Home>Renovation & DIY>Tools & Equipment>How To Use Torque Screwdriver
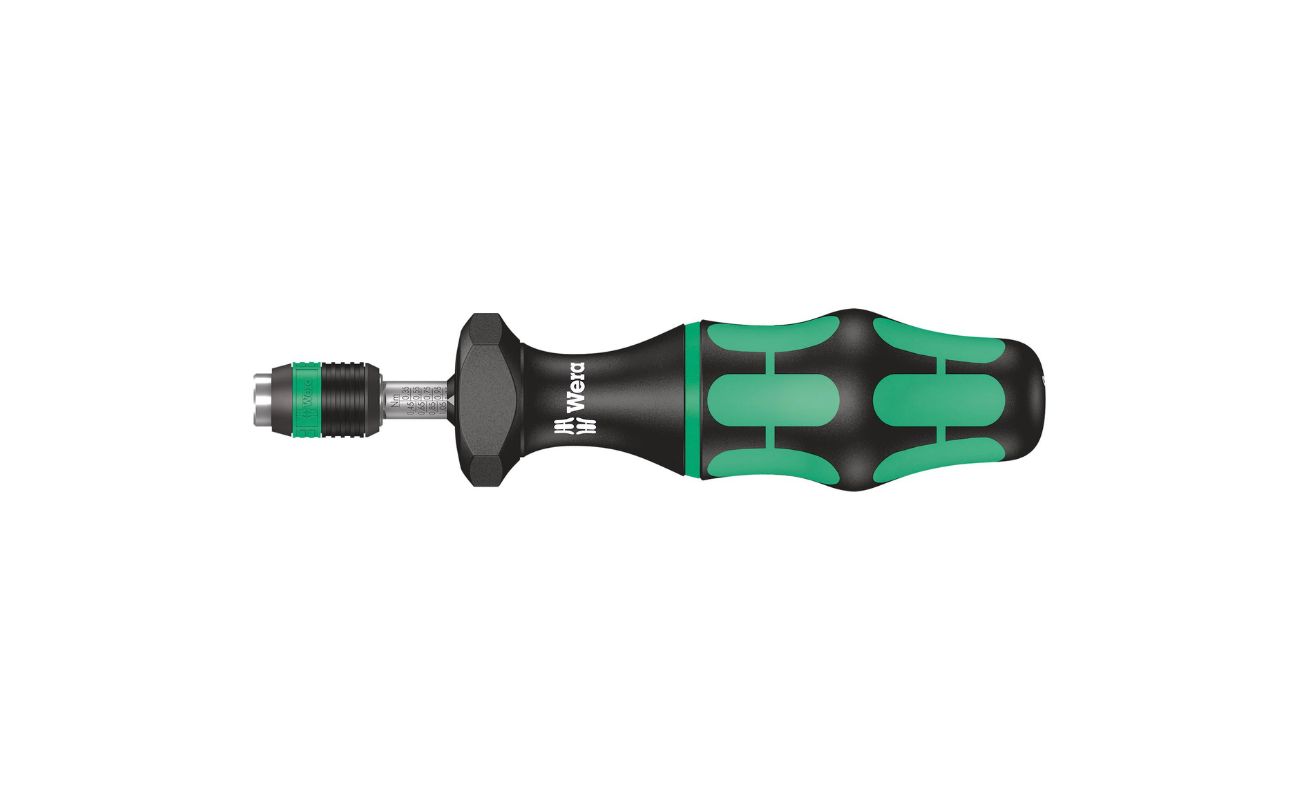
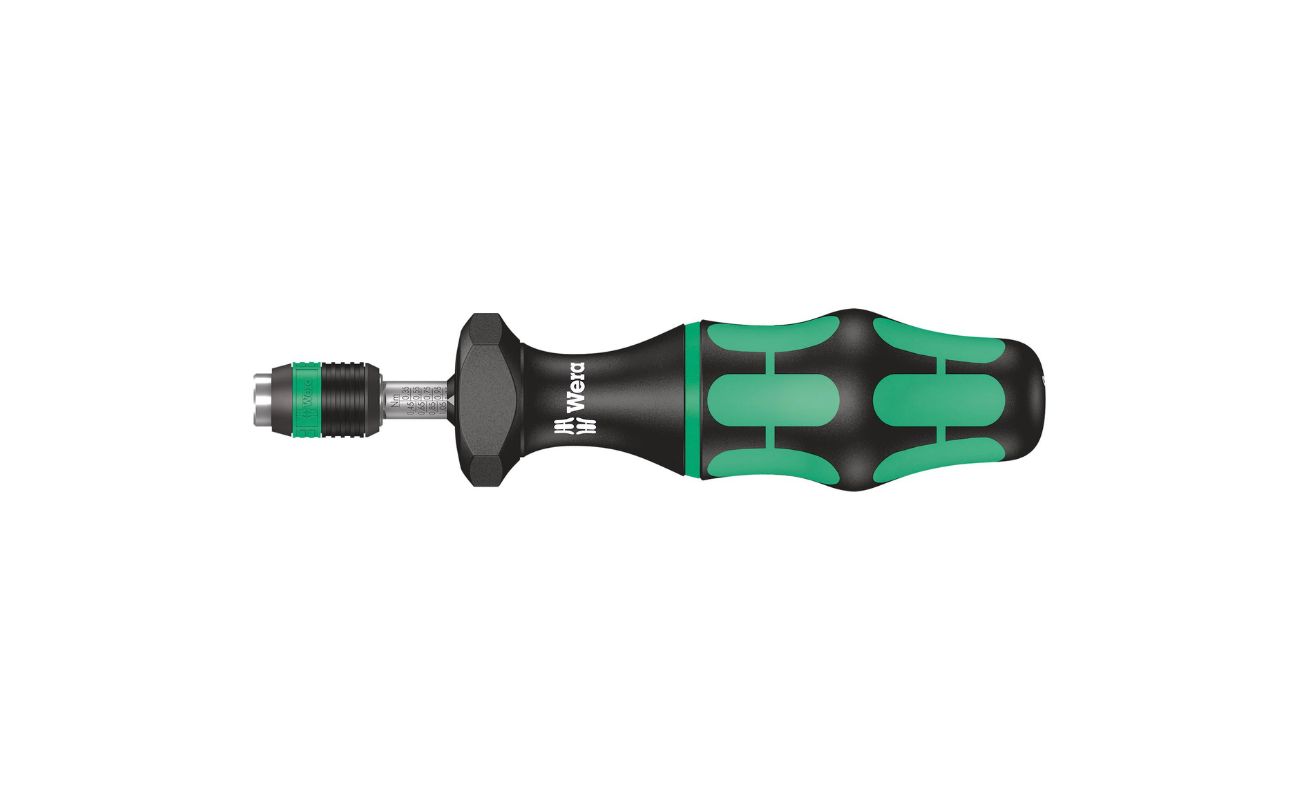
Tools & Equipment
How To Use Torque Screwdriver
Modified: January 4, 2024
Learn how to properly use a torque screwdriver and ensure precise fastening with our comprehensive guide. Explore essential tools and equipment for accurate torque application.
(Many of the links in this article redirect to a specific reviewed product. Your purchase of these products through affiliate links helps to generate commission for Storables.com, at no extra cost. Learn more)
Introduction
Welcome to the world of precision and accuracy in fastening with torque screwdrivers. Whether you are a professional tradesperson, a DIY enthusiast, or someone who appreciates the importance of secure and reliable fastening, understanding how to use a torque screwdriver is essential. In this comprehensive guide, we will explore the intricacies of torque screwdrivers, including their types, applications, and best practices for using them effectively.
Torque screwdrivers are indispensable tools in various industries, including automotive, aerospace, electronics, and manufacturing. Their ability to apply a specific amount of torque to fasteners ensures that components are securely fastened without the risk of over-tightening or under-tightening, which can lead to mechanical failures or damage. By mastering the art of using a torque screwdriver, you can achieve consistent and reliable results, contributing to the longevity and performance of your projects and products.
Whether you are embarking on a new DIY project, assembling precision equipment, or performing routine maintenance tasks, having a solid understanding of torque screwdrivers and their proper usage will empower you to work with confidence and precision. Let's delve into the world of torque screwdrivers and unlock the secrets to achieving optimal fastening results with these indispensable tools.
Key Takeaways:
- Mastering the use of torque screwdrivers ensures precise and reliable fastening, contributing to the longevity and performance of assembled products in various industries.
- Prioritizing safety measures when using torque screwdrivers minimizes hazards, protects personnel, and upholds the integrity of assembled components.
Read more: What Is A Torque Screwdriver
What is a Torque Screwdriver?
A torque screwdriver is a specialized hand tool designed to apply a specific amount of torque, or rotational force, to a fastener, typically a screw. Unlike conventional screwdrivers, which rely on the user’s judgment to determine the appropriate tightness of a fastener, torque screwdrivers provide precise control over the amount of torque applied, ensuring consistent and accurate fastening.
These tools are commonly used in industries where precise torque application is critical, such as electronics manufacturing, automotive assembly, aerospace engineering, and medical device production. By utilizing a torque screwdriver, manufacturers and technicians can achieve uniform fastening results, reduce the risk of damage to delicate components, and maintain the structural integrity of assembled products.
Torque screwdrivers are available in various designs, including manual, electric, and pneumatic models, each offering unique benefits depending on the specific application. Manual torque screwdrivers feature an adjustable torque setting that allows the user to select the desired torque level, typically indicated in inch-pounds or Newton-meters. Electric torque screwdrivers, on the other hand, utilize electric motors to apply torque automatically, offering enhanced efficiency and consistency in high-volume assembly operations. Pneumatic torque screwdrivers harness compressed air to deliver precise torque, making them ideal for applications where electricity is not readily available or poses a safety risk.
One of the key components of a torque screwdriver is the torque-limiting mechanism, which controls the amount of torque transmitted to the fastener. This mechanism may take the form of a clutch, a cam-over design, or electronic sensors, depending on the type of torque screwdriver. When the preset torque level is reached, the torque-limiting mechanism disengages, preventing further tightening and safeguarding the fastener and surrounding components from damage due to over-torquing.
Overall, torque screwdrivers play a crucial role in ensuring the reliability, safety, and quality of assembled products, making them indispensable tools for professionals and enthusiasts alike who prioritize precision and accuracy in fastening applications.
Types of Torque Screwdrivers
Torque screwdrivers come in various types, each tailored to specific applications and user preferences. Understanding the different types of torque screwdrivers is essential for selecting the most suitable tool for a particular task. Let’s explore the common types of torque screwdrivers and their unique characteristics:
- Manual Torque Screwdrivers: Manual torque screwdrivers are operated by hand and feature adjustable torque settings, typically ranging from a few inch-pounds to several dozen inch-pounds. They are versatile, portable, and suitable for a wide range of fastening applications, making them popular choices for precision assembly tasks in industries such as electronics, telecommunications, and small appliance manufacturing.
- Electric Torque Screwdrivers: Electric torque screwdrivers utilize electric motors to apply torque automatically, offering consistent and efficient fastening in high-volume production environments. These tools are favored for their speed, precision, and ergonomic benefits, reducing operator fatigue and enhancing productivity. Electric torque screwdrivers are commonly used in automotive assembly, consumer electronics manufacturing, and other industrial settings that demand fast and reliable fastening operations.
- Pneumatic Torque Screwdrivers: Pneumatic torque screwdrivers, also known as air torque screwdrivers, rely on compressed air to deliver precise torque to fasteners. They are well-suited for applications where electricity is not readily available or poses safety concerns, such as in automotive repair facilities, aerospace maintenance operations, and construction sites. Pneumatic torque screwdrivers offer robust performance and are capable of delivering high torque levels with minimal operator effort.
- Programmable Torque Screwdrivers: Programmable torque screwdrivers feature advanced electronic controls that allow users to set and store multiple torque settings for different fastening tasks. These tools are highly versatile and can accommodate diverse assembly requirements within a single unit. Programmable torque screwdrivers are commonly employed in industries that demand precision, repeatability, and traceability, such as medical device manufacturing, aerospace engineering, and laboratory instrument assembly.
Each type of torque screwdriver offers distinct advantages and is tailored to specific operational needs, making it crucial to assess the requirements of a given application before selecting the most suitable tool. By understanding the characteristics and capabilities of each type, users can make informed decisions and optimize their fastening processes for superior results.
How to Use a Torque Screwdriver
Using a torque screwdriver effectively requires attention to detail, proper technique, and a clear understanding of the fastening task at hand. Whether you are assembling delicate electronics, securing critical components in automotive applications, or performing precision tasks in a workshop, mastering the art of using a torque screwdriver is essential. Here’s a step-by-step guide to using a torque screwdriver with precision and confidence:
- Select the Correct Bit: Begin by choosing the appropriate screwdriver bit that matches the fastener’s head type and size. Ensuring a proper fit between the bit and the fastener is crucial for preventing slippage, minimizing wear, and achieving optimal torque transfer.
- Adjust the Torque Setting: If using a manual torque screwdriver, adjust the torque setting to the desired level based on the fastener’s specifications or the assembly requirements. Electric and pneumatic torque screwdrivers may feature digital displays or adjustable controls for setting the torque level accurately.
- Engage the Fastener: Carefully position the screwdriver bit into the fastener’s recess, ensuring full engagement without applying excessive force. Align the screwdriver perpendicular to the fastener to maintain proper contact and prevent cam-out or stripping of the fastener head.
- Apply Torque Smoothly: Begin applying torque to the fastener in a smooth and controlled manner, using steady pressure without sudden jerks or excessive force. For manual torque screwdrivers, continue turning the handle until the preset torque level is reached, at which point the torque-limiting mechanism will disengage to prevent over-tightening.
- Observe Torque Completion: Pay close attention to the torque screwdriver’s indication of torque completion, which may involve a tactile click, visual signal, or digital readout. Once the screwdriver signals that the preset torque has been reached, immediately cease further tightening to avoid exceeding the specified torque level.
- Inspect Fastener Tightness: After fastening, visually inspect the fastener to ensure that it is securely tightened without being overly stressed or under-torqued. Confirm that the fastener’s head is flush with the mating surface and that no visible damage or deformation has occurred during the fastening process.
By following these steps and exercising precision and care, users can effectively utilize torque screwdrivers to achieve consistent and reliable fastening results across a wide range of applications. Proper technique, attention to detail, and adherence to specified torque levels are paramount in ensuring the integrity and performance of assembled components and products.
When using a torque screwdriver, make sure to set the torque level according to the manufacturer’s specifications for the screw you are using. This will prevent over-tightening and potential damage to the screw or the material you are working with.
Tips for Using a Torque Screwdriver
Mastering the use of a torque screwdriver involves more than just following a set of instructions. To optimize performance, ensure precision, and maintain the longevity of the tool and fasteners, consider the following tips for using a torque screwdriver effectively:
- Calibrate Regularly: Periodically calibrate your torque screwdriver according to the manufacturer’s recommendations or industry standards to ensure accurate torque delivery. Calibration helps maintain the tool’s reliability and prevents under- or over-tightening of fasteners.
- Use the Right Bit Material: Select screwdriver bits made from high-quality materials, such as hardened steel or industrial-grade alloys, to withstand the rigors of torque application and minimize wear. Using the correct bit material enhances durability and ensures optimal torque transfer.
- Follow Manufacturer’s Recommendations: Adhere to the torque screwdriver manufacturer’s guidelines regarding maintenance, storage, and usage to maximize the tool’s performance and longevity. This includes storing the tool in a clean, dry environment and avoiding exposure to extreme temperatures or corrosive agents.
- Apply Torque in Controlled Increments: When tightening fasteners that require higher torque levels, apply torque in controlled increments, allowing the torque screwdriver to disengage and reset between each application. This approach promotes uniform fastening and minimizes the risk of overloading the tool or fasteners.
- Verify Torque Settings: Before each use, double-check the torque setting on the screwdriver to ensure it aligns with the specified torque requirements for the given application. Verifying the torque setting mitigates the risk of under-tightening or over-tightening fasteners, promoting consistent and reliable results.
- Implement Ergonomic Practices: Maintain proper posture and grip when using a torque screwdriver to minimize strain and fatigue. Ergonomic practices, such as maintaining a neutral wrist position and using supportive hand grips, contribute to user comfort and reduce the risk of repetitive strain injuries during prolonged use.
- Monitor Battery Levels (Electric Models): If using an electric torque screwdriver, monitor the battery levels regularly and recharge or replace the batteries as needed to ensure uninterrupted operation. Adequate battery power is essential for consistent torque delivery and reliable performance.
- Document Torque Values: Keep detailed records of torque values applied to critical fasteners, especially in regulated industries or applications where traceability is essential. Documenting torque values facilitates quality assurance, troubleshooting, and compliance with industry standards and specifications.
By incorporating these tips into your torque screwdriver usage practices, you can enhance operational efficiency, promote tool longevity, and achieve precise and consistent fastening results across a diverse range of applications. Attention to detail, proactive maintenance, and adherence to best practices are key to unlocking the full potential of torque screwdrivers in your work environment.
Read more: How To Use A Screwdriver
Safety Precautions
When using torque screwdrivers, prioritizing safety is essential to prevent accidents, protect personnel, and maintain the integrity of assembled components. By adhering to key safety precautions, users can mitigate potential hazards and promote a secure working environment. Here are important safety measures to observe when using torque screwdrivers:
- Wear Personal Protective Equipment (PPE): Prior to using a torque screwdriver, ensure that appropriate personal protective equipment, such as safety glasses, gloves, and, if applicable, hearing protection, is worn to safeguard against potential eye injuries, hand lacerations, and noise exposure.
- Verify Tool Integrity: Before each use, inspect the torque screwdriver for any signs of damage, wear, or malfunction. Ensure that the tool’s components, including the handle, torque adjustment mechanism, and bit holder, are in good condition and free from defects that could compromise safe operation.
- Secure Workpiece Position: Secure the workpiece or assembly in a stable position, utilizing clamps, vises, or other appropriate fixtures to prevent movement during fastening operations. A stable workpiece minimizes the risk of slippage, misalignment, or unexpected movement that could lead to injuries or damage.
- Adhere to Torque Specifications: Always adhere to the specified torque requirements provided by the equipment manufacturer or assembly guidelines. Over-torquing can lead to fastener failure, material deformation, or component damage, while under-torquing may result in loose connections and compromised structural integrity.
- Handle Torque Screwdrivers with Care: Exercise caution when handling torque screwdrivers, avoiding abrupt movements, impacts, or misuse that could affect their performance or compromise safety. Proper handling minimizes the risk of accidental drops, damage to the tool, or unintended torque application.
- Keep Fingers Clear of Rotating Parts: When operating electric or pneumatic torque screwdrivers, keep fingers and loose clothing clear of rotating parts, such as the bit holder or chuck, to prevent entanglement or injuries. Maintain a safe distance from moving components during tool operation.
- Store Tools Safely: Store torque screwdrivers in designated tool storage areas, ensuring they are protected from physical damage, moisture, and unauthorized access. Proper tool storage minimizes the risk of accidental falls, tampering, or exposure to environmental hazards.
- Dispose of Damaged Tools: If a torque screwdriver exhibits signs of damage, wear beyond recommended limits, or compromised functionality, promptly remove it from service and arrange for proper disposal or repair. Continuing to use damaged tools poses safety risks and compromises fastening accuracy.
By integrating these safety precautions into your work practices, you can foster a culture of safety, minimize the risk of accidents, and uphold the reliability and effectiveness of torque screwdrivers in various applications. Prioritizing safety not only protects individuals and assets but also contributes to efficient and successful fastening operations.
Conclusion
As we conclude our exploration of torque screwdrivers, it becomes evident that these precision tools play a pivotal role in achieving consistent and reliable fastening results across a diverse array of industries and applications. From electronics manufacturing and automotive assembly to aerospace engineering and medical device production, torque screwdrivers empower users to secure components with precision, accuracy, and confidence.
By understanding the nuances of torque screwdrivers, including their types, usage techniques, and safety considerations, individuals and professionals alike can elevate their fastening capabilities and contribute to the longevity and performance of assembled products. The ability to apply specific torque levels to fasteners with precision not only enhances the structural integrity of assemblies but also mitigates the risk of damage, material deformation, and mechanical failures.
Furthermore, the incorporation of advanced features, such as programmable torque settings, ergonomic designs, and digital torque readouts, underscores the continuous evolution and innovation within the realm of torque screwdrivers. These advancements empower users to meet the exacting demands of modern manufacturing, assembly, and maintenance tasks with unparalleled efficiency and accuracy.
As you embark on your fastening endeavors, whether in a professional capacity or as a passionate DIY enthusiast, remember that mastering the use of torque screwdrivers is a journey that requires attention to detail, adherence to best practices, and a commitment to safety. By embracing these principles, you can harness the full potential of torque screwdrivers and elevate the quality and reliability of your fastening endeavors.
Ultimately, torque screwdrivers stand as indispensable allies in the pursuit of precision, ensuring that components are securely fastened, products perform as intended, and safety remains paramount in every fastening operation.
Embrace the power of precision with torque screwdrivers, and unlock a world of secure, reliable, and meticulously assembled creations.
Frequently Asked Questions about How To Use Torque Screwdriver
Was this page helpful?
At Storables.com, we guarantee accurate and reliable information. Our content, validated by Expert Board Contributors, is crafted following stringent Editorial Policies. We're committed to providing you with well-researched, expert-backed insights for all your informational needs.
0 thoughts on “How To Use Torque Screwdriver”