Home>Furniture & Design>Interior Design Trends>How Is Glass Made From Sand
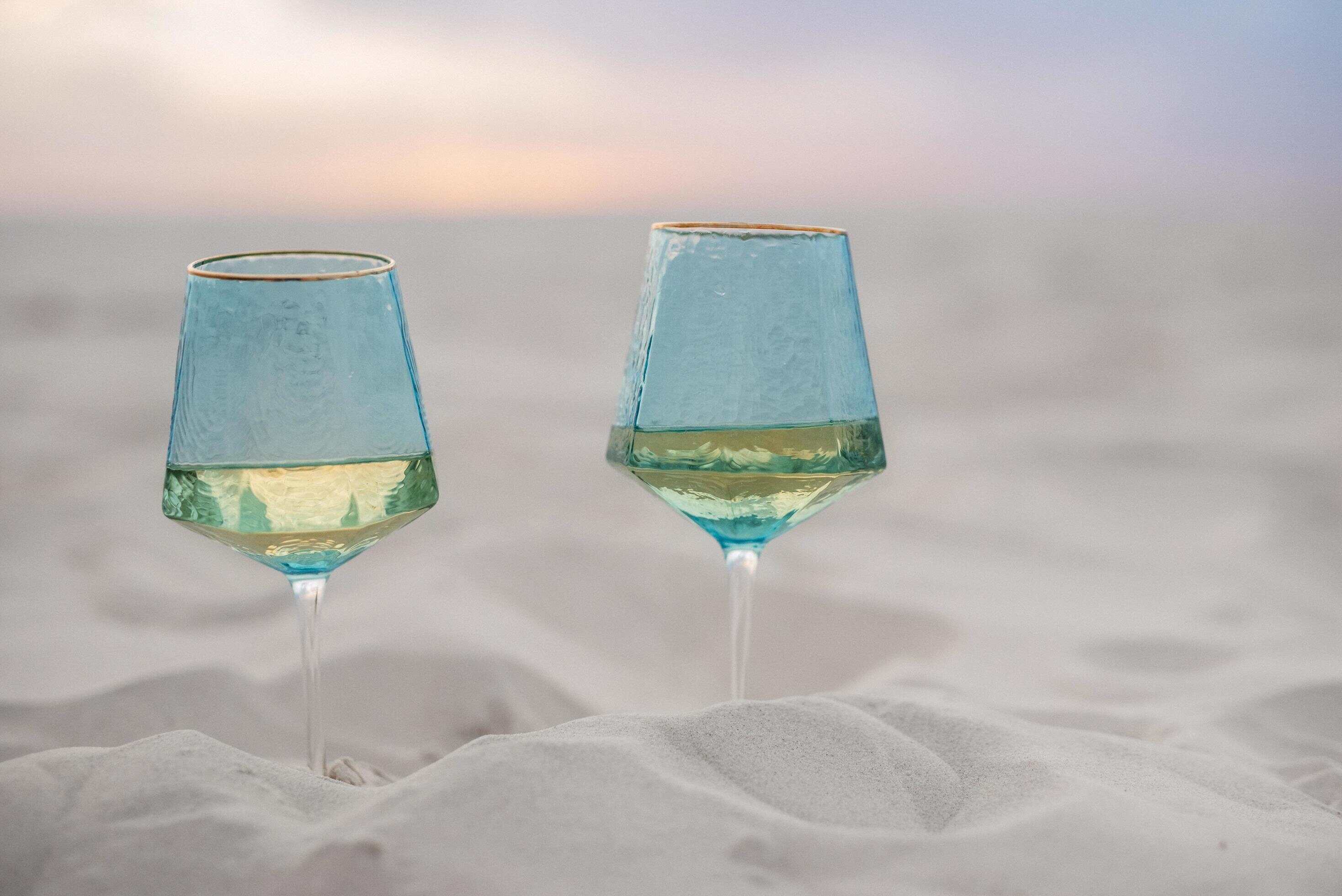
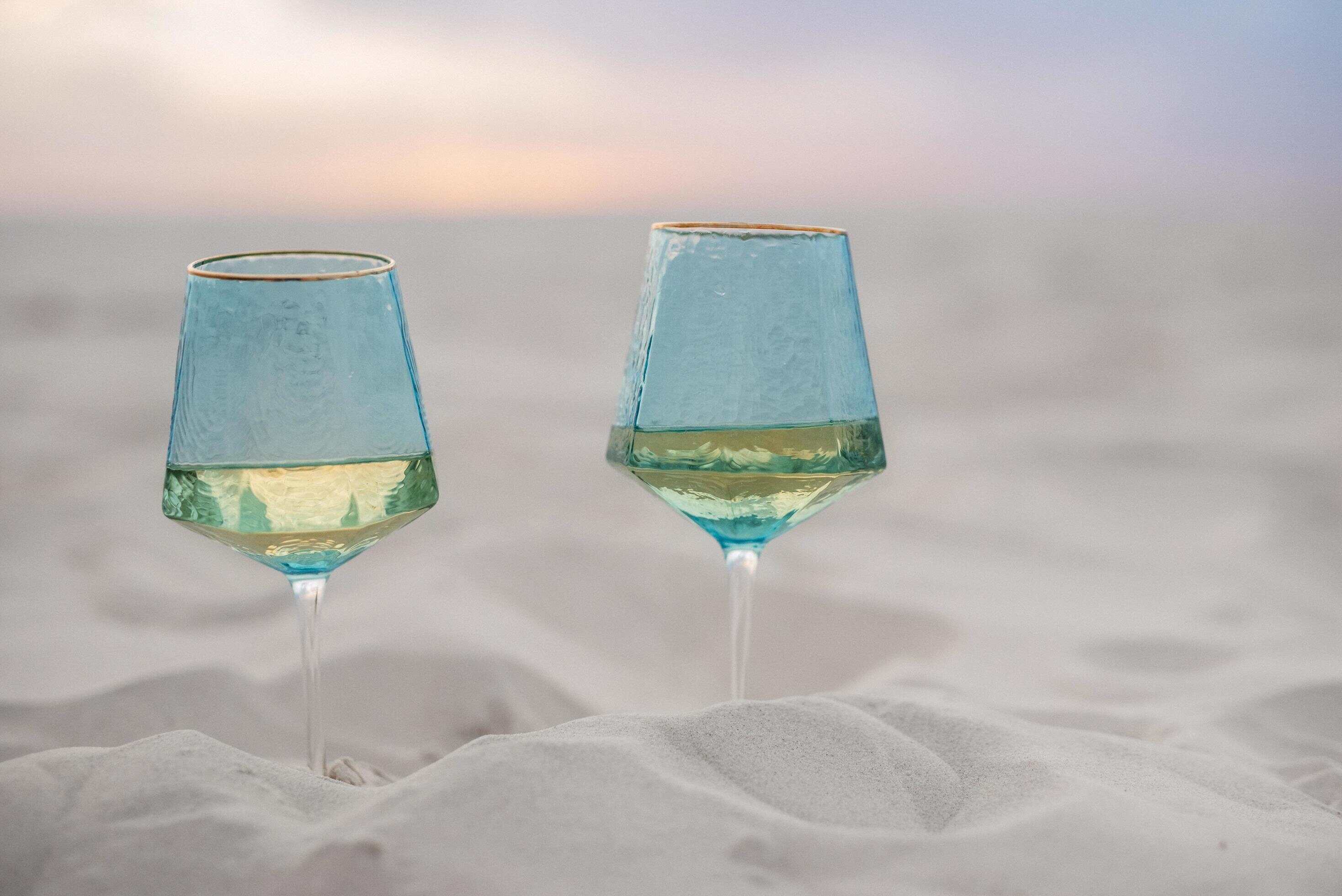
Interior Design Trends
How Is Glass Made From Sand
Modified: October 18, 2024
Discover the fascinating process of turning sand into glass and explore the latest interior design trends inspired by this timeless material. Uncover the secrets of glassmaking and find out how it's shaping modern interior design.
(Many of the links in this article redirect to a specific reviewed product. Your purchase of these products through affiliate links helps to generate commission for Storables.com, at no extra cost. Learn more)
Introduction
Glass is a material that we encounter in our daily lives, from the windows that let light into our homes to the containers that hold our favorite beverages. It's a versatile and fascinating substance that has been used for centuries, and its production process is a marvel of human ingenuity. Have you ever wondered how something as simple as sand can be transformed into the transparent, durable material we know as glass? The answer lies in the intricate and captivating process of glassmaking.
The art of glassmaking dates back thousands of years, with ancient civilizations such as the Egyptians and Romans pioneering the techniques that laid the foundation for modern glass production. Today, the process of creating glass from sand involves a delicate balance of science, technology, and craftsmanship. It's a journey that begins with the most basic of ingredients – sand – and culminates in the creation of a material that is both functional and aesthetically pleasing.
In this article, we will delve into the fascinating world of glassmaking, exploring the ingredients and processes that transform raw materials into the glass products that enhance our daily lives. From the sands of time to the intricate techniques employed by modern artisans, the journey of glassmaking is a story of innovation and creativity. Join us as we unravel the mysteries of this ancient craft and gain a deeper appreciation for the glass that surrounds us.
Key Takeaways:
- Glass is made from sand, soda ash, and limestone, which undergo a fascinating transformation process involving heat and chemistry to create durable and beautiful glass products.
- The art of glassmaking combines nature’s elements with human creativity, resulting in enduring works of art that captivate the eye and enrich everyday life.
Read more: How To Sand Glass
The Ingredients: Sand, Soda Ash, and Limestone
The process of creating glass begins with the most fundamental of ingredients: sand. This seemingly ordinary substance, when combined with other key components, undergoes a remarkable transformation into the transparent material we know as glass. The type of sand used in glassmaking is typically derived from silica, which is abundant in nature and serves as the primary raw material for glass production. Silica sand is chosen for its high purity and uniform particle size, essential qualities that contribute to the clarity and strength of the final glass product.
In addition to sand, two other crucial ingredients play a pivotal role in the glassmaking process: soda ash and limestone. Soda ash, also known as sodium carbonate, acts as a flux, lowering the melting point of the silica to facilitate the glass-forming process. This essential compound enables the raw materials to fuse at lower temperatures, making the manufacturing process more energy-efficient and cost-effective. Limestone, primarily composed of calcium carbonate, serves as a stabilizer, aiding in the durability and workability of the glass.
The careful combination of these three key ingredients sets the stage for the chemical reactions that occur during the glassmaking process. When heated to high temperatures, the silica sand, soda ash, and limestone undergo a complex transformation, culminating in the creation of molten glass. This molten liquid, with its remarkable properties of fluidity and malleability, becomes the foundation for shaping and crafting a wide array of glass products, from delicate ornaments to sturdy window panes.
The precise proportions of these ingredients are meticulously calculated to achieve the desired characteristics of the glass, such as clarity, strength, and thermal resistance. The art and science of glassmaking lie in the careful balance of these components, as even minor variations can significantly impact the quality and properties of the final glass product.
As we embark on this exploration of the glassmaking process, it becomes evident that the seemingly simple act of transforming sand, soda ash, and limestone into glass is a testament to human ingenuity and the harmonious interplay of nature's elements. The next stage of the journey takes us into the mesmerizing world of the melting process, where these basic ingredients undergo a remarkable metamorphosis, giving rise to the captivating substance we know as glass.
The Melting Process
The melting process is the pivotal stage in the transformation of raw materials into glass, where the alchemy of heat and chemistry converges to create the molten liquid that will shape the final glass product. This extraordinary metamorphosis begins with the carefully measured combination of silica sand, soda ash, and limestone, which are introduced into a furnace with precision and expertise.
Inside the furnace, the temperature steadily rises, reaching extreme levels that exceed 1700°C (3092°F). At these searing temperatures, the raw materials undergo a profound change, transitioning from solid to liquid state. The intense heat causes the silica to lose its crystalline structure, allowing it to fuse with the soda ash and limestone, forming a homogeneous molten mass.
The molten glass, with its mesmerizing glow and fluidic grace, embodies the essence of transformation. It becomes a canvas for the artisans and craftsmen who harness its malleable nature to create a myriad of glass products, each bearing the imprint of human creativity and skill.
The process of melting is a delicate dance of precision and control, as the temperature, composition, and duration of heating are meticulously regulated to achieve the desired properties of the glass. The molten liquid is carefully monitored to ensure its homogeneity and purity, as any impurities or irregularities can compromise the integrity of the final glass product.
As the molten glass reaches its optimal state, it embodies a state of potential, ready to be shaped and molded into a myriad of forms. From the graceful curves of a vase to the sleek contours of a drinking glass, the molten glass holds the promise of endless possibilities, awaiting the skilled hands of artisans to breathe life into its form.
The melting process stands as a testament to the harmonious fusion of art and science, where the raw materials undergo a profound metamorphosis, emerging as a medium for human creativity and expression. It is a stage where the ancient alchemy of glassmaking unfolds, bridging the realms of tradition and innovation to yield the timeless beauty of glass.
In the next phase of the glassmaking journey, we will explore the art of shaping and cooling, where the molten glass is sculpted into exquisite forms, embodying the artistry and vision of the craftsmen who shape its destiny.
Glass is made from sand, soda ash, and limestone. The sand is heated to high temperatures to melt it, then it is shaped and cooled to form glass.
Shaping and Cooling
The transition from molten liquid to exquisite glassware marks the pivotal stage of shaping and cooling in the glassmaking process. As the molten glass emerges from the intense heat of the furnace, it embodies a state of fluidic grace, ready to be sculpted into a myriad of forms. This transformative phase is a testament to the skill and artistry of the craftsmen who harness the malleable nature of glass to breathe life into their creations.
The shaping process begins with the gathering of molten glass onto the end of a blowpipe or punty, a long, hollow rod that serves as the foundation for crafting glass objects. The artisan deftly manipulates the molten glass, using a combination of gravity, centrifugal force, and specialized tools to shape and mold it into the desired form. Whether it's the delicate curves of a vase, the intricate patterns of a decorative ornament, or the functional elegance of a drinking glass, the shaping process demands precision and expertise.
As the glass takes on its intended form, it undergoes a gradual transition from a pliable state to a solidified structure. This delicate balance of temperature and manipulation is a testament to the artistry and skill of the craftsmen, who must work swiftly and decisively to capture the essence of their vision before the glass cools and hardens.
Following the shaping process, the newly formed glass object enters a controlled cooling phase, where it is subjected to carefully regulated temperatures to ensure its structural integrity. This gradual cooling process is essential to prevent internal stresses within the glass, which could compromise its strength and durability. The controlled cooling allows the glass to anneal, or gradually relax, reducing internal strains and enhancing its resilience.
The cooling process is a testament to the meticulous craftsmanship and scientific precision that underpin the art of glassmaking. As the glass object transitions from a molten state to a solidified form, it embodies the culmination of human creativity and technical mastery. The interplay of shaping and cooling yields glass objects that not only captivate the eye with their beauty but also endure the test of time with their strength and resilience.
In the realm of glassmaking, the shaping and cooling phase represents the convergence of art and science, where the ethereal beauty of molten glass is transformed into enduring works of art. It is a stage where the vision of the artisan meets the transformative power of heat and craftsmanship, giving rise to the timeless allure of glass.
Quality Control and Finishing
The meticulous process of glassmaking extends beyond the shaping and cooling phases, encompassing a critical stage known as quality control and finishing. This pivotal phase embodies the commitment to excellence and precision, ensuring that each glass product meets exacting standards of quality and craftsmanship.
Quality control begins with a rigorous assessment of the glass objects, where skilled artisans and technicians meticulously inspect every detail to identify any imperfections or irregularities. This meticulous scrutiny encompasses a range of criteria, including clarity, uniformity, and structural integrity. Any deviations from the desired specifications are carefully noted, signaling the need for corrective measures to uphold the uncompromising standards of the glassmaking process.
The finishing touches applied to glass products are a testament to the artistry and attention to detail that define the craft of glassmaking. Whether it's the delicate polishing of a decorative vase or the precise cutting of a crystal goblet, the finishing process demands precision and expertise. Skilled artisans employ specialized techniques to refine the surface of the glass, enhancing its luster and visual appeal. Each stroke of the polishing wheel or cut of the engraving tool reflects the dedication to elevating the aesthetic allure of the glass, transforming it into a work of art that captivates the eye and enriches the surrounding space.
The pursuit of perfection extends to the realm of functionality, where glass products undergo rigorous testing to ensure their suitability for diverse applications. From the resilience of window panes to the thermal resistance of glassware, each product is subjected to stringent assessments to validate its performance and durability. This unwavering commitment to quality control underscores the enduring legacy of glassmaking, where the fusion of artistry and precision yields products that not only inspire admiration but also serve practical purposes in everyday life.
In the realm of glassmaking, the stage of quality control and finishing represents the culmination of the artisan's vision and the uncompromising pursuit of excellence. It is a testament to the enduring legacy of a craft that has transcended centuries, embodying the timeless allure of glass as a medium of beauty, functionality, and enduring quality.
Read more: What Are Sand And Fog Candles Made Of
Conclusion
The journey of glassmaking is a captivating odyssey that intertwines the elements of nature, the ingenuity of human craftsmanship, and the transformative power of heat and chemistry. From the humble grains of sand to the exquisite glass products that grace our lives, the process of creating glass is a testament to the harmonious fusion of art and science.
At its core, glassmaking embodies the timeless pursuit of transformation, where raw materials undergo a profound metamorphosis, emerging as a medium for human creativity and expression. The alchemical dance of melting, shaping, and cooling yields glass objects that not only captivate the eye with their ethereal beauty but also endure the test of time with their strength and resilience.
The art of glassmaking transcends mere functionality, evolving into a symphony of craftsmanship and artistry that enriches our surroundings and elevates our experiences. Whether it's the delicate contours of a hand-blown vase, the intricate patterns of a stained glass window, or the sleek elegance of a modern architectural marvel, glass serves as a canvas for human creativity, capturing the essence of light and form in its transparent embrace.
As we reflect on the intricate process of glassmaking, we gain a deeper appreciation for the artistry and dedication that underpin this ancient craft. The fusion of silica, soda ash, and limestone gives rise to a material that embodies both fragility and resilience, transparency and reflection, simplicity and sophistication. It is a material that transcends its utilitarian purpose, becoming a symbol of beauty, innovation, and enduring quality.
In the modern era, the legacy of glassmaking continues to evolve, embracing technological advancements and innovative techniques while honoring the time-honored traditions of the craft. The allure of glass endures, captivating our imagination and inspiring us with its endless potential for creativity and expression.
As we gaze through the looking glass of history, we witness the enduring legacy of a craft that has shaped civilizations, adorned sacred spaces, and illuminated the realms of art and architecture. The journey of glassmaking is a testament to the transformative power of human creativity, where the most basic of ingredients – sand, soda ash, and limestone – are elevated to the realm of artistry and innovation.
In the symphony of creation, glass stands as a shimmering testament to the boundless possibilities that emerge when nature's elements converge with human vision and skill. It is a material that transcends time and space, embodying the enduring legacy of a craft that has illuminated our world with its timeless allure.
Frequently Asked Questions about How Is Glass Made From Sand
Was this page helpful?
At Storables.com, we guarantee accurate and reliable information. Our content, validated by Expert Board Contributors, is crafted following stringent Editorial Policies. We're committed to providing you with well-researched, expert-backed insights for all your informational needs.
0 thoughts on “How Is Glass Made From Sand”