Home>diy>Building & Construction>What Is An EPC In Construction
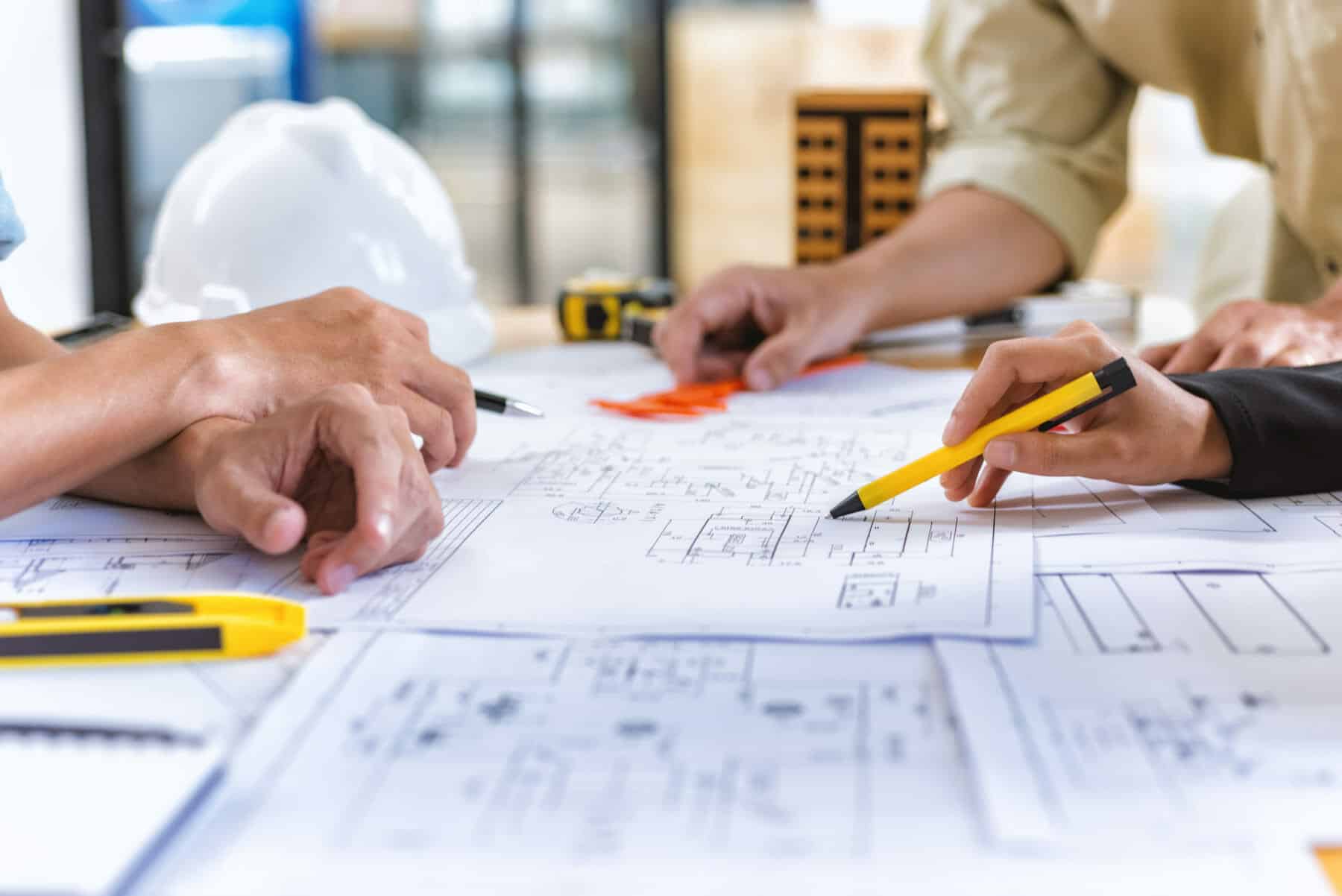
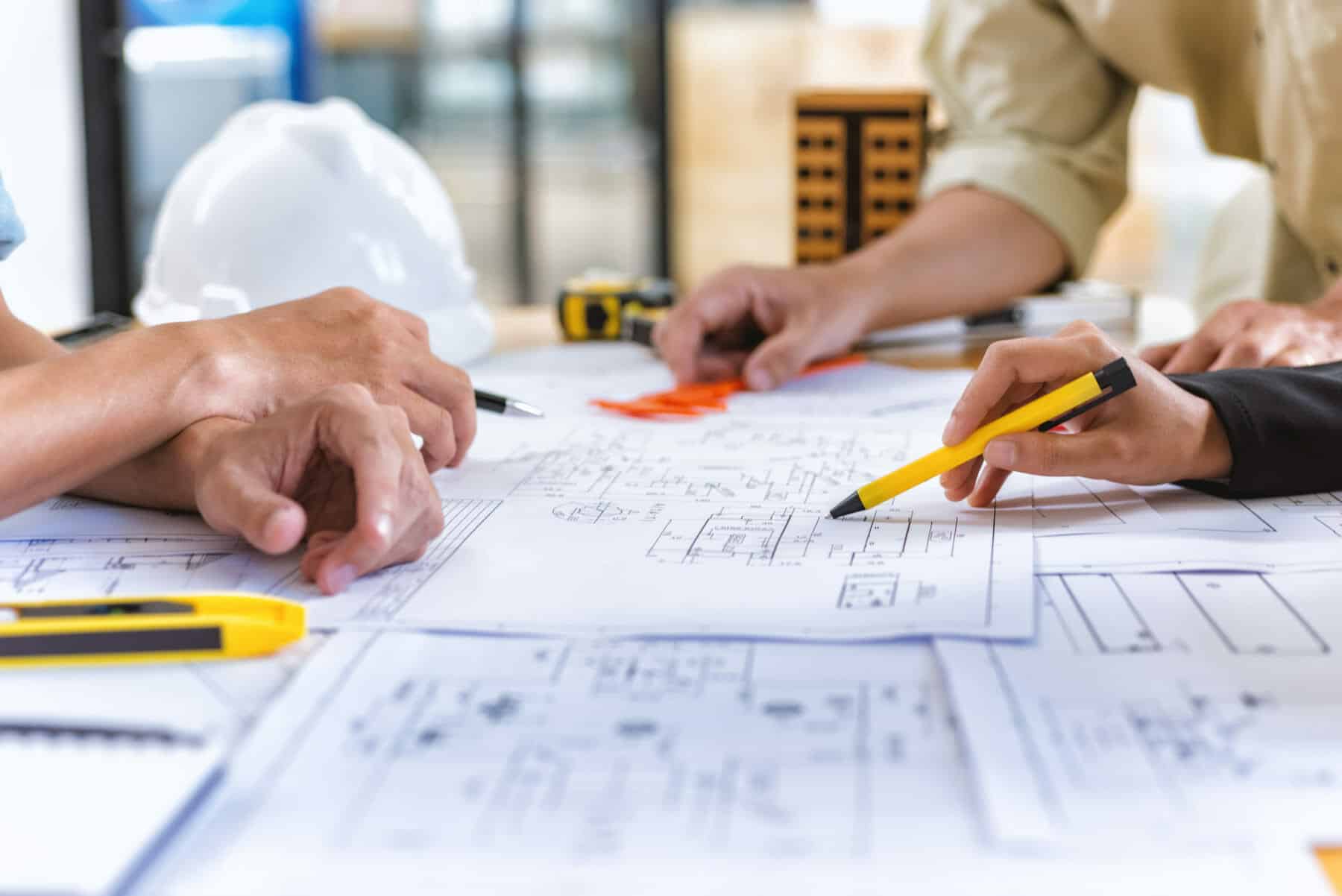
Building & Construction
What Is An EPC In Construction
Modified: September 1, 2024
Learn what an EPC is in construction and how it relates to building-construction. Understand its importance and impact on energy efficiency in buildings.
(Many of the links in this article redirect to a specific reviewed product. Your purchase of these products through affiliate links helps to generate commission for Storables.com, at no extra cost. Learn more)
Introduction
In the world of construction, efficient project management is crucial to ensure successful completion of projects. One important aspect of project management is the EPC (Engineering, Procurement, and Construction) approach. EPC is a comprehensive and integrated way of executing construction projects, providing a wide range of benefits to all stakeholders involved.
In this article, we will delve into the concept of EPC in construction, exploring its definition, role, benefits, key components, process overview, and challenges. By the end, you’ll have a solid understanding of the EPC approach and its significance in the construction industry.
So, what exactly is an EPC in construction? Let’s find out.
Key Takeaways:
- EPC in construction integrates project functions, providing a single point of accountability, streamlined communication, cost certainty, and enhanced project control, revolutionizing project management in the construction industry.
- While EPC offers numerous benefits, challenges such as project complexity, budget overruns, delays, and supply chain risks require proactive risk management and strong project management skills for successful project completion.
Read more: What Is Construction
Definition of EPC
The term EPC stands for Engineering, Procurement, and Construction. It is a project delivery method widely used in the construction industry to streamline and simplify the process of executing complex projects. Under the EPC approach, a single entity, typically an EPC contractor, takes on the responsibility of overseeing and managing all aspects of a construction project from design and engineering to procurement of materials and equipment, and ultimately, construction and commissioning.
Unlike traditional project delivery methods where multiple parties such as architects, engineers, contractors, and suppliers are involved, the EPC approach integrates all these functions into a single entity. This results in a more streamlined and efficient project execution process.
With an EPC contract, the client or project owner has a single point of contact and accountability throughout the project. This simplifies communication and decision-making, reducing the likelihood of delays, conflicts, and cost overruns that often arise from coordinating multiple parties.
The EPC approach is commonly used for large-scale infrastructure projects such as power plants, oil refineries, chemical plants, and major industrial facilities where complex engineering, procurement, and construction processes are involved. However, it can be adapted to various types of construction projects, depending on their size and complexity.
Now that we have established the definition of EPC in construction, let’s explore its role and why it is an advantageous approach for project management.
Role of EPC in Construction
The EPC approach plays a crucial role in the construction industry by providing a comprehensive and streamlined solution for project management. Here are some key roles that EPC plays in construction:
- Project Integration: EPC integrates various project activities such as engineering, procurement, and construction into a cohesive and coordinated process. This ensures seamless communication and collaboration among different project teams, resulting in better project outcomes.
- Project Planning and Design: EPC contractors are involved in the early stages of the project, contributing to the planning and design phase. They provide valuable insights and expertise to optimize the design and ensure its feasibility and constructability.
- Procurement Management: EPC contractors take full responsibility for procuring materials, equipment, and services required for the project. They leverage their networks and purchasing power to source high-quality materials at competitive prices, ensuring timely delivery and reducing procurement risks.
- Construction Management: EPC contractors oversee the construction phase, managing subcontractors, scheduling, and quality control. They ensure that the project is executed according to the agreed specifications and within the allotted time and budget.
- Risk Management: EPC contractors assume a significant portion of the project risks, including construction delays, unforeseen challenges, and cost overruns. They employ their expertise to mitigate risks and provide solutions to any issues that may arise during the project.
- Quality Assurance and Commissioning: EPC contractors are responsible for ensuring the quality of the constructed facility. They conduct rigorous inspections, testing, and commissioning activities to guarantee that the project meets the required standards and specifications.
- Project Handover: EPC contractors facilitate a smooth project handover to the client, providing comprehensive documentation, training, and support. They ensure that the client is equipped with all the necessary information and resources to operate and maintain the facility effectively.
Overall, the role of EPC in construction is to provide a holistic approach to project management, integrating various functions and minimizing the complexities and risks associated with traditional project delivery methods.
In the next section, we will explore the benefits of employing the EPC approach in construction projects.
Benefits of EPC in Construction
The EPC approach offers a multitude of benefits for construction projects of all sizes and complexities. Let’s delve into the advantages of employing the EPC method:
- Single Point of Accountability: With EPC, the client has a single point of contact throughout the project lifecycle. This eliminates the need to coordinate and manage multiple entities, reducing the chances of miscommunication, conflicts, and delays.
- Streamlined Communication: By integrating various project functions, EPC ensures streamlined communication among the project team. This improves coordination, decision-making, and problem-solving capabilities, leading to better project outcomes.
- Efficient Project Execution: EPC contractors have expertise in project management, enabling them to optimize project timelines, minimize construction delays, and enhance overall efficiency. This results in timely project completion, saving both time and costs.
- Cost Certainty: EPC contracts provide cost certainty to clients by incorporating fixed-price contracts. This eliminates pricing uncertainties and helps clients plan their budgets more accurately.
- Expertise and Technical Knowledge: EPC contractors possess extensive experience and technical knowledge in executing complex projects. They bring valuable insights and innovative solutions to ensure the project is designed, procured, and constructed in the most efficient and cost-effective manner.
- Risk Mitigation: EPC contractors assume a significant portion of the project risks, including construction risks and unforeseen challenges. They employ risk management strategies and contingency plans to mitigate potential issues, protecting the client from excessive financial and operational risks.
- Quality Assurance: EPC contractors are committed to delivering high-quality projects. They implement stringent quality control measures, conduct thorough inspections, and ensure compliance with industry standards and regulations.
- Enhanced Project Control: With the EPC approach, clients have better control over their projects. They can monitor the progress, track milestones, and receive regular updates from the EPC contractor, giving them peace of mind and confidence in project delivery.
- Improved Resource Management: EPC contractors efficiently manage resources, including labor, materials, and equipment, optimizing their utilization and minimizing wastage. This leads to cost savings and higher resource efficiency.
- Operational Excellence: EPC contractors prioritize considerations for the operation and maintenance of the facility. By designing and constructing projects with long-term functionality in mind, they enhance the overall operational excellence of the facility.
The benefits of EPC in construction make it an attractive option for clients seeking a streamlined and efficient project delivery method. In the next section, we will explore the key components of an EPC project that contribute to its success.
When reviewing an EPC in construction, pay close attention to the energy efficiency recommendations and estimated cost savings, as these can have a significant impact on the overall project budget and long-term operational expenses.
Key Components of EPC in Construction
A successful EPC project in construction relies on several key components working together harmoniously. Let’s explore these essential components:
- Engineering: The engineering phase involves conceptualizing, designing, and developing the project. It includes detailed engineering designs, feasibility studies, structural analysis, and the creation of construction drawings.
- Procurement: Procurement is a critical component of EPC projects and involves the sourcing and acquisition of materials, equipment, and services necessary for the construction. EPC contractors leverage their network of suppliers and negotiate contracts to ensure timely and cost-effective procurement.
- Construction: Construction is the physical execution of the project, involving activities such as site preparation, earthwork, foundation construction, erection of structures, installation of systems, and commissioning. EPC contractors manage the construction process, coordinating subcontractors and ensuring adherence to project specifications and timelines.
- Quality Control and Assurance: Maintaining and assuring the quality of the project is crucial. EPC contractors implement strict quality control measures during the construction phase, conducting inspections, tests, and audits to ensure that the project meets the required standards and specifications.
- Project Management: Project management is an integral part of EPC projects. It involves planning, scheduling, resource allocation, cost control, risk management, and coordination of various project activities. EPC contractors utilize project management tools and techniques to ensure smooth project execution and successful delivery.
- Commissioning and Handover: The commissioning phase involves testing and integrating various systems and components of the project to ensure their proper functioning. EPC contractors facilitate the commissioning process and ensure that the project is ready for handover to the client. This includes providing training, documentation, and support for the operation and maintenance of the facility.
- Health, Safety, and Environment (HSE): HSE considerations are of utmost importance in EPC projects. EPC contractors prioritize the implementation of effective safety measures and environmental protection practices throughout the project lifecycle, ensuring the well-being of the workforce and minimizing the project’s impact on the environment.
- Contract Management: Effective contract management is vital for the success of EPC projects. EPC contractors negotiate and manage contracts with subcontractors, suppliers, and other project stakeholders, ensuring compliance, resolving disputes, and addressing any contractual issues.
These key components work together to ensure the smooth execution of an EPC project in construction. Now that we understand the important components, let’s move on to explore the overall EPC process and its stages.
Read more: What Is WIP In Construction
EPC Process Overview
The EPC process consists of several stages that encompass the entire lifecycle of a construction project. Let’s explore the different stages of the EPC process:
- Preparation and Planning: This stage involves initial discussions between the client and the EPC contractor to establish project objectives, requirements, and constraints. The EPC contractor conducts feasibility studies, site evaluations, and cost estimates to determine the project’s viability and develop an initial project plan.
- Engineering and Design: In this stage, the detailed engineering and design activities take place. The EPC contractor collaborates with architects, engineers, and design teams to develop comprehensive design documents, construction drawings, and technical specifications.
- Procurement: Once the design is finalized, the EPC contractor begins the procurement process. This involves sourcing materials, equipment, and services needed for the project. The EPC contractor invites bids, assesses suppliers, negotiates contracts, and ensures timely delivery of materials and equipment to the construction site.
- Construction and Execution: The construction phase is where the physical work begins. The EPC contractor mobilizes the necessary resources, manages subcontractors, and oversees the construction activities. They ensure that the project is executed according to the design specifications, quality standards, and safety regulations.
- Quality Control and Assurance: Throughout the construction phase, the EPC contractor conducts regular inspections and tests to maintain quality standards. They verify that the work meets the specified requirements and address any non-compliance issues promptly.
- Commissioning and Handover: Before the project is handed over to the client, the EPC contractor carries out commissioning activities. This involves testing and integrating various systems, conducting performance evaluations, and ensuring the project is ready for operational use. Once completed, the EPC contractor facilitates a smooth handover to the client, providing documentation, training, and support.
- Operation and Maintenance: After project handover, the client assumes responsibility for the ongoing operation and maintenance of the facility. The EPC contractor may provide post-construction support or maintenance services as per the agreed terms.
Each stage of the EPC process is interconnected and requires effective project management, coordination, and communication. By following a systematic approach, EPC projects can be executed efficiently, delivering successful outcomes.
However, it’s important to recognize that EPC projects are not without challenges and risks. Let’s explore some of the common challenges faced in EPC projects in the next section.
Challenges and Risks in EPC Projects
While the EPC approach offers numerous advantages, it is important to be aware of the challenges and risks associated with EPC projects. Here are some common challenges that may arise:
- Complexity: EPC projects are often complex, involving multiple stakeholders, intricate engineering designs, and tight schedules. Managing and coordinating these complexities can be a significant challenge.
- Budget and Cost Overruns: Construction projects are susceptible to cost overruns due to unforeseen circumstances, design changes, or other factors. Proper cost estimation and control measures are crucial to avoid exceeding the budget.
- Project Delays: Delays can occur due to various reasons, such as weather conditions, unforeseen site conditions, or supplier constraints. Effective project management strategies and contingency plans are necessary to mitigate the impact of delays.
- Supply Chain and Procurement Risks: EPC projects depend on the timely delivery of materials and equipment. Any disruptions in the supply chain or procurement process can lead to delays or quality issues.
- Technical and Design Challenges: Complex engineering designs and evolving technologies can present technical and design challenges during the project execution. Proper planning, collaboration, and problem-solving are essential to overcome these challenges.
- Contractual and Legal Issues: EPC projects involve various contracts and legal agreements with subcontractors, suppliers, and other parties. Proper contract management and clear communication are critical to avoid disputes and ensure compliance.
- Health, Safety, and Environmental Risks: Construction sites pose inherent health, safety, and environmental risks. Complying with regulatory standards, implementing robust safety measures, and promoting a culture of safety are essential to mitigate these risks.
- Communication and Coordination: With multiple stakeholders involved in an EPC project, effective communication and coordination are crucial. Ensuring clear communication channels and regular project updates can help prevent misunderstandings and conflicts.
- Change Management: Changes in project requirements, design modifications, or client requests can impact project schedules and cost. Implementing a robust change management process is essential to handle these changes effectively.
- Operational Readiness: Ensuring a seamless transition from construction to operation requires careful planning and coordination. Adequate training, documentation, and support for the client are vital to achieve operational readiness.
Addressing these challenges and risks requires proactive risk management, effective communication, and a strong project management approach. With proper planning and mitigation strategies, the potential negative impacts of these challenges can be minimized, leading to successful project completion.
Now that we have explored the challenges and risks, let’s conclude our discussion on EPC projects.
Conclusion
The EPC (Engineering, Procurement, and Construction) approach has revolutionized project management in the construction industry. By integrating various project functions into a single entity, the EPC method offers numerous benefits, including streamlined communication, efficient project execution, cost certainty, and enhanced project control. It provides a comprehensive and holistic solution for clients, from project planning and design to procurement, construction, and project handover.
Throughout the EPC process, key components such as engineering, procurement, construction, quality control, and project management work together to ensure the successful execution of projects. However, it is important to be mindful of the challenges and risks, such as project complexity, budget overruns, delays, supply chain risks, and contractual issues.
Addressing these challenges requires effective risk management strategies, proactive communication, and proper project planning. EPC projects demand strong project management skills, technical expertise, and attention to detail to ensure successful outcomes.
In conclusion, the EPC approach has significantly transformed the construction industry, providing clients with a streamlined and efficient project delivery method. By leveraging the expertise of EPC contractors, clients can achieve their project objectives and overcome the complexities and risks often associated with large-scale construction projects.
Ultimately, the EPC approach sets the stage for successful construction projects, delivering high-quality results while meeting budget and schedule expectations. By embracing the EPC method, clients can embark on their construction endeavors with confidence, knowing that their projects are in capable hands.
Frequently Asked Questions about What Is An EPC In Construction
Was this page helpful?
At Storables.com, we guarantee accurate and reliable information. Our content, validated by Expert Board Contributors, is crafted following stringent Editorial Policies. We're committed to providing you with well-researched, expert-backed insights for all your informational needs.
0 thoughts on “What Is An EPC In Construction”