Home>diy>Building & Construction>What Is The Difference Between OSHA Construction And General Industry
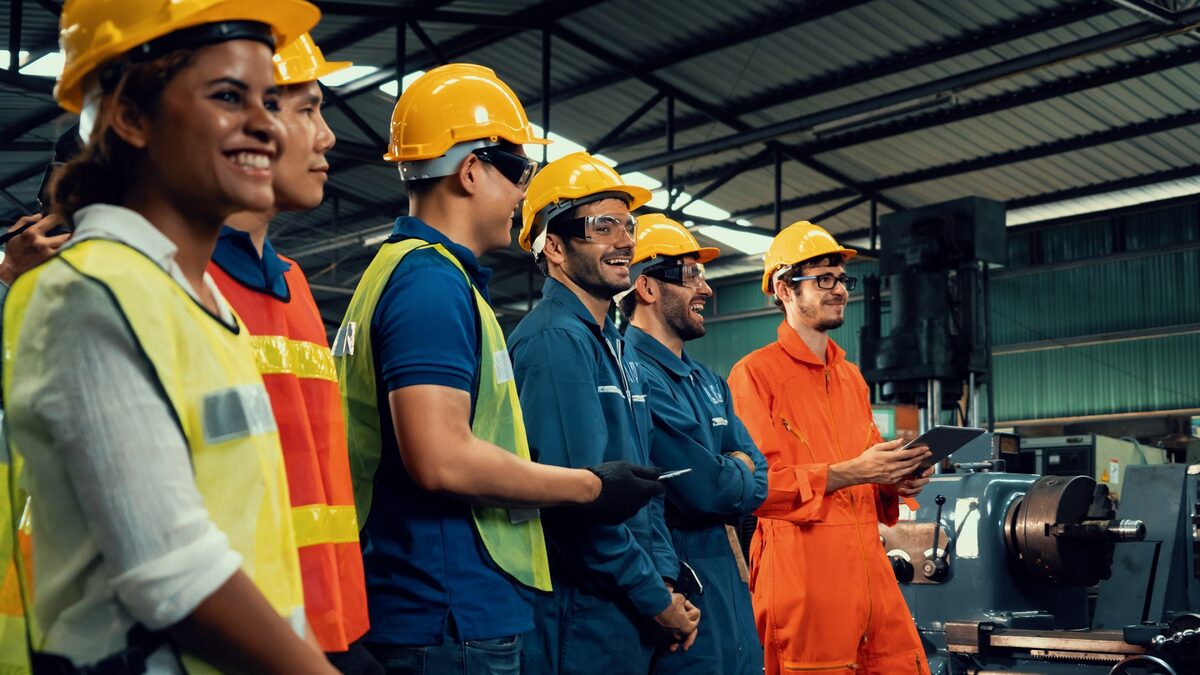
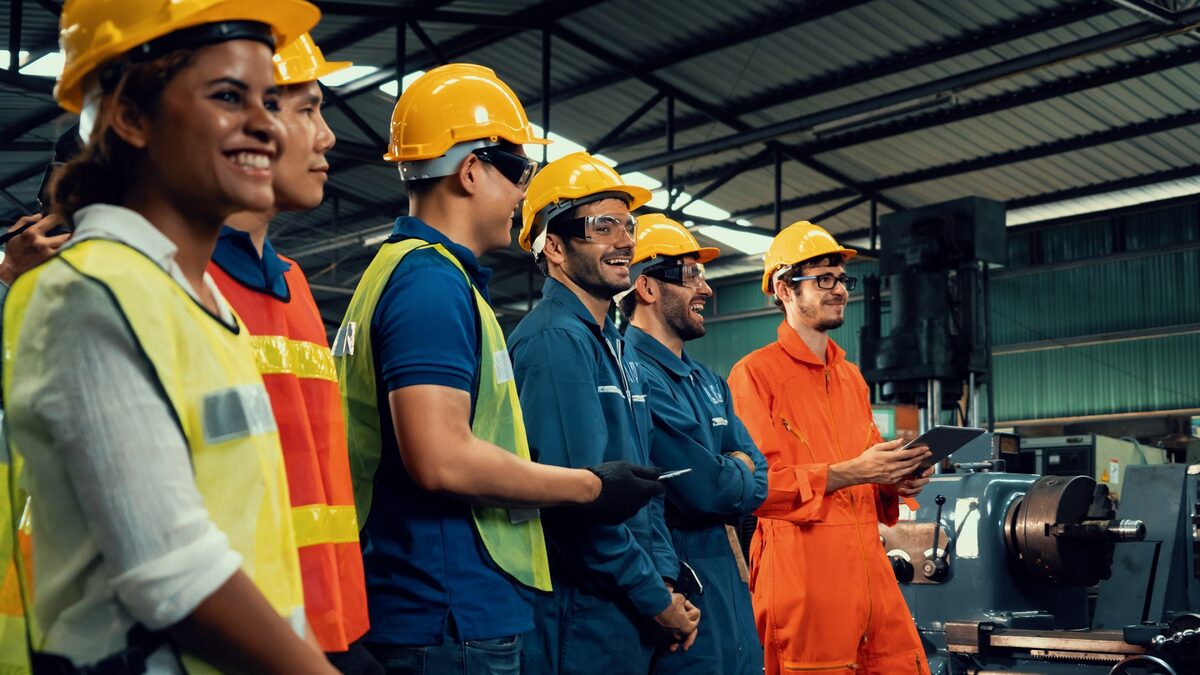
Building & Construction
What Is The Difference Between OSHA Construction And General Industry
Modified: December 7, 2023
Discover the key distinctions between OSHA regulations for building construction and general industry. Stay informed to ensure compliance and keep your workplace safe.
(Many of the links in this article redirect to a specific reviewed product. Your purchase of these products through affiliate links helps to generate commission for Storables.com, at no extra cost. Learn more)
Introduction
Welcome to the world of construction, where buildings rise, bridges span, and infrastructure takes shape. The construction industry is a dynamic and ever-evolving sector, driven by innovation, technology, and the skilled hands of workers. However, with complex projects and inherent risks, safety becomes a paramount concern.
This is where the Occupational Safety and Health Administration (OSHA) steps in. OSHA is a federal agency responsible for ensuring the health and safety of workers across various industries. OSHA sets standards and regulations that employers must adhere to, in order to protect workers from hazardous conditions.
When it comes to construction, OSHA has specific standards in place to address the unique risks and challenges faced by construction workers. Understanding the difference between OSHA construction and general industry standards is crucial for employers, workers, and industry professionals.
In this article, we will explore the similarities and differences between OSHA construction and general industry standards. We will dive into the specific regulations that govern each sector and shed light on the impact they have on employers and workers alike. So, let’s put on our hard hats and embark on this insightful journey.
Key Takeaways:
- OSHA construction standards focus on unique hazards like falls and electrical safety, tailored to the dynamic nature of construction sites. Employers must prioritize specialized training and compliance to ensure worker safety.
- OSHA general industry standards cover common workplace hazards such as machine guarding and ergonomics, applicable across various industries. Employers need to provide comprehensive training and maintain compliance to create a safe work environment.
Overview of OSHA
The Occupational Safety and Health Administration (OSHA) is a federal agency under the United States Department of Labor. Its main objective is to ensure safe and healthy working conditions for employees in various industries. OSHA was established in 1970 under the Occupational Safety and Health Act (OSH Act).
OSHA plays a vital role in preventing workplace injuries, illnesses, and fatalities. The agency develops and enforces regulations that outline safety requirements and standards that employers must follow. OSHA also provides education, training, and assistance programs to help employers and workers understand and comply with these regulations.
OSHA covers a wide range of industries, including construction, manufacturing, healthcare, agriculture, and more. The regulations set forth by OSHA are designed to address the specific hazards and risks associated with each industry, ensuring the well-being of workers across the nation.
One of OSHA’s primary responsibilities is to conduct inspections to ensure compliance with regulations. Inspections can be conducted randomly or in response to complaints, accidents, or referrals. OSHA has the authority to issue citations and penalties for non-compliance, with the goal of encouraging employers to prioritize the safety and health of their workers.
In addition to regulatory enforcement, OSHA offers resources and guidance to employers and workers through its website, training programs, and partnerships with industry organizations. These resources aim to promote knowledge and understanding of workplace safety standards, leading to a safer working environment for all.
Overall, OSHA plays a critical role in safeguarding the well-being of workers in the United States. By setting and enforcing standards, providing education and training, and encouraging a culture of safety, OSHA continues to make significant strides in reducing workplace accidents and ensuring the protection of workers’ rights.
OSHA Construction Industry Standards
The construction industry is known for its unique hazards and risks, which require specific regulations to address them. OSHA has developed a set of standards to protect the safety and health of workers in the construction industry. These standards encompass a broad range of areas, including fall protection, electrical safety, personal protective equipment, and more.
One of the most significant areas covered under OSHA construction standards is fall protection. With workers often working at heights, the risk of falls is a critical concern. OSHA’s standards require employers to provide fall protection systems such as guardrails, safety nets, or personal fall arrest systems to protect employees from falling off elevated surfaces.
Electrical safety is another crucial aspect covered by OSHA construction standards. Construction sites often involve working with electrical equipment and wiring, presenting the potential for electrical hazards. OSHA’s standards outline requirements for electrical safety, including proper grounding, insulation, and lockout/tagout procedures to prevent electrocution and other electrical accidents.
Personal protective equipment (PPE) is also addressed in OSHA construction standards. Construction workers may be exposed to hazards such as flying debris, chemicals, loud noise, or dust. OSHA requires employers to provide appropriate PPE, such as hard hats, safety goggles, ear protection, and respiratory masks, to safeguard workers from these hazards.
In addition to these specific areas, OSHA construction standards also cover topics such as trenching and excavation safety, hazard communication, scaffolding, and machinery safety. These standards aim to ensure that workers have a safe working environment and are protected from the risks associated with construction activities.
It is important for employers in the construction industry to be familiar with and comply with OSHA’s construction standards. This includes conducting regular inspections, providing proper training to workers, maintaining safety records, and correcting any identified hazards or violations. By adhering to these standards, employers can create a culture of safety and protect the well-being of their workers.
OSHA General Industry Standards
While OSHA construction standards focus on the unique hazards and risks of the construction industry, OSHA’s general industry standards apply to a wide range of workplaces, outside of construction. These standards cover various industries, including manufacturing, healthcare, retail, and more.
OSHA’s general industry standards are designed to address common workplace hazards that are not specific to a particular industry. They provide guidance and regulations to ensure the safety and health of workers in these environments. Some of the key areas covered by these standards include hazard communication, machine guarding, respiratory protection, and ergonomics.
Hazard communication is a critical aspect of OSHA’s general industry standards. It requires employers to establish a comprehensive program to communicate information about hazardous substances present in the workplace. This includes proper labeling of hazardous chemicals, providing safety data sheets, and training employees on the potential hazards and proper handling procedures.
Machine guarding is another important area addressed by OSHA’s general industry standards. It focuses on ensuring that machines are properly safeguarded to protect workers from moving parts, rotating equipment, and other machinery hazards. Employers must assess the machinery in their workplace and implement appropriate guards, barriers, or safety devices to prevent accidental contact or entanglement.
Respiratory protection standards outline requirements for employers to protect workers from airborne contaminants. This includes the use of respirators, proper fit testing, medical evaluations, and training on respirator use and maintenance. These standards aim to safeguard the respiratory health of workers who may be exposed to dust, chemicals, fumes, or other harmful substances.
Ergonomics is another significant area covered by OSHA’s general industry standards. It focuses on the design and arrangement of workspaces to optimize human well-being and productivity. Employers are required to assess ergonomic risks in their workplaces and implement appropriate measures to reduce the risk of musculoskeletal disorders and other work-related injuries.
Compliance with OSHA’s general industry standards is essential for employers in non-construction industries. This involves conducting workplace assessments, implementing safety programs, providing training to employees, and maintaining proper records. By adhering to these standards, employers can create a safe and healthy work environment for their employees.
Comparison of OSHA Construction and General Industry Standards
While both OSHA construction and general industry standards aim to protect the safety and health of workers, there are key differences between the two sets of standards. Understanding these differences is crucial for employers and workers to ensure compliance and address industry-specific hazards.
One of the main differences lies in the scope of coverage. OSHA construction standards specifically target hazards and risks that are unique to construction sites, such as falls, electrical safety, and excavation safety. On the other hand, OSHA’s general industry standards have a broader application, covering hazards and regulations applicable to various industries, including manufacturing, healthcare, and retail.
Another difference is the emphasis on specific hazards. OSHA construction standards prioritize hazards that are prevalent in the construction industry, such as falls from heights and electrical accidents. They provide detailed requirements and guidelines related to these hazards to ensure the safety of construction workers. In contrast, OSHA’s general industry standards address more common hazards found in workplaces, including hazard communication, machine guarding, and respiratory protection.
The level of specificity is also different between the two sets of standards. OSHA construction standards often include detailed requirements and specific guidelines tailored to construction activities and equipment. General industry standards, on the other hand, are more general in nature and provide a framework that can be applied across various industries, allowing for flexibility in implementation.
Additionally, the training and compliance requirements may vary between OSHA construction and general industry standards. Construction employers are often required to provide specialized training, such as fall protection and excavation safety, to their workers. General industry employers, on the other hand, may focus on training related to hazard communication, machine operation, and ergonomics, depending on the specific hazards of their industry.
It’s important for employers and workers to understand these differences between OSHA construction and general industry standards. By recognizing the unique hazards and requirements of their industry, employers can tailor their safety programs and training to address industry-specific risks. This will help ensure a safe and healthy working environment for employees and increase overall compliance with OSHA regulations.
When determining whether OSHA construction or general industry standards apply, consider the primary activity being performed at the worksite. Construction standards typically apply to the construction, alteration, and repair of structures, while general industry standards apply to all other industries and activities.
Key Differences between OSHA Construction and General Industry
When it comes to workplace safety, OSHA construction and general industry standards have some key differences that employers and workers need to be aware of. These differences stem from the unique hazards and characteristics of each industry. Let’s explore these differences in more detail.
1. Scope of Coverage: OSHA construction standards specifically target hazards and risks found on construction sites, such as falls from heights, excavation, and electrical safety. In contrast, OSHA’s general industry standards apply to a wide range of industries, covering hazards that are common across different workplaces, like machine guarding, hazard communication, and ergonomics.
2. Specific Regulations: OSHA construction standards provide more detailed and industry-specific regulations compared to general industry standards. Construction standards often include specific requirements for activities like scaffolding, crane operations, and trenching. General industry standards, though also comprehensive, are more broadly applicable, offering flexible guidelines that can be adapted to different workplaces.
3. Emphasis on Hazards: OSHA construction standards prioritize hazards that are prevalent in the construction industry, such as falls, struck-by hazards, and caught-in/between hazards. General industry standards, on the other hand, address hazards that can occur in various industries, including chemical exposures, machine hazards, and ergonomic risks.
4. Training Requirements: Due to the unique risks involved in construction, OSHA construction standards often require specialized training for workers. This includes specific training on fall protection, excavation safety, and the proper use of heavy machinery. General industry standards focus on broader training topics, such as hazard communication, machine operation, and ergonomics.
5. Worksite Dynamics: Construction sites are typically dynamic and ever-changing, with multiple contractors and subcontractors working together. OSHA construction standards encompass regulations that address coordination between employers and ensure the safety of all workers on the site. General industry standards, while still accounting for dynamic work environments, may require different approaches to address the specific needs of individual industries.
Understanding these key differences between OSHA construction and general industry standards is crucial for employers to develop effective safety programs and ensure compliance. By recognizing the unique hazards and regulations applicable to their industry, employers can create a safer work environment and protect the well-being of their workers.
Impact on Employers and Workers
OSHA construction and general industry standards have a significant impact on both employers and workers. Understanding the implications of these standards is crucial for creating a safe and healthy work environment. Let’s explore the impact on employers and workers in more detail.
Employers:
- Legal Compliance: Employers are legally obligated to comply with OSHA standards, whether in the construction industry or general industry. Failure to comply can result in penalties, citations, and potential legal issues.
- Financial Consequences: Non-compliance with OSHA standards can lead to financial implications, including fines and potential lawsuits. Providing a safe work environment not only avoids these costs but also reduces workers’ compensation claims and boosts overall productivity.
- Reputation and Brand Image: Employers who prioritize worker safety and adhere to OSHA standards build a positive reputation and enhance their brand image. This attracts talented professionals, improves employee morale, and can lead to increased customer trust and loyalty.
- Worker Retention and Recruitment: By demonstrating a commitment to safety through compliance with OSHA standards, employers can improve worker retention and attract new employees who prioritize their own safety.
- Productivity and Efficiency: Adhering to OSHA standards promotes a safer and healthier work environment, reducing accidents, injuries, and illnesses. This, in turn, increases productivity, efficiency, and overall business performance.
Workers:
- Enhanced Safety: OSHA standards play a vital role in protecting workers from hazards and creating a safe work environment. Compliance with these standards ensures that workers are provided with the necessary safety measures, reducing the risk of accidents and injuries.
- Increased Awareness: OSHA standards require employers to provide training and education to workers, enhancing their knowledge of workplace safety practices and potential hazards.
- Empowerment: Workers who are aware of their rights and OSHA standards can confidently advocate for their own safety. This empowers them to speak up about potential hazards, report violations, and actively participate in safety programs.
- Health and Well-being: By complying with OSHA standards, employers promote the well-being of workers by addressing potential health risks, ensuring the use of personal protective equipment, and providing proper training to prevent work-related illnesses.
- Quality of Life: Adhering to OSHA standards can significantly impact the quality of life for workers. By minimizing workplace injuries and illnesses, workers can enjoy improved physical and mental well-being both on and off the job.
Overall, the impact of OSHA construction and general industry standards on both employers and workers is substantial. Compliance with these standards leads to a safer work environment, improved productivity, reduced costs, and enhanced overall well-being for everyone involved.
Training and Compliance Requirements
Training and compliance with OSHA standards are essential for employers and workers to maintain a safe and healthy work environment. OSHA has established specific training and compliance requirements to ensure that employers and workers are equipped with the necessary knowledge and skills to prevent workplace accidents and injuries. Let’s explore these requirements in more detail.
Training Requirements:
- OSHA 10-Hour and 30-Hour Training: OSHA requires certain workers, particularly in the construction industry, to complete the OSHA 10-Hour or 30-Hour training programs. These programs provide comprehensive training on workplace hazards, safety practices, and OSHA regulations.
- Industry-Specific Training: Employers are responsible for providing industry-specific training to their workers to address the unique hazards and risks related to their work. This may include training on fall protection, electrical safety, machine operation, chemical handling, and more.
- Hazard Communication Training: OSHA’s Hazard Communication Standard requires employers to provide training to workers on the handling and use of hazardous chemicals present in the workplace. The training should cover information on labels, safety data sheets, and proper procedures to protect against chemical hazards.
- Respiratory Protection Training: Employers must provide training to workers who are required to wear respiratory protection equipment. This training includes proper selection of respirators, fit testing, maintenance, and storage procedures.
- Ergonomics Training: Employers should provide ergonomics training to workers, focusing on proper body mechanics, posture, and techniques to prevent musculoskeletal disorders resulting from repetitive tasks and poor workplace ergonomics.
Compliance Requirements:
- Written Safety Programs: Employers must develop and implement written safety programs that outline policies, procedures, and safety guidelines specific to their industry. These programs should address hazards, emergency response plans, recordkeeping, and compliance with OSHA standards.
- Recordkeeping: Employers are required to maintain accurate records of workplace injuries, illnesses, and safety training. These records help to track incidents, identify trends, and assess the effectiveness of safety programs.
- Regular Inspections: Employers should conduct regular inspections of the workplace to identify and address potential hazards. Inspections help to ensure that work environments are safe, equipment is properly maintained, and workers are adhering to safety protocols.
- Correcting Violations: If violations of OSHA standards are identified during inspections, employers are required to promptly address and correct them. This may involve implementing necessary safety measures, providing additional training, or modifying work processes.
- Cooperation with OSHA Inspections: If selected for an OSHA inspection, employers should cooperate fully with OSHA officials. This includes providing access to the workplace, facilitating interviews with workers, and sharing necessary documentation.
Compliance with training and OSHA standards not only ensures the safety of workers but also helps employers avoid penalties, reduce accidents, and maintain a positive workplace culture. By providing comprehensive training, implementing effective safety programs, and regularly assessing compliance, employers can create a work environment where safety is a top priority.
Conclusion
Ensuring the safety and well-being of workers is of utmost importance in any industry, and OSHA construction and general industry standards play a crucial role in achieving this goal. These standards provide a framework for employers to create a safe and healthy work environment, while also empowering workers to advocate for their own safety.
OSHA construction standards address the unique hazards and risks found on construction sites, such as falls, electrical safety, and excavation. On the other hand, OSHA’s general industry standards cover a wide range of industries and focus on more common workplace hazards like machine guarding, hazard communication, and ergonomics.
Compliance with OSHA standards not only fulfills legal requirements but also has a positive impact on employers and workers alike. Employers who prioritize safety benefit from improved productivity, a positive reputation, and reduced costs associated with accidents and injuries. Workers, in turn, enjoy a safer work environment, enhanced awareness of potential hazards, and improved overall well-being.
Meeting the training and compliance requirements set forth by OSHA is essential. Employers must provide industry-specific training to equip workers with the knowledge and skills necessary to mitigate risks and prevent accidents. Regular inspections, recordkeeping, and correction of identified violations are crucial for maintaining compliance and addressing potential hazards in the workplace.
In conclusion, OSHA construction and general industry standards serve as essential guidelines for employers and workers to promote a culture of safety and protect against workplace hazards. By understanding these standards, fulfilling training requirements, and ensuring compliance, employers can create a work environment that prioritizes the safety, health, and well-being of their most valuable asset – their workers.
Frequently Asked Questions about What Is The Difference Between OSHA Construction And General Industry
Was this page helpful?
At Storables.com, we guarantee accurate and reliable information. Our content, validated by Expert Board Contributors, is crafted following stringent Editorial Policies. We're committed to providing you with well-researched, expert-backed insights for all your informational needs.
0 thoughts on “What Is The Difference Between OSHA Construction And General Industry”