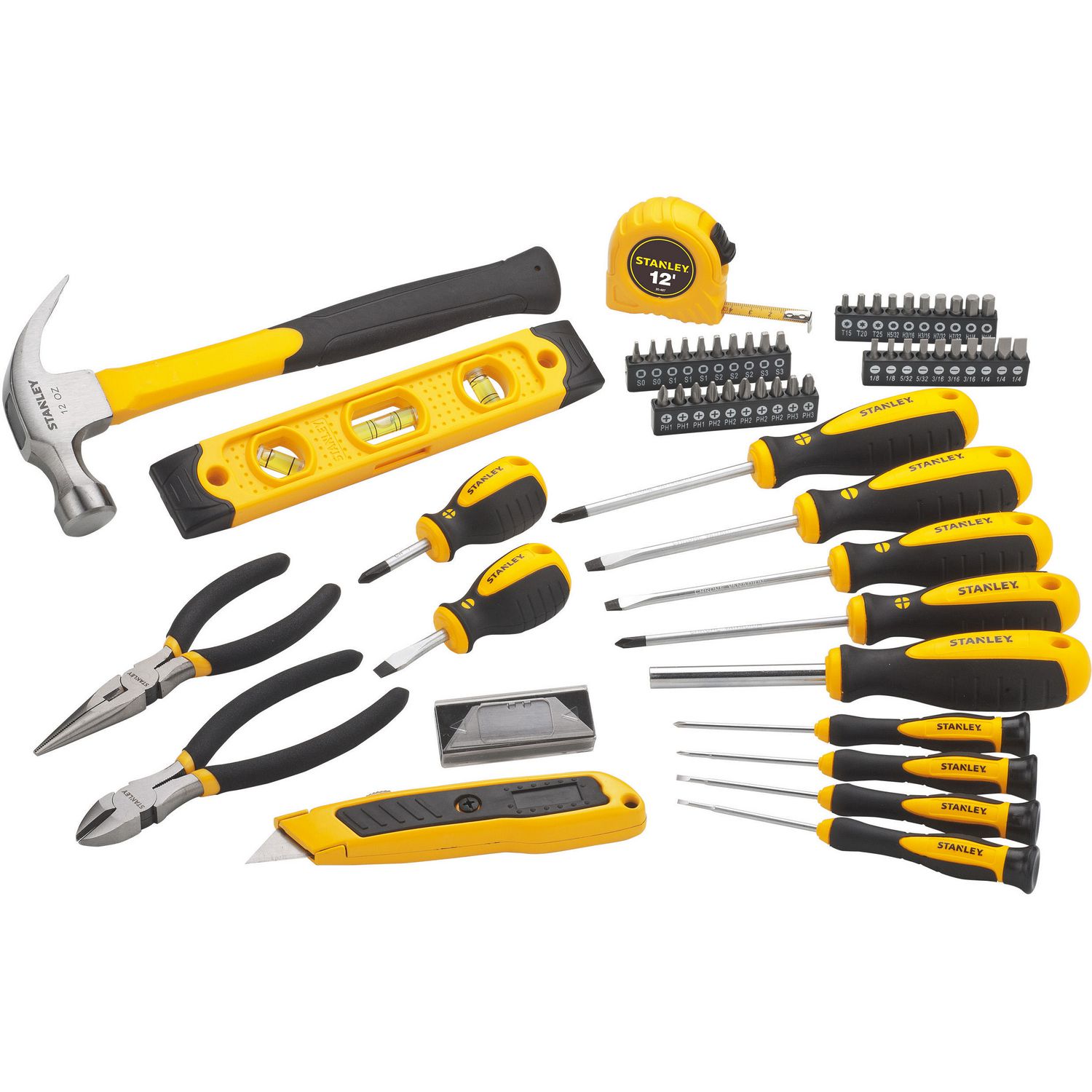
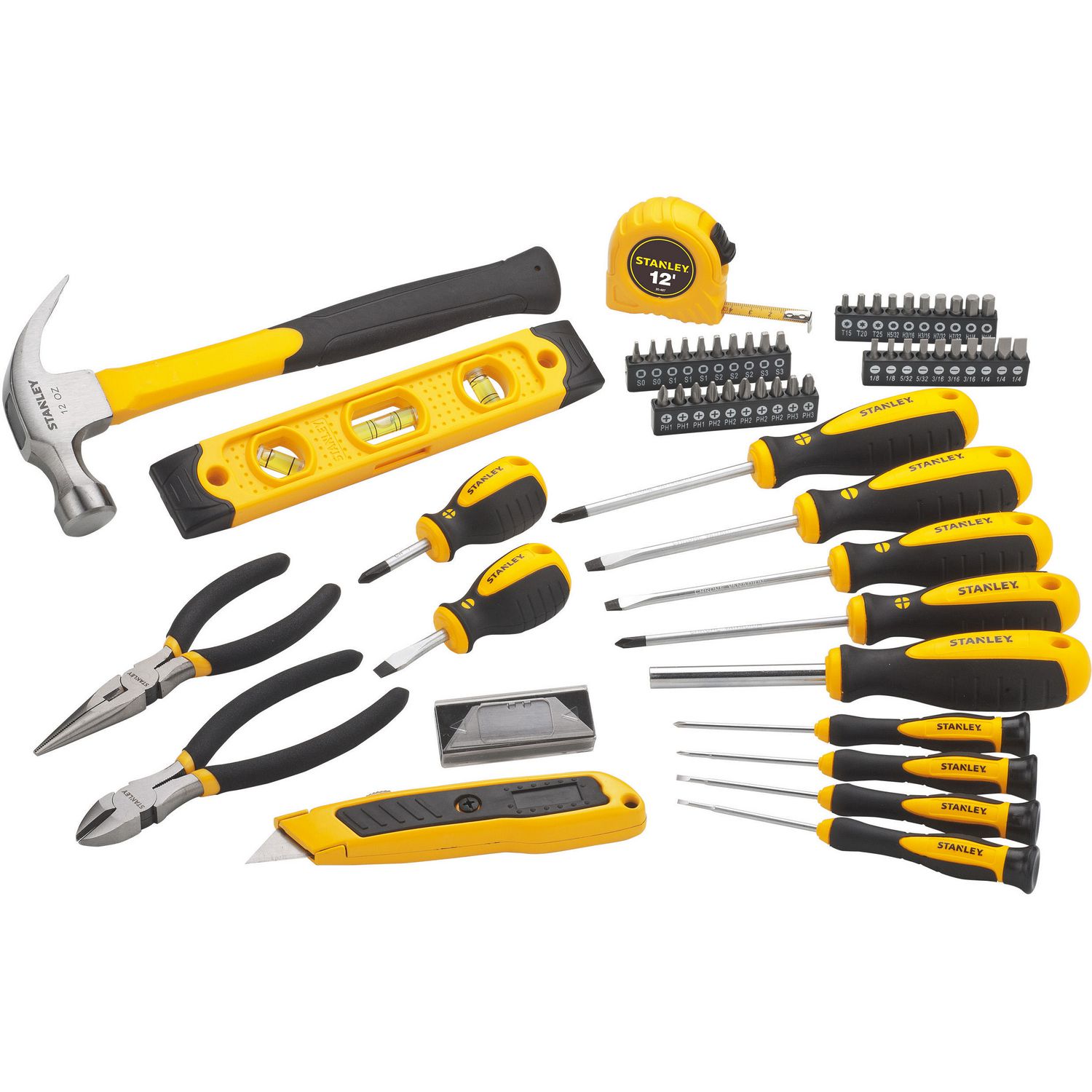
Articles
Where Are Stanley Hand Tools Made
Modified: February 23, 2024
Discover the origin of Stanley hand tools. Explore our informative articles that reveal where these trusted tools are made and what sets them apart.
(Many of the links in this article redirect to a specific reviewed product. Your purchase of these products through affiliate links helps to generate commission for Storables.com, at no extra cost. Learn more)
Introduction
Stanley Hand Tools is a renowned brand that has been providing high-quality tools to professionals and DIY enthusiasts for over a century. From hammers and screwdrivers to tape measures and utility knives, Stanley Hand Tools is synonymous with reliability and durability. But have you ever wondered where these tools are made?
In this article, we will delve into the fascinating world of Stanley Hand Tools manufacturing, exploring the history of the brand, the manufacturing processes, the locations of their production facilities, and the measures taken to ensure quality control. We will also discuss the impact of globalization on their manufacturing practices and delve into future trends and innovations in Stanley Hand Tools production.
So, if you are curious to know more about where Stanley Hand Tools are made and the intricacies behind their manufacturing process, read on!
Key Takeaways:
- Stanley Hand Tools has a rich history dating back to 1843, and its commitment to quality is evident in its meticulous manufacturing processes and stringent quality control measures.
- Globalization has allowed Stanley Hand Tools to expand its market reach, establish efficient supply chains, and embrace innovation, sustainability, and corporate responsibility to remain competitive in the global marketplace.
Read more: Where Are Snap-On Hand Tools Made
History of Stanley Hand Tools
The story of Stanley Hand Tools dates back to 1843 when Frederick Stanley founded a small company in New Britain, Connecticut. Initially, the company focused on producing bolts, hinges, and other hardware items. However, it wasn’t until the late 19th century that Stanley Hand Tools started gaining recognition for their innovative tools.
In 1876, Frederick Stanley’s cousin, Henry Stanley, joined the company, and together they began experimenting with new tool designs. One of their most notable inventions was the Bailey bench plane, which revolutionized woodworking by introducing a more efficient and adjustable design.
Over the years, Stanley Hand Tools continued to introduce groundbreaking tools. In 1931, they launched the first steel tape rule, replacing the traditional cloth or leather tapes. This invention set a new standard for accuracy and durability in measurement tools.
By the mid-20th century, Stanley Hand Tools had established itself as a leader in the industry. They expanded their product line to include a wide range of hand tools such as saws, chisels, levels, and wrenches. Their commitment to quality and innovation made them a trusted brand among professionals and DIY enthusiasts alike.
Stanley Hand Tools also played a crucial role in the war effort during World War II. They produced a variety of tools and equipment for the military, contributing to the war effort and gaining further recognition for their craftsmanship.
Today, Stanley Hand Tools continues to be a prominent and respected brand in the tool industry. Their rich history and dedication to providing reliable tools have made them a household name for professionals and hobbyists around the world.
Manufacturing Process of Stanley Hand Tools
Stanley Hand Tools takes great pride in ensuring that their tools are manufactured to the highest standards of quality and precision. The manufacturing process involves several key steps that guarantee the durability and functionality of each tool.
1. Design and Engineering: Before production begins, Stanley Hand Tools invests significant time and resources in designing and engineering their tools. Their team of engineers and designers utilizes advanced software and technology to create innovative and ergonomic tool designs, ensuring optimal performance and user comfort.
2. Material Selection: A crucial aspect of the manufacturing process is the selection of high-quality materials. Stanley Hand Tools meticulously chooses materials that offer strength, durability, and resistance to wear and tear. From the steel used in sockets to the handles of screwdrivers, each component is carefully considered to ensure longevity and reliability.
3. Tool Manufacturing: Once the designs and materials are finalized, the manufacturing process begins. Depending on the tool, different techniques such as forging, casting, or machining are employed to shape the components. For example, hammers may be forged to create the desired shape and strength, while screwdriver handles may be machined for precise grip and control.
4. Assembly: After the individual components are produced, they are carefully assembled to create the final product. Experienced technicians and craftsmen meticulously fit each piece together, ensuring proper alignment and functionality. Adhesives, fasteners, and welding techniques are used to securely assemble the tools.
5. Finishing: Once the tools are assembled, they undergo several finishing processes. These may include sanding, grinding, polishing, or coating to enhance the appearance and protect against corrosion. The finishing stage also involves quality checks to ensure that the tools meet the brand’s standards.
6. Testing and Quality Control: Stanley Hand Tools places a strong emphasis on quality control throughout the manufacturing process. Each tool undergoes rigorous testing to verify its performance and durability. This includes load testing, torque testing, and various other checks to ensure that the tools can withstand demanding tasks and continue to perform reliably over time.
7. Packaging and Distribution: Once the tools pass the quality control tests, they are packaged and prepared for distribution. Stanley Hand Tools utilizes eco-friendly packaging materials whenever possible, aligning with their commitment to sustainability.
By following these meticulous manufacturing processes, Stanley Hand Tools ensures that each tool meets the highest standards of quality and functionality. This dedication to excellence has established them as a trusted brand in the industry.
Locations of Stanley Hand Tools Manufacturing
Stanley Hand Tools operates manufacturing facilities across the globe to meet the demand for their high-quality tools. These strategically located facilities allow the brand to efficiently produce and distribute their products to customers worldwide. Here are some of the key locations where Stanley Hand Tools are manufactured:
1. New Britain, Connecticut, USA: As the birthplace of the company, New Britain remains an important manufacturing hub for Stanley Hand Tools. The facility here focuses on producing a wide range of hand tools, including wrenches, screwdrivers, and tape measures.
2. Shelbyville, Tennessee, USA: Stanley Hand Tools has a manufacturing facility in Shelbyville that specializes in the production of saws and cutting tools. This location possesses state-of-the-art machinery and equipment to ensure precision and efficiency in the manufacturing process.
3. Mexico: To cater to the growing demand in the Latin American market, Stanley Hand Tools has manufacturing facilities in Mexico. These facilities manufacture a variety of hand tools and are essential in ensuring timely delivery to customers in the region.
4. China: China is a prominent manufacturing base for many global brands, and Stanley Hand Tools is no exception. The brand has several manufacturing facilities in China that produce a wide range of tools, including pliers, hammers, and wrenches. These facilities leverage advanced manufacturing techniques and technologies to meet high production volumes.
5. Europe: Stanley Hand Tools also has manufacturing facilities in various European countries, including the United Kingdom and Germany. These facilities cater to the demand of the European market and ensure localized production to meet specific regional requirements.
6. Other Locations: In addition to the aforementioned locations, Stanley Hand Tools has manufacturing facilities in other countries as well. These locations include Australia, India, and Brazil, among others. Each facility is strategically placed to optimize production and meet the diverse needs of customers in different regions.
Having manufacturing facilities spread across different continents enables Stanley Hand Tools to effectively serve their global customer base. This diverse manufacturing footprint ensures a steady supply of high-quality tools to professionals and DIY enthusiasts worldwide.
Stanley Hand Tools are made in various locations around the world, including the United States, China, Mexico, and the United Kingdom. Check the specific product for its country of origin.
Quality Control Measures in Stanley Hand Tool Production
Stanley Hand Tools is committed to delivering tools of the highest quality, and as such, they implement stringent quality control measures throughout their production process. These measures are designed to ensure that every tool that leaves their manufacturing facilities meets the brand’s standards of excellence. Here are some of the key quality control measures employed by Stanley Hand Tools:
1. Raw Material Inspection: The first step in the quality control process is inspecting the raw materials used in the manufacturing of tools. Stanley Hand Tools carefully selects materials that meet strict criteria for strength, durability, and performance. Upon arrival at the manufacturing facility, these materials undergo thorough inspection to ensure they meet the required standards.
2. In-Process Inspections: During the manufacturing process, various inspections are conducted at critical stages to identify any potential defects or deviations from specifications. Skilled technicians closely monitor each tool’s production, ensuring that the desired quality standards are maintained. Any issues discovered during these inspections are addressed promptly to prevent further manufacturing of substandard products.
3. Performance Testing: Once the tools are assembled, they undergo rigorous testing to assess their performance under real-world conditions. This testing includes load testing, torque testing, and other functional tests, depending on the specific tool type. Tools must meet or exceed predefined performance criteria to pass the quality control standards.
4. Measurement Accuracy: Stanley Hand Tools places a strong emphasis on measurement accuracy, especially for tools such as rulers, levels, and tape measures. These tools are inspected using calibrated devices to ensure that their measurements are precise and reliable. This guarantees that professionals and DIY users can rely on Stanley Hand Tools for accurate measurements in their projects.
5. Random Sampling: In addition to in-process inspections and performance testing, Stanley Hand Tools utilizes random sampling to further verify the quality of their products. This involves randomly selecting tools from the production line and conducting additional inspections to identify any potential issues and ensure consistent quality across the entire product range.
6. Quality Assurance Certifications: Stanley Hand Tools adheres to various international quality assurance standards and holds certifications such as ISO 9001. These certifications validate their commitment to maintaining consistent quality and continuous improvement in their manufacturing processes.
By implementing these robust quality control measures, Stanley Hand Tools ensures that their tools meet the highest standards of performance, durability, and reliability. This commitment to quality has solidified their reputation as a trusted and dependable brand in the hand tool industry.
Read more: Where Are Pittsburgh Hand Tools Made
Impact of Globalization on Stanley Hand Tool Manufacturing
Globalization has had a profound impact on the manufacturing practices of companies worldwide, and Stanley Hand Tools is no exception. As a global brand, Stanley Hand Tools has embraced the opportunities and challenges that come with operating in a globalized market. Here are some key impacts of globalization on Stanley Hand Tool manufacturing:
1. Expanded Market Reach: Globalization has provided Stanley Hand Tools with access to a broader customer base in markets around the world. With manufacturing facilities strategically located across different continents, the brand can efficiently cater to the needs of diverse markets. This expansive reach has significantly contributed to the growth and success of Stanley Hand Tools.
2. Efficient Supply Chain: Globalization has enabled Stanley Hand Tools to establish an efficient and streamlined supply chain. By sourcing materials and components from different locations, the brand can benefit from cost-effective options and ensure a steady supply of resources. This allows for optimized production and faster delivery of their tools to customers worldwide.
3. Manufacturing Cost Optimization: Globalization has prompted Stanley Hand Tools to explore cost optimization strategies. By establishing manufacturing facilities in countries with lower labor and production costs, they can remain competitive in the market. This cost optimization helps to keep the prices of their tools affordable without compromising on quality.
4. Access to Technological Advances: Globalization has facilitated the exchange of ideas and technological advancements in manufacturing processes. Stanley Hand Tools can leverage the latest technologies, machinery, and equipment from different regions to enhance their manufacturing capabilities. This enables them to improve efficiency, precision, and overall product quality.
5. Cultural Exchange and Innovation: Operating on a global scale exposes Stanley Hand Tools to diverse perspectives and ideas. This cultural exchange helps drive innovation and inspires the development of new tools and features. Customers worldwide benefit from the cross-pollination of ideas, resulting in tools that are versatile, practical, and tailored to the specific needs of different markets.
6. Sustainability and Corporate Responsibility: Globalization has also influenced Stanley Hand Tools’ approach to sustainability and corporate responsibility. The brand recognizes the importance of environmental stewardship and social responsibility in today’s globalized world. As such, they strive to minimize their ecological footprint through responsible sourcing, eco-friendly packaging, and sustainable production practices.
While globalization has brought numerous benefits to Stanley Hand Tools, it has also presented challenges. Increased competition from global manufacturers requires them to continuously innovate, enhance product quality, and maintain customer trust. However, as an industry leader, Stanley Hand Tools has successfully navigated these challenges and thrived in the global marketplace.
Future Trends and Innovations in Stanley Hand Tools Manufacturing
As technology and customer needs continue to evolve, Stanley Hand Tools remains at the forefront of innovation in hand tool manufacturing. The brand constantly explores new trends and technologies to deliver tools that are more efficient, ergonomic, and user-friendly. Here are some key future trends and innovations that we can expect to see in Stanley Hand Tools manufacturing:
1. Ergonomic Designs: Stanley Hand Tools recognizes the importance of user comfort and ergonomics. Future tool designs will focus on enhancing user experience through improved grip, reduced fatigue, and optimal weight distribution. These ergonomic designs will make tools more comfortable to use for extended periods, increasing productivity and efficiency.
2. Smart Tools: With the rise of the Internet of Things (IoT), we can anticipate the development of smart hand tools. These tools will be equipped with sensors, Wi-Fi connectivity, and data tracking capabilities. Smart tools could offer real-time feedback, measurement accuracy, and even integrated apps for project management and collaboration.
3. Enhanced Durability: Stanley Hand Tools will continue to invest in research and development to enhance the durability and longevity of their tools. This may involve utilizing advanced materials, coatings, and manufacturing techniques to create tools that are more resistant to wear, corrosion, and impact damage.
4. Multi-purpose Tools: Future tool designs may focus on versatility and multifunctionality, combining multiple tools into a single device. This trend caters to the needs of users seeking compact and space-saving solutions without sacrificing functionality. Multi-purpose tools provide convenience and efficiency in various applications.
5. Integration of Power and Hand Tools: The integration of power and hand tools is another area of innovation in Stanley Hand Tools manufacturing. Hybrid tools that combine the convenience of power tools with the precision and control of hand tools will likely emerge. This integration aims to deliver the best of both worlds, allowing users to tackle a wide range of tasks with a single tool.
6. Integration of New Technologies: Stanley Hand Tools will continue to explore and incorporate emerging technologies into their manufacturing processes. This includes advanced automation, robotics, artificial intelligence, and 3D printing. These technologies will streamline production, improve precision, and provide more customization options.
As Stanley Hand Tools embraces these future trends and innovations, their commitment to quality, durability, and customer satisfaction remains steadfast. Through continuous research and development, they aim to provide professionals and DIY enthusiasts with tools that enable them to accomplish their tasks with greater efficiency and precision.
Conclusion
Stanley Hand Tools has a rich history of providing professionals and DIY enthusiasts with reliable and durable tools for their various projects. From their humble beginnings in New Britain, Connecticut, Stanley Hand Tools has evolved into a global brand with manufacturing facilities across different continents.
Their commitment to delivering high-quality tools is evident in their meticulous manufacturing processes and stringent quality control measures. From the careful selection of materials to the rigorous testing of each tool, Stanley Hand Tools ensures that their products meet the highest standards of excellence.
Globalization has played a significant role in shaping Stanley Hand Tools manufacturing practices. It has allowed them to expand their market reach and establish efficient supply chains, enabling them to meet the demands of customers around the world. While globalization has presented challenges, Stanley Hand Tools has embraced innovation, sustainability, and corporate responsibility to remain competitive in the global marketplace.
Looking towards the future, Stanley Hand Tools continues to pioneer trends and innovations in hand tool manufacturing. With a focus on ergonomic designs, smart tools, enhanced durability, multi-purpose functionality, integration of power and hand tools, and the integration of new technologies, they aim to deliver tools that are efficient, user-friendly, and versatile.
In conclusion, Stanley Hand Tools has cemented its position as a trusted and respected brand in the hand tool industry. With a rich history, a commitment to quality, and a drive for innovation, they continue to provide professionals and DIY enthusiasts with tools that empower them to tackle projects with confidence and precision.
Frequently Asked Questions about Where Are Stanley Hand Tools Made
Was this page helpful?
At Storables.com, we guarantee accurate and reliable information. Our content, validated by Expert Board Contributors, is crafted following stringent Editorial Policies. We're committed to providing you with well-researched, expert-backed insights for all your informational needs.
0 thoughts on “Where Are Stanley Hand Tools Made”