Home>Articles>Why Is Electrical Continuity Required For Metallic Conduit
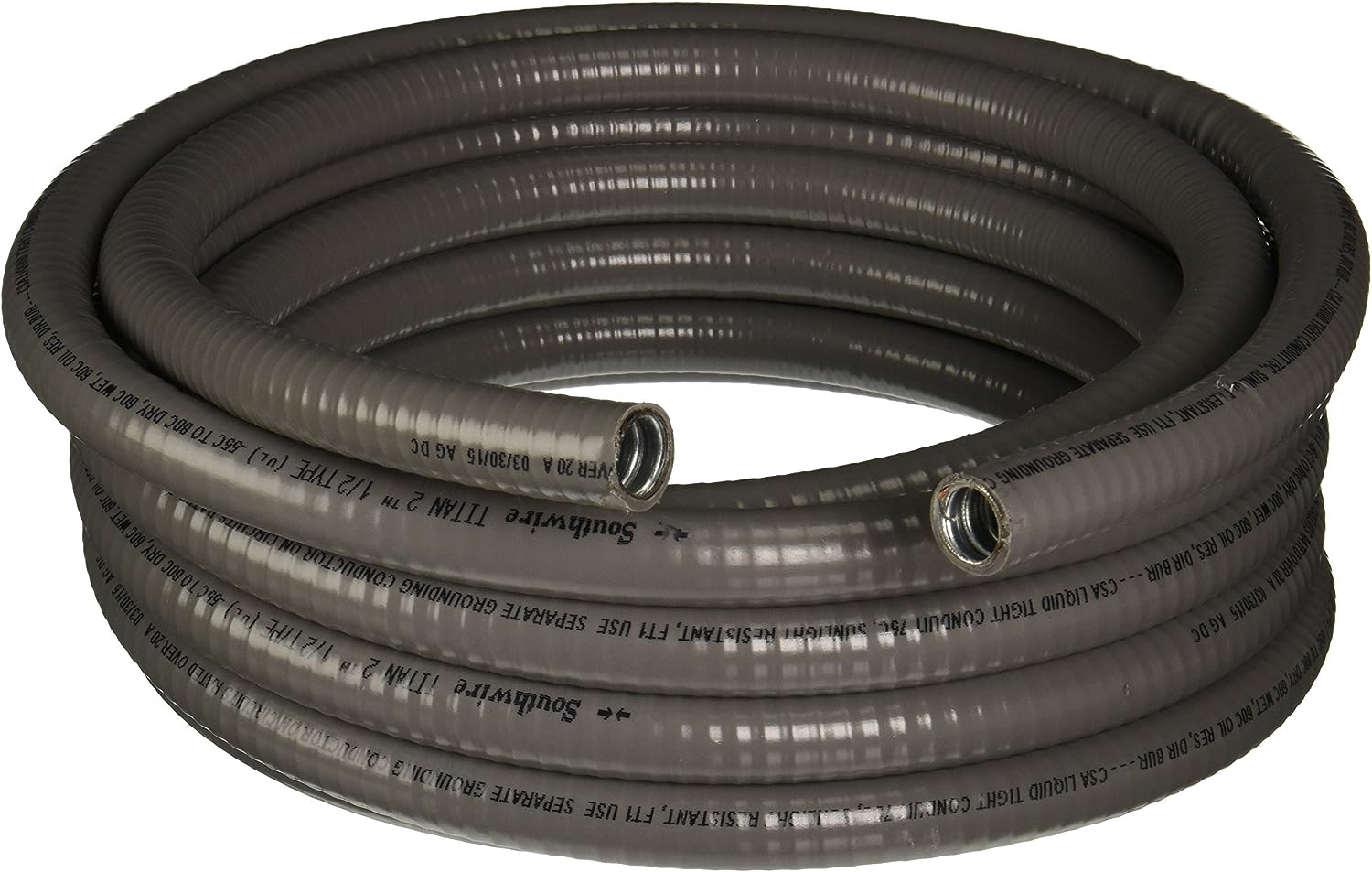
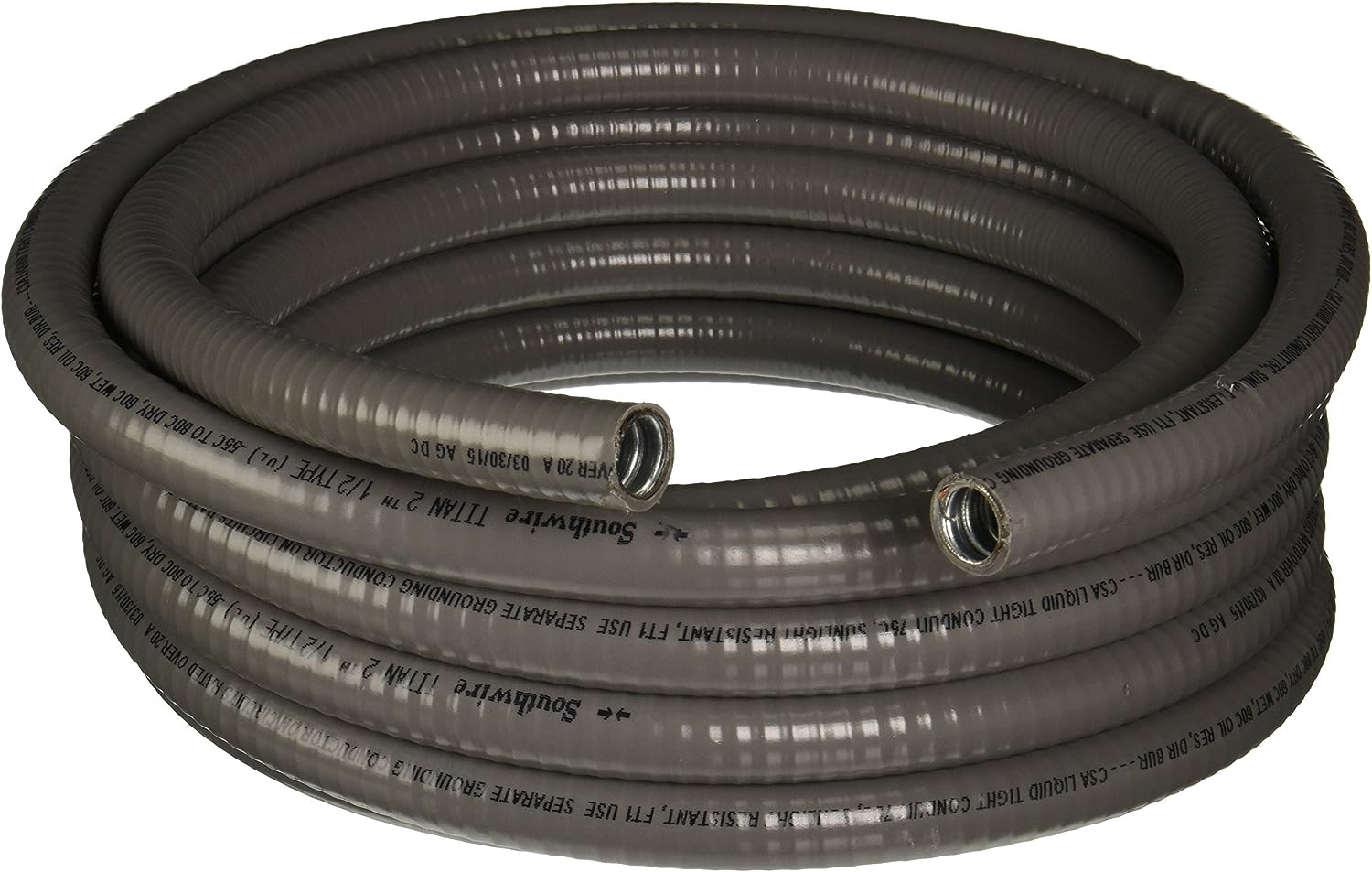
Articles
Why Is Electrical Continuity Required For Metallic Conduit
Modified: December 7, 2023
Discover why electrical continuity is crucial for metallic conduits in this informative article. Learn the importance of maintaining a conductive path to ensure safety and functionality.
(Many of the links in this article redirect to a specific reviewed product. Your purchase of these products through affiliate links helps to generate commission for Storables.com, at no extra cost. Learn more)
Introduction
When it comes to electrical installations, ensuring the safety and reliability of the system is paramount. One critical aspect of electrical installations is the use of metallic conduit, which serves as a protective pathway for electrical wiring. However, simply installing the conduit is not enough to guarantee a secure electrical system. Electrical continuity, a crucial requirement for metallic conduit, plays a significant role in maintaining the integrity of the electrical circuit.
In this article, we will explore the concept of electrical continuity, its importance in metallic conduit, the risks associated with inadequate electrical continuity, factors affecting continuity, testing and measurement methods, and the compliance requirements set forth by electrical codes and standards.
Are you ready to dive deeper into the world of electrical continuity? Let’s get started!
Key Takeaways:
- Electrical continuity is crucial for metallic conduit, ensuring safety, efficient current flow, equipment protection, and compliance with electrical codes. Proper installation, maintenance, and testing are essential for maintaining continuity and a reliable electrical system.
- Inadequate electrical continuity in metallic conduit can lead to electrical hazards, equipment failures, malfunctioning systems, non-compliance, and increased maintenance costs. Compliance with electrical codes, regular inspections, and addressing factors affecting continuity are vital for mitigating these risks.
Read also: 15 Best Electrical Conduit Metal for 2024
Definition of Electrical Continuity
Electrical continuity refers to the uninterrupted flow of electrical current through a conductor or a series of conductors. It is essential in maintaining the integrity and functionality of an electrical circuit. In the context of metallic conduit, electrical continuity ensures that there is a continuous path for the current to flow from the power source to the connected equipment or devices.
When electrical continuity is achieved, it means that there are no breaks, gaps, or interruptions in the conductive path. This is crucial because any disruption in the path can impede the flow of electricity, resulting in malfunctions, safety hazards, and potential damage to the electrical components.
It is important to note that electrical continuity is not limited to the metallic conduit alone. It encompasses the entire electrical system, including the wiring, connections, and grounding. All these components must be properly installed and maintained to ensure a continuous flow of current.
Without proper electrical continuity, the electrical system will suffer from various issues, such as voltage drops, increased resistance, overheating, and potential electrical failures. This is why it is crucial to understand the purpose of metallic conduit and its role in maintaining electrical continuity.
Purpose of Metallic Conduit
Metallic conduit is a type of protective tube or pipe that is used to encase electrical wiring, providing a secure pathway for electrical conductors. Its primary purpose is to protect the wiring from physical damage, moisture, chemicals, and other external factors that could compromise the electrical system’s integrity.
There are several types of metallic conduit available, including rigid metal conduit (RMC), intermediate metal conduit (IMC), and flexible metal conduit (FMC). Each type has its specific use and installation requirements.
The use of metallic conduit offers a range of benefits that contribute to the overall functionality and safety of the electrical system:
- Physical Protection: Metallic conduit provides a durable and robust protective barrier around electrical wires, shielding them from mechanical damage caused by impact, abrasion, or environmental conditions. This is particularly important in industrial settings, where the electrical system may be exposed to heavy machinery or corrosive substances.
- Fire Protection: Metallic conduit has inherent fire-resistant properties, helping to contain and prevent the spread of electrical fires. The conduit acts as a barrier, limiting the exposure of flammable materials to electrical sparks or arcing due to short circuits or overloads.
- EMI/RFI Shielding: Metallic conduit can provide electromagnetic interference (EMI) and radiofrequency interference (RFI) shielding, reducing the effect of electromagnetic waves on sensitive electronic equipment. This is particularly important in environments where there are high levels of electrical noise or in applications where electromagnetic compatibility is crucial.
- Grounding: Metallic conduit can serve as an effective grounding pathway, providing a low impedance path for fault currents to flow, minimizing the risk of electric shock and equipment damage. Proper grounding is essential for electrical safety and compliance with electrical codes and standards.
The purpose of metallic conduit goes beyond protecting the electrical wiring. It also plays a vital role in maintaining electrical continuity, ensuring a reliable and efficient electrical system.
The Importance of Electrical Continuity in Metallic Conduit
Electrical continuity is of utmost importance when it comes to metallic conduit installations. It is the backbone of a functioning and safe electrical system. Here are the key reasons why electrical continuity is crucial in metallic conduit:
- Safety: Electrical continuity ensures proper grounding, which is vital for electrical safety. By having a continuous path for fault currents to flow, any potential electrical faults or short circuits can be safely directed away from sensitive equipment and individuals, reducing the risk of electric shock and electrical fires.
- Efficient Current Flow: When electrical continuity is maintained within metallic conduit, there are no interruptions or resistance in the current flow. This allows for efficient transmission of electricity from the power source to the connected devices or equipment. Interruptions or gaps in continuity can cause voltage drops and increased resistance, leading to inefficiency, power loss, and reduced performance of electrical systems.
- Equipment Protection: Adequate electrical continuity protects the integrity and longevity of electrical equipment. Electrical systems rely on consistent and stable voltage levels to function optimally. Any disruptions in continuity can result in voltage fluctuations, which can damage sensitive components, reduce equipment lifespan, and lead to premature failures.
- Compliance with Electrical Codes: Electrical continuity is a fundamental requirement outlined in electrical codes and standards. Compliance with these regulations is necessary not only to ensure the safety of occupants but also to pass inspections and meet legal obligations. Failing to maintain electrical continuity in metallic conduit can result in non-compliance and potential fines or legal consequences.
Proper installation and maintenance of metallic conduit, along with ensuring electrical continuity, are essential for a reliable, safe, and efficient electrical system. It is crucial to follow industry best practices and adhere to electrical codes and standards to achieve optimal electrical continuity and system performance.
Risks of Inadequate Electrical Continuity
Inadequate electrical continuity within metallic conduit can pose significant risks and consequences. Failing to maintain proper continuity can lead to various issues that compromise the safety, reliability, and functionality of the electrical system. Here are some of the risks associated with inadequate electrical continuity:
- Electrical Hazards: Insufficient electrical continuity can result in increased electrical resistance, causing excessive heat buildup in the wiring and other electrical components. This can lead to overheating, melting, or even electrical fires. Additionally, inadequate continuity can increase the risk of electrical shocks by allowing fault currents to flow through unintended paths, such as equipment grounds or building structures.
- Equipment Failure: Without proper electrical continuity, electrical systems are more susceptible to voltage fluctuations and irregularities. These fluctuations can stress and damage sensitive electronic components, leading to premature equipment failures. The cost of replacing or repairing damaged equipment can be substantial, and downtime due to equipment failures can result in lost productivity and revenue.
- Malfunctioning Systems: Inadequate electrical continuity can cause disruptions in the flow of current, leading to malfunctioning electrical systems. This can result in erratic behavior, unreliable operation, and poor performance of connected devices, machinery, or appliances. For critical systems, such as those in healthcare facilities or data centers, the consequences of malfunctions can be severe, impacting patient care or data integrity.
- Non-compliance: Failure to maintain proper electrical continuity in metallic conduit can result in non-compliance with electrical codes and standards. Building regulations require electrical systems to adhere to specific safety standards, including continuity requirements. Non-compliance can result in legal consequences, fines, and even the shutdown of operations until the necessary corrections are made.
- Increased Maintenance and Repair Costs: Inadequate electrical continuity can lead to frequent breakdowns, power outages, and equipment failures. This translates into increased maintenance and repair costs as technicians are called to diagnose and fix the faulty systems. Moreover, identifying the root cause of the issues may be time-consuming and require extensive troubleshooting.
To mitigate these risks, it is crucial to ensure proper installation, regular maintenance, and periodic inspections of metallic conduit to maintain electrical continuity. Following industry best practices and complying with electrical codes and standards will promote a safe and reliable electrical system.
Electrical continuity is required for metallic conduit to ensure a safe path for fault currents, preventing electrical shock and fire hazards. Use proper fittings and bonding jumpers to maintain continuity.
Read more: Why Is Electrical Conduit So Expensive
Factors Affecting Electrical Continuity
Several factors can impact the electrical continuity within metallic conduit installations. Understanding these factors is essential for maintaining a reliable and efficient electrical system. Here are some key factors that can influence electrical continuity:
- Proper Installation: The correct installation of metallic conduit is crucial for maintaining electrical continuity. Conduit should be securely fastened, properly grounded, and adequately protected against physical damage. Improper installation, such as loose fittings, inadequate grounding, or improper connections, can introduce resistance and interruptions in the conductive path, hindering electrical continuity.
- Conduit Material and Condition: The material and condition of the metallic conduit can impact electrical continuity. Corrosion, rust, or other forms of degradation can inhibit the flow of electrical current. It is important to choose conduit materials that are resistant to corrosion and regularly inspect and maintain them to ensure their integrity.
- Connection Quality: The quality of connections within the metallic conduit system can significantly affect electrical continuity. Proper tightening and securely connecting conductors, junction boxes, fittings, and grounding components are essential to minimize resistance and ensure a continuous and reliable conductive path.
- Environmental Factors: Environmental conditions can impact electrical continuity. Extreme temperatures, humidity, moisture, and exposure to chemicals can lead to corrosion, insulation breakdown, and compromised conductive paths. It is crucial to choose appropriate conduit types and take preventive measures, such as sealing conduit joints and protecting against moisture, to maintain continuity in challenging environments.
- Mechanical Stress: Excessive mechanical stress on metallic conduit can cause deformation, cracks, or breaks, disrupting electrical continuity. Stress can result from improper installation, accidental impacts, or vibration from nearby machinery. Adequate support, protection, and proper bending techniques for conduit installations are necessary to avoid mechanical stress that can compromise continuity.
- Maintenance and Inspections: Regular maintenance and inspections play a vital role in preserving electrical continuity. Conducting periodic assessments to identify and address any signs of damage, degradation, or loose connections can prevent continuity issues before they result in malfunctioning systems or safety hazards.
By considering these factors during installation, maintenance, and routine inspections, it is possible to maintain proper electrical continuity within metallic conduit installations, ensuring a reliable and secure electrical system.
Testing and Measurement of Electrical Continuity
Testing and measuring electrical continuity within metallic conduit installations is essential to ensure the integrity and functionality of the electrical system. Here are some common methods used for testing and measuring electrical continuity:
- Visual Inspection: A visual inspection is the initial step in assessing the continuity of metallic conduit. Inspectors look for any signs of physical damage, loose connections, corrosion, or other abnormalities that may impact electrical continuity. Visual inspections should be performed during installation, maintenance, and periodic assessments.
- Resistance Testing: Resistance testing is a widely used method to measure and confirm electrical continuity. A digital multimeter is used to measure the resistance along the conductive path within the metallic conduit. The meter will display the resistance value, which should be very low (ideally close to zero) if there is proper continuity. Higher resistance values indicate potential interruptions or issues in the conductive path.
- Megger Testing: Megger testing, also known as insulation resistance testing, is conducted to evaluate the overall insulation integrity of the electrical system. It can indirectly assess electrical continuity by detecting any insulation faults that may affect continuity. Megger testing involves applying a high voltage to the system and measuring the resistance of the insulation. Any significant drop in resistance indicates potential continuity issues.
- Continuity Testers: Continuity testers are handheld devices specifically designed to check the continuity of electrical circuits. They typically generate a small electrical current and emit a visual or audible signal when continuity is detected. Continuity testers can be used to check the connectivity of the metallic conduit, ensuring that there are no breaks or interruptions in the conductive path.
- Thermographic Imaging: Thermographic imaging or infrared thermography can be utilized to identify hotspots or abnormal temperature patterns along the metallic conduit. Elevated temperatures could indicate resistance, loose connections, or other issues affecting electrical continuity. Thermographic imaging helps identify potential problems before they lead to failures or safety hazards.
It is important to note that electrical testing and measurement should be performed by trained professionals, following safety protocols and utilizing calibrated equipment. Regular testing and measurement of electrical continuity should be incorporated into the overall maintenance plan to ensure the long-term reliability and safety of the electrical system.
Compliance with Electrical Codes and Standards
Compliance with electrical codes and standards is crucial when it comes to electrical continuity in metallic conduit installations. These codes and standards are established by regulatory bodies to ensure the safety, functionality, and uniformity of electrical systems. Here are some key aspects of compliance with electrical codes and standards:
- National Electrical Code (NEC): The NEC is one of the most widely adopted electrical codes in the United States. It sets the minimum requirements for the design, installation, and maintenance of electrical systems. The NEC includes specific provisions related to electrical continuity, such as proper grounding, bonding, and wiring practices. Following the NEC guidelines is essential for achieving electrical continuity in metallic conduit installations.
- International Electrotechnical Commission (IEC) Standards: The IEC is an international standards organization that develops and publishes a wide range of standards related to electrical systems. These standards provide technical specifications and guidelines for various aspects of electrical installations, including electrical continuity. Compliance with IEC standards ensures international consistency and best practices in achieving electrical continuity.
- Local Electrical Codes and Regulations: In addition to national and international standards, local jurisdictions often have their own electrical codes and regulations. It is important to comply with these local codes to meet specific requirements and ensure conformity with regional electrical standards. Local building departments or authorities can provide information on the specific codes and regulations applicable to the geographic area.
- Inspections and Certifications: Electrical systems, including metallic conduit installations, are subject to inspections by local authorities to verify compliance with codes and standards. Inspections can occur at various stages, such as during installation, modification, or occupancy. Additionally, certifications from recognized testing laboratories may be required to demonstrate compliance with specific industry standards for electrical products and systems.
- Training and Qualifications: Ensuring that electrical work is conducted by trained and qualified professionals is essential for compliance with electrical codes and standards. Electricians and contractors should have the necessary knowledge, skills, and experience to properly install and maintain metallic conduit systems, including ensuring electrical continuity. Ongoing training programs and certifications help professionals stay up-to-date with the latest industry standards and practices.
Non-compliance with electrical codes and standards can result in safety hazards, legal consequences, and potential liability issues. It is crucial to consult and work with qualified professionals who have a thorough understanding of the applicable codes and standards to ensure proper installation, maintenance, and electrical continuity in metallic conduit systems.
Conclusion
Electrical continuity is a critical requirement for metallic conduit installations, playing a vital role in ensuring the safety, reliability, and functionality of electrical systems. Maintaining proper electrical continuity in metallic conduit is essential to prevent electrical hazards, equipment failures, malfunctions, and non-compliance with electrical codes and standards.
The purpose of metallic conduit goes beyond physical protection; it also provides grounding, fire protection, and EMI/RFI shielding. However, without adequate electrical continuity, these benefits cannot be fully realized, and the electrical system may be at risk.
Factors such as proper installation, conduit material and condition, connection quality, environmental factors, mechanical stress, and regular maintenance all influence electrical continuity within metallic conduit systems. It is important to address these factors and perform testing and measurement procedures, such as visual inspections, resistance testing, and thermographic imaging, to verify and ensure proper continuity.
Compliance with electrical codes and standards, such as the NEC and IEC standards, is essential for achieving and maintaining electrical continuity. Following local regulations, undergoing inspections, and ensuring trained and qualified professionals are involved in the installation and maintenance processes are critical steps in meeting these compliance requirements.
In conclusion, electrical continuity is a fundamental aspect of metallic conduit installations. By understanding its importance, addressing relevant factors, conducting testing and measurement procedures, and complying with electrical codes and standards, a reliable and safe electrical system can be achieved. Ensuring proper electrical continuity is vital for protecting individuals, preventing equipment failures, and maintaining compliance with regulatory requirements, ultimately contributing to the overall success of any electrical installation.
Frequently Asked Questions about Why Is Electrical Continuity Required For Metallic Conduit
Was this page helpful?
At Storables.com, we guarantee accurate and reliable information. Our content, validated by Expert Board Contributors, is crafted following stringent Editorial Policies. We're committed to providing you with well-researched, expert-backed insights for all your informational needs.
0 thoughts on “Why Is Electrical Continuity Required For Metallic Conduit”