Home>diy>Building & Construction>What Is O And M In Construction
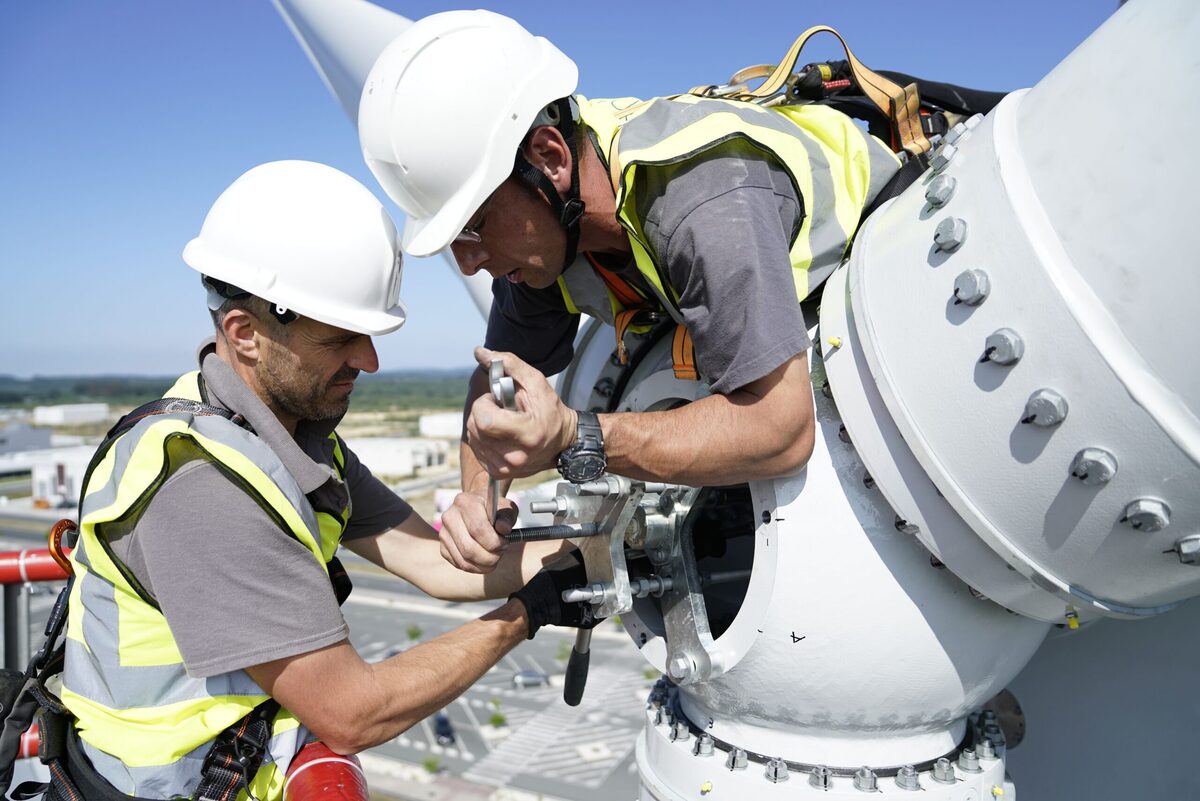
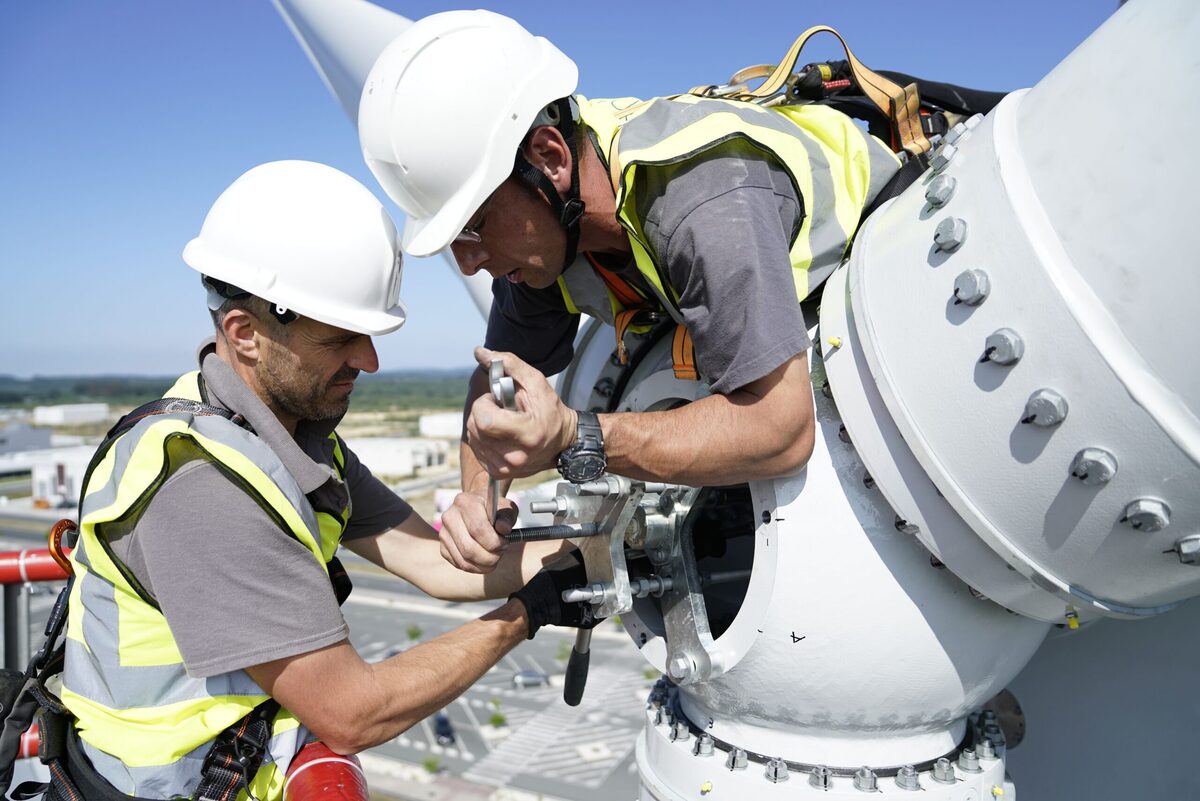
Building & Construction
What Is O And M In Construction
Modified: January 9, 2024
Learn about the importance of O&M in building construction and how it contributes to efficient operations and maintenance processes. Explore key concepts and best practices for optimal project success.
(Many of the links in this article redirect to a specific reviewed product. Your purchase of these products through affiliate links helps to generate commission for Storables.com, at no extra cost. Learn more)
Introduction
Welcome to the world of construction, where buildings come to life and dreams become reality. In this dynamic and ever-evolving industry, there are various processes and stages that go into bringing a construction project to fruition. One crucial aspect of construction that often gets overlooked is operation and maintenance, commonly known as O and M.
O and M in construction refers to the ongoing management and upkeep of a building or infrastructure once it has been completed. It encompasses a wide range of activities, including preventive maintenance, repairs, inspections, and optimization of building systems and components. Essentially, O and M in construction plays a vital role in ensuring the long-term functionality, efficiency, and sustainability of a structure.
It is important to note that O and M in construction is not a one-time process, but rather an ongoing commitment throughout the lifespan of a building. It starts from the moment a construction project is completed and continues indefinitely, as a building needs regular care and maintenance to remain functional and safe.
The importance of O and M in construction cannot be overstated. Without proper operation and maintenance, buildings can deteriorate quickly, leading to safety hazards, reduced performance, and increased costs. O and M activities help extend the lifespan of a building, optimize energy consumption, improve occupant comfort, and enhance the overall efficiency of the construction project.
In addition, O and M in construction is also crucial for meeting regulatory requirements and sustainability goals. Building codes and regulations often mandate specific maintenance practices to ensure compliance with safety standards. Moreover, sustainable building certifications, such as LEED (Leadership in Energy and Environmental Design), place a strong emphasis on ongoing building management and performance optimization.
Now that we understand the importance of O and M in construction, let’s delve deeper into the role it plays in construction projects and explore key components and best practices for effective operation and maintenance.
Key Takeaways:
- O and M in construction is essential for ensuring building safety, longevity, and operational efficiency. From preventive maintenance to energy optimization, effective O and M practices are crucial for sustainable building management.
- Embracing future trends such as predictive maintenance, IoT, and AI technologies will shape the future of O and M in construction. These innovations will drive data-driven decision-making, enhanced efficiency, and improved sustainability in building management.
Read more: What Is An O&M Manual In Construction
Definition of O and M in Construction
Operation and Maintenance (O and M) in construction refers to the ongoing management, upkeep, and optimization of a building or infrastructure once it has been completed. It encompasses a wide range of activities that are crucial for ensuring the long-term functionality, efficiency, and sustainability of a structure.
The operation aspect of O and M involves the day-to-day activities required to keep a building operational and functional. This includes tasks such as cleaning, security, waste management, and utilities management. The operations team is responsible for ensuring that the building systems, such as HVAC (heating, ventilation, and air conditioning), lighting, plumbing, and electrical, are properly maintained and functioning optimally.
The maintenance aspect of O and M focuses on the regular inspection, servicing, and repair of building components and systems. Preventive maintenance plays a vital role in identifying and addressing potential issues before they escalate into major problems. It involves tasks such as lubrication of moving parts, filter replacements, equipment testing, and structural inspections. Reactive maintenance, on the other hand, involves addressing unplanned breakdowns or emergencies and fixing them as quickly as possible to minimize disruptions.
In addition to the day-to-day operations and maintenance activities, optimization is also an essential element of O and M in construction. Optimization involves analyzing building performance data, identifying areas for improvement, and implementing strategies to maximize energy efficiency, occupant comfort, and cost savings. This can include measures such as implementing smart building technologies, upgrading equipment to more energy-efficient models, and adjusting operational parameters to achieve optimal performance.
O and M in construction is a continuous process that starts from the moment a construction project is completed and continues throughout the lifespan of the building. It requires a dedicated team of professionals, including facility managers, maintenance technicians, and operations personnel, who are responsible for ensuring that the building operates smoothly and efficiently.
Overall, the definition of O and M in construction encompasses the ongoing management, maintenance, and optimization efforts required to keep a building operating at its best. It is the backbone of maintaining the functionality, safety, and sustainability of a structure, and its importance cannot be underestimated in the construction industry.
Importance of O and M in Construction
O and M (Operation and Maintenance) in construction is undeniably a crucial aspect of the building lifecycle. Its importance lies in its ability to ensure the long-term functionality, efficiency, and sustainability of a structure. Let’s explore why O and M is so important in the construction industry.
First and foremost, proper O and M practices are essential for the safety of the occupants and users of a building. Regular inspections, preventive maintenance, and prompt repairs help identify and address potential hazards, ensuring a safe environment for everyone. From fire safety systems to structural integrity, O and M protocols prioritize the well-being of people within the building.
Secondly, effective O and M in construction plays a significant role in extending the lifespan of a building. A well-maintained structure can withstand the test of time, reducing the need for premature replacement or extensive repairs. Regular inspections and maintenance activities, such as roof inspections, facade assessments, and HVAC system checks, help identify and rectify issues before they escalate, prolonging the life of the building.
O and M in construction also has a substantial impact on the operational efficiency of a building. Energy optimization measures, such as tuning HVAC systems, retrofitting lighting fixtures, and implementing smart building technologies, can significantly reduce energy consumption and operational costs. With rising energy prices and environmental concerns, efficient O and M practices contribute to sustainability goals, improving the overall environmental performance of the building.
Furthermore, effective O and M is essential in maintaining occupant comfort and satisfaction. Regularly servicing and optimizing building systems ensures that they operate at their peak performance, providing a comfortable and productive environment for occupants. This includes maintaining optimal indoor air quality, temperature control, lighting levels, and water usage. Happy and satisfied occupants contribute to a positive reputation for the building and can attract more tenants or users.
Compliance with regulatory requirements is another critical aspect of O and M in construction. Building codes and regulations often stipulate specific maintenance procedures to meet safety standards and ensure the well-being of occupants. Failure to comply with these requirements can result in legal consequences or jeopardize the insurance coverage of the building.
Finally, effective O and M practices lead to cost savings in the long run. By implementing preventive maintenance strategies and addressing issues proactively, costly emergency repairs can be minimized or avoided altogether. Regular maintenance and optimization also contribute to energy savings, reducing operational expenses and improving the overall financial performance of the building.
In summary, O and M in construction is of paramount importance for several reasons: safety, building longevity, operational efficiency, occupant comfort, regulatory compliance, and cost savings. By prioritizing effective operation and maintenance practices, construction professionals can ensure the ongoing success and sustainability of their projects.
Role of O and M in Construction Projects
O and M (Operation and Maintenance) plays a critical role in construction projects, encompassing various activities that are essential for the long-term success and functionality of a building. Let’s explore the key roles that O and M plays in construction projects.
First and foremost, O and M ensures the smooth transition from the construction phase to the operational phase. It bridges the gap between construction completion and the ongoing management of the building. O and M activities begin immediately after the construction process, ensuring that the building is ready for occupancy and meets all necessary safety and functional requirements.
O and M also plays a significant role in optimizing the performance of building systems and components. During the construction phase, various systems such as electrical, plumbing, HVAC, and building automation are installed. O and M ensures that these systems are properly commissioned, tested, and calibrated to operate efficiently and effectively.
Moreover, O and M is responsible for the ongoing maintenance and servicing of these systems. Regular inspections, preventive maintenance, and timely repairs are carried out to ensure that the systems continue to operate at their optimal levels. This proactive approach helps identify and address potential issues before they lead to major breakdowns or disruptions in building operations.
Another crucial role of O and M is to manage the day-to-day operations and activities of a building. This includes tasks such as cleaning, waste management, security, and utilities management. O and M professionals ensure that the building is well-maintained, clean, and safe for its occupants and visitors.
Furthermore, O and M in construction projects also involve managing the relationships with external service providers and vendors. This includes contract management, scheduling maintenance visits, and coordinating repairs and upgrades. O and M professionals work closely with contractors, suppliers, and service providers to ensure that all maintenance activities and services are carried out effectively and efficiently.
Additionally, O and M plays a crucial role in maintaining regulatory compliance. Ongoing building inspections, safety audits, and adherence to local building codes and regulations are vital aspects of O and M. By ensuring compliance with these requirements, O and M professionals help mitigate legal risks and safety hazards.
Lastly, O and M in construction projects support the overall sustainability and environmental goals. From implementing energy-efficient practices to optimizing water consumption, O and M professionals contribute to reducing the carbon footprint of the building. They also assist in the implementation of sustainable systems and technologies, such as renewable energy sources and green building certifications like LEED (Leadership in Energy and Environmental Design).
In summary, the role of O and M in construction projects is multifaceted. It involves optimizing building systems, ensuring ongoing maintenance, managing day-to-day operations, maintaining regulatory compliance, fostering vendor relationships, and promoting sustainability. By fulfilling these roles, O and M professionals contribute to the success and longevity of construction projects.
Key Components of O and M in Construction
When it comes to O and M (Operation and Maintenance) in construction, there are several key components that are crucial for ensuring the long-term functionality and sustainability of a building. Let’s explore these key components and their importance in O and M practices.
1. Preventive Maintenance: One of the fundamental components of O and M is preventive maintenance. This involves regularly scheduled inspections, servicing, and upkeep of building systems and components to identify and address potential issues before they escalate into major problems. Preventive maintenance can include tasks such as lubrication, filter replacements, equipment testing, and structural inspections. By implementing a proactive approach to maintenance, costly emergency repairs and disruptions to building operations can be minimized or avoided.
2. Repairs and Corrective Maintenance: While preventive maintenance aims to prevent issues, repairs and corrective maintenance are inevitable components of O and M in construction. Reactive maintenance involves addressing unplanned breakdowns or emergencies and restoring systems or components to their functioning state. Timely and efficient repairs are crucial for minimizing downtime and ensuring the smooth operation of the building.
3. Energy Management: Energy optimization is an important aspect of O and M in construction. This includes strategies and measures to minimize energy consumption and maximize energy efficiency. By implementing energy management practices such as optimizing HVAC systems, retrofitting lighting fixtures, and utilizing smart building technologies, the operational costs of the building can be reduced while promoting sustainability.
4. Asset Management: Managing building assets is another key component of O and M. This involves keeping track of the condition, performance, and lifecycle of building systems and components. Asset management includes inventory management, tracking warranty information, and planning for replacements or upgrades as needed. Effective asset management ensures that the resources are utilized efficiently, and replacements are planned in a timely manner to avoid unexpected disruptions.
5. Environmental Management: O and M in construction also involves responsible environmental management. This includes implementing sustainable practices to reduce the carbon footprint of the building, such as optimizing water consumption, promoting recycling, and integrating renewable energy sources. Environmental management focuses on minimizing the impact of the building on the environment and promoting a more sustainable future.
6. Safety and Compliance: Safety is of utmost importance in O and M practices. Regular building inspections, safety audits, and adherence to local building codes and regulations are essential components of ensuring the safety of occupants and complying with legal requirements. This includes fire safety measures, proper emergency signage, and adherence to safety protocols for building systems and operations.
7. Documentation and Reporting: Proper documentation and reporting are essential in O and M in construction. This includes keeping records of all maintenance activities, repairs, inspections, and equipment servicing. Accurate and comprehensive documentation allows for easy access to historical data, tracking of maintenance schedules, and analysis of trends to make informed decisions regarding building management and maintenance.
In summary, the key components of O and M in construction include preventive maintenance, repairs and corrective maintenance, energy management, asset management, environmental management, safety and compliance, and documentation and reporting. By addressing each of these components, construction professionals can ensure the long-term functionality, efficiency, and sustainability of a building.
O&M in construction stands for Operations and Maintenance. It refers to the ongoing management and upkeep of a building or infrastructure after construction is complete. Proper O&M is essential for the long-term functionality and sustainability of a project.
Read more: What Is O&P In Construction
O and M Best Practices in Construction
Effective O and M (Operation and Maintenance) practices are critical for ensuring the long-term functionality, efficiency, and sustainability of a building. To achieve optimal results, construction professionals should implement the following best practices in O and M:
1. Develop a Comprehensive O and M Plan: A well-defined and documented O and M plan is the foundation of successful building management. This plan should include detailed procedures, schedules, and responsibilities for all maintenance activities. It should also outline goals, performance metrics, and strategies for optimizing energy efficiency, occupant comfort, and sustainability.
2. Regular Inspections and Preventive Maintenance: Implementing a regular inspection and preventive maintenance program is crucial for identifying and addressing potential issues early on. This includes scheduling routine inspections, carrying out equipment servicing, lubrication, and filter replacements, and addressing any minor repairs proactively. Such practices help prevent major breakdowns and minimize downtime.
3. Implement Energy Optimization Measures: Energy optimization is a key component of O and M. Implementing energy-efficient practices such as installing programmable thermostats, optimizing HVAC systems, retrofitting lighting fixtures with LED bulbs, and utilizing occupancy sensors can significantly reduce energy consumption and operational costs. Regular monitoring and data analysis can help identify opportunities for further energy optimization.
4. Establish Proper Record-Keeping: Accurate and comprehensive record-keeping is essential for effective O and M. Maintain a centralized system to track all maintenance activities, repairs, inspections, equipment warranties, and service provider contracts. This ensures easy access to essential information, aids in making informed decisions, and facilitates proactive maintenance planning.
5. Prioritize Safety Compliance: Safety should always be a top priority in O and M practices. Regularly conduct safety inspections, fire drills, and ensure that all equipment and systems meet safety standards. Maintain clear emergency action plans, properly display emergency signage, and provide training to building occupants regarding safety protocols. Compliance with regulatory requirements minimizes risks and ensures a safe environment.
6. Foster Communication and Collaboration: Effective communication and collaboration among all stakeholders are vital for successful O and M. Establish clear channels of communication between facility managers, maintenance staff, service providers, and building occupants. Regular meetings, feedback loops, and training sessions can help improve efficiency, address concerns, and ensure smooth coordination.
7. Embrace Technology and Automation: Utilize technology and automation tools to streamline O and M processes. Implement computerized maintenance management systems (CMMS) to track maintenance activities, schedule inspections, and generate work orders. Embrace smart building technologies for energy monitoring, remote equipment diagnostics, and predictive maintenance. These advancements can improve efficiency, reduce manual errors, and enhance productivity.
8. Continuous Improvement and Training: Invest in ongoing training and professional development for O and M staff. Stay updated with the latest trends, regulations, and best practices in the industry. Encourage a culture of continuous improvement, where lessons learned from previous projects are incorporated, and innovative solutions are implemented to enhance O and M effectiveness.
By incorporating these best practices into O and M processes, construction professionals can ensure the long-term success and sustainability of buildings. Effective O and M practices not only optimize building performance and occupant comfort but also contribute to cost savings, compliance with regulations, and environmental sustainability.
Challenges and Solutions in O and M in Construction
While O and M (Operation and Maintenance) is crucial for the long-term functionality and sustainability of a building, it is not without its challenges. Recognizing and addressing these challenges is essential for successful O and M practices in the construction industry. Let’s explore some common challenges and their corresponding solutions:
1. Aging Infrastructure: One of the primary challenges in O and M is managing aging infrastructure. As buildings and systems age, they are more prone to breakdowns and require frequent repairs. The solution is to implement a proactive maintenance approach that focuses on regular inspections, preventive maintenance, and timely replacement of aging components. This can help extend the lifespan of the infrastructure and minimize the risk of unexpected failures.
2. Budget Constraints: Limited budgets can often hinder comprehensive O and M practices. However, investing in preventive maintenance and energy optimization measures can actually save costs in the long run. Demonstrating the financial benefits of these practices through cost analysis and ROI calculations can help secure necessary funding. Additionally, exploring alternative funding sources, such as energy efficiency grants or performance contracts, can provide additional resources for O and M activities.
3. Complex Building Systems: Modern buildings are equipped with complex systems, such as HVAC, electrical, and automation systems, which require specialized knowledge and expertise for maintenance. The solution is to ensure that the O and M staff are well-trained and have access to the necessary resources, manuals, and documentation. Collaborating with system manufacturers and service providers can also help navigate the complexities of maintaining and troubleshooting these systems effectively.
4. Limited Staffing and Expertise: Insufficient staffing and lack of expertise can pose challenges in O and M. Employing a knowledgeable and skilled workforce is crucial for successful O and M practices. Cross-training staff members and investing in professional development programs can help expand the skill set of existing staff. Outsourcing certain O and M tasks to specialized service providers can also supplement staffing constraints and bring in the required expertise.
5. Technological Advancements: Rapid technological advancements can create challenges in O and M practices as older systems and processes become outdated. The solution is to stay updated with the latest technologies and industry trends. Embrace new tools and automation technologies that can streamline O and M processes and improve efficiency. Conduct regular technology assessments to identify areas where upgrades or system integrations can enhance O and M effectiveness.
6. Sustainability and Environmental Compliance: Meeting sustainability goals and complying with environmental regulations can be challenging for O and M practitioners. The solution is to prioritize sustainability in all aspects of O and M. This includes implementing energy-efficient practices, optimizing water consumption, reducing waste, and utilizing renewable energy sources. Regular monitoring and data analysis can help track progress and ensure compliance with environmental standards and certifications.
7. Lack of Communication and Coordination: Inadequate communication and coordination between stakeholders can lead to inefficiencies and delays in O and M processes. The solution is to establish clear lines of communication, both within the O and M team and with other stakeholders, such as building occupants, contractors, and service providers. Regular meetings, feedback sessions, and shared platforms for collaboration can help improve communication and ensure smoother coordination.
By addressing these challenges and implementing the corresponding solutions, construction professionals can overcome obstacles in O and M practices. Proactive maintenance, budget management, skill development, embracing technology, sustainability focus, and effective communication are key elements for successful O and M in the construction industry.
Case Studies of Successful O and M in Construction Projects
Examining real-life examples of successful O and M (Operation and Maintenance) practices in construction projects can provide valuable insights and inspiration for implementing effective strategies. Here are two case studies highlighting such successful O and M projects:
1. Case Study: One World Trade Center, New York City
One World Trade Center, the iconic skyscraper built to replace the Twin Towers after the September 11 attacks, is a prime example of exemplary O and M practices. The building’s management team implemented several key strategies:
– Proactive Maintenance: The management team established a comprehensive preventive maintenance program, conducting regular inspections, servicing mechanical and electrical systems, and addressing potential issues before they became major problems.
– Energy Optimization: One World Trade Center boasts state-of-the-art energy-efficient systems, including a highly efficient HVAC system and a sophisticated lighting control system. These measures contributed to significant energy savings and reduced operational costs.
– Sustainable Practices: The building was designed with sustainability in mind, achieving LEED Gold certification. O and M practices focused on continuous sustainability improvements, including waste reduction, water conservation, and renewable energy utilization.
– Technology Integration: Smart building technologies were employed to optimize the building’s performance. By utilizing advanced building management systems, the team gained real-time insights into energy consumption, system performance, and occupant comfort, enabling proactive adjustments and efficient management.
2. Case Study: The Edge, Amsterdam
The Edge, a cutting-edge sustainable office building in Amsterdam, showcases innovative O and M practices that have earned it the title of one of the world’s most sustainable buildings:
– Energy Efficiency: The Edge utilizes an extensive array of technologies to maximize energy efficiency, including rooftop solar panels, energy storage solutions, and advanced climate control systems. These measures enable the building to produce more energy than it consumes.
– Smart Building Technology: The Edge incorporates a range of smart technologies, such as occupancy sensors, lighting controls, and flexible workspace management systems. These technologies contribute to energy optimization, occupant comfort, and space utilization.
– Dynamic Work Environment: O and M practices at The Edge emphasized creating a flexible and adaptable work environment. The building features various workspace configurations, including shared workstations, collaboration areas, and private offices, accommodating diverse work styles and promoting productivity.
– Integrated Facility Management: The Edge employed an integrated approach to facility management. The on-site facility management team collaborated closely with all stakeholders, including tenants, service providers, and technology partners, to ensure seamless operations and continued sustainability improvements.
These case studies demonstrate the value of implementing effective O and M practices in construction projects. They highlight the importance of proactive maintenance, energy optimization, sustainability, technology integration, and collaborative facility management. By drawing inspiration from successful projects like these, construction professionals can make informed decisions and implement best practices to enhance the O and M processes in their own projects.
Future Trends and Innovations in O and M in Construction
As the construction industry continues to evolve, so do the trends and innovations in O and M (Operation and Maintenance) practices. These advancements are driven by the desire for increased efficiency, sustainability, and occupant comfort. Let’s explore some of the future trends and innovations in O and M in construction:
1. Predictive Maintenance: Predictive maintenance utilizes data analytics and machine learning algorithms to predict equipment failures and optimize maintenance schedules. By analyzing performance data, equipment sensors, and historical maintenance records, O and M teams can identify signs of potential failures and perform maintenance tasks before breakdowns occur.
2. Internet of Things (IoT): The integration of IoT devices and sensors provides real-time monitoring and control of building systems. These sensors can collect data on energy consumption, temperature, humidity, occupant behavior, and more. IoT enables proactive maintenance, energy optimization, and the delivery of personalized comfort to building occupants.
3. Building Information Modeling (BIM): BIM technology allows for the creation of digital models that encompass all aspects of a building, including its systems, components, and maintenance records. O and M teams can leverage BIM data to visualize building systems, access critical information, plan maintenance activities, and simulate the impact of changes before implementation.
4. Augmented Reality (AR) and Virtual Reality (VR): AR and VR technologies offer immersive experiences for training, troubleshooting, and remote collaboration. O and M teams can use AR and VR to access virtual representations of building systems, visualize maintenance procedures, and receive real-time guidance in the field, improving efficiency and reducing errors.
5. Energy Storage and Microgrid Systems: As renewable energy sources become more prevalent, energy storage and microgrid systems are gaining popularity. These systems enable buildings to store excess energy and balance their energy usage with the grid. O and M practices will evolve to include the monitoring and maintenance of these systems to ensure optimal performance.
6. Robotics and Drones: Robotics and drones have the potential to revolutionize O and M in construction. Drones can be used for building inspections, allowing for faster and more detailed assessments of structures, facades, and hard-to-reach areas. Robots can assist in routine maintenance tasks, such as cleaning, maintenance checks, and repairs in hazardous environments.
7. Green Certifications and Standards: The demand for sustainable buildings and energy-efficient operations continues to grow. O and M practices will increasingly focus on achieving and maintaining green certifications such as LEED (Leadership in Energy and Environmental Design) and WELL Building Standard. Compliance with these standards ensures higher energy performance, improved indoor air quality, enhanced occupant comfort, and reduced environmental impact.
8. Artificial Intelligence (AI): AI technologies, such as machine learning and natural language processing, can analyze vast amounts of data to provide actionable insights for O and M. AI-powered chatbots and virtual assistants can also enhance communication and support for building occupants by answering questions, providing guidance on building systems, and troubleshooting common issues.
These future trends and innovations in O and M in construction signify a shift towards a more data-driven, connected, and sustainable approach. Predictive maintenance, IoT, BIM, AR/VR, energy storage, robotics, green certifications, and AI technologies will shape the way buildings are managed and operated in the years to come. By embracing these advancements, construction professionals can enhance efficiency, optimize energy consumption, improve occupant comfort, and ensure the long-term success of their projects.
Read more: What Does “T&M” Mean In Construction
Conclusion
O and M (Operation and Maintenance) in construction is a vital aspect of the building lifecycle that often goes unnoticed but plays a crucial role in ensuring the long-term functionality, efficiency, and sustainability of a structure. From preventive maintenance and repairs to energy optimization and environmental compliance, O and M practices are essential for the ongoing management and upkeep of buildings.
In this article, we delved into the definition of O and M in construction and explored its importance. We discussed the role of O and M in construction projects, highlighting key components such as preventive maintenance, energy management, asset management, and safety compliance. We also examined the best practices in O and M, emphasizing the need for a comprehensive plan, regular inspections, energy optimization, and effective communication.
Furthermore, we discussed the challenges and presented solutions in implementing O and M practices in construction. These included addressing aging infrastructure, budget constraints, complex building systems, limited staffing and expertise, technological advancements, sustainability goals, and communication gaps. Implementing these solutions can help overcome challenges and optimize O and M practices.
Additionally, we provided case studies of successful O and M in construction projects, showcasing real-life examples such as One World Trade Center and The Edge. These case studies highlighted the importance of proactive maintenance, energy efficiency, sustainability, and collaboration in achieving and maintaining the success of O and M initiatives.
Finally, we explored future trends and innovations in O and M in construction. Predictive maintenance, IoT, BIM, AR/VR, energy storage, robotics, green certifications, and AI technologies are poised to shape the future of O and M practices, enabling data-driven decision-making, enhanced efficiency, and improved sustainability.
In conclusion, O and M in construction is a multifaceted discipline that demands expertise, planning, and ongoing commitment. By implementing effective O and M practices, construction professionals can ensure the longevity, functionality, and sustainability of their buildings. From proactive maintenance to energy optimization and embracing technology, the continuous improvement of O and M practices will lead to safer, more efficient, and environmentally responsible buildings.
Frequently Asked Questions about What Is O And M In Construction
Was this page helpful?
At Storables.com, we guarantee accurate and reliable information. Our content, validated by Expert Board Contributors, is crafted following stringent Editorial Policies. We're committed to providing you with well-researched, expert-backed insights for all your informational needs.
0 thoughts on “What Is O And M In Construction”