Home>diy>Building & Construction>What Is An NCR In Construction
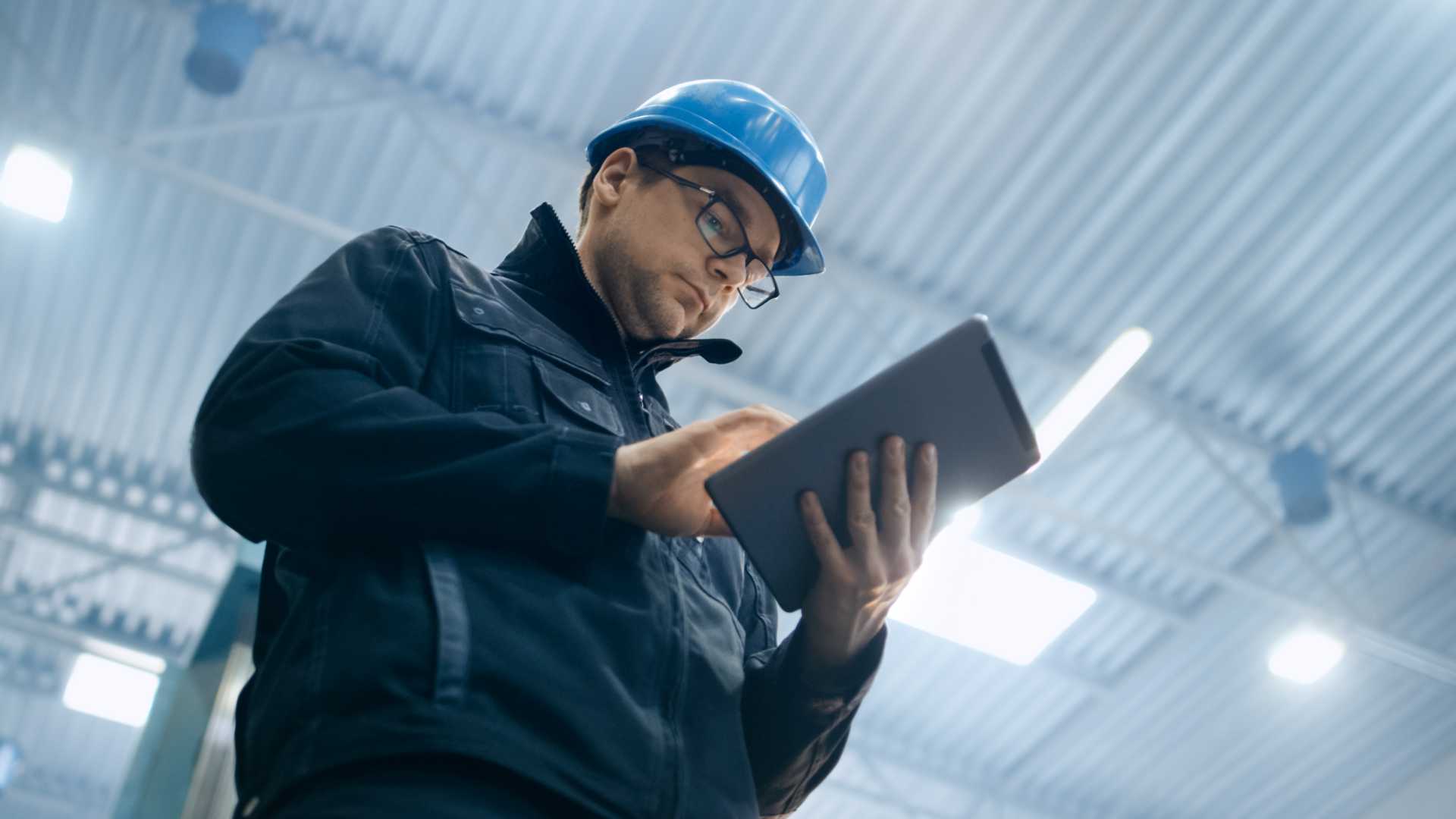
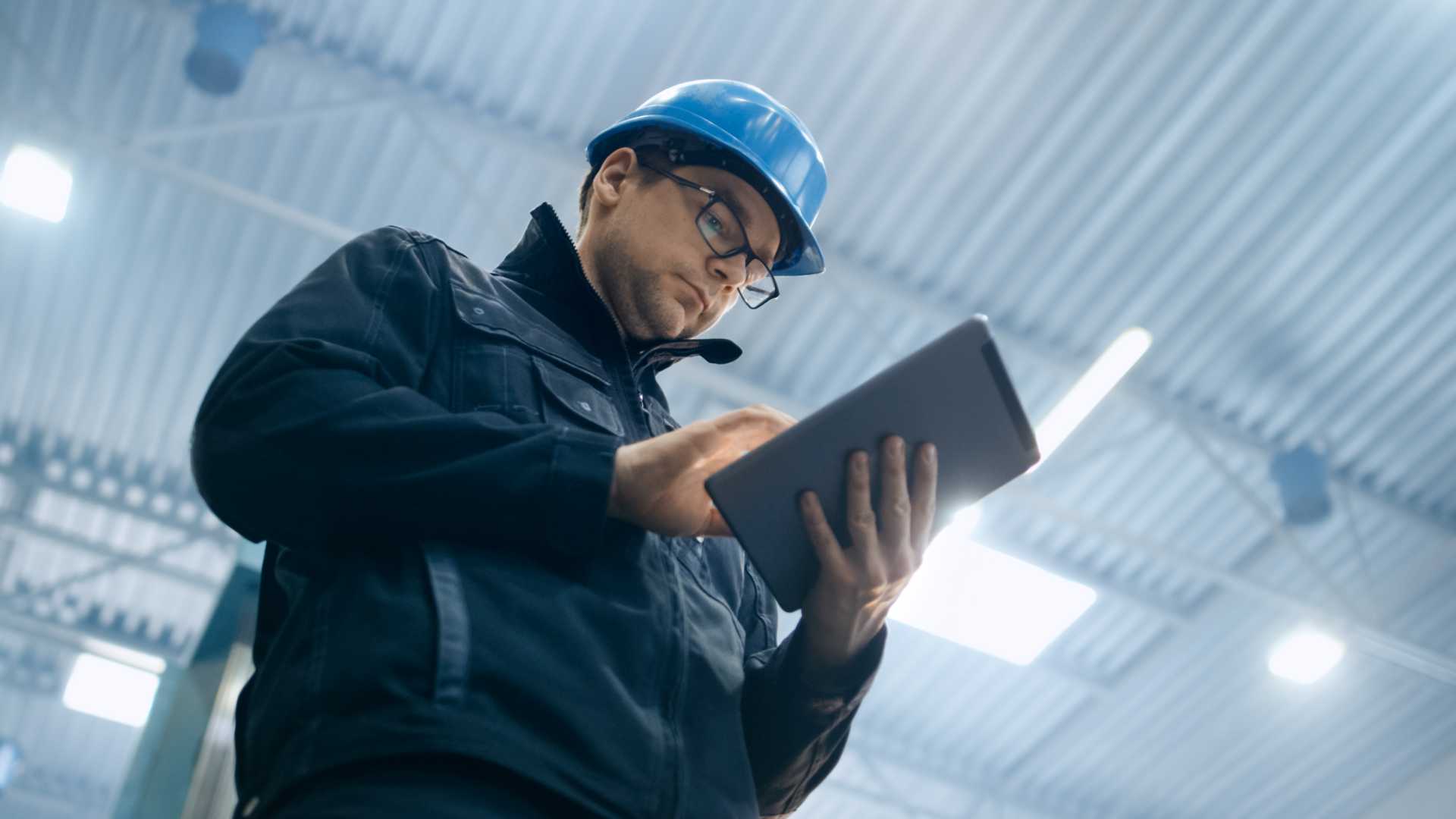
Building & Construction
What Is An NCR In Construction
Modified: January 9, 2024
Discover what an NCR is in the context of building construction and how it impacts the construction process. Gain clarity on the role and importance of NCRs in ensuring quality and compliance.
(Many of the links in this article redirect to a specific reviewed product. Your purchase of these products through affiliate links helps to generate commission for Storables.com, at no extra cost. Learn more)
Introduction
Welcome to the world of construction, where every project involves meticulous planning, precise execution, and unwavering attention to detail. In such a complex and dynamic industry, it is crucial to have effective strategies in place to ensure the smooth progress of construction projects. One such strategy is the implementation of Non-Conformance Reports (NCRs).
An NCR, or Non-Conformance Report, is a valuable tool used in the construction industry to document and address any non-conforming work or issues that arise during the construction process. It serves as a formal record of any deviations from the specified standards, specifications, or requirements outlined in the project plans and contracts.
Throughout the course of a construction project, it is not uncommon to encounter situations where the work performed does not meet the expected quality standards or deviates from the agreed-upon design. These non-conformances can range from minor issues, such as a cosmetic flaw, to major concerns, such as a structural deficiency. Regardless of the severity, it is essential to address these non-conformances in a systematic and proactive manner to ensure the successful completion of the project.
The primary purpose of using NCRs in construction is to identify, document, track, and rectify any non-conforming work or materials. By doing so, it helps maintain accountability, transparency, and control over the construction process. NCRs play a critical role in facilitating communication between various stakeholders, including the contractor, project manager, architect, and client. They serve as a formal mechanism to report and resolve non-conformances, ensuring that the project progresses according to the agreed-upon standards and specifications.
There are various types of NCRs that can be encountered in construction projects. Some common examples include:
- Material non-conformance: When the delivered materials do not meet the specified quality or standards
- Design non-conformance: When the construction work does not conform to the approved design or drawings
- Workmanship non-conformance: When the quality of work performed does not meet the expected standards
- Safety non-conformance: When there are breaches in occupational health and safety requirements
The NCR process in construction typically involves several steps. Initially, the non-conformance is identified and documented through a detailed report that includes a description of the issue, its location, and the severity. The report is then reviewed by the appropriate personnel, such as the project manager or quality control team, who assess the impact of the non-conformance and determine the necessary corrective actions. The responsible parties then implement the corrective measures and verify their effectiveness through inspections or tests. Finally, the closure of the NCR is documented, indicating that the issue has been resolved and the project can proceed.
The importance of NCRs in construction projects cannot be overstated. They play a vital role in maintaining project quality, ensuring compliance, and minimizing risks. By addressing non-conformities in a timely and systematic manner, NCRs help prevent further issues, protect the project’s integrity, and enhance client satisfaction. Moreover, NCRs provide a valuable source of data and lessons learned, aiding in process improvement and contributing to the overall success of future construction projects.
Key Takeaways:
- NCRs are essential in construction for maintaining quality, ensuring compliance, and fostering continuous improvement. They facilitate communication, accountability, and timely resolution of non-conforming issues, ultimately contributing to successful project outcomes.
- Effective NCR management requires clear procedures, training, timely identification, and communication. Root cause analysis, corrective actions, and continuous improvement are crucial for addressing challenges and ensuring quality control in construction projects.
Read more: How To Close NCR In Construction
Definition of NCR in Construction
In the construction industry, an NCR, which stands for Non-Conformance Report, is a formal document used to address and rectify any non-conforming work or materials that do not meet the specified standards, requirements, or contract agreements. Non-conformance refers to any deviation from the approved plans, drawings, specifications, or quality standards set for the construction project.
The purpose of an NCR is to document and track non-conformances throughout the construction process, regardless of their severity or impact. By creating a standardized reporting system, NCRs enable all stakeholders, including contractors, project managers, architects, and clients, to identify and address non-conforming issues in a structured and organized manner.
When a non-conforming issue is identified on a construction project, it is crucial to document it in an NCR. The report includes relevant details such as a description of the non-conformance, its location, the parties involved, and any supporting evidence or documentation. This helps ensure that all relevant information is recorded accurately and can be easily referenced and reviewed by the appropriate stakeholders.
Once an NCR is created, it initiates a formal process whereby the non-conformance is assessed, investigated, and rectified. The responsible parties, such as the contractor or subcontractor, along with the project manager and quality control team, collaborate to determine the root cause of the non-conformance and develop a plan of action to address it.
The NCR process typically involves various steps, including:
- Documentation: The non-conformance is thoroughly documented in the NCR, including its description, location, and any pertinent supporting materials.
- Review and assessment: The NCR is reviewed by the relevant personnel to evaluate the severity and impact of the non-conformance.
- Root cause analysis: The responsible parties investigate the cause of the non-conformance to identify the underlying issues or deficiencies.
- Corrective actions: A plan is developed to rectify the non-conforming work or materials, outlining the necessary steps and timelines for implementation.
- Verification and closure: The corrective actions are implemented, and inspections or tests are conducted to ensure that the non-conformance has been resolved. Once the issue is deemed resolved, the NCR is closed.
It is important to note that NCRs are not limited to identifying and addressing non-conforming work or materials only. They can also be used to flag safety violations, deviations from contractual agreements, breaches in quality standards, and any other issues that arise during the construction process and need to be addressed.
By utilizing NCRs in construction projects, stakeholders can effectively manage and resolve non-conformances, ensuring that the project progresses according to the approved plans and specifications. These reports contribute to maintaining accountability, transparency, and quality control throughout the construction process and ultimately lead to the successful completion of the project.
Purpose of NCRs in Construction
In the construction industry, Non-Conformance Reports (NCRs) serve a crucial purpose in maintaining quality standards, ensuring compliance, and minimizing risks. NCRs are a formal documentation tool used to address and rectify non-conforming work or materials that do not meet the specified requirements, standards, or contractual agreements. The primary purpose of NCRs in construction is to identify, document, track, and resolve any non-conformances encountered during the construction process.
One of the key purposes of NCRs is to provide a reliable system for documenting and reporting non-conforming issues. When a non-conformance is identified, it is crucial to have a standardized format to capture and record relevant details, including a clear description of the issue, its location, parties involved, and any supporting evidence. This documentation helps ensure that all pertinent information is properly recorded, facilitating effective communication and reference for the project team and stakeholders.
NCRs also play a vital role in maintaining accountability and transparency on construction projects. By documenting non-conforming work or materials, NCRs provide a means to attribute responsibility to the parties involved in the non-conformance. The report allows for clear identification of the responsible contractor, subcontractor, or supplier, ensuring that appropriate corrective actions are taken. This accountability fosters a culture of responsibility and quality consciousness within the construction industry.
Furthermore, NCRs facilitate effective communication and collaboration among project stakeholders. When a non-conforming issue arises, NCRs enable the project team and relevant parties, such as the contractor, project manager, architect, or client, to address the issue in a structured and organized manner. The NCR serves as a formal mechanism for reporting and resolving non-conformances, ensuring that all stakeholders are aware of the situation and can collectively work towards finding a resolution.
Another purpose of NCRs is to ensure compliance with project plans, specifications, and contract agreements. By documenting and addressing non-conforming work or materials, NCRs help to maintain the integrity of the construction project and ensure that the final result aligns with the approved design and quality standards. This proactive approach to addressing non-conformances helps prevent further deviations from the project requirements and minimizes the risk of rework, delays, or disputes.
Moreover, NCRs contribute to process improvement and lessons learned in the construction industry. By keeping a record of non-conforming issues and their resolutions, NCRs provide valuable insights into the root causes of non-conformances. This information can be analyzed and used to identify recurring issues, develop corrective actions, and implement preventive measures in future construction projects. NCRs, therefore, serve as a knowledge-sharing tool, enabling the construction industry to continuously improve its practices and quality standards.
To summarize, the purpose of NCRs in construction is to:
- Document and report non-conforming work or materials
- Maintain accountability and transparency
- Facilitate effective communication and collaboration
- Ensure compliance with project plans and specifications
- Contribute to process improvement and lessons learned
By fulfilling these purposes, NCRs play a vital role in ensuring the successful completion of construction projects with the desired quality, safety, and adherence to specifications.
Types of NCRs in Construction
In the construction industry, Non-Conformance Reports (NCRs) are used to document and address different types of non-conformances that may arise during the construction process. These non-conformances can vary in nature and severity, requiring specific attention and corrective measures. Here are some common types of NCRs encountered in construction projects:
- Material Non-Conformance: This type of NCR occurs when the materials delivered to the construction site do not meet the specified quality or standards. It can include issues such as incorrect or substandard materials, out-of-date materials, or materials that do not meet the required specifications. Material non-conformances can have significant consequences on the project’s progress and result in delays, compromised structural integrity, or poor aesthetics.
- Design Non-Conformance: Design non-conformances occur when the construction work deviates from the approved design or drawings. It can include instances where the construction does not align with the design specifications, conflicting dimensions, or incorrect placement of building elements. Design non-conformances can affect the functionality, safety, and overall quality of the project, requiring corrective actions to ensure compliance with the approved design.
- Workmanship Non-Conformance: Workmanship non-conformances arise when the quality of work performed does not meet the expected standards. This can include issues such as poor finishing, uneven surfaces, incorrect installations, or improper application of construction techniques. Workmanship non-conformances can compromise the project’s appearance and performance, necessitating remedial measures to rectify the deficiencies and ensure the project meets the desired quality standards.
- Safety Non-Conformance: Safety is of paramount importance in the construction industry, and any non-conformance related to occupational health and safety must be addressed promptly. Safety non-conformances can include instances where safety protocols are not followed, inadequate safety measures are implemented, or hazardous conditions are present on-site. These non-conformances pose a risk to the health and well-being of workers and can result in accidents or injuries if left unaddressed.
- Contractual Non-Conformance: Contractual non-conformances refer to deviations from the agreed-upon terms and conditions outlined in the construction contract. This can include issues such as non-compliance with project milestones, delivery deadlines, payment terms, or contractual obligations. Contractual non-conformances can have legal implications and require resolution through negotiation or contractual remedies to ensure compliance with the contract terms.
It is important to recognize that these types of NCRs are not mutually exclusive and can often overlap. For example, a non-conformance related to workmanship may also have implications for safety or contractual compliance. Construction projects involve multiple stakeholders, complex processes, and various quality requirements, making it essential to identify and address all types of non-conformances through comprehensive NCR management.
By categorizing and addressing these different types of NCRs, construction projects can mitigate risks, maintain quality standards, and ensure compliance with design specifications, safety regulations, and contractual obligations. Effective management of NCRs allows for timely corrective actions and continuous improvement in construction practices, leading to successful project outcomes.
NCR Process in Construction
The Non-Conformance Report (NCR) process is a structured approach used in the construction industry to address and rectify non-conforming work or materials. The NCR process ensures that deviations from approved plans, specifications, quality standards, or contractual agreements are properly documented, assessed, and resolved. Here are the key steps involved in the NCR process in construction:
- Identification: The NCR process begins with the identification of a non-conformance. This can be done through various means, such as inspections, quality control reviews, client feedback, or internal audits. When a non-conforming issue is identified, it is important to document it in an NCR to initiate the resolution process.
- Documentation: The next step is to create an NCR, which involves documenting essential details related to the non-conformance. The NCR should provide a clear description of the issue, the location where it was observed, the parties involved, any supporting evidence or documentation, and the potential impact on the project. Proper documentation ensures that all relevant information is captured accurately and can be easily referenced throughout the process.
- Review and Assessment: Once the NCR is created, it is reviewed by the appropriate personnel, such as the project manager, quality control team, or relevant stakeholders. The review process involves assessing the severity and impact of the non-conformance, including evaluating any potential risks or implications for the project. This step helps determine the priority and necessary level of action required to address the non-conformance.
- Root Cause Analysis: After the review and assessment, the responsible parties initiate a root cause analysis to identify the underlying cause of the non-conformance. This analysis involves investigating the factors and conditions that led to the non-conforming work or materials. Understanding the root cause is crucial for developing effective corrective actions that prevent similar non-conformances from occurring in the future.
- Corrective Actions: Based on the findings of the root cause analysis, a plan of action is developed to address and rectify the non-conformance. This plan outlines the specific steps and measures required to resolve the issue and bring the work or materials back into compliance with the approved standards. The corrective actions may involve rework, material substitution, additional testing, or any other appropriate measures to rectify the non-conformance.
- Verification and Closure: Once the corrective actions have been implemented, the next step is to verify their effectiveness. This can involve conducting inspections, tests, or any other necessary means to ensure that the non-conformance has been successfully resolved. Upon verification, the NCR is closed, indicating that the issue has been addressed, and the project can proceed without further non-conforming work or materials.
It is crucial to note that effective communication and collaboration among project stakeholders are essential throughout the NCR process. The responsible parties, including contractors, subcontractors, project managers, quality control personnel, and any other relevant stakeholders, need to work together to ensure the timely and proper resolution of non-conformances.
Implementing a well-defined NCR process in construction projects helps maintain accountability, transparency, and quality control. It enables the construction team to systematically address non-conformances, prevent their recurrence, and ensure compliance with the approved plans, specifications, and contractual obligations.
By following the NCR process, construction projects can effectively manage non-conformances, minimize risks, and foster a culture of continuous improvement and quality in the construction industry.
When dealing with NCRs in construction, it’s important to clearly document the issue, provide supporting evidence, and propose a corrective action to ensure timely resolution and avoid project delays.
Read more: What Is Construction
Importance of NCRs in Construction Projects
Non-Conformance Reports (NCRs) play a vital role in the successful execution of construction projects. They serve as a critical tool for maintaining quality standards, ensuring compliance with specifications, and minimizing risks. Here are some key reasons highlighting the importance of NCRs in construction:
- Quality Control: NCRs are essential for maintaining quality control in construction projects. They help identify and document non-conforming work or materials that deviate from the approved plans, specifications, or agreed-upon standards. By addressing these non-conformances promptly, NCRs ensure that the construction progresses with the desired level of quality, minimizing deficiencies, and defects.
- Accountability and Transparency: NCRs promote accountability and transparency by providing a formal mechanism to report and document non-conforming issues. They attribute responsibility to the parties involved in the non-conformance, such as contractors, subcontractors, or suppliers. This accountability ensures that the responsible parties take appropriate corrective actions, leading to improved workmanship and increased confidence in the project delivery process.
- Compliance and Risk Management: NCRs ensure compliance with approved plans, specifications, regulations, and contractual agreements. They flag any non-compliance, allowing for timely corrective actions and risk mitigation strategies. By addressing non-conformances proactively, NCRs help minimize potential risks, such as safety hazards, legal complications, project delays, and cost overruns.
- Communication and Collaboration: NCRs facilitate effective communication and collaboration among all project stakeholders. They serve as a formal tool for reporting non-conforming issues, enabling clear and concise communication between contractors, project managers, architects, and clients. NCRs ensure that non-conformances are acknowledged, documented, and resolved in a structured and collaborative manner, promoting a cooperative and efficient work environment.
- Process Improvement and Lessons Learned: NCRs contribute to process improvement and the accumulation of lessons learned in the construction industry. By documenting non-conformances and their resolutions, NCRs provide valuable insights into areas for improvement. They help identify recurring issues, root causes, and potential preventive measures. This knowledge sharing helps enhance construction practices, project delivery strategies, and overall industry standards.
- Client Satisfaction: NCRs are essential for ensuring client satisfaction in construction projects. By addressing non-conformances promptly and transparently, NCRs demonstrate a commitment to delivering quality work and meeting client expectations. Clients appreciate the transparency provided by NCRs and the proactive approach taken to resolve any issues that arise during the construction process.
Overall, the importance of NCRs in construction projects cannot be overstated. They are a fundamental tool for maintaining quality, ensuring compliance, and managing risks. By implementing an effective NCR process, construction projects can minimize non-conformances, increase accountability, and foster continuous improvement. NCRs contribute to the successful completion of projects that meet quality standards, adhere to specifications, and achieve client satisfaction.
Benefits of Implementing NCRs in Construction
Implementing Non-Conformance Reports (NCRs) in construction projects offers several significant benefits. NCRs serve as a valuable tool for maintaining quality control, ensuring compliance, and promoting continuous improvement. Here are some key benefits of implementing NCRs in construction:
- Improved Quality Management: NCRs play a crucial role in quality management by identifying and addressing non-conforming work or materials. By documenting non-conformance issues, NCRs create a systematic and structured approach to track and resolve deficiencies. This helps to maintain consistent quality standards, reduce rework, and enhance project outcomes.
- Enhanced Communication and Collaboration: NCRs facilitate effective communication and collaboration among project stakeholders. They provide a formal mechanism to report and discuss non-conforming issues, enabling open dialogue and prompt resolution. By promoting transparency and fostering a collaborative work environment, NCRs help to prevent misunderstandings, resolve conflicts, and strengthen relationships among contractors, project managers, architects, and clients.
- Identifying Root Causes: NCRs contribute to the identification of root causes for non-conforming issues. By analyzing the underlying factors that led to the non-conformance, NCRs enable project teams to address the core problems and implement effective corrective actions. Understanding the root causes helps prevent similar non-conformances in the future, leading to improved project performance and reduced risks.
- Efficient Issue Resolution: NCRs provide a systematic and documented process for addressing non-conforming issues. They outline the necessary steps and responsibilities for corrective actions, ensuring prompt resolution and preventing further impacts on the project. This efficient issue resolution minimizes delays, rework, and disruptions, ultimately saving time and resources.
- Lessons Learned and Process Improvement: NCRs serve as a valuable source of lessons learned and contribute to process improvement. By documenting non-conforming issues and their resolutions, NCRs become a repository of knowledge, enabling project teams to review and analyze trends or recurring issues. This information can be used to refine construction practices, update specifications, and implement preventive measures, leading to continuous improvement in project delivery.
- Risk Mitigation: NCRs help to identify and mitigate risks associated with non-conforming work or materials. Early detection and resolution of non-conformances prevent potential safety hazards, legal disputes, and financial losses. By addressing non-conforming issues proactively, NCRs contribute to a safer work environment, minimize project risks, and safeguard the interests of all stakeholders.
- Client Satisfaction: Implementing NCRs demonstrates a commitment to quality and client satisfaction. Clients appreciate the transparency and proactive approach to resolving non-conforming issues. Regular communication and documentation through NCRs instill confidence in the project’s progress and the contractor’s commitment to delivering a high-quality outcome, ultimately leading to enhanced client satisfaction.
In summary, implementing NCRs in construction projects offers multiple benefits. From improved quality management and efficient issue resolution to communication facilitation and risk mitigation, NCRs contribute to successful project delivery. By utilizing NCRs, construction teams can maintain quality standards, ensure compliance, foster continuous improvement, and ultimately enhance client satisfaction.
Challenges in Managing NCRs in Construction
Managing Non-Conformance Reports (NCRs) in construction projects comes with its fair share of challenges. While NCRs are an essential tool for maintaining quality and resolving non-conforming issues, several factors can complicate their effective management. Here are some common challenges encountered in managing NCRs in construction:
- Lack of Awareness and Training: One of the primary challenges in managing NCRs is a lack of awareness or understanding among project stakeholders. Insufficient knowledge about the purpose, process, and importance of NCRs can lead to inconsistent reporting, inadequate documentation, and miscommunication. Providing comprehensive training and clear guidelines on NCR management is crucial for addressing this challenge.
- Timely Identification and Documentation: Timely identification and documentation of non-conforming issues is critical for effective NCR management. However, challenges such as a lack of proper monitoring or inspection processes can hinder the early detection of non-conformances. Additionally, inadequate documentation practices can lead to incomplete or inaccurate NCR reports, impeding the resolution process.
- Communication and Coordination: Effective communication and coordination between project stakeholders are essential for managing NCRs successfully. However, challenges related to communication breakdowns, misinterpretation of information, or ineffective collaboration can delay the resolution of non-conformances. Clear communication channels and regular coordination meetings can help mitigate these challenges.
- Centralized NCR Management: Construction projects often involve multiple subcontractors and various teams, making it challenging to centralize NCR management. The decentralized nature of NCRs can lead to difficulties in tracking and consolidating issues across different subcontractors and disciplines. Implementing a centralized NCR management system or utilizing digital tools can help overcome this challenge.
- Root Cause Analysis: Conducting an effective root cause analysis is crucial for addressing the underlying issues that led to non-conformances. However, challenges may arise in determining the true root causes due to limited resources, time constraints, or complexity of the issues. Thorough investigation and analysis, involving experts if necessary, can help overcome this challenge and ensure appropriate corrective actions.
- Follow-up and Closure: Ensuring timely follow-up and closure of NCRs is vital for their effective management. Challenges can arise in tracking the progress of corrective actions, obtaining proper verification, and closing out NCRs promptly. Establishing clear timelines, assigning responsibilities, and implementing regular follow-up procedures are necessary to address this challenge.
- Resistance to Change: Implementing an effective NCR management process may face resistance from project stakeholders who are accustomed to traditional practices or reluctant to embrace new systems. Overcoming resistance to change requires effective leadership, stakeholder engagement, and a clear communication strategy highlighting the benefits of the improved NCR management approach.
Effective NCR management requires a proactive and diligent approach to overcome these challenges. By addressing these issues head-on, implementing proper training and communication mechanisms, and leveraging technology and best practices, construction projects can streamline NCR management and ensure the successful resolution of non-conformances.
Best Practices for Dealing with NCRs in Construction
Dealing with Non-Conformance Reports (NCRs) effectively is crucial for maintaining quality standards, ensuring compliance, and minimizing risks in construction projects. By implementing best practices, construction teams can streamline the management of NCRs and improve their overall project outcomes. Here are some key best practices for dealing with NCRs in construction:
- Establish Clear NCR Procedures: Develop clear and standardized procedures for the identification, documentation, review, and resolution of NCRs. This ensures consistency and uniformity in handling non-conforming issues across the project. The procedures should specify roles and responsibilities, document submission formats, and timelines for resolution.
- Promote a Culture of Quality: Foster a culture of quality consciousness throughout the construction project. Emphasize the importance of adhering to established standards and specifications. Encourage open communication and collaboration among stakeholders to address non-conformances promptly and effectively.
- Provide Training and Awareness: Train all project stakeholders on the purpose, significance, and process of NCR management. Ensure that everyone involved understands the importance of detecting, documenting, and resolving non-conformances in a timely manner. Regularly provide updates and refresher training to reinforce the knowledge and awareness of NCR procedures.
- Prompt Identification and Documentation: Implement regular inspections, quality control measures, and monitoring systems to identify non-conforming issues as early as possible. Ensure thorough and accurate documentation that includes a clear description of the non-conformance, its location, supporting evidence, and potential impacts. Document non-conformances promptly and consistently using standardized NCR forms or digital tools.
- Ensure Effective Communication: Establish clear communication channels among project stakeholders for reporting and addressing non-conforming issues. Foster open and transparent communication to prevent misunderstandings or delays in resolving NCRs. Maintain regular coordination meetings and utilize digital platforms for real-time communication and collaboration.
- Conduct Root Cause Analysis: Conduct a thorough root cause analysis to identify and address the underlying causes of non-conformances. Involve relevant experts or specialists to investigate complex issues. Use techniques such as the “5 Whys” or fishbone diagrams to trace the root causes and develop effective corrective actions that prevent similar non-conformances in the future.
- Implement Corrective Actions: Develop clear and actionable corrective action plans to rectify non-conformances. Assign responsibilities, set realistic timelines, and ensure the availability of necessary resources. Regularly monitor the progress of corrective actions and provide support or guidance as needed. Verify the effectiveness of the actions through inspections, tests, or reviews.
- Track and Follow-up: Establish a system for tracking and monitoring the status of NCRs. Regularly follow up on open NCRs to ensure prompt closure. Maintain clear records of all NCRs, including their status, resolution, and lessons learned. Utilize digital tools or project management software to automate and streamline the tracking process.
- Continuously Improve: Regularly review and analyze NCR data to identify trends, recurring issues, or potential areas for improvement. Use this information to update specifications, revise construction processes, or implement preventive measures. Encourage feedback and suggestions from project stakeholders to drive continuous improvement in NCR management and overall project quality.
By implementing these best practices, construction projects can effectively manage NCRs, maintain quality standards, and enhance project outcomes. The consistent application of these practices strengthens communication, promotes accountability, and fosters a proactive approach to addressing non-conforming issues throughout the construction process.
Read more: What Are Piles In Construction
Conclusion
Non-Conformance Reports (NCRs) play a vital role in the construction industry, ensuring the maintenance of quality standards, compliance with specifications, and the successful delivery of construction projects. NCRs provide a systematic and structured approach for addressing non-conforming work or materials, facilitating communication, collaboration, and continuous improvement among project stakeholders.
Throughout this article, we have explored the definition of NCRs, their purpose, different types encountered in construction projects, the NCR process, and the importance of NCRs. We have also discussed the benefits of implementing NCRs, as well as the challenges involved in managing them effectively. Lastly, we explored best practices for dealing with NCRs in construction.
By implementing NCRs and adhering to best practices, construction projects can ensure quality control, mitigate risks, and enhance client satisfaction. NCRs serve as a documentation tool, promoting accountability, transparency, and effective communication. They facilitate the identification and resolution of non-conformances, fostering a culture of continuous improvement and process excellence within the construction industry.
The effective management of NCRs requires clear procedures, adequate training, timely identification and documentation, effective communication, root cause analysis, and proper implementation of corrective actions. It also involves tracking and following up on NCRs, promoting a culture of quality, and continuously improving processes based on lessons learned.
In conclusion, NCRs are an integral component of construction project management. By embracing their role and implementing them effectively, construction teams can ensure adherence to quality standards, compliance with specifications, and successful project outcomes. NCRs contribute to the construction industry’s growth and development, promoting collaboration, risk management, and continuous improvement.
Frequently Asked Questions about What Is An NCR In Construction
Was this page helpful?
At Storables.com, we guarantee accurate and reliable information. Our content, validated by Expert Board Contributors, is crafted following stringent Editorial Policies. We're committed to providing you with well-researched, expert-backed insights for all your informational needs.
0 thoughts on “What Is An NCR In Construction”