Home>Construction & Tools>Worksite Management>How To Organize A Warehouse Inventory
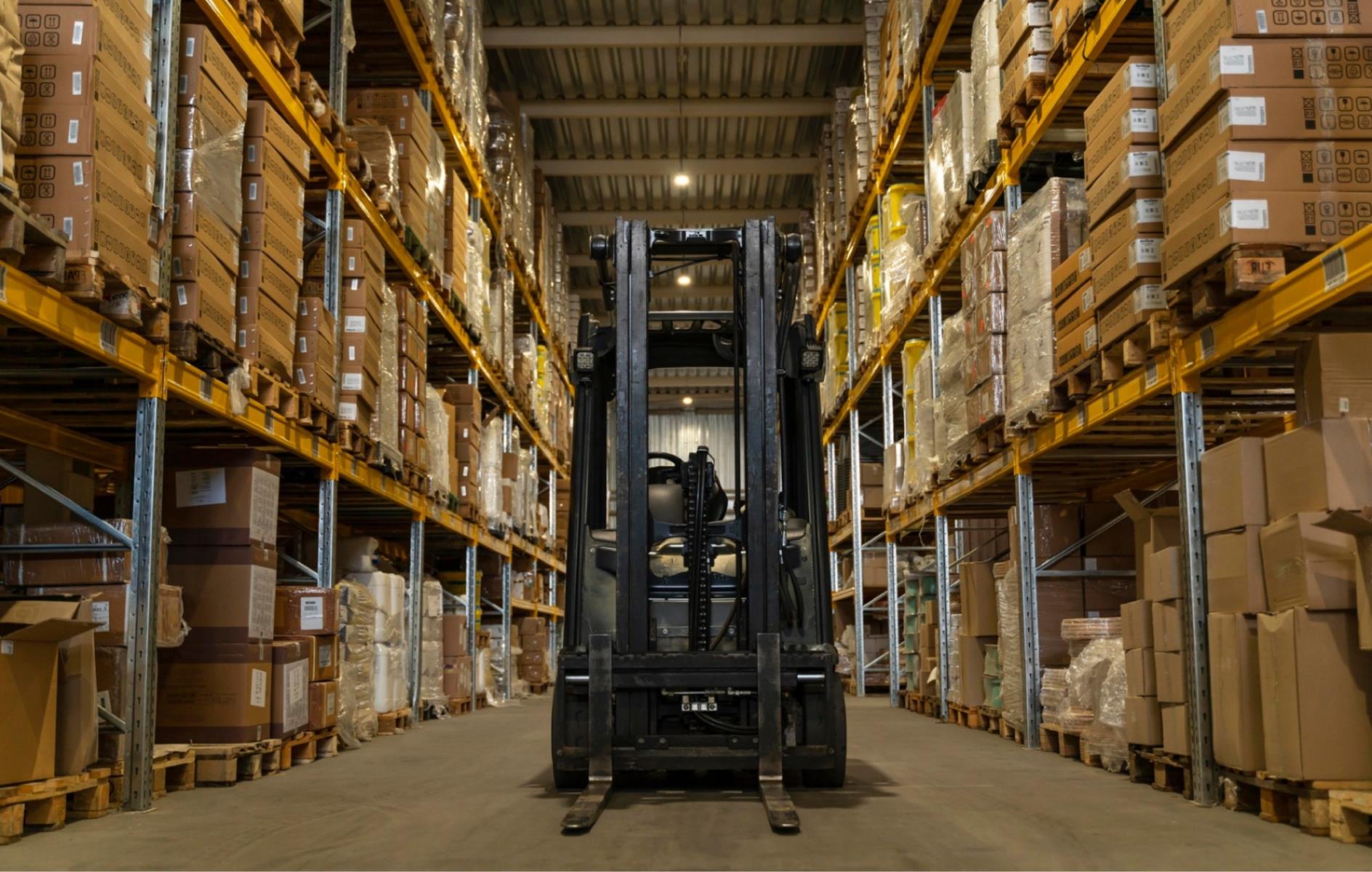
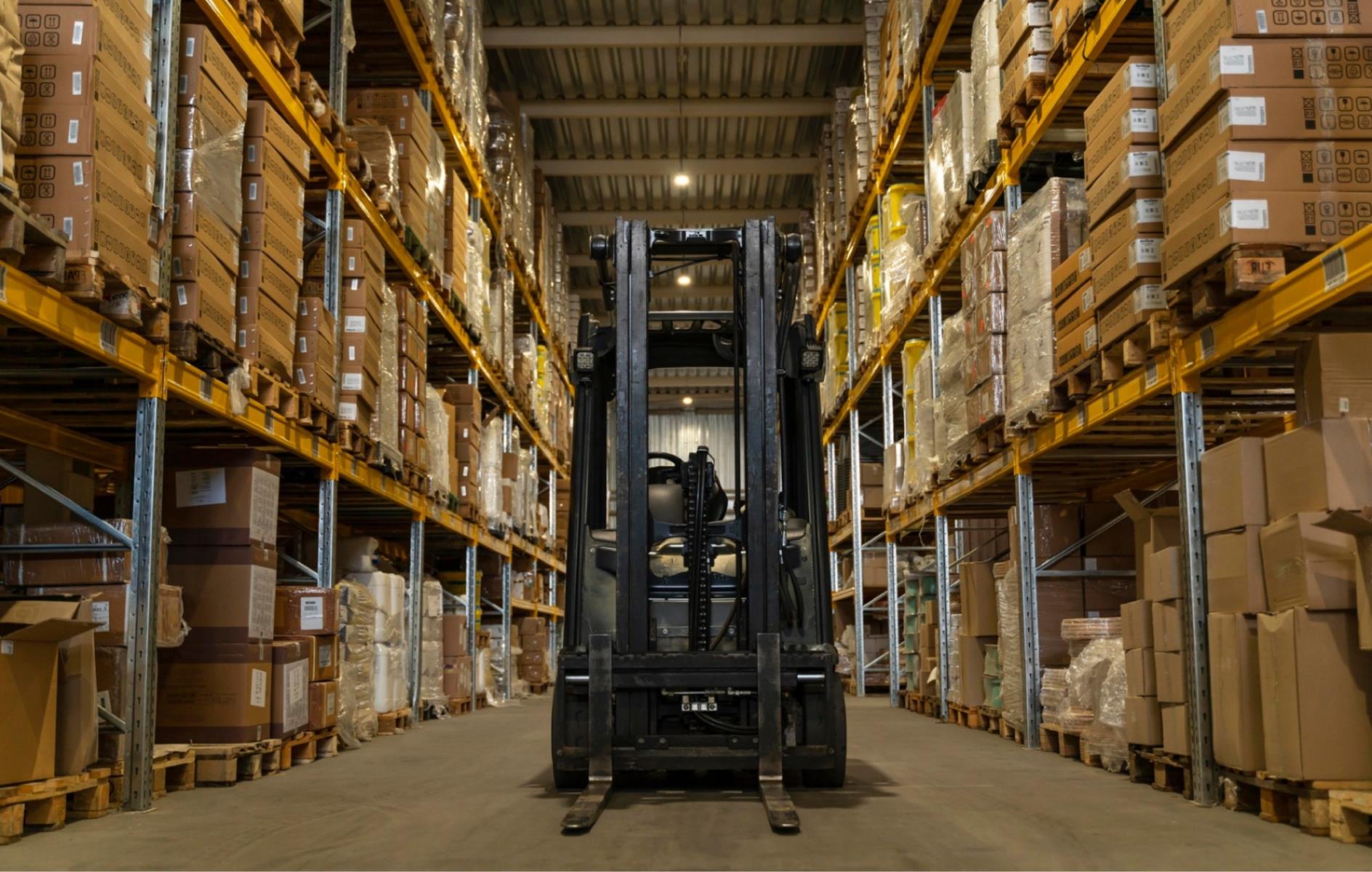
Worksite Management
How To Organize A Warehouse Inventory
Published: March 2, 2024
Learn how to efficiently organize and manage your warehouse inventory with our expert tips and best practices for worksite management. Streamline your operations and improve productivity today!
(Many of the links in this article redirect to a specific reviewed product. Your purchase of these products through affiliate links helps to generate commission for Storables.com, at no extra cost. Learn more)
Introduction
Are you struggling to keep your warehouse inventory organized? Do you find yourself spending too much time searching for items or dealing with overstocked shelves? If so, you're in the right place. In this article, we will explore the essential steps to organize a warehouse inventory effectively. By following these guidelines, you can streamline your operations, improve efficiency, and ultimately save time and money. Let's dive in and discover the key strategies for maintaining a well-organized warehouse inventory.
Key Takeaways:
- Streamline warehouse operations by assessing inventory needs, designing an efficient layout, and implementing a robust management system. This leads to improved efficiency, cost savings, and a safer working environment.
- Regularly conduct inventory audits, train staff on procedures, and implement safety measures to maintain a well-organized warehouse. This ensures accuracy, minimizes errors, and creates a positive experience for employees and customers.
Read more: How To Organize Inventory
Assessing Inventory Needs
Before diving into the process of organizing a warehouse inventory, it's crucial to assess the actual needs of your inventory. This involves evaluating the types of products or materials you store, their demand, and the frequency of restocking. Here are the steps to consider:
-
Analyze Inventory Trends: Review historical data to identify which items are fast-moving and which ones are slow-moving. This analysis will help you prioritize storage space and optimize the layout of your warehouse.
-
Forecast Future Demand: Use sales forecasts, market trends, and historical data to predict future demand for your products. This will guide you in allocating space and determining the appropriate inventory levels to maintain.
-
Categorize Inventory: Classify your inventory into different categories based on their characteristics, such as size, weight, and shelf-life. This categorization will help in determining the most suitable storage methods for each type of product.
-
Assess Storage Requirements: Evaluate the storage needs of different items, considering factors like temperature sensitivity, fragility, and special handling requirements. This assessment will guide you in selecting appropriate storage solutions.
By thoroughly assessing your inventory needs, you can lay a solid foundation for the subsequent steps in organizing your warehouse inventory.
Designing Warehouse Layout
Designing an efficient warehouse layout is crucial for optimizing space and ensuring smooth operations. Here's how to create an effective warehouse layout:
-
Optimize Space Utilization: Utilize vertical space by installing tall shelving units or mezzanines to maximize storage capacity without expanding the warehouse footprint.
-
Create Clear Aisles: Designate wide, clear aisles to facilitate the movement of inventory, equipment, and personnel. This prevents congestion and enhances safety.
-
Implement Logical Flow: Arrange the layout to follow a logical flow, from receiving to storage to shipping. This minimizes unnecessary travel and streamlines processes.
-
Utilize Zone Picking: Divide the warehouse into zones based on product categories or order types. This allows for efficient picking and packing processes.
-
Incorporate Workstations: Integrate packing, labeling, and quality control workstations strategically within the layout to minimize movement and increase productivity.
-
Utilize Technology: Incorporate technology such as barcode scanning and RFID systems to track inventory movement and improve accuracy.
By designing a well-thought-out warehouse layout, you can enhance efficiency, reduce operational costs, and create a more organized inventory management system.
Implementing Inventory Management System
Implementing a robust inventory management system is essential for maintaining control and visibility over your warehouse inventory. Here's a detailed guide on how to effectively implement an inventory management system:
-
Select the Right Software: Choose a suitable inventory management software that aligns with your business needs. Look for features such as real-time tracking, barcode scanning, and integration with other systems like accounting and order management.
-
Barcode and RFID Implementation: Utilize barcode and RFID technology to accurately track and manage inventory. Assign unique codes to each item and use handheld scanners or fixed readers to update inventory records in real time.
-
Centralized Database: Establish a centralized database to store all inventory-related information. This database should include details such as item descriptions, stock levels, reorder points, and supplier information.
-
Set Standard Operating Procedures: Develop standard operating procedures (SOPs) for inventory management processes, including receiving, storing, picking, and shipping. Clearly define the responsibilities of staff members involved in these processes.
-
Training Staff: Provide comprehensive training to warehouse staff on how to use the inventory management system effectively. Ensure they understand how to input data, conduct stock counts, and resolve discrepancies.
-
Real-time Tracking: Implement a system that provides real-time visibility into inventory levels and movements. This allows for proactive decision-making and minimizes the risk of stockouts or overstocking.
-
Automated Alerts: Configure the system to generate automated alerts for low stock levels, expiring items, or discrepancies in inventory counts. These alerts help in timely replenishment and proactive issue resolution.
-
Integration with Suppliers: Explore options for integrating your inventory management system with your suppliers' systems. This can streamline the procurement process, improve order accuracy, and facilitate better communication.
By implementing an effective inventory management system, you can enhance accuracy, efficiency, and overall control of your warehouse inventory. This lays the foundation for a well-organized and optimized inventory management process.
Establishing Receiving and Shipping Processes
Efficient receiving and shipping processes are vital components of a well-organized warehouse inventory system. Here's a comprehensive guide to establishing effective receiving and shipping processes:
-
Streamline Receiving Procedures: Develop a streamlined process for receiving incoming inventory. This includes verifying the accuracy of shipments, inspecting for damages, and promptly updating the inventory records. Utilize barcode scanning or RFID technology to efficiently log received items into the inventory management system.
-
Designate Receiving Areas: Designate specific areas within the warehouse for receiving incoming shipments. Ensure these areas are equipped with the necessary tools such as pallet jacks, forklifts, and receiving docks to facilitate the unloading and inspection of goods.
-
Quality Control Checks: Implement quality control checks during the receiving process to identify any damaged or defective items. This ensures that only high-quality products are accepted into the inventory, reducing the risk of storing unusable or faulty items.
-
Organize Shipping Stations: Create dedicated shipping stations within the warehouse for packaging and preparing outgoing orders. Equip these stations with packaging materials, labeling tools, and shipping documentation to expedite the shipping process.
-
Efficient Order Picking: Implement efficient order picking processes to fulfill customer orders accurately and promptly. Utilize technology such as pick-to-light systems or voice-directed picking to optimize the picking process and minimize errors.
-
Utilize Shipping Software: Invest in shipping software that integrates with your inventory management system. This software should streamline the shipping process by generating shipping labels, calculating shipping costs, and providing real-time tracking information for outgoing orders.
-
Optimize Packaging: Standardize packaging procedures to ensure consistency and minimize excess packaging materials. This not only reduces waste but also optimizes storage space within the warehouse.
-
Carrier Selection: Evaluate and select reliable carriers for shipping based on factors such as cost, delivery speed, and reliability. Establish partnerships with carriers to negotiate favorable shipping rates and service levels.
By establishing efficient receiving and shipping processes, you can ensure the smooth flow of inventory in and out of the warehouse, minimize errors, and provide a positive experience for both suppliers and customers.
Utilize a systematic layout for your warehouse, grouping similar items together and labeling shelves and bins clearly. This will make it easier to locate and access inventory quickly.
Read more: How To Organize Parts Inventory
Utilizing Storage Solutions
Effective utilization of storage solutions is essential for optimizing warehouse space and maintaining a well-organized inventory. Here are the key strategies for maximizing storage efficiency:
-
Vertical Storage: Make use of vertical space by installing tall shelving units, mezzanines, or multi-tier racking systems. This allows you to store more items within the same footprint, effectively utilizing the height of the warehouse.
-
Pallet Racking: Implement pallet racking systems to store goods on pallets. This system provides easy access to inventory and can be configured to accommodate various pallet sizes and weights.
-
Bulk Storage: Utilize bulk storage solutions for items that are not frequently accessed. This can include bulk stacking, drive-in racking, or push-back racking, which are suitable for storing large quantities of homogeneous products.
-
Carton Flow Racks: Implement carton flow racks for high-density storage of cartons or boxes. This system uses gravity to move items forward as others are removed, ensuring efficient stock rotation and picking.
-
Bin Shelving: Utilize bin shelving for small parts and components. These shelving units are designed with compartments or bins, making it easy to organize and access small items without the need for additional containers.
-
Automated Storage and Retrieval Systems (AS/RS): Consider implementing AS/RS for high-density storage and automated picking. These systems use robotic technology to retrieve items from designated storage locations, maximizing space and improving picking efficiency.
-
Cantilever Racking: Utilize cantilever racking for the storage of long, bulky items such as lumber, pipes, or furniture. This system allows for easy access to long items without the obstruction of vertical support beams.
-
Stacking and Nesting: Optimize storage space by utilizing stacking and nesting capabilities of certain items. Stackable and nestable containers or bins can be efficiently stored when not in use, minimizing the space they occupy.
By effectively utilizing a combination of these storage solutions, you can maximize the use of available warehouse space, improve accessibility to inventory, and create a more organized and efficient storage environment.
Conducting Regular Inventory Audits
Regular inventory audits are essential for maintaining accuracy and integrity within the warehouse inventory. Conducting thorough and systematic audits helps in identifying discrepancies, preventing stockouts, and ensuring proper stock rotation. Here's a detailed guide on how to conduct regular inventory audits effectively:
-
Establish Audit Schedule: Set a regular schedule for inventory audits, considering factors such as the volume of inventory turnover, the nature of stored items, and any seasonal fluctuations in demand. This schedule ensures that audits are conducted at appropriate intervals to maintain accuracy.
-
Utilize Cycle Counting: Implement a cycle counting approach where inventory is counted in small, manageable sections on a frequent basis. This method allows for ongoing verification of stock levels without disrupting regular operations.
-
Utilize Technology: Leverage inventory management software and handheld devices to streamline the audit process. Barcode scanning and RFID technology can significantly improve the speed and accuracy of audits, reducing manual errors.
-
Random Sampling: Incorporate random sampling techniques during audits to ensure comprehensive coverage of inventory items. Randomly select items for verification to minimize the potential for bias and ensure a thorough assessment.
-
Document Discrepancies: Document any discrepancies discovered during the audit process. This includes recording damaged items, expired products, or instances where stock levels do not match the recorded inventory.
-
Root Cause Analysis: Conduct a root cause analysis for any discrepancies identified during the audit. Determine the underlying reasons for discrepancies, such as errors in receiving, picking, or data entry, and implement corrective measures to prevent recurrence.
-
Reconcile Inventory Records: Compare the results of the audit with the existing inventory records. Identify any discrepancies and take necessary steps to reconcile the inventory, including adjustments to stock levels and investigating the reasons behind discrepancies.
-
Implement Continuous Improvement: Use the findings from inventory audits to drive continuous improvement in inventory management processes. Identify areas for enhancement, such as tightening receiving procedures, improving storage practices, or enhancing data accuracy.
By conducting regular inventory audits using these strategies, you can maintain the accuracy of inventory records, identify potential issues early, and ensure that the warehouse inventory remains well-organized and reliable.
Training Staff on Inventory Procedures
Training staff on inventory procedures is crucial for ensuring that all employees involved in warehouse operations understand and adhere to established protocols. Here's a detailed approach to effectively train staff on inventory procedures:
-
Develop Comprehensive Training Materials: Create comprehensive training materials that cover all aspects of inventory procedures, including receiving, storing, picking, and shipping. These materials can include written manuals, visual aids, and interactive modules to cater to different learning styles.
-
Hands-On Training: Provide hands-on training sessions where staff members can practice actual inventory procedures under supervision. This practical experience helps in reinforcing theoretical knowledge and allows employees to familiarize themselves with the tools and equipment used in inventory management.
-
Role-Specific Training: Tailor training programs to specific roles within the warehouse, such as forklift operators, inventory clerks, and shipping personnel. Each role may have unique responsibilities and procedures, and targeted training ensures that staff are well-prepared for their specific tasks.
-
Safety Training: Incorporate safety training into inventory procedures training. This includes guidelines for handling hazardous materials, operating equipment safely, and maintaining a clean and organized work environment to prevent accidents and injuries.
-
Continuous Education: Implement ongoing education and refresher training to keep staff updated on any changes in inventory procedures, new technologies, or best practices. Continuous education ensures that staff remain competent and adaptable in their roles.
-
Interactive Workshops: Conduct interactive workshops or group discussions to encourage staff participation and collaboration. This allows employees to share their experiences, ask questions, and learn from each other, fostering a culture of continuous improvement.
-
Performance Assessments: Implement performance assessments to evaluate staff competency in inventory procedures. This can include practical assessments, written tests, or scenario-based evaluations to ensure that staff have grasped the training effectively.
-
Feedback Mechanism: Establish a feedback mechanism where staff can provide input on the effectiveness of the training programs. This feedback can be used to refine and improve the training materials and delivery methods.
-
Recognition and Incentives: Recognize and reward staff members who demonstrate exceptional understanding and adherence to inventory procedures. Incentives can motivate employees to actively engage in training and strive for excellence in their roles.
By implementing a comprehensive training program for inventory procedures, you can ensure that all staff members are well-equipped to handle inventory-related tasks efficiently, accurately, and in compliance with established protocols.
Implementing Safety Measures
Ensuring a safe working environment is paramount in any warehouse setting. Implementing robust safety measures not only protects the well-being of employees but also safeguards the integrity of the inventory. Here's a detailed approach to implementing safety measures within the warehouse:
-
Safety Training: Prioritize comprehensive safety training for all warehouse staff. This should encompass proper lifting techniques, equipment operation, hazard awareness, and emergency procedures. Regular safety refresher courses should also be conducted to reinforce best practices.
-
Personal Protective Equipment (PPE): Mandate the use of appropriate PPE such as hard hats, safety goggles, gloves, and high-visibility vests. Ensure that all staff members are equipped with the necessary protective gear to mitigate the risk of workplace injuries.
-
Equipment Maintenance: Establish a rigorous maintenance schedule for all warehouse equipment, including forklifts, conveyors, and pallet racking systems. Regular inspections and servicing help prevent equipment malfunctions that could compromise safety.
-
Clear Signage: Install clear and prominent signage throughout the warehouse to indicate safety protocols, emergency exits, restricted areas, and the location of safety equipment such as fire extinguishers and first aid kits.
-
Housekeeping Standards: Enforce strict housekeeping standards to keep the warehouse clean and organized. This includes promptly addressing spills, removing debris, and ensuring clear pathways to prevent slips, trips, and falls.
-
Emergency Response Plan: Develop a comprehensive emergency response plan that covers procedures for fires, medical emergencies, chemical spills, and other potential hazards. Conduct regular drills to ensure that all staff are familiar with emergency protocols.
-
Safety Inspections: Conduct regular safety inspections to identify and address potential hazards. This proactive approach helps in mitigating risks and maintaining a safe working environment for all warehouse personnel.
-
Ergonomic Considerations: Implement ergonomic principles in the design of workstations and material handling processes to reduce the risk of musculoskeletal injuries. This can include adjustable workbenches, lift-assist equipment, and ergonomic seating.
-
Safety Committee: Establish a safety committee comprising representatives from different areas of the warehouse. This committee can regularly review safety procedures, address safety concerns raised by staff, and collaborate on initiatives to enhance workplace safety.
-
Incident Reporting and Analysis: Implement a system for reporting and analyzing safety incidents. This allows for the identification of root causes and the implementation of corrective measures to prevent similar incidents in the future.
By diligently implementing these safety measures, warehouse operators can create a secure and compliant working environment, ensuring the well-being of employees and the protection of valuable inventory.
Read more: How To Organize A Reseller Inventory
Conclusion
In conclusion, organizing a warehouse inventory is a multifaceted process that requires careful planning, strategic implementation, and ongoing maintenance. By assessing inventory needs, designing an efficient warehouse layout, implementing a robust inventory management system, establishing effective receiving and shipping processes, utilizing storage solutions, conducting regular inventory audits, training staff on inventory procedures, and implementing safety measures, warehouse operators can create a well-organized and optimized inventory management system.
Maintaining a well-organized warehouse inventory not only enhances operational efficiency but also contributes to cost savings, improved accuracy, and a safer working environment. By following the guidelines outlined in this article, warehouse operators can streamline their inventory management processes, minimize errors, and ultimately provide a better experience for both employees and customers. It's essential to continuously evaluate and adapt these strategies to meet evolving business needs and industry standards, ensuring that the warehouse inventory remains organized and efficient in the long run.
Frequently Asked Questions about How To Organize A Warehouse Inventory
Was this page helpful?
At Storables.com, we guarantee accurate and reliable information. Our content, validated by Expert Board Contributors, is crafted following stringent Editorial Policies. We're committed to providing you with well-researched, expert-backed insights for all your informational needs.
0 thoughts on “How To Organize A Warehouse Inventory”