Home>diy>Building & Construction>What Is EPC In Construction
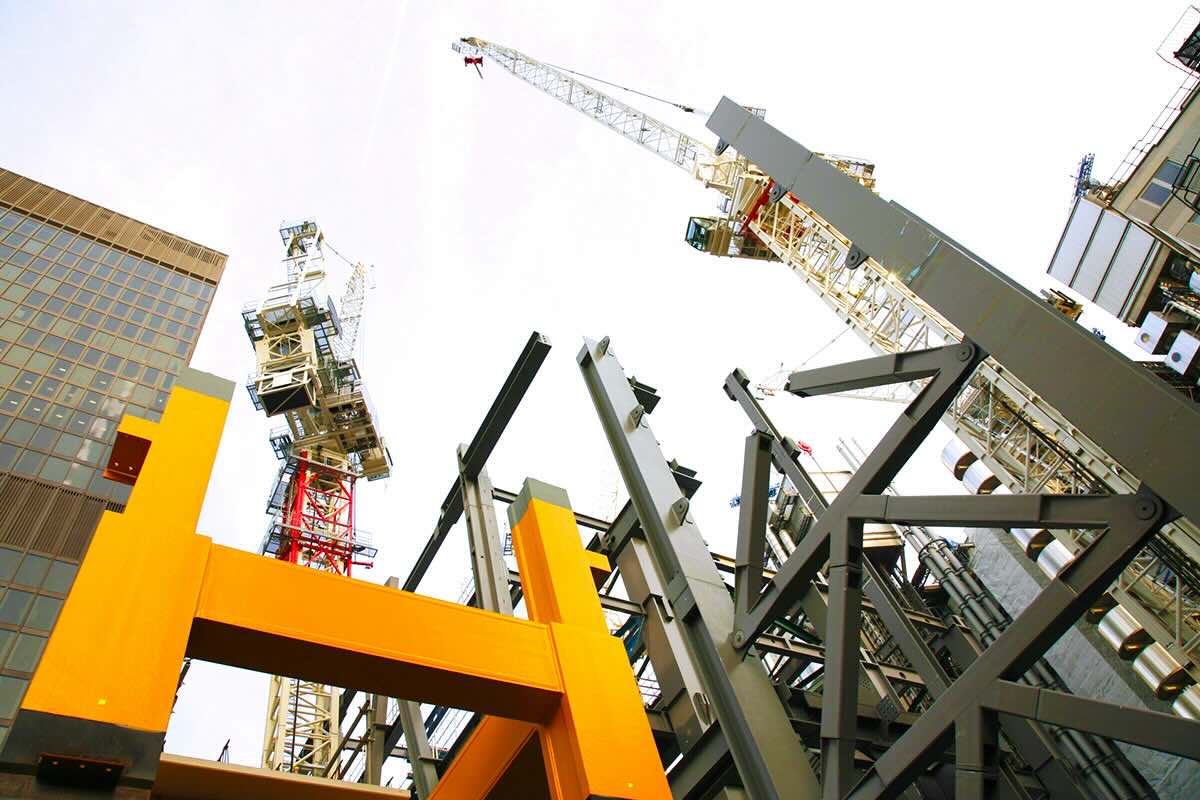
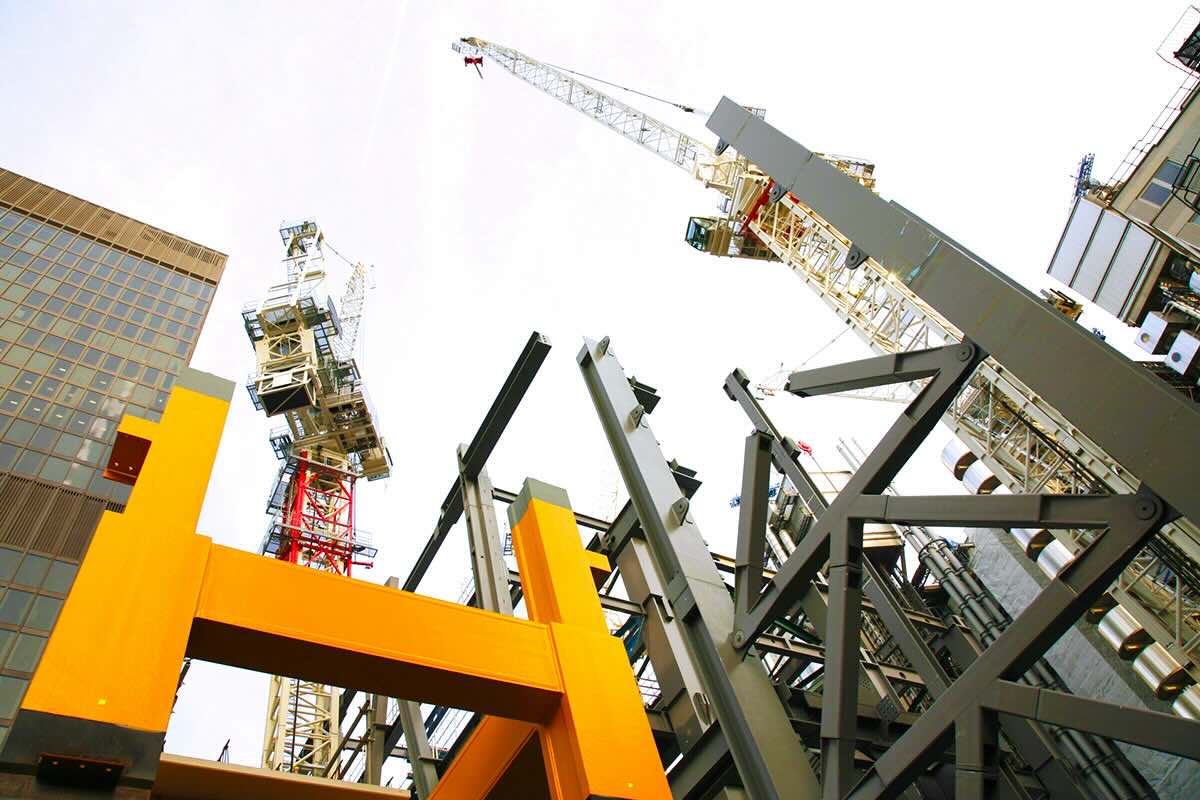
Building & Construction
What Is EPC In Construction
Modified: December 7, 2023
Learn all about EPC in construction, a vital element in building-construction projects. Gain insights into its significance and how it impacts project delivery.
(Many of the links in this article redirect to a specific reviewed product. Your purchase of these products through affiliate links helps to generate commission for Storables.com, at no extra cost. Learn more)
Introduction
When it comes to the world of construction, there are various terms and acronyms that are thrown around. One such acronym is EPC, which stands for Engineering, Procurement, and Construction. EPC is a popular approach in the construction industry, particularly in large-scale projects like power plants, infrastructure development, and industrial facilities.
Understanding what EPC means and how it is implemented is essential for anyone involved in the construction industry. In this article, we will delve into the definition of EPC in construction, explore the key elements of EPC projects, discuss the benefits and challenges associated with this approach, compare it to other project delivery methods, and provide some real-life examples to give you a clearer picture.
So, let’s dive in and unravel the world of EPC in construction.
Key Takeaways:
- EPC in construction offers streamlined project delivery, cost control, and quality assurance through integrated engineering, procurement, and construction activities under a single entity, the EPC contractor.
- The EPC approach reduces administrative burdens for project owners, provides efficient time management, and has been successfully employed in diverse projects, from power plants to renewable energy initiatives.
Read more: What Is An EPC In Construction
Definition of EPC in Construction
EPC, or Engineering, Procurement, and Construction, is a project delivery method widely used in the construction industry. It is a comprehensive approach that streamlines the entire construction process, from conceptual design to project completion. The EPC contractor is responsible for the design, procurement of materials and equipment, and construction execution.
The EPC approach aims to provide a seamless and efficient project delivery process by integrating engineering, procurement, and construction activities under a single entity. This consolidates responsibilities and ensures better coordination, cost control, and time management from the start to the end of the project.
In an EPC project, the contractor is typically engaged by the project owner or developer through an EPC contract. This contract clearly outlines the terms and conditions of the project, including the scope of work, project timeline, budget, and performance standards.
The EPC contractor assumes full responsibility for delivering the project within the agreed-upon parameters. They must adhere to all relevant regulations and codes, manage subcontractors and suppliers, and ensure the quality, safety, and cost-effectiveness of the construction process.
By taking a holistic approach, EPC in construction minimizes the project owner’s risks and burdens. Instead of dealing with multiple contractors and suppliers separately, the owner can entrust the entire project to a single entity, simplifying communication and decision-making.
Overall, EPC in construction offers an efficient and streamlined project delivery method that encompasses all essential aspects of design, procurement, and construction. It is a popular choice for complex projects that require a high level of coordination and expertise.
Understanding the EPC Contract
In an EPC project, the contract between the project owner and the EPC contractor is a crucial document that outlines the rights, responsibilities, and obligations of both parties. The EPC contract serves as a roadmap for the entire project, ensuring clear communication and alignment of expectations.
The EPC contract typically includes the following key elements:
- Scope of Work: This section defines the specific tasks and deliverables that the EPC contractor will be responsible for. It outlines the engineering design, equipment procurement, and construction activities that need to be executed to complete the project.
- Project Timeline: The contract specifies the project duration and milestones. It sets deadlines for major project stages, ensuring that the construction progresses according to a predetermined schedule.
- Budget and Payment Terms: The contract outlines the project budget and payment terms. It defines the total project cost, the payment schedule, and any provisions for cost adjustments or change orders.
- Performance Guarantees: The EPC contractor may be required to provide performance guarantees to assure the project owner of the quality and functionality of the delivered project. This can include performance bonds, warranties, or other forms of assurance.
- Change Management: The contract should include provisions for handling any changes or modifications that may arise during the project. This typically includes a change order process, which outlines how changes will be initiated, assessed, and approved, along with any associated costs or schedule adjustments.
- Termination and Dispute Resolution: In the event of contract termination or disputes, the contract should include provisions for resolution methods, such as mediation, arbitration, or litigation.
- Insurance and Indemnity: The contract should specify the insurance requirements for the project, including liability coverage, and outline the procedure for handling any claims or damages.
- Intellectual Property: If there are any intellectual property rights associated with the project, the contract should address ownership, use, and protection of these rights.
Understanding the intricacies of the EPC contract is crucial for both the project owner and the EPC contractor. It ensures that all parties have a clear understanding of their roles, responsibilities, and the project’s expectations. Consulting legal professionals familiar with construction contracts can help ensure that the EPC contract is comprehensive, fair, and legally binding.
Key Elements of EPC Projects
EPC projects involve several key elements that contribute to their success and effectiveness in the construction industry. These elements are designed to ensure efficient project delivery, cost control, and adherence to quality standards. Let’s explore the key elements of EPC projects:
- Engineering: The engineering phase is one of the initial steps in an EPC project. It involves the development of detailed designs, plans, and specifications for the construction project. The engineering team is responsible for ensuring that the project meets all technical requirements, complies with regulations, and is optimized for efficiency and safety.
- Procurement: The procurement element of an EPC project involves the selection and sourcing of materials, equipment, and services needed for construction. The EPC contractor is responsible for identifying the right suppliers, managing the procurement process, and ensuring timely delivery of materials to the construction site.
- Construction: The construction phase involves the actual execution of the project. It includes site preparation, physical construction, installation of equipment and systems, and overall project management. The EPC contractor is responsible for supervising the construction activities, coordinating subcontractors, ensuring compliance with safety regulations, and maintaining quality control.
- Project Management: Effective project management is a crucial element of EPC projects. It involves overseeing all aspects of the project, including planning, coordination, scheduling, cost control, and risk mitigation. The project manager ensures that the project progresses smoothly, stays on track, and meets the intended outcomes within the specified constraints.
- Quality Assurance and Control: Maintaining high-quality standards is paramount in EPC projects. The EPC contractor implements quality assurance and control measures throughout the project lifecycle, ensuring that the construction meets all specified requirements. This includes conducting inspections, performing tests, and addressing any non-compliance issues promptly.
- Health, Safety, and Environment: EPC projects prioritize the health and safety of workers, as well as environmental protection. The EPC contractor must comply with safety regulations, implement safety protocols, provide appropriate safety training, and maintain a safe working environment. Additionally, environmental considerations such as waste management and sustainability practices should be incorporated into the project.
- Commissioning and Handover: As the project nears completion, the commissioning process begins. This involves testing and verifying the functionality and performance of systems and equipment before handing over the project to the owner. The EPC contractor ensures that all systems are functioning correctly and conducts any necessary adjustments or repairs to meet the project specifications.
- Operations and Maintenance: After the project is handed over, the EPC contractor may provide ongoing operations and maintenance services as per the contract. This includes routine maintenance, inspections, repairs, and addressing any warranty issues. Properly maintaining the completed project ensures its longevity and optimal performance.
These key elements work together to facilitate the smooth execution of EPC projects, from initial design to final handover. By integrating engineering, procurement, and construction under a single entity, EPC projects offer a comprehensive and efficient approach to construction.
When evaluating construction projects, it’s important to understand EPC (Engineering, Procurement, and Construction) contracts. These contracts encompass the design, procurement, and construction phases, providing a comprehensive approach to project delivery.
Benefits and Challenges of EPC in Construction
EPC, or Engineering, Procurement, and Construction, is a project delivery approach that offers several benefits to the construction industry. However, it also presents certain challenges that need to be considered. Let’s explore the benefits and challenges of EPC in construction:
- Streamlined Project Delivery: One of the key advantages of EPC is the streamlined project delivery process. By integrating engineering, procurement, and construction activities under a single entity, EPC projects ensure better coordination, communication, and efficiency. This helps to minimize delays and conflicts that can arise when dealing with multiple contractors and suppliers.
- Single Point of Responsibility: EPC projects assign a single entity, the EPC contractor, the responsibility for the entire project. This provides the project owner with a single point of contact, simplifying decision-making and reducing the owner’s administrative burden. The EPC contractor assumes full accountability for delivering the project within the specified parameters.
- Cost Control: EPC contracts often include fixed-price agreements or capped-price arrangements. This provides cost certainty for the project owner and reduces the risk of cost overruns. The EPC contractor is responsible for managing subcontractors and suppliers, negotiating favorable deals, and ensuring that project costs remain within the agreed budget.
- Quality Assurance: EPC projects emphasize quality assurance and control throughout the construction process. The EPC contractor is responsible for adhering to all project specifications, codes, and standards. By maintaining strict quality control measures and conducting inspections and tests, EPC projects strive to deliver a high-quality end product.
- Efficient Time Management: EPC projects typically have well-defined project timelines and milestones. The integrated nature of EPC allows for better time management and scheduling of activities. By optimizing the construction sequence, coordinating resources effectively, and implementing efficient project management practices, EPC projects aim to deliver projects on time.
While EPC offers significant benefits, it also presents some challenges that need to be addressed:
- Complexity: EPC projects, especially large-scale and complex ones, can be intricate and demanding. Coordinating various disciplines, managing multiple subcontractors, and ensuring compliance with numerous regulations require expertise and effective project management.
- Risk Allocation: The EPC contractor assumes a significant amount of risk in an EPC project. They are responsible for both design and construction aspects, which can be challenging if unforeseen issues arise during the project. Proper risk assessment and management are crucial to mitigate potential risks effectively.
- Contract Clarity: The EPC contract must be well-drafted, clearly defining roles, responsibilities, and expectations. Ambiguous contract terms can lead to disputes and delays. Engaging legal professionals experienced in EPC contracts can help ensure that all parties have a clear understanding of their obligations.
- Procurement Challenges: EPC projects involve extensive procurement of materials and equipment, which requires effective supplier management and negotiation skills. Ensuring timely delivery, quality control, and cost control throughout the procurement process can be a challenge.
Despite the challenges, the benefits of EPC in construction make it a favored project delivery method for many large-scale and complex construction projects. With proper planning, expert execution, and efficient project management, EPC can lead to successful and cost-effective project outcomes.
Read more: What Is EPC Construction
EPC vs. Design-Build vs. Construction Management
When it comes to project delivery methods in construction, EPC, design-build, and construction management are commonly used approaches. Each method has its unique characteristics, advantages, and considerations. Let’s compare EPC, design-build, and construction management:
- EPC (Engineering, Procurement, and Construction): In an EPC project, a single entity, the EPC contractor, is responsible for the design, procurement, and construction of the project. This approach offers streamlined project delivery, single point of responsibility, cost control, and quality assurance. The project owner has reduced administrative burden but limited control over design decisions.
- Design-Build: In a design-build project, a single entity, known as the design-builder, is responsible for both the design and construction of the project. This integrated approach offers benefits like streamlined communication, faster project delivery, and potential cost savings. The project owner has a single point of contact but limited involvement in the design process.
- Construction Management: In construction management, the project owner contracts with a construction manager, who acts as a consultant throughout the project. The construction manager provides expertise in areas like planning, scheduling, cost estimation, and subcontractor management. This approach offers project owner involvement, flexibility, and the ability to make design decisions. However, it requires more active participation from the project owner and potentially more management effort.
Here are some key considerations when choosing between EPC, design-build, and construction management:
- Owner Control: EPC projects and design-build projects offer a more hands-off approach for project owners, as the responsibility for design and construction lies with the contractor. Construction management, on the other hand, allows the owner to have more control and involvement in the decision-making process.
- Project Complexity: EPC projects are well-suited for complex projects that require a high level of coordination and expertise across engineering, procurement, and construction. Design-build projects can also handle complex projects efficiently, relying on the design-builder’s integrated approach. Construction management is suitable for projects where the owner wants more direct control and oversight.
- Time and Cost Considerations: EPC projects and design-build projects are often associated with faster project delivery due to the integrated nature of the approach. Construction management projects may take longer due to increased coordination requirements. Cost control mechanisms can be different in each approach, so it’s important to consider the specific project requirements and budget constraints.
- Risk Allocation: EPC projects and design-build projects typically assign more risk to the contractor, as they are responsible for both design and construction. Construction management projects can have a different risk allocation, depending on the contract agreements between the owner and the construction manager.
In summary, EPC, design-build, and construction management are project delivery methods that cater to different project needs and owner preferences. Each approach offers benefits and considerations that should be carefully evaluated based on the project’s complexity, time and cost constraints, owner involvement, and risk allocation.
Examples of EPC Projects
EPC (Engineering, Procurement, and Construction) projects are commonly found in various industries, ranging from power generation and infrastructure development to oil and gas facilities. Here are a few notable examples of EPC projects:
- Power Plants: Building power plants often involves EPC contracts due to their complex nature. For instance, the Medupi Power Plant in South Africa, one of the largest dry-cooled coal-fired power stations in the world, was executed as an EPC project. The EPC contractor was responsible for the engineering design, procurement of equipment, and construction execution of the entire power plant.
- Water and Wastewater Treatment: Many water and wastewater treatment facilities are executed as EPC projects. The Orange County Water District’s Groundwater Replenishment System in California is a notable example. This project involved the design, procurement, and construction of a state-of-the-art water purification plant that replenishes drinking water supplies by treating wastewater to a high-quality standard.
- Industrial Facilities: EPC projects are commonly used in the construction of industrial facilities. One example is the Ras Tanura Integrated Project in Saudi Arabia. This EPC project involved the expansion and integration of multiple oil and gas facilities, including refineries, petrochemical plants, and utilities, to enhance the country’s energy sector.
- Infrastructure Development: Large-scale infrastructure projects often adopt the EPC approach. The Shanghai Yangshan Deep-Water Port in China, one of the world’s largest automated container ports, was executed as an EPC project. The EPC contractor was responsible for the design, procurement, and construction of the port’s infrastructure, including its quays, container yards, and supporting facilities.
- Renewable Energy Projects: EPC projects are prevalent in the renewable energy sector. The SolarReserve’s Crescent Dunes Solar Energy Project in Nevada, USA, is an example of an EPC project in the solar power industry. It involved the engineering, procurement, and construction of a concentrated solar power plant with advanced energy storage capabilities.
These examples demonstrate the wide range of industries and projects where the EPC approach is applied. EPC projects encompass a diverse set of construction projects that require comprehensive coordination, expertise, and accountability across engineering, procurement, and construction activities.
It’s worth noting that EPC projects can vary in scale and complexity, ranging from large-scale power plants and industrial facilities to smaller-scale projects such as commercial buildings or infrastructure upgrades. The applicability of the EPC approach depends on the specific requirements and objectives of each project.
Conclusion
EPC (Engineering, Procurement, and Construction) in construction is a project delivery method that offers efficiency, streamlined coordination, and comprehensive accountability. It integrates engineering, procurement, and construction activities under a single entity, the EPC contractor, to ensure seamless project execution from start to finish.
By entrusting the entire project to a single entity, EPC projects provide project owners with a single point of contact, reducing administrative burdens and enhancing decision-making processes. This approach offers benefits such as streamlined project delivery, cost control, quality assurance, and efficient time management.
While EPC projects offer numerous advantages, it’s important to consider the specific needs and challenges associated with this approach. EPC projects can be complex, and risk allocation and contract clarity are critical factors to address. The choice between EPC, design-build, and construction management should be based on project complexity, owner involvement preferences, time and cost considerations, and risk allocation.
Throughout various industries, EPC has been successfully employed in a wide range of projects, including power plants, water and wastewater treatment facilities, industrial complexes, infrastructure development, and renewable energy projects. These examples highlight the versatility and effectiveness of the EPC approach in achieving project objectives.
In conclusion, EPC in construction is a valuable project delivery method that offers an integrated approach to engineering, procurement, and construction. It allows for efficient project execution, reduced administrative burden for owners, and delivers projects on time and within budget. By understanding the principles and elements of EPC, stakeholders in the construction industry can make informed decisions and successfully navigate the complexities of construction projects.
Frequently Asked Questions about What Is EPC In Construction
Was this page helpful?
At Storables.com, we guarantee accurate and reliable information. Our content, validated by Expert Board Contributors, is crafted following stringent Editorial Policies. We're committed to providing you with well-researched, expert-backed insights for all your informational needs.
0 thoughts on “What Is EPC In Construction”