Home>Articles>What Is The Normal Operating Temperature Of An Electric Motor
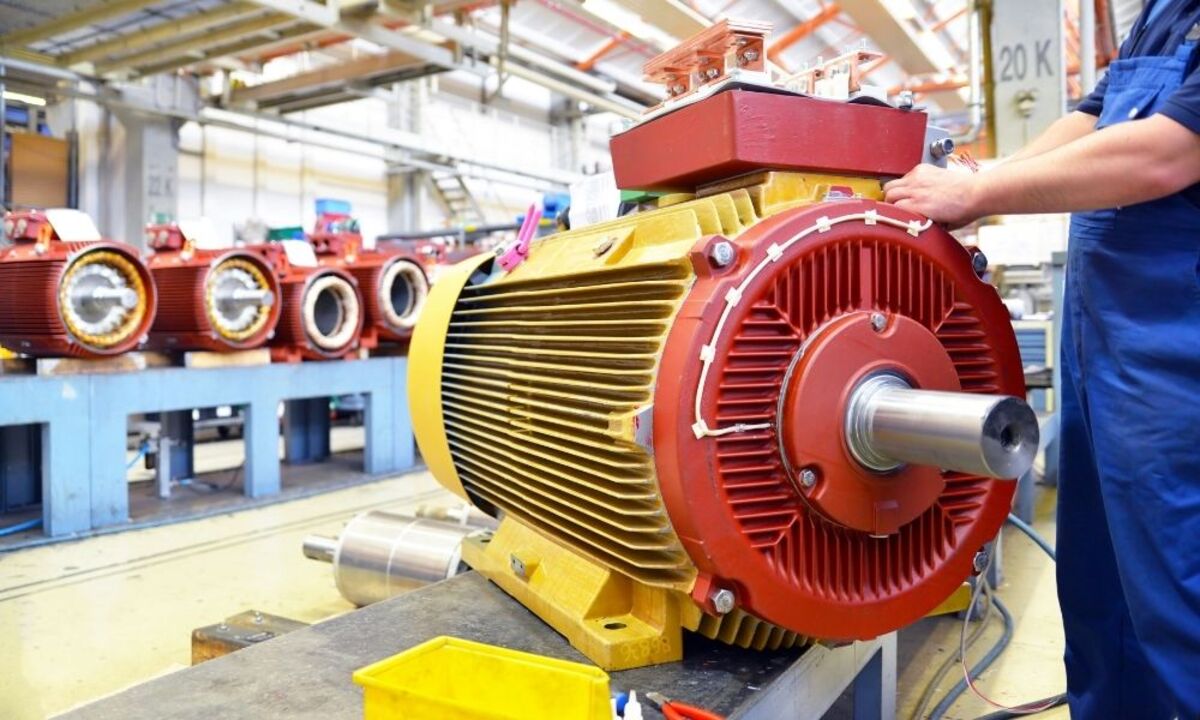
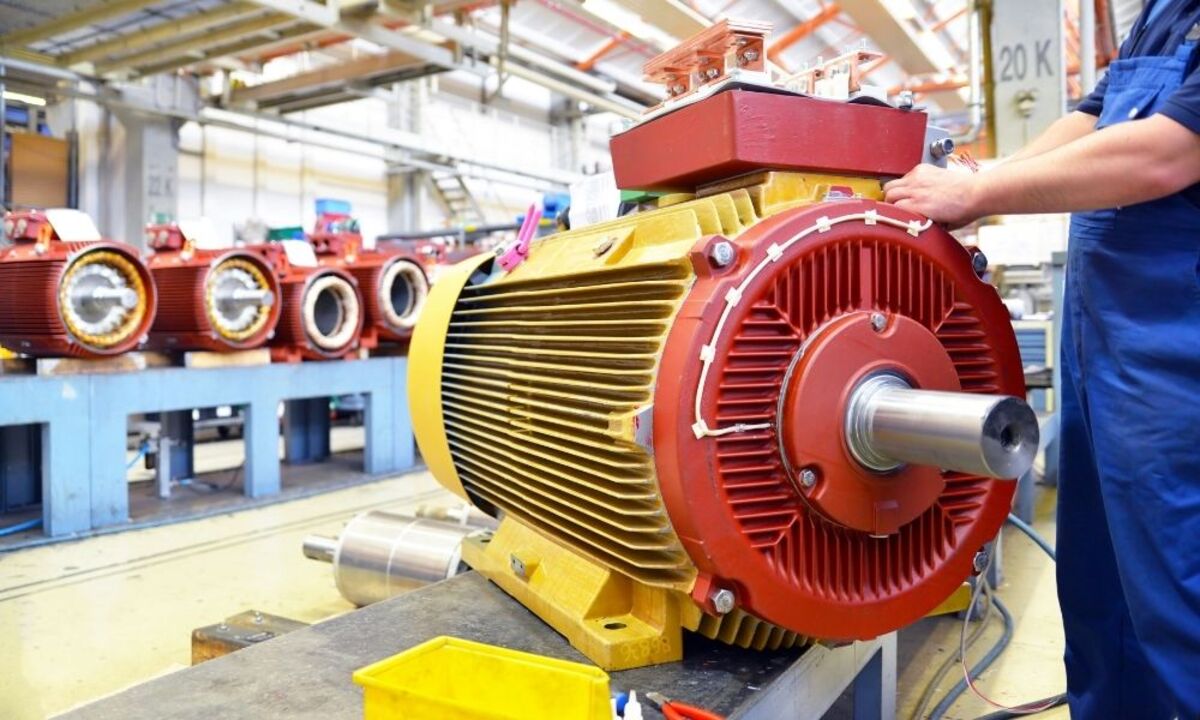
Articles
What Is The Normal Operating Temperature Of An Electric Motor
Modified: December 7, 2023
Discover the normal operating temperature range of electric motors in this comprehensive article. Learn how to maintain optimal conditions for your motor's longevity and performance.
(Many of the links in this article redirect to a specific reviewed product. Your purchase of these products through affiliate links helps to generate commission for Storables.com, at no extra cost. Learn more)
Introduction
Electric motors are widely used in various industries and applications, from powering machinery and equipment to driving vehicles. They play a crucial role in our modern world, converting electrical energy into mechanical energy. However, like any other mechanical device, electric motors generate heat during operation.
The temperature of an electric motor is a critical factor that affects its performance, efficiency, and lifespan. Understanding the normal operating temperature of an electric motor is essential for ensuring optimal functionality and preventing potential problems.
In this article, we will explore what constitutes the normal operating temperature of an electric motor, the factors that influence it, the consequences of operating outside the recommended temperature range, as well as strategies for monitoring and controlling motor temperature.
So, let’s dive into the world of electric motor temperature and gain valuable insights into this crucial aspect of motor operation.
Key Takeaways:
- Maintaining the normal operating temperature range of electric motors is crucial for optimal performance, efficiency, and longevity. Factors like load conditions, insulation class, and cooling mechanisms all influence motor temperature.
- Effective cooling strategies, regular maintenance, and temperature monitoring are essential for preventing overheating and ensuring reliable motor operation. Operating within the recommended temperature range is key to maximizing motor performance and lifespan.
Definition of Electric Motor Operating Temperature
The operating temperature of an electric motor refers to the temperature range within which the motor should ideally operate to ensure optimal performance and longevity. It is typically measured by monitoring the temperature of various motor components, such as the windings, bearings, and housing.
The operating temperature of an electric motor is influenced by several factors, including the motor’s design, load conditions, ambient temperature, cooling mechanisms, and insulation materials used. It is important to note that different types of motors may have different operating temperature ranges.
Electric motors are designed to generate some amount of heat during operation due to the flow of electrical current through the winding coils. This heat is caused by a combination of resistive losses in the conductors and magnetic losses due to hysteresis and eddy currents.
The operating temperature range of an electric motor is usually specified by the motor manufacturer. It is important to adhere to these guidelines to ensure that the motor operates within safe limits and performs optimally.
Operating the motor at temperatures outside the recommended range can have several negative effects. If the motor operates at too high a temperature, it can lead to accelerated aging of insulation materials, degradation of lubricants in bearings, and reduced efficiency. On the other hand, operating the motor at excessively low temperatures can cause issues with condensation, increased viscosity in lubricants, and premature wear of mechanical components.
By monitoring and controlling the operating temperature of an electric motor, it is possible to ensure optimal performance, prevent damage, increase efficiency, and extend the motor’s lifespan. In the next section, we will explore the various factors that influence the operating temperature of electric motors.
Factors Affecting Electric Motor Temperature
Several factors can influence the operating temperature of an electric motor. Understanding these factors is crucial for effectively monitoring and controlling motor temperature. Let’s take a closer look at some key factors:
1. Load Conditions: The load on an electric motor plays a significant role in determining its operating temperature. Motors that are consistently operated under heavy loads will generate more heat than those operating under lighter loads. It is important to ensure that the motor is appropriately sized for the intended load to prevent overheating.
2. Ambient Temperature: The temperature of the surrounding environment can have a direct impact on the operating temperature of the motor. Motors operating in hot environments will naturally experience higher temperatures, while those in cooler environments will operate at lower temperatures. It is essential to consider the ambient temperature when assessing the motor’s operating temperature range.
3. Insulation Class: Electric motors are categorized into different insulation classes, which determine the maximum allowable temperature that the insulation materials can withstand. The insulation class rating indicates the temperature at which the materials start to degrade. It is vital to choose a motor with an appropriate insulation class to ensure reliable operation within the intended temperature range.
4. Cooling Mechanisms: Electric motors employ various cooling methods to dissipate heat generated during operation. These cooling mechanisms can include air cooling, fan cooling, liquid cooling, or a combination of these methods. The effectiveness of the cooling system can significantly impact the operating temperature of the motor.
5. Motor Design: The design of the electric motor itself can influence its operating temperature. Factors such as the motor’s efficiency, ventilation system, and thermal conductivity of the materials used can all affect how effectively heat is dissipated. Motors with better design features tend to operate at lower temperatures and have improved performance.
6. Maintenance and Cleaning: Regular maintenance and cleaning of the motor are essential for optimal performance and temperature control. Dust, dirt, and debris can accumulate on the motor’s surface and hinder proper heat dissipation. Regularly inspecting and cleaning the motor can help prevent overheating.
7. Control System: The control system that regulates the motor’s operation can impact its temperature. Advanced control systems can incorporate features like thermal protection and temperature monitoring, ensuring that the motor operates within a safe temperature range.
By considering these factors, motor operators can better understand and manage the temperature of their electric motors. Monitoring and controlling the motor’s operating temperature is critical to optimizing its performance, efficiency, and lifespan. In the next section, we will discuss the recommended operating temperature range for electric motors.
Recommended Operating Temperature Range
The recommended operating temperature range for electric motors is typically provided by the motor manufacturer and can vary depending on the motor type, design, and insulation class. Operating the motor within this specified temperature range is crucial to ensure optimal performance, efficiency, and longevity.
In general, most standard electric motors have a recommended operating temperature range between 40°C (104°F) to 60°C (140°F). However, it is important to note that this range can vary, and it is always best to refer to the motor’s documentation or consult with the manufacturer for precise temperature guidelines.
Operating the motor within the recommended temperature range offers several benefits. Firstly, it ensures that the motor’s insulation materials maintain their integrity, preventing premature aging, breakdown, or electrical insulation issues. Secondly, it promotes efficient operation, as motors tend to have their highest efficiency within their recommended temperature range. And finally, it helps prolong the motor’s overall lifespan, reducing the risk of mechanical failures or malfunctions.
It is essential to understand that exceeding the upper limit of the recommended temperature range can have detrimental effects on the motor. High temperatures can lead to insulation degradation, increased resistance in the windings, and reduced lubricant effectiveness, which can ultimately result in motor failure or shortened lifespan.
On the other hand, operating the motor at temperatures below the lower limit of the recommended range can also introduce problems. These include increased viscosity of lubricants, reduced efficiency, condensation, and potential issues with bearing lubrication.
To ensure that the motor operates within the recommended temperature range, regular monitoring is essential. This can be achieved by using temperature sensors, thermocouples, or infrared thermometers to measure the temperature of critical motor components. By monitoring the temperature, motor operators can identify any deviations from the recommended range and take appropriate actions to mitigate potential issues.
In the next section, we will discuss the consequences of operating electric motors outside the recommended temperature range and the importance of monitoring and controlling motor temperature.
Consequences of Operating at High or Low Temperatures
Operating an electric motor outside the recommended temperature range can have significant consequences on its performance, efficiency, and overall lifespan. Let’s explore the consequences of operating at both high and low temperatures:
1. High Temperatures:
– Insulation Degradation: Excessive heat can cause the insulation material used in the motor to deteriorate more rapidly. This can lead to insulation breakdown, short circuits, and potential motor failures.
– Bearing Failure: High temperatures can accelerate the degradation of the lubricants used in the motor’s bearings. This can result in reduced bearing life, increased friction, and potential bearing failure.
– Reduced Efficiency: When operating at high temperatures, the motor’s efficiency is often compromised. Increased resistance in the windings and other components can lead to higher energy losses, reducing the overall efficiency of the motor.
– Voltage Instability: High temperatures can affect the voltage regulation of the motor, leading to voltage instability. This instability can have negative effects on the motor’s performance and cause unintended variations in motor speed and torque.
– Reduced Lifespan: Continuous operation at high temperatures can significantly shorten the lifespan of the motor. The accelerated aging of insulation materials, increased wear on mechanical components, and higher stress on the motor’s internal parts can all contribute to a reduced lifespan.
2. Low Temperatures:
– Condensation: Operating an electric motor in extremely low temperatures can result in condensation forming within the motor. This can lead to moisture-related issues, such as corrosion, insulation deterioration, and potential electrical failures.
– Increased Viscosity: Lubricants used in motors tend to become more viscous at low temperatures, hindering their effectiveness in lubricating moving parts. This can lead to increased friction, wear, and potential damage to bearings and other components.
– Efficiency Loss: Motors operating at lower temperatures may experience reduced efficiency due to the increased viscosity of lubricants and higher resistance in the windings. This can result in higher energy consumption and decreased overall performance.
– Mechanical Stress: Cold temperatures can cause contraction of motor components, leading to increased mechanical stress. This stress can result in premature wear, increased friction, and potential mechanical failures.
Operating an electric motor within the recommended temperature range is vital to prevent these consequences. Monitoring and controlling the motor’s temperature with the help of temperature sensors and proper cooling mechanisms can help maintain optimal operating conditions and ensure reliable motor performance.
In the next section, we will discuss various strategies for monitoring and controlling the temperature of electric motors.
The normal operating temperature of an electric motor is typically around 40-50°C (104-122°F). It’s important to monitor the temperature and ensure proper ventilation to prevent overheating.
Read more: What Is An Electric Motor Capacitor?
Monitoring and Controlling Electric Motor Temperature
Monitoring and controlling the temperature of electric motors is essential to ensure optimal performance, efficiency, and longevity. There are several strategies and techniques available to effectively monitor and control motor temperature. Let’s explore some of these:
1. Temperature Sensors: Temperature sensors, such as thermocouples or resistance temperature detectors (RTDs), can be installed at critical points within the motor to monitor temperature accurately. These sensors provide real-time temperature readings and can alert operators if the temperature exceeds the recommended range.
2. Thermal Imaging: Infrared cameras or thermal imaging technology can be used to visualize the heat distribution across different motor components. This allows for quick identification of any hotspots or areas of concern, enabling proactive measures to be taken to prevent potential overheating.
3. Motor Protection Devices: Motor protection devices, such as thermal overload relays or temperature controllers, can be installed to automatically monitor and protect the motor against excessive temperature rise. These devices can initiate protective actions, such as tripping the motor or activating cooling systems, when the temperature exceeds a predetermined threshold.
4. Insulation Monitoring: Regular insulation resistance testing can help assess the integrity of the motor’s insulation system. This testing identifies any insulation breakdown or degradation, which can lead to increased heat generation. By promptly identifying insulation issues, steps can be taken to prevent further damage and maintain safe operating temperatures.
5. Proper Ventilation and Cooling: Ensuring adequate ventilation and cooling for the motor is crucial to dissipate heat effectively. This can involve providing sufficient airflow around the motor, maintaining proper clearances, and utilizing cooling mechanisms such as fans or liquid cooling systems. Optimizing the motor’s cooling system based on the specific operating conditions can help regulate temperature and prevent overheating.
6. Regular Maintenance: Regular maintenance practices, such as cleaning motor components and inspecting for any signs of wear or damage, are vital for temperature control. Keeping the motor free from dust, dirt, and debris can improve heat dissipation and prevent obstructions that could lead to overheating.
7. Load Management: Proper load management is essential to prevent excessive heat generation in the motor. Ensuring that the motor is appropriately sized and not overloaded can help maintain optimal operating temperatures.
By implementing these monitoring and control strategies, motor operators can effectively manage and mitigate temperature-related issues. This leads to improved motor performance, increased energy efficiency, and an extended operational lifespan.
In the next section, we will discuss some common causes of motor overheating and how to address them effectively.
Common Causes of Overheating
Overheating is a common issue that can occur in electric motors and can lead to various performance problems and even motor failure if not addressed promptly. Understanding the common causes of motor overheating is crucial for implementing appropriate preventive measures. Let’s explore some of the common causes:
1. Overloading: Operating the motor beyond its rated capacity or continuously running it under heavy loads can result in excessive heat generation. Overloading can lead to increased current flow, higher resistive losses, and longer operating times, all of which contribute to elevated temperatures.
2. Insufficient Ventilation: Inadequate ventilation around the motor can impede proper heat dissipation. If the motor is enclosed in a tight space or if there are obstructions that restrict airflow, the heat generated during operation may not be effectively dissipated, leading to overheating.
3. Failure of Cooling Mechanisms: Cooling mechanisms, such as fans or cooling fins, can fail due to dust accumulation, mechanical damage, or motor malfunctions. Without proper cooling, heat dissipation is compromised, resulting in increased temperatures.
4. Faulty or Inadequate Cooling Systems: In some cases, the cooling systems designed to remove heat from the motor may be faulty or insufficient. This could be due to blocked coolant flow, malfunctioning fans, or insufficient coolant circulation. Inadequate cooling systems can result in heat build-up and subsequent overheating.
5. Poor Electrical Connections: Loose or faulty electrical connections can lead to increased electrical resistance, resulting in higher resistive losses and heat generation. It is important to ensure that all electrical connections are properly tightened and free from damage or corrosion.
6. Insulation Degradation: Over time, the insulation materials used in the motor can degrade, leading to reduced insulation effectiveness and increased heat generation. This can be caused by factors such as high temperatures, moisture ingress, chemical exposure, or aging of the motor.
7. Excessive Voltage Fluctuations: Voltage fluctuations, such as voltage surges or drops, can cause variations in motor performance and lead to increased heat generation. Fluctuations can result from power supply issues, unstable electrical grids, or motor control system malfunctions.
Addressing these common causes of motor overheating requires a combination of preventive measures and proactive maintenance practices. Regular inspection of the motor, ensuring proper ventilation, maintaining cooling systems, and addressing any issues with electrical connections or insulation can help prevent overheating and optimize motor performance.
In the next section, we will discuss strategies for cooling electric motors effectively to maintain their operating temperatures within the recommended range.
Strategies for Cooling Electric Motors
Cooling electric motors effectively is vital to maintain optimal operating temperatures, prevent overheating, and ensure efficient performance. There are several strategies and techniques available to cool electric motors. Let’s explore some of the most common strategies:
1. Proper Ventilation: Ensuring adequate ventilation around the motor is crucial for effective cooling. This can be achieved by providing sufficient clearance between the motor and surrounding objects and ensuring proper airflow. Ventilation can be enhanced by using vented motor enclosures or installing additional fans or blowers to promote air circulation.
2. Fan Cooling: Many electric motors come equipped with built-in cooling fans. These fans facilitate the movement of air over the motor’s surfaces, assisting in heat dissipation. It is important to ensure that the fan blades are clean, free from obstructions, and functioning properly.
3. Liquid Cooling: Liquid cooling systems can be employed for more demanding applications or motors operating in extreme conditions. These systems utilize coolants, such as water or specialized cooling fluids, to absorb and transfer heat away from the motor. Heat exchangers, pumps, and circulation systems are used to facilitate effective cooling.
4. Heat Sinks: Heat sinks are metallic fins or plates attached to the motor’s housing or specific components to increase the surface area for heat dissipation. Heat sinks help remove heat from sensitive areas, such as high-power electronics or areas prone to overheating, and transfer it to the surrounding air.
5. Thermal Insulation: In certain situations, thermal insulation can be applied to the motor’s housing or specific components to prevent heat transfer to surrounding objects. This helps maintain lower operating temperatures and protects adjacent equipment from excessive heat.
6. Regular Maintenance: Routine maintenance practices, such as cleaning the motor, removing dust, and debris, are essential for effective cooling. Regularly inspecting and cleaning the cooling fans, vents, and heat sinks ensures unobstructed airflow, enhancing cooling efficiency.
7. Temperature Monitoring and Control: Implementing temperature monitoring devices, such as temperature sensors or thermal imaging systems, allows operators to monitor the motor’s temperature in real-time. These systems can trigger alarms or initiate cooling measures when temperatures exceed the recommended range.
It is crucial to note that the selection and implementation of cooling strategies should be based on the specific motor design, application requirements, and environmental conditions. Consulting with motor manufacturers or cooling system experts can provide valuable insights and guidance for selecting the most suitable cooling methods.
By employing effective cooling strategies, motor operators can ensure that their electric motors operate within the recommended temperature range, optimizing performance, increasing efficiency, and prolonging the motor’s lifespan.
In the final section, we will conclude our discussion on electric motor operating temperatures.
Conclusion
Understanding and managing the operating temperature of electric motors is crucial for their optimal performance, efficiency, and longevity. Operating motors within the recommended temperature range ensures reliable operation and prevents potential issues that can arise from overheating or operating at excessively low temperatures.
Factors such as load conditions, ambient temperature, insulation class, cooling mechanisms, and motor design all play a role in determining the motor’s operating temperature. Monitoring and controlling the motor’s temperature can be achieved through various strategies, including temperature sensors, thermal imaging, motor protection devices, and regular maintenance practices.
Operating electric motors at high temperatures can lead to insulation degradation, bearing failures, reduced efficiency, and shortened lifespan. Conversely, operating at low temperatures can result in condensation, increased viscosity of lubricants, reduced efficiency, and mechanical stress. It is important to adhere to the recommended temperature range to prevent these consequences.
Effective cooling strategies, including proper ventilation, fan cooling, liquid cooling, heat sinks, and thermal insulation, can help maintain optimal operating temperatures and prevent overheating. Regular maintenance practices, such as cleaning the motor and monitoring electrical connections, also contribute to cooling efficiency.
By implementing these strategies and practices, motor operators can ensure that their electric motors operate within the recommended temperature range, thereby maximizing their performance, energy efficiency, and longevity.
In conclusion, maintaining the normal operating temperature of electric motors is essential for their reliable and efficient functioning. Through careful monitoring, control, and cooling, motor operators can create an environment that promotes optimal performance and extends the lifespan of their electric motors.
Frequently Asked Questions about What Is The Normal Operating Temperature Of An Electric Motor
Was this page helpful?
At Storables.com, we guarantee accurate and reliable information. Our content, validated by Expert Board Contributors, is crafted following stringent Editorial Policies. We're committed to providing you with well-researched, expert-backed insights for all your informational needs.
0 thoughts on “What Is The Normal Operating Temperature Of An Electric Motor”