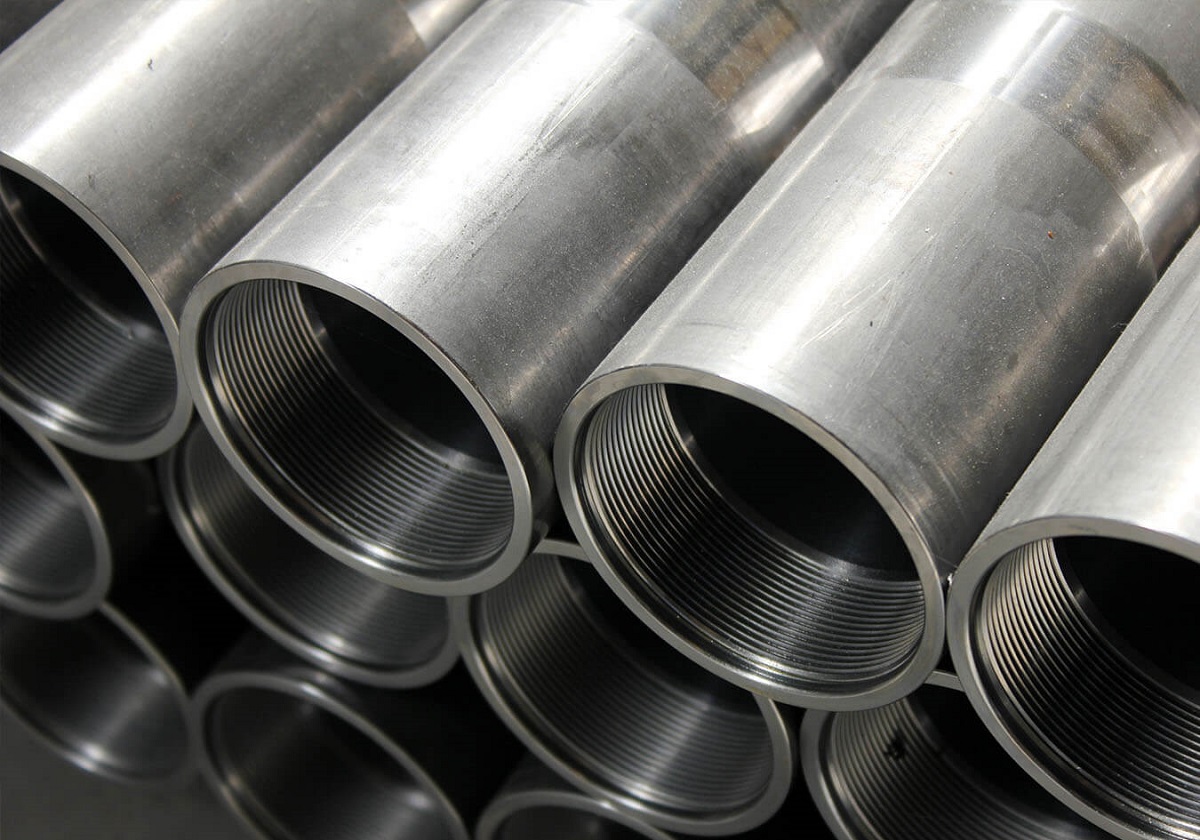
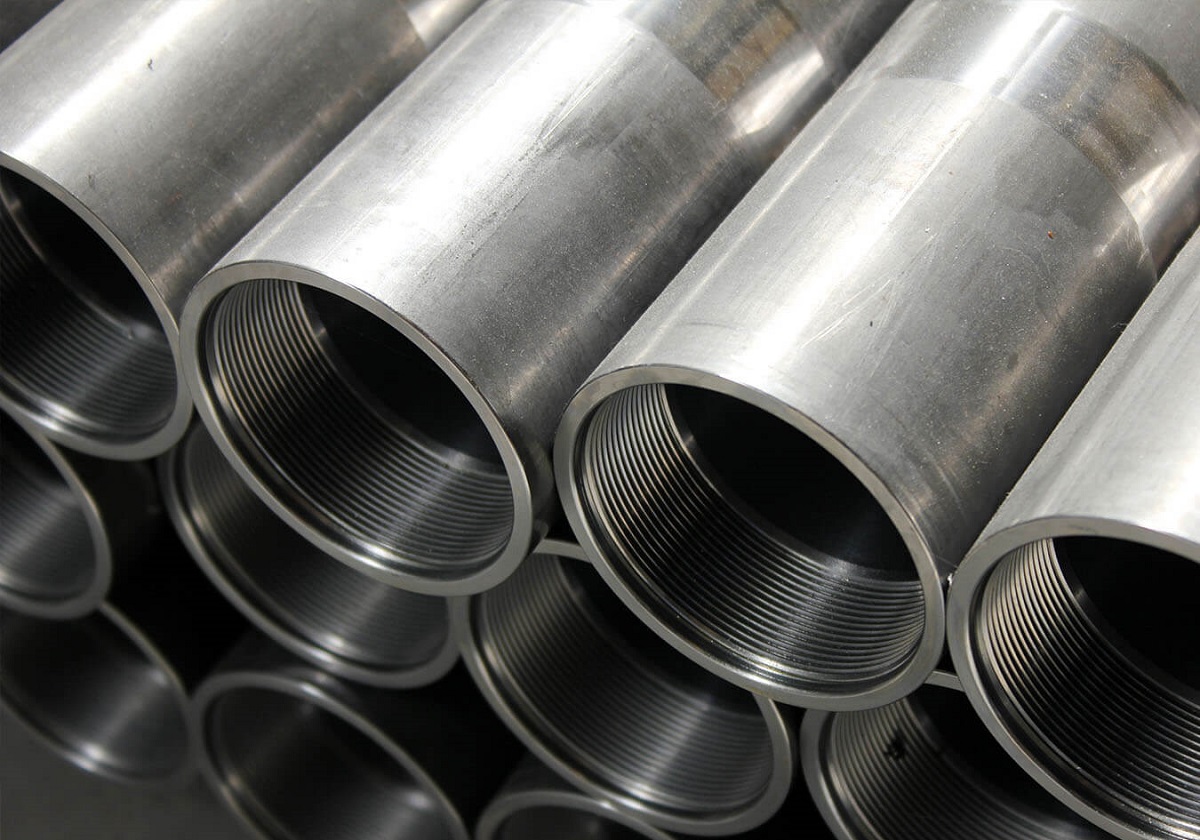
Articles
What Is Rigid Metal Conduit
Modified: May 6, 2024
Discover everything you need to know about rigid metal conduit in this enlightening article. Gain valuable insights and stay informed!
(Many of the links in this article redirect to a specific reviewed product. Your purchase of these products through affiliate links helps to generate commission for Storables.com, at no extra cost. Learn more)
Introduction
Rigid metal conduit, also known as RMC, is a type of electrical conduit used for protecting and routing electrical wiring in commercial and industrial applications. It is made of durable and rigid materials, typically steel or aluminum, and provides excellent protection against physical damage, moisture, and other environmental factors.
RMC is widely regarded as one of the most reliable and secure types of conduit due to its inherent strength and durability. It is often used in more demanding or hazardous environments where protection from mechanical impact or corrosive agents is essential.
This article explores the key features, advantages, applications, installation process, maintenance considerations, and a comparison of rigid metal conduit with other types of conduit.
Key Takeaways:
- Rigid metal conduit (RMC) is a durable and fire-resistant option for protecting electrical wiring in demanding environments, making it ideal for industrial facilities, outdoor installations, and high fire risk areas.
- When compared to other types of conduit, RMC stands out for its robust protection, grounding capability, and large wiring capacity, making it a preferred choice for applications where durability and fire resistance are crucial considerations.
Read more: What Is A Metal Conduit Made Of
Definition of Rigid Metal Conduit
Rigid metal conduit (RMC) is a thick-walled metallic tubing designed to protect electrical wiring from damage. It is typically made of galvanized steel or aluminum and is available in various sizes, ranging from ½ inch to 6 inches in diameter.
RMC is characterized by its rigidity and durability, making it suitable for use in demanding applications. The metal construction provides excellent protection against physical impact, moisture, and corrosive substances. It is also fire-resistant, making it ideal for installations in areas with high fire risk.
The walls of RMC are significantly thicker compared to other types of conduit, such as Electrical Metallic Tubing (EMT) or PVC conduit. This added thickness enhances the conduit’s resistance to damage, making it more suitable for applications where mechanical protection is crucial.
RMC is typically used in commercial and industrial settings where wiring needs robust protection. It is commonly found in factories, warehouses, power plants, and outdoor installations.
It is important to note that RMC is often used in conjunction with fittings, such as couplings, elbows, and connectors, to create a complete conduit system. These fittings allow for changes in direction, connection points, and customization to facilitate the routing and installation of the electrical wiring.
Advantages of Rigid Metal Conduit
Rigid metal conduit (RMC) offers several advantages that make it a popular choice for electrical wiring installations. Here are some of the key advantages of using RMC:
- Durability: RMC is highly durable and can withstand physical impact, making it suitable for installations in areas prone to mechanical damage. It can protect electrical wiring from being crushed, pierced, or damaged by heavy objects.
- Fire Resistance: RMC is inherently fire-resistant due to its metal construction. In the event of a fire, it can help prevent the spread of flames and protect the wiring inside. This is especially crucial in commercial and industrial settings where fire safety is paramount.
- Corrosion Resistance: RMC is typically made of galvanized steel or aluminum, which provides excellent resistance against corrosion. This feature makes it suitable for outdoor installations or in environments where moisture or corrosive substances may be present.
- Secure Wiring: RMC provides a secure and tamper-resistant conduit system. The rigid construction prevents unauthorized access to the wiring, protecting it from accidental damage or interference.
- Grounding Capability: The metal construction of RMC enables it to act as an effective grounding conductor. It can help dissipate electrical faults and safeguard against electrical shock hazards.
- Large Wiring Capacity: RMC has a larger internal diameter compared to other types of conduit. This allows for easier installation and accommodates larger bundles of wires, making it suitable for applications requiring multiple electrical circuits.
- Longevity: RMC has a long lifespan and can provide reliable protection for electrical wiring over an extended period. It is resistant to degradation from environmental factors, making it a cost-effective choice in the long run.
Overall, the advantages of RMC make it a preferred conduit option for installations where durability, fire resistance, corrosion resistance, and secure wiring are crucial considerations.
Applications of Rigid Metal Conduit
Rigid metal conduit (RMC) is widely used in a variety of applications where the protection of electrical wiring is essential. Its durability, fire resistance, and physical protection qualities make it suitable for numerous commercial and industrial settings. Here are some common applications of RMC:
- Industrial Facilities: RMC is commonly used in industrial facilities such as factories, power plants, refineries, and manufacturing plants. These environments often have harsh conditions, including exposure to heavy machinery, chemicals, and extreme temperatures. RMC provides superior protection for electrical wiring in such challenging settings.
- Commercial Buildings: In commercial buildings such as offices, hospitals, schools, and retail spaces, RMC is favored for its durability and ability to withstand high usage volumes. It ensures the safety and integrity of the electrical systems, particularly in areas with heavy foot traffic or areas prone to accidental damage.
- Outdoor Installations: RMC is an excellent choice for outdoor installations due to its resistance to moisture, harsh weather conditions, and UV exposure. It is often used for outdoor lighting, parking lot installations, and outdoor signage to provide a reliable conduit system that protects the wiring from the elements.
- High Fire Risk Areas: RMC is commonly installed in areas with elevated fire risks, such as chemical plants, storage facilities, or sites with flammable materials. Its fire resistance helps prevent the spread of flames and provides crucial protection for the electrical systems in the event of a fire.
- Hazardous Environments: RMC is suitable for use in hazardous environments that involve the presence of combustible gases, vapors, or dust. Its robust construction and ability to withstand impact make it ideal for protecting electrical wiring in areas such as oil refineries, chemical processing plants, or grain handling facilities.
These are just a few examples of where RMC is commonly used. Its versatility and ability to provide reliable protection for electrical wiring make it a preferred choice in applications where ruggedness, fire resistance, and physical security are crucial considerations.
Rigid metal conduit (RMC) is a thick-walled, heavy-duty metal tubing used to protect electrical wires in commercial and industrial applications. It provides excellent protection against physical damage and is suitable for outdoor and indoor use.
Installation Process of Rigid Metal Conduit
The installation process of rigid metal conduit (RMC) involves several steps to ensure proper routing and protection of electrical wiring. Here is a general overview of the installation process:
- Planning and Design: Before starting the installation, it is important to assess the electrical requirements and determine the appropriate size and route for the RMC. This involves taking measurements, considering the load requirements, and planning the conduit path.
- Preparation: Begin by gathering the necessary tools and materials for the installation, which may include RMC pipes, fittings, couplings, connectors, a conduit bender, a hacksaw, and a deburring tool.
- Marking and Layout: Use a measuring tape and pencil to mark the route of the conduit on the walls or ceiling where it will be installed. Ensure that the marks are level and aligned according to the planned path.
- Attach Fittings: Begin the installation by attaching fittings to the ends of the RMC pipes. This may include couplings, elbows, or connectors, depending on the direction changes or connection points required along the route.
- Bending the Conduit: If there are bends in the conduit path, use a conduit bender to create the necessary bends. Follow the manufacturer’s instructions and use a bending guide to ensure accurate and precise bending angles.
- Cutting and Deburring: Measure and mark the RMC pipes according to the desired lengths. Use a hacksaw to cut the pipes to the appropriate size. After cutting, use a deburring tool to remove any sharp edges or burrs from the cut ends.
- Mounting and Securing: Use straps or clamps to secure the RMC to the walls or ceiling, maintaining proper spacing and support as required by local electrical codes. Ensure that the conduit is securely fastened to prevent movement or sagging.
- Pulling and Securing Wires: Once the RMC is installed, proceed with pulling the electrical wires through the conduit. Attach a pulling rope or fish tape to the wires and carefully feed them through the conduit, ensuring they are not overly strained or damaged. Use appropriate connectors or bushings to secure the wires at entry and exit points.
- Grounding and Bonding: RMC, being metal, can serve as an effective grounding conductor. Ensure that proper grounding connections are made within the conduit system to create a safe electrical installation.
It is important to follow local electrical codes and regulations during the installation process to ensure a safe and compliant electrical system. Consulting with a certified electrician is recommended for complex installations or if you are unsure about any aspect of the process.
Read also: 14 Best Rigid Conduit for 2024
Maintenance and Safety Considerations for Rigid Metal Conduit
Rigid metal conduit (RMC) requires proper maintenance to ensure its continued effectiveness and safety. Here are some maintenance and safety considerations to keep in mind:
- Regular Inspections: Conduct routine inspections to check for any signs of damage, corrosion, or deterioration. Inspect the RMC for dents, bends, or any loose fittings or connections. Additionally, inspect the conduit supports, such as straps or clamps, to ensure they are secure.
- Cleanliness: Keep the RMC free from debris, dust, or any obstructions that could impede the proper function of the conduit. Regularly remove dirt or buildup from the exterior of the conduit to maintain its visual appearance and to prevent potential damage caused by corrosion.
- Protection from Physical Damage: Avoid any activities that could potentially damage the RMC, such as striking it with heavy objects or applying excessive force. Install protective barriers or guards in areas where the RMC is susceptible to accidental impact from vehicles or other equipment.
- Protection from Corrosion: While RMC is known for its corrosion resistance, it is still important to take measures to prevent corrosion. Ensure that all fittings and connections are securely tightened to prevent moisture penetration into the conduit. Apply appropriate corrosion-resistant coatings or paint to any exposed or vulnerable areas.
- Avoiding Overfilling: Avoid overfilling the RMC beyond its specified capacity. Overfilling may result in overheating and potentially damage the electrical wires. Refer to local electrical codes and guidelines to determine the maximum fill capacity for the specific size of RMC being used.
- Handling Electrical Faults: In the event of an electrical fault or malfunction, exercise caution and follow proper safety protocols. Turn off the power supply before inspecting or performing any maintenance on the RMC. Wear appropriate personal protective equipment (PPE) and seek the assistance of a qualified electrician if necessary.
- Comply with Electrical Codes: Ensure that all RMC installations and maintenance activities are in compliance with local electrical codes and regulations. Familiarize yourself with the specific requirements and seek professional advice when needed.
By following these maintenance and safety considerations, you can help extend the lifespan of the RMC and maintain a safe electrical environment. Regular inspections and proper care will ensure the continued functionality and reliability of the conduit system.
Comparison of Rigid Metal Conduit with Other Types of Conduit
When it comes to electrical conduit options, there are various types to choose from, each with its own advantages and considerations. Let’s compare rigid metal conduit (RMC) with other common types of conduit:
- Electrical Metallic Tubing (EMT): EMT is a thinner-walled conduit made of galvanized steel or aluminum. While it is more flexible and lightweight compared to RMC, it offers less protection against physical damage and is not as fire-resistant. RMC, on the other hand, provides robust protection and is suited for more demanding applications.
- Flexible Metal Conduit (FMC): FMC is a type of conduit that consists of a flexible metal outer covering with a plastic inner lining. It offers flexibility, making it easier to route in tight spaces or where movement is required. However, FMC is not as rigid as RMC and may not provide the same level of physical protection.
- PVC Conduit: PVC conduit is made of a durable and lightweight plastic material. It is an affordable option, easy to work with, and resistant to corrosion. However, PVC conduit is more susceptible to physical damage and has lower fire resistance compared to RMC.
- Intermediate Metal Conduit (IMC): IMC is similar to RMC but has a thinner wall, providing a balance between strength and weight. While IMC is lighter and easier to handle, it may not offer the same level of durability and protection against physical damage as RMC.
In summary, RMC stands out for its durability, fire resistance, and robust protection. It is commonly chosen for applications where physical protection is essential or in environments with high fire risks. However, other types of conduit may be suitable for different scenarios, depending on factors such as flexibility, cost, or ease of installation.
It is important to consider the specific requirements of the electrical installation, follow local electrical codes, and consult with professionals to determine the most appropriate type of conduit for a specific project.
Conclusion
Rigid metal conduit (RMC) is a reliable and durable option for protecting electrical wiring in commercial and industrial applications. With its inherent strength, fire resistance, and ability to withstand physical damage, RMC provides a robust conduit solution for demanding environments.
Throughout this article, we have explored the definition, advantages, applications, installation process, maintenance considerations, and a comparison of RMC with other types of conduit. RMC’s durability, corrosion resistance, grounding capability, and large wiring capacity make it an excellent choice for various industries and installations.
Whether it’s safeguarding electrical wiring in industrial facilities, outdoor installations, high fire risk areas, or hazardous environments, RMC offers the necessary protection and reliability. Its longevity and ability to meet the stringent requirements of electrical codes make it a cost-effective choice in the long term.
However, it’s important to consider specific project requirements and consult with professionals, taking into account factors such as flexibility, cost, and ease of installation, to determine the most suitable conduit option.
In conclusion, rigid metal conduit is a top choice for ensuring the safety, longevity, and integrity of electrical systems. By selecting RMC and following proper installation and maintenance practices, you can have confidence in the secure and efficient operation of your electrical infrastructure.
Curious about upgrading your setup? If you found our guide on rigid metal conduit enlightening, don't miss out on our next piece where we delve into the top choices for metal conduit for the upcoming year. Whether you're planning a major project or just looking to stay ahead with the best materials, this article will provide all the insights you need for making informed decisions. Ensure your projects are built to last with the best options available.
Frequently Asked Questions about What Is Rigid Metal Conduit
Was this page helpful?
At Storables.com, we guarantee accurate and reliable information. Our content, validated by Expert Board Contributors, is crafted following stringent Editorial Policies. We're committed to providing you with well-researched, expert-backed insights for all your informational needs.
0 thoughts on “What Is Rigid Metal Conduit”