Home>Articles>Which Of The Following Is Not A Recommended Safety Measure For Power Tools?
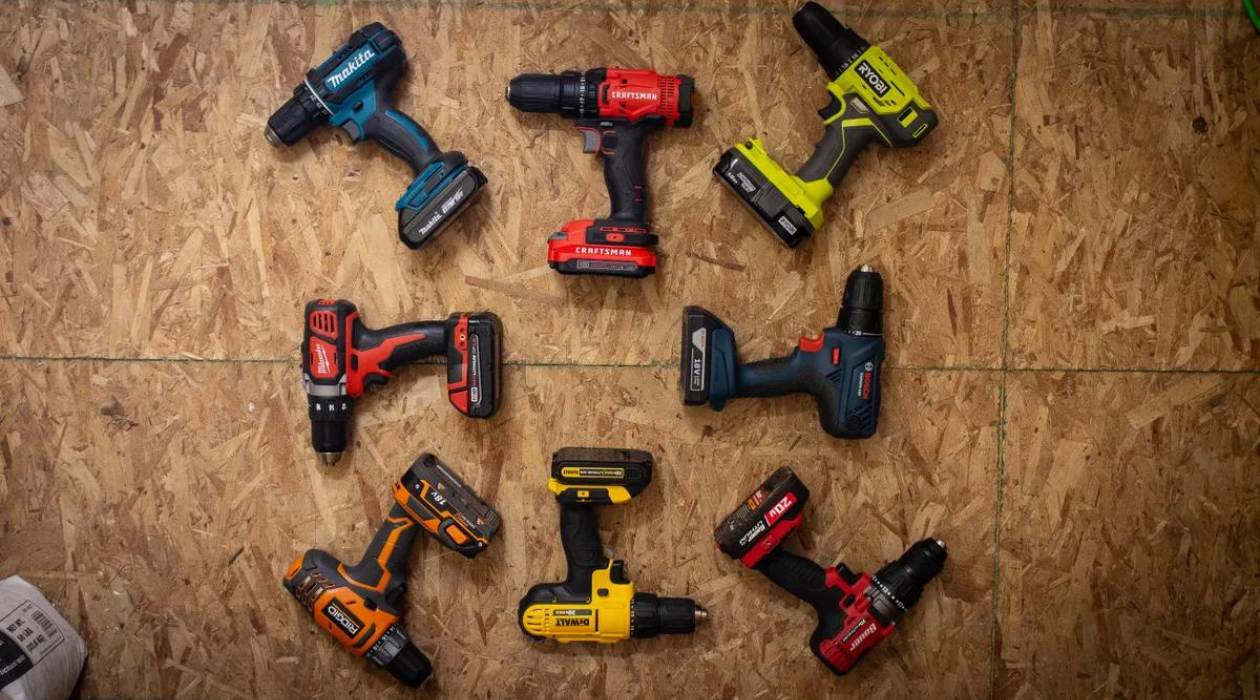
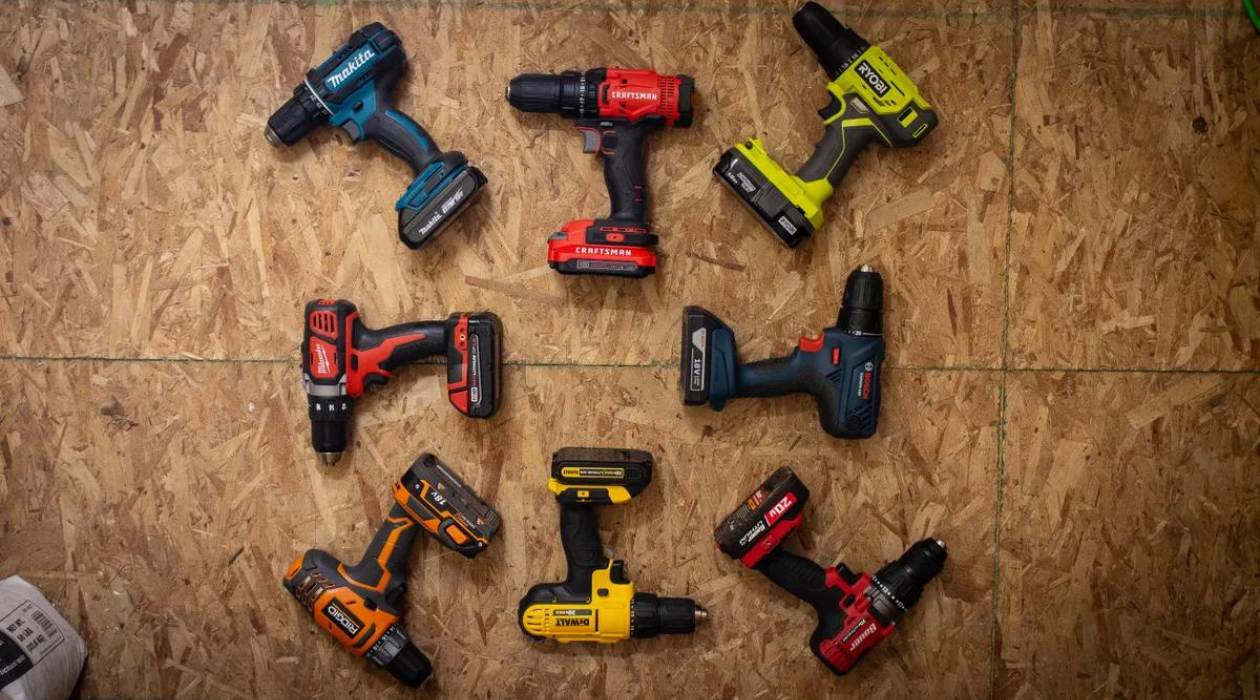
Articles
Which Of The Following Is Not A Recommended Safety Measure For Power Tools?
Modified: December 7, 2023
Discover important safety measures for power tools and learn why articles play a crucial role in maintaining a safe working environment.
(Many of the links in this article redirect to a specific reviewed product. Your purchase of these products through affiliate links helps to generate commission for Storables.com, at no extra cost. Learn more)
Introduction
Power tools are essential tools used in various industries and professions, from construction and woodworking to automotive repair and DIY projects. These tools serve as a great aid in boosting productivity and efficiency. However, it is crucial to prioritize safety while using power tools to prevent accidents and injuries.
According to the Occupational Safety and Health Administration (OSHA), thousands of injuries and even fatalities occur each year due to improper use of power tools. This emphasizes the importance of implementing and following recommended safety measures to ensure the well-being of workers and individuals using power tools.
In this article, we will discuss the significance of safety measures for power tools and explore some of the recommended practices that should be followed to promote a safe working environment. By understanding and implementing these safety measures, users can reduce the risk of accidents and injuries while maximizing the benefits of power tools.
It is important to note that safety measures can vary depending on the type of power tool and the specific task being performed. However, there are general guidelines and practices that can be applied across different tools and industries.
Let’s dive into the various safety measures that should be taken into consideration while working with power tools. By following these recommendations, individuals can minimize the risk of accidents, improve personal safety, and maintain a productive work environment.
Key Takeaways:
- Prioritize safety when working with power tools by wearing appropriate PPE, understanding tool functions, and creating a safe work environment. Regular maintenance and reporting safety issues are crucial for a safer workplace.
- Implement recommended safety measures for power tools to minimize accidents and injuries. This includes proper tool handling, following manufacturer’s instructions, using safety devices, and disconnecting power sources during maintenance.
Importance of Safety Measures for Power Tools
When it comes to working with power tools, safety should always be the top priority. The implementation of proper safety measures is essential due to the nature of these tools and the potential hazards they can pose. Here are some key reasons why safety measures are crucial when using power tools:
1. Prevention of Accidents and Injuries: Power tools have the potential to cause serious accidents and injuries if not used correctly. Safety measures such as wearing personal protective equipment (PPE), following proper handling techniques, and understanding tool functions can significantly reduce the risk of accidents and injuries.
2. Protection of Life and Well-being: Power tool accidents can result in severe injuries, including cuts, amputations, burns, and electrical shocks. By implementing safety measures, individuals can protect their own lives and well-being, as well as the lives of their co-workers and others in the vicinity.
3. Compliance with Regulations: Many countries have regulations and standards in place regarding the use of power tools. By following safety measures, individuals can ensure compliance with these regulations and avoid legal consequences.
4. Preservation of Tools and Equipment: Neglecting safety measures when using power tools can lead to damage or premature wear of the tools. By using tools properly and taking necessary precautions, individuals can extend the lifespan of their tools and equipment, reducing the need for frequent repairs or replacement.
5. Enhanced Productivity: By incorporating safety measures into their work habits, individuals can streamline their workflow and perform tasks more efficiently. Feeling confident in their safety allows workers to focus on their work, leading to increased productivity.
6. Positive Work Culture: Prioritizing safety creates a positive work culture where individuals feel valued and protected. This fosters an environment where everyone looks out for each other’s well-being and encourages open communication about safety concerns.
By understanding the importance of safety measures and taking the necessary precautions, individuals can create a safer working environment, promote personal well-being, and prevent accidents and injuries associated with power tools. The next section will outline some of the recommended safety measures that should be followed when using power tools.
Recommended Safety Measures for Power Tools
To ensure safe and responsible use of power tools, it is important to follow a set of recommended safety measures. By implementing these practices, individuals can minimize the risk of accidents and injuries while working with power tools. Here are ten essential safety measures to consider:
1. Wearing Appropriate Personal Protective Equipment (PPE): Always wear the correct PPE for the task at hand. This may include safety glasses, hearing protection, gloves, and steel-toed shoes. PPE acts as a physical barrier against potential hazards, protecting the body from flying objects, excessive noise, and chemical exposure.
2. Understanding Tool Functions and Limitations: Familiarize yourself with the specific power tool you are using. Read the user manual, learn about its functions, limitations, and any safety precautions provided by the manufacturer. Using a tool outside of its intended purpose can lead to accidents or damage.
3. Regular Inspections and Maintenance: Before using a power tool, inspect it thoroughly for any signs of damage or wear. Check for loose parts, frayed cords, or broken switches. Regularly clean and lubricate tools as recommended by the manufacturer. This ensures that the tool is in proper working condition, minimizing the risk of malfunctions.
4. Proper Tool Handling Techniques: Always hold power tools with a firm grip and use both hands whenever possible. Avoid overreaching or operating tools in awkward positions. Maintain a balanced stance and ensure proper body positioning to have better control over the tool.
5. Safe Work Environment: Create a safe and well-lit workspace that is free from clutter, tripping hazards, and flammable materials. Keep the area around the power tool clear to prevent accidental contact or entanglement.
6. Training and Education: Ensure that individuals using power tools have received adequate training and have a thorough understanding of the tool’s operation and safety protocols. Ongoing education and training can keep individuals up to date with the latest safety practices and techniques.
7. Following Manufacturer’s Instructions: Always follow the manufacturer’s instructions for the specific power tool. This includes guidelines for assembly, use, and maintenance. Ignoring these instructions can lead to accidents or malfunctions.
8. Using Safety Devices and Guards: Power tools often come equipped with safety devices such as blade guards, safety switches, or adjustable handles. These safety features are designed to protect users from potential hazards, so it is important to use them as intended.
9. Disconnecting Power Source before Performing Maintenance or Repairs: Before making any adjustments, changing accessories, or performing maintenance on a power tool, ensure that it is properly disconnected from the power source. This eliminates the risk of accidental operation and electrical shocks.
10. Reporting and Addressing Safety Issues: Encourage a culture of reporting and addressing safety concerns. If any issues or malfunctions are observed with a power tool, it should be immediately reported to the appropriate personnel for inspection and repairs.
By incorporating these recommended safety measures into your work habits, you can minimize the risk of accidents, injuries, and damage while using power tools. Remember, safety should always be prioritized over speed or convenience. A few extra minutes spent on precautionary measures can make a significant difference in preventing potential hazards.
Wearing Appropriate Personal Protective Equipment (PPE)
Personal Protective Equipment (PPE) is essential when working with power tools. It acts as a barrier between the user and potential hazards, protecting various parts of the body from injury. Wearing the appropriate PPE is crucial for ensuring personal safety. Here are some key points to consider when it comes to PPE:
a) Safety Glasses: Safety glasses are designed to protect the eyes from flying debris, sparks, and other potential hazards. When working with power tools, such as saws, drills, or grinders, there is a risk of particles being propelled towards the face. Safety glasses with impact-resistant lenses should be worn to provide adequate eye protection.
b) Hearing Protection: Power tools often produce high levels of noise that can cause permanent hearing damage. To guard against this, wearing hearing protection, such as earmuffs or earplugs, is essential. It is crucial to choose hearing protection that is appropriate for the noise level and duration of exposure.
c) Gloves: Gloves are essential for protecting hands from cuts, burns, and exposure to chemicals. Different tasks may require different types of gloves. For example, leather gloves can provide protection against cuts and abrasions, while heat-resistant gloves are necessary when handling hot surfaces or materials.
d) Steel-toed Shoes: Power tools can pose a significant risk to the feet, especially in construction or workshop settings where heavy objects are frequently moved. Steel-toed shoes offer protection against impact and compression, reducing the risk of foot injuries.
e) Respiratory Protection: Some power tools generate dust, fumes, or other airborne particles that can be harmful to the respiratory system. Using respirators, such as dust masks or respirators with appropriate filters, helps prevent inhalation of hazardous substances.
It is important to note that PPE should be selected based on the specific hazards associated with the task and the power tool being used. Different tools and environments may require additional or specialized PPE.
When selecting and using PPE, ensure that it fits properly and is in good condition. Inspect PPE regularly for signs of wear, damage, or deterioration, and replace it as needed. Ill-fitting or damaged PPE may not provide adequate protection, putting the user at risk.
In addition to wearing appropriate PPE, it is essential to understand the limitations of PPE. PPE should not be considered a substitute for proper tool handling, training, or other safety measures. It is a supplementary safeguard that, when used in conjunction with other safety practices, helps create a well-rounded and comprehensive approach to staying safe while using power tools.
By wearing the appropriate PPE for the task at hand, individuals can significantly reduce the risk of injuries to their eyes, ears, hands, feet, and respiratory system. Prioritizing personal safety through the use of proper PPE is a fundamental safety measure when working with power tools.
Understanding Tool Functions and Limitations
To ensure safe and effective use of power tools, it is crucial to have a thorough understanding of their functions and limitations. Each power tool has specific features, operating procedures, and capabilities that users must be familiar with to prevent accidents and maximize efficiency. Here are some key points to consider when it comes to understanding tool functions and limitations:
a) Read the User Manual: The user manual provided by the manufacturer contains valuable information about the tool’s operation, safety guidelines, and limitations. Take the time to read the manual thoroughly before using the tool. This will give you an in-depth understanding of how the tool works and the precautions you need to take.
b) Identify the Purpose of the Tool: Power tools are designed for specific tasks, such as cutting, drilling, sanding, or shaping. Understanding the intended purpose of the tool will help you use it appropriately and select the right tool for each job. Using a power tool for a task it is not designed for can result in accidents or damage to the tool.
c) Know the Tool’s Limitations: Each power tool has its limitations, such as maximum cutting depth, speed, or load capacity. Exceeding these limitations can cause the tool to malfunction, resulting in accidents or damage. Familiarize yourself with the tool’s limitations as stated in the user manual, and always operate the tool within these parameters.
d) Use the Correct Accessories and Attachments: Power tools often come with a variety of accessories and attachments that can enhance their functionality. However, it is essential to use the right accessories and attachments recommended by the manufacturer. Using incompatible or poorly fitting accessories can compromise the tool’s performance and safety.
e) Consider Power Requirements: Power tools require a consistent and adequate power supply to operate effectively. Ensure that the tool is connected to a power source with the correct voltage and capacity. Using an improper power source can damage the tool and pose a safety risk.
f) Be Mindful of Tool Weight and Balance: Different power tools have varying weights and balances. It is crucial to consider the weight and balance of the tool, especially when working for extended periods. Properly supporting the tool and maintaining a stable grip will help you maintain control and reduce the risk of accidents.
g) Stay Informed of New Technology and Updates: Power tool technology is constantly evolving, with new features and safety enhancements being introduced. Keep yourself informed about advancements in power tool technology and any product updates from the manufacturer. This information can help you work more efficiently and safely.
Understanding the functions and limitations of power tools is essential for safe and efficient operation. By familiarizing yourself with the tool’s user manual, identifying its purpose, and adhering to the manufacturer’s recommendations, you can work confidently, prevent accidents, and prolong the lifespan of the tool. Always remember that using a power tool without a clear understanding of its functions and limitations can lead to hazardous situations.
Read more: Which Injury Prevention Measure For Poisoning Will Help Preserve Home Safety Recommendation
Regular Inspections and Maintenance
Regular inspections and maintenance are crucial for keeping power tools in optimal condition and ensuring safe operation. By implementing a routine inspection and maintenance schedule, you can identify and address any issues before they escalate into safety hazards. Here are some key points to consider when it comes to regular inspections and maintenance:
a) Pre-Use Inspection: Before using a power tool, conduct a thorough visual inspection. Check for any signs of damage, such as cracks, frayed cords, loose parts, or worn-out switches. Ensure that all safety features, guards, and handles are in place and functional. If any damage or issues are detected, refrain from using the tool and address the problem before proceeding.
b) Regular Cleaning: Power tools can accumulate dust, debris, and residue during use. Regular cleaning helps prevent buildup, which can impact the tool’s performance and safety. Use appropriate cleaning methods recommended by the manufacturer, such as using compressed air or a soft brush to remove debris from the tool’s exterior and interior components.
c) Lubrication: Some power tools, such as drills or saws, require lubrication to ensure smooth operation. Refer to the manufacturer’s instructions to determine if and where lubrication is needed. Apply lubricants as recommended to movable parts, such as gears, bearings, and slides, to reduce friction and maintain the tool’s efficiency.
d) Inspection of Power Cords and Plugs: Power cords and plugs can wear out over time, making them prone to damage or electrical hazards. Regularly inspect power cords for any signs of fraying, cracking, or exposed wires. Make sure that plugs are intact and firmly connected to the power source. Any damaged cords or plugs should be replaced immediately.
e) Calibration and Adjustment: Some power tools, such as measuring devices or cutting tools, require calibration or adjustment for accurate performance. Follow the manufacturer’s guidelines for calibrating and adjusting the tool, ensuring that it is functioning within specified tolerances.
f) Replacement of Worn-out Parts: As power tools are used over time, certain parts may wear out and require replacement. This can include blades, bits, belts, or brushes. Regularly inspect these consumable parts and replace them when necessary to maintain optimal performance and safety.
g) Professional Servicing: Periodically, consider getting your power tools professionally serviced. This can include thorough inspections, testing, and maintenance performed by qualified technicians. Professional servicing can help identify hidden issues and ensure that the tool is operating at its best.
By incorporating regular inspections and maintenance into your power tool routine, you can mitigate potential safety risks, prolong the lifespan of your tools, and maintain optimal performance. Taking the time to inspect, clean, lubricate, and address any issues will not only enhance safety but also improve your overall productivity and efficiency. Remember, a well-maintained tool is a safer tool.
Proper Tool Handling Techniques
Proper tool handling techniques are essential for safe and effective use of power tools. When tools are used correctly, the risk of accidents and injuries is significantly reduced. Additionally, proper handling techniques contribute to improved tool performance and longevity. Here are some key points to consider when it comes to proper tool handling techniques:
a) Firm Grip: Always maintain a firm grip on the tool handles. This provides better control and stability while operating the tool. Use both hands whenever possible to achieve a balanced stance and minimize the risk of losing control.
b) Positioning: Position your body and limbs in a way that allows for comfortable and safe operation of the tool. Stand with a stable base, distribute your weight evenly, and avoid leaning or overreaching. Proper positioning ensures better control and reduces the risk of injuries.
c) Concentration: Stay fully focused and attentive while using power tools. Avoid distractions and interruptions that can divert your attention from the task at hand. Concentration is crucial for maintaining awareness of your surroundings and adhering to safety protocols.
d) Start Slowly: When starting a power tool, begin with a slow speed or low power setting. This allows you to establish control and get accustomed to the tool’s response. Gradually increase the speed or power as needed while maintaining steady control.
e) Never Force the Tool: Let the tool do the work. Forcing a power tool to perform beyond its capabilities can cause it to malfunction or kick back, leading to accidents or damage. Use a steady and controlled force, allowing the tool to cut, drill, or grind at its designed pace.
f) Clear Workspace: Keep your workspace clean and organized. Remove any potential obstacles, debris, or clutter that may interfere with the tool’s operation or cause accidents. Clutter-free work areas provide a safer and more efficient working environment.
g) Use the Right Tool for the Job: Select the appropriate power tool for the specific task at hand. Different tools are designed for different purposes and have varying capabilities. Using the right tool for the job ensures better results and reduces the risk of accidents or damage caused by inappropriate tool use.
h) Secure Workpieces: When working on a piece of material or object, ensure that it is properly secured in place. This prevents unexpected movements or slippage that can lead to accidents. Use clamps, vices, or other appropriate methods to stabilize the workpiece.
i) Turning Off and Storing Safely: After use, always turn off the power tool and wait for it to come to a complete stop before setting it down or storing it. This prevents accidental activation and avoids potential injuries or damage.
j) Preventive Measures: Implement additional preventive measures based on the specific power tool and task. For example, when using a saw, always cut away from your body, and when using a drill, use a stable work surface to prevent sudden movements.
By applying these proper tool handling techniques, individuals can minimize the risk of accidents, injuries, and damage while utilizing power tools. Remember, practice and familiarity with the specific tool are essential for mastering proper handling techniques. Always prioritize safety and take the necessary precautions to ensure safe operation.
Always wear appropriate personal protective equipment (PPE) such as safety glasses, gloves, and hearing protection when using power tools. This will help protect you from potential injuries.
Safe Work Environment
Creating a safe work environment is essential when using power tools. A well-organized and hazard-free workspace promotes safety, reduces the risk of accidents, and allows for efficient and productive work. Here are some key elements to consider when establishing a safe work environment:
a) Clear and Organized Workspace: Keep your work area clean, clear, and well-organized. Remove any unnecessary items or debris that may obstruct your movement or cause accidents. Proper organization ensures that tools and equipment are easily accessible and minimizes the risk of tripping or falling.
b) Adequate Lighting: Ensure that your work area has adequate lighting. Proper illumination is crucial for clear visibility, allowing you to see potential hazards or obstructions. If needed, use additional lighting sources, such as task lights or portable work lights, to enhance visibility in specific areas.
c) Proper Ventilation: Some power tools produce dust, fumes, or other airborne particles. It is important to have proper ventilation in your workspace to prevent the buildup of harmful substances. Use fans, windows, or ventilation systems to ensure a well-ventilated environment.
d) Fire Safety Measures: Implement fire safety measures in your workspace, such as having fire extinguishers readily available and knowing how to use them. Keep flammable substances stored in appropriate containers and away from potential ignition sources. Regularly check fire alarms and emergency exit routes to ensure they are functioning properly.
e) Electrical Safety: Ensure that the electrical outlets and wiring in your workspace are in good condition. Avoid overloading circuits and use surge protectors when necessary. If you are using extension cords, choose ones that are suitable for the power load and inspect them regularly for any damages or frayed wires.
f) Slip and Trip Prevention: Reduce slip and trip hazards by keeping the floor clear of obstacles, loose cords, and spills. Use anti-slip mats to provide traction on smooth or slippery surfaces. Properly secure power cords and hoses to prevent tripping hazards.
g) Emergency Preparedness: Familiarize yourself with the location of emergency exits, fire extinguishers, and first aid kits in your workspace. Ensure that these items are easily accessible and that you know how to use them. Train yourself and others on emergency procedures to be prepared for any unforeseen circumstances.
h) Communication and Warning Signs: Use clear and visible warning signs to alert others to potential hazards. Place signs indicating restricted areas, electrical hazards, or areas under construction. Establish effective communication channels to keep everyone informed of safety protocols and any changes or updates.
i) Personal Workspace Organization: Keep your personal workspace organized and free from clutter. Arrange tools, equipment, and materials in a systematic manner to prevent accidental contact or damage. Proper storage and organization ensure a safer and more efficient work environment.
j) Regular Inspections: Conduct regular inspections of your workspace to identify any potential hazards or safety concerns. Address any issues promptly, such as repairing damaged flooring or replacing faulty equipment.
Creating a safe work environment is a shared responsibility. Encourage all individuals in the workspace to adhere to safety protocols and report any hazards or concerns. By fostering a culture of safety, you will create an environment where individuals can work confidently, minimizing the risk of accidents and injuries while using power tools.
Training and Education
Training and education are vital components of promoting safety when working with power tools. Proper training ensures that individuals have the knowledge and skills to operate tools safely and effectively. Ongoing education keeps individuals updated with the latest safety practices and techniques. Here are some key points to consider when it comes to training and education:
a) Initial Training: Provide comprehensive training to individuals who will be working with power tools. This training should cover basic tool operation, safety guidelines, and proper handling techniques. Ensure that individuals understand the potential hazards associated with power tools and how to mitigate them.
b) Tool-Specific Training: Different power tools have unique features, functions, and safety considerations. Provide tool-specific training to individuals based on the tools they will be using. This training should cover tool operation, maintenance, and any specific safety protocols related to the tool.
c) Safety Workshops and Courses: Encourage individuals to attend safety workshops and courses related to power tool usage. These workshops provide in-depth knowledge about safety practices, risk assessment, and emergency response procedures. They often include hands-on activities and demonstrations to enhance learning.
d) Continuing Education: Safety standards, regulations, and technology related to power tools are constantly evolving. Encourage individuals to engage in continuing education to stay informed of the latest advancements and best practices. This can include attending conferences, webinars, or subscribing to industry publications.
e) Hands-On Training: Hands-on training is essential for individuals to develop the necessary skills to operate power tools safely. Provide opportunities for supervised practice and guidance to ensure individuals gain confidence and competence in their abilities.
f) Mentoring and Supervision: Assign experienced individuals as mentors to those who are new to working with power tools. Mentors can provide guidance, answer questions, and ensure that proper safety practices are followed. Supervision is crucial, especially during the initial stages, to ensure safe operation of power tools.
g) Safety Demonstrations: Conduct regular safety demonstrations to reinforce safe practices and highlight potential hazards. These demonstrations can focus on proper tool usage, handling techniques, and the use of safety devices. By visually demonstrating the importance of safety, individuals are more likely to retain the information.
h) Toolbox Talks: Organize periodic toolbox talks to discuss safety-related topics. These short sessions can be conducted at the beginning of shifts or during team meetings. Toolbox talks provide an opportunity to address specific safety concerns, share best practices, and encourage open dialogue about safety among team members.
i) Safety Assessments and Feedback: Regularly assess individual performance and provide feedback on safety practices. Conduct safety audits and inspections to identify gaps or areas that need improvement. Use these assessments as an opportunity to reinforce training and educate individuals on any changes or updates to safety protocols.
Promoting a culture of safety that emphasizes training and education is essential for minimizing the risk of accidents and injuries. By investing in comprehensive training programs, ongoing education, and fostering a continuous learning environment, individuals can enhance their skills, knowledge, and awareness of safety practices when working with power tools.
Read more: Which Power Tools Are Made In The Usa
Following Manufacturer’s Instructions
Following the manufacturer’s instructions is critical when it comes to ensuring the safe and proper use of power tools. The manufacturer provides specific guidelines and recommendations to maximize user safety and the tool’s performance. Here are some key points to consider when it comes to following the manufacturer’s instructions:
a) User Manual: The user manual provided by the manufacturer contains essential information about the power tool’s operation, maintenance, and safety precautions. It is important to read and understand the entire manual before using the tool. Pay close attention to sections on safety guidelines, recommended accessories, and any limitations or restrictions.
b) Tool Assembly: If any assembly is required, carefully follow the manufacturer’s instructions. Ensure that the tool is assembled correctly, with all parts securely attached and tightened. Incorrect assembly can compromise the tool’s performance and lead to accidents.
c) Safety Guidelines: The manufacturer’s instructions often include specific safety guidelines related to the tool. This can include recommendations for using safety devices, wearing appropriate personal protective equipment (PPE), and avoiding specific actions or conditions that may pose a risk. Adhere to these guidelines to prevent accidents and injuries.
d) Tool Maintenance: The manufacturer’s instructions provide guidance on how to properly maintain the power tool. This may include cleaning, lubrication, or regular inspections to ensure that the tool is in good working condition. Following the maintenance procedures outlined by the manufacturer will help prolong the tool’s lifespan and prevent unexpected failures.
e) Power Requirements: Manufacturers specify the power requirements for their power tools, including voltage, amperage, or wattage. It is crucial to ensure that the power source matches the tool’s requirements. Using the wrong power source can damage the tool or create safety hazards.
f) Safe Operating Procedures: The manufacturer’s instructions often contain step-by-step operating procedures for the power tool. These procedures outline safe practices, starting and stopping the tool, and recommended techniques for optimal performance. Following these procedures exactly as specified by the manufacturer will help prevent accidents and ensure proper tool operation.
g) Limitations and Restrictions: Manufacturers provide information on the tool’s limitations and restrictions. This can include maximum operating speeds, recommended materials or applications, and duty cycles. It is important to adhere to these limitations and restrictions to avoid exceeding the tool’s capabilities and compromising safety.
h) Service and Repairs: The manufacturer’s instructions often provide guidance on authorized service centers or procedures for repairs and maintenance. If the power tool requires servicing or repairs, follow the instructions provided to ensure the work is done by qualified technicians and using approved replacement parts.
By following the manufacturer’s instructions, individuals can ensure proper tool operation, minimize the risk of accidents, and maximize the tool’s performance and lifespan. The manufacturer has designed the tool with safety and efficiency in mind, and their instructions provide valuable guidance for safe usage. Remember, deviating from the manufacturer’s instructions can lead to accidents, tool damage, or potential warranty issues.
Using Safety Devices and Guards
Safety devices and guards are essential components of power tools that help protect users from potential hazards and prevent accidents. These devices are designed to mitigate the risks associated with power tool operation. Here are some key points to consider when it comes to using safety devices and guards:
a) Blade Guards: Many power tools, such as saws and grinders, come equipped with blade guards. Blade guards cover the sharp edges of cutting or grinding blades, preventing accidental contact and minimizing the risk of cuts or amputations. Always ensure that the blade guard is in place and functioning properly before operating the tool.
b) Safety Switches: Power tools often feature safety switches that require deliberate and intentional operation to prevent accidental activation. These switches are designed to prevent the tool from being turned on or to shut it off automatically when released. Familiarize yourself with the location and operation of the safety switch for the specific tool you are using.
c) Adjustable Handles: Some power tools, such as drills or sanders, have adjustable handles that allow for better control and stability during operation. Use these handles to maintain a secure grip and reduce the risk of losing control of the tool.
d) Dust Collection Systems: Dust collection systems are safety devices that capture and collect airborne dust and particles generated by power tool operations. These systems help reduce the risk of respiratory issues and maintain a cleaner and safer work environment. Connect power tools to appropriate dust collection systems whenever possible.
e) Kickback Prevention Devices: Kickback is a sudden and unexpected reaction that can occur when a power tool binds or stalls. Kickback prevention devices, such as riving knives or anti-kickback pawls, are designed to minimize the risk of kickback and keep the tool under control. Ensure that these devices are correctly installed and maintained.
f) Protective Shields and Screens: Some power tools, such as sanders or grinders, are equipped with protective shields or screens to prevent debris, sparks, or fragments from being thrown towards the user. These shields provide a physical barrier and should always remain in place during operation.
g) Anti-Vibration Features: Power tools that produce significant vibrations, such as jackhammers or rotary hammers, may have built-in anti-vibration features. These features help reduce the risk of hand-arm vibration syndrome (HAVS) and minimize the strain on the user’s hands and arms. Utilize these features to reduce the risk of long-term injuries.
h) Safety Key Systems: Certain power tools, such as table saws, may utilize safety key systems. These systems require a specific key to start the tool, ensuring that it cannot be used without authorization. When not in use, remove the safety key and store it securely to prevent unauthorized access or use of the tool.
i) Interlocks: Interlocks are safety devices that automatically disengage the power supply when certain conditions are not met or when access to hazardous areas is detected. These devices provide an additional layer of protection to prevent accidental contact with moving parts or activating the tool during maintenance or repairs.
Utilizing safety devices and guards as intended by the manufacturer is crucial for maintaining a safe working environment when using power tools. These devices are designed to minimize the risk of accidents and protect users from potential hazards. Always ensure that safety devices are in place, properly adjusted, and well-maintained before operating any power tool. Remember, compromising or removing safety devices can lead to severe injuries or accidents, so they should never be bypassed or ignored.
Disconnecting Power Source before Performing Maintenance or Repairs
Disconnecting the power source is a crucial safety measure when performing maintenance or repairs on power tools. It is important to cut off the power supply to the tool to prevent accidental activation and minimize the risk of electrical shocks or other injuries. Here are some key points to consider when it comes to disconnecting the power source before maintenance or repairs:
a) Unplug the Tool: Prior to performing any maintenance or repairs, always unplug the power tool from the electrical outlet. This ensures that there is no power flowing to the tool and eliminates the risk of accidental start-up.
b) Remove the Battery: If the power tool is battery-operated, remove the battery pack or disconnect it from the tool. This prevents the tool from drawing power from the battery and minimizes any chance of accidental activation.
c) Lockout/Tagout Procedures: In workplace settings, where multiple individuals may have access to power tools, it is important to follow lockout/tagout procedures. Lockout/tagout involves securing the power source with a lock or tag to prevent unauthorized use during maintenance or repairs. This provides an additional layer of safety by ensuring that no one can inadvertently re-energize the tool while maintenance work is being conducted.
d) Wait for the Tool to Cool Down: Some power tools, such as those with motors or heating elements, may become hot during use. Before performing any maintenance or repairs, allow the tool to cool down completely. Hot surfaces can cause burns or other injuries, so it is important to exercise caution and not rush the maintenance process.
e) Follow Manufacturer’s Instructions: Always refer to the manufacturer’s instructions for specific guidance on disconnecting the power source for your power tool. The instructions may include recommendations for specific power disconnection procedures or precautions to take.
f) Inspect Power Cords and Switches: Before performing any maintenance or repairs, visually inspect the power cord and switches for any signs of damage or wear. If any issues are found, refrain from using the tool and address the problem before proceeding. Damaged power cords or switches can pose electrical risks and should be repaired or replaced by a qualified professional.
g) Use Lock-out Devices: In addition to unplugging or disconnecting the power source, consider using lock-out devices to secure switches or controls in the off position. Lock-out devices prevent accidental activation and act as a visible reminder to others that maintenance or repairs are taking place.
Taking the time to disconnect the power source properly before performing maintenance or repairs on power tools is crucial for personal safety. By following these steps, you can minimize the risk of electrical shocks, accidental activation, and other potential hazards. Always prioritize safety when working on power tools, and if you are uncertain about any aspect of the maintenance or repair process, consult a professional or contact the manufacturer for guidance.
Reporting and Addressing Safety Issues
Reporting and addressing safety issues is a vital part of maintaining a safe working environment when working with power tools. Promptly addressing safety concerns ensures that potential hazards are identified and corrective actions are taken to prevent accidents and injuries. Here are some key points to consider when it comes to reporting and addressing safety issues:
a) Reporting Procedures: Familiarize yourself with the reporting procedures established in your workplace for safety concerns. Understand whom to contact or how to submit a report when you identify a safety issue. Reporting procedures may vary depending on the organization, but it is important to follow the established protocols.
b) Documenting Safety Issues: When reporting a safety issue, provide as much detail as possible. Clearly describe the issue, including the location, nature of the problem, and any relevant observations. Providing accurate and comprehensive information helps those responsible for addressing the issue better understand and resolve it.
c) Timely Reporting: Report safety issues as soon as they are identified. Do not delay reporting, as a quick response is essential for resolving the issue promptly and preventing accidents or further hazards. Taking immediate action helps maintain a safe working environment for yourself and others.
d) Communication and Collaboration: Communication is key in addressing safety issues effectively. Communicate with supervisors, managers, or designated safety personnel to ensure that the issue is acknowledged and appropriately addressed. Collaborate with others in your workplace to provide a holistic view of the problem and work together towards finding viable solutions.
e) Hazard Identification and Risk Assessment: When reporting a safety issue, consider conducting a hazard identification and risk assessment. Identify any potential risks associated with the problem and assess the likelihood and severity of those risks. This information can help prioritize and address the issue efficiently.
f) Corrective Actions: Once a safety issue is reported, appropriate corrective actions need to be taken. This may include repairing or replacing faulty equipment, modifying procedures or processes, implementing additional safety measures, or providing additional training. Ensure that the corrective actions are documented and followed through to completion.
g) Continuous Improvement: Use reported safety issues as learning opportunities for continuous improvement. Analyze the root cause of the problem and identify any underlying trends or patterns. Implement measures to prevent similar issues from occurring in the future, such as revising procedures, enhancing training programs, or updating safety protocols.
h) Feedback and Follow-up: Provide feedback and follow-up on reported safety issues. Recognize and acknowledge individuals who bring forth safety concerns and actively participate in resolving them. Regularly communicate updates and progress on addressing the reported issues to keep everyone informed and involved.
i) Learning Culture: Foster a learning culture that encourages reporting and addressing safety issues. Encourage individuals to speak up about potential hazards or safety concerns without fear of retribution. Promote open communication, active participation, and a shared responsibility for maintaining a safe work environment.
By reporting and addressing safety issues, you play an active role in preventing accidents and maintaining a safe working environment. Be proactive in identifying and reporting safety concerns, and collaborate with others to find effective solutions. Together, we can create a culture of safety where everyone feels empowered to speak up and contribute to a safer workplace.
Read more: Which Power Tools Are The Best
Conclusion
When it comes to working with power tools, safety should always be the top priority. By implementing and following recommended safety measures, individuals can minimize the risk of accidents and injuries while maximizing the benefits of power tools.
In this article, we have discussed the importance of safety measures for power tools and explored ten recommended practices to promote a safe working environment. These measures include wearing appropriate personal protective equipment (PPE), understanding tool functions and limitations, conducting regular inspections and maintenance, practicing proper tool handling techniques, ensuring a safe work environment, prioritizing training and education, following the manufacturer’s instructions, using safety devices and guards, disconnecting the power source before maintenance or repairs, and reporting and addressing safety issues.
By wearing the appropriate PPE, individuals protect themselves from potential hazards. Understanding tool functions and limitations ensures that tools are used correctly and safely. Regular inspections and maintenance help identify and address issues before they escalate into safety hazards. Proper tool handling techniques minimize the risk of accidents and injuries. Creating a safe work environment reduces the likelihood of accidents and promotes efficiency. Training and education provide individuals with the necessary knowledge and skills to operate power tools safely. Following the manufacturer’s instructions guarantees proper tool operation and reduces the risk of accidents. Using safety devices and guards adds an extra layer of protection. Disconnecting the power source before maintenance or repairs prevents accidental activation and electrical shocks. Reporting and addressing safety issues contributes to a continuous improvement culture, ensuring a safer work environment for all.
Remember, safety is a collective responsibility. It requires individual commitment, open communication, and adherence to established safety protocols. By prioritizing safety and incorporating these recommended measures into your work habits, you can create a safer work environment, prevent accidents and injuries, and fully maximize the benefits and potential of power tools.
Stay vigilant, stay informed, and always prioritize safety when working with power tools. Together, we can ensure a safer and more productive working environment for everyone.
Frequently Asked Questions about Which Of The Following Is Not A Recommended Safety Measure For Power Tools?
Was this page helpful?
At Storables.com, we guarantee accurate and reliable information. Our content, validated by Expert Board Contributors, is crafted following stringent Editorial Policies. We're committed to providing you with well-researched, expert-backed insights for all your informational needs.
0 thoughts on “Which Of The Following Is Not A Recommended Safety Measure For Power Tools?”