide. Wash hands thoroughly before and after handling the chemical to prevent any potential cross-contamination or ingestion.
9. Training and Education: Provide comprehensive training to employees on proper storage and handling procedures for sodium hydroxide. Ensure that they are aware of the importance of avoiding contamination and understand the potential risks associated with improper storage practices.
By following these guidelines and maintaining a strict focus on avoiding contamination, you can ensure that sodium hydroxide remains pure and effective throughout its storage period. Minimizing the risk of contamination enhances the chemical’s stability and safety, allowing for its optimal utilization in various applications.
Store sodium hydroxide in a tightly sealed container, away from moisture and air. Keep it in a cool, dry place, and away from any acids or other incompatible materials.
Labeling and Documentation
Proper labeling and documentation are crucial when storing sodium hydroxide to ensure safety and facilitate easy identification and handling. Accurate labeling and thorough documentation provide important information about the chemical, its hazards, and any necessary precautions. Here are some guidelines for effective labeling and documentation when storing sodium hydroxide:
1. Chemical Identification: Clearly label all storage containers with the chemical name, concentration, and any other relevant identifiers. This helps identify the contents of the container at a glance and prevents confusion or potential mixing with other chemicals.
2. Hazard Warnings: Use appropriate hazard warning symbols, such as the skull and crossbones, corrosive symbol, or exclamation mark, on the labels to indicate the potential dangers associated with sodium hydroxide. These symbols help raise awareness of the risks involved and prompt individuals to take necessary precautions.
3. Storage Information: Provide specific storage instructions on the labels, including temperature requirements, humidity considerations, and any other storage-related guidelines. This ensures that sodium hydroxide is stored under the optimal conditions for maximum stability and effectiveness.
4. Emergency Contacts: Include emergency contact information for local poison control centers, fire departments, or other relevant authorities on the labels. This information should be easily accessible to anyone handling or responding to emergencies involving sodium hydroxide.
5. Material Safety Data Sheets (MSDS): Keep updated MSDS for sodium hydroxide readily available in the storage area. These documents provide comprehensive information about the chemical, including physical and chemical properties, hazards, proper handling procedures, and emergency response measures. Ensure that employees are familiar with MSDS and know where to find them.
6. Documentation of Usage: Maintain accurate records of sodium hydroxide usage, including dates, quantities used, and purpose of use. This documentation aids in inventory management and ensures proper tracking of the chemical’s usage and replenishment.
7. Safety Data Sheets (SDS): Obtain and review SDS for sodium hydroxide from the manufacturer or supplier. These sheets provide detailed information about the chemical’s hazards, handling precautions, first-aid measures, and regulatory compliance requirements. Ensure that employees have access to the most recent SDS and understand its contents.
8. Regular Inspections and Updates: Periodically inspect and review the labels and documentation to ensure they are accurate and up-to-date. Replace or update labels as needed or when any changes occur regarding the chemical’s concentration or storage requirements.
9. Employee Training: Train employees on the importance of reading and understanding labels and documentation. Ensure they are familiar with the necessary precautions and procedures associated with sodium hydroxide storage and handling.
By following these guidelines for labeling and documentation, you enhance safety and ensure proper handling of sodium hydroxide. Clear and accurate information enables employees to make informed decisions while handling the chemical and aids emergency responders in effectively addressing any accidents or spills involving sodium hydroxide.
Ventilation Requirements
Proper ventilation is crucial when storing sodium hydroxide to ensure a safe and healthy environment. Adequate ventilation helps remove fumes, gases, and odors, thereby preventing the buildup of potentially hazardous substances. Here are some guidelines for maintaining appropriate ventilation when storing sodium hydroxide:
1. Natural Ventilation: If possible, store sodium hydroxide in a well-ventilated area with access to fresh air. Natural ventilation can be achieved by opening windows, doors, or using vents or louvers to facilitate air circulation. This promotes the exchange of indoor and outdoor air, helping to disperse any fumes or gases that may be emitted.
2. Mechanical Ventilation: In areas where natural ventilation is limited or insufficient, consider using mechanical ventilation systems. Install exhaust fans or ductwork to remove contaminated air and bring in fresh air from outside. Mechanical ventilation is especially important in confined spaces or areas with poor air circulation.
3. Hazardous Fume Cabinets: If sodium hydroxide is stored in hazardous quantities or in a laboratory setting, use dedicated fume cabinets or hoods. These cabinets effectively control and exhaust fumes, ensuring the safety of personnel and preventing the release of hazardous vapors into the surrounding environment.
4. Local Exhaust Ventilation: Employ local exhaust ventilation systems near areas where sodium hydroxide is handled or dispensed. These systems capture and remove fumes directly at the source, minimizing their dispersal into the larger storage area or workspace.
5. Avoid Recirculation: Be cautious to avoid recirculating air within the storage area or workspace. Recirculation may lead to the concentration of fumes or gases, increasing the risk of exposure. Instead, ensure that the ventilation system directs air outside or to a proper exhaust system.
6. Regular Inspections: Regularly inspect ventilation systems to ensure they are functioning correctly. Check for any obstructions in the ducts or filters that may hinder proper air exchange. Maintain and clean the ventilation system as recommended by the manufacturer.
7. Employee Awareness: Train employees on the importance of proper ventilation and the potential hazards associated with poor air circulation. Encourage them to report any ventilation issues or concerns promptly.
8. Comply with Regulations: Ensure compliance with local regulations and codes regarding ventilation requirements for storing sodium hydroxide. Different jurisdictions may have specific guidelines for adequate ventilation in storage areas, laboratories, or industrial settings.
By maintaining proper ventilation, you reduce the risk of exposure to harmful fumes or gases, minimize odor buildup, and create a safer working environment. Ensuring adequate airflow and proper ventilation safeguards the health and well-being of personnel involved in sodium hydroxide storage and handling.
Handling and Transportation
Proper handling and transportation of sodium hydroxide are crucial to ensure safety and prevent accidents or spills. Whether you need to move the chemical within your facility or transport it to another location, following industry best practices is essential. Here are some guidelines for safe handling and transportation of sodium hydroxide:
1. Personal Protective Equipment (PPE): Wear appropriate PPE, including chemical-resistant gloves, goggles, and a lab coat, when handling sodium hydroxide. Gloves made of nitrile or neoprene are recommended as they provide good resistance to the chemical.
2. Secure Packaging: Use secure and leak-proof containers specifically designed for transporting hazardous chemicals. Ensure that the lids or caps are tightly sealed to prevent any spills or leakage during transportation.
3. Container Integrity: Inspect the containers for any damage or signs of corrosion before handling or transportation. Damaged containers can lead to leaks or spills and should not be used. Replace them with new, undamaged containers to ensure the integrity of the chemical during transport.
4. Proper Lifting Techniques: When moving containers, use proper lifting techniques to minimize the risk of injury. Lift with the legs, not the back, and use mechanical aids like dollies or forklifts when necessary. Do not overload yourself or the equipment being used.
5. Secure Transport: Ensure that containers are securely placed and immobilized during transportation to prevent shifting or rolling. Secure them with straps, ties, or other restraints to minimize the risk of accidents or spills during transit.
6. Separation: During transportation, separate sodium hydroxide from incompatible substances, such as acids or oxidizing agents. Use proper segregation practices and follow any regulatory requirements for the transport of hazardous materials.
7. Plan the Route: Plan the transportation route in advance, considering potential road conditions and any restrictions or permits required for hazardous materials. Choose the shortest and safest route possible.
8. Emergency Response Equipment: Carry appropriate emergency response equipment, such as spill kits, absorbents, and personal protective equipment, during transportation. This enables quick and effective response in case of any accidents or spills.
9. Regulatory Compliance: Follow all local, regional, and national regulations regarding the transportation of sodium hydroxide. Familiarize yourself with applicable laws, labeling requirements, and any necessary permits or certifications.
10. Documentation: Maintain proper documentation throughout the handling and transportation process. Keep records of the quantity, dates, locations, and any incidents or spills that occur during transport.
By following these guidelines for proper handling and transportation of sodium hydroxide, you minimize the risk of accidents, spills, and exposure to the chemical. Prioritizing safety measures and adhering to regulatory requirements ensure the well-being of those involved in the handling and transportation process, as well as the protection of the environment.
Emergency Response Procedures
Being prepared for emergencies is essential when handling and storing sodium hydroxide. Accidents or spills involving sodium hydroxide can pose significant risks to both humans and the environment. Having well-defined emergency response procedures in place ensures a swift and effective response to mitigate any potential hazards. Here are some guidelines for emergency response procedures when dealing with sodium hydroxide:
1. Emergency Contacts: Maintain a list of emergency contact numbers, including local poison control centers, fire departments, and hazardous materials response teams. Ensure that these numbers are readily accessible and known to all personnel involved in handling sodium hydroxide.
2. Evacuation Plan: Develop and communicate a clear evacuation plan to all employees working in the area where sodium hydroxide is stored. Designate primary and secondary evacuation routes, assembly points, and procedures for accounting for all personnel during an evacuation.
3. Personal Protective Equipment (PPE): Ensure that all employees are trained on the proper use of PPE and have access to the necessary equipment. In the event of an emergency, personnel should quickly don appropriate PPE, including gloves, goggles, and respiratory protection, as needed.
4. Spill Response: Establish procedures for responding to sodium hydroxide spills. Train employees on proper spill response techniques, including containing the spill, preventing it from spreading, and safely cleaning up the spilled material. Use appropriate absorbent materials and containment measures to minimize the environmental impact.
5. First Aid Measures: Provide adequate training in first aid procedures for sodium hydroxide exposure. Educate employees on the appropriate steps to take in case of skin contact, eye exposure, or ingestion of sodium hydroxide. Have first aid kits readily available in the storage area and ensure employees know their location.
6. Communication: Establish a communication protocol to ensure that all relevant parties are informed of an emergency situation. This includes alerting employees, neighboring businesses, emergency responders, and regulatory agencies as necessary. Clear communication helps coordinate the response and ensures the safety of all involved.
7. Documentation: Maintain accurate and up-to-date records of any emergency situations, including incident reports, spill response actions, and any follow-up measures taken. Proper documentation aids in evaluating the effectiveness of emergency response procedures and serves as a reference for improvement if needed.
8. Training and Drills: Regularly conduct training sessions and drills to familiarize employees with emergency response procedures. Engage in mock scenarios to test the effectiveness of the emergency plan and identify areas for improvement. Training ensures that employees are prepared to handle emergencies involving sodium hydroxide.
Remember, in the event of an emergency, personal safety should always be the top priority. If the situation is beyond your capabilities, immediately contact emergency response professionals for assistance. By implementing and regularly reviewing these emergency response procedures, you can effectively manage and mitigate any potential risks associated with sodium hydroxide handling and storage.
Conclusion
In conclusion, proper storage and handling of sodium hydroxide is of utmost importance to ensure safety, maintain the chemical’s integrity, and prevent accidents or reactions. By following the guidelines and best practices outlined in this comprehensive guide, you can effectively store sodium hydroxide while minimizing risks and maintaining a safe working environment.
From safety precautions to storing in appropriate containers, controlling humidity, avoiding contamination, labeling, ensuring proper ventilation, handling and transportation, and implementing emergency response procedures, each aspect plays a crucial role in the overall storage process.
Remember to prioritize safety by wearing personal protective equipment, choosing the right storage containers, maintaining suitable storage temperature and humidity, avoiding contamination by segregating incompatible substances, properly labeling and documenting, ensuring proper ventilation, and being prepared for emergencies with well-defined response procedures.
Proper storage and handling practices not only protect individuals involved but also safeguard the environment from potential harm. Compliance with local regulations and regulations for hazardous materials storage and transport is vital to ensure legal and ethical practices.
Regular training, inspections, and record-keeping are essential components of a comprehensive storage plan. By continuously monitoring and updating storage practices, you can optimize the longevity and effectiveness of sodium hydroxide while minimizing potential risks.
Remember, safety should be the main focus when working with any hazardous substance, including sodium hydroxide. Stay vigilant, keep your employees informed, and always prioritize the well-being of those involved in the storage and handling process.
By following these guidelines and best practices, you can confidently store and handle sodium hydroxide in a manner that ensures safety, protects the environment, and maintains the chemical’s efficacy. Implementing these practices will contribute to a well-organized and secure storage system, allowing you to harness the benefits of sodium hydroxide effectively for your intended applications.
Frequently Asked Questions about How To Store Sodium Hydroxide
Was this page helpful?
At Storables.com, we guarantee accurate and reliable information. Our content, validated by Expert Board Contributors, is crafted following stringent Editorial Policies. We're committed to providing you with well-researched, expert-backed insights for all your informational needs.
0 thoughts on “How To Store Sodium Hydroxide”