Home>diy>Building & Construction>What Is ICF Construction
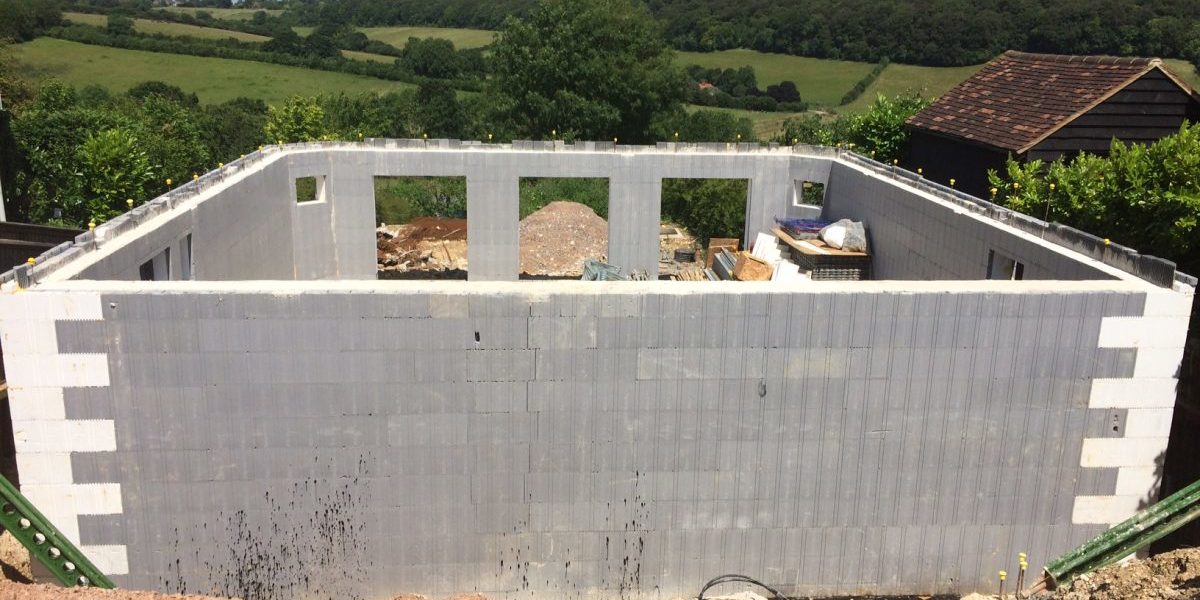
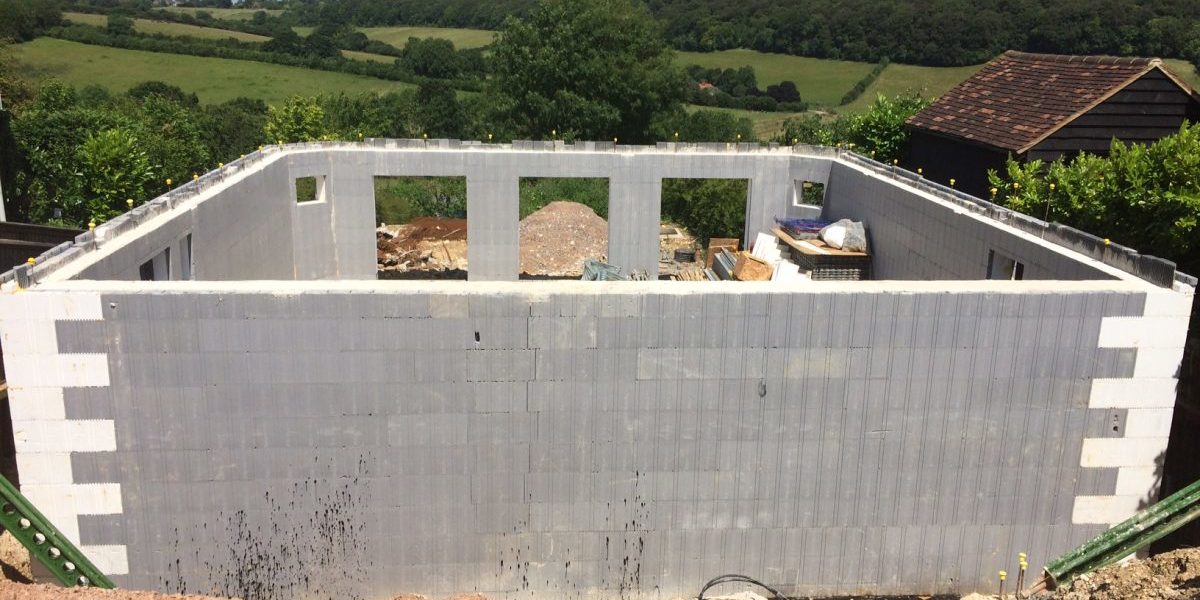
Building & Construction
What Is ICF Construction
Modified: December 7, 2023
Learn about the benefits of ICF construction for building-construction. Discover its energy efficiency and durability, making it an ideal choice for your next project.
(Many of the links in this article redirect to a specific reviewed product. Your purchase of these products through affiliate links helps to generate commission for Storables.com, at no extra cost. Learn more)
Introduction
Welcome to the world of building construction, where innovation and technology continuously evolve to create structures that are not only durable but also sustainable. In recent years, there has been a significant shift towards more energy-efficient and environmentally friendly construction methods. One such method that has gained popularity is Insulated Concrete Form (ICF) construction.
ICF construction is a cutting-edge approach that combines the durability of concrete with the insulation properties of foam. This unique combination results in buildings that are both structurally sound and energy-efficient. Whether you are a homeowner planning to build your dream house or a developer working on a commercial project, understanding the basics of ICF construction is essential.
In this article, we will delve deep into the world of ICF construction, exploring its definition, how it works, its advantages and disadvantages, common applications, cost considerations, and a comparison with traditional building methods. By the end of this article, you will have a comprehensive understanding of ICF construction and its potential to revolutionize the construction industry.
Key Takeaways:
- ICF construction combines concrete and foam for energy-efficient, durable buildings. It offers superior insulation, soundproofing, and design flexibility, revolutionizing the construction industry.
- While ICF construction may have higher initial costs and require specialized skills, its long-term benefits and environmental sustainability make it a compelling choice for efficient and resilient structures.
Read more: What Is Construction
Definition of ICF Construction
Insulated Concrete Form (ICF) construction is a building technique that utilizes interlocking foam blocks or panels as the framework for pouring concrete walls. These foam blocks or panels act as a formwork and remain in place after the concrete has set, providing both insulation and structural support.
The foam blocks used in ICF construction are typically made from expanded polystyrene (EPS) or extruded polystyrene (XPS). EPS is a lightweight, rigid foam that offers excellent thermal insulation properties. XPS, on the other hand, is a denser foam that provides higher compressive strength. Both types of foam blocks have proven to be effective in ICF construction.
The foam blocks or panels in ICF construction come in various shapes and sizes, allowing for flexibility in design. They are stacked and secured together to create the desired wall thickness, creating a solid and continuous surface for pouring the concrete. The blocks have pre-formed interlocking mechanisms that ensure proper alignment during construction.
Once the foam blocks are in place, rebar reinforcement is inserted vertically and horizontally within the cavities of the blocks. This reinforcement adds strength to the structure, making it capable of withstanding the forces of nature, such as wind and seismic activity.
After the rebar is positioned, concrete is poured into the cavities of the foam blocks, filling the entire space. The concrete then cures and hardens, becoming the load-bearing structure of the building. The foam acts as both insulation and formwork, remaining in place permanently and eliminating the need for additional insulation or wall finishes.
ICF construction is highly versatile and can be used for various types of structures, including residential homes, commercial buildings, and even high-rise structures. It offers superior thermal performance, sound insulation, and durability compared to traditional construction methods.
Now that we have a clear understanding of what ICF construction is, let’s explore how it works and the advantages it offers.
How ICF Construction Works
ICF construction follows a step-by-step process that involves precise planning and implementation. Here is a breakdown of how ICF construction works:
- Design and Planning: The first step in any construction project is careful design and planning. Architects and engineers collaborate to create detailed drawings and specifications, ensuring that the structure meets all safety, functional, and aesthetic requirements.
- Site Preparation: Before construction can begin, the site needs to be prepared. This includes clearing the land, leveling the area, and ensuring proper drainage. It is essential to have a solid and stable base for the ICF walls.
- Formwork Installation: The foam blocks or panels are assembled and secured in place according to the designed wall thickness and layout. The interlocking mechanisms ensure proper alignment and structural integrity.
- Rebar Placement: Vertical and horizontal reinforcing bars (rebar) are inserted into the cavities of the foam blocks. The rebar provides additional strength and reinforcement, ensuring structural stability.
- Concrete Pouring: Once the formwork and rebar are in place, concrete is poured into the cavities of the foam blocks. It fills the entire space, encapsulating the rebar and creating a solid, monolithic structure. Care must be taken to ensure proper consolidation of the concrete to eliminate air gaps.
- Curing and Finishing: After the concrete is poured, it needs time to cure and harden. The curing process typically takes a few weeks, during which time the concrete gains strength and durability. Once cured, the surface can be finished with various materials, such as stucco, siding, or brick, to enhance aesthetics.
- Interior Finishes: The interior of the building can be finished as per the design requirements. This includes insulation, drywall installation, flooring, and other interior details.
- Utilities and Systems Integration: Electrical, plumbing, and HVAC systems are installed within the walls and ceilings. Proper integration of these systems is crucial to ensure functionality and efficiency.
- Final Inspections and Occupancy: Before occupancy, the construction will undergo multiple inspections to ensure compliance with building codes and regulations. Once approved, the building is ready for use.
ICF construction provides a streamlined process with fewer steps compared to traditional construction methods. The foam blocks act as both insulation and formwork, reducing the need for separate insulation installation and eliminating the need for temporary formwork removal.
Now that we understand how ICF construction works, let’s explore the advantages it offers over traditional building methods.
Advantages of ICF Construction
ICF construction offers a range of advantages that make it an attractive choice for both homeowners and builders. Let’s explore some of the key benefits of ICF construction:
- Energy Efficiency: One of the biggest advantages of ICF construction is its exceptional energy efficiency. The foam insulation used in ICF walls provides a continuous thermal barrier, reducing heat transfer and preventing energy loss. This results in reduced heating and cooling costs, making buildings more environmentally friendly and cost-effective.
- Strength and Durability: ICF walls are incredibly strong and durable. The combination of concrete and foam creates a solid structure capable of withstanding extreme weather conditions, including high winds and earthquakes. ICF walls have high fire resistance and are resistant to rot, mold, and pests, ensuring long-lasting performance and low maintenance.
- Noise Reduction: The insulating properties of ICF walls contribute to excellent sound insulation. They effectively reduce the transmission of sound from the outside, creating a quieter interior environment. This is particularly beneficial for residential buildings located in noisy areas or near busy roads.
- Improved Indoor Air Quality: The foam insulation used in ICF construction is free from harmful chemicals and allergens. This helps to improve indoor air quality by reducing the infiltration of outdoor pollutants, such as dust, pollen, and allergens. It creates a healthier and more comfortable living environment for occupants.
- Design Flexibility: ICF construction offers a wide range of design possibilities. The foam blocks can be easily customized and shaped to meet various architectural styles and design preferences. With ICF, it is possible to create curved walls, arches, and unique architectural features that would be challenging to achieve with traditional construction methods.
- Construction Speed: ICF construction can be faster than traditional construction methods. The interlocking foam blocks or panels simplify the building process and reduce the need for multiple trades. Additionally, the insulation and formwork are already integrated into the system, eliminating the need for separate insulation installation and temporary formwork removal.
- Environmental Sustainability: ICF construction is considered more environmentally sustainable compared to traditional construction methods. The use of foam insulation reduces energy consumption, and the use of concrete decreases the reliance on wood, which helps conserve natural resources. Additionally, ICF walls have excellent thermal mass properties, which can contribute to more stable indoor temperatures and further reduce energy consumption.
These advantages make ICF construction an attractive option for homeowners and builders who prioritize energy efficiency, durability, and comfort. However, it is important to consider the potential disadvantages before deciding on this construction method, which we will explore in the next section.
Disadvantages of ICF Construction
While ICF construction offers numerous benefits, it is essential to consider the potential disadvantages before committing to this construction method. Here are some of the drawbacks associated with ICF construction:
- Higher Initial Cost: The upfront cost of ICF construction can be higher compared to traditional construction methods. The cost of the foam blocks and specialized construction techniques may result in higher initial expenses. However, it is important to consider the long-term savings in energy costs and maintenance when evaluating the overall cost-effectiveness.
- Specialized Skills and Knowledge: ICF construction requires specialized skills and knowledge. Builders and contractors need to be well-trained in ICF construction techniques to ensure proper installation and the structural integrity of the building. This may limit the pool of available contractors and increase construction time.
- Limited Availability of Contractors: In some regions, finding experienced contractors who specialize in ICF construction may be challenging. It is important to research and ensure that there are qualified professionals available in the area before proceeding with an ICF construction project.
- Planning Considerations: ICF construction requires meticulous planning to ensure accurate dimensions and alignment of the foam blocks. The architectural and engineering design must be carefully coordinated to accommodate the specific requirements of ICF construction, which may require additional time and attention during the planning stage.
- Building Code Compliance: Building codes and regulations may vary by region, and it is essential to ensure that ICF construction meets the specific requirements of the local building code. Additional inspections and approvals may be necessary to ensure compliance, which can add time and cost to the construction process.
- Increased Wall Thickness: ICF walls are typically thicker than traditional walls due to the foam insulation and formwork. This can result in reduced interior space and potentially impact the overall design and layout of the building.
- Limited Exterior Finish Options: The foam blocks or panels used in ICF construction require a compatible exterior finish. While there are various options available, such as stucco, siding, or brick, the choices may be more limited compared to traditional construction methods.
Despite these disadvantages, many builders and homeowners find that the advantages of ICF construction outweigh the drawbacks. Understanding these potential challenges allows for proper planning and informed decision-making during the construction process.
Now that we have explored the advantages and disadvantages of ICF construction, let’s take a look at some of the common applications of this building method.
ICF construction stands for Insulated Concrete Form construction, which uses interlocking foam blocks filled with concrete to create strong, energy-efficient walls. It’s important to ensure proper installation and sealing to maximize the benefits of ICF construction.
Read more: What Is CSI In Construction
Common Applications of ICF Construction
ICF construction is a versatile building method that can be applied to various types of structures. Here are some of the common applications of ICF construction:
- Residential Homes: ICF construction is particularly popular for residential homes. Whether it’s a single-family house or a multi-unit development, the energy efficiency, durability, and sound insulation qualities of ICF make it an excellent choice for homeowners. ICF walls provide a comfortable and quiet living environment, reducing energy consumption and offering long-term savings on heating and cooling costs.
- Commercial Buildings: ICF construction is often used in the construction of commercial buildings as well. From office buildings to retail spaces and hotels, the energy-efficient properties of ICF contribute to lower operating costs and create a comfortable indoor environment for occupants. Additionally, the strength and durability of ICF walls provide added safety and security for commercial structures.
- Institutional Buildings: Schools, healthcare facilities, and government buildings can benefit from ICF construction. The excellent sound insulation properties of ICF walls create a conducive environment for learning and healing. The energy efficiency also helps reduce operating costs for these institutions, allowing for more resources to be allocated to other areas.
- High-Rise Buildings: Although less common, ICF construction can be utilized in the construction of high-rise buildings. The combination of concrete and foam offers excellent structural stability and fire resistance. Proper engineering and design considerations are essential when applying ICF construction to high-rise structures to ensure compliance with building codes and regulations.
- Industrial Buildings: Industrial structures, such as warehouses and manufacturing facilities, can benefit from ICF construction. The energy efficiency and durability of ICF walls contribute to better insulation and lower maintenance costs. The ability to regulate indoor temperatures more effectively makes it an ideal choice for environments that require controlled temperature conditions.
- Green Buildings: ICF construction aligns well with green building principles and sustainable design practices. The energy efficiency and reduced environmental impact make ICF an attractive choice for those seeking environmentally friendly construction methods. Additionally, the durability and longevity of ICF structures contribute to reduced waste from renovation or demolition.
These are just a few examples of the common applications of ICF construction. The versatility and benefits of this building method make it suitable for a wide range of structures across different sectors.
Now, let’s delve into the cost considerations of ICF construction and explore how it compares to other building methods.
Cost of ICF Construction
When considering ICF construction, it is important to take into account the cost implications associated with this building method. While ICF construction offers numerous advantages, it can come with a higher initial cost compared to traditional construction methods. Here are some key cost considerations:
- Material Costs: The cost of materials for ICF construction typically includes the foam blocks or panels, concrete, rebar reinforcement, and any additional materials required for installation. The cost of foam blocks can vary depending on the type and quality of foam used.
- Labor Costs: The labor costs for ICF construction can be higher compared to traditional methods. ICF construction requires specialized skills and knowledge, and finding experienced ICF contractors may be more challenging in certain regions. It is essential to consider the labor costs when budgeting for an ICF construction project.
- Design and Engineering Costs: The design and engineering phase of an ICF construction project may require additional costs. The precise planning, coordination, and structural engineering involved in ICF construction can result in higher design and engineering fees compared to traditional methods.
- Additional Cost Considerations: There are additional cost considerations that may arise during the ICF construction process. These can include the need for specialized equipment for concrete pouring, inspections and permits, and the cost of exterior finishes compatible with the foam blocks or panels used.
- Long-Term Savings: While the initial cost of ICF construction may be higher, it is important to consider the long-term savings that ICF can offer. The energy efficiency of ICF walls can result in reduced heating and cooling costs over the lifetime of the building. Additionally, the durability and low maintenance requirements of ICF structures can lead to long-term cost savings.
It is important to conduct a thorough cost analysis when considering ICF construction. This analysis should include a comparison of ongoing energy savings, maintenance costs, and potential resale value. Consulting with experienced ICF professionals and obtaining multiple cost estimates can help ensure a comprehensive understanding of the financial implications of ICF construction.
Now, let’s compare ICF construction to traditional building methods to gain a better understanding of its advantages and differences.
Comparing ICF Construction to Other Building Methods
ICF construction offers several distinct advantages when compared to traditional building methods. Let’s take a closer look at how ICF construction compares to other building methods:
- Energy Efficiency: ICF construction is known for its exceptional energy efficiency. The foam insulation used in ICF walls provides a continuous thermal barrier, minimizing heat transfer and reducing energy consumption. In comparison, traditional construction methods often require additional insulation installation, which can be less effective and time-consuming.
- Durability: ICF construction offers enhanced durability compared to traditional construction methods. ICF walls are capable of withstanding extreme weather conditions, providing better resistance to high winds, seismic activity, and fire. Additionally, ICF walls are less susceptible to rot, mold, and pests, ensuring long-term structural integrity.
- Noise Reduction: ICF construction provides superior sound insulation compared to traditional construction. The foam insulation inherent in ICF walls effectively reduces the transmission of sound, creating a quieter interior environment. In contrast, traditional construction methods may require additional soundproofing measures to achieve a similar level of noise reduction.
- Construction Speed: ICF construction can be faster compared to traditional construction methods. The interlocking foam blocks or panels simplify the building process and reduce the need for multiple trades. Additionally, the insulation and formwork are already integrated into the system, eliminating the need for separate installation and temporary formwork removal, which can often be time-consuming and labor-intensive.
- Design Flexibility: ICF construction offers flexibility in design. The foam blocks can be easily customized and shaped to accommodate various architectural styles and design preferences. With ICF, it is possible to create curved walls, arches, and unique architectural features that may be challenging to achieve with traditional construction methods.
- Environmental Impact: ICF construction has a lower environmental impact compared to traditional building methods. The use of foam insulation reduces energy consumption, and the use of concrete decreases the reliance on wood, which helps conserve natural resources. Additionally, the durability and long lifespan of ICF structures contribute to reduced waste and environmental footprint.
While ICF construction offers numerous advantages, it is important to note that traditional construction methods have their own benefits. Traditional construction methods often have lower initial material costs and a larger pool of available contractors, making them more accessible in certain regions. Additionally, traditional construction methods might offer more options and flexibility for exterior and interior finishes.
Ultimately, the choice between ICF construction and traditional methods depends on various factors, including project requirements, budget, and personal preferences. It is essential to thoroughly evaluate these factors and consult with professionals to determine the most suitable construction method for a specific project.
To conclude, ICF construction is a forward-thinking building method that offers significant advantages in terms of energy efficiency, durability, and sound insulation. While it may have higher initial costs and require specialized skills, the long-term benefits and environmental sustainability make ICF construction a compelling choice for those seeking to build efficient and resilient structures.
Conclusion
ICF construction has emerged as a game-changer in the field of building construction. This innovative method combines the structural strength of concrete with the insulating properties of foam, resulting in energy-efficient, durable, and soundproof buildings.
In this article, we explored the definition and working principles of ICF construction. We discussed how foam blocks or panels are stacked and secured together to create the formwork, which is then filled with concrete to form the walls of the building. We also highlighted the advantages of ICF construction, such as energy efficiency, durability, noise reduction, and design flexibility.
While ICF construction offers numerous benefits, it is important to consider the potential drawbacks, including higher initial costs, the need for specialized skills, and limited availability of contractors. However, these challenges can be addressed with careful planning, budgeting, and engaging experienced professionals in the construction process.
ICF construction is commonly used in various applications, including residential homes, commercial buildings, institutional structures, high-rise buildings, and industrial facilities. Its energy efficiency, durability, and environmental sustainability make it an attractive choice for those seeking to create comfortable, cost-effective, and environmentally friendly structures.
We also discussed the cost considerations of ICF construction, including material costs, labor costs, and long-term savings. While the initial costs may be higher compared to traditional construction methods, the energy savings and reduced maintenance requirements can contribute to long-term cost savings and improved return on investment.
Finally, we compared ICF construction to traditional building methods, highlighting the advantages of ICF construction in terms of energy efficiency, durability, noise reduction, construction speed, design flexibility, and environmental impact. However, it is important to recognize that traditional construction methods have their own benefits and may be more suitable for specific projects.
In conclusion, ICF construction is a cutting-edge building method that offers a range of benefits, including energy efficiency, durability, noise reduction, and design flexibility. By considering the advantages and disadvantages, as well as project requirements and budget, individuals can make informed decisions and leverage the advantages of ICF construction to transform their vision into reality.
Frequently Asked Questions about What Is ICF Construction
Was this page helpful?
At Storables.com, we guarantee accurate and reliable information. Our content, validated by Expert Board Contributors, is crafted following stringent Editorial Policies. We're committed to providing you with well-researched, expert-backed insights for all your informational needs.
0 thoughts on “What Is ICF Construction”