Home>diy>Building & Construction>What Is Construction Quality Management
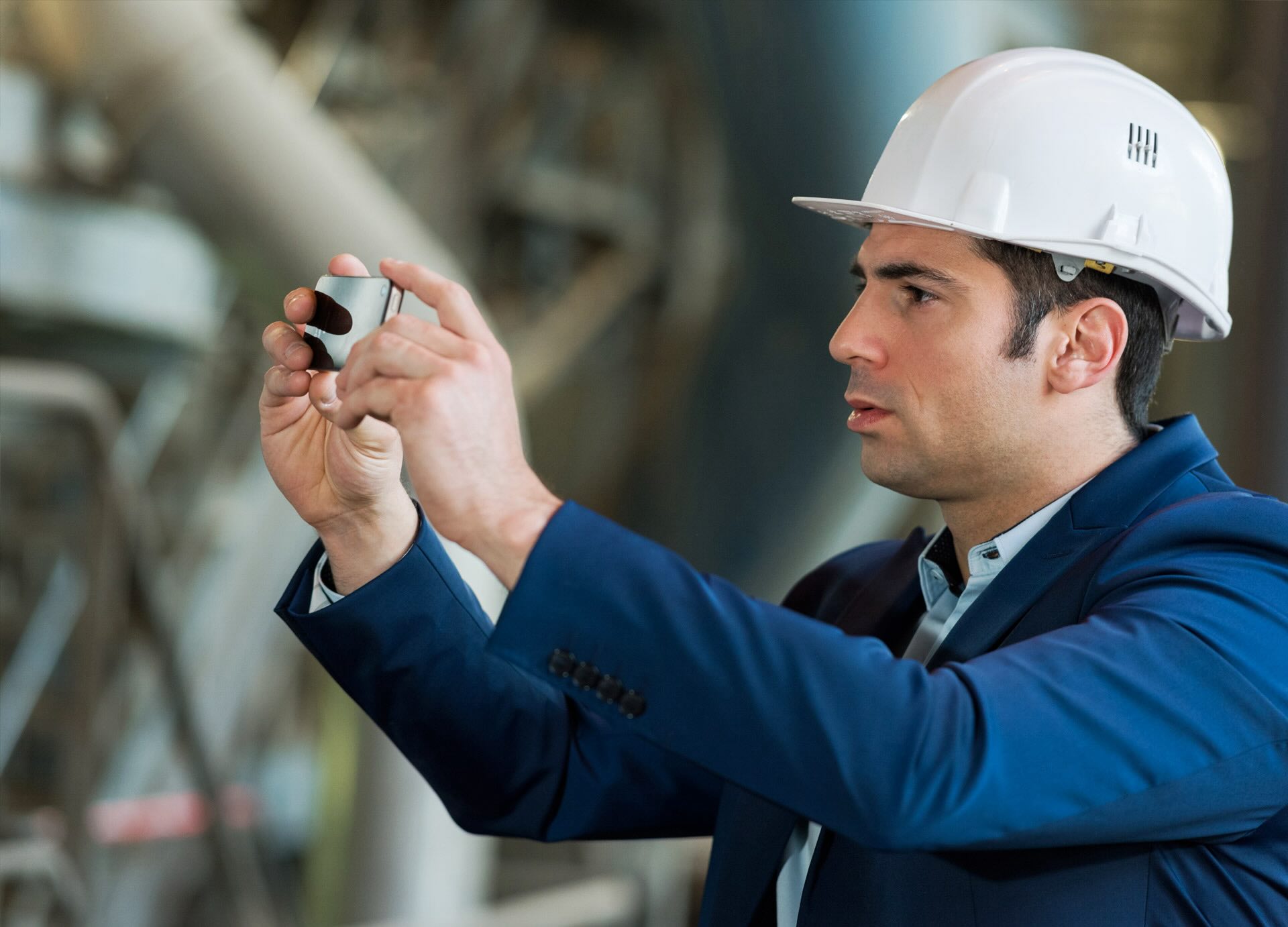
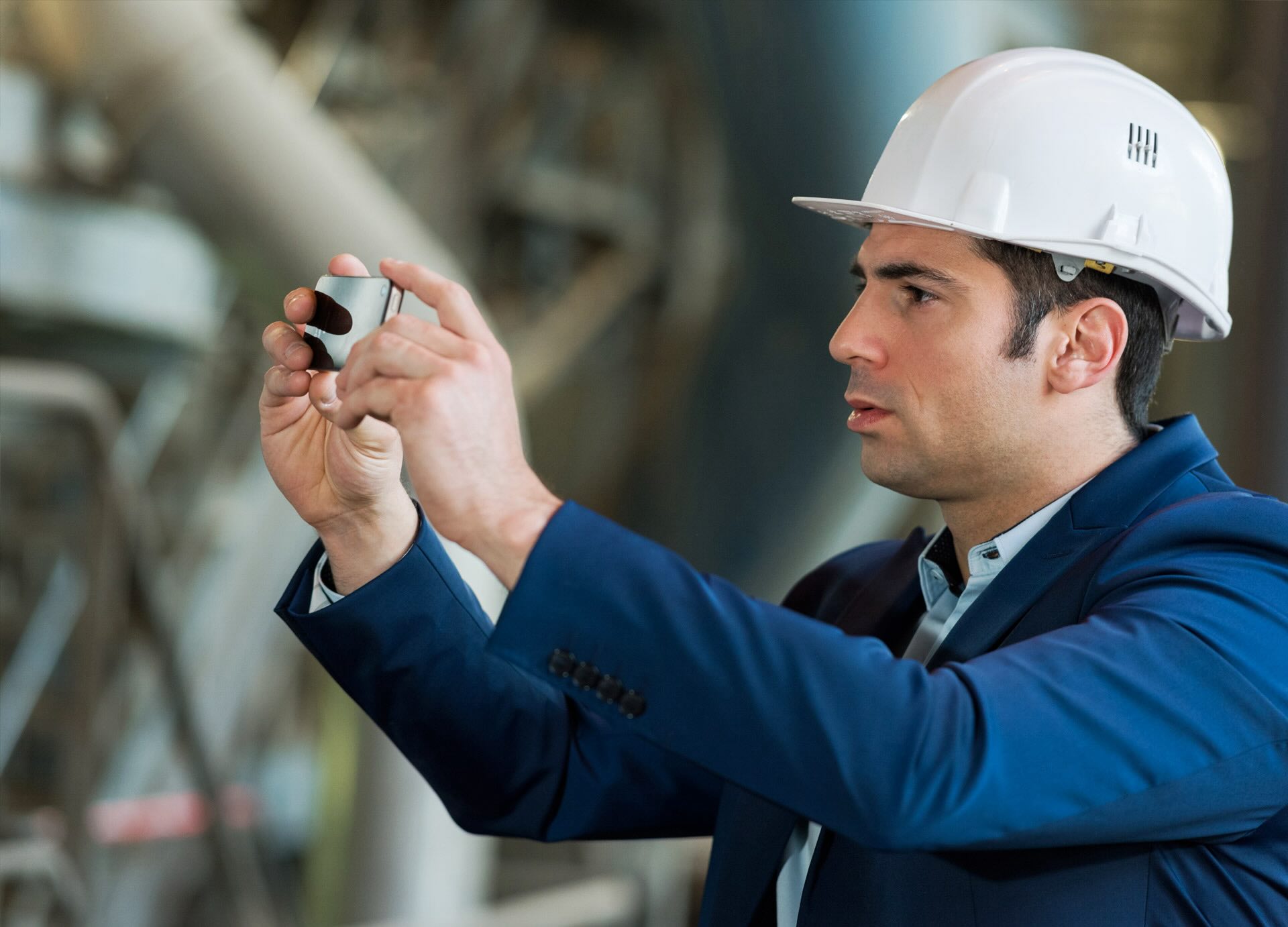
Building & Construction
What Is Construction Quality Management
Modified: January 24, 2024
Learn about construction quality management and its importance in building construction. Gain insights into the role it plays in ensuring high-quality construction projects.
(Many of the links in this article redirect to a specific reviewed product. Your purchase of these products through affiliate links helps to generate commission for Storables.com, at no extra cost. Learn more)
Introduction
Welcome to the world of construction quality management! In the realm of building construction, quality management is a crucial aspect that plays a significant role in ensuring the success of any project. Whether it’s a residential complex, commercial building, or infrastructure development, the quality of construction directly impacts its durability, safety, and overall functionality.
Construction quality management involves various processes and practices that aim to achieve excellence in the construction industry. It encompasses the planning, monitoring, and execution of activities that adhere to established standards, codes, and specifications. The ultimate goal is to deliver high-quality structures that meet or exceed client expectations while ensuring the safety and satisfaction of all stakeholders involved.
In this article, we will delve into the fundamentals of construction quality management, exploring its definition, importance, key principles, roles and responsibilities, benefits, challenges, tools and techniques, best practices, and real-world case studies. By the end, you will have a comprehensive understanding of how construction quality management is essential to the success of any building project.
So, let’s get started and uncover the world of construction quality management!
Key Takeaways:
- Construction quality management is essential for ensuring safety, durability, functionality, and customer satisfaction in building projects. It involves proactive planning, continuous monitoring, and a commitment to excellence.
- Successful implementation of construction quality management requires clear communication, robust quality control processes, advanced tools and techniques, and a culture of continuous improvement. Real-world case studies demonstrate the impact of quality management on iconic construction projects.
Read more: What Is The Scope Of Construction Management
Definition of Construction Quality Management
Construction quality management can be defined as a systematic approach to ensure that construction projects are completed to meet or exceed the specified quality standards. It involves the implementation of processes and procedures that focus on every aspect of a construction project, from the planning and design stages to the execution and handover phases.
The primary objective of construction quality management is to minimize defects, errors, and failures during the construction process. It involves the identification, prevention, and correction of any potential quality issues that may arise, with the aim of delivering a final product that meets the client’s requirements and expectations.
Construction quality management encompasses a wide range of activities, including quality planning, quality control, and quality assurance. Quality planning involves the development of strategies and procedures for achieving the desired level of quality, while quality control focuses on real-time monitoring and inspection of construction activities to identify and rectify any deviations from the quality standards. Quality assurance, on the other hand, involves the establishment of systems and processes to ensure that the project is being executed according to the planned quality requirements.
It is important to note that construction quality management is not limited to the physical aspects of construction. It also includes considerations for other critical factors such as safety, environmental impact, and regulatory compliance. A comprehensive approach to quality management takes into account all these factors to ensure the overall success of the project.
In summary, construction quality management is a multifaceted process that involves careful planning, proactive monitoring, and meticulous execution to deliver construction projects that meet the highest standards of quality and client satisfaction.
Importance of Construction Quality Management
Construction quality management is of paramount importance in the building industry. It has a direct impact on the success and longevity of construction projects. Let’s explore some key reasons why construction quality management is so crucial:
- Ensuring Safety: One of the primary reasons for implementing construction quality management is to ensure the safety of all individuals who interact with the construction site. By following established quality standards and guidelines, potential hazards and risks can be identified and mitigated, reducing the chances of accidents and injuries.
- Enhancing Durability: High-quality construction practices help to ensure the durability and longevity of the structure. By using quality materials, following proper construction techniques, and adhering to standards and regulations, the building can withstand the tests of time, weather, and daily usage.
- Maintaining Functionality: Construction quality management ensures that the building functions as intended. By focusing on quality during the design and execution phases, potential issues that may impact the performance and functionality of the building can be identified and resolved, resulting in a structure that meets the needs and expectations of the end-users.
- Enhancing Customer Satisfaction: Quality construction leads to happy clients. By delivering projects that meet or exceed the client’s requirements, expectations, and standards, construction quality management contributes to customer satisfaction. Satisfied customers are more likely to provide positive feedback, recommend your services, and engage in future projects.
- Reducing Rework and Costs: Implementing construction quality management processes minimizes the need for rework and repair. By identifying and addressing quality issues early on, the chances of costly rework and delays are significantly reduced, saving both time and money for all parties involved.
- Ensuring Compliance: Construction projects need to comply with various building codes, regulations, and legal requirements. Construction quality management ensures that these requirements are met, minimizing the risk of legal disputes, penalties, and delays due to non-compliance.
Overall, construction quality management is crucial for achieving project success, maintaining safety, durability, and functionality, ensuring customer satisfaction, and minimizing costs. By prioritizing quality throughout all stages of construction, stakeholders can mitigate risks, maximize value, and deliver exceptional projects that stand the test of time.
Key Principles of Construction Quality Management
Construction quality management is guided by several key principles that serve as the foundation for ensuring the successful implementation of quality practices throughout a project. Let’s explore these principles:
- Clear Communication: Effective communication is essential in construction quality management. It involves clear and concise exchange of information between all stakeholders, including clients, designers, contractors, and subcontractors. Transparent communication ensures that everyone is on the same page regarding quality requirements, expectations, and project updates.
- Proactive Planning: A strong emphasis on proactive planning is essential to achieve quality in construction projects. This includes comprehensive pre-construction planning, which involves defining quality objectives, preparing detailed project specifications, and establishing quality control and assurance processes. Effective planning allows for the anticipation and prevention of potential quality issues.
- Risk Management: Construction quality management involves identifying and mitigating risks that could impact the quality of the project. Risk assessment should be conducted at various stages, from design and materials selection to construction and commissioning. By proactively addressing potential risks, such as design errors or inadequate workmanship, the quality of the end product can be safeguarded.
- Continuous Monitoring: Regular monitoring is critical to ensure that construction activities align with established quality standards and requirements. This involves conducting inspections, tests, and audits at different stages of the project to identify any deviations and take corrective actions promptly. Continuous monitoring helps to catch and rectify quality issues before they become major problems.
- Quality Training and Competency: Construction quality management relies on the skills and knowledge of the individuals involved. Providing adequate training and ensuring that the workforce possesses the necessary competencies is essential. This includes training on quality control measures, proper construction techniques, and adherence to regulatory and industry standards.
- Supplier and Subcontractor Management: Collaboration with suppliers and subcontractors is a crucial aspect of construction quality management. Selecting reliable and qualified suppliers, and maintaining effective communication with subcontractors ensures that the materials and workmanship meet the required quality criteria. Regular evaluation of supplier and subcontractor performance helps to foster a culture of quality throughout the supply chain.
- Continuous Improvement: The pursuit of continuous improvement is a fundamental principle of construction quality management. Regularly reviewing project performance, seeking feedback from stakeholders, and identifying opportunities for enhancement contribute to the ongoing improvement of quality practices and processes. This allows for the refinement of techniques and the implementation of lessons learned in future projects.
By adhering to these key principles, construction quality management can effectively steer projects towards successful outcomes, ensuring adherence to quality standards, minimizing risks, and promoting a culture of excellence within the construction industry.
Roles and Responsibilities in Construction Quality Management
In construction quality management, various stakeholders have specific roles and responsibilities to ensure the successful implementation and management of quality practices. Let’s take a closer look at the key roles and their associated responsibilities:
- Client: The client is the party commissioning the construction project. Their role in quality management includes clearly communicating their quality requirements and expectations to the project team. They are responsible for providing necessary information and approvals, as well as reviewing and approving project documentation and deliverables.
- Project Manager: The project manager oversees the overall execution of the project. They play a crucial role in quality management by ensuring that quality objectives and project specifications are clearly defined and communicated. The project manager is responsible for establishing and implementing quality control and assurance processes, coordinating inspections and audits, and monitoring the project’s progress against quality targets.
- Designers: Designers are responsible for developing the architectural and engineering drawings and specifications for the project. They play a critical role in quality management by ensuring that the designs meet the required standards, codes, and regulations. Designers should coordinate with other stakeholders to ensure that the design intent is followed during the construction phase.
- Contractor: The contractor, or construction company, is responsible for executing the construction work as per the project specifications and quality standards. They are accountable for implementing quality control measures, coordinating with subcontractors and suppliers, and ensuring that construction activities adhere to the approved plans and designs.
- Suppliers and Subcontractors: Suppliers provide materials, equipment, and components required for the construction project. They are responsible for delivering high-quality products that meet the specified standards and requirements. Subcontractors, on the other hand, are responsible for specific parts of the construction work. They must maintain quality workmanship and adhere to the project’s quality control measures.
- Quality Manager: The quality manager is responsible for overseeing the implementation of quality management processes. They ensure that quality policies and procedures are developed, communicated, and implemented effectively. The quality manager conducts regular inspections, audits, and tests to identify and rectify quality issues. They also provide recommendations for continuous improvement.
- Inspectors and Quality Control Team: Inspectors and the quality control team play a crucial role in monitoring and controlling the quality of construction activities. They conduct regular inspections, checks, and tests to ensure that workmanship and materials meet the required standards. They are responsible for identifying any non-conformance and raising the appropriate corrective actions to address the issues.
- Quality Assurance Team: The quality assurance team is responsible for establishing and managing the systems and processes that ensure the project is being executed according to the planned quality requirements. They develop quality plans, perform risk assessments, and ensure compliance with regulatory requirements. The quality assurance team also conducts internal audits to evaluate and improve quality performance.
Effective collaboration and clear communication among these stakeholders contribute to the successful implementation of construction quality management. Each role has specific responsibilities that, when carried out effectively, ensure that quality objectives are met, risks are mitigated, and the project progresses towards a successful outcome.
Benefits of Implementing Construction Quality Management
Implementing construction quality management brings a wide array of benefits to all stakeholders involved in a project. Let’s explore some of the key advantages:
- Improved Project Success: Construction quality management enhances the overall success of a project. By implementing quality control measures, projects are completed with minimal defects and issues, leading to higher client satisfaction and project outcomes that align with the desired quality standards.
- Enhanced Safety: Prioritizing quality in construction directly contributes to improved safety on the construction site. By identifying and addressing potential hazards and risks, construction quality management ensures that safety protocols are followed, reducing the likelihood of accidents and injuries.
- Reduced Rework and Delays: Quality management processes help identify and rectify quality issues early on, reducing the need for rework and avoiding delays in project timelines. By adhering to quality standards and continuous monitoring, potential errors and deviations are identified and corrected promptly, saving time and avoiding costly delays.
- Increased Cost Savings: Implementing construction quality management can lead to cost savings in the long run. By minimizing rework, reducing the likelihood of costly repairs, and optimizing project efficiency, unnecessary expenses are avoided. Additionally, improved quality reduces the risk of claims and disputes, further protecting the project’s financial viability.
- Enhanced Reputation: Quality management is closely tied to the reputation of construction companies. By consistently delivering high-quality projects, companies establish a reputation for excellence and reliability. A positive reputation attracts new clients, increases client retention, and leads to higher business opportunities.
- Improved Risk Management: Construction quality management involves proactive risk identification and mitigation. By addressing quality-related risks early on, such as design errors or substandard materials, the overall project risk is reduced. Managing risks effectively helps to ensure project success and prevent costly issues down the line.
- Higher Customer Satisfaction: Prioritizing quality leads to improved customer satisfaction. Delivering projects that meet or exceed client expectations, in terms of quality, functionality, and durability, enhances client satisfaction and fosters long-term relationships. Satisfied clients often result in positive recommendations and future business opportunities.
- Compliance with Regulations: Construction quality management ensures compliance with building codes, regulations, and legal requirements. By adhering to these standards, companies avoid penalties, regulatory disputes, and project delays caused by non-compliance.
In summary, implementing construction quality management offers numerous benefits, including improved project success, enhanced safety, reduced rework and delays, increased cost savings, an enhanced reputation, improved risk management, higher customer satisfaction, and compliance with regulations. By investing in quality practices and processes, stakeholders can achieve better project outcomes, mitigate risks, and build a strong foundation for success in the construction industry.
Regularly inspect and monitor construction activities to ensure compliance with quality standards and specifications. This will help identify and address any issues early on, preventing costly rework and ensuring a high-quality end result.Challenges in Implementing Construction Quality Management
Implementing construction quality management practices comes with its fair share of challenges. Let’s explore some of the key obstacles that organizations may encounter:
- Resistance to Change: Introducing quality management practices can face resistance from employees and stakeholders who are accustomed to existing processes. Overcoming resistance to change requires effective communication, training, and demonstrating the benefits of quality management.
- Complex Project Dynamics: Construction projects often involve multiple stakeholders, complex supply chains, and changing site conditions. Managing quality in such dynamic environments can be challenging, as coordinating activities, ensuring consistency, and maintaining quality standards across all project elements requires effective project management and collaboration.
- Substandard Suppliers and Subcontractors: Reliance on external suppliers and subcontractors can pose challenges in maintaining consistent quality. Ensuring that suppliers and subcontractors meet the required standards, monitoring their performance, and managing the quality of materials and workmanship they provide is crucial in construction quality management.
- Limited Resources: Insufficient resources, including human resources, finances, and time, can hinder the effective implementation of construction quality management. This includes allocating adequate personnel for quality control and assurance activities, providing training, and investing in appropriate quality management tools and technologies.
- Fragmented Communication: Communication breakdowns among project participants can lead to misunderstandings, errors, and compromised quality. Effective communication between stakeholders, including clients, designers, contractors, and subcontractors, is essential in ensuring that quality expectations are clear, and information is shared accurately and in a timely manner.
- Compliance with Regulations: Meeting legal and regulatory requirements can pose challenges in construction quality management. This includes keeping up with constantly evolving regulations, navigating complex permit processes, and ensuring compliance with building codes and industry standards.
- Operational Constraints: Construction projects often face operational constraints, such as tight schedules, limited access to resources, and site-specific challenges. These constraints can impact quality management efforts by limiting the time and resources available for dedicated quality activities.
- Monitoring and Documentation: Continuous monitoring and proper documentation of quality-related activities are essential in construction quality management. However, challenges may arise in terms of resource availability, data management, and ensuring that accurate records are maintained throughout the project lifecycle.
Overcoming these challenges requires a proactive approach, effective planning, and a commitment to continuous improvement. By addressing these obstacles head-on, organizations can successfully implement construction quality management practices and reap the benefits of improved project outcomes and client satisfaction.
Tools and Techniques for Construction Quality Management
Implementing construction quality management requires the use of various tools and techniques to ensure that quality standards are met and maintained throughout the project. Let’s explore some of the key tools and techniques:
- Quality Planning: Quality planning involves the development of a comprehensive strategy to define quality objectives, establish quality control measures, and determine the necessary resources for quality management. This process includes identifying quality requirements, setting performance standards, and creating a quality assurance plan.
- Inspections and Audits: Inspections and audits are essential tools for monitoring and evaluating quality performance. Regular inspections are conducted to assess the compliance of construction activities with established standards and specifications. Audits, on the other hand, provide an in-depth review of quality management processes and identify areas for improvement.
- Quality Control Tools: Various quality control tools can be employed, such as checklists, flowcharts, control charts, and statistical analysis techniques. These tools help to identify non-conformities, track quality metrics, and analyze data to identify trends and patterns that may impact the quality of the project.
- Testing and Sampling: Testing and sampling techniques are utilized to assess the quality of materials and workmanship. This includes conducting laboratory tests on materials and components to ensure they meet specified standards. Random sampling of construction activities is carried out to verify compliance with quality requirements and identify any deviations.
- Quality Management Systems: Quality management systems (QMS) provide a structured approach to managing quality throughout the project. These systems consist of documented processes and procedures that guide quality management activities, including document control, change management, corrective actions, and continuous improvement.
- Training and Education: Building a competent workforce is crucial for effective quality management. Training and education programs provide employees with the necessary knowledge and skills to understand and implement quality practices. This includes training on quality control techniques, safety procedures, and compliance with regulations.
- Software and Technology: Construction quality management can be supported by various software and technology solutions. These tools help in managing documentation, tracking quality performance, analyzing data, and facilitating communication among project stakeholders. Examples include project management software, document management systems, and cloud-based collaboration platforms.
- Continuous Improvement: A fundamental aspect of quality management is a commitment to continuous improvement. Tools and techniques such as root cause analysis, lessons learned sessions, and feedback mechanisms are valuable for identifying areas of improvement and implementing necessary corrective actions.
By utilizing these tools and techniques, organizations can effectively manage and monitor quality performance, identify areas for improvement, and ensure that projects are completed to meet or exceed the specified quality standards. Implementing the appropriate tools and techniques in construction quality management contributes to the overall success of the project and the satisfaction of all stakeholders involved.
Best Practices in Construction Quality Management
Implementing best practices in construction quality management helps ensure that projects are executed with excellence and meet the highest standards of quality. Here are some key best practices to consider:
- Engage Stakeholders: Effective stakeholder engagement is crucial for successful quality management. Involve all stakeholders, including clients, designers, contractors, and subcontractors, in the quality planning and decision-making processes. Foster open communication and collaboration to align everyone’s understanding of quality requirements and expectations.
- Establish Clear Quality Objectives: Clearly define quality objectives and performance targets for the project. Set measurable and achievable goals that align with client expectations, regulatory requirements, and industry standards. Communicate these objectives to all project stakeholders and continuously monitor progress towards their attainment.
- Develop Robust Quality Control Processes: Implement comprehensive quality control processes to ensure that construction activities adhere to established standards and specifications. Conduct regular inspections and quality checks at various stages of the project to identify any deviations and take corrective actions promptly.
- Implement Quality Assurance Measures: Establish quality assurance measures to proactively ensure that the project is being executed according to the planned quality requirements. Develop quality control plans, perform audits, and implement feedback loops to continuously improve quality performance and minimize the risk of non-compliance.
- Invest in Training and Development: Provide adequate training and development programs to enhance the skills and knowledge of the project team. Offer training on quality control techniques, safety protocols, regulatory compliance, and the use of quality management tools. This empowers the workforce to effectively implement and sustain quality practices throughout the project.
- Promote a Culture of Quality: Foster a culture of quality within the organization and project team. Encourage a mindset that prioritizes quality in all actions and decisions. Recognize and reward individuals and teams for their commitment to quality, and promote continuous improvement by capturing and sharing lessons learned from each project.
- Implement Document Control: Establish robust document control processes to manage project documentation. Ensure that relevant quality documents, including specifications, drawings, and inspection reports, are properly controlled, updated, and accessible to the project team. This helps in maintaining consistency and preventing the use of outdated or incorrect information.
- Monitor and Analyze Quality Metrics: Regularly monitor and analyze quality metrics to measure performance and identify areas for improvement. Track key quality indicators, such as rework rates, defect rates, and client satisfaction scores. Use this data to identify trends, implement corrective actions, and drive continuous improvement initiatives.
- Engage in Continuous Learning: Stay updated with the latest industry trends, technological advancements, and regulatory changes related to construction quality. Engage in professional development opportunities, attend seminars and workshops, and participate in industry associations to bolster knowledge and stay ahead in the field of construction quality management.
- Encourage Supplier Collaboration: Collaborate closely with suppliers and subcontractors to ensure that they understand and adhere to quality requirements. Establish clear communication channels, conduct periodic supplier evaluations, and foster a collaborative relationship that promotes mutual understanding and commitment to delivering high-quality materials and workmanship.
By implementing these best practices, organizations can establish a strong foundation for construction quality management, ensure project success, and deliver exceptional results that meet or exceed client expectations. Continuous improvement and a dedication to excellence are key to sustaining these practices and driving continuous enhancement in quality management processes.
Read more: What Is Facility Management In Construction
Case Studies of Successful Construction Quality Management Implementation
Real-world case studies showcase the successful implementation of construction quality management practices and their impact on project outcomes. Here are a few notable examples:
- Case Study 1: The Burj Khalifa, Dubai: The construction of the iconic Burj Khalifa, the tallest building in the world, exemplifies the successful implementation of construction quality management. Rigorous quality control measures were in place throughout the project, including stringent material testing, robotics-assisted precision construction, and advanced monitoring systems. These practices ensured the highest quality in design, engineering, and construction, resulting in a safe, durable, and visually stunning structure.
- Case Study 2: California High-Speed Rail, USA: The California High-Speed Rail project showcased successful quality management practices in a large-scale infrastructure development. The project management team implemented a comprehensive quality control plan that involved regular inspections, extensive material testing, and robust communication among stakeholders. By ensuring compliance with stringent construction standards and using advanced quality assurance techniques, they achieved high levels of quality and safety in the construction of the rail system.
- Case Study 3: Sydney Opera House, Australia: The construction of the Sydney Opera House is a classic example of maintaining quality amidst complex design and engineering challenges. The project team embraced a culture of excellence, with frequent design reviews, precise material selection, and extensive quality inspections. The focus on quality control and attention to detail resulted in the creation of an architectural masterpiece that has stood the test of time and garnered international acclaim.
- Case Study 4: Tokyo Skytree, Japan: The Tokyo Skytree, the tallest tower in Japan, exemplifies effective construction quality management. Meticulous planning, rigorous material testing, and continuous monitoring were key elements of the quality management process. The project team employed advanced technologies and sophisticated quality control techniques to ensure the structural integrity, safety, and aesthetic perfection of the tower, contributing to its iconic status as a symbol of modern construction excellence.
- Case Study 5: Marina Bay Sands, Singapore: The construction of Marina Bay Sands, an integrated resort complex in Singapore, placed significant emphasis on quality management. The project team implemented robust quality control processes, including detailed documentation, regular inspections, and performance evaluations of subcontractors. Through systematic quality planning, continuous monitoring, and proactive issue resolution, they achieved exceptional quality in both the architectural and engineering aspects of the project, resulting in a world-class destination.
These case studies demonstrate that successful construction quality management requires a commitment to excellence, a proactive approach to addressing quality challenges, and the implementation of robust quality control and assurance processes. By incorporating best practices and leveraging advanced technologies, these projects achieved outstanding quality standards, resulting in iconic structures that have become benchmarks in the construction industry.
Conclusion
Construction quality management is a crucial aspect of every building project. It ensures that projects are executed to meet or exceed the specified quality standards, resulting in safe, durable, and high-performing structures. Throughout this article, we explored the definition of construction quality management, its importance, key principles, roles and responsibilities, benefits, challenges, tools and techniques, and best practices.
Construction quality management encompasses various processes and practices that focus on planning, monitoring, and maintaining the quality of construction projects. It involves the engagement of stakeholders, clear communication, proactive planning, risk management, continuous monitoring, and a commitment to continuous improvement.
By implementing construction quality management practices, organizations can reap numerous benefits. These include improved project success, enhanced safety, reduced rework and delays, increased cost savings, an enhanced reputation, improved risk management, higher customer satisfaction, and compliance with regulations.
However, implementing construction quality management does come with its fair share of challenges. These challenges include resistance to change, complex project dynamics, substandard suppliers and subcontractors, limited resources, fragmented communication, compliance with regulations, operational constraints, and monitoring and documentation.
To overcome these challenges, organizations should leverage various tools and techniques, such as quality planning, inspections and audits, quality control tools, testing and sampling, quality management systems, training and education, software and technology, and continuous improvement practices. By adopting these practices, organizations can effectively manage and monitor the quality of construction projects.
Real-world case studies illustrate the successful application of construction quality management principles. Projects such as the Burj Khalifa, California High-Speed Rail, Sydney Opera House, Tokyo Skytree, and Marina Bay Sands demonstrate how the implementation of quality management practices leads to exceptional project outcomes, iconic structures, and international acclaim.
In conclusion, construction quality management plays a vital role in the success of building projects. By embracing the principles, best practices, and tools discussed in this article, stakeholders can ensure that their projects are executed with excellence, meet the highest quality standards, and achieve long-term success in the dynamic and demanding construction industry.
Frequently Asked Questions about What Is Construction Quality Management
Was this page helpful?
At Storables.com, we guarantee accurate and reliable information. Our content, validated by Expert Board Contributors, is crafted following stringent Editorial Policies. We're committed to providing you with well-researched, expert-backed insights for all your informational needs.
0 thoughts on “What Is Construction Quality Management”