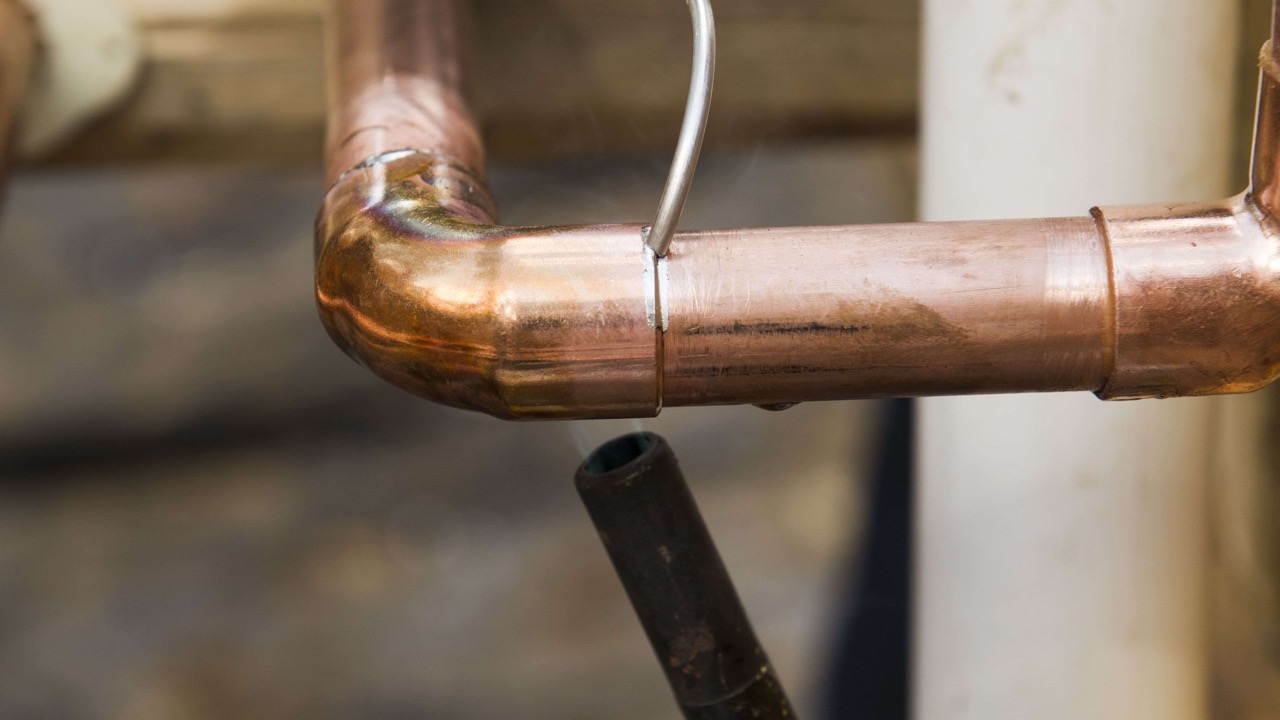
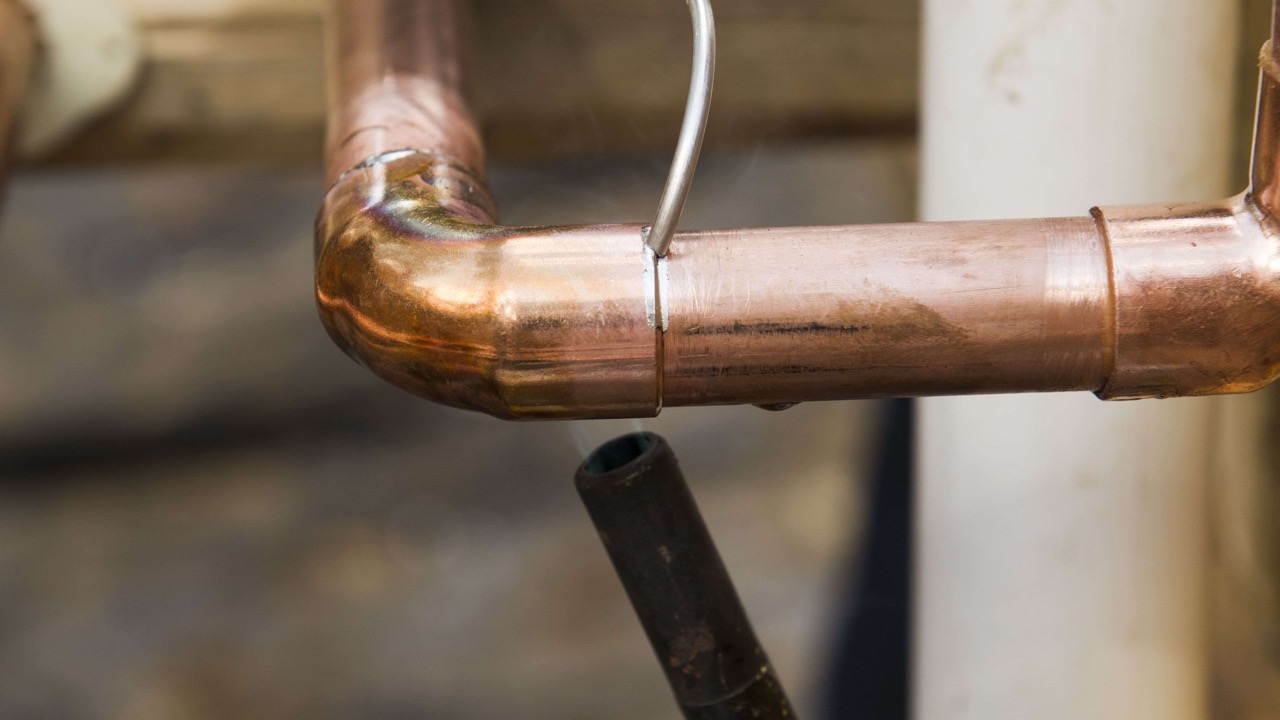
Articles
What Temperature Does Plumbing Solder Melt
Modified: March 1, 2024
Discover the ideal temperature at which plumbing solder melts and learn how to effectively use it in your plumbing projects. Read more in our informative articles.
(Many of the links in this article redirect to a specific reviewed product. Your purchase of these products through affiliate links helps to generate commission for Storables.com, at no extra cost. Learn more)
Introduction
When it comes to plumbing, soldering is an essential skill that every plumber must possess. Soldering involves joining two pieces of metal, such as copper pipes, using a filler metal known as solder. This process forms a strong and leak-proof bond that ensures the integrity of plumbing systems. However, to successfully solder plumbing joints, it is crucial to understand the melting temperature of plumbing solder.
In this article, we will explore what plumbing solder is and delve into the factors that determine its melting temperature. We will also discuss the different types of plumbing solder available in the market and their varying melting temperature ranges. Finally, we will highlight the importance of choosing the right soldering temperature and provide some useful tips for soldering plumbing joints effectively.
Whether you are a seasoned plumber or a DIY enthusiast looking to tackle some plumbing repairs, understanding the melting temperature of plumbing solder is vital to ensure successful and long-lasting connections. So, let us dive into the fascinating world of plumbing solder and discover its secrets.
Key Takeaways:
- Understanding the melting temperature of plumbing solder is crucial for creating strong and durable connections in plumbing systems, ensuring long-lasting and leak-free joints.
- By considering factors such as solder composition, flux type, and heat source, plumbers and DIY enthusiasts can select the appropriate solder alloy and achieve successful soldering connections.
Read more: At What Temperature Does Crystal Glass Melt?
Understanding Plumbing Solder
Solder is a type of metal alloy that is used to join two pieces of metal together by melting the solder and allowing it to cool and solidify. In the context of plumbing, soldering is commonly used to connect copper pipes and fittings. Plumbing solder typically consists of a combination of tin and lead, although lead-free solder alternatives are becoming increasingly popular due to health and environmental concerns.
The composition of plumbing solder plays a crucial role in determining its melting temperature and soldering properties. The addition of other metals, such as silver or antimony, can modify the melting temperature and improve the strength and durability of the solder joint.
Solder is available in various forms, including solid wire, core wire, and soldering paste. Solid wire solder is the most commonly used form and is available in different diameters. Core wire solder contains a flux core, which aids in cleaning and preparing the surfaces to be soldered. Soldering paste consists of a mixture of flux and solder powder and is often used for intricate soldering applications.
The flux is an essential component in the soldering process as it helps remove oxidation and impurities from the metal surfaces, ensuring a clean and reliable solder joint. Flux is available in liquid, paste, or solid form and should be applied to the surfaces before soldering.
It is important to note that plumbing solder has a distinct melting temperature, which must be reached during the soldering process to achieve a successful joint. Understanding the factors that affect the melting temperature of plumbing solder is crucial in ensuring proper soldering techniques.
Now that we have a basic understanding of plumbing solder, let us explore the factors that influence its melting temperature and how they can impact the soldering process.
Factors Affecting Solder Melting Temperature
The melting temperature of solder is influenced by several factors, which affect the overall strength and quality of the solder joint. Understanding these factors is essential for achieving successful soldering in plumbing applications. Let’s explore the key factors affecting solder melting temperature:
- Composition: The composition of the solder alloy greatly affects its melting temperature. Different combinations of metals, such as tin, lead, silver, and antimony, result in solder alloys with varying melting points. For instance, lead-based solders tend to have lower melting temperatures compared to lead-free alternatives.
- Lead Content: Lead is commonly used in solder alloys due to its low melting point and excellent soldering properties. However, due to environmental concerns and health risks associated with lead exposure, lead-free solders have gained popularity. Lead-free solders typically have higher melting temperatures compared to lead-based solders, making them a suitable alternative for various plumbing applications.
- Flux: The type and quality of flux used during soldering can affect the melting temperature of the solder. The flux helps remove oxides and impurities from the metal surfaces, promoting better wetting and adhesion. The presence of flux can lower the effective melting temperature of the solder, allowing it to flow and bond with the metal surfaces effectively.
- Heat Source: The heat source used during soldering plays a significant role in achieving the appropriate soldering temperature. Different heat sources, such as soldering irons, torches, or soldering stations, produce varying amounts of heat, influencing the rate at which the solder melts. It is essential to choose a heat source that provides enough heat to melt the solder without damaging the surrounding components or materials.
- Application: The specific application and intended use of the solder joint can also impact the desired melting temperature. For instance, soldering joints in high-temperature environments or those exposed to constant stress may require solder with a higher melting temperature to ensure long-term durability.
- Soldering Technique: The soldering technique employed can affect the melting temperature and overall quality of the solder joint. Factors such as the duration and intensity of heat applied, proper flux application, and adequate surface preparation play crucial roles in achieving optimal soldering temperature and creating a reliable bond.
By considering these factors, plumbers and DIY enthusiasts can select the appropriate solder alloy and adjust their soldering techniques to ensure a successful and durable solder joint.
Common Types of Plumbing Solder
There are several types of plumbing solder available in the market, each with its own unique melting temperature range and properties. Let’s explore some of the most common types of plumbing solder:
- Lead-Tin Solder: Lead-tin solder is one of the traditional types of solder used in plumbing applications. It typically consists of a mixture of tin and lead, with varying ratios depending on the desired properties. Lead-tin solder has a relatively low melting temperature, making it easy to work with. However, due to health and environmental concerns, lead-based solders are becoming less common and are being phased out in many regions.
- Lead-Free Solder: Lead-free solder is the preferred choice for plumbing applications due to its safer and more eco-friendly composition. Lead-free solders are typically composed of alloys such as tin, silver, and copper. These solders have a higher melting temperature compared to lead-tin solder. Common lead-free solder alloys include Sn-Cu (tin-copper), Sn-Cu-Ag (tin-copper-silver), and Sn-Ag-Cu (tin-silver-copper).
- Silver Solder: Silver solder, also known as silver brazing, is a type of solder that contains a significant amount of silver. Silver solder has a higher melting temperature compared to lead-based and lead-free solders, making it suitable for applications where high strength and durability are required. Silver solder is often used in plumbing applications where copper pipes are joined.
- Aluminum Solder: Aluminum solder is specifically designed for soldering aluminum and aluminum alloys. It has a lower melting temperature compared to other solders, allowing for successful bonding without damaging the base metal. Aluminum solder typically contains zinc and other elements to promote better adhesion and strength.
- Flux-Core Solder: Flux-core solder, also known as rosin-core solder, is a type of solder that has a flux core running through the center of the solder wire. Flux-core solder simplifies the soldering process by eliminating the need for separate flux application. The flux core assists in cleaning and preparing the metal surfaces for soldering.
It is important to identify the specific type of plumbing solder needed for each application based on factors such as the materials being joined, the desired strength and durability, and the necessary melting temperature. Consulting with a knowledgeable professional or referring to manufacturer guidelines can help ensure the correct selection of plumbing solder for a particular project.
The melting point of plumbing solder is typically around 450-470°F (232-243°C). It’s important to use a soldering iron or torch at the appropriate temperature to ensure a strong and secure bond.
Melting Temperature Range of Plumbing Solder
The melting temperature range of plumbing solder can vary depending on the specific type of solder alloy used. Understanding these temperature ranges is crucial for achieving successful soldering connections. Let’s explore the melting temperature ranges of some common types of plumbing solder:
- Lead-Tin Solder: Lead-tin solder typically has a melting temperature range between 180°C (356°F) and 190°C (374°F). The exact melting temperature can vary depending on the composition of the solder alloy, with higher lead content resulting in a lower melting temperature. It is important to note that lead-based solders are being phased out due to health and environmental concerns in many regions.
- Lead-Free Solder: Lead-free solders generally have higher melting temperature ranges compared to lead-tin solder. The melting temperature can range from 220°C (428°F) to 250°C (482°F). The specific melting temperature depends on the composition of the lead-free solder alloy, with variations such as tin-silver-copper (Sn-Ag-Cu) solder typically having a lower melting temperature compared to tin-copper-silver (Sn-Cu-Ag) solder.
- Silver Solder: Silver solder, also known as silver brazing, has a higher melting temperature compared to lead-based and lead-free solders, typically ranging from 600°C (1112°F) to 800°C (1472°F). This higher melting temperature makes silver solder suitable for applications where high strength and durability are required, such as joining copper pipes.
- Aluminum Solder: Aluminum solder has a lower melting temperature range compared to other solder alloys, usually between 380°C (716°F) and 450°C (842°F). This lower melting temperature helps prevent damage to the aluminum base metal during soldering while ensuring a strong bond.
- Flux-Core Solder: Flux-core solder typically has a melting temperature range similar to the solder alloy it contains. For example, lead-tin flux-core solder will have a range between 180°C (356°F) and 190°C (374°F), similar to lead-tin solder without a flux core. Similarly, lead-free flux-core solder will have a melting temperature range corresponding to the lead-free solder alloy used.
It is important to note that these melting temperature ranges serve as general guidelines, and specific solder alloys may have slightly different temperature requirements. Always refer to the manufacturer’s guidelines and instructions when using plumbing solder to ensure proper melting temperatures and achieve reliable and durable soldered connections.
Read more: What Temperature Do Candles Melt
Importance of Choosing the Right Soldering Temperature
Choosing the correct soldering temperature is crucial for achieving successful soldered connections in plumbing projects. The right temperature ensures proper bonding, strength, and durability of the solder joint. Let’s explore the importance of choosing the right soldering temperature:
- Effective Flow and Bonding: Soldering at the correct temperature allows the solder to melt and flow smoothly, ensuring good wetting and bonding between the solder and the metal surfaces being joined. This creates a strong and reliable bond that can withstand the rigors of plumbing applications, such as pressure and temperature fluctuations.
- Prevention of Cold Joints: Cold joints occur when the solder does not fully melt or does not bond properly with the metal surfaces. This can result in weak and unreliable connections that are prone to leaks and failure. By soldering at the appropriate temperature, the solder can fully penetrate and bond with the metal, minimizing the risk of cold joints.
- Avoidance of Overheating: Soldering at excessively high temperatures can lead to overheating, which can damage the plumbing components, such as pipes, fittings, or nearby materials. Overheating can weaken the structural integrity of the materials and result in leaks or other issues. By using the correct soldering temperature, the heat is focused on melting the solder instead of damaging the surrounding components.
- Prevention of Underheating: Underheating occurs when the soldering temperature is too low for the solder to melt properly, resulting in weak and unreliable joints. Underheated joints are more prone to leaks and failure, compromising the overall integrity of the plumbing system. By using the appropriate soldering temperature, the solder can reach its full melting potential, ensuring secure and durable connections.
- Optimal Soldering Conditions: Each type of solder alloy has a specific temperature range within which it performs optimally. Operating within this range ensures that the solder flows, adheres, and solidifies correctly, producing strong and durable joints. Consulting the manufacturer’s guidelines or technical data sheets for the specific solder alloy being used can provide valuable information regarding the recommended soldering temperature.
By selecting the right soldering temperature and ensuring proper heat application during the soldering process, plumbers and DIY enthusiasts can achieve reliable, leak-free soldered connections that withstand the test of time. It is crucial to consistently monitor and adjust the heat source to maintain the desired soldering temperature throughout the process.
Tips for Soldering Plumbing Joints
Soldering plumbing joints requires precision and proper technique to ensure strong and leak-free connections. Here are some useful tips to follow when soldering plumbing joints:
- Clean Surfaces: Before soldering, ensure that the surfaces to be soldered are clean and free from debris, oxidation, and grease. Use a wire brush or abrasive cloth to remove any residue and create a clean surface for better solder adhesion.
- Apply Flux: Apply flux to the cleaned surfaces of the plumbing components. Flux helps remove oxidation, improves solder flow, and promotes better wetting. Use a brush or applicator to evenly apply the flux to the joint surfaces.
- Heat Distribution: Distribute the heat evenly around the joint by moving the heat source, such as a soldering iron or torch, in a circular motion. This ensures that the solder melts uniformly and creates strong bonds throughout the joint.
- Avoid Excessive Heat: Avoid applying excessive heat to the joint as it can damage the plumbing components or neighboring areas. Find the right balance between providing enough heat to melt the solder and preventing overheating that can compromise the integrity of the joint.
- Proper Solder Application: Apply the solder to the joint, allowing it to flow into the gap between the two plumbing components. Ensure that the solder covers the joint completely, creating a watertight seal. Avoid excessive solder, as it can lead to drips or uneven joints.
- Watch for Capillary Action: Take advantage of capillary action, which is the ability of the solder to be drawn into the joint through the heat and flux. As you apply heat and solder, observe how the solder is drawn into the joint, indicating proper bonding and penetration.
- Cooling without Disturbance: Allow the soldered joint to cool naturally without any disturbance. Moving or jostling the joint while it is still hot can lead to weakened connections or leaks. Give it sufficient time to cool and solidify before handling or applying any pressure.
- Inspect for Leaks: After the joint has cooled, inspect it for any signs of leaks or weak spots. Use a dry cloth to wipe away any excess flux or solder residue. Test the joint by running water through the plumbing system and closely examine for any leaks. If any leaks are detected, heat and reflow the solder to reinforce the joint.
- Practice and Patience: Soldering requires practice and patience to master the technique. Don’t be discouraged if your first attempts are not perfect. Take the time to practice on scrap pieces of pipe or fittings to improve your soldering skills before tackling important plumbing projects.
By following these tips, you can ensure proper soldering techniques and achieve strong, durable, and leak-free plumbing joints. Remember to prioritize safety by wearing appropriate protective gear and working in a well-ventilated area during the soldering process.
Conclusion
Soldering is an essential skill for plumbers and DIY enthusiasts alike, ensuring secure and leak-free connections in plumbing systems. Understanding the melting temperature of plumbing solder is crucial for achieving successful soldered joints. By choosing the right soldering temperature and using the appropriate solder alloy, you can create strong and durable connections that withstand the test of time.
We have explored the factors that influence solder melting temperature, such as the composition of the solder alloy, the presence of flux, the heat source used, and the specific application. We have also discussed the common types of plumbing solder available, including lead-tin, lead-free, silver, aluminum, and flux-core solder.
It is important to remember the melting temperature range of different solder alloys and select the appropriate one based on your specific needs and plumbing application. Lead-free solder, in particular, has gained popularity due to its safer and more environmentally friendly composition.
By following the recommended tips for soldering plumbing joints, such as cleaning the surfaces, applying flux, and distributing heat evenly, you can ensure proper solder adhesion and minimize the risk of leaks or weak connections. Regularly inspecting soldered joints for leaks and making any necessary adjustments or repairs further ensures the longevity and integrity of your plumbing system.
Remember that soldering requires practice and patience to master. Don’t be discouraged if your initial soldering attempts are not perfect. With time and experience, you will develop the skills necessary to achieve professional-level soldered joints.
In conclusion, understanding the melting temperature of plumbing solder and following proper soldering techniques are essential for creating reliable and durable connections in plumbing systems. With the right knowledge and skills, you can confidently tackle plumbing projects and ensure the integrity of your plumbing system for years to come.
Frequently Asked Questions about What Temperature Does Plumbing Solder Melt
Was this page helpful?
At Storables.com, we guarantee accurate and reliable information. Our content, validated by Expert Board Contributors, is crafted following stringent Editorial Policies. We're committed to providing you with well-researched, expert-backed insights for all your informational needs.
0 thoughts on “What Temperature Does Plumbing Solder Melt”