Home>Home Security and Surveillance>How Often Should Non-Supervised Employee Alarm Systems Be Tested Per OSHA
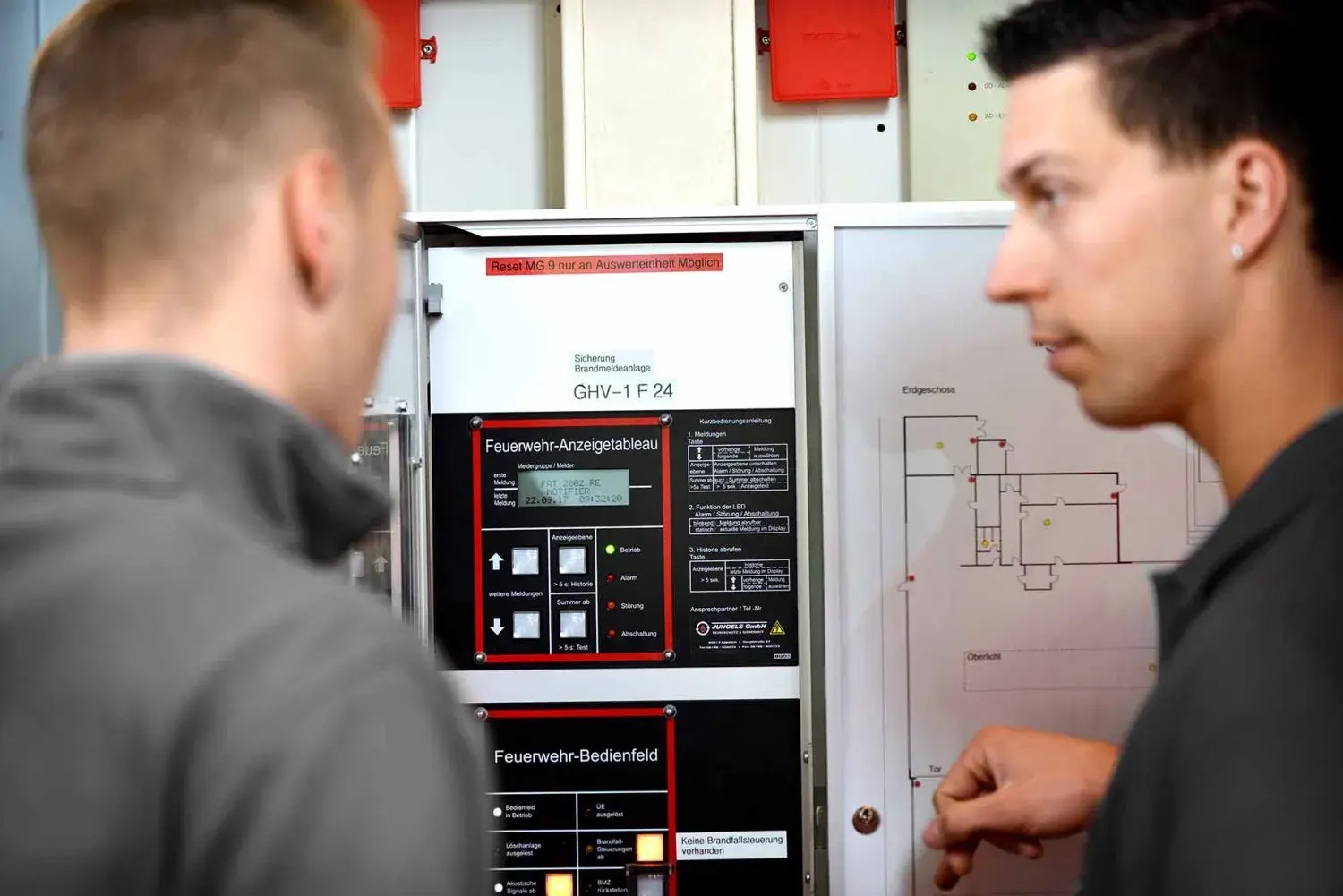
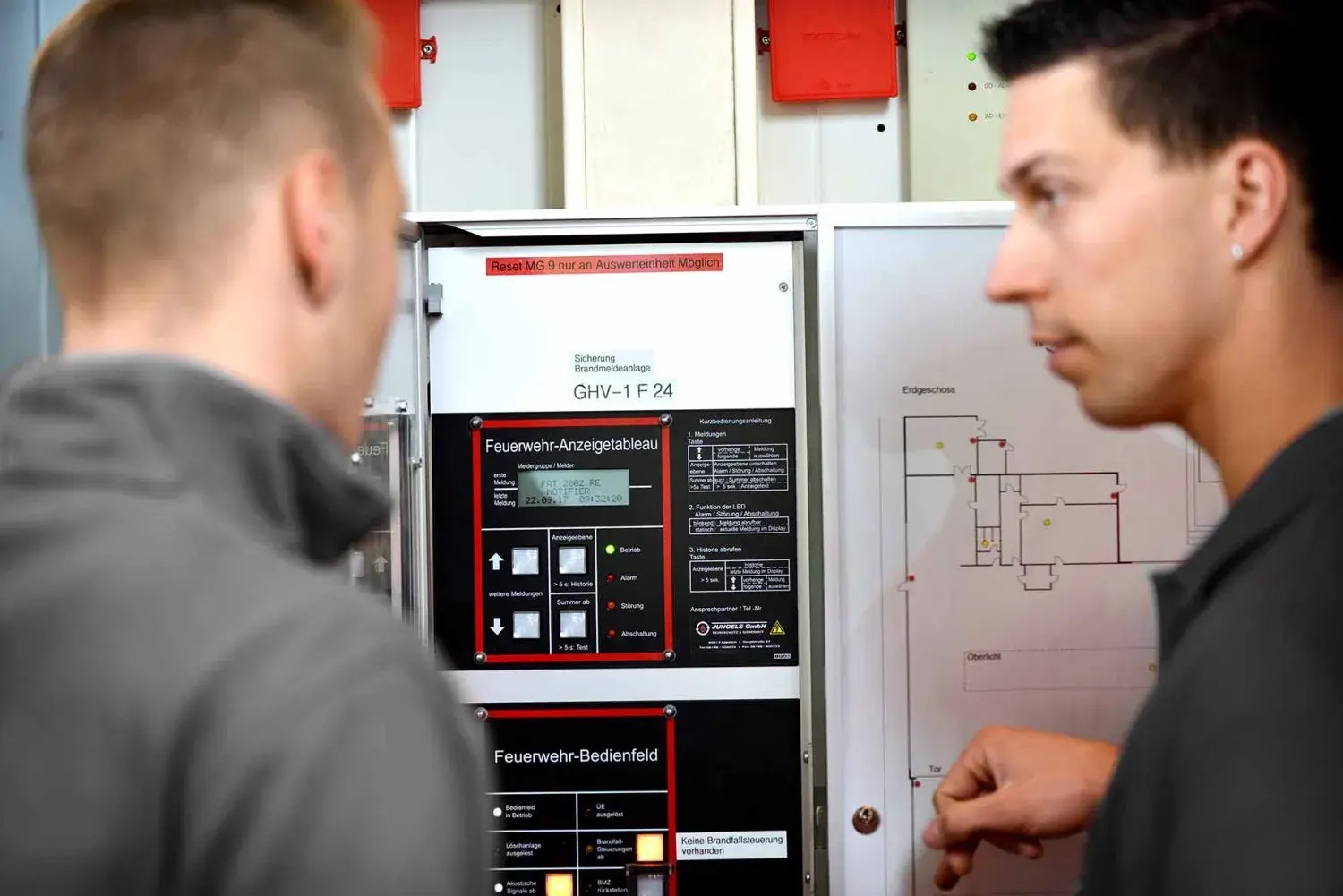
Home Security and Surveillance
How Often Should Non-Supervised Employee Alarm Systems Be Tested Per OSHA
Modified: March 6, 2024
Ensure compliance with OSHA regulations by regularly testing non-supervised employee alarm systems at home for optimum home security and surveillance.
(Many of the links in this article redirect to a specific reviewed product. Your purchase of these products through affiliate links helps to generate commission for Storables.com, at no extra cost. Learn more)
Introduction
Welcome to the world of non-supervised employee alarm systems, where safety and security are paramount. In today’s fast-paced and ever-evolving workplace, ensuring the well-being of employees is of utmost importance. One critical aspect of maintaining a safe work environment is testing non-supervised employee alarm systems regularly.
Non-supervised employee alarm systems are designed to alert employees in the event of emergencies such as fires, chemical spills, or other hazardous situations. These systems play a vital role in ensuring that employees are aware of potential dangers and can take immediate action to protect themselves and others.
Testing these alarm systems on a regular basis is not only crucial for compliance with the Occupational Safety and Health Administration (OSHA) guidelines but also for the overall effectiveness of the system. Regular testing helps identify any potential issues or malfunctions, allowing for timely repairs or replacements, thus preventing any unfortunate incidents.
Throughout this article, we will explore the importance of testing non-supervised employee alarm systems, guidelines provided by OSHA for testing, factors to consider when determining testing frequency, recommended testing frequency, testing procedures, common challenges, and solutions, as well as documentation and training requirements.
So, if you are responsible for the safety and security of your workplace, buckle up as we steer you through the ins and outs of testing non-supervised employee alarm systems. Let’s dive in!
Key Takeaways:
- Regular testing of non-supervised employee alarm systems is crucial for workplace safety, compliance with regulations, and early detection of potential problems, ensuring a safe and secure work environment.
- Proper training and documentation are essential for employees to effectively test non-supervised employee alarm systems, promoting a culture of safety and preparedness in the workplace.
Importance of Testing Non-Supervised Employee Alarm Systems
Testing non-supervised employee alarm systems is crucial for safeguarding the well-being of employees and ensuring a prompt response in case of emergencies. Here are some key reasons why testing these systems is of utmost importance:
1. Reliability and Functionality
Regular testing helps ensure that the non-supervised employee alarm systems are reliable and functioning optimally. It allows you to identify and address any issues or malfunctions promptly, reducing the risk of system failures during critical situations. Employees need to have confidence in the alarm system’s ability to alert them in emergencies, and regular testing fosters this trust.
2. Compliance with Regulations
Adhering to regulatory standards, such as those set by OSHA, is essential for any workplace. OSHA requires employers to provide a safe working environment for employees, including proper emergency response systems. Regularly testing non-supervised employee alarm systems is an important aspect of compliance with OSHA guidelines.
3. Early Detection of Problems
Testing non-supervised employee alarm systems allows you to detect any potential problems early on. Whether it’s a faulty sensor, a malfunctioning alarm panel, or a weak battery, identifying and addressing these issues proactively can prevent accidents and minimize downtime in case of emergencies.
Read more: How Often Should I Test My Smoke Detector
4. Employee Preparedness
Regular testing of alarm systems helps train employees to respond effectively and efficiently during emergencies. Familiarity with the system’s alarms, evacuation routes, and emergency protocols can save precious time in critical situations. Through testing, employees become more aware of the alarms and are better prepared to take appropriate actions when they sound.
5. Liability and Risk Mitigation
By testing non-supervised employee alarm systems at regular intervals, you take proactive steps to minimize liability and mitigate potential risks. In the unfortunate event of an emergency, having properly functioning alarm systems can demonstrate due diligence in providing a safe working environment, potentially reducing legal and financial repercussions.
In summary, testing non-supervised employee alarm systems is crucial for maintaining their reliability, complying with regulations, detecting and addressing problems early, preparing employees for emergencies, and minimizing liability. It is an essential aspect of ensuring the safety and security of your workplace and its occupants.
OSHA Guidelines for Testing Non-Supervised Employee Alarm Systems
The Occupational Safety and Health Administration (OSHA) provides specific guidelines for testing non-supervised employee alarm systems to ensure workplace safety. Familiarizing yourself with these guidelines is essential for compliance. Here are the key OSHA guidelines for testing non-supervised employee alarm systems:
1. Regular Testing
OSHA emphasizes the importance of regular testing of non-supervised employee alarm systems. The frequency of testing should be determined based on the specific characteristics of the workplace, the type of alarms used, and the potential hazards present. Regular testing typically entails monthly, quarterly, or annual inspections to verify the functioning of the alarm systems.
2. Audible and Visual Alarms
Non-supervised employee alarm systems often include both audible and visual alarms to ensure employees are alerted effectively. According to OSHA guidelines, both types of alarms should be tested during each inspection. Audible alarms should be loud enough to be heard clearly, while visual alarms should be bright and flashing to catch employees’ attention, especially in noisy or busy environments.
3. Testing in Different Areas
OSHA recommends testing non-supervised employee alarm systems in various areas of the workplace to ensure coverage throughout the premises. This includes testing alarms in different departments, floors, and workspaces. It ensures that employees across the entire facility can hear and see the alarms, enabling them to respond promptly to emergencies.
4. Alarm Response Verification
In addition to testing the alarms, OSHA guidelines also stress the importance of verifying employees’ response to the alarms during testing. This includes conducting evacuation drills where employees practice the designated emergency evacuation routes and assembly points. Verifying that employees understand and follow the designated emergency procedures is crucial for their safety during real emergencies.
5. Documentation and Record-Keeping
OSHA requires employers to keep comprehensive records of all non-supervised employee alarm system tests and inspections. These records should include the date of the test, the specific areas tested, any issues identified, and the actions taken to remedy them. Proper documentation demonstrates compliance with OSHA guidelines and serves as a reference for future inspections or audits.
By adhering to OSHA guidelines for testing non-supervised employee alarm systems, you can ensure that your workplace meets the necessary safety standards. Regular testing and compliance not only protect your employees but also contribute to a culture of safety and preparedness in your organization.
Read more: How Often Should You Have HVAC Serviced
Factors to Consider when Determining Testing Frequency
When determining the frequency of testing for non-supervised employee alarm systems, several factors must be taken into consideration. Adhering to these factors ensures that the testing frequency aligns with the specific needs and characteristics of your workplace. Here are some key factors to consider when determining the testing frequency:
1. Regulations and Standards
Complying with the regulations and industry standards is a top priority when determining the testing frequency. OSHA guidelines provide general recommendations, but specific industries or local authorities may have additional requirements. Familiarize yourself with these regulations and ensure your testing frequency meets or exceeds the prescribed standards.
2. Type of Alarm System
The type of non-supervised employee alarm system installed in your workplace will influence the testing frequency. Different alarm systems may have varying components and requirements. For example, if your alarm system includes smoke detectors, heat detectors, and carbon monoxide detectors, you may need to test them more frequently than a system with only audible alarms.
3. Environment and Hazards
The particular environment and potential hazards in your workplace should also be taken into account. Some workplaces, such as those with high dust or moisture levels, may require more frequent testing due to the increased likelihood of sensor malfunctions. Similarly, workplaces with hazardous materials or complex machinery may warrant more stringent testing schedules to ensure proper alarm functionality.
Read more: How Long Should My HVAC Fan Run Per Hour
4. Occupancy and Activity Levels
The occupancy and activity levels of your workplace can also impact the testing frequency. If your workplace experiences high employee turnover or operates in multiple shifts, more frequent testing may be necessary to ensure all employees are familiar with the alarm system. Additionally, workplaces with high levels of activity, such as manufacturing plants or construction sites, may require more frequent testing to account for potential wear and tear on the alarm system.
5. Historical Performance and Maintenance Records
Reviewing the historical performance and maintenance records of your alarm system can provide valuable insights into the testing frequency. If previous inspections have uncovered recurring issues or if maintenance has been insufficient, more frequent testing may be required to address these concerns and improve the overall reliability of the system.
By carefully considering these factors, you can determine an appropriate testing frequency for your non-supervised employee alarm systems. Regular testing ensures that the system remains in optimal condition, minimizing the risks of malfunctions and providing a safe and secure work environment for your employees.
Recommended Testing Frequency for Non-Supervised Employee Alarm Systems
Establishing a recommended testing frequency for non-supervised employee alarm systems is crucial to ensure their reliable and effective functioning. While specific testing frequencies may vary depending on factors such as regulations and workplace characteristics, here are some general recommendations to consider:
1. Monthly Inspections
Conducting monthly inspections is a common recommendation for non-supervised employee alarm systems. This frequency allows for regular checks and ensures that any issues or malfunctions are identified and addressed in a timely manner. Monthly inspections help maintain the reliability and performance of the alarm systems.
Read more: How Often Should You Change HVAC Air Filter
2. Quarterly Testing
In addition to monthly inspections, quarterly testing provides a more thorough assessment of the alarm system’s functionality. This frequency allows for a comprehensive examination of all alarm components, including audible alarms, visual alarms, sensors, control panels, and communication systems. Quarterly testing helps identify any emerging issues and provides an opportunity for more in-depth maintenance and repairs.
3. Semi-Annual Maintenance
Performing semi-annual maintenance on non-supervised employee alarm systems is another recommended practice. This frequency ensures that critical components, such as batteries, wiring, and connections, are checked and maintained regularly. Semi-annual maintenance helps prolong the lifespan of the alarm systems and reduces the risk of unexpected failures.
4. Annual Certification
Obtaining annual certification from a qualified professional is essential for ensuring the overall effectiveness of non-supervised employee alarm systems. This certification verifies that the alarm system meets all applicable regulations and industry standards. It involves a thorough inspection, functional testing of all alarm components, and documentation of the system’s compliance.
5. Considerations for Specific Environments
Keep in mind that certain environments may require more frequent testing. For example, workplaces with high humidity, dust, or chemicals may necessitate more frequent inspections to prevent sensor malfunctions. Similarly, industries where employee turnover is high or where the alarm system is subject to excessive wear and tear may warrant more frequent testing.
Remember that these recommended testing frequencies are general guidelines, and it is essential to tailor them to the specific needs of your workplace. Always consult relevant regulations and industry standards to ensure compliance and consider any specific factors that may impact the alarm system’s performance. Regular testing and maintenance contribute to a safe and secure work environment, providing peace of mind for both employers and employees.
Read more: How To Test A Burglar Alarm
Testing Procedures for Non-Supervised Employee Alarm Systems
Testing non-supervised employee alarm systems is a crucial step in ensuring their reliability and effectiveness. Having proper testing procedures in place contributes to a safe work environment and promotes a culture of preparedness. Here are the key steps to follow when conducting testing for non-supervised employee alarm systems:
1. Create a Testing Schedule
Develop a testing schedule that outlines the frequency of testing for your non-supervised employee alarm systems. Determine whether you will conduct monthly, quarterly, or annual inspections, as well as any additional testing required for specific components or environments. Clearly documenting the testing schedule helps ensure consistency and accountability.
2. Notify Employees
Prior to conducting testing, notify employees about the date, time, and duration of the testing. This notification allows them to be aware that testing will occur and helps prevent unnecessary panic or confusion when the alarms sound. Consider posting reminders or sending out email notifications to ensure that all employees are adequately informed.
3. Gather Testing Equipment
Before starting the testing process, gather all necessary equipment and tools. This may include ladders, testing devices, replacement batteries, and any other specific equipment required for your alarm system. Ensuring that you have everything on hand before starting the testing helps streamline the process and avoids unnecessary delays.
Read more: How Often Should You Clean Your HVAC Ducts
4. Test Audible Alarms
During the testing, begin by checking the functionality of the audible alarms. Activate the alarms one by one and listen for clear and loud alerts. Ensure that the alarms are audible from various areas of the workplace, including offices, production floors, and break rooms. Make note of any alarms that are not functioning correctly or are not audible in specific areas.
5. Test Visual Alarms
In addition to audible alarms, test the visual alarms of the non-supervised employee alarm system. Activate the visual alarms and verify that they are bright and clearly visible, even in well-lit areas or during daytime hours. Check for any malfunctioning or damaged visual alarms that need repair or replacement.
6. Test Communication Systems
If your non-supervised employee alarm system includes communication systems, such as intercoms or speaker systems, test these components as well. Verify that communication is clear and audible, allowing for effective instructions and updates during emergencies. Troubleshoot any issues with communication systems and make the necessary adjustments or repairs.
7. Evaluate Sensor Functionality
Inspect and test the functionality of all sensors in the system, such as smoke detectors or heat detectors. Simulate different emergency scenarios to ensure that the sensors accurately detect potential hazards. Replace any faulty or outdated sensors to maintain the effectiveness of the alarm system.
Read more: How Many Hours Should An AC Run Per Day
8. Test Battery Backup
Most non-supervised employee alarm systems are equipped with battery backup in case of power failure. Test the battery backup to ensure its functionality and longevity. Replace any weak or depleted batteries to guarantee uninterrupted alarm system operation.
9. Document and Address Issues
Throughout the testing process, document any malfunctioning components, repairs made, or issues identified. Maintain a comprehensive record of the testing results, including any necessary follow-up actions required. Address any identified issues promptly to maintain the reliability of the alarm system.
By following these testing procedures, you can ensure that your non-supervised employee alarm systems are fully functional and prepared for any emergencies that may arise. Regular testing and proactive maintenance contribute to the safety and well-being of employees and provide peace of mind in the workplace.
Common Challenges and Solutions in Testing Non-Supervised Employee Alarm Systems
Testing non-supervised employee alarm systems can sometimes pose challenges that require careful consideration and problem-solving. Being aware of these common challenges and having effective solutions in place ensures a smooth and successful testing process. Here are some challenges you may encounter and their corresponding solutions:
1. False Alarms
One common challenge is the occurrence of false alarms during testing. False alarms can cause disruption, confusion, and loss of trust in the alarm system. To mitigate this, clearly communicate to employees that these are test alarms and provide them with advance notice to avoid unnecessary panic. Inform nearby emergency response teams or authorities about the testing to prevent any unnecessary response actions.
2. Maintenance and Repairs
During the testing process, you may discover maintenance or repair needs for the alarm system. It is important to promptly address these issues to maintain the reliability of the system. Regularly schedule maintenance and inspections, and establish a process for reporting and resolving any repairs identified during testing. Maintain a well-documented record of all maintenance and repair activities for future reference.
3. Compatibility Issues
Compatibility issues may arise when integrating alarm systems with new or existing equipment. For example, if you have recently installed a new communication system, it must synchronize effectively with the alarm system to ensure proper functionality during emergencies. It is important to work closely with vendors or experts to ensure seamless integration and resolve any compatibility challenges that may arise.
4. Testing in Remote or Hazardous Areas
In some workplaces, testing alarm systems in remote or hazardous areas can be quite challenging. Areas that are difficult to access or pose safety risks require special consideration. Develop alternative testing procedures, such as remote testing equipment or testing during pre-scheduled maintenance shutdowns. Prioritize employee safety and ensure that proper safety protocols are in place when testing in hazardous areas.
5. Training and Familiarity
Ensuring that all employees are familiar with the alarm system and know how to respond during emergencies is crucial. One challenge is ensuring that new employees receive proper training on the alarm system and emergency procedures. Implement a comprehensive onboarding process that includes training on the alarm system. Conduct regular drills and exercises to reinforce employee familiarity. Utilize informative signage and employee handbooks to provide clear instructions on alarm response protocols.
Read more: How To Test HVAC Capacitor
6. Monitoring and Maintenance Management
Efficient monitoring and maintenance management can be a challenge, especially in larger workplaces or organizations. Implement a system for monitoring the alarm system’s performance and conducting regular inspections and maintenance. Utilize technology solutions, such as centralized alarm monitoring systems, to streamline monitoring and maintenance processes. Consider outsourcing monitoring and maintenance tasks to specialized service providers if necessary.
By anticipating and addressing these common challenges, you can ensure smooth testing processes and maintain the reliability of your non-supervised employee alarm systems. Regular testing, effective maintenance, and responsive problem-solving contribute to a safe and secure work environment for all employees.
Documentation and Record-Keeping Requirements for Testing
Documentation and record-keeping are integral components of testing non-supervised employee alarm systems. They ensure compliance with regulations, provide a historical reference for future inspections, and demonstrate the diligence in maintaining a safe work environment. Here are the key documentation and record-keeping requirements to consider:
1. Testing Schedule
Establish a testing schedule that outlines the frequency and details of each testing session. Include the date, time, and location of the testing, as well as the components or areas being tested. This schedule serves as a reference point for coordinating and tracking testing activities.
2. Testing Reports
Generate comprehensive testing reports for each testing session. These reports should detail the specific tests conducted, the results obtained, and any issues or observations noted during the testing process. Include corrective actions taken or recommended for addressing any identified concerns. These reports provide a clear record of the testing activities and serve as a reference for future inspections or audits.
Read more: How Often Should You Service Your AC
3. Maintenance and Repair Logs
Maintain detailed logs of all maintenance and repair activities related to the non-supervised employee alarm systems. This includes recording the date, nature of the maintenance or repair, and any components replaced or repaired. These logs help track the history of maintenance performed on the system, identify recurring issues, and ensure appropriate maintenance schedules are followed.
4. Calibration Records
If the alarm system includes sensors or detectors requiring calibration, maintain records of the calibration process. Keep track of calibration dates, calibration results, and any adjustments made during the process. Proper calibration ensures the accuracy and reliability of the alarm system, and keeping records demonstrates compliance with calibration requirements.
5. Test Results and Findings
Record and document all test results and findings obtained during the testing process. This includes any issues identified, such as faulty alarms, malfunctioning sensors, or weak battery backups. Document the actions taken to address these findings, such as repairs, replacements, or adjustments. These records serve as references for future inspections and help track the system’s performance over time.
6. Training Records
Maintain records of employee training related to the non-supervised employee alarm systems. Document the date of the training, the employees who participated, and the content covered during the training session. These records verify that employees have received proper training on alarm system operation and emergency response procedures.
Read more: How Often Is A Burglar Alarm False
7. Compliance Certificates or Documentation
Keep any compliance certificates or documentation provided by qualified professionals, such as annual certifications or inspection reports. These documents serve as validation that the non-supervised employee alarm systems meet all regulatory and industry standards. Maintain these certificates in an organized manner for easy reference during inspections or audits.
Proper documentation and record-keeping are crucial for demonstrating compliance, maintaining the history of maintenance and testing activities, and ensuring a safe and secure work environment. Implement a systematic approach to capturing and storing this information, leveraging technology when possible. By adhering to documentation and record-keeping requirements, you can enhance safety protocols, facilitate future inspections, and ensure continuous improvement of your non-supervised employee alarm systems.
Training Requirements for Testing Non-Supervised Employee Alarm Systems
Proper training is essential for ensuring that employees are prepared to effectively test non-supervised employee alarm systems. Training provides employees with the necessary knowledge and skills to carry out testing procedures safely and accurately. Here are the key training requirements to consider:
1. Initial Training
When employees are first introduced to non-supervised employee alarm systems, they should undergo comprehensive initial training. This training should cover the basics of the alarm system’s operation, including how to activate and deactivate alarms, interpret alarm signals, and follow emergency response procedures. It is crucial to ensure that employees understand the importance of testing and the impact of their actions on the overall safety of the workplace.
2. Periodic Refresher Training
Periodic refresher training should be conducted to reinforce employees’ understanding of the alarm system and its testing procedures. Regular refreshers help employees stay up-to-date with any changes or updates to testing protocols. Consider conducting refresher training sessions at least once a year or whenever there are significant updates to the alarm system or testing requirements.
Read more: How To Test HVAC Blower Motor
3. Hands-on Practice
Hands-on practice is an integral part of training for testing non-supervised employee alarm systems. Provide employees with opportunities to physically engage with the alarm system and its components. This includes simulating alarm activations, practicing response procedures, and familiarizing themselves with testing equipment. Hands-on practice builds confidence and ensures employees are well-prepared to undertake testing responsibilities.
4. Emergency Response Training
While the focus of training for testing non-supervised employee alarm systems is on the testing process, it is essential to incorporate emergency response training as well. Employees should be trained on emergency evacuation procedures, assembly points, and communication protocols. This training ensures that employees are prepared to respond appropriately in real emergency situations and understand the connection between testing and actual emergencies.
5. Documentation and Record-Keeping Training
Training employees on the importance of documentation and record-keeping is crucial for maintaining a systematic approach to testing. Ensure employees understand how to accurately complete testing reports, record test results, and document any issues or observations. Emphasize the significance of detailed record-keeping for compliance purposes and as a reference for future inspections or audits.
6. Ongoing Communication and Awareness
Establish ongoing communication channels and maintain open lines of communication with employees regarding testing requirements and updates. Regularly share reminders, updates, and any changes to testing protocols. Encourage employees to report any issues or concerns related to the alarm system promptly. Foster a culture of safety and awareness by prioritizing communication and feedback.
Training requirements for testing non-supervised employee alarm systems ensure employees are equipped with the knowledge and skills necessary to conduct effective testing. By investing in comprehensive and periodic training, you empower employees to contribute to a safe and secure work environment, promoting a culture of safety throughout your organization.
Read more: How Many HVAC Vents Per Square Foot
Conclusion
Testing non-supervised employee alarm systems is a critical aspect of maintaining a safe and secure work environment. By following the guidelines provided by OSHA and considering factors such as regulations, workplace characteristics, and industry standards, you can establish an appropriate testing frequency for your alarm systems.
The importance of testing non-supervised employee alarm systems cannot be overstated. Regular testing ensures the reliability and functionality of the alarm system, compliance with regulations, and early detection of potential problems. It enhances employee preparedness and helps mitigate liability and risks for employers.
When conducting testing procedures, it is essential to create a testing schedule, notify employees, gather necessary equipment, and methodically test audible and visual alarms, sensors, communication systems, and battery backups. Proper documentation and record-keeping of testing activities, maintenance, repairs, and training are crucial for compliance, future reference, and maintaining a historical record of the alarm system’s performance.
Common challenges in testing non-supervised employee alarm systems, such as false alarms, maintenance and repairs, compatibility issues, testing in remote or hazardous areas, training, and monitoring, can be mitigated with effective solutions. By addressing these challenges proactively, you can ensure a smooth and successful testing process.
Training requirements for testing non-supervised employee alarm systems play a vital role in equipping employees with the necessary knowledge and skills. Initial training, periodic refresher training, hands-on practice, emergency response training, and training on documentation and record-keeping contribute to a culture of safety and preparedness.
In conclusion, testing non-supervised employee alarm systems is essential to promote workplace safety, comply with regulations, and ensure the well-being of employees. By following proper testing procedures, overcoming common challenges, and maintaining accurate documentation, you can contribute to a safe and secure work environment where employees are prepared to respond effectively during emergencies.
Frequently Asked Questions about How Often Should Non-Supervised Employee Alarm Systems Be Tested Per OSHA
Was this page helpful?
At Storables.com, we guarantee accurate and reliable information. Our content, validated by Expert Board Contributors, is crafted following stringent Editorial Policies. We're committed to providing you with well-researched, expert-backed insights for all your informational needs.