Home>Construction & Tools>Building Materials>How To Organize Parts Inventory
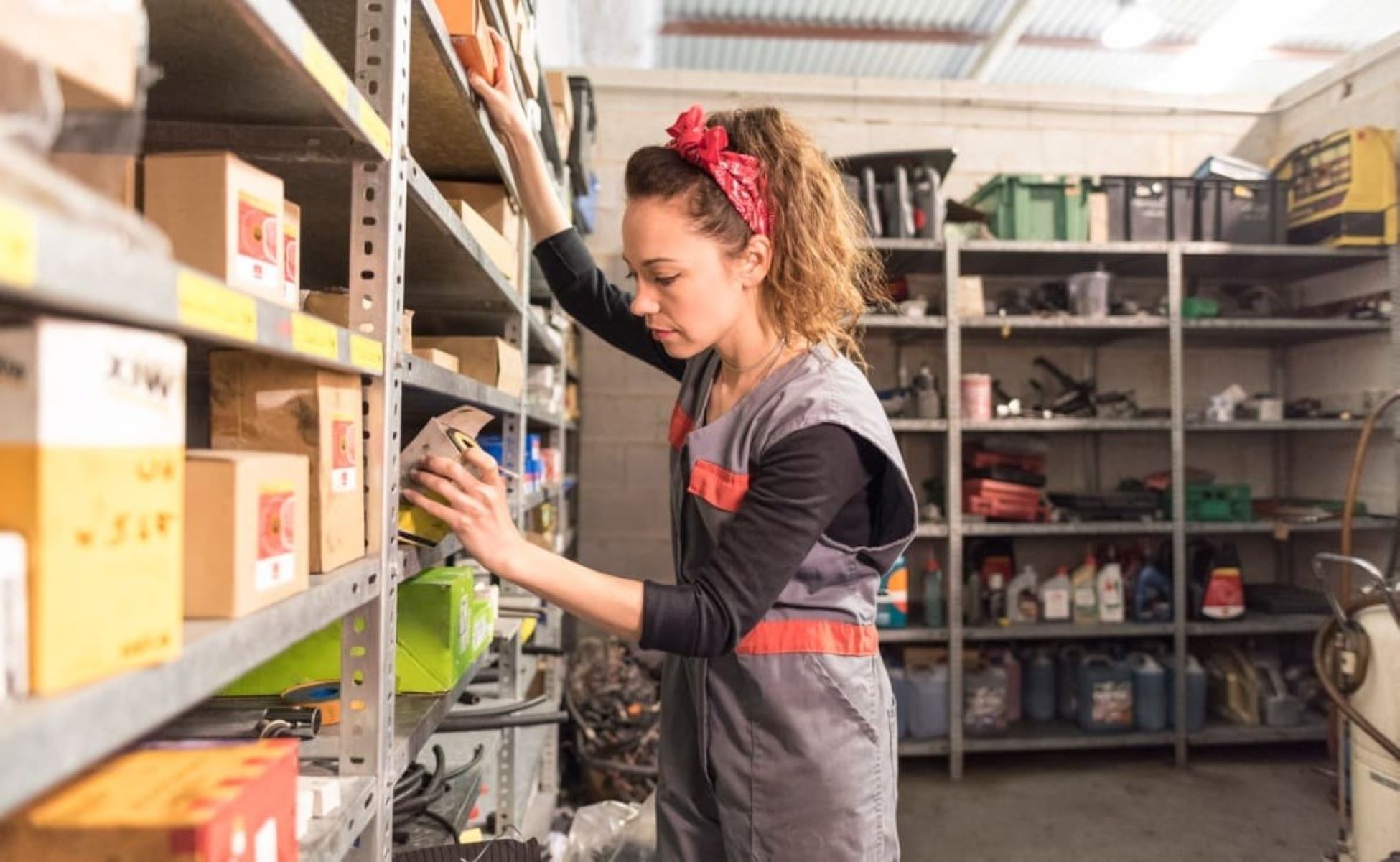
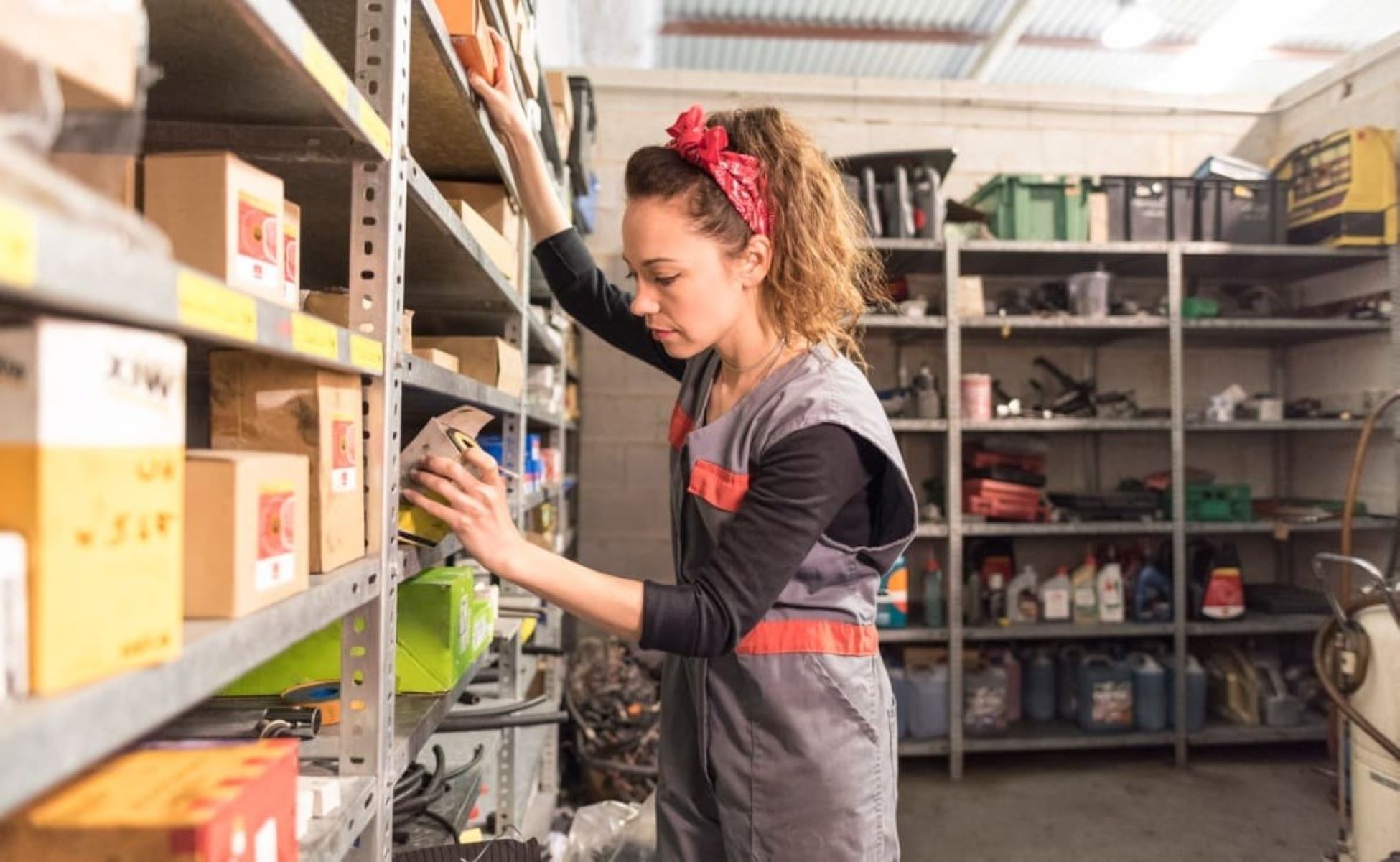
Building Materials
How To Organize Parts Inventory
Published: March 1, 2024
Learn how to efficiently organize your building materials inventory with our expert tips and strategies. Streamline your operations and improve productivity today!
(Many of the links in this article redirect to a specific reviewed product. Your purchase of these products through affiliate links helps to generate commission for Storables.com, at no extra cost. Learn more)
Introduction
Are you tired of spending hours searching for the right parts in your workshop or garage? Organizing your parts inventory can save you time, money, and frustration. Whether you're a DIY enthusiast or a professional tradesperson, having a well-organized parts inventory can make your projects run more smoothly and efficiently. In this article, we'll explore the importance of organizing your parts inventory and provide you with practical steps and best practices to help you maintain a tidy and efficient workspace.
Key Takeaways:
- Organizing your parts inventory saves time, money, and reduces frustration. It helps you work more efficiently, project professionalism, and maintain a safer workspace.
- Follow practical steps and best practices to organize and maintain your parts inventory. Regular audits, replenishment strategies, and adaptability are key to long-term organization and efficiency.
Read more: How To Organize Inventory
Importance of Organizing Parts Inventory
Organizing your parts inventory is crucial for several reasons:
-
Time-Saving: When your parts inventory is well-organized, you can quickly locate the items you need without wasting time searching through clutter. This means less downtime and more time spent on actual projects.
-
Cost-Effective: Proper organization can prevent you from purchasing duplicate items because you couldn't find the ones you already had. This saves you money and prevents unnecessary waste.
-
Efficiency: An organized parts inventory allows you to work more efficiently. You can focus on the task at hand instead of getting sidetracked by the chaos of a disorganized workspace.
-
Professionalism: Whether you're a DIY enthusiast or a professional tradesperson, an organized parts inventory reflects positively on your work ethic and attention to detail. It also helps you project a more professional image to clients and colleagues.
-
Safety: A cluttered workspace can be hazardous. By organizing your parts inventory, you can reduce the risk of accidents and injuries caused by tripping over or mishandling scattered items.
-
Peace of Mind: Knowing exactly where your parts are located can provide a sense of calm and control, reducing stress and frustration during projects.
-
Inventory Management: Proper organization is essential for keeping track of your parts inventory. It allows you to monitor stock levels, identify items that need replenishing, and plan for future projects more effectively.
In summary, organizing your parts inventory is not just about tidiness; it's about saving time, money, and effort while improving safety and productivity in your workspace.
Steps to Organize Parts Inventory
-
Assessment and Sorting: Begin by assessing your current inventory. Sort through all the parts and categorize them based on type, size, and usage. This initial step will give you a clear understanding of what you have and how you can best organize it.
-
Storage Solutions: Invest in suitable storage solutions such as bins, drawers, shelves, and cabinets. Choose containers that are transparent or label-friendly to make it easy to identify and locate items. Utilize stackable containers to maximize vertical space and keep the workspace tidy.
-
Labeling: Label each storage container or shelf with the specific contents it holds. Clear and concise labeling is essential for quick and accurate identification of parts. Consider using a labeling machine or adhesive labels for a professional and organized look.
-
Inventory Management System: Implement an inventory management system, whether it's a simple spreadsheet or specialized software. Keep track of the quantities, locations, and reorder points for each part. Regularly update the system as you add or use up items.
-
Zone Organization: Create designated zones for different types of parts. For example, have a separate area for electrical components, plumbing supplies, and hardware. This zoning system streamlines the retrieval process and minimizes the chances of misplacing items.
-
Regular Maintenance: Schedule regular maintenance sessions to review and reorganize the inventory. Check for expired or damaged parts, and dispose of them appropriately. This practice ensures that your inventory remains up-to-date and clutter-free.
-
Workstation Organization: Keep frequently used parts within easy reach of your workstation. Utilize pegboards, magnetic strips, or small parts organizers to store commonly accessed items. This setup enhances efficiency and reduces the time spent searching for specific parts.
-
Documentation: Maintain a detailed inventory log that records the movement of parts in and out of the inventory. This documentation helps in tracking usage patterns, identifying trends, and making informed purchasing decisions.
By following these steps, you can transform a chaotic parts inventory into a well-organized and efficient system that supports your DIY and home improvement projects.
Use a labeling system to categorize and organize parts inventory. This will make it easier to locate and track items, saving time and reducing errors.
Best Practices for Maintaining Organized Parts Inventory
Maintaining an organized parts inventory requires ongoing effort and dedication. Here are some best practices to help you sustain the organization and efficiency of your inventory:
-
Regular Audits: Conduct periodic audits of your parts inventory to ensure that everything is in its designated place. This practice helps identify any misplaced items and allows you to make necessary adjustments to maintain order.
-
Replenishment Strategy: Establish a replenishment strategy for frequently used parts. Monitor stock levels closely and set reordering triggers to prevent shortages. This proactive approach ensures that essential items are always available when needed.
-
Training and Guidelines: If you have a team or family members who access the parts inventory, provide training on the organization system and guidelines for maintaining it. Clear communication and understanding of the inventory management process are crucial for sustained organization.
-
Cleanliness and Maintenance: Keep the storage area clean and well-maintained. Regularly dust shelves, wipe down containers, and ensure that the storage space is free from clutter. A clean environment contributes to the overall organization and longevity of the parts.
-
Feedback Loop: Encourage feedback from individuals who interact with the inventory. They may have valuable insights on improving the organization or identifying items that are frequently misplaced. Implementing feedback can lead to continuous improvement.
-
Adaptability: Be open to adapting the organization system based on evolving needs. As your projects and inventory change, the organization system may need adjustments. Flexibility and adaptability are key to maintaining long-term organization.
-
Documentation Updates: Continuously update the inventory documentation to reflect any changes, additions, or removals. Accurate documentation ensures that everyone involved is working with the most current information.
-
Quality Control: Regularly inspect the condition of parts to ensure that they remain usable. Dispose of any damaged or expired items promptly to prevent them from cluttering the inventory and causing confusion.
By incorporating these best practices into your maintenance routine, you can uphold the organization of your parts inventory and enjoy the benefits of a streamlined and efficient workspace.
Conclusion
In conclusion, organizing your parts inventory is a fundamental aspect of maintaining an efficient and productive workspace, whether it's a DIY enthusiast's garage or a professional tradesperson's workshop. By investing time and effort into sorting, labeling, and maintaining your parts inventory, you can save time, reduce costs, enhance safety, and project a professional image. The steps outlined in this article, along with the best practices for sustaining organization, provide a comprehensive guide to transforming a cluttered inventory into a well-organized system. By implementing these strategies, you can streamline your projects, minimize downtime, and enjoy the peace of mind that comes with knowing exactly where your parts are located. Embracing organization in your parts inventory is a valuable investment that yields long-term benefits for your DIY and home improvement endeavors.
Frequently Asked Questions about How To Organize Parts Inventory
Was this page helpful?
At Storables.com, we guarantee accurate and reliable information. Our content, validated by Expert Board Contributors, is crafted following stringent Editorial Policies. We're committed to providing you with well-researched, expert-backed insights for all your informational needs.
0 thoughts on “How To Organize Parts Inventory”