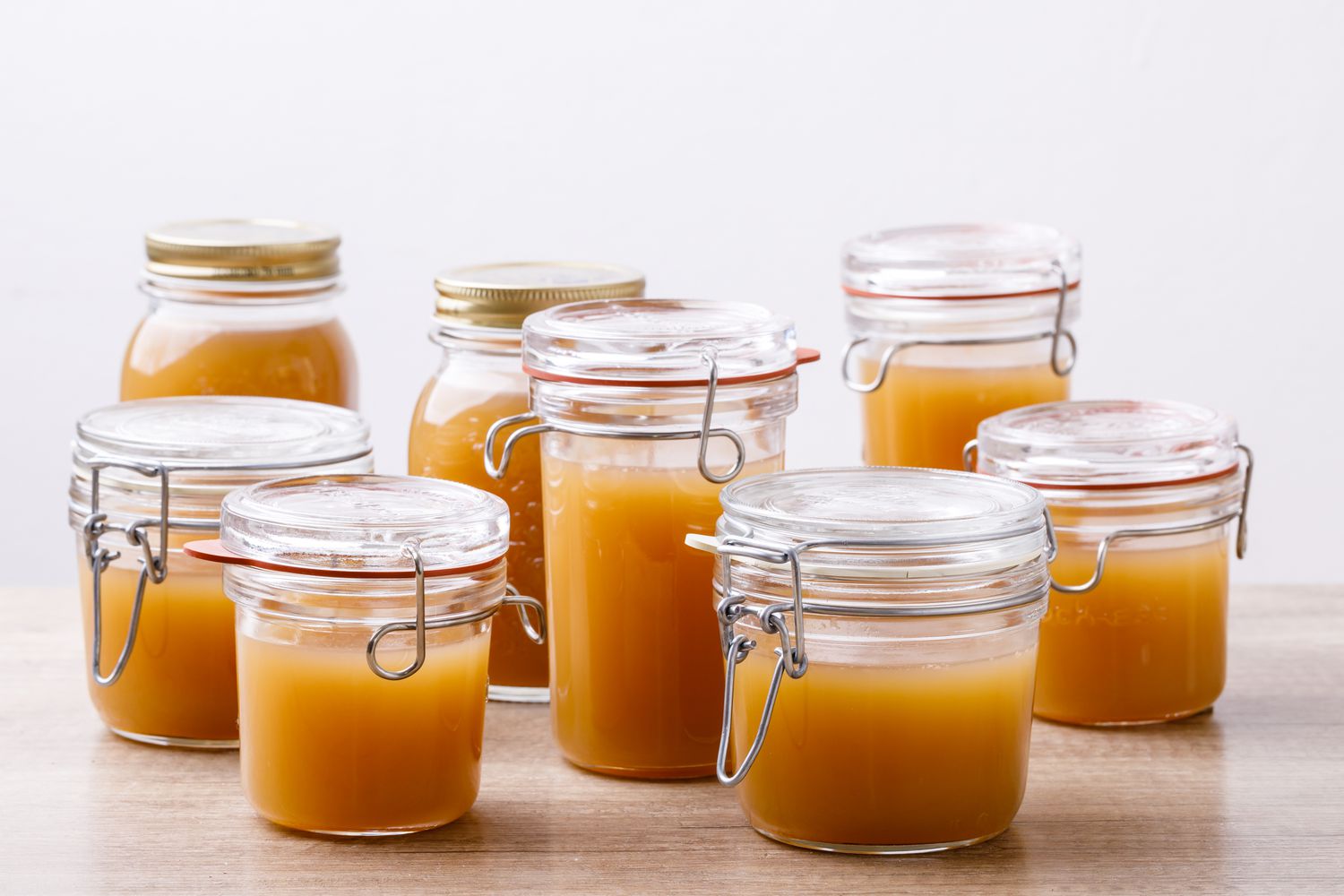
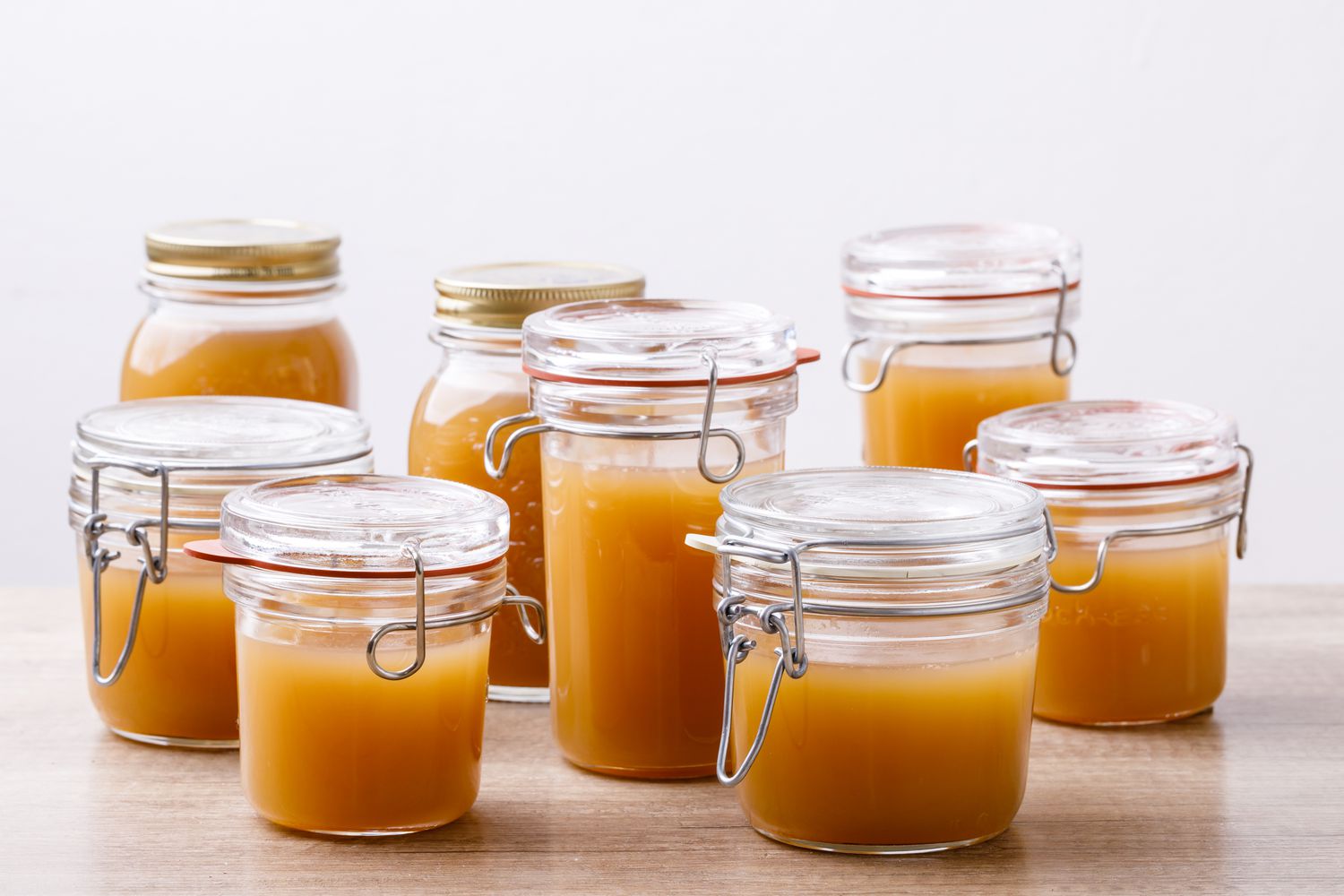
Articles
How To Store Stock
Modified: December 7, 2023
Learn how to effectively store articles and keep your stock organized with our helpful guide. Find out the best practices for article storage and maintain a well-organized stock.
(Many of the links in this article redirect to a specific reviewed product. Your purchase of these products through affiliate links helps to generate commission for Storables.com, at no extra cost. Learn more)
Introduction
When it comes to efficient stock management, proper storage is crucial. Whether you are a small business owner, a warehouse supervisor, or simply someone looking to organize their belongings, knowing how to store your stock effectively can save you time, money, and headaches down the line.
In this article, we will guide you through the process of storing stock and provide you with valuable tips to optimize your storage methods. From choosing the right storage area to implementing a first-in, first-out (FIFO) system, we will cover all the important steps to ensure your stock is stored in a way that maximizes accessibility, minimizes damage, and prevents inventory expiration.
So, if you’re ready to take control of your stock and create a well-organized storage system, let’s dive in!
Key Takeaways:
- Efficient stock management relies on choosing the right storage area, organizing stock by category, and implementing a first-in, first-out (FIFO) system to prevent obsolescence and maximize accessibility.
- Proper labeling, regular stock checks, and maintaining cleanliness and pest control are essential for preserving stock quality, minimizing losses, and ensuring efficient inventory management.
Read more: How To Store Stockings
Step 1: Choose the right storage area
The first step in effectively storing your stock is selecting the appropriate storage area. The ideal storage area will depend on several factors, such as the size and type of your stock, available space, and accessibility requirements. Here are a few key considerations to keep in mind:
- Space: Ensure that the storage area has enough space to accommodate your stock comfortably. It should allow for easy movement and access to items without overcrowding.
- Security: Choose a storage area that is secure and protected from theft, vandalism, and unauthorized access. Install security systems, such as cameras and alarms, if necessary.
- Accessibility: Depending on the frequency of stock retrieval, consider the convenience of accessing the storage area. If you need constant access to your stock, choose a location that is easily reachable, preferably near the main workspace.
- Environmental conditions: Evaluate the environmental conditions, such as temperature, humidity, and ventilation, to ensure they are suitable for your stock. Certain items may require specific temperature controls or protection from moisture.
- Safety regulations: Familiarize yourself with any safety regulations or guidelines specific to your industry. Adhere to these regulations to ensure compliance and prevent any potential hazards.
When selecting a storage area, it’s important to consider both short-term and long-term needs. Anticipate future growth and changes, and choose a storage area that allows for flexibility and scalability.
Remember, the storage area you choose will serve as the foundation for your stock management system, so it’s essential to make the right decision from the start. By considering these factors, you can ensure that your storage area meets your requirements and sets the stage for an organized and efficient stock storage process.
Step 2: Organize your stock by category
Once you have chosen the right storage area, the next step is to organize your stock by category. Organizing your stock in a systematic and logical way makes it easier to locate specific items, reduces the risk of misplacement, and improves overall efficiency. Here’s how you can effectively organize your stock:
- Categorize based on product type: Divide your stock into categories based on the type of products. This could include categories like electronics, clothing, kitchenware, or office supplies. Grouping similar items together will make it easier to find specific products when needed.
- Use labels or color coding: Label your storage shelves, bins, or containers accordingly, so you can quickly identify which category each item belongs to. Consider using color coding systems to further enhance organization and visual distinction.
- Create an inventory tracking system: Implement an inventory tracking system to keep tabs on your stock levels and easily locate items. This can be as simple as using spreadsheets or using specialized inventory management software.
- Arrange based on demand: Consider the frequency at which different items are accessed or restocked. Place frequently used or high-demand items in easily accessible locations, while less frequently used items can be stored in less accessible areas.
- Allocate dedicated spaces: Assign specific areas or shelves for each category. This prevents mixing and confusion among different products and ensures that there is a designated spot for each item.
By organizing your stock by category, you create a clear structure that allows for efficient stock management. Not only does this save time searching for items, but it also helps optimize space utilization and reduces the chances of items getting damaged or lost.
Remember to review and adjust your organizational system as needed. As your stock inventory changes or expands, you may need to reorganize or introduce new categories to accommodate growth. Regularly reassess and tweak your organization process to maintain an effective stock management system.
Step 3: Determine appropriate storage methods
Once you have organized your stock by category, it’s time to determine the appropriate storage methods for each type of item. Different products may have specific storage requirements to maintain their quality and prevent damage. Consider the following factors when determining storage methods:
- Size and shape: Take into account the size and shape of your stock items when selecting storage methods. Some items may require specialized shelving or racks, while others can be stored in bins or containers.
- Weight: Consider the weight of your stock items and choose storage solutions that can safely support them. Heavy items may require sturdy shelves or pallet racking systems.
- Stackability: Determine if your items can be stacked on top of each other. Stackable bins or collapsible containers can help maximize vertical space without compromising access to the lower layers.
- Fragility: If you have fragile items, ensure they are stored in a way that minimizes the risk of breakage. Use protective materials such as bubble wrap or foam inserts, and consider storing delicate items in a separate area to reduce the likelihood of accidental damage.
- Hazardous materials: If you deal with hazardous materials or substances, make sure to follow all safety regulations and use appropriate storage methods, such as chemical storage cabinets or designated areas with proper ventilation.
It’s important to consider both short-term and long-term storage requirements. If you anticipate the need for easy item retrieval, opt for storage options that allow for quick access, such as open shelving or clear containers. For items with a longer shelf life, consider sealed and airtight containers to maintain freshness and extend their lifespan.
Remember to document and communicate the chosen storage methods to your team members or employees. This ensures consistency and helps everyone adhere to the established storage protocols.
By determining appropriate storage methods, you can protect your stock items, optimize space utilization, and ensure that the storage solutions align with the specific needs of each category of products.
Step 4: Label your stock
Labeling your stock is a crucial step in maintaining organization and ease of inventory management. Proper labeling enables quick identification of items, reduces errors in picking or restocking, and allows for efficient tracking of stock levels. Follow these tips to effectively label your stock:
- Clear and consistent labeling: Use clear and legible labels that can be easily read from a distance. Ensure consistency in labeling format, font size, and placement to avoid confusion.
- Include essential information: Each label should include important information such as the product name or code, category, batch or lot number, expiration date (if applicable), and any other relevant details for identification or tracking purposes.
- Barcode or QR codes: Consider incorporating barcodes or QR codes on the labels. This allows for automated scanning and tracking of stock using inventory management systems, saving time and minimizing human errors.
- Color-coded labels: Utilize color-coded labels to visually distinguish between different categories or characteristics of your stock. For example, you can use different colors to signify different product types or indicate urgency for restocking.
- Location labels: It can be helpful to place additional labels on storage shelves or bins to indicate the specific location where each item should be stored. This ensures proper placement during restocking and facilitates easier item retrieval.
Regularly review and update your labels as needed. If there are any changes in product information, such as batch numbers or expiry dates, make sure to update the labels accordingly to maintain accuracy.
Proper labeling not only streamlines the storage and retrieval process but also improves inventory accuracy, reduces the risk of mistakes, and enhances overall stock management efficiency.
By implementing clear and consistent labeling practices, you can easily identify and track your stock items, leading to smoother operations and improved productivity.
Read more: How To Store Homemade Stock
Step 5: Implement a first-in, first-out (FIFO) system
Implementing a first-in, first-out (FIFO) system is an essential practice to ensure that your stock does not become outdated or spoil. FIFO is a method of inventory management where the oldest stock is used or sold first, reducing the risk of stock obsolescence or expiration. Here’s how you can implement a FIFO system:
- Organize stock based on arrival date: Arrange your stock in such a way that the oldest items are positioned in the front or at the top, while the newer items are placed towards the back or at the bottom. This ensures that the oldest stock is used first.
- Regular stock rotation: Regularly rotate your stock to ensure that older items are brought to the front or top for utilization. This involves periodically reviewing stock levels, moving older items forward, and placing newer items at the back.
- Monitoring expiry dates: If you deal with perishable or time-sensitive items, closely monitor the expiry dates and prioritize their use or sale accordingly. Use inventory management systems or manual tracking to ensure that items are not kept past their expiration date.
- Proper stock placement: Store your stock in a way that allows for easy identification and access. Label shelves or bins with the arrival date or batch number to facilitate the FIFO system and minimize confusion.
- Employee training: Educate your employees on the importance of the FIFO system and provide training on how to implement it effectively. Encourage them to follow the system consistently to maintain its integrity.
Implementing a FIFO system helps prevent stock wastage, reduces the risk of holding obsolete inventory, and ensures that items are used or sold in a timely manner. By prioritizing older stock, you can reduce costs associated with expired or unsellable items and maintain a fresh and up-to-date inventory.
Regular audits and monitoring of stock levels, along with proper adherence to the FIFO system, will help you make informed purchasing decisions and maintain a healthy stock rotation.
By implementing a robust FIFO system, you can effectively manage your stock inventory and minimize the potential for losses due to stagnant or expired stock.
Store stock in a cool, dry place away from direct sunlight. Keep items off the ground to prevent moisture damage. Use shelves or pallets for proper air circulation. Rotate stock regularly to ensure older items are used first.
Step 6: Regularly check and rotate stock
Regularly checking and rotating your stock is a crucial step in maintaining inventory accuracy and preventing stock obsolescence. By conducting frequent stock inspections and rotation, you ensure that items are used or sold before they become outdated or unusable. Follow these steps to effectively check and rotate your stock:
- Schedule regular stock checks: Set a schedule to conduct regular stock checks to assess the quantity and condition of your inventory. This can be done on a weekly, monthly, or quarterly basis, depending on your business needs.
- Verify stock levels: Compare physical stock levels with your records to ensure accuracy and identify any discrepancies. This helps prevent stock shortages or overstocking.
- Inspect for quality: Examine stock items for any signs of damage, deterioration, or expiration. Discard any items that are past their expiration date or have become unsellable.
- Rotate stock strategically: Implement a rotation system that moves older stock to the front or top of storage shelves, ensuring that it is used or sold first. This helps maintain the FIFO (first-in, first-out) system and prevents stock from becoming obsolete.
- Adjust stock levels: Based on the stock check results, make necessary adjustments to reorder depleted items or reduce excess stock. This helps maintain optimal stock levels and prevents unnecessary storage costs.
- Keep records: Maintain accurate records of stock checks, rotations, and adjustments made. This helps track patterns, identify any recurring issues, and facilitates future stock planning.
Regularly checking and rotating your stock not only ensures inventory accuracy but also helps optimize space utilization and reduce the risk of stock obsolescence. By identifying and addressing any issues promptly, you can maintain a healthy and efficient stock management system.
Remember to involve your team in the stock check and rotation process, as their insights and contributions can improve the overall accuracy and efficiency of the operations.
By regularly checking and rotating your stock, you can stay on top of inventory management, minimize losses, and provide your customers with fresh and up-to-date products.
Step 7: Use appropriate storage containers
Choosing the right storage containers is essential for ensuring the safety, organization, and efficient management of your stock. The appropriate containers will protect your items from damage, facilitate easy access, and maximize storage space. Consider the following factors when selecting storage containers:
- Size and capacity: Determine the appropriate size and capacity of the containers based on the dimensions and quantity of your stock items. Opt for containers that provide enough space for each item without excessive wasted space.
- Durability: Choose containers that are sturdy and durable to withstand the weight and handling of your stock. Consider the material construction, such as plastic, metal, or cardboard, based on the nature of your items and storage conditions.
- Stackability: If you have limited storage space, look for containers that are stackable. This allows you to maximize vertical space and keep your stock organized while also facilitating easy access to items at the bottom.
- Accessibility: Select containers that provide easy access to your stock. Consider options with hinged lids, sliding doors, or removable tops that allow for convenient retrieval and restocking without needing to unpack the entire container.
- Visibility: Transparent or semi-transparent containers can enhance visibility and make it easier to identify items without the need to open each container. This is especially useful when searching for specific items or conducting stock checks.
- Specialized containers: Certain items may require specialized containers to ensure proper storage and protection. For example, you may need anti-static containers for electronic components or airtight containers for perishable goods.
When selecting storage containers, consider the specific needs and characteristics of your stock. Your goal is to choose containers that provide optimal protection, organization, and accessibility, while also considering space efficiency and cost-effectiveness.
Remember to label each container properly to indicate the contents, stock category, and any other relevant information. This helps expedite the retrieval and restocking process.
By using appropriate storage containers, you can maintain the integrity of your stock, minimize the risk of damage, and create a well-organized storage system that maximizes space utilization and efficiency.
Step 8: Consider temperature and humidity control
Controlling the temperature and humidity of your storage area is crucial for preserving the quality and longevity of certain stock items. Temperature and humidity fluctuations can lead to spoilage, deterioration, or damage, especially for sensitive materials. Consider the following steps to ensure proper temperature and humidity control:
- Evaluate stock requirements: Identify the stock items that are sensitive to temperature or humidity variations. This can include perishable goods, electronics, pharmaceuticals, or delicate materials.
- Set temperature and humidity parameters: Determine the ideal temperature and humidity levels for your storage area based on the requirements of your stock items. Consult product specifications or guidelines from manufacturers or regulatory bodies for recommendations.
- Invest in climate control systems: Install climate control systems, such as air conditioning units, dehumidifiers, or humidifiers, to regulate temperature and humidity levels. These systems help maintain a consistent environment for your stock.
- Monitor and adjust: Regularly monitor temperature and humidity levels using thermometers and hygrometers. Make necessary adjustments to the climate control systems as needed to maintain optimal conditions.
- Insulate storage area: Ensure that your storage area is properly insulated to prevent external factors, such as extreme weather or temperature changes, from affecting the internal environment. This includes sealing windows, doors, and any gaps that might allow outside air to enter.
- Separate temperature-sensitive stock: If possible, store temperature-sensitive stock items in a separate area or a designated climate-controlled room to provide additional protection.
- Backup power supply: Consider having a backup power supply, such as a generator or battery-powered devices, to ensure that your climate control systems continue operating during power outages.
Proper temperature and humidity control play a crucial role in preventing stock degradation, extending shelf life, and preserving the value of your items. By creating and maintaining a controlled environment, you can protect your stock from adverse conditions and ensure its quality for a longer period.
Remember to regularly inspect and maintain your climate control systems to ensure they are functioning properly and providing the required conditions for your stock items.
By considering temperature and humidity control, you can safeguard your stock and enhance its longevity, ultimately reducing the risk of losses due to spoiled or damaged items.
Read more: How To Store Chicken Stock
Step 9: Ensure proper lighting in the storage area
Proper lighting in your storage area is essential for maintaining a safe and efficient environment. Good lighting enhances visibility, reduces the risk of accidents or injuries, and facilitates easy stock identification and retrieval. Consider the following steps to ensure proper lighting in your storage area:
- Assess lighting needs: Evaluate the size and layout of your storage area to determine the lighting requirements. Consider factors such as ceiling height, aisle width, and the type of stock being stored.
- Choose appropriate lighting fixtures: Select lighting fixtures that are suitable for the storage area. It is important to choose fixtures that are durable, energy-efficient, and capable of providing adequate illumination for the entire space.
- Position lighting strategically: Place lighting fixtures strategically to ensure even distribution of light throughout the storage area. Avoid shadows or dark spots that can hinder visibility or make it difficult to locate items.
- Consider natural light: If possible, utilize natural light sources such as windows or skylights to supplement artificial lighting. However, be cautious of potential issues such as glare or excessive heat that may affect the stock.
- Install motion-activated lighting: Consider installing motion-activated lighting systems or sensors. This ensures that the lights will automatically turn on when someone enters the storage area, improving energy efficiency and safety.
- Maintain and clean light fixtures: Regularly clean the light fixtures and remove any obstructions to maintain optimal illumination. Replace any burnt-out bulbs or faulty fixtures promptly to avoid dark areas.
Proper lighting in the storage area not only enhances safety but also increases productivity and reduces the chances of errors or accidents. Employees will be able to locate and handle stock efficiently, leading to smoother operations and improved overall efficiency.
Remember to consider the specific requirements of your stock items. Some products may be sensitive to light exposure, so ensure that the lighting level is appropriate to prevent any potential damage or degradation.
By ensuring proper lighting in your storage area, you create a well-lit and safe environment that enables easy accessibility and efficient stock management.
Step 10: Maintain cleanliness and pest control
Maintaining cleanliness and implementing effective pest control measures in your storage area are vital for preserving the quality and integrity of your stock. A clean and pest-free environment ensures that your items remain free from contamination and damage. Follow these steps to maintain cleanliness and implement pest control in your storage area:
- Establish cleaning protocols: Develop a regular cleaning schedule for your storage area. Assign specific tasks, such as sweeping, dusting, and disinfecting, to ensure that all areas are consistently maintained.
- Remove clutter: Regularly remove any unnecessary items or clutter from your storage area. This not only improves organization but also eliminates potential hiding places for pests.
- Proper waste management: Dispose of waste properly and promptly. Regularly empty trash cans, use sealed containers for garbage, and implement recycling practices as applicable. This helps prevent attracting pests and maintains cleanliness.
- Seal entry points: Inspect the storage area for any cracks, gaps, or openings that pests could use to gain access. Seal these entry points to prevent pests from entering the storage area.
- Implement pest monitoring: Set up pest monitoring devices, such as traps or baits, to detect any signs of pest activity. Regularly check and maintain these devices and address any pest issues promptly.
- Engage professional pest control services: Consider hiring professional pest control services to conduct regular inspections and implement pest control measures. They can help identify potential pest problems and suggest appropriate solutions.
- Train employees: Educate your employees about the importance of cleanliness and pest control. Encourage them to report any signs of pests and provide training on how to prevent pest infestations.
- Use pest-resistant storage solutions: Consider using pest-resistant containers or materials for storing your stock. This can include using sealed plastic bins, metal shelving, or storing items on pallets to minimize direct contact with the floor.
- Regularly inspect incoming stock: Inspect incoming stock for signs of pests before storing them. This prevents introducing pests into your storage area and spreading infestations.
Maintaining cleanliness and implementing effective pest control measures help protect your stock from damage, contamination, and potential loss. By creating a clean and pest-free environment, you ensure that your stock remains in optimal condition.
Remember to comply with any applicable health and safety regulations when implementing pest control measures and using pest control products.
By prioritizing cleanliness and pest control, you maintain a hygienic and secure storage area that preserves the quality and value of your stock.
Conclusion
Properly storing your stock is essential for efficient inventory management and ensuring the longevity and quality of your items. By following the ten steps outlined in this article, you can establish an organized and effective stock storage system that optimizes accessibility, minimizes damage, and prevents inventory expiration. Let’s recap the steps:
- Choose the right storage area that meets your space, security, and accessibility needs.
- Organize your stock by category for easy identification and retrieval.
- Determine appropriate storage methods based on the size, weight, and fragility of your items.
- Label your stock accurately to facilitate tracking and prevent confusion.
- Implement a first-in, first-out (FIFO) system to prevent stock obsolescence.
- Regularly check and rotate stock to maintain inventory accuracy and prevent expiration.
- Use appropriate storage containers to protect your items and maximize space utilization.
- Consider temperature and humidity control to preserve the quality of sensitive stock.
- Ensure proper lighting in the storage area for visibility and safety.
- Maintain cleanliness and implement effective pest control measures to prevent contamination and damage.
By following these steps, you can create a well-organized, safe, and efficient storage environment for your stock. Always remember to periodically review and update your storage system as needed to accommodate changes in inventory and optimize stock management.
Effective stock storage not only leads to improved productivity but also minimizes losses, reduces wastage, and enhances customer satisfaction. It allows you to easily locate and access items, fulfill orders promptly, and maintain the overall integrity of your stock.
Investing time and effort into implementing these steps will pay off in the long run, as you’ll have a storage system that is tailored to your needs and promotes a smooth and successful stock management process.
So, take control of your stock storage today and enjoy the benefits of a well-organized and optimized inventory management system!
Frequently Asked Questions about How To Store Stock
Was this page helpful?
At Storables.com, we guarantee accurate and reliable information. Our content, validated by Expert Board Contributors, is crafted following stringent Editorial Policies. We're committed to providing you with well-researched, expert-backed insights for all your informational needs.
0 thoughts on “How To Store Stock”