Home>diy>Building & Construction>What Is KPI In Construction
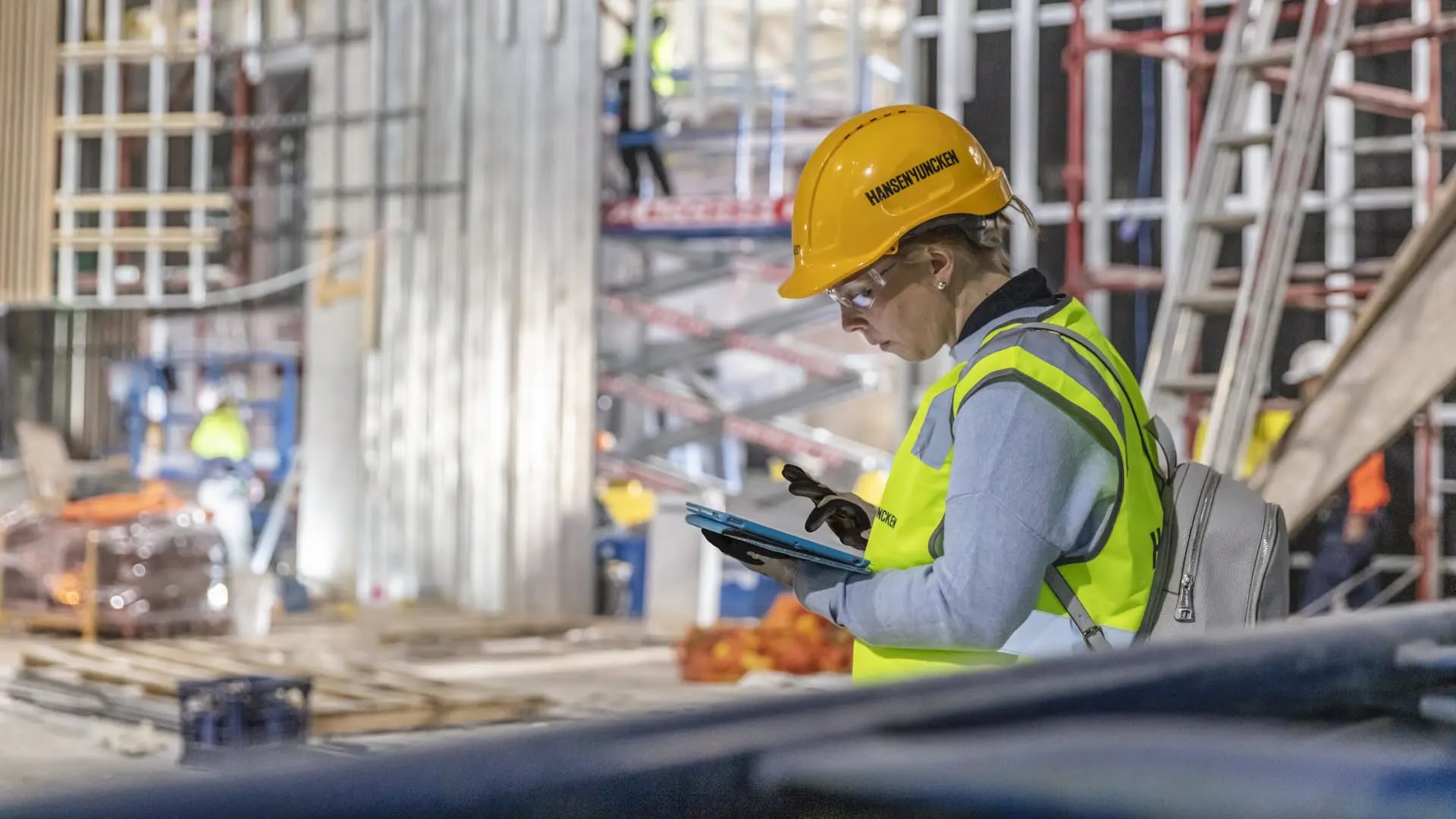
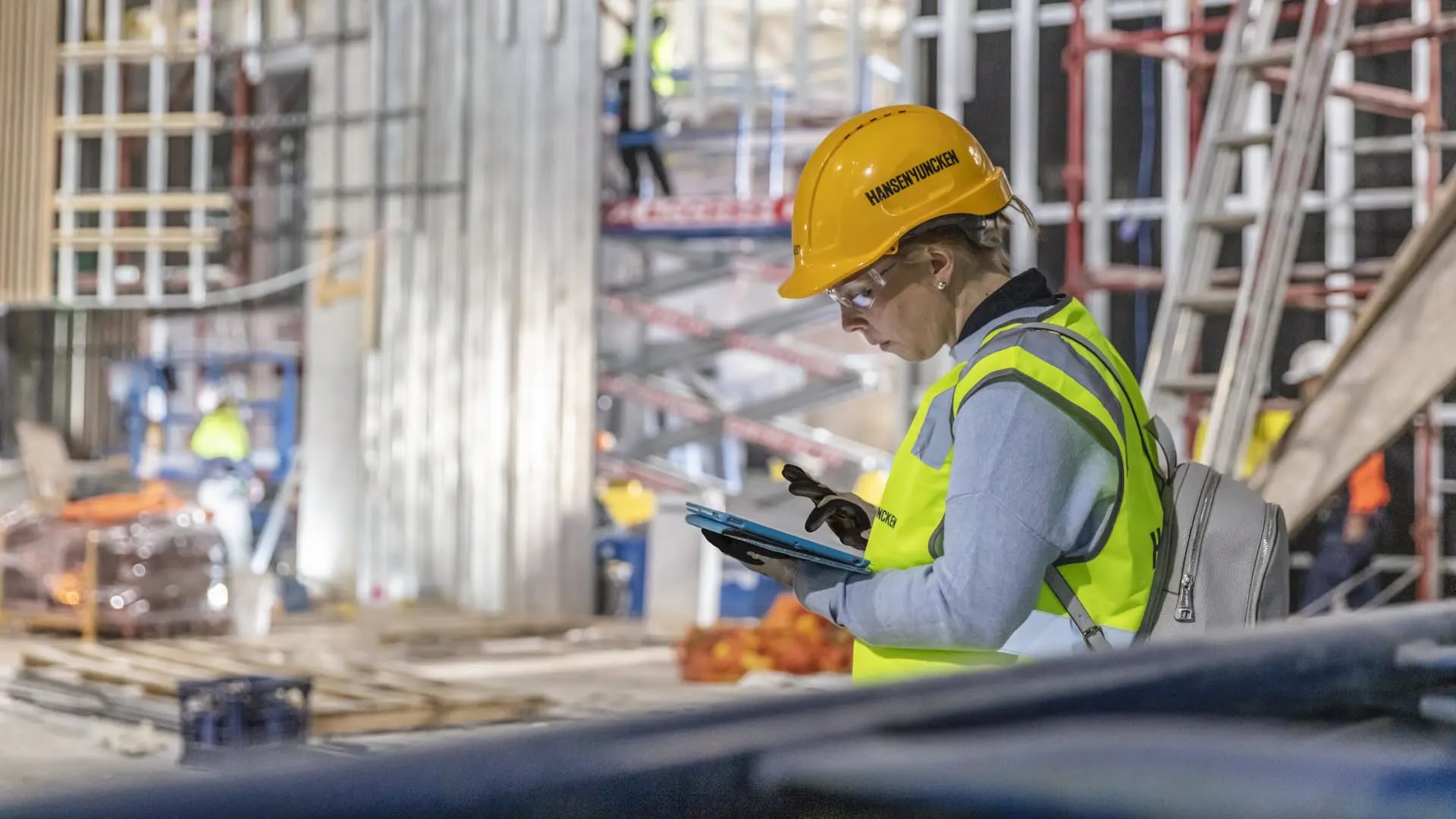
Building & Construction
What Is KPI In Construction
Modified: September 1, 2024
Learn about Key Performance Indicators (KPIs) in the context of building construction. Understand how these metrics can measure and track performance in the construction industry.
(Many of the links in this article redirect to a specific reviewed product. Your purchase of these products through affiliate links helps to generate commission for Storables.com, at no extra cost. Learn more)
Introduction
Welcome to the world of construction, where complex projects are brought to life, skyscrapers touch the sky, and infrastructure connects nations. The construction industry is a dynamic and challenging field that requires meticulous planning, precise execution, and effective management. In this fast-paced environment, it is crucial for construction companies to have a clear understanding of their performance and progress. This is where Key Performance Indicators (KPIs) come into play.
KPIs are essential tools that help businesses measure, evaluate, and track their performance against set goals and objectives. They provide valuable insights into various aspects of a construction project, such as cost, productivity, quality, safety, and schedule adherence. By monitoring and analyzing these key metrics, construction companies can identify areas for improvement, make informed decisions, and drive operational excellence.
The importance of KPIs in the construction industry cannot be understated. With the growing complexity of projects, tight budgets, and strict timelines, KPIs enable companies to stay on track and ensure project success. Whether it’s a small residential construction project or a large-scale infrastructure development, having the right KPIs in place acts as a compass, guiding the company towards its goals.
However, implementing and effectively using KPIs in construction comes with its own set of challenges. The unique nature of construction projects, with their diverse stakeholders, ever-changing conditions, and unforeseen obstacles, poses challenges in defining and measuring relevant KPIs. Additionally, the availability and reliability of data, as well as the integration of different systems and processes, can hinder the successful implementation of KPIs.
Despite these challenges, the benefits of using KPIs in construction outweigh the difficulties. By establishing clear, measurable goals and aligning them with the company’s strategic objectives, construction companies can monitor their performance to ensure they are on track to achieve success. KPIs also facilitate communication and collaboration among project teams, enabling them to work towards common goals and address issues proactively.
In this article, we will explore the key KPIs in the construction industry, the benefits of using them, and best practices for implementing and utilizing KPIs effectively. We will also examine real-life examples of successful KPI implementation in construction, showcasing how companies have leveraged these metrics to drive performance and achieve project success.
Key Takeaways:
- KPIs are essential in construction for measuring performance, aligning goals, and driving data-driven decision-making. They enable companies to improve safety, sustainability, productivity, cost management, and project progress, leading to enhanced project success.
- Successful KPI implementation in construction, as demonstrated by industry leaders, showcases the power of KPIs in driving performance improvement and achieving project success. By following best practices, construction companies can leverage KPIs to optimize resources, mitigate risks, and deliver projects with excellence.
Read more: What Is Construction
Definition of KPI
In order to understand the role of Key Performance Indicators (KPIs) in the construction industry, it is essential to first define what exactly a KPI is.
A Key Performance Indicator is a measurable value that demonstrates how effectively a company is achieving its key objectives and targets. It serves as a performance measurement tool that provides valuable insights into the success or failure of a particular process, project, or overall business performance.
KPIs are typically derived from the company’s goals and objectives, and they help in monitoring progress towards these targets. They provide a clear and objective way to evaluate and communicate performance, enabling companies to make informed decisions and take necessary actions to drive improvement.
When it comes to the construction industry, KPIs play a vital role in measuring various aspects of project performance. They can be used to assess factors such as productivity, cost efficiency, quality, safety, schedule adherence, customer satisfaction, and sustainability.
For instance, in construction, KPIs related to productivity can include metrics such as the number of completed tasks, the amount of work accomplished within a specific time frame, or the efficiency of labor utilization. KPIs related to cost efficiency can include metrics such as budget variance, cost per square meter, or cost per project phase.
It is important to note that KPIs should be specific, measurable, attainable, relevant, and time-bound (SMART). This means that they should be clearly defined, quantifiable, achievable, aligned with the company’s goals, and have a predetermined timeframe for evaluation.
Furthermore, KPIs should not be seen in isolation but rather as part of a holistic performance management system. They work in conjunction with other performance metrics and indicators to provide a comprehensive view of project or business performance.
In summary, KPIs in construction serve as performance measurement tools that help companies evaluate their progress towards achieving goals and objectives. They provide valuable insights into various aspects of project performance and enable companies to monitor, analyze, and improve their performance to drive success.
Importance of KPI in Construction
The construction industry is highly complex and involves numerous interconnected processes, stakeholders, and variables. In such a dynamic environment, having Key Performance Indicators (KPIs) in place is of utmost importance. Let’s explore why KPIs are crucial in the construction industry:
1. Performance Measurement: KPIs provide a framework for measuring and evaluating the performance of construction projects. They enable companies to assess their progress, identify areas of improvement, and make informed decisions based on quantitative data. By having clear performance metrics in place, construction companies can objectively evaluate their performance against set goals and objectives.
2. Goal Alignment: KPIs ensure that every aspect of a construction project is aligned with the company’s strategic goals. By defining and monitoring relevant KPIs, companies can ensure that their efforts are directed towards achieving the desired outcomes. KPIs act as a compass, guiding the project teams towards common objectives and facilitating collaboration.
3. Data-Driven Decision Making: KPIs provide construction companies with data and insights that enable them to make data-driven decisions. By analyzing KPI metrics, companies can identify trends, patterns, and potential issues that can impact the project’s success. This allows for timely interventions and proactive risk management.
4. Performance Tracking: KPIs allow for continuous tracking and monitoring of project performance. Regular assessment against KPIs helps companies stay on track and make adjustments as necessary. It provides real-time visibility into progress, enabling project teams to address issues promptly and keep the project on schedule and within budget.
5. Communication and Transparency: KPIs promote transparency and facilitate communication among project teams, stakeholders, and clients. By having clearly defined KPIs, everyone involved in the construction project can understand the goals, expectations, and performance standards. This encourages collaboration, accountability, and effective communication among all parties involved.
6. Performance Improvement: KPIs serve as a catalyst for performance improvement. By tracking key metrics, construction companies can identify areas for enhancement and implement targeted strategies to drive performance. KPIs highlight where resources, processes, or systems may need adjustments, leading to increased efficiency and effectiveness.
7. Benchmarking and Best Practices: KPIs allow construction companies to benchmark their performance against industry standards and best practices. By comparing their performance to peers or industry averages, companies can identify areas of competitive advantage or areas that need improvement. This benchmarking process can lead to the adoption of industry best practices and the implementation of strategies for continuous improvement.
Ultimately, KPIs play a crucial role in the construction industry by providing a quantifiable framework for performance measurement, goal alignment, data-driven decision making, performance tracking, communication, performance improvement, and benchmarking. By leveraging KPIs effectively, construction companies can enhance their project management, achieve better results, and drive overall success in a highly competitive industry.
Challenges in Implementing KPI in Construction
While Key Performance Indicators (KPIs) are essential tools for measuring and improving performance in the construction industry, their successful implementation is not without challenges. The unique nature of construction projects and the complex dynamics within the industry present several hurdles that need to be addressed. Let’s explore some of the key challenges:
1. Lack of Standardization: One of the major challenges in implementing KPIs in construction is the lack of standardized metrics and definitions. Each construction project is unique, with varying goals, objectives, and stakeholder requirements. This makes it challenging to develop a universally applicable set of KPIs that can be easily implemented across different projects and organizations.
2. Data Availability and Reliability: Construction projects generate vast amounts of data, but obtaining timely, accurate, and reliable data can be a challenge. Many construction companies struggle with inadequate data collection systems, data silos, and inconsistencies in data formats. Lack of integration between different software and systems used in construction further complicates data availability and reliability, making it difficult to establish meaningful KPIs.
3. Complex Stakeholder Environment: Construction projects involve multiple stakeholders, including owners, contractors, subcontractors, suppliers, architects, engineers, and regulatory bodies. Aligning the goals and expectations of these diverse stakeholders and defining relevant KPIs can be a complex task. Ensuring consensus and cooperation among all parties is crucial for successful KPI implementation.
4. Dynamic Nature of Construction Projects: Construction projects are highly dynamic and subject to frequent changes, uncertainties, and unforeseen events. These changes may impact the initially defined KPIs, requiring constant reassessment and adjustment. Flexibility and adaptability are essential in order to accommodate the evolving nature of construction projects and their associated KPIs.
5. Cultural Resistance to Change: Implementing KPIs often requires cultural change within an organization. Resistance to change, both at the individual and organizational level, can hinder the successful implementation and utilization of KPIs. It is crucial to address this resistance through employee education and engagement, effective communication, and leadership support.
6. Overwhelming Number of KPIs: Construction projects involve numerous variables, and it can be tempting to define too many KPIs to cover every aspect of performance. However, an excessive number of KPIs can lead to information overload and dilute the focus on critical metrics. It is essential to strike a balance and prioritize KPIs that are directly aligned with strategic objectives and have the most significant impact on project success.
7. Establishing Baselines and Targets: Setting realistic baselines and targets for KPIs can be challenging in the construction industry. The lack of historical data or industry benchmarks, along with the uniqueness of each project, makes it difficult to establish meaningful benchmarks and targets for performance evaluation. Proper analysis, expert input, and industry research can help in setting achievable and relevant baselines and targets.
Overcoming these challenges is essential to successfully implement and utilize KPIs in construction projects. Acknowledging these challenges and developing strategies and processes to address them will enable construction companies to leverage the power of KPIs and improve their overall performance and project success.
Key KPIs in the Construction Industry
In the construction industry, selecting the right Key Performance Indicators (KPIs) is crucial for measuring and improving project performance. While the specific KPIs may vary depending on the nature of the project and the company’s objectives, there are several key metrics that are commonly used in the construction industry. Let’s explore some of these key KPIs:
1. Cost Performance Index (CPI): CPI measures the efficiency of cost utilization in a construction project. It compares the actual costs incurred with the budgeted costs. A CPI value greater than 1 indicates that the project is under budget, while a value less than 1 indicates cost overruns.
2. Schedule Performance Index (SPI): SPI measures the efficiency of schedule adherence in a construction project. It compares the actual progress achieved with the planned progress. An SPI value greater than 1 indicates that the project is ahead of schedule, while a value less than 1 indicates delays in project completion.
3. Safety Incident Rate (SIR): SIR measures the number of safety incidents per unit of work, such as accidents, injuries, or near misses. It provides insights into the effectiveness of safety measures and the overall safety culture of the construction project.
4. Earned Value (EV): EV is a performance measurement technique that integrates cost, time, and work accomplishment. It measures the value of work completed, allowing project managers to assess if they are on track in terms of cost and schedule.
5. Productivity Rate: Productivity rate measures the amount of work completed per unit of time or effort. It helps in evaluating the efficiency of labor, equipment, and materials utilization. Productivity rate KPIs can be specific to different aspects of the project, such as labor productivity or equipment utilization.
6. Quality Control Index: Quality control index measures the level of adherence to quality standards and specifications in a construction project. It assesses the number of defects, rework, and non-compliance incidents and provides insights into the effectiveness of quality management processes.
7. Customer Satisfaction Score (CSAT): CSAT measures the satisfaction level of clients or end-users with the completed construction project. It can be measured through surveys or feedback mechanisms and helps in assessing if the project meets the expectations and requirements of the stakeholders.
8. Sustainability Metrics: With the growing emphasis on sustainable construction practices, KPIs related to sustainability are increasingly relevant. These metrics can include energy efficiency, waste reduction, carbon footprint, and other environmental impact indicators.
While these are some of the key KPIs in the construction industry, it is important to tailor the selection of KPIs to the specific project and organizational objectives. By selecting and monitoring the right KPIs, construction companies can assess and improve their performance in critical areas, ensure project success, and drive continuous improvement.
When setting KPIs in construction, ensure they are specific, measurable, achievable, relevant, and time-bound (SMART). This will help track progress and drive performance.
Read more: What Is OSHA In Construction
Benefits of Using KPI in Construction
Implementing Key Performance Indicators (KPIs) in the construction industry offers numerous benefits that contribute to the overall success of projects. Let’s explore the key advantages of using KPIs:
1. Performance Measurement and Evaluation: KPIs provide a structured and quantitative way to measure and evaluate project performance. By tracking the relevant metrics, companies can assess how effectively they are achieving their goals and objectives. This enables them to identify areas of strength and areas that require improvement, leading to better decision-making and enhanced project management.
2. Goal Alignment and Focus: KPIs ensure that the efforts of the project team are aligned with the company’s strategic goals. By setting specific KPIs, construction companies can establish a clear roadmap for success. KPIs keep the focus on critical performance areas, helping project teams prioritize their efforts and resources towards achieving the desired outcomes.
3. Proactive Decision Making: KPIs enable proactive decision making by providing timely and accurate data. By tracking performance against set metrics, companies can identify issues or deviations from the plan early on. This allows project teams to take corrective actions promptly and avoid potential delays or cost overruns. KPIs help in managing risks and ensuring efficient project execution.
4. Performance Improvement: KPIs facilitate performance improvement by highlighting areas of inefficiency or underperformance. By monitoring metrics related to productivity, cost efficiency, quality, or safety, companies can identify gaps and implement targeted improvement strategies. KPIs act as a driving force for continuous improvement, enabling construction companies to constantly enhance their operations and deliver better outcomes.
5. Resource Allocation and Optimization: KPIs assist in effective resource allocation and utilization. By analyzing performance metrics, companies can identify areas where resources are being overutilized or underutilized. This helps in optimizing resource allocation, maximizing productivity, and reducing waste. KPIs provide insights into areas such as labor efficiency, equipment utilization, and material consumption, enabling better resource management.
6. Stakeholder Communication and Transparency: KPIs promote effective communication and transparency among project stakeholders. By defining and tracking key metrics, construction companies can provide stakeholders, including clients, contractors, and regulatory bodies, with objective performance data. This fosters transparency, builds trust, and enhances collaboration, leading to better project outcomes and customer satisfaction.
7. Benchmarking and Best Practices: KPIs facilitate benchmarking against industry standards and best practices. By comparing their performance with peers or industry averages, companies can identify areas of competitive advantage or areas that need improvement. This benchmarking process allows for the adoption of best practices, innovation, and continuous learning, driving overall industry progress.
8. Accountability and Motivation: KPIs promote accountability among project team members. By establishing clear performance expectations, employees have a measurable target to strive for. KPIs create a sense of ownership and motivation, as progress is monitored and recognized. This leads to increased productivity, higher engagement, and a positive work culture within the construction company.
Overall, using KPIs in the construction industry brings numerous benefits, including improved performance measurement, goal alignment, proactive decision making, performance improvement, resource optimization, stakeholder communication, benchmarking, and enhanced accountability. By leveraging these advantages, construction companies can drive project success, achieve better outcomes, and excel in this competitive industry.
Best Practices for Implementing KPI in Construction
Implementing Key Performance Indicators (KPIs) in the construction industry requires careful planning, effective implementation strategies, and ongoing monitoring. To ensure the successful adoption and utilization of KPIs, here are some best practices that construction companies should consider:
1. Define Clear Objectives: Before selecting KPIs, it is crucial to define clear objectives and establish specific targets that align with the company’s overall strategy. Clear objectives provide a foundation for selecting relevant KPIs and ensure that the metrics chosen are directly linked to the desired outcomes.
2. Select Relevant and Measurable KPIs: Choose KPIs that are relevant to the objectives and measurable based on available data. The selected KPIs should be specific, quantifiable, and align with the construction project’s goals. Avoid selecting too many KPIs to prevent data overload and ensure that the chosen metrics provide meaningful insights.
3. Align KPIs with Stakeholder Requirements: Engage with key stakeholders, including clients, contractors, and regulatory bodies, to identify their specific requirements and expectations. Align the selected KPIs with these stakeholder needs to enhance collaboration, transparency, and accountability throughout the project lifecycle.
4. Establish Baselines and Targets: Set realistic baselines and targets for each KPI to provide a benchmark for measuring progress. Baselines can be established using historical data, industry benchmarks, or expert judgment. These baselines serve as starting points and help in evaluating performance against set targets.
5. Ensure Data Availability and Reliability: Establish a robust data collection and management system to ensure the availability and reliability of data for KPI measurement. Invest in technologies and software that facilitate seamless data integration from various sources and ensure data integrity. Regularly validate and verify the accuracy of data to enhance the reliability of KPI measurements.
6. Implement Effective Performance Reporting: Develop a comprehensive performance reporting system that provides timely and actionable insights. Utilize visual dashboards, reports, and analytics tools to present KPI data in a format that is easily understandable and accessible to all stakeholders. Ensure that the performance reports are updated regularly and disseminated to the relevant parties.
7. Foster a Data-Driven Culture: Create a data-driven culture within the organization by promoting the importance of KPIs and encouraging employees to actively engage with performance metrics. Educate the project teams on the significance of KPIs, provide training on data analysis and interpretation, and encourage employees to take ownership of their performance and contribute to continuous improvement.
8. Regularly Monitor and Review KPIs: Continuously monitor and review the selected KPIs to ensure that they remain relevant and aligned with changing project requirements. Regularly assess progress against targets and conduct periodic reviews to identify areas for improvement and make necessary adjustments to the KPIs or implementation strategies.
9. Establish Accountability and Recognition: Foster accountability and recognition for KPI performance among project team members. Hold individuals and teams accountable for their performance against the defined targets. Recognize and celebrate achievements, and provide constructive feedback to promote a culture of continuous learning and improvement.
10. Continuously Improve KPI Selection and Implementation: KPI implementation is an iterative process. Continuously evaluate the effectiveness of the selected KPIs and implementation strategies. Seek feedback from stakeholders and project teams to identify areas for improvement and make necessary adjustments. Regularly reassess the relevance, accuracy, and usefulness of KPIs to ensure their continued value.
By following these best practices, construction companies can successfully implement and utilize KPIs to improve project performance, enhance decision-making, and drive success in the dynamic and challenging construction industry.
Examples of Successful KPI Implementation in Construction
Successful implementation of Key Performance Indicators (KPIs) in construction projects has yielded impressive results for many companies. Let’s examine a few real-life examples of how construction firms have effectively utilized KPIs to drive performance and achieve project success:
1. Turner Construction: Turner Construction, one of the largest construction firms in the United States, is known for its focus on safety. They implemented a Safety Incident Rate (SIR) KPI to measure safety performance on their projects. By consistently tracking and analyzing safety incidents, Turner Construction reduced their SIR by 60% over a span of five years. This success can be attributed to their strong safety culture, proactive risk management, and continuous improvement efforts driven by the KPI.
2. Skanska: Skanska, a global construction company, implemented a KPI called the Sustainability Index to measure and improve their sustainability performance. This KPI tracked various metrics such as energy efficiency, waste reduction, and materials sourcing. By using the Sustainability Index, Skanska was able to achieve significant reductions in carbon emissions and waste generation across their projects, showcasing their commitment to sustainable construction practices.
3. McCarthy Building Companies: McCarthy Building Companies used KPIs to drive productivity and efficiency in their construction projects. They implemented a Labor Productivity KPI, which measured the amount of work completed per unit of labor. By closely monitoring this metric, McCarthy was able to identify opportunities for process improvement, optimize resource allocation, and increase productivity on their projects. This resulted in shorter project durations and cost savings for the company.
4. PCL Construction: PCL Construction, a leading North American construction firm, utilized KPIs to improve project cost management. They implemented the Cost Performance Index (CPI) as a KPI to measure the efficiency of cost utilization. By regularly tracking and analyzing CPI, PCL Construction was able to identify cost overruns early on and make necessary adjustments to bring projects back on budget. This KPI implementation led to improved cost control and financial performance on their projects.
5. BAM Construction: BAM Construction, a European construction company, implemented the Earned Value (EV) KPI to monitor project progress, cost, and schedule adherence. By integrating EV into their project management processes, BAM Construction was able to accurately measure the value of work completed and compare it to the planned value. This allowed them to proactively manage project risks, identify deviations, and take corrective actions to keep projects on track.
These examples demonstrate how KPI implementation can drive performance improvement and project success in the construction industry. By selecting and monitoring relevant KPIs, construction companies can effectively manage safety, sustainability, productivity, cost, and schedule performance. These success stories highlight the power of KPIs in enabling construction firms to make data-driven decisions, enhance collaboration, and continuously improve their operations.
Conclusion
Key Performance Indicators (KPIs) play a pivotal role in the construction industry by providing a structured framework for measuring, evaluating, and improving project performance. They serve as powerful tools that enable construction companies to track progress, align goals, and make data-driven decisions to drive success.
In this article, we have explored the definition of KPIs and their importance in the construction industry. We have discussed the challenges that come with implementing KPIs and the key KPIs commonly used in construction projects, including cost performance, schedule adherence, safety, productivity, quality, customer satisfaction, and sustainability metrics.
The benefits of using KPIs in construction are significant. KPIs facilitate performance measurement, goal alignment, proactive decision-making, performance improvement, resource optimization, stakeholder communication, benchmarking, and accountability. By implementing KPIs effectively, construction companies can enhance project management, achieve better outcomes, and excel in a competitive industry.
To successfully implement KPIs in construction, it is crucial to follow best practices such as defining clear objectives, selecting relevant and measurable metrics, aligning KPIs with stakeholder requirements, establishing baselines and targets, ensuring data availability and reliability, implementing effective performance reporting, fostering a data-driven culture, and regularly monitoring and reviewing KPIs.
Real-life examples of successful KPI implementation in construction have showcased how companies have leveraged KPIs to drive performance and achieve project success. Companies like Turner Construction, Skanska, McCarthy Building Companies, PCL Construction, and BAM Construction have demonstrated how KPIs can be utilized to improve safety, sustainability, productivity, cost management, and project progress.
In conclusion, the effective implementation and utilization of KPIs in the construction industry can lead to improved performance, enhanced decision-making, and increased project success. By selecting the right KPIs, monitoring performance, and continuously improving processes, construction companies can optimize resources, mitigate risks, and deliver projects with excellence. KPIs act as valuable compasses, guiding construction companies towards their goals and helping them build a successful future.
Frequently Asked Questions about What Is KPI In Construction
Was this page helpful?
At Storables.com, we guarantee accurate and reliable information. Our content, validated by Expert Board Contributors, is crafted following stringent Editorial Policies. We're committed to providing you with well-researched, expert-backed insights for all your informational needs.
0 thoughts on “What Is KPI In Construction”