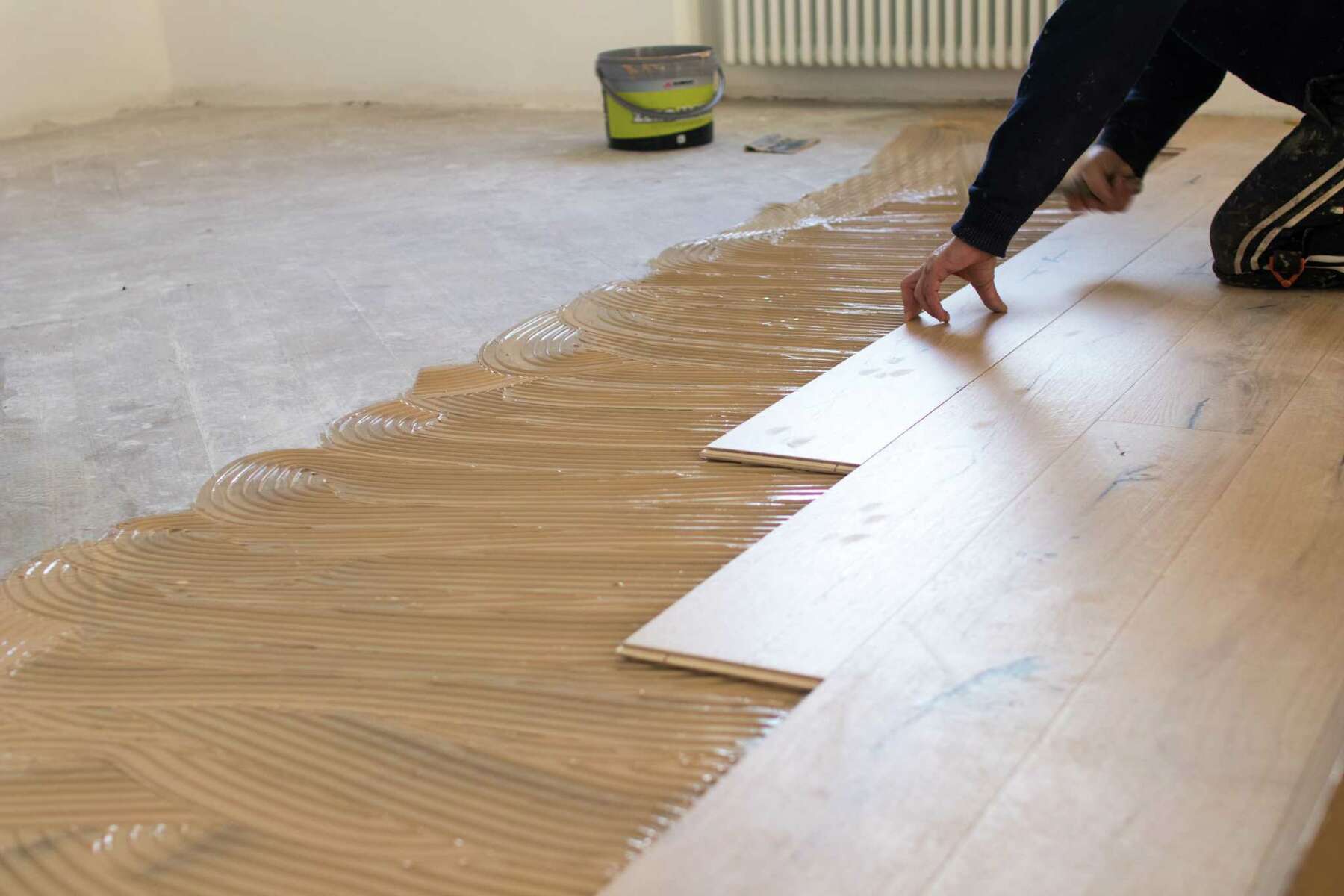
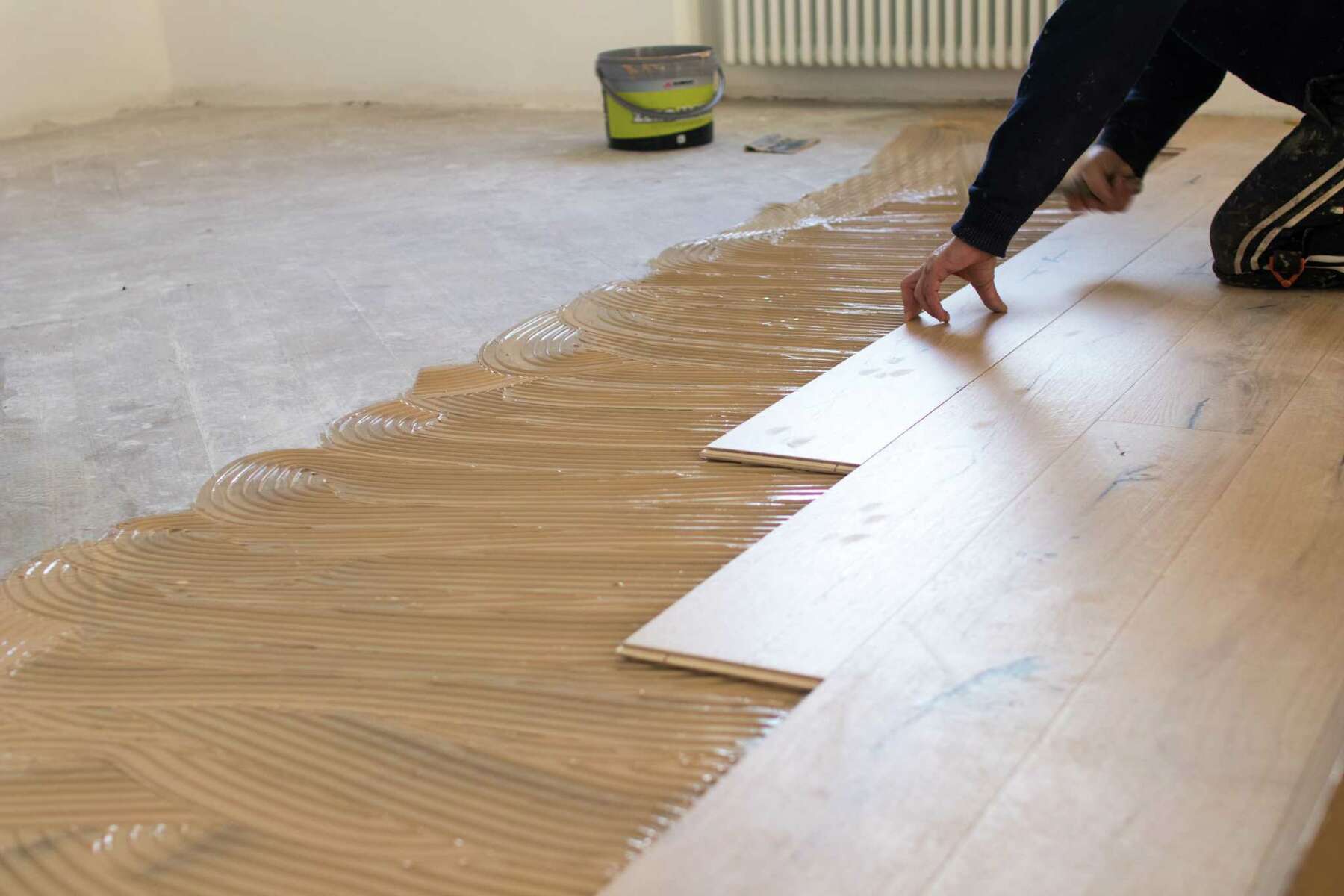
Articles
What Is A Subfloor
Modified: September 1, 2024
Discover everything you need to know about sub floors in this comprehensive collection of informative articles. Explore different types, installation methods, and maintenance tips.
(Many of the links in this article redirect to a specific reviewed product. Your purchase of these products through affiliate links helps to generate commission for Storables.com, at no extra cost. Learn more)
What is a Subfloor?
A subfloor is a crucial structural component of a building’s flooring system. It is a layer of material that is installed directly on the joists and serves as a foundation for the finished flooring material. The subfloor provides stability and support to the floor, ensuring it remains level and durable.
The main purpose of a subfloor is to create a solid and even surface for the finished flooring material, such as hardwood, laminate, tile, or carpet, to be installed on. It acts as a buffer between the structural components of the building and the visible flooring, preventing any damage or wear from being directly absorbed by the underlying structure.
Subfloors also play a crucial role in soundproofing and insulation. They help to reduce noise transfer between levels of a building and provide a layer of insulation against heat loss or gain from the ground or lower levels.
Subfloors are typically made of different materials depending on the building design, budget, and the type of finished flooring to be installed. The most common types of subfloors include concrete, plywood, and particle board.
Key Takeaways:
- A subfloor is a critical component of a building’s flooring system, providing stability, soundproofing, and insulation. Proper material selection, installation, and maintenance are essential for long-term durability and performance.
- Subfloors offer advantages such as enhanced structural integrity and versatility, but also come with considerations like moisture issues and potential squeaking. Careful preparation, installation, and maintenance are key to maximizing the lifespan of the flooring system.
Read more: How To Install Subfloor Over A Crawl Space
Definition
A subfloor is a structural layer of material that is installed on the joists of a building’s flooring system. It serves as a foundation for the finished flooring material and provides stability and support to the floor. The subfloor acts as an intermediate layer between the structural components of the building and the visible flooring, protecting the underlying structure from wear and tear.
The subfloor is an essential component of any building’s flooring system and is responsible for ensuring that the finished flooring remains level, durable, and properly installed. It acts as a base on which the flooring material is installed, creating a solid and smooth surface.
Depending on the type of building and the intended use of the space, different materials can be used for the subfloor. The choice of material will depend on factors such as cost, location, building regulations, and the type of finished flooring to be installed.
Overall, a subfloor is a critical element in the construction of a building. It provides structural integrity, stability, and support to the floor, while also offering soundproofing and insulation qualities. Without a properly installed and well-maintained subfloor, the integrity and longevity of the finished flooring material can be compromised.
Importance of a Subfloor
The subfloor is an integral part of any building’s flooring system and plays a vital role in ensuring the stability, durability, and overall performance of the finished flooring. Here are some key reasons why a subfloor is important:
1. Supports the Flooring:
The subfloor provides a sturdy foundation for the finished flooring material to be installed on. It distributes the weight evenly across the floor, preventing sagging or unevenness. This support is crucial for ensuring the longevity and structural integrity of the flooring.
2. Enhances Stability:
A well-constructed subfloor helps to stabilize the flooring system by minimizing movement or flexing, which can lead to damage or dislodging of the finish flooring. It acts as a stable base that holds everything together, providing a solid, level surface for walking and other activities.
3. Reduces Noise:
The subfloor contributes to soundproofing by absorbing and reducing noise transfer between different levels of a building. It helps to minimize the impact of footsteps or other sounds, ensuring a more peaceful and comfortable environment.
4. Provides Insulation:
Subfloors also offer insulation properties by creating a barrier against heat loss or gain from the ground or lower levels. This insulation helps to maintain a consistent indoor temperature, resulting in energy savings and improved comfort.
5. Protects the Structure:
The subfloor acts as a protective layer between the visible flooring and the underlying structure of the building. It prevents moisture from seeping into the joists, which can lead to rot, mold, or structural damage. By keeping the structural components dry and protected, the subfloor helps to maintain the overall integrity of the building.
In summary, the subfloor is crucial for the stability, durability, and performance of a building’s flooring system. It supports the finished flooring, enhances stability, reduces noise, provides insulation, and protects the underlying structure. Investing in a high-quality subfloor ensures that the finished flooring material will perform optimally and stand the test of time.
Types of Subfloors
Subfloors can be constructed using several different materials, each offering its own unique characteristics and advantages. The choice of subfloor material will depend on factors such as the building design, budget, and the type of finished flooring to be installed. Here are some of the most common types of subfloors:
1. Concrete Subfloors:
Concrete subfloors are commonly found in basements and ground-level areas. They are made of a poured or precast concrete slab that provides a strong and durable foundation for the finished flooring. Concrete subfloors are known for their excellent moisture resistance, making them suitable for areas prone to moisture or humidity. They are commonly used for tile, hardwood, and laminate flooring installations.
2. Plywood Subfloors:
Plywood subfloors consist of multiple layers of wood veneers glued together. They are strong, stable, and offer excellent dimensional stability. Plywood subfloors are highly versatile and can be used with various types of finished flooring materials. They are popular for their affordability and ease of installation. Plywood subfloors are often used in residential and commercial buildings.
3. Particle Board Subfloors:
Particle board subfloors are made from wood particles, fibers, and adhesives that are compressed together. They are affordable and easy to install, making them popular in residential construction. However, particle board subfloors are less durable than other types and can be easily damaged by moisture or impact. They are commonly used for carpet and vinyl flooring installations.
4. OSB (Oriented Strand Board) Subfloors:
OSB subfloors are made from wood strands or flakes that are oriented in multiple layers and bonded together with adhesives. They offer good stability, strength, and moisture resistance. OSB subfloors are commonly used in residential and commercial construction and can be used with a variety of finished flooring materials.
Read more: What Is a Kegerator and What Is It Used For?
5. Gypsum Fiberboard Subfloors:
Gypsum fiberboard subfloors are made from a combination of wood fibers and gypsum. They are moisture-resistant, lightweight, and easy to install. Gypsum fiberboard subfloors are commonly used in areas where moisture is a concern, such as bathrooms or kitchens, and can be paired with a wide range of finished flooring materials.
Each type of subfloor material has its own advantages and considerations. It’s important to select the appropriate subfloor material based on the specific requirements of your project, including the type of finished flooring, the location of the installation, and the level of moisture or humidity in the area.
Concrete Subfloors
Concrete subfloors are a popular choice for basements, ground-level areas, or buildings with concrete slab foundations. They provide a strong and durable foundation for various types of finished flooring materials, including tile, hardwood, and laminate. Concrete subfloors offer several advantages and considerations that are important to understand before installation.
Advantages of Concrete Subfloors:
1. Strength and Durability: Concrete is known for its exceptional strength and durability. It can withstand heavy loads and is resistant to wear and tear, making it an ideal choice for high-traffic areas.
2. Moisture Resistance: Concrete has inherent moisture resistance properties, making it suitable for areas prone to moisture or humidity. It helps prevent moisture from seeping into the subfloor and causing damage to the finished flooring above.
3. Stability: Concrete subfloors offer excellent dimensional stability, meaning they are less likely to expand or contract with changes in temperature and humidity. This stability helps to maintain the integrity and flatness of the finished flooring.
4. Compatibility: Concrete subfloors are compatible with a wide range of finished flooring materials. Whether you prefer tile, hardwood, laminate, or even carpet, concrete subfloors can accommodate different installation methods and provide a solid base for the flooring material.
Considerations for Concrete Subfloors:
1. Moisture Testing: Before installing any finished flooring on a concrete subfloor, it is important to conduct a moisture test. Excess moisture in the subfloor can lead to delamination, warping, or mold growth. Proper moisture mitigation measures, such as sealing or the use of moisture barriers, may be necessary depending on the test results.
2. Subfloor Preparation: Concrete subfloors need to be properly prepared before installation. This includes ensuring the surface is clean, level, and free of any debris, cracks, or imperfections that could affect the adhesion or installation of the finished flooring.
3. Thermal Insulation: Concrete subfloors have a tendency to feel cold, especially in colder climates. To improve thermal comfort, consider adding a layer of underlayment with insulation properties before installing the finished flooring. This will help to minimize heat loss and create a more comfortable living environment.
4. Subfloor Height: Concrete subfloors can increase the overall height of the floor. This may require adjustments to door heights, transitions between rooms, and consideration of any baseboards or trim that may need to be adjusted or replaced to accommodate the change in height.
Concrete subfloors are a popular choice due to their strength, durability, and moisture resistance. However, proper preparation and moisture testing are essential to ensure a successful installation and to maintain the integrity of the finished flooring material.
Read more: Juicer vs Blender: What’s The Difference?
Plywood Subfloors
Plywood subfloors are a versatile and popular choice for both residential and commercial buildings. They consist of multiple layers of wood veneers that are glued and pressed together to form a sturdy and stable subflooring material. Plywood subfloors offer several advantages and considerations that are important to understand before installation.
Advantages of Plywood Subfloors:
1. Strength and Stability: Plywood subfloors are known for their strength and stability. They provide a solid and durable base for the finished flooring, ensuring it remains level and resistant to movement or flexing. Plywood’s strength also makes it suitable for heavy load-bearing applications.
2. Dimensional Stability: Plywood is less prone to expansion and contraction compared to other subfloor materials. It has excellent dimensional stability, meaning it is less likely to warp or develop gaps due to changes in temperature and humidity. This stability helps to maintain the integrity and flatness of the finished flooring.
3. Versatility: Plywood subfloors are compatible with a wide range of finished flooring materials, including hardwood, laminate, vinyl, and carpet. They can be installed using different methods, such as glue-down, nail-down, or floating installations. This versatility allows for more flexibility in design and flooring choices.
4. Ease of Installation: Plywood subfloors are relatively easy to install. They come in standard 4×8-foot sheets and can be easily cut to fit the desired area. Plywood’s uniform thickness and consistent quality make installation smoother and quicker than other subfloor materials.
Considerations for Plywood Subfloors:
1. Moisture Protection: Plywood is susceptible to damage from moisture, so it is important to take proper precautions to protect it. Before installation, it is recommended to apply a moisture barrier or vapor barrier to prevent moisture from penetrating the subfloor. In areas prone to moisture, such as bathrooms or basements, using exterior-grade plywood or a waterproofing membrane is advisable.
2. Subfloor Preparation: Like any subfloor material, proper preparation is crucial for plywood subfloors. Before installation, ensure the surface is clean, level, and free from debris or protrusions that could affect the installation of the finished flooring. Any loose or damaged sections of plywood should be repaired or replaced before proceeding with the flooring installation.
3. Squeak Prevention: Plywood subfloors may develop squeaks over time. To minimize this issue, it is recommended to use a combination of adhesive and mechanical fasteners, such as nails or screws, during installation to secure the plywood sheets firmly to the joists. Additionally, ensuring proper spacing and nailing patterns can help reduce the occurrence of squeaks.
4. Insulation: Plywood subfloors don’t offer much in terms of thermal insulation. To improve energy efficiency and comfort, consider adding a layer of underlayment with insulation properties before installing the finished flooring.
Plywood subfloors are a popular choice due to their strength, stability, versatility, and ease of installation. By taking appropriate moisture protection measures and following proper installation guidelines, plywood subfloors can provide a solid and reliable foundation for various types of finished flooring materials.
Particle Board Subfloors
Particle board subfloors are a cost-effective option for residential construction and are commonly used in areas where carpet or vinyl flooring will be installed. They are made from wood particles, fibers, and adhesives that are compressed together to form a solid panel. Particle board subfloors offer certain advantages and considerations that should be taken into account before installation.
Advantages of Particle Board Subfloors:
1. Affordability: Particle board subfloors are relatively inexpensive compared to other subfloor materials. They are a budget-friendly option for homeowners or contractors looking to keep costs down.
2. Easy Installation: Particle board subfloors are lightweight and easy to install. They come in standard 4×8-foot sheets and can be cut to fit the desired area. This ease of installation can save time and labor during the construction process.
3. Sound Absorption: Particle board subfloors offer good sound absorption properties. They can help reduce noise transmission between floors, creating a quieter and more comfortable living environment.
4. Smooth Surface: Particle board subfloors typically have a smooth surface, making it suitable for carpet or vinyl flooring installations. This smoothness allows for a seamless look once the finished flooring is installed.
Considerations for Particle Board Subfloors:
1. Moisture Sensitivity: Particle board is highly susceptible to moisture damage. It can easily swell or warp when exposed to excessive moisture. Therefore, particle board subfloors should only be used in areas where moisture is not a concern, such as bedrooms or living rooms. It is not recommended for use in bathrooms, kitchens, or basements.
2. Lack of Structural Strength: Particle board has lower structural strength compared to other subfloor materials. It is more prone to dents, scratches, and damage from heavy loads or impacts. It is important to take extra precautions to protect the subfloor during construction or renovation processes.
3. Limited Compatibility: Particle board subfloors are primarily suited for carpet or vinyl flooring installations. They are not recommended for use under hardwood, tile, or laminate flooring due to their limited structural integrity and susceptibility to moisture damage.
4. Limited Lifespan: Particle board subfloors tend to have a shorter lifespan compared to other subfloor materials. With time and wear, they can break down or degrade, impacting the overall stability and performance of the finished flooring.
When considering particle board subfloors, it is crucial to assess environmental conditions, intended use, and future flooring plans. Proper moisture protection measures and regular maintenance are essential to prolonging the lifespan and ensuring the functionality of particle board subfloors.
Advantages of a Subfloor
A subfloor is an essential component of a building’s flooring system and offers several advantages that contribute to the overall stability, durability, and performance of the finished flooring. Here are some key advantages of having a subfloor:
1. Enhanced Structural Integrity:
A subfloor provides a solid and stable foundation for the finished flooring material. It helps to distribute the weight of foot traffic, furniture, and other loads evenly across the floor, reducing the risk of sagging, flexing, or damage to the underlying structure. This enhanced structural integrity ensures that the floor remains level, safe, and long-lasting.
Read more: Rattan vs Wicker: What’s The Difference?
2. Improved Soundproofing:
A well-insulated subfloor can significantly reduce noise transmission between floors. It acts as a buffer, absorbing and minimizing the transfer of footsteps, voices, and other sounds. This improved soundproofing creates a quieter and more peaceful indoor environment, enhancing comfort and privacy.
3. Moisture Protection:
Many subfloor materials offer inherent moisture resistance or can be paired with moisture barriers, helping to protect the underlying structure from water damage. Moisture can seep through the finished flooring, especially in areas like bathrooms or kitchens, and cause mold, rot, or structural problems. A subfloor acts as a barrier, preventing moisture from reaching the structural components.
4. Thermal Insulation:
Depending on the type of subfloor material and additional insulation layers, a subfloor can provide thermal insulation properties. It helps to reduce heat loss or gain from the ground or lower levels, improving energy efficiency and maintaining a comfortable indoor temperature. This can lead to energy savings and a more environmentally friendly building.
5. Versatility and Compatibility:
A subfloor provides a versatile platform that is compatible with various types of finished flooring materials. Whether it’s hardwood, tile, laminate, carpet, or vinyl, the subfloor accommodates different installation methods and ensures a proper and secure attachment of the flooring. It allows for flexibility in design and the ability to change or update the flooring in the future.
Read more: What Is Vegan Leather and What Is It Made Of
6. Easy Maintenance and Repairs:
A subfloor simplifies the maintenance and repair process of the finished flooring. If damage or wear occurs, it is often easier and more cost-effective to repair or replace the top layer than to address issues within the subfloor or structural components. The subfloor acts as a protective buffer, extending the lifespan and minimizing repair needs.
In summary, a subfloor offers numerous advantages that contribute to the overall quality and longevity of a building’s flooring system. It enhances structural integrity, improves soundproofing, provides moisture protection and thermal insulation, offers versatility and compatibility with different flooring materials, and simplifies maintenance and repairs. Investing in a well-designed and properly maintained subfloor is crucial for ensuring a stable, comfortable, and durable flooring surface.
Disadvantages of a Subfloor
While subfloors offer numerous advantages, it is important to consider the potential disadvantages they may have. Here are some key disadvantages of subfloors:
1. Increased Construction Costs:
Subfloors can add to the overall cost of construction or renovation projects. The cost of materials, labor, and installation associated with a subfloor can increase the budget, especially if high-quality materials or specialized installation techniques are required.
2. Height Increase:
Installing a subfloor can increase the overall height of the floor. This can pose challenges when transitioning between rooms or when adjusting door heights. It may require modifications to baseboards, door frames, or other elements to accommodate the change in floor height, which can add additional complexity and cost to the project.
Read more: What Is A Bathtub?
3. Limited Ceiling Height:
In some cases, installing a subfloor can reduce the ceiling height of a space. This can be a concern, especially in areas with low ceiling clearances, as it may make the room feel smaller or claustrophobic. Proper planning and consideration are needed to ensure sufficient headroom is maintained.
4. Moisture and Mold Issues:
Subfloors, particularly those made from materials that are susceptible to moisture damage, such as particle board or certain types of plywood, can be vulnerable to moisture accumulation and mold growth. Moisture can seep through cracks or gaps in the finished flooring or from the surrounding environment, leading to a damp subfloor and potential mold issues if not properly addressed and maintained.
5. Squeaking or Creaking:
Over time, subfloors can develop squeaks or creaks, especially if there are gaps or movement between the subfloor and the joists. This can be a source of annoyance and discomfort, as the noise can be amplified throughout the space. Proper installation techniques and addressing any subfloor movement can help minimize this issue.
6. Difficult Repairs:
If a subfloor becomes damaged or requires repairs, it can be more challenging and time-consuming to fix compared to surface-level issues with the finished flooring. Repairing or replacing a subfloor often involves extensive work and may require professionals to ensure proper structural integrity is maintained.
Overall, while subfloors offer many benefits, they can introduce additional costs, height constraints, potential moisture and mold issues, squeaking or creaking noises, and complex repair processes. These disadvantages should be taken into consideration when planning and designing the flooring system to ensure the best possible outcome for the project.
Read more: What Is Woodworking
Common Issues with Subfloors
While subfloors play a crucial role in providing stability and support to the finished flooring, they can be susceptible to various issues that can impact their performance. Here are some of the most common issues that can arise with subfloors:
1. Moisture Damage:
Subfloors, especially those made from wood or wood-based materials like plywood or particle board, are vulnerable to moisture damage. Excessive moisture, whether from leaks, floods, or elevated humidity levels, can cause swelling, warping, or rotting of the subfloor material. This can compromise the structural integrity and lead to the growth of mold and mildew.
2. Subfloor Movement:
Subfloor movement can occur when the subfloor material becomes loose or detached from the underlying joists. This can cause squeaking, creaking noises, or an uneven flooring surface. Subfloor movement can be due to insufficient fasteners, improper installation, or structural issues. It is important to address subfloor movement promptly to prevent further damage and ensure a safe and stable flooring system.
3. Subfloor Unevenness:
An uneven subfloor can lead to noticeable issues with the finished flooring, such as gaps, bulges, or an uneven appearance. Unevenness can be caused by variations in the subfloor material, improper installation, or settling of the building foundation. It is essential to properly level and prepare the subfloor before installing the finished flooring to ensure a smooth and even surface.
Read more: What Is Dinnerware?
4. Subfloor Moisture-related Issues:
Moisture-related issues with subfloors can include mold and mildew growth, musty odors, and the release of moisture into the living space. Subfloor moisture issues can be caused by poor ventilation, high humidity levels, or moisture infiltration from the ground or other sources. Proper moisture mitigation measures, such as moisture barriers or ventilation systems, should be implemented to prevent these issues.
5. Subfloor Insufficient Strength:
Some subfloor materials may have insufficient strength to support heavy loads or withstand high foot traffic. This can lead to flexing, sagging, or even cracking of the subfloor, which can result in damages to the finished flooring. Choosing a subfloor material that is appropriate for the intended use and following proper installation methods can help mitigate this issue.
6. Subfloor Dust and Debris:
Dust and debris can accumulate within the subfloor structure over time, especially in unfinished basements or crawl spaces. This can be a breeding ground for pests, allergens, and odors. Regular cleaning and maintenance of the subfloor area, including vacuuming or sweeping, can help prevent the buildup of dust and debris.
Regular inspections and maintenance are essential to identify and address these common issues with subfloors. Proper installation, moisture management, and routine care will help ensure the longevity and performance of both the subfloor and the finished flooring above.
Subfloor Installation Process
The installation of a subfloor is a critical step in the construction or renovation of a building’s flooring system. Proper installation ensures the stability, durability, and performance of the finished flooring. Here is a general overview of the subfloor installation process:
Read more: What Are Calipers
1. Assess and Prepare the Space:
Before installing the subfloor, assess the space and ensure that the area is clean, structurally sound, and free from any debris or obstacles that may interfere with the installation. Take accurate measurements and determine the required quantity of subfloor material.
2. Choose the Subfloor Material:
Select the appropriate subfloor material based on factors such as building design, budget, and the type of finished flooring to be installed. Common subfloor materials include concrete, plywood, or particle board. Consider the specific requirements of the project, including moisture resistance, strength, and compatibility with the finished flooring.
3. Acclimate the Subfloor Material:
If using plywood or other wood-based subfloor materials, it is important to acclimate the lumber to the environment where it will be installed. This allows the material to adjust to the moisture content and prevent any warping or expansion issues after installation.
4. Mark the Layout:
Determine the layout of the subfloor, keeping in mind any recommended patterns or installation guidelines specific to the chosen subfloor material. Use a measuring tape, level, and chalk lines to mark the layout on the floor, ensuring proper alignment and squareness.
Read more: What Is Spikeball?
5. Cut and Install the Subfloor Material:
If using plywood or particle board, measure and cut the subfloor panels to fit the marked layout. Begin installing the subfloor panels at one corner of the room, working your way across and ensuring a snug fit between panels. Secure the subfloor panels to the underlying joists using appropriate fasteners, such as screws or nails, as recommended by the manufacturer.
6. Check for Levelness and Stability:
As you install each subfloor panel, check for levelness and stability. Use a level to ensure the panels are even, and make any necessary adjustments to achieve a level surface. Ensure that each panel is securely fastened to the joists, minimizing any movement or flexing.
7. Fill Gaps and Seal the Subfloor:
Fill any gaps between subfloor panels with a suitable filler material to create a smooth surface. This will help prevent squeaks or creaks and ensure a level finished flooring installation. Additionally, consider sealing the subfloor with an appropriate sealant or moisture barrier to provide additional protection against moisture damage.
8. Allow for Proper Drying and Curing:
If using materials such as concrete, allow sufficient time for drying or curing. Follow the manufacturer’s instructions for recommended drying or curing time before proceeding with the installation of the finished flooring.
Read more: What Is Lemongrass For
9. Conduct a Final Inspection:
Once the subfloor installation is complete, conduct a final inspection to ensure that the subfloor is level, stable, and free from any visible issues. Address any remaining concerns or discrepancies before proceeding with the installation of the finished flooring.
Remember that the specific installation process may vary based on the chosen subfloor material and the requirements of the project. It is essential to follow the manufacturer’s instructions and consult with professionals when needed to ensure a successful and durable subfloor installation.
Subfloor Preparation
The preparation of the subfloor is a crucial step in ensuring a successful and durable flooring installation. Proper subfloor preparation creates a stable and smooth foundation for the finished flooring material. Here are the key steps involved in subfloor preparation:
1. Remove Existing Flooring:
If there is existing flooring in the space, remove it to expose the subfloor. This may involve removing carpet, tile, vinyl, or any other covering. Ensure that all adhesive, nails, or staples used in the previous flooring are completely removed to provide a clean and level surface for the new subfloor installation.
2. Clean the Subfloor:
Thoroughly clean the subfloor to remove any dirt, dust, or debris. Use a broom, vacuum, or mop to ensure that the surface is clean and free from any loose particles. This will promote better adhesion and bonding of the subfloor material to the underlying structure.
Read more: What Is Television
3. Check for Moisture:
Before proceeding with subfloor installation, it is important to check for moisture issues in the space. Excessive moisture can lead to subfloor damage, mold growth, or flooring issues. Use a moisture meter or conduct a moisture test to assess the moisture content of the subfloor. If high moisture is detected, additional moisture mitigation measures, such as a moisture barrier, may be required.
4. Address Subfloor Unevenness:
Check the subfloor for any unevenness or irregularities. Use a long straightedge or level to identify any high spots, low spots, or significant variations in the subfloor. Unevenness can be corrected by sanding down high spots or filling in low spots with a suitable leveling compound or patching material. This will ensure a level and smooth surface for the subfloor installation.
5. Repair Subfloor Damage:
Inspect the subfloor for any visible damage, such as cracks, loose boards, or rot. Repair or replace any damaged sections of the subfloor to ensure structural stability. Secure loose boards or plywood panels by adding additional screws or nails. It is important to have a solid and stable subfloor to prevent any issues with the finished flooring down the line.
6. Install Subfloor Underlayment:
In certain cases, it may be necessary to install an underlayment on top of the subfloor. Underlayments can provide additional cushioning, soundproofing, or moisture resistance. Follow the manufacturer’s instructions for the specific underlayment material being used. Ensure proper alignment and positioning during installation.
Read more: What Are Coasters For
7. Allow for Subfloor Drying or Acclimation:
If using wood-based subfloor materials such as plywood, give the material sufficient time to acclimate to the environment. This allows the subfloor to adjust to the moisture content and reduce the risk of warping or expansion after installation. Follow the manufacturer’s recommendations for acclimation time.
8. Conduct a Final Inspection:
Once the subfloor preparation is complete, conduct a final inspection to ensure that the subfloor is clean, level, and free from any visible issues. Address any remaining concerns or discrepancies before proceeding with the installation of the finished flooring.
Proper subfloor preparation is essential for a successful flooring installation. Taking the time to prepare the subfloor adequately will not only provide a stable foundation for the finished flooring but also help prevent future issues and ensure the longevity of the flooring system.
Subfloor Maintenance and Repair
Maintaining and repairing the subfloor is crucial for the long-term durability and performance of the flooring system. Proper care and timely repairs ensure that the subfloor remains structurally stable and provides a solid foundation for the finished flooring material. Here are some important considerations for subfloor maintenance and repair:
1. Regular Cleaning:
Keep the subfloor clean by regularly sweeping or vacuuming to remove dust, dirt, and debris. This prevents the accumulation of particles that could potentially scratch or damage the finished flooring. Avoid using excessive water or harsh cleaners that can cause moisture damage to the subfloor. Follow the manufacturer’s recommendations for cleaning the specific subfloor material.
Read more: What Are Coasters For
2. Monitoring Moisture Levels:
Monitor the moisture levels in the subfloor, particularly in areas prone to moisture, such as bathrooms or basements. Excess moisture can lead to subfloor damage, warping, or mold growth. Use a moisture meter to periodically check the moisture content of the subfloor and address any moisture issues promptly. Install proper ventilation systems or dehumidifiers if necessary.
3. Addressing Squeaks or Creaks:
If squeaks or creaks develop in the subfloor over time, it is important to address them promptly. Squeaking noises are often caused by subfloor movement or gaps between the subfloor and the underlying joists. To fix this issue, identify the squeaky areas and secure the subfloor to the joists using appropriate fasteners. This can help to minimize movement and eliminate the unwanted noises.
4. Repairing Subfloor Damage:
If the subfloor becomes damaged, it is essential to repair it as soon as possible. Common subfloor damages include cracks, water damage, or loose boards. Repair any cracks by filling them with a suitable patching compound or epoxy. For water damage, identify the source of the moisture and address it before repairing the affected subfloor sections. If there are loose or damaged boards, secure them with additional nails or screws.
5. Inspecting for Mold or Pest Infestation:
Regularly inspect the subfloor for signs of mold or pest infestation. Mold growth can be a result of moisture issues within the subfloor, while pests like termites can cause structural damage. If mold or pests are found, address the underlying issue and consult with professionals to properly remediate the problem.
Read more: What Are Coasters For
6. Maintaining Proper Temperature and Humidity:
Maintain a stable temperature and humidity level in the space to prevent potential damage to the subfloor. Fluctuations in temperature or humidity can cause the subfloor material to expand or contract, leading to instability or warping. Use a humidifier or dehumidifier to maintain an appropriate humidity level, especially in areas where moisture control is crucial.
7. Consulting Professionals:
If you are unsure about subfloor maintenance or require major repairs, it is recommended to consult with professionals. They can assess the condition of the subfloor, provide expert advice, and perform necessary repairs or maintenance to ensure its longevity and functionality.
By implementing proper maintenance practices and addressing any issues promptly, you can extend the lifespan of the subfloor and maintain a solid foundation for the finished flooring, contributing to the overall durability and performance of the flooring system.
Conclusion
Subfloors play a crucial role in the construction and functionality of a building’s flooring system. They provide stability, support, and protection for the finished flooring, ensuring it remains durable, level, and long-lasting. Proper subfloor installation, maintenance, and repair are essential for achieving optimal performance and maximizing the lifespan of the flooring system.
The selection of the appropriate subfloor material is an important decision that should consider various factors, such as the type of finished flooring, budget, building design, and moisture resistance requirements. Concrete, plywood, and particle board are common subfloor materials, each offering their own advantages and considerations.
Advantages of subfloors include enhanced structural integrity, improved soundproofing, moisture protection, thermal insulation properties, versatility, and compatibility with different flooring materials. However, subfloors come with their own set of considerations and potential disadvantages, such as increased construction costs, height constraints, and potential moisture or squeaking issues.
Proper subfloor preparation is crucial before installation, including removing existing flooring, cleaning the subfloor, checking for moisture, addressing unevenness, and repairing any damage. During installation, it is important to ensure a level, stable, and securely fastened subfloor for optimal performance.
Maintaining the subfloor involves regular cleaning, monitoring moisture levels, addressing squeaks or creaks, repairing damages promptly, inspecting for mold or pest infestation, and maintaining proper temperature and humidity levels. Timely repairs and effective maintenance practices contribute to the overall longevity and functionality of the subfloor and the finished flooring above.
In conclusion, a well-designed, properly installed, and well-maintained subfloor is essential for creating a sturdy, durable, and aesthetically pleasing flooring system. It provides stability, support, and protection for the finished flooring, ensuring optimal performance and longevity. By understanding the importance of subfloors and implementing appropriate measures, you can create a solid foundation for your flooring, enhancing the overall quality and value of your building.
Frequently Asked Questions about What Is A Subfloor
Was this page helpful?
At Storables.com, we guarantee accurate and reliable information. Our content, validated by Expert Board Contributors, is crafted following stringent Editorial Policies. We're committed to providing you with well-researched, expert-backed insights for all your informational needs.
0 thoughts on “What Is A Subfloor”