Home>diy>Building & Construction>What Are Construction Costs
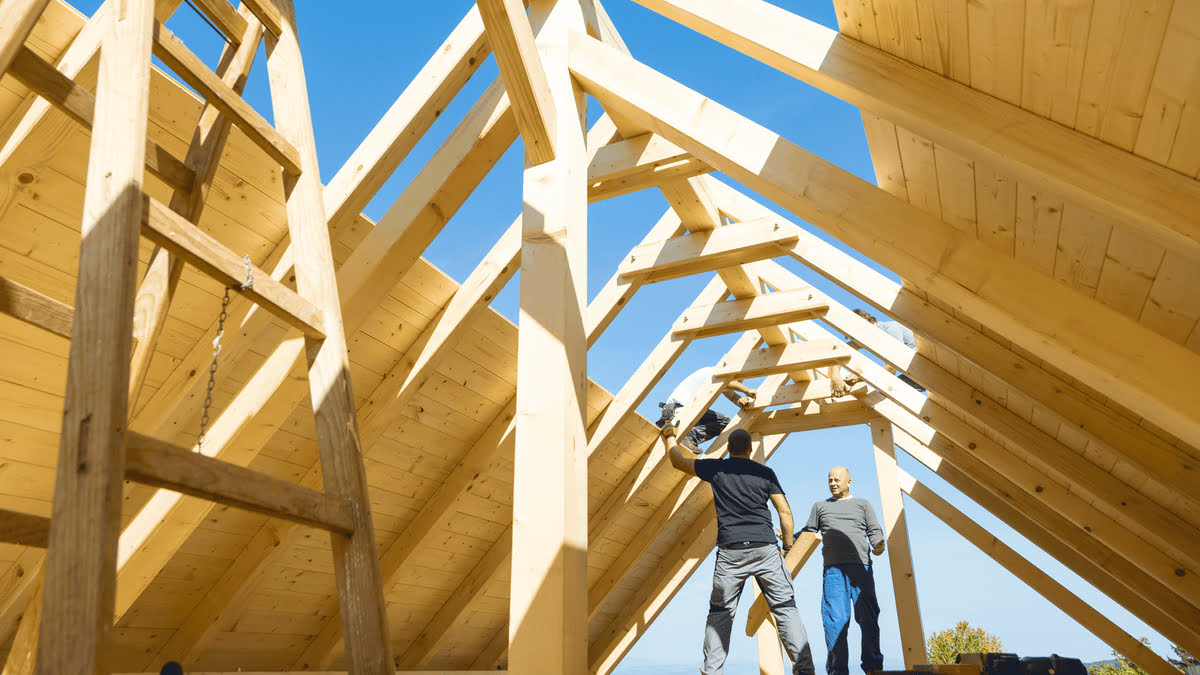
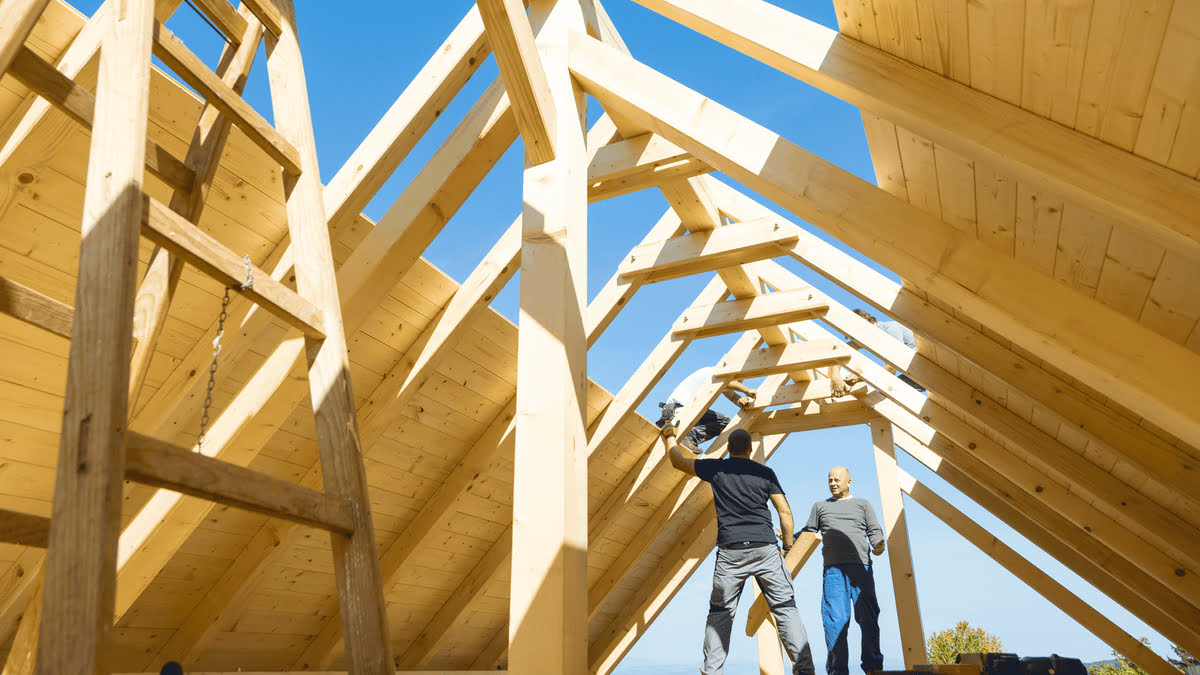
Building & Construction
What Are Construction Costs
Modified: January 24, 2024
Learn about construction costs for building construction and understand the factors that can influence the overall expenses of your construction projects.
(Many of the links in this article redirect to a specific reviewed product. Your purchase of these products through affiliate links helps to generate commission for Storables.com, at no extra cost. Learn more)
Introduction
When undertaking a construction project, one of the most critical factors to consider is the cost. Construction costs encompass a wide range of expenses, including labor, materials, equipment, subcontractors, permits, and more. Understanding the various factors that influence construction costs is essential for proper budgeting and project management.
In this article, we will delve into the key elements that impact construction costs. We’ll explore the different cost components and how they intertwine to determine the overall expense of a construction project. By gaining insight into these factors, you’ll be better equipped to plan and execute your construction projects more efficiently.
So let’s dive in and explore the world of construction costs!
Key Takeaways:
- Understanding the various factors that influence construction costs, from labor and material expenses to overhead and contingency costs, is crucial for accurate budgeting and successful project management.
- By comprehensively considering all cost components, construction professionals can ensure accurate cost estimation, effective resource allocation, and successful project delivery. Regular monitoring, risk assessment, and collaboration are essential for controlling costs and achieving project goals.
Read more: What Are Soft Costs For Construction
Factors Affecting Construction Costs
Construction costs can vary significantly depending on a variety of factors. Understanding and analyzing these factors is crucial for accurate cost estimation and budgeting. Let’s take a look at some of the key factors that can impact construction costs:
- Project Scope: The size and complexity of the project have a significant impact on construction costs. Larger and more complex projects typically require additional resources, materials, and manpower, resulting in higher costs. Factors such as the number of floors, building height, and architectural intricacies all contribute to the overall scope and subsequently affect the cost.
- Location: The location of the construction site can influence costs. Factors such as accessibility, availability of resources, and local building codes and regulations can vary from one location to another. Construction in remote areas may require additional transportation costs for materials and equipment, while construction in urban areas may involve higher land costs and stricter regulations.
- Market Conditions: Construction costs are also influenced by market conditions, including supply and demand dynamics. During times of high demand and limited supply, construction costs tend to rise. Conversely, during periods of low demand, costs may be more competitive.
- Labor Costs: The cost of labor is a significant factor in construction expenses. Skilled labor, such as architects, engineers, and construction workers, commands different rates depending on the region and the complexity of the project. Labor costs can also fluctuate based on market conditions, labor union agreements, and wage scales.
- Material Costs: The cost of building materials, such as concrete, steel, lumber, and electrical components, can greatly impact construction expenses. These costs can fluctuate due to market conditions, availability, and changes in material specifications. Prices can also vary depending on the quality and sourcing of materials.
- Equipment Costs: Construction projects often require specialized equipment, such as cranes, excavators, and scaffolding. Renting or purchasing these equipment can add to the overall project cost. The duration and complexity of the project dictate the type and quantity of equipment needed.
- Subcontractor Costs: Depending on the project, subcontractors may be hired to handle specific tasks, such as plumbing, electrical work, or HVAC installation. The cost of subcontractors can vary depending on their expertise, availability, and market conditions.
- Overhead Costs: Overhead costs include various indirect expenses that are necessary for the overall management and execution of the project. These can include administrative costs, insurance, office rent, utilities, and general project supervision. Overhead costs are typically calculated as a percentage of the direct costs.
It is important to consider these factors comprehensively while assessing construction costs. Each project is unique, and the influence of these elements can vary depending on the specific circumstances. By carefully analyzing these factors and incorporating them into your cost estimation process, you can develop more accurate and realistic construction budgets.
Labor Costs
When it comes to construction projects, labor costs play a crucial role in determining the overall expense. Labor costs can account for a significant portion of the budget, so understanding the factors that influence these costs is essential for accurate cost estimation and project management.
The labor costs in construction projects can be affected by various factors, including:
- Skilled vs. Unskilled Labor: The skills and expertise required for a particular project can impact labor costs. Skilled tradespeople, such as carpenters, electricians, and plumbers, tend to command higher wages due to their specialized knowledge and experience. On the other hand, unskilled laborers who perform general tasks may have lower hourly rates.
- Labor Availability: The availability of labor in a particular region or market can affect costs. In areas with high demand and limited supply of skilled workers, labor costs tend to be higher. Conversely, in regions with a surplus of available workers, labor costs may be more competitive.
- Union Rates: In some regions, construction labor unions set standard wage rates and working conditions for their members. If your project involves unionized workers, you may need to account for union contract requirements and associated costs. Union rates may be higher than non-union rates due to factors such as collective bargaining agreements and benefits provided to workers.
- Project Complexity: The complexity of the construction project can also impact labor costs. Projects that require specialized skills, intricate architectural details, or advanced technical knowledge may require hiring more experienced and highly skilled workers, leading to higher labor costs. Moreover, complex projects often require more time and effort on the part of the workforce, which can also contribute to increased labor expenses.
- Workforce Productivity: The productivity of the construction workforce can have a direct impact on labor costs. Factors such as work ethic, efficiency, and collaboration among team members can affect how quickly tasks are completed and, thus, the overall labor cost. Effective project management and proper coordination can help optimize workforce productivity and minimize labor expenses.
- Overtime and Shift Work: If a construction project requires working overtime or outside of regular hours, labor costs can increase. Overtime wages, shift differentials, and additional labor premiums may need to be factored into the project budget. Proper planning and scheduling can help minimize the need for overtime and associated labor costs.
Navigating labor costs in construction projects requires careful consideration and analysis. It is essential to collaborate closely with contractors, subcontractors, and project managers to assess labor requirements accurately. By understanding the various factors that influence labor costs, you can effectively allocate resources and manage your construction project’s budget.
Material Costs
Material costs are a significant component of construction expenses. The type, quantity, and quality of materials used in a project can greatly influence the overall cost. Understanding the factors that affect material costs is crucial for accurate budgeting and cost estimation in construction projects.
Here are some key factors that can impact material costs:
- Market Conditions: Material costs are subject to market fluctuations. Factors such as supply and demand, inflation, and changes in raw material prices can all affect the cost of construction materials. It’s important to stay up to date with market trends and pricing to anticipate any potential changes in material costs during the project planning stage.
- Material Type and Specifications: The type of materials used in a construction project can significantly impact costs. Different building materials, such as concrete, steel, lumber, and electrical components, have varying price points. Additionally, the quality and specifications of materials, such as grade, strength, or fire resistance, can also affect costs. Balancing cost and quality is crucial to ensure the construction project meets the required standards.
- Supplier Relationships: Building strong relationships with suppliers can be beneficial for managing material costs. Long-term partnerships and bulk purchasing agreements can often result in better pricing and discounts. It’s important to research and compare prices from multiple suppliers to ensure you are getting the best value for your materials.
- Transportation and Handling: The transportation and handling of materials can add to the overall cost. The distance between the supplier and the construction site, as well as the quantity and weight of the materials, can impact transportation expenses. Proper logistics planning and optimizing delivery routes can help minimize transportation costs.
- Sustainability and Energy Efficiency: Green building practices and energy-efficient materials may have higher upfront costs but can lead to long-term savings in terms of energy consumption and maintenance. Incorporating sustainable and energy-efficient materials into construction projects can help reduce operating costs and address environmental concerns.
- Availability: The availability of materials can impact costs. In some cases, certain materials may be in high demand or have limited supply, leading to higher prices. It’s important to consider material availability and potential lead times when planning a construction project to avoid delays and unexpected cost increases.
- Waste and Recycling: Proper waste management and recycling practices can help minimize material costs. Reusing or recycling materials from previous projects or reducing waste through efficient construction practices can result in cost savings. It’s important to explore sustainable waste management options to control material costs and minimize the project’s environmental impact.
By considering these factors, closely monitoring market conditions, and working closely with suppliers and project teams, you can effectively manage material costs in construction projects. Balancing quality, sustainability, and cost-effectiveness will help ensure the success of your construction endeavors.
Equipment Costs
Equipment costs are an important consideration in construction projects. The use of specialized machinery and equipment is often necessary to carry out various tasks, such as excavation, lifting heavy materials, and concrete pouring. Understanding the factors that influence equipment costs is crucial for accurate cost estimation and efficient project management.
Here are some key factors that can impact equipment costs in construction:
- Type of Equipment: The type of equipment needed for a construction project can vary significantly depending on the nature of the work. Equipment such as excavators, bulldozers, cranes, and concrete mixers may be required. Different equipment types have varying costs associated with renting or purchasing.
- Equipment Rental: Renting equipment is a common choice for many construction projects, especially when the equipment is only needed temporarily. Rental costs can vary based on factors such as the duration of the rental, the type of equipment, and any additional services required like transportation or maintenance. Comparing rental options from multiple suppliers can help identify the most cost-effective solution.
- Purchasing Equipment: For long-term or specialized projects, purchasing equipment may be more beneficial. However, purchasing costs should consider not only the initial purchase price but also ongoing maintenance, repair, and operational costs. Additionally, depreciation should be factored in when estimating equipment costs over an extended period.
- Equipment Specifications and Features: Equipment with advanced features or higher specifications may be more expensive to rent or purchase. These features can enhance efficiency, productivity, or safety, but their added cost should be carefully assessed to ensure they are necessary for the project’s requirements and budget.
- Equipment Maintenance and Repairs: Proper maintenance and regular servicing of equipment are essential to ensure their optimal performance and longevity. Budgeting for ongoing maintenance and repair costs is necessary to avoid unexpected expenses and equipment downtime that can hinder project progress.
- Equipment Utilization and Efficiency: Maximizing equipment utilization and efficiency is crucial to controlling costs. Proper scheduling and coordination of equipment usage can reduce idle time and optimize productivity. Ensuring trained operators and maintenance personnel are available can also mitigate the risk of equipment breakdowns and delays.
- Equipment Safety and Compliance: Safety regulations and compliance requirements may impact equipment costs. Ensuring that equipment meets safety standards and following proper protocols can help prevent accidents and costly legal issues.
Efficiently managing equipment costs is essential to maintain project budgets and timelines. Proper planning, evaluating rental versus purchase options, conducting cost-benefit analyses, and considering factors such as utilization, maintenance, and safety are essential steps in controlling equipment costs in construction projects.
Read more: What Are Soft Costs In Construction
Subcontractor Costs
In construction projects, subcontractors play a vital role in completing specific tasks or trades. Hiring subcontractors can help leverage specialized skills and expertise, manage workloads, and ensure efficient execution of different project components. Understanding the factors that influence subcontractor costs is crucial for accurate cost estimation and successful project management.
Here are some key factors that can impact subcontractor costs:
- Scope of Work: The complexity and scope of the work subcontractors are hired for can impact their costs. Tasks that require specialized skills, such as plumbing, electrical work, or HVAC installation, may come with higher costs due to the expertise and certifications required.
- Market Conditions: Subcontractor costs can be influenced by market conditions. In areas with high demand and limited supply of specialized labor, subcontractor rates may be higher. Conversely, during slower periods or in regions with more available subcontractors, costs may be more competitive.
- Experience and Reputation: Subcontractors with extensive experience and a good reputation may command higher rates due to the quality of their work and level of expertise. While hiring reputable subcontractors can come at a higher cost, their reliability and superior craftsmanship can contribute to the overall success of the project.
- Availability and Scheduling: Subcontractor costs may also be influenced by their availability and scheduling demands. If subcontractors need to adjust their schedules or work during non-standard hours, additional costs may be incurred. This can be especially true for projects with tight timelines or those that require subcontractors to work alongside other trades.
- Contract Terms: The terms of the subcontractor’s contract can impact costs. Factors such as payment schedules, warranties, and additional services required can affect the overall project budget. Evaluating and negotiating contract terms with subcontractors can help manage costs effectively.
- Quality Control and Performance: Ensuring quality control and monitoring subcontractor performance can help mitigate potential cost overruns. Clearly defining project requirements and deliverables, regular site inspections, and prompt issue resolution can help maintain subcontractor costs within the agreed-upon scope.
- Coordination and Communication: Effective coordination and communication between subcontractors and other project stakeholders are crucial for avoiding delays and additional costs. Clear communication channels, regular project meetings, and a collaborative approach can help ensure subcontractors stay on schedule and minimize disruptions.
Managing subcontractor costs requires careful consideration and planning. It’s essential to thoroughly evaluate subcontractor qualifications, gather multiple bids, and establish clear expectations and contract terms. By closely monitoring subcontractor performance and fostering strong working relationships, you can effectively manage costs while maintaining project quality and timeliness.
Tip: When estimating construction costs, consider factors such as materials, labor, permits, and site preparation. Get multiple quotes and factor in potential unforeseen expenses to create a realistic budget.
Overhead Costs
Overhead costs are indirect expenses associated with the overall management and operation of a construction project. These costs are not directly attributable to specific tasks or materials but are necessary for the project’s execution and its successful completion. Understanding and estimating overhead costs is essential for accurate budgeting and ensuring the project’s financial success.
Here are some key factors that can contribute to overhead costs in construction:
- Administrative Costs: Administrative costs include expenses related to project management and administration, such as salaries for administrative staff, office rent, utilities, office supplies, and insurance. These costs support the day-to-day operation and coordination of the project.
- Licensing and Permit Fees: Construction projects often require various permits, licenses, and certifications. These typically come with associated fees and expenses. It’s important to consider these costs during the planning stage to avoid unexpected financial burdens.
- Legal and Professional Fees: Legal fees and expenses related to contracts, dispute resolution, consulting services, and professional advice should be factored into the budget. Collaborating with legal and professional experts can help mitigate risks and ensure compliance with regulations.
- Equipment and Tools: Overhead costs may include expenses related to equipment and tools necessary for project management and administration. This can include office equipment, computers, software, and communication systems. Regular maintenance and upgrades should also be considered in the budget.
- Training and Education: Investing in the training and education of project personnel can contribute to improved project efficiency and quality. Costs associated with employee development, certifications, workshops, and seminars should be included in the overhead budget.
- Marketing and Business Development: Overhead costs may also include expenses related to marketing, advertising, and business development activities to promote the construction company and secure future projects. These costs help maintain a competitive edge in the market.
- Risk Management and Contingency: Overhead costs should account for contingency planning and risk management. Unforeseen events, project delays, and changes in scope can impact the project budget. Allocating a certain percentage of the overall budget for contingencies can help mitigate potential financial risks.
Properly estimating and managing overhead costs is crucial for the financial success of a construction project. Thoroughly analyzing and budgeting for these expenses will help ensure that the necessary resources are allocated appropriately. Regular monitoring and adjustment of overhead costs throughout the project’s lifecycle will help keep the project on track and within budget.
Design Costs
Design costs are an important component of construction projects, as they encompass the expenses associated with the architectural and engineering design services. Proper design is crucial for creating functional, structurally sound, and aesthetically pleasing buildings. Understanding the factors that impact design costs is essential for accurate budgeting and successful project execution.
Here are some key factors that can contribute to design costs in construction:
- Design Complexity: The complexity of the architectural and engineering design required for a project can impact design costs. Projects with unique or intricate designs, irregular layouts, or unconventional building materials may require more time and expertise from the design team, resulting in higher costs.
- Design Team Experience and Expertise: The experience and expertise of the design professionals involved in the project can influence design costs. More experienced and renowned architects and engineers may command higher fees due to their reputation and track record. However, their expertise and attention to detail can contribute to the successful completion of the project.
- Project Size and Scope: The size and complexity of the project impact design costs. Larger projects often require more extensive design work and documentation. The number of floors, building height, and intricate design requirements can all contribute to increased design costs.
- Design Iterations and Revisions: Design costs can be affected by the number of iterations and revisions required to finalize the design. Multiple design phases and revisions can extend the design timeline and increase costs. Effective communication and collaboration between the project team and the design professionals can help minimize revisions and associated costs.
- Regulatory Compliance: Compliance with local building codes and regulations is a critical aspect of the design process. The complexity and strictness of these regulations can impact design costs. Design professionals need to ensure that the design meets all relevant codes and regulations, which may require additional time and resources.
- Design Software and Tools: Design costs may include expenses related to design software, computer systems, and other tools utilized by the design professionals. These technology investments enable efficient and accurate design work, but they also incur ongoing maintenance and licensing costs.
- Data Collection and Site Analysis: Design costs can be influenced by the level of data collection and site analysis required during the design process. Conducting thorough site inspections, soil tests, and environmental assessments may be necessary, particularly for projects with unique site conditions. These activities can contribute to design costs but are essential for ensuring the design is tailored to the specific site requirements.
Properly budgeting for design costs ensures that the necessary resources and expertise are allocated to create a well-designed and functional building. It’s important to collaborate closely with design professionals, clearly communicate project requirements, and plan for potential design revisions to manage costs effectively. By valuing the importance of good design, you can enhance the overall success and value of your construction project.
Site Preparation Costs
Site preparation is a crucial phase in any construction project, as it involves clearing and preparing the land before construction activities can commence. Proper site preparation is essential for ensuring a solid foundation and smooth construction process. Understanding the factors that influence site preparation costs is vital for accurate budgeting and successful project execution.
Here are some key factors that can contribute to site preparation costs:
- Site Conditions: The existing conditions of the construction site can drastically impact site preparation costs. Sites with uneven terrain, poor soil conditions, or existing structures may require additional work, such as grading, excavation, or demolition. These tasks can contribute to increased costs due to the complexity and additional labor and equipment needed.
- Site Access: The ease of access to the construction site plays a role in site preparation costs. Sites that are difficult to access due to limited roadways, bridges, or obstacles may require additional resources for transportation and logistics. Ensuring proper access routes are in place can help minimize costs and facilitate timely delivery of materials and equipment.
- Site Clearing and Demolition: Before construction can begin, existing structures, debris, vegetation, and trees may need to be cleared and removed from the site. The extent of site clearing and demolition required can impact costs. Factors such as the size of the site, type of structures, and environmental considerations may influence the complexity and associated expenses of these activities.
- Utility Connections: Connecting the construction site to necessary utilities, such as water, electricity, gas, and telecommunications, is an essential aspect of site preparation. The distance of the site from existing utility services and the complexity of the connections required can affect costs. Extensive utility work, including trenching or installing infrastructure, may be necessary, and associated costs should be considered during budgeting.
- Environmental Considerations: Construction projects are subject to environmental regulations and considerations. Environmental assessments, mitigation measures, and compliance with environmental laws may be required during the site preparation phase. These activities can contribute to additional costs, but they are important for minimizing environmental impact and ensuring sustainable construction practices.
- Site Security: Protecting the construction site from trespassing, theft, and vandalism is a concern during site preparation. Costs associated with site security measures, such as security fencing, surveillance cameras, and security personnel, should be factored into the budget.
- Site Stabilization and Drainage: Ensuring proper site stabilization and drainage is crucial to prevent soil erosion, water damage, and structural issues. Measures such as installing retaining walls, drainage systems, and erosion control mechanisms may be necessary. These activities contribute to site preparation costs but are essential for creating a sturdy foundation and maintaining the longevity of the construction project.
Thoroughly assessing the site conditions, collaborating with engineering and site preparation experts, and considering potential challenges during the planning phase are essential for managing site preparation costs effectively. By allocating the necessary resources and attention to site preparation, you can lay the groundwork for a successful construction project.
Read more: What Is Overhead Cost In Construction
Permitting and Inspection Costs
Obtaining the necessary permits and conducting inspections are crucial steps in the construction process to ensure compliance with local regulations and building codes. Permitting and inspection costs are essential components that should be considered when budgeting for a construction project. These costs cover the fees associated with obtaining permits, submitting documents, and conducting inspections throughout the various stages of the project.
Here are the key elements that contribute to permitting and inspection costs:
- Permit Fees: Each construction project requires certain permits, which vary depending on factors such as the project type, location, and size. Permit fees are determined by local authorities and cover the administrative costs associated with reviewing and approving permit applications. The complexity and scale of the project typically influence permit fees.
- Plan Review: Before permits are issued, the project plans and specifications are reviewed by relevant authorities. Plan review fees are charged to compensate for the time and expertise required to ensure the proposed project complies with building codes and regulations. The size and complexity of the project can affect plan review fees, as more time and resources may be needed for review and approval.
- Specialized Permits: Depending on the nature of the project, specialized permits may be required. These can include permits for activities such as excavation, environmental impact, historical preservation, or the installation of specific equipment. Obtaining specialized permits often involves additional fees and may require additional time for review and approval.
- Inspection Fees: Inspections are conducted at various stages of the construction process to ensure compliance with building codes and regulations. Inspection fees cover the cost of sending inspectors to the construction site to review the work being performed. The number and frequency of inspections required for a project can vary depending on factors such as the project scope, complexity, and local regulations.
- Reinspections: If any deficiencies are identified during inspections, reinspections may be required once corrections have been made. Reinspection fees cover the cost of the follow-up inspections conducted to verify that the necessary changes have been implemented and compliance has been achieved.
- Code Compliance: Ensuring that the project meets all building code requirements is crucial for obtaining permits and passing inspections. Costs associated with code compliance may include fees for additional design or engineering work needed to meet code specifications, as well as fees for tests and certifications required to demonstrate compliance.
- Timing and Delays: Permitting and inspection costs may be influenced by timing issues and scheduling delays. Costs can increase if permits are obtained on an expedited basis or if inspections need to be rescheduled due to construction delays or changes in project timelines.
Properly budgeting for permitting and inspection costs is essential to avoid delays and ensure compliance with local regulations. It’s important to work closely with the regulatory authorities, engage in clear communication, and allocate adequate resources to meet the necessary permitting requirements and pass inspections successfully. By factoring in these costs, you can ensure a smooth and compliant construction process.
Contingency Costs
Contingency costs are an essential aspect of construction budgeting and planning. They are a buffer set aside to account for unforeseen circumstances, unexpected expenses, and potential risks that may arise during the course of a construction project. Contingency costs provide a financial cushion to address unforeseen challenges without jeopardizing the overall project budget or timeline.
Here are the key considerations regarding contingency costs in construction:
- Scope Changes: During the course of a construction project, changes in project scope are not uncommon. These changes may arise due to design revisions, client requests, or unforeseen site conditions. Contingency costs help cover the additional expenses associated with accommodating scope changes and ensuring the project can adapt without disrupting the overall budget.
- Unforeseen Site Conditions: Despite thorough pre-construction site analysis, unexpected site conditions may be encountered once construction commences. These conditions may require additional work, such as soil stabilization, remediation, or unexpected utility relocations. Contingency funds help cover the costs associated with addressing these unexpected site conditions.
- Market Fluctuations: Construction projects can be affected by market fluctuations, such as changes in material prices, labor rates, or fuel costs. These fluctuations can impact the project’s overall budget. Contingency costs act as a safeguard against such market uncertainties, allowing the project to absorb any cost increases without compromising its financial viability.
- Weather Delays: Inclement weather conditions can significantly impact construction schedules and timelines. Unexpected weather delays can require additional resources or extended project durations, resulting in higher costs. Contingency funds help mitigate the financial implications of weather-related disruptions, ensuring the project stays on track despite unforeseen weather events.
- Change Orders: Change orders often occur in construction projects due to client requests or unforeseen circumstances. These changes may require adjustments to project plans, materials, or labor. Contingency costs provide a financial cushion to accommodate approved change orders without negatively affecting the project’s overall budget.
- Project Risks: Construction projects inherently come with risks, such as safety incidents, legal disputes, or unforeseen delays. Contingency funds help manage and mitigate these risks by providing the necessary financial resources to address unexpected challenges as they arise throughout the project lifecycle.
- Quality Assurance: Maintaining quality standards throughout the construction process is critical. Unexpected issues related to quality or workmanship may require additional resources or corrective measures. Contingency costs can cover these unforeseen expenses, ensuring that the project meets the desired quality standards.
Contingency costs should be budgeted and allocated based on the unique characteristics of each project. The percentage of contingency funds will vary depending on several factors, including project size, complexity, and level of risks involved. It is essential for project managers to continually assess project progress, monitor risks, and manage the use of contingency funds effectively.
By properly factoring in contingency costs, construction projects can be better prepared to navigate unexpected challenges and maintain financial stability throughout the construction process.
Conclusion
Construction costs are a fundamental consideration in any construction project. Understanding the various factors that influence these costs is essential for accurate budgeting, successful project management, and overall project success. From labor and material costs to equipment and subcontractor costs, each element plays a vital role in determining the total expense. Overhead costs, design costs, site preparation costs, and permitting and inspection costs are also significant components to consider.
Labor costs are influenced by factors such as skill level, labor availability, and project complexity. Material costs can vary based on market conditions, material type and specifications, and supplier relationships. Equipment costs depend on the type of equipment needed, rental or purchase options, and equipment utilization and efficiency. Subcontractor costs are impacted by scope of work, market conditions, and workforce experience and reputation.
Overhead costs cover the administrative, legal, and operational expenses associated with the construction project. Design costs involve the architectural and engineering design services required for the project. Site preparation costs encompass site clearing, stabilization, and utility connections. Permitting and inspection costs cover the fees associated with obtaining permits and conducting inspections throughout the project.
Finally, contingency costs are a crucial consideration to account for unforeseen circumstances, scope changes, and market fluctuations that can impact the project’s budget and schedule.
By comprehensively considering all these factors and incorporating them into the budgeting and planning stages, construction professionals can ensure a more accurate cost estimation, effective resource allocation, and successful project delivery. Balancing cost-efficiency, quality, and adherence to regulations is a key challenge in managing construction costs. Regular monitoring, risk assessment, and collaboration with stakeholders and professionals in the industry are essential for controlling costs and achieving project goals.
Ultimately, by understanding and carefully managing construction costs, construction projects can be executed with confidence, resulting in successful outcomes and client satisfaction.
Frequently Asked Questions about What Are Construction Costs
Was this page helpful?
At Storables.com, we guarantee accurate and reliable information. Our content, validated by Expert Board Contributors, is crafted following stringent Editorial Policies. We're committed to providing you with well-researched, expert-backed insights for all your informational needs.
0 thoughts on “What Are Construction Costs”