Home>Others>Specialized Home Improvement Topics>How To Organize Inventory
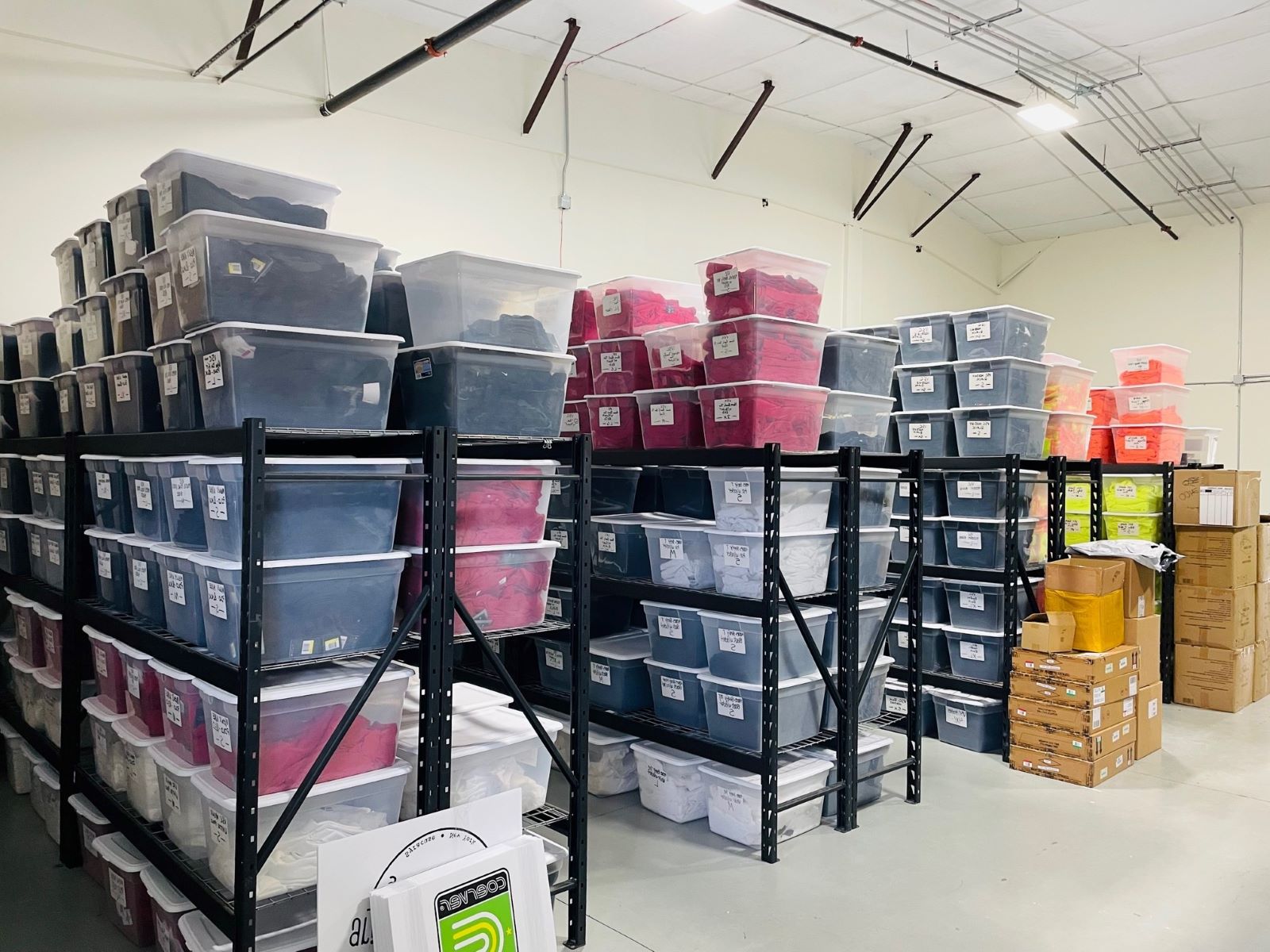
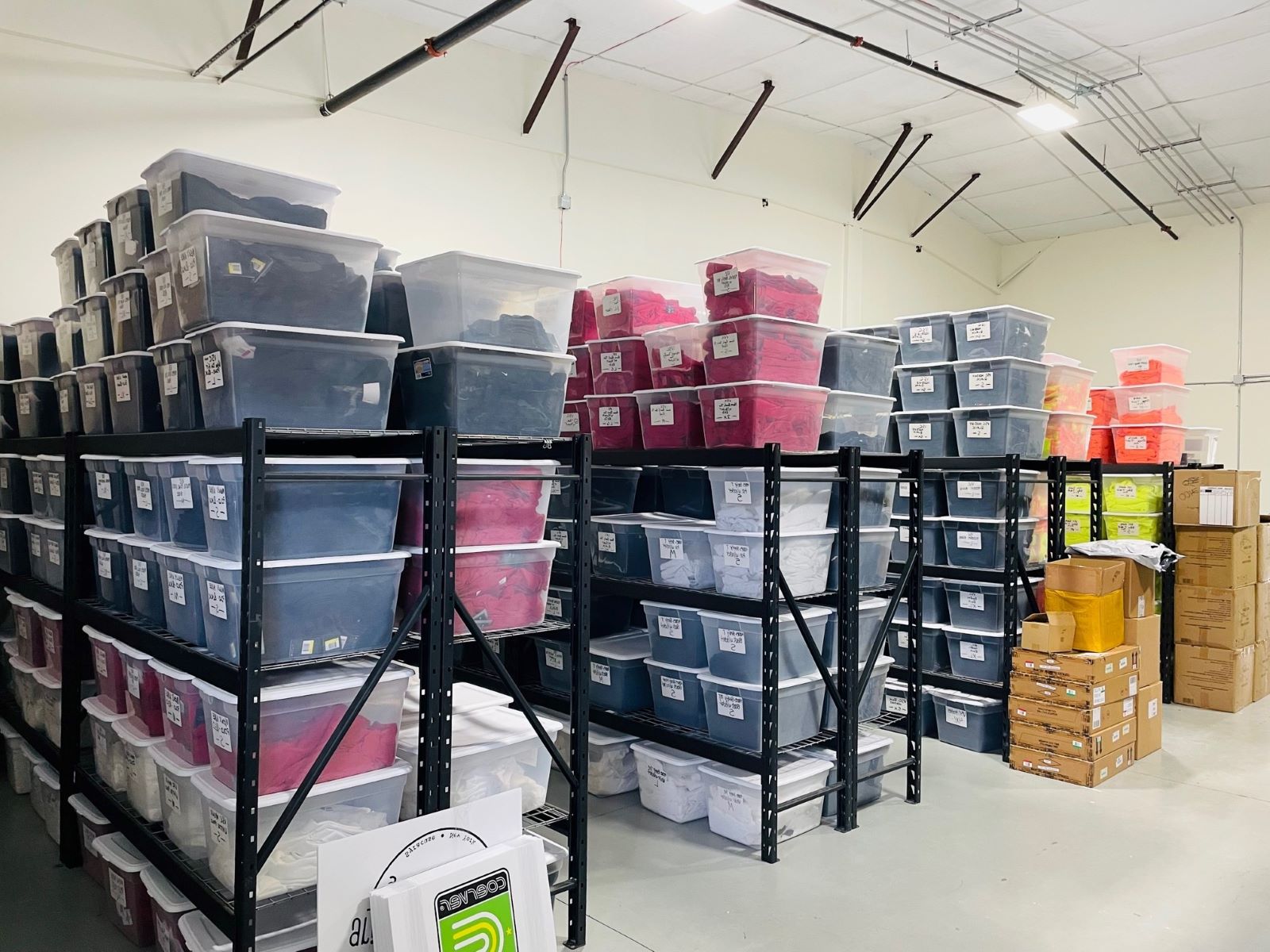
Specialized Home Improvement Topics
How To Organize Inventory
Published: March 2, 2024
Learn how to efficiently organize your inventory with our specialized home improvement topics. Streamline your storage and management processes today!
(Many of the links in this article redirect to a specific reviewed product. Your purchase of these products through affiliate links helps to generate commission for Storables.com, at no extra cost. Learn more)
Introduction
Are you struggling to keep track of your inventory? Do you find yourself spending too much time searching for items or constantly running out of essential supplies? If so, it's time to get your inventory organized. In this article, we will explore the importance of inventory organization and provide you with practical tips on how to streamline your inventory management process. Whether you're a small business owner, a warehouse manager, or simply looking to tidy up your home supplies, these tips will help you take control of your inventory and save time and money in the long run. Let's dive in!
Key Takeaways:
- Efficient inventory organization saves time, money, and reduces errors. It improves customer satisfaction and optimizes space utilization, benefiting businesses and households alike.
- Implementing inventory management software and establishing control procedures, along with conducting regular audits, streamlines operations and enhances overall efficiency.
Read more: How To Organize A Warehouse Inventory
Importance of Inventory Organization
Organizing your inventory is crucial for several reasons. Here's why it's so important:
-
Efficiency: Proper organization of your inventory can significantly improve efficiency. When items are neatly categorized and stored in designated areas, it becomes much easier to locate them when needed. This can save valuable time, especially in a fast-paced work environment.
-
Cost Savings: A well-organized inventory helps prevent overstocking or running out of essential items. By knowing exactly what you have and where it's located, you can avoid unnecessary purchases and reduce waste. This, in turn, can lead to cost savings for your business or household.
-
Customer Satisfaction: For businesses, having a well-organized inventory means being able to fulfill orders promptly and accurately. This can lead to increased customer satisfaction and loyalty, as customers receive their orders in a timely manner without any errors.
-
Space Optimization: Proper organization allows you to make the most of your available storage space. By utilizing storage solutions such as shelving, bins, and labeling, you can maximize the use of your space and avoid clutter.
-
Inventory Accuracy: When items are organized, it's easier to keep track of what's in stock and what needs to be replenished. This leads to improved inventory accuracy, reducing the likelihood of stockouts and backorders.
In summary, the importance of inventory organization cannot be overstated. It impacts efficiency, cost savings, customer satisfaction, space optimization, and inventory accuracy. By taking the time to organize your inventory, you can reap these benefits and create a more streamlined and productive environment.
Setting Up Inventory Categories
Setting up inventory categories is a fundamental step in organizing your inventory. By grouping similar items together, you can streamline the storage and retrieval process. Here's how to do it effectively:
-
Assess Your Inventory: Begin by assessing the types of items you need to categorize. This could include products, supplies, equipment, or materials. Take stock of the different types of items and their usage frequency.
-
Identify Common Characteristics: Look for common characteristics among the items. This could be their use, size, shape, or any other relevant factor. For example, if you're organizing office supplies, you might categorize items such as pens, paper, and staplers separately based on their use.
-
Create Clear Labels: Once you've identified the categories, create clear and descriptive labels for each. Use labels that are easy to read and understand. This could involve using color-coding, numerical systems, or clear text labels.
-
Allocate Storage Space: Allocate specific storage space for each category. This could involve using shelves, bins, or designated areas within a warehouse or storage room. Ensure that the storage space is appropriate for the quantity and size of items in each category.
-
Consider Accessibility: When setting up inventory categories, consider accessibility. Frequently used items should be easily accessible, while less frequently used items can be stored in less accessible areas. This ensures that items are readily available when needed.
-
Review and Adjust: Periodically review your inventory categories to ensure they still align with your needs. As your inventory changes, you may need to adjust or add new categories to accommodate new items.
By setting up clear and well-defined inventory categories, you can create a more organized and efficient inventory management system. This not only saves time but also reduces the likelihood of errors and misplaced items.
Implementing Inventory Management Software
Implementing inventory management software can revolutionize the way you handle your inventory. Here's a detailed guide on how to effectively implement this game-changing tool:
-
Assess Your Needs: Before choosing an inventory management software, assess your specific needs. Consider factors such as the size of your inventory, the number of users who will access the system, and the features you require, such as barcode scanning, reporting, and integration with other systems.
-
Research Options: There are numerous inventory management software options available, each with its own set of features and pricing. Research different software providers to find the one that best aligns with your requirements and budget.
-
Training and Support: Once you've selected a software solution, ensure that adequate training and support are provided. This is crucial for a smooth transition and effective utilization of the software. Many providers offer training sessions and support resources to help users get up to speed.
-
Data Migration: If you're transitioning from a manual or existing system, consider the process of migrating your data to the new software. Ensure that your data is accurately transferred to the new system without any loss or discrepancies.
-
Integration with Existing Systems: If you have existing systems such as accounting software or point-of-sale systems, ensure that the inventory management software can seamlessly integrate with these systems. This integration can streamline operations and data management across different functions.
-
Customization and Configuration: Depending on your specific needs, the software may require customization and configuration. This could involve setting up user permissions, defining workflows, and tailoring the system to match your unique inventory management processes.
-
Testing and Feedback: Before fully implementing the software, conduct thorough testing to identify any issues or areas for improvement. Gather feedback from users and make necessary adjustments to ensure that the software meets your requirements.
-
Go-Live Plan: Develop a comprehensive go-live plan for the implementation of the inventory management software. This plan should include timelines, user training schedules, data migration strategies, and contingency plans in case of any unforeseen challenges.
-
Ongoing Evaluation: Once the software is implemented, continuously evaluate its performance and user satisfaction. Address any issues promptly and consider regular updates or enhancements to further optimize the system.
By following these steps, you can effectively implement inventory management software and leverage its capabilities to streamline your inventory processes, improve accuracy, and enhance overall efficiency.
Use a consistent labeling system for all inventory items to easily track and locate them. Include important information such as item name, location, and quantity.
Establishing Inventory Control Procedures
Establishing robust inventory control procedures is essential for maintaining order and efficiency in managing your inventory. Here's a comprehensive guide on how to establish effective inventory control procedures:
-
Standard Operating Procedures (SOPs): Develop detailed SOPs for all inventory-related activities, including receiving, storing, picking, packing, and shipping. These procedures should outline the specific steps to be followed, quality standards, safety protocols, and responsibilities of personnel involved in each process.
-
Inventory Replenishment Rules: Establish clear rules for inventory replenishment based on factors such as reorder points, lead times, and economic order quantities. This ensures that stock levels are maintained at optimal levels, preventing stockouts or overstocking.
-
Quality Control Measures: Implement quality control measures to ensure that incoming inventory meets specified quality standards. This could involve inspection processes, quality checks, and adherence to supplier certifications.
-
Inventory Handling Guidelines: Define guidelines for handling and storing different types of inventory items. This includes considerations for perishable goods, fragile items, hazardous materials, and any specific storage requirements based on the nature of the products.
-
Barcode and Labeling Standards: Establish standardized barcode and labeling practices to uniquely identify and track inventory items. This facilitates accurate tracking, picking, and inventory visibility throughout the supply chain.
-
Cycle Counting Procedures: Develop procedures for conducting regular cycle counts to verify the accuracy of inventory records. This involves counting a subset of items on a frequent basis, allowing for ongoing reconciliation and identification of discrepancies.
-
Stock Rotation Policies: Implement stock rotation policies, especially for perishable or time-sensitive items. This ensures that older stock is used or sold first, reducing the risk of product expiration or obsolescence.
-
Security and Loss Prevention Protocols: Define security measures to prevent inventory shrinkage due to theft, damage, or unauthorized access. This could involve access controls, surveillance systems, and employee training on security protocols.
-
Documentation and Record-Keeping: Establish clear documentation and record-keeping procedures for all inventory-related activities. This includes maintaining accurate records of receipts, issues, adjustments, and any other inventory transactions.
-
Continuous Improvement Processes: Implement processes for continuous improvement, such as regular reviews of inventory control procedures, feedback mechanisms from staff, and analysis of key performance indicators to identify areas for enhancement.
By establishing comprehensive inventory control procedures, you can ensure that your inventory management processes are well-structured, efficient, and aligned with best practices in the industry. These procedures serve as a foundation for maintaining accuracy, minimizing errors, and optimizing the overall management of your inventory.
Read more: How To Organize Parts Inventory
Conducting Regular Inventory Audits
Regular inventory audits are essential for maintaining the accuracy and integrity of your inventory records. Here's a detailed guide on how to conduct effective inventory audits:
-
Schedule Audits: Establish a regular schedule for conducting inventory audits. The frequency of audits may vary based on the size of your inventory, the rate of inventory turnover, and the nature of the items being audited. For example, high-value or high-demand items may require more frequent audits.
-
Audit Planning: Plan the audit process in advance, considering factors such as the areas or sections of the inventory to be audited, the personnel involved, and the tools or technology to be used. Ensure that audits are scheduled at times that minimize disruption to regular operations.
-
Use of Technology: Leverage technology such as barcode scanners, RFID systems, or inventory management software to streamline the audit process. These tools can expedite the counting and verification of items, reduce human error, and provide real-time visibility into audit progress.
-
Physical Counting: Conduct physical counts of inventory items to verify their presence and accuracy against the recorded quantities. Ensure that the counting process is thorough and systematic, covering all designated areas and items within the inventory.
-
Verification of Documentation: Compare the results of the physical count with the existing inventory records, such as the inventory management system or manual logs. Identify any discrepancies and investigate the root causes, such as data entry errors, shrinkage, or inaccuracies in receiving or issuing processes.
-
Root Cause Analysis: In cases where discrepancies are identified, perform a root cause analysis to determine the reasons behind the discrepancies. This could involve reviewing transaction records, interviewing personnel involved in inventory handling, and examining the physical condition of items.
-
Corrective Actions: Based on the findings of the audit, implement corrective actions to address any discrepancies or issues identified. This could involve adjusting inventory records, investigating potential theft or loss, improving receiving and storage processes, or enhancing data entry accuracy.
-
Documentation of Audit Results: Maintain detailed documentation of the audit results, including the findings, corrective actions taken, and any recommendations for process improvements. This documentation serves as a valuable reference for future audits and continuous improvement efforts.
-
Reporting and Analysis: Generate comprehensive reports from the audit findings, highlighting key metrics such as accuracy rates, variance analysis, and trends in inventory discrepancies. Analyze the data to identify patterns or recurring issues that require attention.
-
Continuous Improvement: Use the insights gained from the audit process to drive continuous improvement in inventory management. This could involve refining inventory control procedures, enhancing training for personnel, or investing in additional technology to bolster accuracy and efficiency.
By conducting regular inventory audits and following these best practices, you can ensure that your inventory records remain accurate, minimize the risk of stock discrepancies, and uphold the integrity of your inventory management processes.
Conclusion
In conclusion, organizing your inventory is not just a matter of tidiness; it is a strategic imperative for businesses and households alike. By implementing effective inventory organization practices, such as setting up clear categories, leveraging inventory management software, establishing control procedures, and conducting regular audits, you can streamline operations, reduce costs, and enhance overall efficiency. The benefits of well-organized inventory extend beyond mere convenience; they contribute to improved customer satisfaction, optimized space utilization, and heightened accuracy in inventory management. Therefore, investing time and resources into organizing your inventory yields long-term dividends, making it a worthwhile endeavor for any entity that deals with managing stocks and supplies. Embracing these best practices will undoubtedly position you for success in maintaining a well-ordered and efficient inventory system.
Frequently Asked Questions about How To Organize Inventory
Was this page helpful?
At Storables.com, we guarantee accurate and reliable information. Our content, validated by Expert Board Contributors, is crafted following stringent Editorial Policies. We're committed to providing you with well-researched, expert-backed insights for all your informational needs.
0 thoughts on “How To Organize Inventory”