Home>diy>Building & Construction>What Are The OSHA Standards For Construction And General Industry
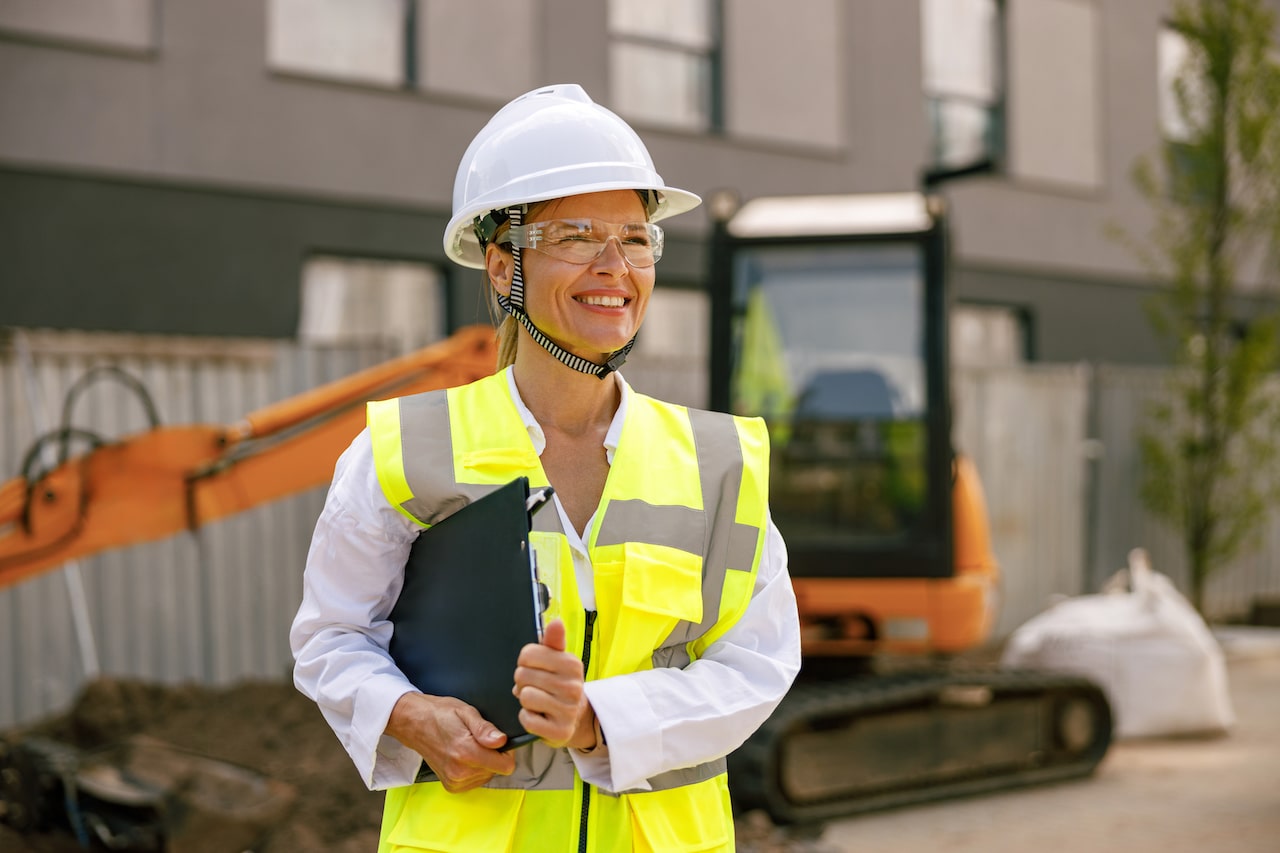
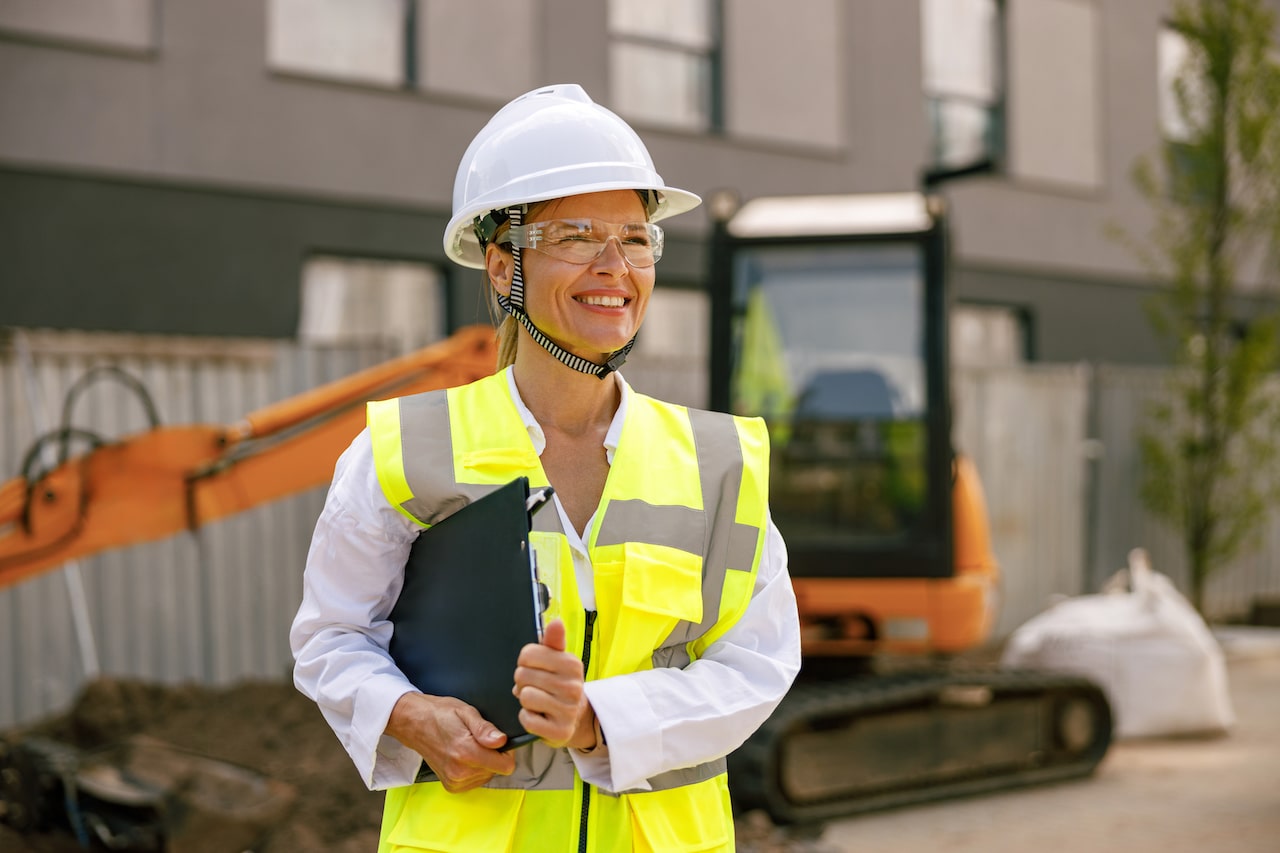
Building & Construction
What Are The OSHA Standards For Construction And General Industry
Modified: January 23, 2024
Learn about the OSHA standards for construction and general industry, including safety regulations and guidelines for building construction.
(Many of the links in this article redirect to a specific reviewed product. Your purchase of these products through affiliate links helps to generate commission for Storables.com, at no extra cost. Learn more)
Introduction
Construction is an essential industry that plays a vital role in shaping our cities and communities. However, the nature of construction work also poses significant risks and hazards to workers. To ensure the safety and well-being of construction workers, the Occupational Safety and Health Administration (OSHA) has established comprehensive standards that are designed to protect employees in the construction industry.
OSHA is a regulatory agency under the United States Department of Labor responsible for enforcing workplace safety and health regulations. Their mission is to prevent work-related injuries, illnesses, and fatalities by setting and enforcing standards and providing training, outreach, education, and assistance to employers and workers.
OSHA standards cover a wide range of areas in construction and general industry, including hazard identification and prevention, training and education, recordkeeping, and personal protective equipment. These standards are crucial for ensuring that construction sites are safe and compliant with regulations to protect workers from potential hazards.
In this article, we will explore the OSHA standards for the construction and general industry, highlighting key regulations and requirements that employers and workers need to be aware of to maintain a safe working environment.
Key Takeaways:
- Prioritizing OSHA standards in the construction and general industry is crucial for creating a culture of safety, minimizing workplace hazards, and protecting the well-being of employees through comprehensive safety measures and regular compliance.
- Employers must proactively assess workplaces, provide thorough training, maintain accurate records, and implement specific safety measures such as hazard communication, PPE, fall protection, electrical safety, machine guarding, and respiratory protection to ensure a secure and healthy working environment.
OSHA Standards Overview
The OSHA standards are a set of guidelines and regulations that employers in the construction and general industry must follow to ensure the safety and health of their workers. These standards are based on extensive research, industry best practices, and input from experts in the field. By adhering to these standards, employers can create a work environment that minimizes the risk of accidents, injuries, and illnesses.
OSHA standards are designed to address various aspects of workplace safety and health, including hazard communication, personal protective equipment (PPE), fall protection, electrical safety, machine guarding, respiratory protection, and many others. They provide specific requirements that employers must follow to protect their employees, and failure to comply can result in penalties and fines.
It is important to note that OSHA standards are not static; they are regularly updated and revised to address emerging issues and advancements in technology and best practices. Therefore, it is crucial for employers to stay informed about any changes or updates to the standards that may affect their operations.
Furthermore, OSHA standards are enforced through regular inspections conducted by OSHA compliance officers. These inspections can be triggered by various events, such as complaints from employees or reports of workplace incidents. During an inspection, the officer will assess the employer’s compliance with the applicable standards, identify any violations, and provide recommendations for corrective actions.
Moreover, OSHA encourages employers to go beyond mere compliance and strive for continuous improvement in their safety and health programs. This can be achieved through regular training and education, hazard assessments, employee involvement and feedback, and a proactive approach to identifying and mitigating workplace hazards.
In the following sections, we will delve into the specific OSHA standards for the construction industry and general industry, providing an overview of key regulations and requirements that employers and workers need to be familiar with to maintain a safe and compliant workplace.
Construction Industry Standards
OSHA has developed specific standards for the construction industry to address the unique hazards and risks associated with construction work. These standards cover a wide range of areas, including fall protection, electrical safety, excavation and trenching, scaffolding, and more.
One of the most critical standards in the construction industry is the Fall Protection standard (29 CFR 1926.501), which requires employers to provide fall protection systems to workers who are exposed to fall hazards of six feet or more. This standard includes provisions for guardrail systems, safety net systems, and personal fall arrest systems.
Another essential standard is the Electrical Safety standard (29 CFR 1926.400), which addresses electrical hazards in construction work. It requires employers to implement safety measures such as grounding, guarding, and using personal protective equipment to protect workers from electrocution and other electrical-related accidents.
The Excavation and Trenching standard (29 CFR 1926.650) sets requirements for safely excavating and working in trenches. It covers topics such as protective systems, cave-in protection, access and egress, and hazard assessments to prevent accidents and injuries related to trenching activities.
Scaffolding is commonly used in construction work, and the Scaffold standard (29 CFR 1926.451) provides guidelines for the safe installation, use, and dismantling of scaffolding systems. It includes requirements for proper construction, fall protection, and inspections to ensure the stability and integrity of the scaffold.
Other construction industry standards include the Respiratory Protection standard (29 CFR 1926.103), which addresses the use of respiratory protection when workers are exposed to hazardous substances or environments, and the Hazard Communication standard (29 CFR 1926.59), which requires employers to train workers on the hazards of chemicals used in the construction industry.
These are just a few examples of the OSHA standards that apply specifically to the construction industry. Employers in the construction field must familiarize themselves with these standards, implement appropriate safety measures, and train their workers to ensure compliance and promote a safe working environment.
General Industry Standards
In addition to the construction industry standards, OSHA has established a comprehensive set of standards that apply to various industries outside of construction. These standards, known as the General Industry standards, cover a wide range of workplace safety and health topics applicable to most workplaces, including manufacturing, healthcare, retail, and service industries.
One of the fundamental General Industry standards is the Hazard Communication standard (29 CFR 1910.1200), also known as the “Right-to-Know” standard. This standard requires employers to provide information and training to employees regarding the hazardous chemicals present in the workplace. It includes requirements for labeling of containers, safety data sheets, and written hazard communication programs.
The Personal Protective Equipment (PPE) standard (29 CFR 1910.132) is another critical standard that applies to all workplaces. It mandates that employers assess the workplace for hazards, provide necessary PPE to employees, and ensure proper use and maintenance of the equipment. Examples of PPE include safety glasses, gloves, helmets, and respiratory protection.
The Lockout/Tagout standard (29 CFR 1910.147) addresses the control of hazardous energy during maintenance and servicing of machines and equipment. It requires employers to develop and implement detailed procedures to isolate and prevent the release of hazardous energy sources, protecting workers from unexpected startups and other accidents.
The Electrical Safety standard (29 CFR 1910.303) for general industry provides guidelines for the safe use of electrical equipment and installations. It covers topics such as guarding of live parts, grounding of electrical systems, and protection against electric shock hazards, helping to prevent electrical accidents and injuries in the workplace.
Additionally, other General Industry standards address specific hazards such as machine guarding (29 CFR 1910.212), which requires employers to install and maintain safeguards on machines to prevent injuries from moving parts, and the Respiratory Protection standard (29 CFR 1910.134), which focuses on the proper use and protection of workers from airborne contaminants.
These are just a few examples of the many General Industry standards that employers in non-construction-related industries must comply with. It is essential for employers to identify the specific standards applicable to their industry and work activities and ensure full compliance to provide a safe and healthy workplace for their employees.
OSHA Inspections and Compliance
Ensuring compliance with OSHA standards is essential for maintaining a safe and healthy work environment. OSHA conducts inspections to enforce compliance and identify any violations of the standards. These inspections can be scheduled or unannounced, and they are performed by OSHA compliance officers who have the authority to enter workplaces and assess compliance with the applicable standards.
OSHA inspections can be triggered by various reasons, including employee complaints, reports of workplace incidents or fatalities, or randomly selected high-risk industries or workplaces. The goal of these inspections is to identify hazards, assess the effectiveness of safety measures, and ensure that employers are taking appropriate steps to protect their workers.
During an inspection, the OSHA compliance officer will typically follow a standardized process. This includes an opening conference with the employer, where the purpose of the inspection is explained, and the officer will request certain documentation, such as injury and illness records, safety and training programs, and safety data sheets.
After the opening conference, the compliance officer will conduct a walkthrough of the workplace, inspecting various areas, equipment, and processes to identify potential hazards. They will also interview employees to gather information about their work tasks, training, and any concerns they may have regarding safety and health conditions.
If violations of the OSHA standards are identified during the inspection, the compliance officer will issue citations and propose penalties, if applicable. Employers then have the opportunity to respond and address the violations by either complying with the standards, negotiating with OSHA, or contesting the citations if they believe they are unwarranted.
It’s important for employers to understand the OSHA inspection process and to proactively ensure compliance with the applicable standards to minimize the risk of citations, penalties, and, most importantly, to protect the safety and well-being of their workers.
By implementing a strong safety and health program, conducting regular self-audits and inspections, and addressing any identified hazards promptly, employers can demonstrate a commitment to workplace safety and maintain compliance with OSHA standards.
Read more: What Is OSHA In Construction
Training and Education Requirements
Training and education play a crucial role in ensuring the safety and well-being of workers. OSHA has specific requirements for employers to provide training to employees on various topics related to workplace hazards and safe work practices.
Employers are responsible for identifying the training needs specific to their workplace and job tasks. They must develop and implement a comprehensive training program to address these needs. The training should be provided to both new employees and existing employees when new hazards are introduced or when changes occur in work processes, equipment, or procedures.
Some of the key training requirements as outlined by OSHA include:
-
Hazard Communication: Employers must provide training to employees regarding the hazards of chemicals they may be exposed to, how to interpret and understand safety data sheets and labels, and the proper use of personal protective equipment related to hazardous chemicals.
-
Fall Protection: If employees are exposed to fall hazards, employers must provide training on how to recognize and avoid fall hazards, proper use of fall protection systems, and procedures for rescue in the event of a fall.
-
Electrical Safety: Workers who may be exposed to electrical hazards must be trained in electrical safety practices, including how to recognize and avoid electricity-related risks, proper use of electrical equipment and devices, and procedures for de-energizing and locking out/tagging out equipment.
-
Machine Guarding: Employees who operate or work near machinery must receive training on the hazards associated with machine operation, proper use of machine guards, and safe work practices to prevent injuries.
-
Respiratory Protection: When workers are required to use respiratory protection due to exposure to hazardous substances or environments, employers must provide training on the use, limitations, and maintenance of respiratory protective equipment, as well as proper fit-testing procedures.
It’s important for employers to ensure that the training provided is effective and tailored to the specific needs of their employees and workplace. This includes using appropriate instructional methods, materials, and resources, as well as evaluating the effectiveness of the training through assessments and feedback from employees.
By prioritizing training and providing ongoing education, employers can empower their employees to understand and mitigate the risks associated with their work, fostering a culture of safety and reducing the likelihood of accidents, injuries, and illnesses in the workplace.
Recordkeeping and Reporting
Recordkeeping and reporting are essential aspects of OSHA compliance that help employers track workplace injuries, illnesses, and incidents, as well as identify trends and areas for improvement. OSHA requires employers to maintain specific records and report certain events to ensure transparency and accountability in promoting workplace safety and health.
Employers are required to keep records of work-related injuries and illnesses using the OSHA Form 300, the Log of Work-Related Injuries and Illnesses. This form must be completed for each recordable injury or illness, and it includes information such as the nature of the injury or illness, the date it occurred, the affected body part, and the number of days away from work. The information on the OSHA Form 300 helps employers analyze trends and identify areas for improvement in their safety programs.
Additionally, employers must also prepare an Annual Summary, known as the OSHA Form 300A, which provides a summary of the total number of recordable injuries and illnesses for the year and is displayed in a prominent location in the workplace. This summary must be completed and posted from February 1st to April 30th of each year to inform employees and others about the safety performance of the workplace.
In certain cases, employers may be required to report specific incidents to OSHA. Severe injuries such as hospitalizations, amputations, or fatalities must be reported to OSHA within 8 hours of the incident. This can be done by phone or through OSHA’s online reporting system.
Furthermore, employers must also maintain records of employee exposure to toxic substances or harmful agents, medical records related to workplace hazards, and certain training records, including documentation of training conducted on specific hazards and the names and qualifications of trainers.
Accurate recordkeeping and reporting are crucial for employers to assess the effectiveness of their safety programs, identify problem areas, and take proactive measures to prevent future incidents. It also enables OSHA to analyze injury and illness data to target their enforcement efforts and develop effective safety standards.
Employers should ensure that their recordkeeping and reporting processes comply with OSHA requirements. This includes proper documentation, timely reporting of incidents, and adequate maintenance of records for the required period (five years) to demonstrate compliance and facilitate future analysis and review.
By maintaining accurate records and reporting incidents as required, employers can contribute to a safer work environment and support OSHA’s efforts to protect workers from hazards and improve overall workplace safety.
Always ensure that you are familiar with the OSHA standards for construction and general industry to maintain a safe work environment and avoid potential violations.
Hazard Communication
Hazard communication is a critical aspect of workplace safety and is governed by OSHA’s Hazard Communication Standard (HCS), also known as the “Right-to-Know” standard. The purpose of this standard is to ensure that employers and employees are aware of the hazards associated with the chemicals they work with and the necessary precautions to protect themselves.
The Hazard Communication Standard requires employers to develop and implement a comprehensive written program that includes information about hazardous chemicals present in the workplace, along with the necessary measures to communicate the hazards to employees.
One of the key components of the Hazard Communication Standard is proper labeling of containers. Employers must ensure that containers of hazardous chemicals are labeled with appropriate hazard warnings, including the identity of the chemical, signal words (such as “Danger” or “Warning”), pictograms, and precautionary statements. This labeling allows employees to quickly identify the potential hazards associated with a particular chemical.
Employees must also have access to Safety Data Sheets (SDS) for all hazardous chemicals they may be exposed to. The SDS provides detailed information about the hazards, safe handling procedures, protective measures, and emergency response protocols for each chemical. Employers are responsible for ensuring that SDSs are readily available, easily accessible, and properly organized.
Training is a crucial aspect of hazard communication. Employers must provide employees with information and training on hazardous chemicals in their work area, including the hazards associated with those chemicals, how to read and interpret labels, and how to access and use SDSs. Employees should be trained on safe handling, storage, and disposal of hazardous chemicals, as well as the appropriate personal protective equipment (PPE) to use when working with hazardous substances.
A comprehensive hazard communication program ensures that employees are aware of the potential hazards they may encounter in the workplace, and empowers them to take necessary precautions to protect themselves and their colleagues. By promoting effective communication of hazards, employers can significantly reduce the risk of chemical-related accidents, injuries, and illnesses.
In summary, the Hazard Communication Standard requires employers to:
- Properly label containers of hazardous chemicals.
- Provide access to Safety Data Sheets (SDS).
- Conduct training on hazardous chemicals, including safe handling and storage.
By proactively implementing a robust hazard communication program, employers can ensure that their employees have the knowledge and tools to work safely in environments where hazardous chemicals are present.
Personal Protective Equipment (PPE)
Personal Protective Equipment (PPE) is equipment worn by workers to minimize exposure to hazards that can cause injuries or illnesses in the workplace. The use of PPE is an important control measure, as it acts as a last line of defense when other safety measures alone cannot eliminate or adequately reduce the risk.
OSHA requires employers to assess the workplace for potential hazards and provide appropriate PPE to employees. The selection of PPE should be based on the nature of the work, the hazards present, and the specific needs of the employee. Employers are also responsible for ensuring that employees receive proper training on the use, maintenance, and limitations of the PPE provided.
PPE can encompass a wide range of equipment, including:
- Eye and Face Protection: Safety glasses, goggles, or face shields protect against eye and face hazards, including flying objects, chemical splashes, or radiation.
- Head Protection: Hard hats protect against head injuries caused by falling objects, electrical hazards, or bumping into objects. Different types of hard hats are available for specific hazards.
- Hearing Protection: Earplugs or earmuffs are used to protect against excessive noise levels that can cause hearing loss. Employers must conduct noise assessments to determine when hearing protection is required.
- Respiratory Protection: Respirators protect against harmful airborne substances, such as gases, particles, or fumes. Employers must establish respiratory protection programs and train employees on proper use, maintenance, and storage of respirators.
- Hand Protection: Gloves are used to protect hands from cuts, burns, chemical exposures, or other hazards. The appropriate type of gloves depends on the specific task and the substances or materials being handled.
- Foot Protection: Safety shoes or boots provide protection against foot injuries caused by falling objects, punctures, electrical hazards, or slippery surfaces. Different footwear options are available for various workplace environments.
- Body Protection: Protective clothing, such as coveralls, aprons, or protective suits, shield the body from hazards like chemicals, heat, flames, or biological agents.
It is crucial for employers to ensure that PPE is properly selected, maintained, and used by employees. Employers must conduct regular assessments to verify that the PPE is appropriate for the hazards present in the workplace and that it fits each employee correctly. Employees should also receive training on how to inspect, don, doff, adjust, and use PPE correctly.
While PPE is an important safety measure, it is vital to remember that it should be used in conjunction with other control measures, such as engineering controls (e.g., guards, ventilation) and administrative controls (e.g., training, work procedures) to create a comprehensive approach to workplace safety.
By implementing a robust PPE program and ensuring that employees are appropriately equipped and trained, employers can significantly reduce the risk of workplace injuries and illnesses, creating a safer and healthier work environment for all.
Read more: What Is The Construction Industry
Fall Protection
Falls are one of the leading causes of serious injuries and fatalities in the workplace, particularly in the construction industry. To prevent fall-related accidents, OSHA has established specific regulations and requirements for fall protection in various work environments.
The Fall Protection Standard (29 CFR 1926.501) applies to the construction industry and mandates that employers provide fall protection systems to employees who are exposed to fall hazards. The standard requires employers to assess the work site to identify fall hazards, implement measures to eliminate or minimize these hazards, and provide appropriate fall protection systems when hazards cannot be eliminated.
Some essential fall protection measures and systems include:
- Guardrail Systems: Employers should install guardrail systems along open edges, roofs, and elevated platforms to prevent falls. Guardrails should be able to withstand a force of at least 200 pounds applied within 2 inches of the top edge.
- Safety Net Systems: Safety nets can be used as a means of fall protection to catch workers who may fall from elevated surfaces. They should be installed below the working area and positioned to prevent the worker from hitting the ground or lower levels.
- Personal Fall Arrest Systems: A personal fall arrest system typically includes an anchorage, a full-body harness, a lanyard or lifeline, and may also include a deceleration device. It is designed to stop a fall and minimize the forces on the body if a fall occurs.
- Warning Line Systems: Warning lines, consisting of ropes or wires with flags, can be used in specific situations to warn workers that they are approaching an unprotected edge. This system is typically used on low-slope roofs with a low risk of falls.
- Controlled Access Zones: Controlled access zones are designated areas where only authorized workers are allowed to enter and perform work near an unprotected edge. These areas are demarcated with barriers such as ropes or tapes.
Employers must also ensure that employees receive proper training on the use of fall protection systems, including how to inspect and don equipment, how to recognize fall hazards, and the procedures for working safely at heights. Training should also cover the limitations of the fall protection systems and the importance of proper anchor point selection.
It’s crucial for employers to regularly inspect fall protection equipment and systems to ensure their effectiveness and integrity. Employees should also be encouraged to report any issues or malfunctions promptly to prevent accidents.
By implementing comprehensive fall protection measures, providing appropriate training, and ensuring regular inspections and maintenance, employers can significantly reduce the risk of falls in the workplace, safeguarding the well-being of their employees.
Electrical Safety
Electrical hazards pose a significant risk in many workplaces and can result in severe injuries or even fatalities. To mitigate these risks, OSHA has established specific regulations and standards to ensure electrical safety in the workplace.
The Electrical Safety Standard (29 CFR 1910.303) applies to general industry and provides guidelines for the safe use of electrical equipment and installations. It covers a broad range of electrical hazards, including electric shock, electrocution, fires, and explosions.
Employers are responsible for ensuring that electrical systems and equipment are in compliance with the established standards and that employees are properly trained on electrical safety practices. Some key requirements and best practices for electrical safety include:
- Electrical System Maintenance: Regular inspections, testing, and maintenance of electrical systems are essential to identify and address potential hazards. This includes checking for frayed wires, damaged cords, loose connections, and ensuring the integrity of protective equipment.
- Lockout/Tagout Procedures: When servicing or maintaining electrical systems or equipment, employers must implement lockout/tagout procedures to prevent the accidental or unexpected startup of machines or equipment. This involves isolating the energy source, locking and tagging it, and verifying that the equipment is de-energized before work begins.
- Proper Grounding: Grounding electrical systems and equipment helps prevent electrical shock by providing a safe path for electrical current. Employers must ensure that all electrical systems, tools, and equipment are properly grounded and regularly inspected for grounding continuity.
- Safe Work Practices: Employees should be trained on safe work practices, such as de-energizing equipment before working on it, using appropriate personal protective equipment (PPE), and properly handling and storing electrical equipment.
- Electrical Safety Training: Employers must provide comprehensive training to employees on electrical safety practices, including recognizing electrical hazards, proper use of electrical equipment, and emergency response procedures in the event of an electrical incident.
- Electrical Protective Devices: Employers should provide and ensure the proper use of personal protective equipment (PPE), such as insulated gloves, face shields, and arc flash protective clothing, when working on or near energized electrical equipment or systems.
By following these electrical safety practices and ensuring compliance with OSHA standards, employers can significantly reduce the risk of electrical accidents and injuries in the workplace. Regular inspections and maintenance, employee training, and proper use of protective equipment play a crucial role in creating a safe and secure work environment when working with or near electrical systems.
It is important for employers to stay updated with the latest electrical safety standards and best practices to protect their employees and maintain a safe workplace.
Machine Guarding
Machine guarding is a crucial aspect of workplace safety, as it helps prevent workers from coming into contact with hazardous machine parts, such as rotating blades, gears, and moving components. The OSHA standard for machine guarding (29 CFR 1910.212) provides guidelines to protect workers from potential injuries and ensure machine safety.
The machine guarding standard requires employers to assess machinery in the workplace and implement guards or protective devices to prevent accidental contact with hazardous machine parts. Here are some key elements of machine guarding:
- Point of Operation Guards: Guards must be in place to prevent workers from reaching into the point of operation, where the machine performs its intended function. These guards should provide a physical barrier to protect employees from coming into contact with moving parts.
- Power Transmission Guards: Machinery with power transmission components, such as belts, pulleys, and chains, must have guards to prevent accidental contact. These guards should cover the hazardous areas and prevent workers from getting entangled in the moving parts.
- Safeguarding Devices: In addition to physical guards, machine safeguarding devices such as presence-sensing devices, two-hand controls, or barrier guards can be used to enhance the safety of machine operations. These devices help to stop or prevent machine operation when workers are in the danger zone.
- Training and Education: Employers must provide training to workers on the importance of machine guarding, how to recognize machine hazards, and the safe operation and maintenance of machinery. Proper training promotes awareness and ensures that workers understand the potential risks and how to protect themselves.
- Maintenance and Inspection: Regular maintenance and inspections of machines and guards are necessary to ensure their effectiveness. Employers should establish procedures to routinely inspect machine guards, repair or replace any damaged or missing guards, and address any issues promptly to maintain a safe working environment.
Failure to properly guard machinery can lead to severe injuries, such as amputations, fractures, or lacerations. Employers must prioritize machine guarding measures and ensure that workers are protected from hazardous machine components.
Furthermore, it’s important to involve employees in the machine guarding process. Workers should be encouraged to report any concerns or hazards related to machine safety and actively participate in ongoing safety improvement initiatives.
By implementing effective machine guarding measures, providing appropriate training, and conducting regular inspections and maintenance, employers can create a safer workplace environment, reduce the risk of machine-related injuries, and protect the well-being of their workers.
Respiratory Protection
Respiratory protection is a critical aspect of workplace safety, especially in environments where employees may be exposed to hazardous substances or airborne contaminants. The OSHA Respiratory Protection Standard (29 CFR 1910.134) sets guidelines to ensure that workers are protected from respiratory hazards and that employers provide appropriate respiratory protection.
The Respiratory Protection Standard applies to various industries and requires employers to assess respiratory hazards in the workplace, implement controls to minimize exposures, and provide employees with suitable respiratory protection when necessary.
Here are key elements of respiratory protection:
- Hazard Assessments: Employers must conduct assessments to identify potential respiratory hazards in the workplace. This includes evaluating airborne contaminants, monitoring exposure levels, and determining the appropriate respiratory protection based on the identified hazards.
- Respiratory Protection Program: Employers must develop and implement a written respiratory protection program that outlines procedures for selecting and using appropriate respirators, medical evaluations, fit testing, training, and maintenance of respirators. The program should be regularly reviewed and updated as needed.
- Respirator Selection: The type of respirator selected should be suitable for the identified hazards and the level of protection required. There are different types of respirators available, including disposable respirators, half-face respirators, and powered air-purifying respirators (PAPRs). It is crucial to select the correct respirator for the specific hazards in the workplace.
- Training and Fit Testing: Employers must provide comprehensive training on the proper use, limitations, maintenance, and storage of respirators. Employees should also undergo fit testing to ensure that the respirator fits properly and forms a secure seal, as any gaps can compromise its effectiveness.
- Medical Evaluations: Before using a respirator, employees must undergo a medical evaluation to assess their ability to wear a respirator safely. This evaluation helps identify any health conditions that may interfere with the use of a respirator.
- Regular Maintenance and Inspection: Respirators need to be regularly maintained and inspected to ensure they are clean, functional, and free from defects. This includes proper storage, cleaning, disinfection, and regular inspection of all components.
Employers are also responsible for establishing procedures to address emergency situations, such as malfunctioning respirators or unexpected exposures. These procedures should include rescue plans and protocols for immediate response.
By adhering to the Respiratory Protection Standard, employers can protect their employees from harmful airborne substances and create a safer and healthier workplace. Implementing a comprehensive respiratory protection program that includes thorough hazard assessments, proper respirator selection, comprehensive training, regular maintenance, and clear emergency procedures is crucial for maintaining effective respiratory protection.
Read more: What Is The Future Of Construction Industry
Conclusion
In the construction and general industry, adherence to OSHA standards is crucial for maintaining a safe and healthy work environment. The OSHA standards cover a wide range of topics, including fall protection, electrical safety, machine guarding, respiratory protection, hazard communication, and more. By complying with these standards, employers can protect their workers from potential hazards and reduce the risk of accidents, injuries, and illnesses.
OSHA inspections and compliance play a significant role in ensuring workplace safety. Employers should proactively assess their workplaces, implement necessary safety measures, and maintain proper documentation and reporting systems to demonstrate compliance with OSHA standards. Engaging in regular training and education for employees highlights the importance of safety and equips workers with the knowledge and skills to identify and mitigate workplace hazards.
Recordkeeping and reporting are critical components of OSHA compliance. Employers must maintain accurate records of workplace injuries, illnesses, and incidents, and report specific incidents to OSHA as required. These records and reports provide valuable insights into workplace safety trends and help identify areas for improvement, leading to the development of more effective safety programs.
Specific safety measures such as hazard communication, personal protective equipment (PPE), fall protection, electrical safety, machine guarding, and respiratory protection are essential for mitigating hazards and safeguarding workers. Employers must provide appropriate training, implement safety protocols, and ensure that equipment and machinery are properly maintained to minimize risk.
In conclusion, prioritizing OSHA standards and incorporating them into workplace practices is paramount for employers in the construction and general industry. By creating a culture of safety, adhering to regulations, and continually improving safety protocols, employers can provide a secure and healthy working environment where employees can thrive without compromising their well-being.
Frequently Asked Questions about What Are The OSHA Standards For Construction And General Industry
Was this page helpful?
At Storables.com, we guarantee accurate and reliable information. Our content, validated by Expert Board Contributors, is crafted following stringent Editorial Policies. We're committed to providing you with well-researched, expert-backed insights for all your informational needs.
0 thoughts on “What Are The OSHA Standards For Construction And General Industry”