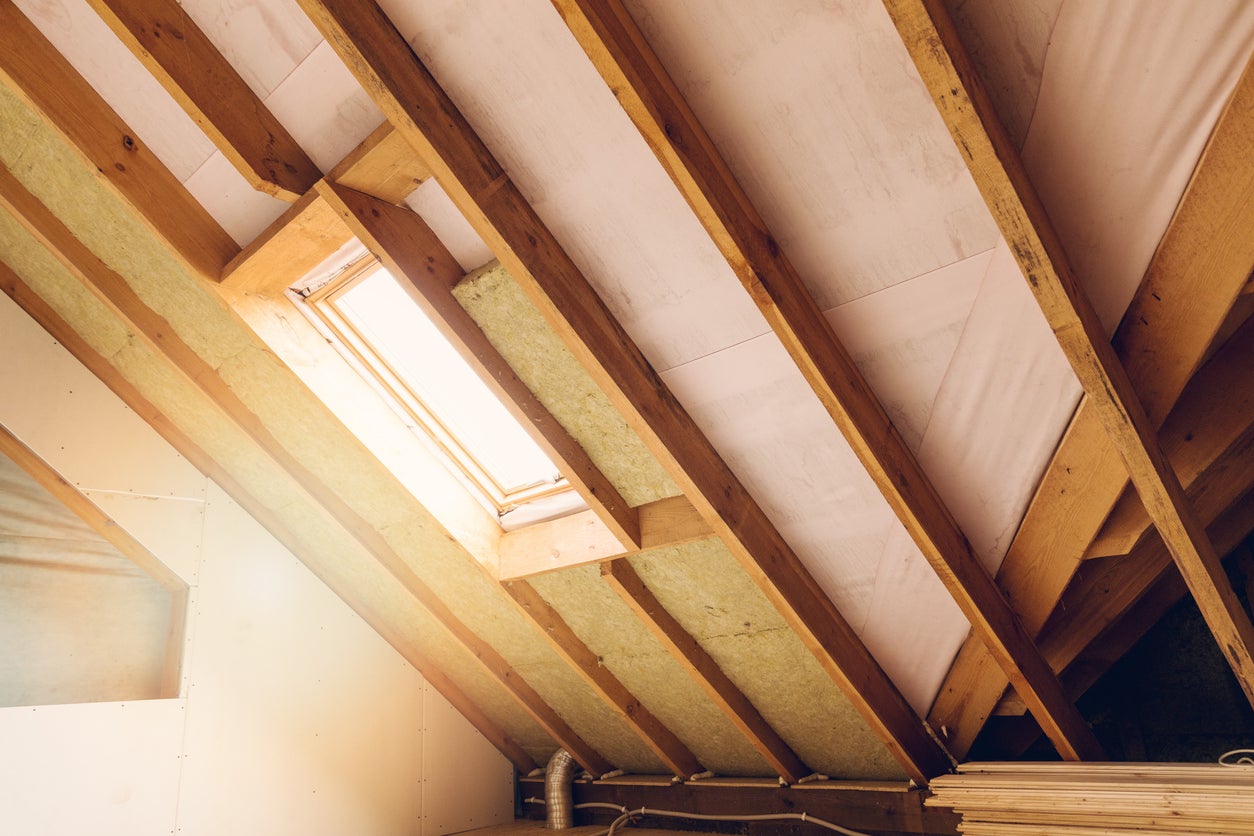
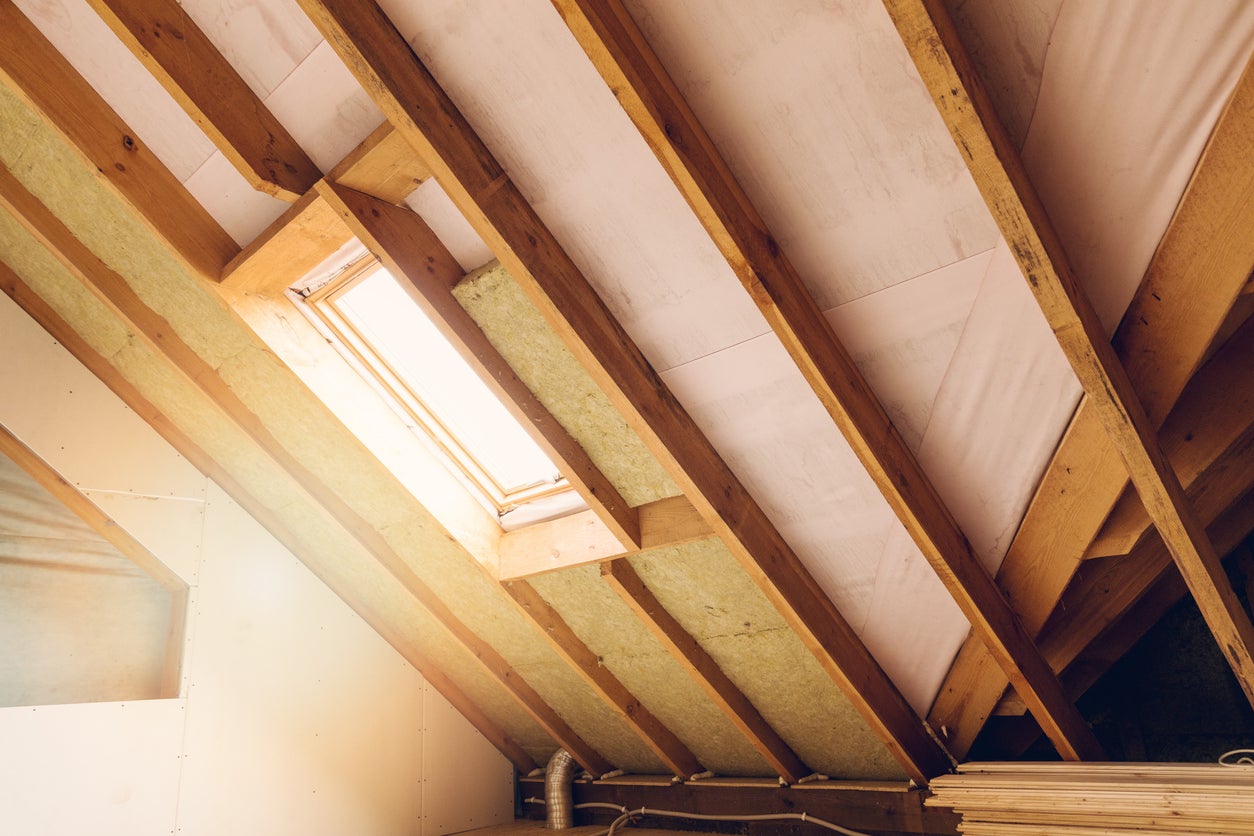
Articles
What Is Rockwool Insulation Made Out Of
Modified: February 23, 2024
Discover what rockwool insulation is made out of. This informative article explores the composition and benefits of rockwool insulation.
(Many of the links in this article redirect to a specific reviewed product. Your purchase of these products through affiliate links helps to generate commission for Storables.com, at no extra cost. Learn more)
Introduction
Rockwool insulation, also known as stone wool or mineral wool insulation, is a popular and effective insulation material used in residential, commercial, and industrial buildings. It offers excellent thermal insulation, soundproofing capabilities, and fire resistance, making it a versatile choice for insulation needs.
Rockwool insulation is made from a combination of natural and synthetic materials, which undergo a manufacturing process to form durable and high-quality insulation products. This article will provide an overview of the composition, manufacturing process, properties, and applications of rockwool insulation, as well as its comparison with other insulation materials.
One of the key components of rockwool insulation is basalt rock, a volcanic rock that is melted at extremely high temperatures. Along with the basalt rock, other ingredients such as limestone and coke are added to the mix. These materials are abundantly available, making rockwool insulation a sustainable choice.
Another important element in the production of rockwool insulation is the binder, which holds the fibers together. There are different types of binders used, including organic binders and inorganic binders. These binders help create a uniform and stable structure for the insulation material.
In addition to the basic ingredients, certain additives may be incorporated into the manufacturing process to enhance specific properties of rockwool insulation. These additives can improve factors such as moisture resistance, acoustic performance, and overall durability.
The manufacturing process of rockwool insulation involves several steps. It starts with the melting of the raw materials in a furnace at temperatures exceeding 1,500 degrees Celsius. The molten material is then directed to a spinning wheel or rotor, where it is spun into fine fibers. These fibers are then collected and bonded together using the binder.
After the fibers are formed and bonded, the rockwool insulation goes through a curing process, where it is exposed to heat to further strengthen the structure. Once cured, the insulation material is cut and shaped into various forms, such as rolls, batts, or boards, for easy installation.
Rockwool insulation offers numerous benefits. Its excellent thermal insulation properties help regulate indoor temperatures, reducing the need for excessive heating or cooling. It is also highly effective in soundproofing, minimizing noise transmission between rooms or from outside sources.
Furthermore, rockwool insulation exhibits exceptional fire resistance. It is non-combustible and can withstand high temperatures without melting or releasing toxic fumes. This makes it a safe and reliable choice for fire protection in buildings.
In addition to its thermal and acoustic properties, rockwool insulation is also resistant to moisture. It does not absorb water, preventing the growth of mold or mildew and maintaining its insulation performance over time.
Rockwool insulation is a sustainable option for insulation needs. Its manufacturing process utilizes readily available materials, minimizing the environmental impact. Additionally, rockwool insulation is recyclable and can be reused or repurposed at the end of its life cycle.
In comparison to other insulation materials, rockwool insulation offers certain advantages. While fiberglass insulation is another commonly used material, rockwool insulation provides better fire resistance and soundproofing capabilities. It also tends to be more durable and retains its insulation properties for longer periods.
Cellulose insulation, on the other hand, is made from recycled paper materials and treated with chemicals for fire resistance. While cellulose insulation is a sustainable choice, rockwool insulation offers superior thermal and moisture resistance.
Spray foam insulation provides excellent air sealing, but may not offer the same level of thermal insulation and fire resistance as rockwool insulation.
Rockwool insulation is widely used in various applications. In residential buildings, it is installed in walls, roofs, and floors to improve energy efficiency and reduce heating and cooling costs. In commercial buildings, rockwool insulation is used in office spaces, retail stores, and healthcare facilities for soundproofing and fire protection.
Industrial facilities often rely on rockwool insulation for its thermal insulation and fire resistance properties. It is commonly used in power plants, manufacturing plants, and warehouses to maintain stable temperatures and enhance safety.
When installing rockwool insulation, it is important to follow proper handling and protective measures, as the fibers can be irritating to the skin and respiratory system. Protective clothing, gloves, and masks should be worn during installation to minimize exposure.
Overall, rockwool insulation is a versatile and efficient insulation material that offers excellent thermal insulation, soundproofing, and fire resistance. Its sustainable properties and wide range of applications make it a popular choice for both residential and commercial buildings.
Key Takeaways:
- Rockwool insulation, made from basalt rock and binders, offers superior thermal insulation, soundproofing, and fire resistance. Its sustainable composition and wide applications make it a versatile and efficient choice for buildings.
- When compared to other insulation materials, rockwool insulation stands out with its exceptional fire resistance, soundproofing capabilities, and moisture resistance. Its wide range of applications and sustainable properties make it a top choice for both residential and commercial buildings.
Read more: Where To Buy Rockwool Insulation
Composition of Rockwool Insulation
Rockwool insulation is composed of various materials that come together to form a durable and effective insulation product. Understanding the composition of rockwool insulation can help us better appreciate its properties and benefits. Let’s explore the basic ingredients, binder, and additives that make up rockwool insulation.
Basic Ingredients:
The primary ingredient in rockwool insulation is basalt rock. Basalt is a volcanic rock that is abundant in many regions of the world. It is known for its excellent thermal and mechanical properties, making it an ideal choice for insulation materials.
In addition to basalt rock, other ingredients such as limestone and coke are commonly used in the production of rockwool insulation. These ingredients help enhance the melting properties and improve the overall structure of the insulation material.
Binder:
The binder is a crucial component in rockwool insulation. It holds the fibers together, forming a cohesive and stable structure. There are different types of binders used in rockwool insulation, including organic binders and inorganic binders.
Organic binders, such as starch, are often used in the production of rockwool insulation. These binders are derived from natural sources and provide excellent bonding properties. They help create a strong and resilient insulation material.
Inorganic binders, such as mineral-based binders, are also utilized in some rockwool insulation products. These binders offer high heat resistance and further enhance the fire resistance properties of the insulation material.
Additives:
Various additives may be incorporated into the manufacturing process of rockwool insulation to enhance specific properties. These additives can improve factors such as moisture resistance, acoustic performance, and overall durability.
For example, hydrophobic additives can be included to make the insulation material water repellent. This helps prevent the absorption of moisture, preventing the growth of mold or mildew and maintaining the insulation performance over time.
Acoustic enhancers are another type of additive that can be used to improve the soundproofing capabilities of rockwool insulation. These additives help absorb and attenuate sound waves, reducing noise transmission and creating a quieter indoor environment.
Additionally, certain additives can be included to enhance the fire resistance properties of rockwool insulation. These additives work in conjunction with the inherent fire-resistant properties of basalt rock to create an insulation material that can withstand high temperatures without melting or releasing toxic fumes.
Overall, the composition of rockwool insulation involves a combination of basalt rock, binders, and additives. These materials come together during the manufacturing process to form a durable, fire-resistant, and versatile insulation material. The specific combination and formulation of these ingredients may vary depending on the desired properties and application of the rockwool insulation product.
Manufacturing Process of Rockwool Insulation
The manufacturing process of rockwool insulation involves several steps that transform the raw materials into a finished insulation product. These steps include melting and spinning, fiber formation, binding, curing, and cutting and shaping. Let’s take a closer look at each stage of the manufacturing process.
Melting and Spinning:
The first step in manufacturing rockwool insulation is the melting of the basic ingredients. The basalt rock, along with other materials such as limestone and coke, is heated in a furnace at temperatures exceeding 1,500 degrees Celsius. This extreme heat causes the ingredients to melt and become molten.
Once the ingredients are melted, they are directed to a spinning wheel or rotor. The molten material is spun at a high speed, and as it spins, fine fibers are formed. The spinning process is what gives rockwool insulation its characteristic fibrous structure.
Fiber Formation:
As the molten material is spun, it is also subjected to centrifugal force, which helps to further stretch and disperse the fibers. This creates a tangled and interwoven network of fibers, forming a strong, flexible, and three-dimensional structure.
During the spinning process, it is essential to regulate the speed and distance between the spinning wheel and the collection surface to achieve the desired fiber thickness. The parameters of the spinning process are carefully controlled to ensure consistent and uniform fiber formation.
Binding:
After the fibers are formed, they are collected and sprayed with a binder solution. The binder is responsible for holding the fibers together, creating a bonded and stable insulation material.
There are different types of binders used in rockwool insulation, such as organic binders and inorganic binders. The choice of binder depends on factors such as the desired properties of the insulation material and the specific application requirements.
The binder is evenly distributed throughout the fibers, ensuring that each fiber is securely held in place. This binding process contributes to the overall durability and integrity of the rockwool insulation product.
Curing:
Once the fibers are bonded together, the rockwool insulation goes through a curing process. Curing involves subjecting the insulation material to heat treatment, typically in a curing oven. The heat helps to further strengthen the structure of the insulation material.
During the curing process, the binder undergoes a chemical reaction, forming a rigid and thermally stable matrix. This matrix enhances the insulation material’s resistance to heat, fire, and other external factors, ensuring long-lasting performance.
Cutting and Shaping:
After the curing process, the rockwool insulation is carefully cut and shaped into various forms. It can be cut into rolls, batts, or boards, depending on the specific application requirements.
Specialized machinery is used to cut the insulation material to precise dimensions. The cutting process also allows for the creation of specific shapes, such as tapered pieces for insulating pipes or custom-sized pieces for insulation in tight spaces.
Finally, the cut and shaped rockwool insulation products are packaged and prepared for distribution and installation.
The manufacturing process of rockwool insulation combines the melting and spinning of raw materials, fiber formation, binding, curing, and cutting and shaping. This careful process results in a high-quality insulation material that provides exceptional thermal insulation, soundproofing, and fire resistance properties.
Properties and Benefits of Rockwool Insulation
Rockwool insulation offers an array of properties and benefits that make it a popular choice for residential, commercial, and industrial applications. Let’s explore the key attributes of rockwool insulation, including its thermal insulation capabilities, soundproofing abilities, fire resistance, moisture resistance, and sustainability.
Thermal Insulation:
Rockwool insulation is highly effective in providing thermal insulation. Its dense and fibrous structure traps air pockets, which reduces heat transfer through conduction and convection. This helps maintain comfortable indoor temperatures and reduces the need for excessive heating or cooling. The high R-value of rockwool insulation ensures excellent thermal performance, resulting in energy savings and lower utility bills.
Soundproofing Abilities:
An additional benefit of rockwool insulation is its exceptional soundproofing capabilities. The fibrous structure of rockwool absorbs sound waves, reducing noise transmission between rooms and from external sources. This makes it an ideal choice for homes, offices, studios, and other spaces where noise reduction is desired. Rockwool insulation can significantly enhance acoustic comfort by creating a quieter and more peaceful environment.
Fire Resistance:
One of the standout features of rockwool insulation is its inherent fire resistance property. Basalt, the main component of rockwool insulation, is a naturally fire-resistant material. It can withstand high temperatures without melting or releasing toxic fumes. In the event of a fire, rockwool insulation acts as a barrier, slowing down the spread of flames and providing valuable time for evacuation. This makes it a reliable choice for fire protection in buildings and contributes to overall safety.
Moisture Resistance:
Rockwool insulation is resistant to moisture, making it a durable and long-lasting insulation solution. Unlike some other insulation materials, rockwool does not absorb water, preventing the growth of mold or mildew. This moisture resistance ensures that the insulation material maintains its performance over time, even in humid environments. Rockwool insulation helps create a dry and healthy indoor environment while protecting the building structure from water-related damage.
Sustainability:
Rockwool insulation is considered a sustainable choice for insulation needs. It is made from abundant and naturally occurring raw materials, such as basalt rock. These materials can be sourced locally, reducing the need for long-distance transportation and minimizing environmental impact. Additionally, rockwool insulation is recyclable and can be reused or repurposed at the end of its life cycle. The sustainability of rockwool insulation aligns with the growing demand for eco-friendly building materials and contributes to a greener and more sustainable future.
In summary, rockwool insulation offers a range of properties and benefits that make it an attractive choice for various applications. Its thermal insulation capabilities ensure energy efficiency and reduced heating and cooling costs. The soundproofing abilities of rockwool insulation create a quieter indoor environment. Fire resistance and moisture resistance properties add an extra level of safety and durability. Lastly, the sustainability of rockwool insulation aligns with the increasing focus on environmentally friendly building materials. Choosing rockwool insulation can provide comfort, protection, and peace of mind for building occupants while minimizing environmental impact.
Comparison with Other Insulation Materials
When it comes to insulation materials, rockwool insulation stands out among the options available in the market. Let’s compare rockwool insulation with other commonly used insulation materials such as fiberglass insulation, cellulose insulation, and spray foam insulation to understand the differences and advantages of each.
Read more: What Is Insulation Made Of
Fiberglass Insulation:
Fiberglass insulation is a widely used insulation material known for its affordability. It is made from tiny glass fibers that trap air, providing thermal insulation. However, fiberglass insulation has some differences compared to rockwool insulation:
- Fiberglass insulation has a lower resistance to heat compared to rockwool insulation, resulting in a slightly lower R-value.
- In terms of soundproofing, rockwool insulation outperforms fiberglass insulation due to its denser and more fibrous structure.
- Rockwool insulation has better fire resistance properties as basalt, the main component, is naturally fire-resistant. Fiberglass insulation requires the addition of fire-retardant chemicals.
- Moisture resistance of rockwool insulation is superior to fiberglass insulation, as rockwool does not absorb water and is not affected by mold or mildew growth.
- Rockwool insulation is more sustainable as it is made from abundant and naturally occurring materials, while fiberglass insulation requires a significant amount of energy and resources during production.
Cellulose Insulation:
Cellulose insulation is made from recycled paper materials, treated with chemicals to enhance fire resistance. While cellulose insulation has its own advantages, it differs from rockwool insulation in the following ways:
- Rockwool insulation has better thermal insulation capabilities and a higher R-value compared to cellulose insulation.
- Cellulose insulation is known to settle over time, reducing its effectiveness as an insulation material. Rockwool insulation, on the other hand, maintains its rigidity and insulation performance over the long term.
- Rockwool insulation is moisture resistant, while cellulose insulation can absorb and retain moisture, increasing the risk of mold or mildew growth.
- When it comes to fire resistance, rockwool insulation is inherently fire-resistant, while cellulose insulation requires chemical treatment to achieve fire-retardant properties.
- Rockwool insulation offers better soundproofing capabilities than cellulose insulation due to its denser and more fibrous structure.
- Both rockwool and cellulose insulation can contribute to sustainability efforts as they are made from recycled or natural materials.
Spray Foam Insulation:
Spray foam insulation is a unique insulation material that expands when applied, providing an airtight seal. While spray foam insulation has its own advantages, here are the key differences compared to rockwool insulation:
- Spray foam insulation offers excellent air sealing capabilities that help reduce energy loss due to air leakage. Rockwool insulation, on the other hand, may require additional sealing measures to achieve a similar level of air tightness.
- Rockwool insulation provides better thermal insulation and has a higher R-value compared to spray foam insulation.
- Spray foam insulation may require professional installation due to its application process, while rockwool insulation can be easily installed as batts or rolls by homeowners.
- Fire resistance properties are superior in rockwool insulation, as spray foam insulation requires the addition of fire-retardant chemicals.
- Both rockwool and spray foam insulation offer soundproofing qualities, but rockwool insulation generally performs better due to its denser and more fibrous structure.
- Rockwool insulation is more sustainable as it is made from naturally occurring materials, while spray foam insulation is typically made from petrochemicals.
Each insulation material has its unique strengths and considerations. While rockwool insulation excels in thermal insulation, soundproofing, fire resistance, moisture resistance, and sustainability, it’s important to consider the specific needs and requirements of your project when choosing the right insulation material.
Applications of Rockwool Insulation
Rockwool insulation is a versatile insulation material that finds applications in a wide range of buildings and facilities. Its excellent thermal insulation, soundproofing capabilities, fire resistance, and durability make it suitable for various construction projects. Let’s explore the key applications of rockwool insulation in residential buildings, commercial buildings, and industrial facilities.
Read more: How To Install Rockwool Insulation
Residential Buildings:
In residential buildings, rockwool insulation is a popular choice for enhancing energy efficiency and comfort. It can be used in various areas such as:
- Walls: Rockwool insulation can be installed in the exterior and interior walls of homes. It helps reduce heat transfer, keeping the indoor temperature stable and lowering heating and cooling costs.
- Roofs: Installing rockwool insulation in the attic or roof space creates a thermal barrier, preventing heat loss in the winter and heat gain in the summer. This leads to improved energy efficiency and increased comfort.
- Floors: Rockwool insulation installed in the floors helps reduce heat loss, minimize sound transmission, and improve acoustic comfort in multi-story residential buildings.
- Basements and Crawl Spaces: Rockwool insulation can be used in basements and crawl spaces to control moisture, prevent heat loss, and create a more comfortable environment.
Commercial Buildings:
In commercial buildings, rockwool insulation provides effective thermal insulation, soundproofing, and fire protection. It is commonly used in:
- Office Spaces: Rockwool insulation helps create a comfortable and quiet working environment by reducing heat transfer and minimizing noise transmission between offices.
- Retail Stores: Installing rockwool insulation in retail spaces improves thermal comfort for customers and creates a peaceful shopping experience by reducing outside noise.
- Healthcare Facilities: Rockwool insulation is used in hospitals and medical centers to enhance fire safety and soundproofing, creating a safe and quiet environment for patients and healthcare professionals.
- Hotels and Hospitality: Rockwool insulation in hotels provides thermal comfort and soundproofing, ensuring a peaceful and relaxing stay for guests.
Industrial Facilities:
In industrial facilities, rockwool insulation plays a crucial role in maintaining stable temperatures, ensuring safety, and improving energy efficiency. It is commonly used in:
- Power Plants: Rockwool insulation is used in power plants to insulate boilers, turbines, and ductwork, reducing heat loss and maximizing energy efficiency.
- Manufacturing Plants: In manufacturing facilities, rockwool insulation helps regulate temperatures in equipment, process areas, and storage areas.
- Warehouses: Rockwool insulation provides thermal insulation in warehouses, preventing temperature fluctuations that can damage stored goods.
- Industrial Ovens and Furnaces: Rockwool insulation is used to insulate ovens and furnaces, maintaining high temperatures and improving energy efficiency in industrial heating processes.
These are just a few examples of the many applications of rockwool insulation. Its versatility, durability, fire resistance, and excellent thermal and soundproofing properties make it an ideal choice for a wide range of residential, commercial, and industrial construction projects.
Installation and Safety Considerations
Installing rockwool insulation requires careful handling and adherence to safety measures to ensure a successful and secure installation process. Let’s explore the key considerations when it comes to handling and protective measures, installation methods, and safety precautions for rockwool insulation.
Read more: How To Cut Rockwool Insulation
Handling and Protective Measures:
When working with rockwool insulation, it is important to take the following handling and protective measures:
- Protective Clothing: Wear long-sleeved shirts, long pants, gloves, and safety glasses to protect your skin and eyes from irritation.
- Masks or Respirators: Use dust masks or respirators to prevent inhalation of airborne fibers. Choose masks with proper filtration capabilities.
- Ventilation: Work in well-ventilated areas or use an exhaust system to remove dust and fibers from the work area.
- Proper Storage: Store rockwool insulation in a dry and covered area to prevent moisture absorption, which can affect its performance.
- Handling Techniques: Handle the insulation material with care to avoid tearing or damaging the fibers. Avoid aggressive pulling or twisting that can cause excessive fiber release.
Installation Methods:
Rockwool insulation can be installed using different methods depending on the specific application. The most common installation methods include:
- Batts or Rolls: Rockwool insulation is available in pre-cut batts or rolls, which can be easily fitted between wall studs, rafters, or joists. Simply measure the space, cut the insulation to fit, and press it firmly into place.
- Blown-in: For larger areas or hard-to-reach spaces, rockwool insulation can be blown-in using specialized equipment. This method provides a customized fit and works well for attics or wall cavities.
- Spray or Adhesive Application: In some cases, rockwool insulation can be sprayed or applied using an adhesive to create a seamless coverage in irregularly shaped spaces or hard-to-access areas.
Consult the manufacturer’s instructions and guidelines for specific installation methods, as they may vary depending on the product and application.
Safety Precautions:
In addition to handling and protective measures, it is important to follow these safety precautions when working with rockwool insulation:
- Avoid Skin Contact: Minimize direct contact with the insulation material to prevent skin irritation. If skin contact does occur, wash the affected area thoroughly with soap and water.
- Avoid Inhalation: Avoid breathing in airborne fibers by using proper masks or respirators. If you do inhale fibers, move to an area with fresh air and seek medical attention if necessary.
- Dispose of Waste Properly: Collect any waste material and dispose of it according to local regulations. Avoid leaving loose fibers in the air or allowing them to accumulate in the work area.
- Keep Children and Pets Away: Restrict access to the installation area to prevent unintentional exposure to the insulation material.
- Work in a Well-Ventilated Area: Ensure sufficient airflow by opening windows, using fans, or using mechanical ventilation to help mitigate the concentration of airborne fibers.
By following these safety precautions and handling and protective measures, you can ensure a safe and successful installation of rockwool insulation, minimizing any potential health risks and achieving optimal performance.
Conclusion
Rockwool insulation is a versatile and highly effective insulation material that offers a range of properties and benefits. From residential buildings to commercial spaces and industrial facilities, rockwool insulation has proven to be a reliable choice for enhancing thermal insulation, soundproofing, fire resistance, and moisture resistance.
The composition of rockwool insulation, including its basalt rock core, binder, and additives, contributes to its durability and performance. The manufacturing process, which involves melting and spinning, fiber formation, binding, curing, and cutting and shaping, ensures the creation of a high-quality insulation material.
The thermal insulation capabilities of rockwool insulation help maintain comfortable indoor temperatures, reduce energy consumption, and lower heating and cooling costs. Its soundproofing abilities make it an ideal choice for creating quiet and peaceful environments in homes, offices, and other spaces.
Rockwool insulation’s inherent fire resistance exceeds the requirements of many building codes, providing reliable protection against potential fires. Its moisture resistance helps prevent the growth of mold or mildew and maintains its insulation performance over time.
In addition to its performance qualities, rockwool insulation is a sustainable choice. It is made from natural and abundant materials, reducing its environmental impact. Furthermore, it is recyclable and can be reused or repurposed at the end of its life cycle.
When comparing rockwool insulation to other common insulation materials, such as fiberglass insulation, cellulose insulation, and spray foam insulation, it offers advantages such as better fire resistance, soundproofing, and moisture resistance.
The applications of rockwool insulation are widespread. It can be used in residential buildings for walls, roofs, floors, and basements; in commercial buildings for offices, retail stores, and healthcare facilities; and in industrial facilities for power plants, manufacturing plants, and warehouses.
During the installation process, it is important to adhere to proper handling and protective measures, follow specific installation methods, and take necessary safety precautions to ensure the success and safety of the project.
In conclusion, rockwool insulation is a reliable, versatile, and sustainable insulation material that offers excellent thermal insulation, soundproofing, fire resistance, and moisture resistance. Its applications are vast, and its performance qualities contribute to energy efficiency, comfort, and safety in various building types. When choosing insulation for your project, consider the benefits and advantages of rockwool insulation to ensure optimal results and long-lasting performance.
Frequently Asked Questions about What Is Rockwool Insulation Made Out Of
Was this page helpful?
At Storables.com, we guarantee accurate and reliable information. Our content, validated by Expert Board Contributors, is crafted following stringent Editorial Policies. We're committed to providing you with well-researched, expert-backed insights for all your informational needs.
0 thoughts on “What Is Rockwool Insulation Made Out Of”